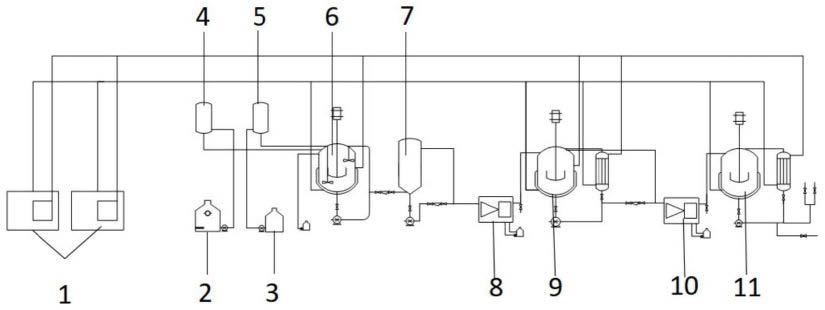
1.本发明属于石墨烯膜制备技术领域,具体涉及一种氧化石墨烯浆料连续分散循环系统及方法。
背景技术:2.石墨烯由于其高导热率和高比表面积,使其在电子器件散热导热领域有着巨大前景,这时石墨烯膜的制备尤为重要,而要得到石墨烯膜,必须优先制备氧化石墨烯浆料,氧化石墨烯浆料的制备必经搅拌分散均质过程,才能达到后续生产石墨烯膜所需性能要求,现有公开的分散氧化石墨烯浆料采用较为原始的搅拌系统配合均质机,一般均质压力35-60mpa,浆料粘度超100000mpa
·
s,压力不够,一方面不适用与高粘度浆料,另一方面整个搅拌分散工艺不连贯,不合理,生产效率比较低,无法满足连续生产需求。
技术实现要素:3.针对现有技术存在问题中的一个或多个,本发明提供一种氧化石墨烯浆料连续分散循环系统,包括配料制备系统、称量系统、搅拌系统、均质系统和循环冷却系统,所述配料制备系统用于配置去离子水和添加剂,所述称量系统用于称量配料制备系统配置的去离子水和添加剂,所述搅拌系统用于搅拌称量系统称量的去离子水和添加剂以及氧化石墨烯饼料,形成氧化石墨烯浆料;所述均质系统用于对搅拌系统搅拌后的氧化石墨烯浆料进行至少两次均质,所述循环冷却系统用于对搅拌系统和均质系统进行循环冷却。
4.根据本发明的一个方面,所述配料制备系统包括去离子水储料罐和添加剂储料罐,所述称量系统包括去离子水称量罐和添加剂称量罐,所述搅拌系统包括搅拌罐,所述去离子水储料罐与去离子水称量罐连通,所述去离子水称量罐与搅拌罐连通,所述添加剂储料罐与添加剂称量罐连通,添加剂称量罐与所述搅拌罐连通;优选地,所述添加剂原液和去离子水的配置比例为1:5-1:20,进一步优选地,所述添加剂原液和去离子水的配置比例为1:9,由于添加剂原液占比量小直接添加,搅拌不均匀,产生色差,出于对氧化石墨烯滤饼与去离子水搅拌充分,对添加剂进行稀释,稀释总量控制在10%左右,兼顾氧化石墨烯搅拌与添加剂的融合。
5.根据本发明的一个方面,还包括中转系统,所述中转系统在所述搅拌系统和均质系统之间中转氧化石墨烯浆料,优选地,所述中转系统为中转罐。搅拌后增加中转罐,便于高生产率连续性生产,若没有中转罐,使用搅拌机直连均质系统,均质时搅拌机只能停止运行,待均质完成后,才可进行下一步的搅料。根据本发明的一个方面,所述均质系统包括多个均质机,相邻均质机之间通过均质冷却罐连通,所述循环冷却系统对均质机内的以及均质冷却罐内的氧化石墨烯浆料进行循环冷却。
6.根据本发明的一个方面,所述均质系统还包括多个旋转粘度计,所述旋转粘度计设置在均质机的放料口,用于测量均质后氧化石墨烯浆料的粘度。
7.根据本发明的一个方面,所述均质系统包括依次连通的一次均质机、一次均质冷
却罐、二次均质机和二次均质冷却罐,所述一次均质机与搅拌系统连通,所述一次均质机、一次均质冷却罐、二次均质机和二次均质冷却罐分别与循环冷却系统连通。
8.根据本发明的一个方面,一次均质机均质后的氧化石墨烯浆料的粘度为42000-60000mpa
·
s,控制一次均质粘度范围,是为了经过二次均质后浆料的粘度在一定程度上满足刮涂上料的要求,粘度低于42000mpa
·
s经过二次均质后粘度会降低更多会影响涂布粘度情况;二次均质机均质后的氧化石墨烯浆料的粘度为28000-41000mpa
·
s,二次均质后的粘度控制在此范围符合现有涂布刮涂的高厚度的上料方式,粘度太低流动性强无法涂布,粘度超高了之后对于浆料中的气泡难以处理,综合考虑将粘度范围控制在一定的范围内较适合涂布。
9.根据本发明的一个方面,所述去离子水的ph值为5.0-7.5,去离子水的ph值范围要求防止偏酸性或者是偏碱性对后面浆料ph的调节产生影响,一般要求在中性左右即可;优选地,所述去离子水的温度为28℃
±
3℃,去离子水在此温度范围有利于石墨烯的搅拌分散,解决难搅拌,影响分散效果,;优选地,所述去离子水的电导率≤20μs/cm,通过控制去离子水的电导率控制水中的金属离子的含量,防止在石墨化过程中排除吸附在石墨化炉子的电极感应线圈,防止侵蚀设备器件。
10.根据本发明的一个方面,所述氧化石墨烯浆料的固含在2.0%-5.0%,固含在上述范围,是确保浆料粘度满足涂布要求以及对产品性能保障的一个范围,固含低于2%的粘度低刮刀式涂布较难把控,不能涂厚膜;固含高于5%的,对应的浆料粘度更高,流动性差不适合涂布,浆料气泡难以消除,优选地,氧化石墨烯浆料的固含在4.6%-5.0%,固含的提升有利于一次性涂成厚膜,浆料粘度适中,满足涂布要求。。
11.根据本发明的一个方面,所述循环冷却系统为循环水冷却系统;优选地,冷水温度设定为13℃,水温太低,冷水机负荷容易过载,报警停机,带来不必要的麻烦,因为均质完后的浆料温度非常高(出口料温50℃左右),冷却水温度设置高了,降温时间较长,影响浆料的周转速度,一般在上述温度冷却在30min即可;优选地,所述循环冷却系统包括多个循环水冷机。
12.根据本发明的一个方面,所述均质系统一次均质时的压力为60-80mpa,二次均质时的压力为80-100mpa,一次均质压力较二次均质压力要小是因为搅拌前分散的颗粒饼料存在未完全搅开,前后均质压力一样大容易造成均质机进料堵塞,均质机空打或者进入空气容易造成泵头的损坏,二次均质压力提高是在一次均质的基础之上将go的尺寸打的更小更加均匀。
13.根据本发明的另一个方面,提供一种氧化石墨烯浆料连续分散循环的方法,包括:
14.配置去离子水,称量配置的去离子水;
15.配置添加剂,称量配置的添加剂;
16.搅拌称量的去离子水和添加剂以及氧化石墨烯饼料,形成氧化石墨烯浆料;
17.对搅拌后的氧化石墨烯浆料进行至少两次均质;
18.其中,对搅拌过程中、均质过程中和均质后的氧化石墨烯浆料进行循环冷却。
19.根据本发明的另一个方面,所述对搅拌后的氧化石墨烯浆料进行至少两次均质的步骤包括:
20.对搅拌后的氧化石墨烯浆料进行中转;
21.中转后的氧化石墨烯浆料进行至少两次均质;
22.其中,多批氧化石墨烯浆料分别在搅拌、中转和均质不同步骤中连续循环运行。
23.根据本发明的另一个方面,所述对搅拌后的氧化石墨烯浆料进行至少两次均质的步骤包括:
24.对氧化石墨烯浆料进行两次均质。
25.优选地,一次均质的压力为60-80mpa,二次均质的压力为80-100mpa,一次均质压力较二次均质压力要小是因为搅拌前分散的颗粒饼料存在未完全搅开,前后均质压力一样大容易造成均质机进料堵塞,均质机空打或者进入空气容易造成泵头的损坏,二次均质压力提高实在一次均质的基础之上将go的尺寸打的更小更加均匀。
26.优选地,一次均质后的氧化石墨烯浆料的粘度为42000-60000mpa
·
s;二次均质后的氧化石墨烯浆料的粘度为28000-41000mpa
·
s,控制一次均质粘度范围,是为了经过二次均质后浆料的粘度在一定程度上满足刮涂上料的要求,粘度低于42000mpa
·
s,经过二次均质后粘度会降低更多会影响涂布粘度情况,二次均质后的粘度控制在28000-41000mpa
·
s范围符合现有涂布刮涂的高厚度的上料方式,粘度太低流动性强无法涂布,粘度超高了之后对于浆料中的气泡难以处理,综合考虑将粘度范围控制在一定的范围内较适合涂布。
27.根据本发明的另一个方面,所述搅拌称量的去离子水和添加剂以及氧化石墨烯饼料,形成氧化石墨烯浆料的步骤包括:
28.连续分步称量的去离子水和添加剂以及氧化石墨烯饼料,包括:将称量的氧化石墨烯饼料和添加剂一次投入,分步多次投入去离子水,优选地,分3-4步投入去离子水,分步添加水量有利于充分搅拌,防止有挂壁或者粘在搅拌桨上,多次投水使浆料充分搅拌,避免一次性加完水后,过程中出现异常后调整难度增大。
29.根据本发明的另一个方面,所述搅拌称量的去离子水和添加剂以及氧化石墨烯饼料,形成氧化石墨烯浆料的步骤包括:
30.形成氧化石墨烯浆料的固含在2.0%-5.0%,优选地,形成氧化石墨烯浆料的固含在4.6%-5.0%。
31.根据本发明的另一个方面,所述搅拌称量的去离子水和添加剂以及氧化石墨烯饼料,形成氧化石墨烯浆料的步骤包括:
32.搅拌时公转和自转同时进行,且转速均可根据浆料状态进行调整,例如,通过打开搅拌系统预留观察口,探照灯察看浆料的颜色及粘稠情况,如遇饼料沉底粘度低,浆料搅拌不开,开启底部阀门经螺杆泵从下往上循环,促进搅拌分散。
33.根据本发明的另一个方面,所述配置去离子水的步骤包括:
34.将去离子水的ph值调整到5.0-7.5;优选地,还包括:对去离子水进行预热,进一步,优选地,将去离子水的温度预热到28℃。
35.根据本发明的另一个方面,所述对搅拌过程中、均质过程中和均质后的氧化石墨烯浆料进行循环冷却的步骤包括:
36.采用水冷方式对对搅拌过程中、均质过程中和均质后的氧化石墨烯浆料进行循环冷却,优选地,冷水温度设定为13℃。
37.本发明氧化石墨烯浆料连续分散循环系统包括配料制备系统、称量系统、搅拌系统、均质系统和循环冷却系统,通过均质系统对搅拌系统搅拌后的氧化石墨烯浆料进行多
次均质,通过循环冷却系统对搅拌系统和均质系统进行循环冷却,为更加合理化,产业化,效率高的氧化石墨烯浆料连续分散循环系统。本发明氧化石墨烯浆料连续分散循环系统还包括中转系统,搅拌后的氧化石墨烯浆料通过中转系统进入均质系统,均质系统均质时,搅拌系统不停止搅拌,可以实现冷却与搅拌、均质同时进行,极大缩短了氧化石墨烯浆料制备过程,有利于高生产率连续生产,可以实现连续配料、搅拌、均质,最大程度缩短工序间停留时间,每步工艺步骤时间控制在90min以内。
38.本发明可以实现高固含、高粘度的氧化石墨烯浆料搅拌分散。
39.本发明可以实现将浆料粘度超过1000000mpa
·
s降至30000mpa
·
s左右。
40.本发明可以最大化利用现有各步骤设备与人员,缩短氧化石墨烯浆料制备时间,极大提高氧化石墨烯浆料制备效率,极大提高制备出氧化石墨烯浆料的稳定性。
附图说明
41.图1是本发明所述氧化石墨烯浆料连续分散循环系统的示意图;
42.图2是本发明所述氧化石墨烯浆料均质前的sem图;
43.图3是本发明所述氧化石墨烯浆料均质一次的sem图;
44.图4是本发明所述氧化石墨烯浆料均质二次的sem图;
45.图5是本发明所述氧化石墨烯浆料均质三次的sem图。
具体实施方式
46.在下文中,仅简单地描述了某些示例性实施例。正如本领域技术人员可认识到的那样,在不脱离本发明的精神或范围的情况下,可通过各种不同方式修改所描述的实施例。因此,附图和描述被认为本质上是示例性的而非限制性的。
47.以下结合附图对本发明的优选实施例进行说明,应当理解,此处所描述的优选实施例仅用于说明和解释本发明,并不用于限定本发明。
48.图1是本发明所述氧化石墨烯浆料连续分散循环系统的示意图,如图1所示,所述氧化石墨烯浆料连续分散循环系统包括配料制备系统、称量系统、搅拌系统6、均质系统和循环冷却系统1,所述配料制备系统用于配置去离子水和添加剂,所述称量系统用于称量配料制备系统配置的去离子水和添加剂,所述搅拌系统6用于搅拌称量系统称量的去离子水和添加剂以及氧化石墨烯饼料,形成氧化石墨烯浆料;所述均质系统用于对搅拌系统搅拌后的氧化石墨烯浆料进行至少两次均质,所述循环冷却系统1用于对搅拌系统和均质系统进行循环冷却。
49.优选地,所述添加剂为r01添加剂,氨水添加剂,起到中和作用,go饼料分散后的溶液酸性较强,对设备有腐蚀作用,添加r01把酸性中和,另外还有一个作用就是有利于饼料搅拌时的颗粒剥离分散打开。
50.在一个实施例中,所述配料制备系统包括去离子水储料罐2和添加剂储料罐3,所述称量系统包括去离子水称量罐4和添加剂称量罐5,所述搅拌系统包括搅拌罐,所述去离子水储料罐与去离子水称量罐连通,所述去离子水称量罐与搅拌罐连通,所述添加剂储料罐与添加剂称量罐连通,添加剂称量罐与所述搅拌罐连通;优选地,所述添加剂原液和去离子水的配置比例为1:5-1:20。
51.在一个实施例中,还包括中转系统7,所述中转系统在所述搅拌系统和均质系统之间中转氧化石墨烯浆料,优选地,所述中转系统为中转罐。
52.在一个实施例中,所述均质系统包括多个均质机,相邻均质机之间通过均质冷却罐连通,所述循环冷却系统对均质机内的以及均质冷却罐内的氧化石墨烯浆料进行循环冷却。
53.优选地,所述均质系统包括依次连通的一次均质机8、一次均质冷却罐9、二次均质机10和二次均质冷却罐11,所述一次均质机与搅拌系统连通,所述一次均质机、一次均质冷却罐、二次均质机和二次均质冷却罐分别与循环冷却系统连通。
54.本发明还提供一种氧化石墨烯浆料连续分散循环的方法,包括:
55.步骤s1,配置去离子水,称量配置的去离子水;
56.步骤s2,配置添加剂,称量配置的添加剂;
57.步骤s3,搅拌称量的去离子水和添加剂以及氧化石墨烯饼料,形成氧化石墨烯浆料,其中,氧化石墨烯饼料可以直接添加至搅拌系统,称量去离子水混合搅拌,再添加添加剂搅拌形成氧化石墨烯浆料;
58.步骤s4,对搅拌后的氧化石墨烯浆料进行至少两次均质;
59.其中,对搅拌过程中、均质过程中和均质后的氧化石墨烯浆料进行循环冷却。
60.在一个实施例中,所述步骤s4包括:
61.对搅拌后的氧化石墨烯浆料进行中转;
62.中转后的氧化石墨烯浆料进行至少两次均质;
63.其中,多批氧化石墨烯浆料分别在搅拌、中转和均质不同步骤中连续循环运行。
64.在一个实施例中,所述步骤s4中,对氧化石墨烯浆料进行两次均质,图2是步骤s3获得的氧化石墨烯浆料均质前的sem图,图3是本发明所述氧化石墨烯浆料均质一次的sem图,图4是本发明所述氧化石墨烯浆料均质二次的sem图,图5是本发明所述氧化石墨烯浆料均质三次的sem图,从图2-图5可以看出,二次均质在一次均质的基础之上将go的尺寸打的更小更加均匀,经过两次均质,三次均质粒子片径无明显的变化。
65.优选地,一次均质的压力为60-80mpa,二次均质的压力为80-100mpa,一次均质压力较二次均质压力要小是因为搅拌前分散的颗粒饼料存在未完全搅开,前后均质压力一样大容易造成均质机进料堵塞,均质机空打或者进入空气容易造成泵头的损坏,二次均质压力提高实在一次均质的基础之上将go的尺寸打的更小更加均匀。
66.优选地,一次均质后的氧化石墨烯浆料的粘度为42000-60000mpa
·
s;二次均质后的氧化石墨烯浆料的粘度为28000-41000mpa
·
s,控制一次均质粘度范围,是为了经过二次均质后浆料的粘度在一定程度上满足刮涂上料的要求,粘度低于42000mpa
·
s,经过二次均质后粘度会降低更多会影响涂布粘度情况,二次均质后的粘度控制在28000-41000mpa
·
s范围符合现有涂布刮涂的高厚度的上料方式,粘度太低流动性强无法涂布,粘度超高了之后对于浆料中的气泡难以处理,综合考虑将粘度范围控制在一定的范围内较适合涂布。
67.最后应说明的是:以上所述仅为本发明的优选实施例而已,并不用于限制本发明,尽管参照前述实施例对本发明进行了详细的说明,对于本领域的技术人员来说,其依然可以对前述各实施例所记载的技术方案进行修改,或者对其中部分技术特征进行等同替换。凡在本发明的精神和原则之内,所作的任何修改、等同替换、改进等,均应包含在本发明的
保护范围之内。