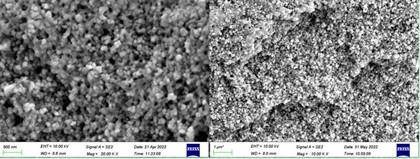
1.本发明涉及3d打印材料和方法的技术领域,特别涉及一种提高光固化打印精度及力学性能的氧化锆陶瓷浆料及其制备方法。
背景技术:2.氧化锆作为一种生物惰性陶瓷,具有较高的抗弯强度及断裂韧性,在人体内无毒、无过敏和无致癌反应,结合合理的设计可用来制造可靠、性能优异的产品。但利用模具铸造等传统陶瓷成型方法已无法满足精细结构制造和高精度成型的要求,这限制了陶瓷材料在制造复杂几何结构领域的应用,比如定制个性化的牙冠。
3.3d打印(am)是一种不同于传统制造的新兴制造技术,它结合了多个领域的科学知识,如计算机、材料加工和机械加工等。其中光固化3d打印技术是一种通过光活化聚合反应选择性固化光聚合材料的增材制造工艺。在该技术中,模型是一层一层构建的,通过扫描聚合点(立体光刻-sla)或一次性投影整个层(数字光处理
‑ꢀ
dlp)来完成。光固化技术可用来制备高清晰度及表面光滑的模型,并且不需要对表面进行机械后处理即可具有高精度,从而在增材制造领域显示出巨大的潜力。将光固化3d打印技术与陶瓷材料相结合可实现高精度、定制化、个性化的设计,舍弃了复杂的模具依赖、降低了时间与成本、解决了多种功能变化的零件制造困难问题,为陶瓷材料的精加工提供了较好的技术手段。而且光固化3d打印技术在设备设置和材料要求方面是高度通用的,所以被认为是陶瓷制造中最有前景的增材制造技术。
4.在陶瓷光固化3d打印技术中,陶瓷浆料作为主要的光固化反应材料,在铺料过程中,由于浆料流平性及润湿性不佳铺料表面往往会出现缩孔、划痕、不易铺展等问题,致使打印模型精度下降,所以制备浆料的中心环节是不仅粉体要分散均匀不絮凝,还要保证浆料高固含、低粘度、流平性好,确保铺料过程中浆料可以形成一个平整、光滑、均匀的涂膜,这需要一定粘度的光敏树脂、粉体以及其他助剂的相互配合。另外打印模型精度下降的另一原因是预混液与粉体的折射率之差相差较大,在光固化过程中产生散射,降低打印精度。此外浆料制备工艺在陶瓷浆料加工过程中也尤为重要,球磨法可使陶瓷粉体被分散,但所需时间过长且不适用于大规模生产。
技术实现要素:5.基于此,本发明的目的是针对现有技术的不足,提供一种提高光固化打印精度及力学性能的氧化锆陶瓷浆料及其制备方法。
6.为达到上述目的,本发明采用以下技术方案:一种提高光固化打印精度及力学性能的氧化锆陶瓷浆料,以氧化锆陶瓷粉体、低聚物、单体、分散剂、柔润剂、成膜剂与溶剂为主要原料制备得到;所述低聚物包含环氧丙烯酸酯类和聚氨酯丙烯酸酯类;所述单体采用多种官能度
单体复配的方式,分别包含单官能度单体、双官能度单体和多官能度单体;所述柔润剂为蔗糖硬脂酸酯、甘油硬脂酸酯中的任意一种,所述成膜剂为三甲基硅氧基硅酸酯、聚二甲基硅氧烷、聚甲基硅氧烷、聚甲基丙烯酸甲酯中的任意一种;所述溶剂为巯基乙醇;其中:所述低聚物与单体的质量比值在7/3~1/9;所述分散剂占陶瓷粉体质量的2%~7%;所述溶剂占陶瓷粉体质量的0.5%~3%;所述柔润剂占浆料总质量的0.5%~1.5%;所述成膜剂占浆料总质量的0.5%~1.5%;采用本浆料打印得到的样条素坯模型,其长度精度变化范围在0.2%~0.5%之间,宽度精度变化范围在0.8%~2%之间,高度精度变化范围在0%~0.5%之间。
7.作为本发明的进一步改进,所述单官能度单体包括丙烯酰吗啉、异癸基丙烯酸酯、丙烯酸2-羟基乙酯中的一种或多种,双官能度单体包括1,6-己二醇二丙烯酸酯、三丙二醇二丙烯酸酯、聚乙二醇二丙烯酸酯中的一种或多种,多官能度单体包括三羟甲基丙烷三丙烯酸酯、乙氧化三羟甲基丙烷三丙烯酸酯、乙氧基季戊四醇四丙烯酸酯中的一种或多种。
8.作为本发明的进一步改进,所述分散剂为具有空间位阻作用的kos110、byk-180、byk-163、byk-110中的一种或几种。
9.作为本发明的进一步改进,所述环氧丙烯酸酯类与聚氨酯丙烯酸酯类的质量比值为1/5~5/3。
10.一种提高光固化打印精度及力学性能的氧化锆陶瓷浆料的制备方法,包括以下步骤:步骤一、粉体处理:将氧化锆陶瓷粉体在真空干燥箱中烘干处理,根据粉体的粒径大小,选用不同目数的筛网进行粗细粉分离,并放置于干燥无光处备用;所使用粉体的中位粒径在100~500 nm之间,粉体筛网可选择60~200目,干燥时间在12~24h之间;步骤二、配制预混液:称取一定量的低聚物与单体于研磨器具中,搅拌均匀后加入分散剂、柔润剂、成膜剂和溶剂,通过机械搅拌器在300-360r/min条件下进行充分搅拌得到预混液;步骤三、陶瓷浆料配制:向预混液中分批加入氧化锆陶瓷粉体,通过均质机对浆料进行初步分散,然后向其中加入光引发剂tpo,之后加入所需的全部粉体,并调整均质参数;随后利用三辊研磨机对团聚颗粒进行粉碎,其后在均质机真空模式下调整均质参数对浆料进行高转速、长时间脱泡处理,以得到分散均匀的浆料;步骤四、浆料性能测试:分别利用刮板细度计及流变仪对浆料进行细度与粘度测试;步骤五、材料试验:将已层切的用于材料试验的模型文件传输至打印机中,并将浆料平铺于打印平台,设置合理的光强及时间进行单层固化并测量厚度;步骤六、打印实验:进行打印机初始化及模型传输,设置层切层厚分别为20μm或25μm,曝光参数需保证固化层厚为层切层厚的2-5倍,曝光参数可依照步骤五材料试验结果;打印后得到样条素坯并利用游标卡尺测量尺寸;步骤七、脱脂烧结:对打印素坯在不同的脱脂烧结参数下进行处理;步骤八、性能测试:对样条烧结件进行抗弯强度、维氏硬度测试,并对样条进行表面及断面扫描电镜分析。
11.作为本发明的进一步改进,所述步骤三中,当氧化锆陶瓷粉体添加量在总质量的70~80%之间时,采用多段均质参数进行浆料初步混匀,转速在800~1800r/min之间,时间选择30~120s;当达到最大固含量后采用二段均质方式,转速在1200~2500r/min之间,时间分别为30~100s;所述三辊研磨机对浆料进行分散研磨过程采用5段参数,入辊间隙在100~2μm之间,出辊间隙在70~1μm之间,每段研磨1~2次,转速在50~100r/min之间;所述真空脱泡处理转速为2500r/min,脱泡时间为120s。
12.作为本发明的进一步改进,所述步骤五中可利用螺旋测微仪记录固化厚度。
13.作为本发明的进一步改进,步骤六打印的用于后期性能测试的样条层切模型尺寸为长
ⅹ
宽
ⅹ
高=45mm
ⅹ
5mm
ⅹ
3.8mm。
14.作为本发明的进一步改进,采用本制备方案得到的样条素坯模型,其长度精度变化范围在0.2~0.5%之间,宽度精度变化范围在0.8%~2%之间,高度精度变化范围在0%~0.5%之间。
15.作为本发明的进一步改进,所述步骤七中脱脂范围在25℃至1000℃之间,升温速率在0.5℃/min-2℃/min之间;烧结范围在25℃-1480℃之间,升温速率在0.5℃/min-5℃/min之间。
16.本发明的有益效果是:1.通过本发明提供的陶瓷浆料组分结合制备方法所得的浆料,极大地提升了模型打印精度,且脱脂烧结后模型无裂纹,力学性能优异;2.通过添加具有表面活性的柔润剂,可降低浆料的表面张力,改善浆料流平性;另外,所选的部分柔润剂折射率要高于大多数低聚物及单体,添加以后可降低预混液与粉体的折射率之差,提高打印精度;3.添加成膜剂可有效防止配方中粉末凝聚,使浆料保持自由流动,铺料过程中形成连续的涂膜,避免出现针眼、缩孔等缺陷;4.添加折射率较高的溶剂,可提高预混液整体折射率,降低与粉体折射率之差,提高打印精度;5.利用均质机与三辊研磨机相结合的方式,短时间内即可达到减少颗粒团聚,降低体系粘度的目的;6.通过多种官能团单体复配的方式使光固化速率适中,打印过程在低光强、短时间内即可完成,可避免因光固化速率较大导致只有表面固化的情形,也可避免因速率较低延长打印时间造成过度曝光的问题;7.通过控制脱脂烧结速率及保温点时间使得空气气氛下烧结件无裂纹且收缩率较稳定。
附图说明
17.为了更清楚地说明本发明实施例或现有技术中的技术方案,下面将对实施例或现有技术描述中所需要使用的附图作简单地介绍,显而易见地,下面描述中的附图仅仅是本发明的一些实施例,对于本领域普通技术人员来讲,在不付出创造性劳动的前提下,还可以根据这些附图获得其他的附图。
18.附图1为 七组浆料在剪切速率32s-1时的粘度对比图;附图2为实施例2中浆料铺料效果图;附图3为对比例2中浆料铺料效果图;附图4 为实施例2(左)与对比例2(右)中烧结样条的表面微观形貌图;附图5为实施例3(左)与对比例3(右)样条素坯的断面扫描电镜图;附图6为实施例3(左)与对比例3(右)烧结样条断面扫描电镜图;附图7 为球磨工艺所配浆料在打印过程中的实际状态图;附图8为球磨工艺所配浆料打印后样条表面实际状态图;附图9 为实施例与对比例烧结后抗弯强度对比图;附图10为利用三种浆料打印、烧结后的实物图。
具体实施方式
19.下面将结合附图,对本发明实施例中的技术方案进行清楚、完整地描述。显然,所描述的实施例仅仅是本发明一部分实施例,而不是全部的实施例。基于本发明中的实施例,本领域普通技术人员在没有做出创造性劳动前提下所获得的所有其他实施例,都属于本发明保护的范围。
20.实施例1:配制质量分数为83%的陶瓷浆料,步骤如下:步骤一、粉体处理:对粒径为200 nm的氧化锆粉体在100℃真空干燥箱中干燥15h后取出,利用90目筛网进行筛分备用;步骤二、配制预混液:称取一定量的低聚物与单体于研磨器具中,手动搅拌均匀后加入分散剂kos110、柔润剂甘油硬脂酸酯、成膜剂三甲基硅氧基硅酸酯,并向其中加入巯基乙醇,在机械搅拌器350r/min条件下搅拌3h得预混液。
21.其中低聚物为ea/20%tpgda,单官能度单体选用ida,双官能度单体选用tpgda,多官能度单体选用tmp3eota。低聚物与单体的质量比为2:3, 单体比例为2:5:3,分散剂kos110添加量为粉体质量的4%,柔润剂和成膜剂分别占浆料总质量的0.7%和0.5%,溶剂巯基乙醇添加量为粉体质量的2%。
22.步骤三、配制陶瓷浆料:向预混液中分批加入氧化锆陶瓷粉体,在陶瓷粉添加量为粉体总量的80%前用均质机将其进行初步分散,设置三段均质参数,分别为800r/min,30s、1800r/min,120s、1000 r/min,60s。当质量达80%后,向浆料中加入光引发剂tpo,质量为光敏树脂的0.8%,之后加入所需的全部粉体。此时参数调整为二段均质参数,分别为1200 r/min、30s,2000 r/min、100s。然后再利用三辊研磨机对团聚颗粒进行粉碎,最后在均质机真空模式、转速2500r/min条件下对浆料脱泡处理120s,得到质量分数为83%的陶瓷浆料。
23.上述三辊研磨参数共设置5段,参数如表1:表1 三辊机研磨参数编号入辊间隙(μm)出辊间隙(μm)研磨次数转速(r/min)参数1100701100参数250201100参数31551100参数4422100
参数5212100步骤四、浆料性能测试:利用流变仪对浆料进行粘度测试,其中测试温度为25℃,浆料剪切速率为32s-1
时的粘度为53 pa.s,并利用刮板细度计测试最大团聚粒径为1.5 μm。
24.步骤五、材料试验:对浆料进行材料试验以确定打印参数,将用于材料试验的stl文件传输于打印机后,手动将浆料平铺于打印平台,分别进行5次固化后利用螺旋测微仪测量固化厚度。曝光参数分别选择20、2s,20、3s,30、2s,30、3s,40、2s,相应固化厚度分别为35μm、51μm、50μm、75μm、67μm。
25.步骤六、打印实验:将待打印模型导入软件后进行模型层切,其中样条模型尺寸为长
ⅹ
宽
ⅹ
高=45mm
ⅹ
5mm
ⅹ
3.8mm。层切参数设置首层层厚60μm,曝光能量及时间设置为40、5s,打印层厚选择25μm,打印光强及时间分别为30、3s,将层切文件传输至打印机后将浆料置于两端料槽中开始打印,打印过程中铺料平整不存在缩孔现象。打印结束后取下模型素坯并将表面多余浆料利用异丙醇清除。测量该打印参数下得到的样条的尺寸,其中长、宽、高分别为45.10mm、5.04mm、3.80mm,相应收缩率为0.2%、0.8%、0%。
26.步骤七、脱脂烧结:其中脱脂烧结环境为空气气氛,脱脂工艺为从室温以2℃/min升至250℃,保温1h,以0.5℃/min速率分别升至360℃后保温2h、450℃保温2h、700℃保温2h,后以1℃/min的升温速率升至1000℃后保温2h,而后随炉冷却至室温。
27.烧结工艺为从室温以3℃/min的升温速率升至1200℃后以0.8℃/min的速率升至1500℃,保温1.5h,后以2℃/min的速率降温至900℃后随炉冷却至室温。
28.步骤八、性能测试:烧结后样条无裂纹且不翘曲,测量烧结后样条在长、宽、高方向上的尺寸并记录,利用万能试验机对10根样条进行抗弯强度测试并计算平均值,其中加载速度设置为0.5mm/min,跨距选择30mm,最终平均抗弯强度为675mpa。利用维氏硬度仪对断裂后的10根样条进行硬度测试并计算平均值,其中加载力及加载时间设置为10kg、5s,平均维氏硬度为1420hv。
29.最后对样条进行断面及表面扫描电镜分析,发现晶粒分布均匀,无过度生长,尺寸在300-400nm之间,断裂方式为穿晶断裂,表面晶粒排列紧密。
30.实施例2:配制质量分数为80%的陶瓷浆料,步骤如下:步骤一、粉体处理:对粒径为150 nm的氧化锆粉体在100℃的真空干燥箱中处理15 h,取出后利用170目筛网进行筛分备用;步骤二、配制预混液:称取一定量的低聚物与单体于黑色研磨罐中,手动搅拌均匀后加入分散剂kos110、柔润剂蔗糖硬脂酸酯及成膜剂三甲基硅氧基硅酸酯,在机械搅拌器下以350r/min搅拌3h得预混液。
31.其中低聚物为ea,单官能度单体选用acmo,双官能度单体选用hdda,多官能度单体选用tmpta。低聚物与单体的质量比为3:5, 单体比例为1:2:1,分散剂kos110添加量为粉体质量的3%,柔润剂添加量为浆料总质量的0.5%,成膜剂添加量为浆料总质量的0.5%。
32.步骤三、配制陶瓷浆料:向预混液中分批加入氧化锆陶瓷粉体,在陶瓷粉添加量为粉体总量的70%前用均质机将其进行初步分散,设置四段均质参数,分别为500r/min,30s、1200r/min,60s、1800r/min,60s、1000r/min,60s。当质量达70%后,向浆料中加入光引发剂tpo,质量为光敏树脂的0.5%,之后加入所需的全部粉体,此时参数调整为二段均质参数,分别为1500r/min、30s,2500r/min、100s。然后再利用三辊研磨机对团聚颗粒进行粉碎,最后
在均质机真空模式、转速2500r/min条件下对浆料脱泡处理120s,得到质量分数为80%的陶瓷浆料。
33.上述三辊研磨参数共设置5段,参数如表2:表2 三辊研磨分散参数编号入辊间隙(μm)出辊间隙(μm)研磨次数转速(r/min)参数18060150参数25020150参数3155250参数442250参数521250步骤四、浆料性能测试:利用流变仪对浆料进行粘度测试,其中测试温度为25℃,浆料剪切速率为32s-1
时的粘度为62 pa.s,并利用刮板细度计测试最大团聚粒径为0.8 μm。
34.步骤五、材料试验:对浆料进行材料试验,将用于材料试验的stl文件传输于打印机后,手动将浆料平铺于打印平台,分别进行5次固化后利用螺旋测微仪测量固化厚度。曝光参数分别选择20、2s,20、3s,25、2s,25、3s,30、2s,相应固化厚度分别为32μm、46μm、40μm、60μm、50μm。
35.步骤六、打印实验:将待打印模型导入软件后进行模型层切,其中样条模型尺寸为长
ⅹ
宽
ⅹ
高=45mm
ⅹ
5mm
ⅹ
3.8mm。层切参数中首层层厚为60μm,曝光能量及时间设置为40、5s,打印层厚选择20μm,打印光强及时间分别为25、3s,将层切文件传输至打印机后将浆料置于两端料槽中进行打印,打印过程中铺料平整无针眼、缩孔等缺陷。打印结束后取下模型素坯并将表面多余浆料利用异丙醇清除。测量该打印参数下得到的样条的尺寸,其中长、宽、高分别为45.19mm、5.07mm、3.81mm,相应收缩率为0.4%、1.4%、0.2%。打印的样条及义齿素坯精度优良,无明显过度曝光。
36.步骤七、脱脂烧结:其中脱脂环境为空气气氛,脱脂工艺为从室温以1℃/min升至250℃,保温1h,以0.8℃/min速率分别升至350℃后保温2h、450℃保温2h、700℃保温2h,后以2℃/min的升温速率升至1000℃后保温2h,而后随炉冷却至室温。
37.其中烧结工艺为从室温以5℃/min的升温速率升至1000℃后以2℃/min速率升至1200℃,再以1℃/min的速率升至1450℃,保温2h,后以2℃/min的速率降温至900℃后随炉冷却至室温。
38.步骤八、性能测试:烧结后样条无表面及层间裂纹且不翘曲,测量烧结后样条在长、宽、高方向上的尺寸并记录,利用万能试验机对10根样条进行抗弯强度测试并计算平均值,其中加载速度设置为0.5mm/min,跨距选择30mm,最终平均抗弯强度为450mpa。利用维氏硬度仪对断裂后的10根样条进行硬度测试并计算平均值,其中加载力及加载时间设置为10kg、5s,平均维氏硬度为1232hv。
39.最后对样条进行断面及表面扫描电镜分析,断面晶粒尺寸在300-450nm,之间,无过度生长现象,断裂方式为穿晶断裂,表面晶粒排列紧密(见图4左)。
40.实施例3:配制质量分数为83%的陶瓷浆料,步骤如下:步骤一、粉体处理:对粒径为200 nm的氧化锆粉体在100℃真空干燥箱中干燥15h后取出利用80目筛网进行筛分备用;
步骤二、配制预混液:称取一定量的低聚物与单体于黑色研磨罐中,手动搅拌均匀后加入分散剂byk-180、柔润剂蔗糖硬脂酸酯、成膜剂三甲基硅氧基硅酸酯以及溶剂巯基乙醇,在机械搅拌器350r/min条件下充分搅拌3h得预混液。
41.其中低聚物为pua/20%hdda,单体包括单官能度单体ida,双官能度单体hdda,三官能度单体tmpta。低聚物与单体的质量比为1:4, 单官能度单体:双官能度:三官能度=1:3:2。其中byk-180添加量为粉体质量的5%,柔润剂和成膜剂均占浆料总质量的0.5%与0.5%,巯基乙醇占粉体质量的1%。
42.步骤三、配制陶瓷浆料:将陶瓷粉分批加入预混液中,在陶瓷粉添加量为粉体总量的80%前用均质机进行初步分散,设置三段均质参数,分别为800r/min,30s、1800r/min,120s、1000r/min,60s。当质量达80%后,向浆料中加入光引发剂tpo,质量为光敏树脂的1.2%,之后加入剩余粉体均质,此时参数调整为二段均质参数,分别为1500r/min,30s、2200r/min,100s。然后再利用三辊研磨机对团聚颗粒进行粉碎。最后在均质机真空模式、转速2500r/min条件下对浆料脱泡处理120s,得到质量分数为83%的陶瓷浆料。
43.上述三辊研磨参数共设置5段,参数如表3:表3 三辊机研磨参数编号入辊间隙(μm)出辊间隙(μm)研磨次数转速(r/min)参数110060150参数24020150参数31551100参数4422100参数5212100步骤四、浆料性能测试:在均质机2500r/min条件下对浆料进行180s的脱泡处理后进行粘度及粒度测试,经测试该浆料在25℃、剪切速率为32s-1
时的粘度为72 pa.s,最大团聚粒径为1.5 μm。
44.步骤五、材料试验:对浆料进行材料试验,将用于材料试验的stl文件传输于打印机后,手动将浆料平铺于打印平台,分别进行5次固化后利用螺旋测微仪测出固化厚度。曝光参数分别选择20、3s,25、3s,28、3s,32、3s,35、3s,相应固化厚度分别为52μm、65μm、75μm、84μm、91μm。
45.步骤六、打印实验:将待打印模型导入软件后进行模型层切,其中样条模型尺寸为长
ⅹ
宽
ⅹ
高=45mm
ⅹ
5mm
ⅹ
3.8mm。层切参数中首层层厚60μm,曝光能量及时间设置为60、4s,打印层厚选择25μm,打印光强及时间分别为28、3s,将层切文件传输至打印机后将浆料置于两端料槽中进行打印,打印过程中铺料平整无针眼、缩孔等缺陷。打印结束后取下模型素坯并将表面多余浆料利用异丙醇清除。测量该打印参数下得到的样条的尺寸,其中长、宽、高分别为45.11mm、5.06mm、3.81mm,相应收缩率为0.24%、1.2%、0.2%。打印的样条及义齿素坯精度优良,无明显过度曝光。
46.步骤七、脱脂烧结:其中脱脂烧结环境均为空气气氛。脱脂工艺为从室温以0.8℃/min升至250℃,保温1h,以0.2℃/min速率分别升至360℃后保温2h、450℃保温2h、700℃保温2h,后以1℃/min的升温速率升至1000℃后保温2h,而后随炉冷却至室温。
47.烧结工艺为从室温以3℃/min的升温速率升至1200℃后以0.8℃/min的速率升至
1500℃,保温2h,后以2℃/min的速率降温至900℃后随炉冷却至室温。
48.步骤八、性能测试:烧结后样条无表面及层间裂纹且不翘曲,测量烧结后样条在长、宽、高方向上的尺寸并记录,利用万能试验机对10根样条进行抗弯强度测试并计算平均值,其中加载速度设置为0.5mm/min,跨距选择30mm,最终平均抗弯强度为510mpa。利用维氏硬度仪对断裂后的10根样条进行硬度测试并计算平均值,其中加载力及加载时间设置为10kg、5s,平均维氏硬度为1337hv。
49.最后对样条进行断面及表面扫描电镜分析,发现晶粒尺寸在300-400之间,无过度生长,断裂模式为穿晶断裂(见图6左),表面晶粒排列紧密。
50.对比例1:与实施例1相比,本对比例除在步骤二配制预混液中不添加溶剂巯基乙醇外,其他步骤及添加组分种类及含量与实施例1完全一致,具体步骤如下:步骤一、粉体处理:粉体粒径、干燥条件及筛分条件同实施例1。
51.步骤二、配制预混液:除不添加溶剂巯基乙醇外,其余组分种类及添加量同实施例1。
52.步骤三、陶瓷浆料配制:步骤完全同实施例1。
53.步骤四、浆料性能测试:利用流变仪对浆料进行粘度测试,温度设置为25℃,在剪切速率32s-1
时浆料粘度为78pa.s,利用刮板细度计对颗粒团聚粒径进行测量,最大为1.5μm。
54.步骤五、材料试验:对浆料进行材料试验以确定打印参数,将用于材料试验的stl文件传输于打印机后,将浆料平铺于打印平台,分别进行5次固化后利用螺旋测微仪测量固化厚度。曝光参数分别选择20、2s,20、3s,30、2s,30、3s,40、2s,与实施例1保持一致,相应固化厚度分别为28μm、40μm、39μm、58μm、52μm,从结果上看不添加巯基乙醇的条件下固化厚度较实施例1有所减小,当曝光强度及时间为40、3s,其固化厚度可达到75μm。
55.步骤六、打印实验:将待打印样条模型导入软件后进行模型层切,其中模型尺寸为长
ⅹ
宽
ⅹ
高=45mm
ⅹ
5mm
ⅹ
3.8mm。层切参数设置首层层厚60μm,曝光能量及时间设置为40、5s,打印层厚选择25μm,打印光强及时间分别为40、3s,将层切文件传输至打印机后将浆料置于两端料槽中开始打印,打印过程中铺料平整不存在缩孔现象。打印结束后取下模型素坯并将表面多余浆料利用异丙醇清除,发现样条存在轻微翘曲。测量该打印参数下得到的样条的尺寸,其中长、宽、高分别为45.19mm、5.13mm、3.88mm,相应收缩率为0.4%、2.6%、2.1%。由上述结果可知,不添加巯基乙醇,不仅降低了光固化速率,同时由于曝光能量过大造成样条在固化过程中应力分布不均产生翘曲,同时打印精度也有所下降。
56.步骤七、脱脂烧结:脱脂烧结参数同实施例1。
57.步骤八、性能测试:烧结后样条无表面及层间裂纹,但存在略微翘曲现象,测量烧结后样条在长、宽、高方向上的尺寸并记录,利用万能试验机对10根样条进行抗弯强度测试并计算平均值,其中加载速度设置为0.5mm/min,跨距选择30mm,最终平均抗弯强度为410mpa。利用维氏硬度仪对断裂后的10根样条进行硬度测试并计算平均值,其中加载力及加载时间设置为10kg、5s,平均维氏硬度为1120hv,对样条进行断面扫描电镜分析,发现晶粒尺寸在300-400nm之间,断裂方式为穿晶断裂。
58.对比例2:
与实施例2相比,本对比例在步骤二配制预混液中不添加柔润剂蔗糖硬脂酸酯及成膜剂三甲基硅氧基硅酸酯外,其他步骤及添加组分种类及含量与实施例2完全一致,具体步骤如下:步骤一、粉体处理:粉体粒径、干燥条件及筛分条件同实施例2。
59.步骤二、配制预混液:除不添加蔗糖硬脂酸酯及成膜剂三甲基硅氧基硅酸酯外,其余组分种类及添加量同实施例2。
60.步骤三、陶瓷浆料配制:步骤完全同实施例2。
61.步骤四、浆料性能测试:利用流变仪对浆料进行粘度测试,温度设置为25℃,在剪切速率32s-1
时浆料粘度为63pa.s,利用刮板细度计对颗粒团聚粒径进行测量,最大为1.2μm。
62.步骤五、材料试验:对浆料进行材料试验以确定打印参数,将用于材料试验的stl文件传输于打印机后,将浆料平铺于打印平台,分别进行5次固化后利用螺旋测微仪测量固化厚度。曝光参数分别选择20、2s,20、3s,25、2s,25、3s,30、2s,与实施例2保持一致,相应固化厚度分别为20μm、32μm、26μm、37μm、33μm,从结果上看不添加柔润剂及成膜剂的条件下固化厚度较实施例2有所减小,这是由于此时预混液与粉体的折射率相差较大在固化过程中导致光照被反射,固化厚度下降。所以将曝光能量设置为40、3s,其固化厚度可达61μm。
63.步骤六、打印实验:将待打印样条模型导入软件后进行模型层切,其中模型尺寸为长
ⅹ
宽
ⅹ
高=45mm
ⅹ
5mm
ⅹ
3.8mm。层切参数设置首层层厚60μm,曝光能量及时间设置为40、5s,打印层厚选择20μm,打印光强及时间分别为40、3s,将层切文件传输至打印机后将浆料置于两端料槽中开始打印,打印过程中发现铺料不平整且存在针眼、缩孔现象。打印结束后取下模型素坯并将表面多余浆料利用异丙醇清除,样条存在轻微翘曲。测量该打印参数下得到的样条的尺寸,其中长、宽、高分别为45.23mm、5.16mm、3.85mm,相应收缩率为0.5%、3.2%、1.3%。综上,不添加柔润剂蔗糖硬脂酸酯与成膜剂三甲基硅氧基硅酸酯,不仅导致铺料效果较差,而且降低了光固化速率,样条产生翘曲,同时打印精度也有所下降。
64.步骤七、脱脂烧结:脱脂烧结参数同实施例2。
65.步骤八、性能测试:烧结后样条无表面裂纹但存在层间裂纹,且存在轻微翘曲现象,测量烧结后样条在长、宽、高方向上的尺寸并记录,利用万能试验机对10根样条进行抗弯强度测试并计算平均值,其中加载速度设置为0.5mm/min,跨距选择30mm,最终平均抗弯强度为205mpa。利用维氏硬度仪对断裂后的10根样条进行硬度测试并计算平均值,其中加载力及加载时间设置为10kg、5s,平均维氏硬度为1030hv,对断裂后的样条进行扫描电镜分析,晶粒尺寸在400-500之间,但由于表面含有微米级别的小孔(见图4右)且存在层间裂纹,造成抗弯强度过低。
66.对比例3:与实施例3相比,本对比例在步骤二配制预混液中除不添加成膜剂三甲基硅氧基硅酸酯外,其他步骤及添加组分种类及含量与实施例3完全一致,利用流变仪对浆料进行粘度测试,测得该浆料粘度为84s-1
,最大团聚粒径为2.3μm左右。在材料试验过程中当单层固化层厚为75μm时,曝光强度及时间分别为25、3s,利用此参数对样条模型进行打印,发现铺料过程中浆料表面存在针眼缺陷,打印样条不翘曲。素坯样条长、宽、高分别为45.13mm、5.07mm、3.83mm,相应收缩率为0.28%、1.4%、0.79%。脱脂烧结后测得抗弯强度为365mpa,维
氏硬度为1230hv,进行断面扫描电镜分析后,发现晶粒出现过度生长,晶粒尺寸不均一,最大可达700nm(见附图6右)。由上述结论可知,缺少成膜剂会导致浆料团聚颗粒增大造成粘度增加(见附图5右),从而铺料过程中由于流平性较差出现缺陷,另外大颗粒也会导致固化后样条厚度增加导致精度下降,经过烧结,大颗粒继续生长,最终造成抗弯强度下降。
67.对比例4:与实施例1相比,此对比例除浆料配制过程不一样,其他步骤与实施例1保持完全一致。
68.在浆料配制过程中,主要利用球磨机对浆料进行混合,首先将称取的预混液各组分置于球磨机研磨罐中,在转速350r/min条件下研磨3h得到混合均匀的预混液,然后平均分4批加入氧化锆粉体,前两批由于浆料粘度低,转速保持350r/min,研磨球的尺寸及比例为3mm:5mm=1:3,球磨8h。随后将剩余粉体分2次加入球磨罐中,由于浆料粘度增大,为以防团聚颗粒过大,将转速调整为600r/min,研磨球的尺寸及比例为1mm:3mm=1:1,球磨10h,最后加入光引发剂tpo,质量为光敏树脂的0.8%,继续在该条件下球磨2h得陶瓷浆料。该浆料在剪切速率32s-1时粘度为140pa.s,且聚集最大颗粒在3.5μm左右。对该浆料进行材料实验,发现铺料过程中浆料无法铺平且固化厚度时大时小,不稳定,打印过程中由于浆料粘度过大导致流平性较差(见图7),改变刮刀速度后可打印成型但精度很差且存在翘曲现象(见图8),所以并未对其进行脱脂烧结及性能测试。
69.以上是本技术实施例的实施方式,应当指出,对于本技术领域的普通技术人员来说,在不脱离本技术实施例原理的前提下,还可以做出若干改进和润饰,这些改进和润饰也视为本技术的保护范围。