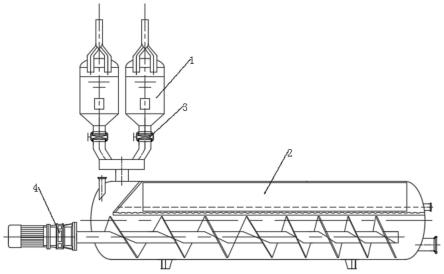
1.本发明涉及碱制品生产技术领域,特别是涉及一种使用高浊度轻灰生产低盐优质重灰的重灰生产工艺系统及其生产工艺。
背景技术:2.随着《纯碱行业节能降碳改造升级实施指南(2022)的出台,国家和行业要求“加强前沿技术开发应用,培育标杆示范企业”。纯碱生产企业,需要加强前沿技术的开发应用,推动现有落后产能的改造升级,应用绿色技术工艺、使用节能装备,应用新型装备技术,降低污染物排放,实现企业的绿色低碳发展。
3.以轻质纯碱(轻灰)为原料生产重质纯碱(重灰)的水合方法有两种:液相水合法和固相水合法。上述两种生产工艺研发时间均早于上世纪90年代,受当时技术水平和装配制造水平的制约,均存在一定的弊端。
4.固相水合法因水与轻灰未能实现充分接触,反应时间不易控制,水合率相对较低,成品粒度均匀性较差、强度较差、易碎,容易产生粉尘。产品质量无法在水合工序调节,产品粒度稳定性难以控制。重灰盐分受轻灰影响大,难以实现重灰成品的低盐化。
5.液相水合法可以使轻灰与液体充分混合,水合率高,晶粒均匀,产品粒度较好,盐分可以控制,易于生产低盐优质重灰。但其工艺方法在生产和应用过程中存在以下缺点和函待解决的问题:
6.1.水合结晶器原料为>150℃的粉体,进料采用“粉体自然坠落式投料”;水合结晶器内的液体为温度85-90℃的饱和母液,水合结晶器工作温度范围为95-100℃,(沸点为106.5℃)。这种传统的生产工艺方法受投料速度,循环冷却水流量等影响,反应温度不易控制,操作难度较高。水合反应属于放热反应,易使母液中的水分气化。粉体与水汽结合后,极易在容器内结疤,需要定期(倒罐)停用清洗。现有技术重灰液相水合工艺操作法中,主反应器需要设置用于清洗倒换的设备(3运行1倒用),无法实现单体设备长时间的连续生产(原专利cn02148849.5中“水合结晶器的使用周期为8天”)。
7.2.优质重质纯碱要求“水不溶物的质量分数”≤0.02%。而在重质纯碱的生产过程中,并没有采用工艺方法去降低水不溶物的含量,只能通过要求原料轻灰降低这一指标来实现,所以传统的重灰生产方法要求轻灰必须为“优等品”,进而保证重灰产品的质量。如果轻灰浊度指标(由水不溶物的质量分数决定)不合格,则无法生产出优质重灰。这不但提高了对原料的要求,而且限制了生产布置和工艺流程。
8.3.液相水合结晶工艺核心设备水合结晶器,需要设置备用设备,且水合反应后续流程长,设备多、投资比固相水合法高,影响了该生产工艺的市场竞争力。
技术实现要素:9.本发明的目的是针对现有技术中存在的技术缺陷,而提供一种重灰生产工艺系统。
10.本发明的另一目的,是提供一种重灰生产工艺。
11.为实现本发明的目的所采用的技术方案是:
12.一种重灰生产工艺系统,包括原料输送装置、水合反应装置、产品后处理装置和废固废液处理装置;
13.所述水合反应装置包括用于晶核产生的水合晶核生成器和用于晶核生长的除盐调浆器;所述水合晶核生成器与所述除盐调浆器之间选择性连通或隔绝;
14.所述水合晶核生成器包括生成器本体、开设在所述生成器本体顶部的轻灰入口和穿过所述生成器本体侧壁并深入至其内部空腔的饱和母液输送管道;所述饱和母液输送管道位于所述生成器本体内部空腔的端部设置有微界面发生器;饱和母液经所述饱和母液输送管道输送后在所述微界面发生器的作用下分散成微米级液滴;所得微米级液滴与经轻灰入口飘落的轻灰接触进行水合反应,形成晶核;
15.所述除盐调浆器包括稠厚器本体和变螺距螺旋桨;所述变螺距螺旋桨受电机减速机驱动水平设置在所述稠厚器本体的内部空腔内;
16.所述稠厚器本体上开设有一个或多个供晶核进入的混合物入口、用于补充轻灰的轻灰入口、用于补充饱和母液的饱和母液补充口、含盐母液出口和一水碱混合物出口;其中所述混合物入口、轻灰入口和饱和母液补充口位于稠厚器本体靠近电机减速机的一端;所述含盐母液出口和一水碱混合物出口位于稠厚器本体的另一端。
17.在上述技术方案中,所述水合晶核生成器的数量为一个或多个。
18.在上述技术方案中,所述微界面发生器包括覆盖在所述饱和母液输送管道端部的一级多孔板、含有二级多孔板的第一套筒、含有三级多孔板的第二套筒和导流桶;
19.经一级多孔板流出的饱和母液进入第一套筒后从所述二级多孔板流出;经二级多孔板流出的饱和溶液进入第二套筒后从三级多孔板流出,进入导流桶。
20.在上述技术方案中,所述一级多孔板的孔径为0.2-0.5mm;所述二级多孔板的孔径为0.1-0.2mm;所述三级多孔板的孔径为0.05-0.08mm;所述一级多孔板上覆盖有一级丝网;所述一级丝网的孔径为75-100μm;所述二级多孔板上覆盖有二级丝网;所述二级丝网的孔径为50-70μm;所述三级多孔板上覆盖有三级丝网;所述三级丝网的孔径为5-25μm。
21.在上述技术方案中,所述导流桶呈向上开口的喇叭状。
22.在上述技术方案中,所述除盐调浆器内还设置有换热板,以导出反应热。
23.在上述技术方案中,所述稠厚器本体上还开设有浆液循环口、循环回流口和分析取样口。
24.在上述技术方案中,所述原料输送装置采用气力输送。
25.在上述技术方案中,所述产品后处理装置包括依次连接的带式过滤机、干燥/冷却一体式换热设备和产品包装机。
26.在上述技术方案中,所述废固废液处理装置包括母液配制槽、浮浆过滤器、冷冻除盐器、树脂交换器和高盐母液外排器;所述除盐调浆器的含盐母液出口管道分成两路;其中一路依次与浮浆过滤器、树脂交换器和母液配制槽依次相连;另一路与冷冻除盐器相连;冷冻除盐器的液相出口与高盐母液外排器相连,以将溶解在液体里的nacl随着母液外排;冷冻除盐器的浆料出口与母液配制槽相连,以将冷析结晶物送到母液配置槽。
27.本发明的另一方面,一种重灰生产工艺,包括以下步骤:
28.步骤1:轻灰原料经原料输送装置输送至母液配制槽,配置饱和碳酸钠溶液;将饱和碳酸钠溶液在脉冲加压泵的驱动下,经饱和母液输送管道输送至所述的水合结晶反应装置中的水合晶核生成器内,同时在微界面发生器的作用下破碎成微米级液滴;与此同时,轻灰原料经原料输送装置输送后经轻灰入口进入水合晶核生成器内;
29.步骤2:所得微米级饱和碳酸钠液滴与轻灰颗粒接触进行水合反应,反应90-150s形成晶核;
30.步骤3:连通所述水合晶核生成器与所述除盐调浆器,使反应生成的晶核进入权利要求1中所述的水合结晶反应装置中的除盐调浆器;继续向除盐调浆器内补充轻灰和饱和碳酸钠溶液,使晶核继续生长至成品尺寸;晶核生长过程中,在变螺距螺旋桨的驱动、挤压作用下,逐步接近重颗粒灰颗粒出口,并在重灰出口处形成一水碱颗粒混合物;一水碱颗粒混合物经一水碱混合物出口导出,水合结晶反应结束;
31.步骤4:所得一水碱颗粒混合物经产品后处理装置处理得产品。
32.在上述技术方案中,步骤1中,轻灰与饱和碳酸钠溶液的质量比为1:(1.5-2.5);
33.步骤3中,补充的轻灰和饱和碳酸钠溶液的质量比为1:(2.5-4)。
34.在上述技术方案中,步骤3中,生长温度为80-90℃;生长压力为0.005-0.01mpa;生长时间为8-12min。
35.本发明的另一方面,一种重灰生产工艺系统,包括原料输送装置、如权利要求1-7任一项所述的水合反应装置、产品后处理装置和废固废液处理装置;
36.所述原料输送装置采用气力输送;
37.所述产品后处理装置包括依次连接的带式过滤机、干燥/冷却一体式换热设备和产品包装机;
38.所述废固废液处理装置包括母液配制槽、浮浆过滤器、冷冻除盐器、树脂交换器和高盐母液外排器;所述除盐调浆器的含盐母液出口管道分成两路;其中一路依次与浮浆过滤器、树脂交换器和母液配制槽依次相连;另一路与冷冻除盐器相连;冷冻除盐器的液相出口与高盐母液外排器相连,以将溶解在液体里的nacl随着母液外排;冷冻除盐器的浆料出口与母液配制槽相连,以将冷析结晶物送到母液配置槽。
39.与现有技术相比,本发明的有益效果是:
40.1.本发明提供的重灰生产工艺系统,将晶核生成和晶体长大分置于两个腔体内,用阀门切断。晶核形成所需时间占水合反应总时间的比例较低,可以认为是瞬时完成,而晶核长大过程占据时间长,这个过程在“除盐调浆器”内完成。“除盐调浆器”与2-3台“晶核生成器”相连接。因此可以在不影响整个水合反应的前提下,实现对水合晶核生成器的轮换清洗,实现不设置备用主体设备(除盐调浆器)的前提下,确保生产的连续进行。
41.2.本发明提供的重灰生产工艺系统,所得的一水碱晶体颗粒均匀、密实,获得的产品颗粒度可以达到并优于优质重灰对粒度的指标要求,提升产品质量。
42.3.本发明提供的重灰生产工艺系统,微界面发生器可以将饱和溶液打散形成微米级液滴。由于液滴尺寸的减小,界面附着力增强,使在传统界面尺寸下无法生成一水碱的水不溶物与优质轻灰一起形成一水碱晶核,并随着晶核成长,形成合格的重灰产品,从而摆脱重灰生产对轻灰浊度指标(水不溶物的质量分数%)的要求。
附图说明
43.图1所示为水合结晶反应装置的结构示意图;
44.图2所示为水合晶核生成器的结构示意图;
45.图3所示为微界面发生器的结构示意图;
46.图4所示为除盐调浆器的结构示意图;
47.图5所示为重灰生产工艺系统的示意图。
48.图中:1-水合晶核生成器,11-生成器本体,12-轻灰入口,13-饱和母液输送管道,14-微界面发生器,141-一级多孔板,142-二级多孔板,143-三级多孔板,144-导流桶,145-上封板,146-下封板,2-除盐调浆器,21-稠厚器本体,22-变螺距螺旋桨,23-换热板,24-混合物入口,25-轻灰入口,26-饱和母液补充口,27-含盐母液出口,28-一水碱混合物出口,29-浆液循环口,210-循环回流口,211-分析取样口,3-自控阀,4-电机减速机。
具体实施方式
49.以下结合具体实施例对本发明作进一步详细说明。应当理解,此处所描述的具体实施例仅仅用以解释本发明,并不用于限定本发明。
50.实施例1
51.一种重灰生产工艺系统,如图5所示,包括原料输送装置、水合反应装置、产品后处理装置和废固废液处理装置;
52.其中,所述原料输送装置采用气力输送(即图5中所述的粉体输送系统);详见《联碱装置轻灰和重灰气力输送的可行性研究》
53.(doi:10.16554/j.cnki.issn1005-8370.2020.03.008)。
54.所述水合结晶反应装置包括水合晶核生成器和除盐调浆器;轻灰和饱和母液在水合晶核生成器内水合反应,形成晶核然后进入除盐调浆器;晶核在除盐调浆器生长至产品尺寸。
55.所述产品处理装置包括带式过滤机、干燥/冷却一体式换热设备和产品包装机。经除盐调浆器2一水碱混合物出口28导出的固液比(体积比)60%以上的一水碱颗粒混合物经带式过滤机过滤后,进入风干/粉体流冷却一体式换热器冷却,最后由产品包装机包装。
56.所述废固废液处理装置包括母液配制槽、浮浆过滤器、冷冻除盐器(操作温度在10-20摄氏度之间)、树脂交换器(在树脂中加入含银离子溶液进行载银处理,通过载银树脂中的银离子与溶液中的钠离子进行离子交换,银离子与氯离子结合生成不溶于水的氯化银沉淀,进而达到母液除盐的目的.实现除盐处理后的母液可以得到循环利用)和高盐母液外排器;所述除盐调浆器2的含盐母液出口27管道分成两路;其中一路依次与浮浆过滤器、树脂交换器和母液配制槽依次相连;另一路与冷冻除盐器相连;冷冻除盐器的液相出口与高盐母液外排器相连,以将溶解在液体里的nacl随着母液外排;冷冻除盐器的浆料出口与母液配制槽相连,以将冷析结晶物送到母液配置槽。经含盐母液出口27流出的含盐母液有两种除盐方案,一种是经浮浆过滤器过滤后在树脂交换器内进行树脂交换,然后回收进入母液配制槽;另一种是经冷冻除盐器除盐后,将高盐母液排出,将剩余溶液回收进入母液配制槽。
57.所述水合晶核生成器与母液配制槽之间设置有碱尘回收装置,所述碱尘回收装置
为湿式电除尘器,将从水合晶核生成器内回收回来的碱尘除尘后回收进入母液配制槽。
58.所述原料输送装置与水合晶核生成器和除盐调浆器分别连通,一方面为水合反应形成晶核提供轻灰,另一方面为晶核生长提供轻灰。
59.所述母液配制槽与所述水合晶核生成器相连通,为后者提供饱和母液。
60.实施例2
61.本实施例是在实施例1的基础上介绍其水合结晶反应装置。
62.一种水合结晶反应装置,如图1所示,包括一个或多个用于晶核产生的水合晶核生成器1和一个用于晶核生长的除盐调浆器2;所述水合晶核生成器1与所述除盐调浆器2之间通过自控阀3控制其连通或隔绝。
63.所述水合晶核生成器1如图2所示,为立式容器,包括生成器本体11、开设在所述生成器本体11顶部的轻灰入口12和穿过所述生成器本体11侧壁并深入至其内部空腔的饱和母液输送管道13;所述饱和母液输送管道13位于所述生成器本体11内部空腔的端部设置有微界面发生器14;饱和母液经饱和母液输送管道13输送后在微界面发生器14的作用下分散成微米级液滴(10-50μm),与经轻灰入口12飘落的轻灰接触进行水合反应,形成晶核。
64.所述微界面发生器14如图3所示,包括覆盖在所述饱和母液输送管道13端部的一级多孔板141、套装在所述饱和母液输送管道13端部的二级多孔板142、套装在所述二级多孔板142外部的三级多孔板143和套装在所述三级多孔板143外部的导流桶144;所述二级多孔板142的上下两端分别设置有上封板145和下封板146;所述二级多孔板142与上封板145和下封板146组合形成第一套筒,经一级多孔板141流出的饱和母液进入第一套筒后从所述二级多孔板142流出;所述三级多孔板143的下端向内弯折延伸,与所述二级多孔板142相连;所述三级多孔板143的上端通过上封板145与母液输送管道13连接;所述三级多孔板143和所述上封板145组合形成第二套筒;经二级多孔板142流出的饱和溶液进入第二套筒后从三级多孔板143流出,进入导流桶144;所述导流桶144呈向上开口的喇叭状;饱和母液在外接脉冲加压泵的驱动下,经过一级多孔板141、二级多孔板142、三级多孔板143分散成微米级液滴在导流桶144的作用下向上分散喷射,与轻灰接触。在微米级液滴生成过程中,随着压力的不断消耗,使液滴被破碎,液体压力近似降为常压。
65.其中,一级多孔板141的孔径为0.2-0.5mm、二级多孔板142的孔径为0.1-0.2mm、三级多孔板143的孔径为0.05-0.08mm。为提高多孔板对饱和母液的破碎效果,所述一级多孔板141上覆盖有一级丝网;所述一级丝网的孔径为75-100μm;所述二级多孔板142上覆盖有二级丝网;所述二级丝网的孔径为50-70μm;所述三级多孔板143上覆盖有三级丝网;所述三级丝网的孔径为5-25μm。
66.所述除盐调浆器2如图4所示,为卧式容器,包括稠厚器本体21、变螺距螺旋桨22和换热板23;所述变螺距螺旋桨22受电机减速机4驱动水平设置在所述稠厚器本体21的内部空腔内;所述换热板23焊接在所述稠厚器本体21的内部空腔内以导出反应热;所述稠厚器本体21上开设有一个或多个供晶核进入的混合物入口24、用于补充轻灰的轻灰入口25、用于补充饱和母液的饱和母液补充口26、含盐母液出口27和一水碱混合物出口28;其中所述混合物入口24、轻灰入口25和饱和母液补充口26位于稠厚器本体21靠近电机减速机4的一端;所述含盐母液出口27和一水碱混合物出口28位于稠厚器本体21的另一端。所述稠厚器本体21上还开设有浆液循环口29、循环回流口210和分析取样口211;所述分析取样口211用
于检测产品是否达到预期指标;所述浆液循环口29、循环回流口210通过管线连接,当产品没有达到预期指标使,使物料再经过设备入口进行一次循环,使产品指标合格。
67.水合晶核生成器1内生成的晶核通过混合物入口24进入稠厚器本体21,晶核在稠厚器本体21内继续接触轻灰及饱和母液,使晶核不断生长至成品尺寸。同时在变螺距螺旋桨22的作用下通过沉降、“挤压”(挤压是靠螺旋实现的,沉降是靠重力自然实现的)的方式使含有一水碱的饱和溶液脱水、除盐(盐分是存在于液相之中,将水分挤出的同时,即将盐分去除。变螺距螺旋所带来的体积的变化,配合重力沉降作用,会使液体从螺旋上部排除,下部的混合物的水分会逐渐变小),形成固液比(体积比)60%以上的一水碱颗粒混合物。其中含盐母液经含盐母液出口27流出;一水碱颗粒混合物经一水碱混合物出口28导出。
68.实施例3
69.本实施例是在实施例1和2的基础上介绍一种重灰生产工艺。
70.一种重灰生产工艺,包括以下步骤:
71.步骤1:轻灰原料经原料输送装置输送至母液配制槽,配置90℃的饱和碳酸钠溶液;将90℃的饱和碳酸钠溶液在脉冲加压泵的驱动下,经饱和母液输送管道13输送至水合晶核生成器1内,同时在微界面发生器14的作用下破碎成微米级液滴;
72.与此同时,轻灰原料经原料输送装置输送后经轻灰入口12进入水合晶核生成器1内;
73.此步骤中,轻灰与饱和碳酸钠溶液的质量比为1:2.5;
74.步骤2:微米级饱和碳酸钠液滴与轻灰颗粒接触进行水合反应,反应90-150s形成晶核;
75.步骤3:打开自控阀3,使反应生产的晶核进入除盐调浆器2;继续向除盐调浆器2内补充轻灰和饱和碳酸钠溶液,使晶核继续生长至成品尺寸;晶核生长过程中,在变螺距螺旋桨22的驱动、挤压作用下,逐步接近重颗粒灰颗粒出口28,并在一水碱混合物出口28处形成固液比(体积比)60%以上的一水碱颗粒混合物;一水碱颗粒混合物经一水碱混合物出口28导出,水合结晶反应结束;
76.生长温度为90℃;生长压力为0.01mpa;生长时间为12min;
77.本步骤中,补充的轻灰和饱和碳酸钠溶液的质量比为1:2.5。
78.步骤4:所得一水碱颗粒混合物经产品后处理装置处理得产品。
79.实施例4
80.本实施例是在实施例1和2的基础上介绍一种重灰生产工艺。
81.一种重灰生产工艺,包括以下步骤:
82.步骤1:轻灰原料经原料输送装置输送至母液配制槽,配置90℃的饱和碳酸钠溶液;将90℃的饱和碳酸钠溶液在脉冲加压泵的驱动下,经饱和母液输送管道13输送至水合晶核生成器1内,同时在微界面发生器14的作用下破碎成微米级液滴;
83.与此同时,轻灰原料经原料输送装置输送后经轻灰入口12进入水合晶核生成器1内;
84.此步骤中,轻灰与饱和碳酸钠溶液的质量比为1:1.5;
85.步骤2:微米级饱和碳酸钠液滴与轻灰颗粒接触进行水合反应,反应90-150s形成晶核;
86.步骤3:打开自控阀3,使反应生产的晶核进入除盐调浆器2;继续向除盐调浆器2内补充轻灰和饱和碳酸钠溶液,使晶核继续生长至成品尺寸;晶核生长过程中,在变螺距螺旋桨22的驱动、挤压作用下,逐步接近重颗粒灰颗粒出口28,并在一水碱混合物出口28处形成固液比(体积比)60%以上的一水碱颗粒混合物;一水碱颗粒混合物经一水碱混合物出口28导出,水合结晶反应结束;
87.生长温度为90℃;生长压力为0.005mpa;生长时间为12min;
88.本步骤中,补充的轻灰和饱和碳酸钠溶液的质量比为1:4。
89.步骤4:所得一水碱颗粒混合物经产品后处理装置处理得产品。
90.实施例5
91.本实施例是在实施例1和2的基础上介绍一种重灰生产工艺。
92.一种重灰生产工艺,包括以下步骤:
93.步骤1:轻灰原料经原料输送装置输送至母液配制槽,配置80℃的饱和碳酸钠溶液;将80℃的饱和碳酸钠溶液在脉冲加压泵的驱动下,经饱和母液输送管道13输送至水合晶核生成器1内,同时在微界面发生器14的作用下破碎成微米级液滴;
94.与此同时,轻灰原料经原料输送装置输送后经轻灰入口12进入水合晶核生成器1内;
95.此步骤中,轻灰与饱和碳酸钠溶液的质量比为1:2.0;
96.步骤2:微米级饱和碳酸钠液滴与轻灰颗粒接触进行水合反应,反应90-150s形成晶核;
97.步骤3:打开自控阀3,使反应生产的晶核进入除盐调浆器2;继续向除盐调浆器2内补充轻灰和饱和碳酸钠溶液,使晶核继续生长至成品尺寸;晶核生长过程中,在变螺距螺旋桨22的驱动、挤压作用下,逐步接近重颗粒灰颗粒出口28,并在一水碱混合物出口28处形成固液比(体积比)60%以上的一水碱颗粒混合物;一水碱颗粒混合物经一水碱混合物出口28导出,水合结晶反应结束;
98.生长温度为80℃;生长压力为0.01mpa;生长时间为8min;
99.本步骤中,补充的轻灰和饱和碳酸钠溶液的质量比为1:3。
100.步骤4:所得一水碱颗粒混合物经产品后处理装置处理得产品。
101.实施例6
102.本实施例是在实施例1和2的基础上介绍一种重灰生产工艺。
103.一种重灰生产工艺,包括以下步骤:
104.步骤1:轻灰原料经原料输送装置输送至母液配制槽,配置80℃的饱和碳酸钠溶液;将80℃的饱和碳酸钠溶液在脉冲加压泵的驱动下,经饱和母液输送管道13输送至水合晶核生成器1内,同时在微界面发生器14的作用下破碎成微米级液滴;
105.与此同时,轻灰原料经原料输送装置输送后经轻灰入口12进入水合晶核生成器1内;
106.此步骤中,轻灰与饱和碳酸钠溶液的质量比为1:2.5;
107.步骤2:微米级饱和碳酸钠液滴与轻灰颗粒接触进行水合反应,反应90-150s形成晶核;
108.步骤3:打开自控阀3,使反应生产的晶核进入除盐调浆器2;继续向除盐调浆器2内
补充轻灰和饱和碳酸钠溶液,使晶核继续生长至成品尺寸;晶核生长过程中,在变螺距螺旋桨22的驱动、挤压作用下,逐步接近重颗粒灰颗粒出口28,并在一水碱混合物出口28处形成固液比(体积比)60%以上的一水碱颗粒混合物;一水碱颗粒混合物经一水碱混合物出口28导出,水合结晶反应结束;
109.生长温度为80℃;生长压力为0.005mpa;生长时间为8min;
110.本步骤中,补充的轻灰和饱和碳酸钠溶液的质量比为1:3.5。
111.步骤4:所得一水碱颗粒混合物经产品后处理装置处理得产品。
112.实施例3-6介绍的水合结晶反应工艺制得的成品尺寸分布如下表所示:
[0113][0114]
由上表可知,所得的一水碱晶体颗粒均匀、密实,获得的产品颗粒度可以达到并优于优质重灰对粒度的指标要求,提升产品质量。且经过测试,所得产品中水不溶物的含量均小于0.01%,满足优质重质纯碱的产品标准。
[0115]
以上所述仅是本发明的优选实施方式,应当指出的是,对于本技术领域的普通技术人员来说,在不脱离本发明原理的前提下,还可以做出若干改进和润饰,这些改进和润饰也应视为本发明的保护范围。