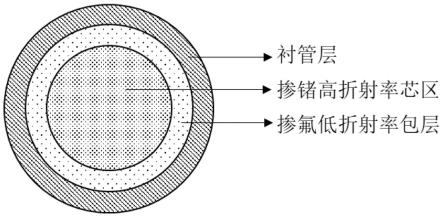
1.本发明专利属于光纤制造技术领域,涉及一种大数值孔径预制棒的制备方法。
背景技术:2.光纤传像束是一种可任意弯曲的传输图像的无源器件,它与传统的光学成像器件相比,具有重量轻、使用自由度大、易实现复杂空间结构图像传递等优势。由于其优良的传像特性、可任意弯曲的特殊性能以及体积小的特征,使其被普遍地应用于医学、工业及科研、航天、军事等多种领域。光纤内窥镜在医学领域的应用,是光纤传像束目前在各行各业中应用的最普遍也是最成功的,以光纤传像束为关键核心部件制成的医用内窥镜在医疗上的成功应用也带来了医疗手段的革命。
3.目前研制的产品普遍存在单元丝径无法做小,导致分辨率低,单元丝直径小于50μm,排列难度大,容易产生畸变、错位等结构缺陷问题。此外,受制于传像束用大数值孔径光纤预制棒及光纤增强技术的限制,研制的光纤传像束的抗弯性能较差,弯曲半径仅能达到40mm左右。
技术实现要素:4.本发明专利所要解决的技术问题是提供一种大数值孔径预制棒的制备方法,采用石墨电阻炉加热型化学气相沉积法fcvd,首先在衬管内沉积掺氟的低折射率包层,然后再接着沉积掺锗的高折射率芯层,沉积完成后对衬管进行高温熔缩和烧实,最后对实心棒进行机械打磨和火焰抛光,最终得到满足要求的大数值孔径光纤预制棒,其材料的性质更稳定,不易析晶,材料的强度更大,集成度更高,操作步骤更少,数值孔径、芯包比、棒径等关键参数可以根据需求自由设计调节。
5.为解决上述技术问题,本发明专利所采用的技术方案是:一种大数值孔径预制棒的制备方法,它包括如下步骤:步骤1,预热及刻蚀,采用fcvd设备及工艺,高纯石英管作为沉积衬管,对衬管的内壁进行刻蚀;步骤2,掺氟低射率包层的制备,向衬管中通入四氯化硅、氧气、六氟化硫和氦气的混合气体,制备掺氟低折射率石英包层;步骤3,掺锗高射率芯区的制备,向衬管中通入四氯化硅、四氯化锗、三氯氧磷、氧气和氦气的混合气体,制备掺锗高折射率石英芯层;步骤4,熔缩烧实,通过设备的压力控制系统保持管内压力,对沉积完的衬管进行熔缩和烧实;步骤5,机械打磨,将熔缩、烧实制备的预制棒通过专用夹具固定在外圆磨床上进行粗磨,再对预制棒进行精磨;步骤6,清洗干燥,对精磨过的预制棒先后进行碱性清洗剂、氢氟酸和硝酸的混合酸及纯水的清洗,并使用高纯氮气吹扫干燥;
步骤7,火焰抛光,采用氢氧焰对高纯氮气吹扫干燥后的预制棒进行多次的火焰抛光,直至预制棒外表面透亮无瑕疵;该预制棒即为所制备的大数值孔径光纤预制棒。该预制棒的数值孔径在0.25以上,预制棒的芯区和包层直径比在1:1.1到1比2之间。
6.在步骤1中,先对沉积衬管进行预热及升温,待温度达到1600℃,向沉积衬管内通入六氟化硫和氧气,对衬管的内壁进行多次刻蚀,达到完全消除存在于衬管内壁上的缺陷和杂质。
7.在步骤2中,同时向衬管中通入四氯化硅、氧气、六氟化硫和氦气的混合气体,其中四氯化硅料源是装于鼓泡瓶中采用氧气鼓泡的形式被携带进入衬管中的,以上四氯化硅的流量在50-400sccm之间,以上六氟化硫的流量在20-200sccm之间,以上四氯化硅和六氟化硫的流量比小于2:1;以上混合气体被石墨电阻炉加热后发生氧化还原反应,制备以二氧化硅为主要产物的含氟的石英包层,通过石墨电阻炉的往复移动沉积不同厚度的掺氟低折射率石英包层材料。
8.在步骤3中,同时向衬管中通入四氯化硅、四氯化锗、三氯氧磷、氧气和氦气的混合气体,其中四氯化锗料源同四氯化硅,也是装于鼓泡瓶中采用氧气鼓泡的形式被携带进入衬管中的,以上四氯化锗的流量在50-500sccm之间,以上四氯化硅的流量在25-250sccm之间,以上四氯化硅和四氯化锗的流量比在2:1到1:2之间;以上混合气体被石墨电阻炉加热后发生氧化还原反应,生成二氧化硅、二氧化锗相混合的高折射率芯层材料;通过石墨电阻炉的往复移动沉积不同厚度的掺锗高折射率石英芯层材料。
9.在步骤4中,管内压力为-50pa~+50pa之间,温度1790
°
~1810℃。
10.在步骤5中,粗磨时,粗磨砂轮目数为200-500目,打磨掉预制棒最外部的高纯石英衬管层材质,再对预制棒外表面进行精磨,精磨砂轮目数1000目以上。
11.本发明专利的主要有益效果主要体现于:采用化学气相沉积法制备的石英基预制棒,相比其它金属氧化物玻璃体系材料,其材料的性质更稳定,不易析晶,材料的强度更大。
12.石英基预制棒材料的纯度更高、光传输损耗小、导光能力强。
13.采用fcvd制备的该大数值孔径预制棒包层沉积、芯层沉积、熔缩和烧实在同一台设备上一次完成,集成度更高,操作步骤更少。
14.该石英预制棒的数值孔径、芯包比、棒径等关键参数可以根据需求自由设计调节。
附图说明
15.下面结合附图和实施例对本发明专利作进一步说明。
16.图1为本发明熔缩烧实制得的预制棒的结构示意图。
17.图2为本发明机械打磨后制得的预制棒的结构示意图。
18.图3为本发明打磨前预制棒的折射率剖面。
具体实施方式
19.如图1~图3中,一种大数值孔径预制棒的制备方法,它包括如下步骤:步骤1,预热及刻蚀,采用fcvd设备及工艺,高纯石英管作为沉积衬管,对衬管的内壁进行刻蚀;
步骤2,掺氟低射率包层的制备,向衬管中通入四氯化硅、氧气、六氟化硫和氦气的混合气体,制备掺氟低折射率石英包层;步骤3,掺锗高射率芯区的制备,向衬管中通入四氯化硅、四氯化锗、三氯氧磷、氧气和氦气的混合气体,制备掺锗高折射率石英芯层;步骤4,熔缩烧实,通过设备的压力控制系统保持管内压力,对沉积完的衬管进行熔缩和烧实;熔缩烧实制得的预制棒如图1。
20.步骤5,机械打磨,将熔缩、烧实制备的预制棒通过专用夹具固定在外圆磨床上进行粗磨,再对预制棒进行精磨;步骤6,清洗干燥,对精磨过的预制棒先后进行碱性清洗剂、氢氟酸和硝酸的混合酸及纯水的清洗,并使用高纯氮气吹扫干燥;步骤7,火焰抛光,采用氢氧焰对高纯氮气吹扫干燥后的预制棒进行多次的火焰抛光,直至预制棒外表面透亮无瑕疵;该预制棒即为所制备的大数值孔径光纤预制棒。该预制棒的数值孔径在0.25以上,预制棒的芯区和包层直径比在1:1.1到1比2之间。
21.优选的方案中,在步骤1中,先对沉积衬管进行预热及升温,待温度达到1600℃,向沉积衬管内通入六氟化硫和氧气,对衬管的内壁进行多次刻蚀,达到完全消除存在于衬管内壁上的缺陷和杂质。
22.优选的方案中,在步骤2中,同时向衬管中通入四氯化硅、氧气、六氟化硫和氦气的混合气体,其中四氯化硅料源是装于鼓泡瓶中采用氧气鼓泡的形式被携带进入衬管中的,以上四氯化硅的流量在50-400sccm之间,以上六氟化硫的流量在20-200sccm之间,以上四氯化硅和六氟化硫的流量比小于2:1;以上混合气体被石墨电阻炉加热后发生氧化还原反应,制备以二氧化硅为主要产物的含氟的石英包层,通过石墨电阻炉的往复移动沉积不同厚度的掺氟低折射率石英包层材料。
23.优选的方案中,在步骤3中,同时向衬管中通入四氯化硅、四氯化锗、三氯氧磷、氧气和氦气的混合气体,其中四氯化锗料源同四氯化硅,也是装于鼓泡瓶中采用氧气鼓泡的形式被携带进入衬管中的,以上四氯化锗的流量在50-500sccm之间,以上四氯化硅的流量在25-250sccm之间,以上四氯化硅和四氯化锗的流量比在2:1到1:2之间;以上混合气体被石墨电阻炉加热后发生氧化还原反应,生成二氧化硅、二氧化锗相混合的高折射率芯层材料;通过石墨电阻炉的往复移动沉积不同厚度的掺锗高折射率石英芯层材料。
24.优选的方案中,在步骤4中,管内压力为-50pa~+50pa之间,温度1790
°
~1810℃。
25.优选的方案中,在步骤5中,粗磨时,粗磨砂轮目数为200-500目,打磨掉预制棒最外部的高纯石英衬管层材质,再对预制棒外表面进行精磨,精磨砂轮目数1000目以上。机械打磨后制得的预制棒如图2。
26.上述预制棒为圆柱体结构,其端面结构包含两部分,中间圆形区域主要为掺锗的二氧化硅高折射率材料区称为芯区,外部圆环形区域主要为掺氟的二氧化硅低折射率材料区称为包层,以上预制棒的数值孔径在0.25以上,预制棒的数值孔径等于(n
2芯区-n
2包层
)
1/2
,其中n
芯区
是芯区材料的折射率,n
包层
是包层材料的折射率,以上预制棒的芯区和包层直径比在1:1.1到1比2之间。
27.以上光纤预制棒在被拉制成外径均匀的石英细丝后,将成千上万根这种石英细丝整齐排列再次拉制即可拉制成光纤束产品。
28.实施例:1、预热及刻蚀,采用fcvd设备及工艺,使用外径31mm,壁厚3mm的高纯石英管作为沉积衬管,先对沉积衬管进行预热及升温,待温度达到了1600℃,向沉积衬管内通入50sccm六氟化硫和1000sccm氧气,对衬管的内壁进行3次刻蚀。
29.2、掺氟低射率包层的制备,同时向衬管中通入180sccm的四氯化硅、1200sccm的氧气、120sccm的六氟化硫和500sccm氦气的混合气体,以上混合气体被石墨电阻炉加热后发生氧化还原反应,生成以二氧化硅为主要产物的含氟的石英包层材料,通过石墨电阻炉的往复移动沉积53层。
30.3、掺锗高折射率芯区的制备,同时向衬管中通入250sccm的四氯化硅、1200sccm的氧气、200sccm的四氯化锗和500sccm氦气的混合气体。以上混合气体被石墨电阻炉加热后发生氧化还原反应,生成二氧化硅、二氧化锗相混合的高折射率玻璃材料。通过石墨电阻炉的往复移动沉积27层。
31.4、熔缩烧实,通过设备的压力控制系统保持管内压力处于+25pa间,温度1800℃对沉积完的衬管进行熔缩和烧实。
32.5、机械打磨,将熔缩、烧实制备的预制棒通过专用夹具固定在外圆磨床上进行粗磨,砂轮目数300,打磨掉预制棒最外部的高纯石英衬管层材质,再对预制棒外表面进行精磨砂轮目数1000的精磨。
33.6、清洗干燥,对精磨过的预制棒先后进行碱性清洗剂、氢氟酸和硝酸的混合酸及纯水的清洗,并使用高纯氮气吹扫干燥。
34.7、火焰抛光,采用氢氧焰对高纯氮气吹扫干燥后的预制棒进行5次火焰抛光,直至预制棒外表面透亮无瑕疵。
35.为了说明上述实施例制得的预制棒的效果,对熔缩烧实未机械打磨的预制棒进行了折射率剖面测试,其折射率剖面如图3,其关键参数如下表1所示。
36.表1 打磨前预制棒的关键参数由以上预制棒的制备过程和测试结果来看,利用本方法可以成功制备棒径在10mm以上,包层折射率1.4399,芯区折射率1.4775,预制棒数值孔径达到0.332的大数值孔径预制棒。需要指出的是使用该方法通过调整包层制备过程中通入的四氯化硅和六氟化硫的流量和比值,通过调整芯区制备过程中通入的四氯化硅和二氧化锗的流量和比值,通过调整包层和芯区制备过程中的沉积层数,可以制备各种包芯直径比、各种数值孔径的预制棒。
37.上述的实施例仅为本发明专利的优选技术方案,而不应视为对于本发明专利的限制,本技术中的实施例及实施例中的特征在不冲突的情况下,可以相互任意组合。本发明专利的保护范围应以权利要求记载的技术方案,包括权利要求记载的技术方案中技术特征的等同替换方案为保护范围。即在此范围内的等同替换改进,也在本发明专利的保护范围之内。