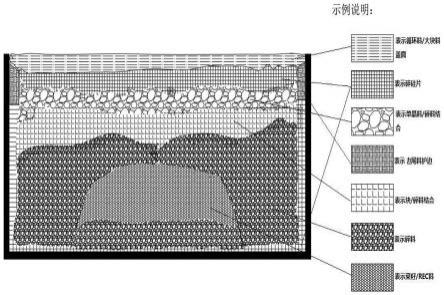
1.本发明涉及太阳能单晶用提纯锭铸锭的技术领域,具体涉及一种单晶用提纯锭铸锭方法。
背景技术:2.现阶段太阳能硅片领域,单晶占主导,多晶市场被挤压,用铸锭炉生产单晶用提纯锭是多晶铸锭厂家主要方向和盈利方式。
3.现阶段单晶提纯锭料况复杂,碎片、碎料、菜籽料、颗粒料等小直径料比例超过80%,相对于正常中高效锭小直径料比例低于30%而言,装料难度增大,如没有合理的装料搭配方法,装料量低、成本高,且小直径料清洗后易酸碱残留,容易对坩埚形成腐蚀造成硅液溢流;此种配料结构需开发、匹配相对应的铸锭工艺,匹配不当会造成熔化阶段坩埚底部硅料二次凝固,对坩埚造成挤压,导致硅液溢流;单晶用提纯锭对硅锭杂质阴影缺陷要求严格,铸锭工艺需保证金属、碳、氮化硅等杂质排至硅锭顶部,提升产品得率。
技术实现要素:4.本发明的主要目的在于提供一种单晶用提纯锭铸锭方法,同时通过设计铸锭工艺匹配,解决单晶用提纯锭装料量低、成本高、硅液溢流风险高、排杂难的问题。
5.为解决上述技术问题,本发明所采用的技术方案是:提纯锭铸锭方法包括坩埚装料方法及铸锭工艺控制方法,单晶提纯锭料主要以块料、碎料、碎片、颗粒料为主,块料装在坩埚的中间和顶端盖面,碎料、碎片、颗粒料装在坩埚的底部和四周;
6.铸锭工艺控制方法主要是通过在坩埚顶、侧、底部同时加热,控制坩埚顶部和四周先熔化,坩埚底部后熔化。
7.坩埚装料方法的步骤如下:s1、在坩埚底部0~20mm及坩埚四周中底部用碎硅片铺地、靠边,碎片间留有缝隙;
8.s2、在坩埚20~300mm的底部位置装入碎料;
9.s3、在坩埚100~300mm的中间位置装入rec/菜籽料;
10.s4、在坩埚300~380mm位置装入小块料与碎料混合;
11.s5、在坩埚380~450mm位置装入大块料与碎料混合;
12.s6、在坩埚450~490mm位置装入碎片,其填充在大块料之间的缝隙,同时盖住碎料;
13.s7、在坩埚顶部和四周用相对规则的循环料护边,保护氮化硅涂层,该位置处在固体熔化至液体的截面线;
14.s8、坩埚顶部装入不规则的循环料,主要用作盖面。
15.优选方案中,s2中碎料的为单晶沫子料、多晶碎料、粉末料。
16.优选方案中,s3中物料堆放呈圆形。
17.优选方案中,s4中物料交叉装填,填充缝隙,保证装料量。
18.优选方案中,s5中物料交叉装填,不留缝隙,提升装料量,同时大块料位置相对靠上。
19.铸锭工艺控制方法步骤如下:a1、熔化第1步1175℃为功率模式转化为温度模式控制,并填入氩气,排出硅料和坩埚中的水分、杂质,在顶、侧、底部同时加热;
20.a2、熔化第2~9步为升温、熔化阶段,在此过程中保持顶、侧、底部高功率输出,坩埚顶部、底部同时化料,且根据化料速率调整顶侧功率系数;
21.a3、熔化第10步熔化阶段结束,通过观察孔、功率曲线、底部温度等判断硅料是否熔化结束;
22.a4、熔化第11~13步为硅料熔化后降温,设定时间持续保持硅液对流,杂质外排,最终为长晶阶段做准备。
23.本发明提供了一种单晶用提纯锭铸锭方法,有益效果:
24.1、针对单晶用提纯锭小颗粒料比例偏高现状,此装料发明方法既能保证投料量的增加,也能合理的保证坩埚四周和底部空间,漏硅风险大大降低;
25.2、针对此配料结构和装料方法,开发、匹配最优熔化工艺方法,通过熔化阶段顶、侧、底部同时加热方法,防止顶部硅液流至底部二次凝固挤压坩埚棱角造成漏硅风险;同时此工艺设计能有效缩短熔化时间,降低氮化硅保护涂层被冲击强度;
26.3、此工艺熔化配方及时保证硅液对流强度,上下翻滚,将杂质既能通过氩气流通而带走,也能使杂质尽可能的往硅锭顶部排,有效降低硅锭在长晶阶段杂质分凝难度,提升硅锭铸锭得率,满足市场品质低杂质需求。
附图说明
27.下面结合附图和实施例对本发明作进一步说明:
28.图1是本发明坩埚内物料装填示意图。
具体实施方式
29.实施例1
30.如图1所示,一种单晶用提纯锭铸锭方法,本专利针对单晶用提纯锭装料的工艺方法详细说明:
31.坩埚底部0-20mm及坩埚四周中底部用碎硅片铺底、靠边,保护坩埚底部及侧部氮化硅涂层,且碎片间有缝隙,防止硅料熔化挤压底部及四周,对坩埚形成冲击。
32.坩埚底部20-300mm位置主要以碎料为主(单晶沫子料、多晶碎料、粉末料),碎料因颗粒直径0-2mm左右,如装在坩埚上部或顶部会导致硅料在铸锭炉抽真空环节中抽出至炉内,造成硅料浪费,并形成假漏硅而意外停炉;碎料在硅料清洗、腐蚀过程易形成酸、碱残留,直接接触坩埚会腐蚀坩埚,提高硅液溢流风险。
33.在坩埚高度100-200mm左右且中间位置装rec/菜籽料,此类料外观呈圆形,硬度高、易滚动,且化料时呈爆炸性膨胀,不能靠近坩埚四周、或底部,且保证其不流动,控制风险。
34.在坩埚高度300-380mm左右位置主要装填小块料与碎料混合,交叉装填,尽可能填充缝隙,保证装料量。小块料的直径为0.2-20cm。
35.在坩埚高度380-450mm左右位置装填相对大块料(如锅底、焖炉、单晶棒等)与碎料混合,交叉装填,无缝隙,提升装料量,同时大块料位置相对靠上,能保证硅料化料速度,节省电耗。大块料的直径为20cm以上。
36.在坩埚高度450-490mm左右装填碎片,其主要作用一方面是填充大块料之间的缝隙,保证装料量,同时盖住碎料,防止在铸锭炉抽真空时被抽出。
37.在坩埚顶部四周用相对规则的循环料(主要指边料、尾料、t2料)护边,保护氮化硅涂层,该位置处在固体熔化至液体的界面线(固液界面线),长时间受硅液冲击,极其容易粘埚,护边操作极其重要。
38.坩埚顶部主要装填不规则的循环料(如块料、t2料等),主要用做盖面。
39.实施例2
40.本专利针对单晶用提纯锭铸锭炉熔化工艺设计主要菜单说明:如表1所示:
41.熔化第1步1175℃为功率模式转化为温度模式控制,并填入氩气,排出硅料和坩埚中的水分、杂质,顶、侧、底部同时加热。
42.熔化第2-9步主要为升温、熔化阶段,在此过程中保持顶、侧、底部高功率输出,坩埚顶部、底部同时化料,防止坩埚底部温度过低导致顶部硅液流至底部二次凝固而挤压坩埚,且根据化料速率调整顶侧功率系数,保证硅料化料均匀、快速,缩短在高温情况下高温液体对氮化硅保护涂层的冲击时间,同时硅液保持热量对流,使杂质及时对流至硅锭定部或通过氩气流通带走。
43.熔化第10步为熔化阶段化料结束跳转步骤,人为通过观察孔、功率曲线、底部温度等判断硅料是否熔化结束,可跳至下一步。
44.熔化第11-13步主要为硅料熔完后降温步骤,设定时间继续保持硅液对流,杂质外排,最终为长晶阶段做准备。
[0045][0046]
表1:铸锭炉熔化工艺流程表
[0047]
上述的实施例仅为本发明的优选技术方案,而不应视为对于本发明的限制,本发明的保护范围应以权利要求记载的技术方案,包括权利要求记载的技术方案中技术特征的等同替换方案为保护范围。即在此范围内的等同替换改进,也在本发明的保护范围之内。