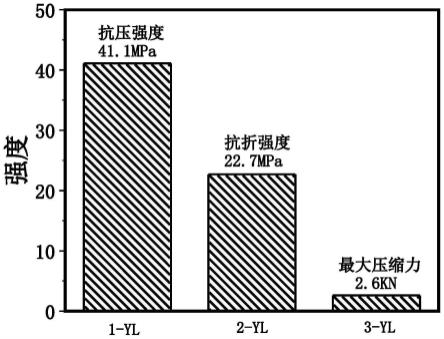
1.本发明属于建材技术领域和固废资源综合利用技术领域,具体涉及一种用于浇筑体系新型原料的制备方法及应用。
背景技术:2.钢渣是冶金工业中产生的废渣,其产生率为粗钢产量的8%~15%,2012 年全世界排钢渣量约1.8亿吨。中国的钢渣产生量随着钢铁工业的快速发展而迅速递增。因此,钢铁企业废渣的处理和资源化利用问题也越来越受到重视。
3.国家发展规划中指出,钢渣的综合利用率应达86%以上,基本实现“零排放”。然而,综合利用的现状与该规划相差甚远,尤其是素有“劣质水泥熟料”之称的转炉钢渣的利用率仅为10%~20%。国内钢铁企业产生的钢渣不能及时处理,致使大量钢渣占用土地,污染环境。然而钢渣并非不可用固体废弃物,其中含有大量的渣钢、氧化钙、铁以及氧化镁等可利用组分。所以,为使钢铁企业创造经济和环境效益,选择合适的处理工艺和利用途径来开发钢渣的再利用价值是十分必要和迫切的。
4.目前利用钢渣制备混凝土的建筑产品有很多,其中部分产品取得较好的效果,但是由于建筑装修行业性能指标越来越来高,导致对高强度的产品需求也越来越大,其中石材以其独特的优势得到广泛关注。
技术实现要素:5.本发明的目的是提供一种用于浇筑体系新型原料的制备方法及应用,通过以碳化钢渣为原料解决co2大量排放和钢渣污染问题,还解决建筑行业天然石材资源缺乏问题,制得强度高、浇筑制品。
6.为实现上述目的,本技术是通过以下技术方案实现的:
7.一种用于浇筑体系新型原料的制备方法,包括如下步骤:
8.s1、将润湿后的废料钢渣在高浓度co2加压环境中碳化处理;
9.s2、将步骤s1的碳化钢渣与炉渣、水泥、石英砂、硅灰、硫脲渣中的一种或多种混合搅拌得到混合干料;
10.s3、将减水剂与增强剂溶液混合得到混合溶液,把混合溶液和混合干料按重量比为1:10-4:10混合均匀搅拌形成浇筑浆料;
11.s4、将浇筑浆料在塑料模具中密封养护成型,最后脱模干燥,得到浇筑产品基体;
12.s5、将浇筑产品基体置于二氧化碳环境中二次碳化处理,得到高强度浇筑产品。
13.进一步的,步骤s1中的钢渣的主要矿物组成为硅酸三钙、硅酸二钙、铁酸二钙、ro或游离石灰。
14.进一步的,步骤s1中的湿润条件为湿度大于80%。
15.进一步的,步骤s1中的co2浓度为50%-100%;碳化压力为0.1mpa-0.6mpa;碳化时间为5min-30min。
16.进一步的,步骤s2中混合干料质量比为碳化钢渣:炉渣:水泥:石英砂:硅灰:硫脲渣=(50-90):(10-30):(5-10):(5-10):(2-5):(2-4)。
17.进一步的,步骤s3中的增强剂为mgso4、khco3、kcl、nahco3、nacl中的一种或多种,增强剂与水质量比为:1-30:30-100。
18.进一步的,步骤s3中的减水剂为萘系高效减水剂、脂肪族高效减水剂、氨基高效减水剂或聚羧酸高性能减水剂,减水剂与增强剂水溶液的质量比为 1:4-1:70。
19.进一步的,步骤s4中,密封养护时间为8h-72h;干燥时间为1h-72h;干燥温度为20℃-80℃。
20.进一步的,步骤s5中的二次碳化的碳化压力为常压;碳化时间为2h-48h;碳化浓度为20%-100%。
21.一种用于浇筑体系新型原料的应用,上述任一项的制备方法制备的高强度浇筑产品,至少应用于混凝土行业、石材领域、道路、建筑行业或装修行业。
22.本发明的有益效果是:
23.钢渣的利用可减少co2排放,且可替代水泥、石粉等混凝土原料,在混凝土行业、石材领域和道路等建筑装修行业广泛使用,具有很好的发展前景。
24.通过碳化钢渣制备高性能混凝土,不仅实现了钢渣的资源化利用,还吸收了大量的co2。这种石材强度高、技术简单,而且花纹丰富,解决了天然石材资源不足人造石材开裂强度低等问题,满足市场对石材的需求。
附图说明
25.图1是本发明实施例1、2、3制备的浇筑制品强度图。
具体实施方式
26.在本技术的技术方案中,所使用的试剂或材料除有特别说明外,均可以通过商业获得。
27.将工业废料钢渣在湿度大于80%、co2浓度50%-100%的加压环境中碳化处理;所述的钢渣的主要矿物组成为硅酸三钙、硅酸二钙、铁酸二钙、ro(镁、铁、锰的氧化物)、游离石灰等;碳化时间为5min-30min。
28.将碳化钢渣与炉渣、硫脲渣、石材细沙和玻璃砂混合搅拌得到混合干料;所述的混合干料质量比为碳化钢渣:炉渣:水泥:石英砂:硅灰:硫脲渣=(50-90):(10-30):(5-10):(5-10):(2-5):(2-4)。
29.将减水剂与增强剂溶液得到混合溶液,把混合溶液和混合干料混合均匀搅拌形成浇筑浆料;所述的增强剂为mgso4、khco3、kcl、nahco3、nacl中的一种或多种,增强剂与水质量比为:1-30:30-100;所述的减水剂如萘系高效减水剂、脂肪族高效减水剂、氨基高效减水剂、聚羧酸高性能减水剂等,减水剂与增强剂水溶液的质量比为1:4-1:70;所述的混合溶液的用量为原料的 10%-40%。
30.将料浆在塑料模具中密封养护成型,最后脱模干燥,得到一种浇筑产品基体;所述的密封养护时间为8h-72h;所述的干燥时间为1h-72h;干燥温度为 20℃-80℃。
31.将基体再次置于二氧化碳环境中二次碳化处理,得到高强度浇筑产品;所述的二
次碳化的碳化压力为常压;碳化时间为2h-48h;碳化浓度为50%-100%。
32.以下结合附图并通过实施例对本发明的技术方案进行详细的说明,以下的实施例仅是示例性的,仅能用来解释和说明本发明的技术方案,而不能解释为是对本发明技术方案的限制。
33.实施例1
34.本实施例提出一种浇筑体系新型原料的制备方法,由以下步骤制得:
35.将钢渣放置于湿度大于80%,co2浓度为60%的反应室中,在压力为0.3mpa 环境条件下进行10min碳化处理,得到碳化钢渣。
36.将碳化钢渣1230g、炉渣295g、普通硅酸盐水泥157g、石英粉157g、硅灰78g、硫脲渣50g搅拌混合得到混合干料。
37.将10gkcl溶于200g水中混合搅拌得到增强剂水溶液。
38.将50g聚羧酸减水剂溶于300g增强剂水溶液,得到混合液。
39.将混合液和混合干料混合,搅拌15min得到浇筑料浆。
40.将浇筑料浆倒入10cm*10cm*10cm的塑料模具中,密封条件下下养护12h 后脱模成型;在40℃下干燥24h失水率达到32%,得到浇筑石材基体。
41.将浇筑石材基体在co2环境中,常压碳化36h得到一种新型石材,并命名为1-yl;所述co2环境中co2的体积浓度为60%。
42.实施例2
43.本实施例提出一种浇筑体系新型原料的制备方法,由以下步骤制得:
44.将钢渣放置于湿度大于80%,co2浓度为60%的反应室中,在压力为0.3mpa 环境条件下进行10min碳化处理,得到碳化钢渣。
45.将碳化钢渣1230g、炉渣295g、普通硅酸盐水泥157g、石英粉157g、硅灰78g、硫脲渣50g搅拌混合得到混合干料。
46.将10gkcl溶于200g水中混合搅拌得到增强剂水溶液。
47.将50g聚羧酸减水剂溶于300g增强剂水溶液,得到混合液。
48.将混合液和混合干料混合,搅拌15min得到浇筑料浆。
49.将浇筑料浆倒入20cm*20cm*3cm的塑料模具中,密封条件下养护12h后脱模成型;在40℃下干燥24h失水率达到32%,得到浇筑板材基体。
50.将浇筑板材基体在co2环境中,常压碳化24h得到一种新型板材,并命名为2-yl;co2环境中co2的体积浓度为60%。
51.实施例3
52.本实施例提出一种浇筑体系新型原料的的制备方法,由以下步骤制得:
53.将钢渣放置于湿度大于80%,co2浓度为60%的反应室中,在压力为0.3mpa 环境条件下进行10min碳化处理,得到碳化钢渣。
54.将碳化钢渣1230g、炉渣295g、普通硅酸盐水泥157g、石英粉157g、硅灰78g、硫脲渣50g搅拌混合得到混合干料。
55.将10gkcl溶于200g水中混合搅拌得到增强剂水溶液。
56.将50g聚羧酸减水剂溶于300g增强剂水溶液,得到混合液。
57.将混合液和混合干料混合,搅拌15min得到浇筑料浆。
58.将浇筑料浆倒入直径为2cm的圆状骨料模具中,密封条件下养护12h后脱模成型;在40℃下干燥16h失水率达到32%,得到骨料基体。
59.将骨料基体在co2环境中,常压碳化24h得到一种新型骨料,并命名为 3-yl;co2环境中co2的体积浓度为60%。
60.相关检测
61.实施例1-3分别是以碳化钢渣为主要原料制备的浇筑石材、浇筑板材、浇筑骨料。由图1可知,这种碳化钢渣作为原料制得的产品都拥有较高的强度,这是因为钢渣在经过足够湿润环境下与高浓度co2进行压力碳化反应,在短时间内生成具有一定强度的碳酸钙。在浇筑实验中以这种碳化钢渣作为主原料,通过密封养护使其内部反应原料继续水化增加强度,并继续参与二次碳化反应,吸收更多的co2,除此之外碳化完全的部分可起到支撑及孔隙的作用。
62.其他有益效果:
63.1)本发明提供的新型原料解决了工业co2废气的大量排放。
64.2)本发明提供的新型原料有效的提高了废料钢渣的利用率,解决环境污染问题。
65.3)本发明提供的新型原料,其原料廉价易得,操作简单方便。
66.4)本发明提供的新型原料制得的浇筑制品强度高。
67.5)该碳化钢渣可在建筑行业应用,具有很高的应用价值和良好的发展前景。
68.以上所述本发明的具体实施方式,并不构成对本发明保护范围的限定。任何根据本发明的技术构思所做出的各种其他相应的改变与变形,均应包含在本发明权利要求的保护范围内。