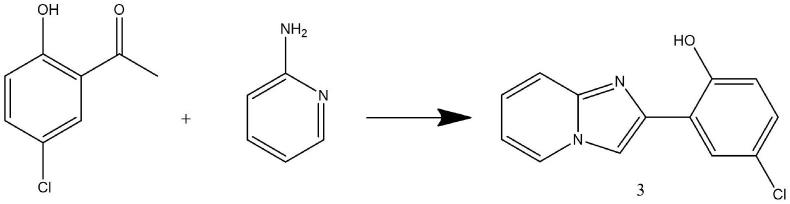
1.本发明涉及钠离子电池领域,具体涉及一种基于高温烧结改性的生物质基硬碳材料生产工艺。
背景技术:2.钠离子电池以其资源丰富、价格低廉的优点而受到研究者的广泛关注。然而,钠离子电池负极材料的电化学性能有待进一步提高,主要存在的问题是:较大的离子半径和原子质量导致na
+
脱/嵌动力学性能较差,很难嵌入到负极材料中,从而引起钠离子电池循环寿命、容量、首次库伦效率和倍率性能较差。
3.生物质硬碳因其原材料丰富、制备工艺简单、价格低廉、又能解决焚烧生物质带来的大气污染问题,使其成为钠离子电池理想的负极材料。
4.如何改善现有的生物质基硬碳材料的电化学性能不佳,有待进一步提高是本发明的关键,因此,亟需一种基于高温烧结改性的生物质基硬碳材料生产工艺来解决以上问题。
技术实现要素:5.为了克服上述的技术问题,本发明的目的在于提供一种基于高温烧结改性的生物质基硬碳材料生产工艺:通过将松果加入至去离子水中超声清洗,之后干燥、粉碎、过筛,得到松果粉,将松果粉加入至真空管式炉中保温处理,随炉冷却到室温,得到炭化粉,将炭化粉加入至氢氧化钾溶液处理,之后加入至盐酸溶液中进行处理,之后洗涤、干燥,得到活化炭化粉,将活化炭化粉、掺杂剂以及去离子水进行搅拌混合,之后干燥,得到掺杂炭化粉,将掺杂炭化粉加入至真空管式炉中保温处理,随炉冷却到室温,得到该基于高温烧结改性的生物质基硬碳材料,解决了现有的生物质基硬碳材料的电化学性能不佳,有待进一步提高的问题。
6.本发明的目的可以通过以下技术方案实现:
7.一种基于高温烧结改性的生物质基硬碳材料生产工艺,包括以下步骤
8.步骤一:将松果加入至去离子水中,在超声频率为55-65khz的条件下超声清洗20-30min,之后放置于真空干燥箱中,在温度为70-80℃的条件下干燥10-15h,之后取出粉碎,过200-300目筛,得到松果粉;
9.步骤二:将松果粉加入至真空管式炉中,通入氮气保护,之后在温度为500-550℃的条件下保温处理2-3h,随炉冷却到室温,得到炭化粉;
10.步骤三:将炭化粉、氢氧化钾溶液加入至安装有搅拌器、温度计的三口烧瓶中,在温度为70-75℃,搅拌速率为450-550r/min的条件下搅拌3-4h,之后真空抽滤,将滤饼放置于盐酸溶液中,在温度为60-65℃,超声频率为55-65khz的条件下超声处理1-2h,之后真空抽滤,将滤饼用蒸馏水洗涤3-5次,之后放置于真空干燥箱中,在温度为80-90℃的条件下干燥6-8h,得到活化炭化粉;
11.步骤四:将活化炭化粉、掺杂剂以及去离子水加入至安装有搅拌器、温度计以及回
流冷凝管的三口烧瓶中,在搅拌速率为450-550r/min的条件下升温至回流,之后继续搅拌8-10h,反应结束后将反应产物真空抽滤,将滤饼放置于真空干燥箱中,在温度为65-70℃的条件下干燥3-4h,得到掺杂炭化粉;
12.步骤五:将掺杂炭化粉加入至真空管式炉中,通入氮气保护,之后在温度为800-1600℃的条件下保温处理2-3h,随炉冷却到室温,得到该基于高温烧结改性的生物质基硬碳材料。
13.作为本发明进一步的方案:步骤三中的所述炭化粉、氢氧化钾溶液以及盐酸溶液的用量比为10g:40-50ml:40-50ml,所述氢氧化钾溶液的质量分数为20-30%,所述盐酸溶液的质量分数为36-38%。
14.作为本发明进一步的方案:步骤四中的活化炭化粉、掺杂剂以及去离子水的用量比为10g:1-10g:80-100ml。
15.作为本发明进一步的方案:所述掺杂剂由以下步骤制备得到:
16.a1:将季戊四醇、1,4-二氧六环加入至安装有搅拌器、温度计、导气管以及恒压滴液漏斗的三口烧瓶中,通入氮气保护,在温度为20-25℃,搅拌速率为450-550r/min的条件下搅拌反应30-40min,之后升温至80-85℃的条件下边搅拌边逐滴加入三氯氧磷,控制滴加速率为1-2滴/s,之后升温至100-105℃的条件下继续搅拌反应6-7h,反应结束后将反应产物冷却至室温,之后真空抽滤,将滤饼用正己烷洗涤2-3次,之后放置于真空干燥箱中,在温度为70-80℃的条件下干燥8-10h,得到中间体1;
17.反应原理如下:
[0018][0019]
a2:将中间体1、无水乙腈加入至安装有搅拌器、温度计、导气管以及恒压滴液漏斗的三口烧瓶中,通入氮气保护,在温度为20-25℃,搅拌速率为450-550r/min的条件下搅拌反应5-10min,之后升温至35-40℃的条件下边搅拌边逐滴加入氯乙酰氯,控制滴加速率为1-2滴/s,之后升温至60-65℃的条件下继续搅拌反应10-15h,反应结束后将反应产物冷却至室温,之后旋转蒸发去除溶剂,之后用蒸馏水洗涤2-3次,之后放置于真空干燥箱中,在温度为70-80℃的条件下干燥10-15h,得到中间体2;
[0020]
反应原理如下:
[0021]
[0022]
a3:将2-羟基-5-氯苯乙酮、2-氨甲基吡啶以及碘加入至安装有搅拌器、温度计以及恒压滴液漏斗的三口烧瓶中,在温度为110-115℃,搅拌速率为450-550r/min的条件下搅拌反应4-5h,之后降温至65-70℃的条件下继续搅拌反应10-15h,之后加入氢氧化钠溶液继续搅拌反应1-1.5h,之后加入二氯甲烷继续搅拌反应10-15min,之后用盐酸溶液调节ph为4-5,之后静置分层,将有机相用无水硫酸钠干燥,之后真空抽滤,将滤液旋转蒸发去除溶剂,得到中间体3;
[0023]
反应原理如下:
[0024][0025]
a4:将甲萘胺和邻二氯苯加入至安装有搅拌器、温度计以及恒压滴液漏斗的三口烧瓶中,在温度为25-30℃,搅拌速率为450-550r/min的条件下搅拌反应20-30min,之后边逐滴加入浓硫酸,控制滴加速率为1-2滴/s,滴加完毕后升温至回流继续搅拌反应6-7h,之后降温至125-130℃的条件下加入碳酸钠调节ph为8-9,之后降温至90-95℃的条件下静置分层,将水相旋转蒸发,之后冷却至5-10℃,析出晶体,之后真空抽滤,将滤饼放置于真空干燥箱中,在温度为70-80℃的条件下干燥4-5h,得到中间体4;
[0026]
反应原理如下:
[0027][0028]
a5:将中间体3、中间体4、氢氧化钠、苄基三乙基氯化铵以及二氯甲烷加入至安装有搅拌器、温度计、导气管以及恒压滴液漏斗的三口烧瓶中,通入氮气保护,在温度为80-85℃,搅拌速率为450-550r/min的条件下搅拌反应20-30h,反应结束后将反应产物趁热真空抽滤,将滤饼用无水乙醇洗涤2-3次,之后放置于真空干燥箱中,在温度为65-70℃的条件下干燥6-8h,得到中间体5;
[0029]
反应原理如下:
[0030][0031]
a6:将中间体2、中间体5以及无水乙腈加入至安装有搅拌器、温度计以及导气管的三口烧瓶中,通入氮气保护,在温度为35-40℃,搅拌速率为450-550r/min的条件下搅拌反应20-30min,之后升温至75-80℃的条件下继续搅拌反应10-15h,反应结束后将反应产物冷却至室温,之后真空抽滤,将滤饼用正己烷洗涤2-3次,之后放置于真空干燥箱中,在温度为70-80℃的条件下干燥10-15h,得到掺杂剂。
[0032]
反应原理如下:
[0033][0034]
作为本发明进一步的方案:步骤a1中的所述季戊四醇、1,4-二氧六环以及三氯氧磷的用量比0.1mol:50-60ml:0.1mol。
[0035]
作为本发明进一步的方案:步骤a2中的所述中间体1、无水乙腈以及氯乙酰氯的用量比为0.1mol:70-80ml:0.2-0.25mol。
[0036]
作为本发明进一步的方案:步骤a3中的所述2-羟基-5-氯苯乙酮、2-氨甲基吡啶、碘、氢氧化钠溶液以及二氯甲烷的用量比为0.1mol:0.2-0.25mol:0.11-0.13mol:30-40ml:80-100ml,所述氢氧化钠溶液的质量分数为40-45%,所述盐酸溶液的质量分数为15-20%。
[0037]
作为本发明进一步的方案:步骤a4中的甲萘胺、邻二氯苯以及浓硫酸的用量比为0.1mol:50-60ml:6-9ml,所述浓硫酸的质量分数为95-98%。
[0038]
作为本发明进一步的方案:步骤a5中的所述中间体3、中间体4、氢氧化钠、苄基三乙基氯化铵以及二氯甲烷的用量比为0.1mol:0.11-0.13mol:4.5-5.0g:0.2-0.5g:80-100ml。
[0039]
作为本发明进一步的方案:步骤a6中的所述中间体2、中间体5以及无水乙腈的用量比为0.1mol:0.1mol:80-100ml。
[0040]
本发明的有益效果:
[0041]
本发明的一种基于高温烧结改性的生物质基硬碳材料生产工艺,通过将松果加入至去离子水中超声清洗,之后干燥、粉碎、过筛,得到松果粉,将松果粉加入至真空管式炉中保温处理,随炉冷却到室温,得到炭化粉,将炭化粉加入至氢氧化钾溶液处理,之后加入至盐酸溶液中进行处理,之后洗涤、干燥,得到活化炭化粉,将活化炭化粉、掺杂剂以及去离子水进行搅拌混合,之后干燥,得到掺杂炭化粉,将掺杂炭化粉加入至真空管式炉中保温处
理,随炉冷却到室温,得到该基于高温烧结改性的生物质基硬碳材料;该生产工艺中利用生物质材料松果作为原料,原料丰富、制备工艺简单、价格低廉、又能解决焚烧生物质带来的大气污染问题,将松果粉炭化形成炭化粉,经过氢氧化钾活化可以使炭化粉出现很多孔隙结构,而且还能在炭化粉表面引入官能团,盐酸酸洗后主要是有利于去除经碳化后炭化粉中未除尽的杂质,进一步的增加孔隙,得到活化炭化粉,之后将活化炭化粉、掺杂剂以及去离子水进行搅拌混合,掺杂剂储存在活化炭化粉表面以及其内部孔隙中,从而向活化炭化粉中引入大量的硫、磷、氮以及氧元素,从而提升了基于高温烧结改性的生物质基硬碳材料的电子电导率,增加材料的储钠活性位点,有效提高基于高温烧结改性的生物质基硬碳材料的储钠性能。
[0042]
在制备基于高温烧结改性的生物质基硬碳材料的过程中首先制备了一种掺杂剂,首先利用季戊四醇上的羟基与三氯氧磷上的氯原子发生亲核取代反应,得到中间体1,之后中间体1上的羟基与氯乙酰氯上的氯原子发生亲核取代反应,同时引入氯原子,得到中间体2,利用2-羟基-5-氯苯乙酮、2-氨甲基吡啶反应生成含有羟基和氯原子的中间体3,之后利用甲萘胺和浓硫酸进行反应,经过磺化后引入磺酸基,之后与磺酸基与碳酸钠反应形成磺酸钠,得到中间体4,之后中间体3上的氯原子与中间体4上的氨基发生亲核取代反应,得到中间体5,之后中间体2上的氯原子与中间体5上的羟基发生亲核取代反应,得到掺杂剂;该掺杂剂的分子结构上含有大量的杂环以及苯环,含碳量高,易于炭化,而且掺杂剂的分子结构上含有大量的氮元素、氧元素,还有磷元素和硫元素,将其掺杂于活化炭化粉中后向其中引入大量引入杂元素,不仅可以调节层间距,还可以增加活性位点,提高基于高温烧结改性的生物质基硬碳材料的电导率和反应活性,从而提升其储钠性能。
具体实施方式
[0043]
下面将结合本发明实施例,对本发明实施例中的技术方案进行清楚、完整地描述,显然,所描述的实施例仅仅是本发明一部分实施例,而不是全部的实施例。基于本发明中的实施例,本领域普通技术人员在没有作出创造性劳动前提下所获得的所有其它实施例,都属于本发明保护的范围。
[0044]
实施例1:
[0045]
本实施例为一种掺杂剂的制备方法,包括以下步骤:
[0046]
a1:将0.1mol季戊四醇、50ml1,4-二氧六环加入至安装有搅拌器、温度计、导气管以及恒压滴液漏斗的三口烧瓶中,通入氮气保护,在温度为20℃,搅拌速率为450r/min的条件下搅拌反应30min,之后升温至80℃的条件下边搅拌边逐滴加入0.1mol三氯氧磷,控制滴加速率为1滴/s,之后升温至100℃的条件下继续搅拌反应6h,反应结束后将反应产物冷却至室温,之后真空抽滤,将滤饼用正己烷洗涤2次,之后放置于真空干燥箱中,在温度为70℃的条件下干燥8h,得到中间体1;
[0047]
a2:将0.1mol中间体1、70ml无水乙腈加入至安装有搅拌器、温度计、导气管以及恒压滴液漏斗的三口烧瓶中,通入氮气保护,在温度为20℃,搅拌速率为450r/min的条件下搅拌反应5min,之后升温至35℃的条件下边搅拌边逐滴加入0.2mol氯乙酰氯,控制滴加速率为1滴/s,之后升温至60℃的条件下继续搅拌反应10h,反应结束后将反应产物冷却至室温,之后旋转蒸发去除溶剂,之后用蒸馏水洗涤2次,之后放置于真空干燥箱中,在温度为70℃
的条件下干燥10h,得到中间体2;
[0048]
a3:将0.1mol2-羟基-5-氯苯乙酮、0.2mol2-氨甲基吡啶以及0.11mol碘加入至安装有搅拌器、温度计以及恒压滴液漏斗的三口烧瓶中,在温度为110℃,搅拌速率为450r/min的条件下搅拌反应4h,之后降温至65℃的条件下继续搅拌反应10h,之后加入30ml质量分数为40%的氢氧化钠溶液继续搅拌反应1h,之后加入80ml二氯甲烷继续搅拌反应10min,之后用质量分数为15%的盐酸溶液调节ph为4,之后静置分层,将有机相用无水硫酸钠干燥,之后真空抽滤,将滤液旋转蒸发去除溶剂,得到中间体3;
[0049]
a4:将0.1mol甲萘胺和50ml邻二氯苯加入至安装有搅拌器、温度计以及恒压滴液漏斗的三口烧瓶中,在温度为25℃,搅拌速率为450r/min的条件下搅拌反应20min,之后边逐滴加入6ml质量分数为95%的浓硫酸,控制滴加速率为1滴/s,滴加完毕后升温至回流继续搅拌反应6h,之后降温至125℃的条件下加入碳酸钠调节ph为8,之后降温至90℃的条件下静置分层,将水相旋转蒸发,之后冷却至5℃,析出晶体,之后真空抽滤,将滤饼放置于真空干燥箱中,在温度为70℃的条件下干燥4h,得到中间体4;
[0050]
a5:将0.1mol中间体3、0.11mol中间体4、4.5g氢氧化钠、0.2g苄基三乙基氯化铵以及80ml二氯甲烷加入至安装有搅拌器、温度计、导气管以及恒压滴液漏斗的三口烧瓶中,通入氮气保护,在温度为80℃,搅拌速率为450r/min的条件下搅拌反应20h,反应结束后将反应产物趁热真空抽滤,将滤饼用无水乙醇洗涤2次,之后放置于真空干燥箱中,在温度为65℃的条件下干燥6h,得到中间体5;
[0051]
a6:将0.1mol中间体2、0.1mol中间体5以及80ml无水乙腈加入至安装有搅拌器、温度计以及导气管的三口烧瓶中,通入氮气保护,在温度为35℃,搅拌速率为450r/min的条件下搅拌反应20min,之后升温至75℃的条件下继续搅拌反应10h,反应结束后将反应产物冷却至室温,之后真空抽滤,将滤饼用正己烷洗涤2次,之后放置于真空干燥箱中,在温度为70℃的条件下干燥10h,得到掺杂剂。
[0052]
实施例2:
[0053]
本实施例为一种掺杂剂的制备方法,包括以下步骤:
[0054]
a1:将0.1mol季戊四醇、60ml1,4-二氧六环加入至安装有搅拌器、温度计、导气管以及恒压滴液漏斗的三口烧瓶中,通入氮气保护,在温度为25℃,搅拌速率为550r/min的条件下搅拌反应40min,之后升温至85℃的条件下边搅拌边逐滴加入0.1mol三氯氧磷,控制滴加速率为2滴/s,之后升温至105℃的条件下继续搅拌反应7h,反应结束后将反应产物冷却至室温,之后真空抽滤,将滤饼用正己烷洗涤3次,之后放置于真空干燥箱中,在温度为80℃的条件下干燥10h,得到中间体1;
[0055]
a2:将0.1mol中间体1、80ml无水乙腈加入至安装有搅拌器、温度计、导气管以及恒压滴液漏斗的三口烧瓶中,通入氮气保护,在温度为25℃,搅拌速率为550r/min的条件下搅拌反应10min,之后升温至40℃的条件下边搅拌边逐滴加入0.25mol氯乙酰氯,控制滴加速率为2滴/s,之后升温至65℃的条件下继续搅拌反应15h,反应结束后将反应产物冷却至室温,之后旋转蒸发去除溶剂,之后用蒸馏水洗涤3次,之后放置于真空干燥箱中,在温度为80℃的条件下干燥15h,得到中间体2;
[0056]
a3:将0.1mol2-羟基-5-氯苯乙酮、0.25mol2-氨甲基吡啶以及0.13mol碘加入至安装有搅拌器、温度计以及恒压滴液漏斗的三口烧瓶中,在温度为115℃,搅拌速率为550r/
min的条件下搅拌反应5h,之后降温至70℃的条件下继续搅拌反应15h,之后加入40ml质量分数为45%的氢氧化钠溶液继续搅拌反应1.5h,之后加入100ml二氯甲烷继续搅拌反应15min,之后用质量分数为20%的盐酸溶液调节ph为5,之后静置分层,将有机相用无水硫酸钠干燥,之后真空抽滤,将滤液旋转蒸发去除溶剂,得到中间体3;
[0057]
a4:将0.1mol甲萘胺和60ml邻二氯苯加入至安装有搅拌器、温度计以及恒压滴液漏斗的三口烧瓶中,在温度为30℃,搅拌速率为550r/min的条件下搅拌反应30min,之后边逐滴加入9ml质量分数为98%的浓硫酸,控制滴加速率为2滴/s,滴加完毕后升温至回流继续搅拌反应7h,之后降温至130℃的条件下加入碳酸钠调节ph为9,之后降温至95℃的条件下静置分层,将水相旋转蒸发,之后冷却至10℃,析出晶体,之后真空抽滤,将滤饼放置于真空干燥箱中,在温度为80℃的条件下干燥5h,得到中间体4;
[0058]
a5:将0.1mol中间体3、0.13mol中间体4、5.0g氢氧化钠、0.5g苄基三乙基氯化铵以及100ml二氯甲烷加入至安装有搅拌器、温度计、导气管以及恒压滴液漏斗的三口烧瓶中,通入氮气保护,在温度为85℃,搅拌速率为550r/min的条件下搅拌反应30h,反应结束后将反应产物趁热真空抽滤,将滤饼用无水乙醇洗涤3次,之后放置于真空干燥箱中,在温度为70℃的条件下干燥8h,得到中间体5;
[0059]
a6:将0.1mol中间体2、0.1mol中间体5以及100ml无水乙腈加入至安装有搅拌器、温度计以及导气管的三口烧瓶中,通入氮气保护,在温度为40℃,搅拌速率为550r/min的条件下搅拌反应30min,之后升温至80℃的条件下继续搅拌反应15h,反应结束后将反应产物冷却至室温,之后真空抽滤,将滤饼用正己烷洗涤3次,之后放置于真空干燥箱中,在温度为80℃的条件下干燥15h,得到掺杂剂。
[0060]
实施例3:
[0061]
本实施例为一种基于高温烧结改性的生物质基硬碳材料生产工艺,包括以下步骤
[0062]
步骤一:将松果加入至去离子水中,在超声频率为55khz的条件下超声清洗20min,之后放置于真空干燥箱中,在温度为70℃的条件下干燥10h,之后取出粉碎,过200目筛,得到松果粉;
[0063]
步骤二:将松果粉加入至真空管式炉中,通入氮气保护,之后在温度为500℃的条件下保温处理2h,随炉冷却到室温,得到炭化粉;
[0064]
步骤三:将10g炭化粉、40ml质量分数为20%的氢氧化钾溶液加入至安装有搅拌器、温度计的三口烧瓶中,在温度为70℃,搅拌速率为450r/min的条件下搅拌3h,之后真空抽滤,将滤饼放置于40ml质量分数为36%的盐酸溶液中,在温度为60℃,超声频率为55khz的条件下超声处理1h,之后真空抽滤,将滤饼用蒸馏水洗涤3次,之后放置于真空干燥箱中,在温度为80℃的条件下干燥6h,得到活化炭化粉;
[0065]
步骤四:将10g活化炭化粉、1g来自于实施例1中的掺杂剂以及80ml去离子水加入至安装有搅拌器、温度计以及回流冷凝管的三口烧瓶中,在搅拌速率为450r/min的条件下升温至回流,之后继续搅拌8h,反应结束后将反应产物真空抽滤,将滤饼放置于真空干燥箱中,在温度为65℃的条件下干燥3h,得到掺杂炭化粉;
[0066]
步骤五:将掺杂炭化粉加入至真空管式炉中,通入氮气保护,之后在温度为800℃的条件下保温处理2h,随炉冷却到室温,得到该基于高温烧结改性的生物质基硬碳材料。
[0067]
实施例4:
[0068]
本实施例为一种基于高温烧结改性的生物质基硬碳材料生产工艺,包括以下步骤
[0069]
步骤一:将松果加入至去离子水中,在超声频率为65khz的条件下超声清洗30min,之后放置于真空干燥箱中,在温度为80℃的条件下干燥15h,之后取出粉碎,过300目筛,得到松果粉;
[0070]
步骤二:将松果粉加入至真空管式炉中,通入氮气保护,之后在温度为550℃的条件下保温处理3h,随炉冷却到室温,得到炭化粉;
[0071]
步骤三:将10g炭化粉、50ml质量分数为30%的氢氧化钾溶液加入至安装有搅拌器、温度计的三口烧瓶中,在温度为75℃,搅拌速率为550r/min的条件下搅拌4h,之后真空抽滤,将滤饼放置于50ml质量分数为38%的盐酸溶液中,在温度为65℃,超声频率为65khz的条件下超声处理2h,之后真空抽滤,将滤饼用蒸馏水洗涤5次,之后放置于真空干燥箱中,在温度为90℃的条件下干燥8h,得到活化炭化粉;
[0072]
步骤四:将10g活化炭化粉、10g来自于实施例2中的掺杂剂以及100ml去离子水加入至安装有搅拌器、温度计以及回流冷凝管的三口烧瓶中,在搅拌速率为550r/min的条件下升温至回流,之后继续搅拌10h,反应结束后将反应产物真空抽滤,将滤饼放置于真空干燥箱中,在温度为70℃的条件下干燥4h,得到掺杂炭化粉;
[0073]
步骤五:将掺杂炭化粉加入至真空管式炉中,通入氮气保护,之后在温度为1600℃的条件下保温处理3h,随炉冷却到室温,得到该基于高温烧结改性的生物质基硬碳材料。
[0074]
对比例1:
[0075]
对比例1与实施例4的不同之处在于,不添加掺杂剂。
[0076]
对比例2:
[0077]
对比例2与实施例4的不同之处在于,使用尿素代替掺杂剂。
[0078]
对比例3:
[0079]
对比例3与实施例4的不同之处在于,步骤五:将掺杂炭化粉加入至真空管式炉中,通入氮气保护,之后在温度为1000℃的条件下保温处理3h,随炉冷却到室温,得到该基于高温烧结改性的生物质基硬碳材料。
[0080]
对比例4:
[0081]
对比例4与实施例4的不同之处在于,步骤五:将掺杂炭化粉加入至真空管式炉中,通入氮气保护,之后在温度为1200℃的条件下保温处理3h,随炉冷却到室温,得到该基于高温烧结改性的生物质基硬碳材料。
[0082]
对比例5:
[0083]
对比例5与实施例4的不同之处在于,步骤五:将掺杂炭化粉加入至真空管式炉中,通入氮气保护,之后在温度为1400℃的条件下保温处理3h,随炉冷却到室温,得到该基于高温烧结改性的生物质基硬碳材料。
[0084]
将实施例3-4以及对比例1-5基于高温烧结改性的生物质基硬碳材料的性能进行检测,检测条件下为电流密度0.1c(30ma/g),电压范围0.001-2v,检测结果如下表所示:
[0085]
样品可逆比容量,mah/g120次循环后容量保持率,%实施例321893.5实施例435494.2对比例112185.1
对比例216988.9对比例330292.5对比例432993.4对比例536594.7
[0086]
参阅上表数据,根据实施例4与对比例1-2比较,可以得知添加尿素、掺杂剂进行掺杂能够提升基于高温烧结改性的生物质基硬碳材料的性能,且掺杂剂具有更佳的提升效果,可逆比容量能够保持200mah/g以上,且120次循环后充电比容量保持率能够保持在93%以上,根据实施例4与对比例3-5比较,可以得知高温烧结温度对基于高温烧结改性的生物质基硬碳材料的性能有所影响,而其中高温烧结温度为1400℃表现出最佳的效果。
[0087]
在本说明书的描述中,参考术语“一个实施例”、“示例”、“具体示例”等的描述意指结合该实施例或示例描述的具体特征、结构、材料或者特点包含于本发明的至少一个实施例或示例中。在本说明书中,对上述术语的示意性表述不一定指的是相同的实施例或示例。而且,描述的具体特征、结构、材料或者特点可以在任何的一个或多个实施例或示例中以合适的方式结合。
[0088]
以上内容仅仅是对本发明所作的举例和说明,所属本技术领域的技术人员对所描述的具体实施例做各种各样的修改或补充或采用类似的方式替代,只要不偏离发明或者超越本权利要求书所定义的范围,均应属于本发明的保护范围。