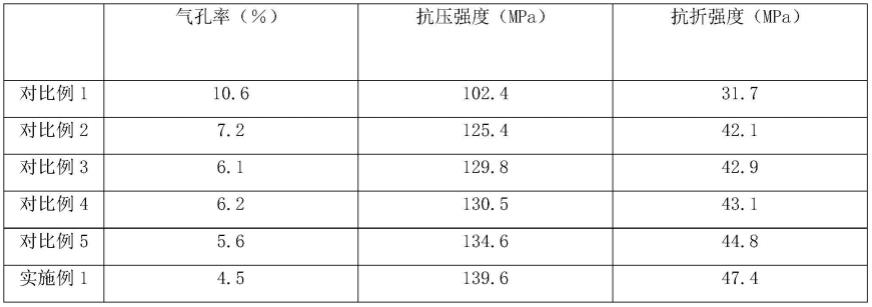
1.本发明涉及坩埚技术领域,更具体地说,本发明涉及高强度高致密性石英坩埚的制备工艺。
背景技术:2.坩埚是一种实验室中使用的杯状器皿,主要用来对固体进行高温加热。石英是一种由硅和氧组成的矿物,化学式为sio2;石英主要应用于玻璃、陶瓷、机械铸造、耐火材料、化工和冶金等传统行业领域。石英是地壳中第二丰富的矿物;石英坩埚可以在1850℃以下使用,分为透明和不透明两种;使用电弧法制的半透明石英坩埚是拉制大直径单晶硅,是发展大规模集成电路必不可少的基础材料;当今,世界半导体工业发达国家已用此坩埚取代了小的透明石英坩埚;它具有高纯度、尺寸大、耐温性强、精度高、节约能源、保温性好、质量稳定等优点;石英坩埚适于用k2s2o7,khso4作熔剂熔融样品和用na2s2o7(先在212℃烘干)作熔剂处理样品。
3.现有的石英坩埚质脆,结构强度较差,容易发生破损。
技术实现要素:4.为了克服现有技术的上述缺陷,本发明的实施例提供高强度高致密性石英坩埚的制备工艺。
5.为实现上述目的,本发明提供如下技术方案:高强度高致密性石英坩埚的制备工艺,具体制备步骤如下:
6.步骤一:称取石英注浆浆料;
7.步骤二:将步骤一中的石英注浆浆料向模具中进行注浆后,施加240~300mpa静压3~5min,开模,得到素坯;
8.步骤三:将步骤二中制得的素坯放入到双面顶压机中,进行高温高压处理11~15min,得到高强度高致密性石英坩埚。
9.进一步的,在步骤一中,所述石英注浆浆料按照重量百分比计算包括:57.8~59.8%的石英复合粉体、5.78~5.98%的黏结剂、余量为溶剂。
10.进一步的,所述石英复合粉体按照重量百分比计算包括:7.6~8.6%的硼化锆微粉、0.8~1.2%的碳化锆微粉、0.8~1.2%的氧化镧、9.6~10.6%的氧化钇、2.7~3.7%的聚乙烯亚胺,余量为熔融石英砂;
11.所述石英注浆浆料的制备方法如下:
12.s1:按照上述重量百分比称取黏结剂、溶剂和石英复合粉体原料中的硼化锆微粉、碳化锆微粉、氧化镧、氧化钇、聚乙烯亚胺、熔融石英砂;
13.s2:将步骤s1中的硼化锆微粉、碳化锆微粉、氧化镧、氧化钇、聚乙烯亚胺、熔融石英砂进行共混送入到气流粉碎机中进行粉碎处理,得到石英复合粉体;
14.s3:将步骤s2中制得的石英复合粉体和步骤s1中的黏结剂、溶剂加入到球磨机中
进行球磨处理2~4小时,得到石英注浆浆料。
15.进一步的,所述石英注浆浆料按照重量百分比计算包括:57.8%的石英复合粉体、5.78%的黏结剂、余量为溶剂;所述石英复合粉体按照重量百分比计算包括:7.6%的硼化锆微粉、0.8%的碳化锆微粉、0.8%的氧化镧、9.6%的氧化钇、2.7%的聚乙烯亚胺,余量为熔融石英砂。
16.进一步的,所述石英注浆浆料按照重量百分比计算包括:59.8%的石英复合粉体、5.98%的黏结剂、余量为溶剂;所述石英复合粉体按照重量百分比计算包括:8.6%的硼化锆微粉、1.2%的碳化锆微粉、1.2%的氧化镧、10.6%的氧化钇、3.7%的聚乙烯亚胺,余量为熔融石英砂。
17.进一步的,所述石英注浆浆料按照重量百分比计算包括:58.8%的石英复合粉体、5.88%的黏结剂、余量为溶剂;所述石英复合粉体按照重量百分比计算包括:8.1%的硼化锆微粉、1.0%的碳化锆微粉、1.0%的氧化镧、10.1%的氧化钇、3.2%的聚乙烯亚胺,余量为熔融石英砂。
18.进一步的,所述黏结剂为聚乙烯醇缩丁醛,所述溶剂为乙醇溶液,所述乙醇溶液的浓度为75%。
19.进一步的,在步骤三中,双面顶压机处理素坯时的高压为3.5~3.7gpa,温度为1800~1900℃;在步骤s2中,采用螺旋式气流粉碎机进行粉碎处理,空气耗量为9~11m3/min,空气压力为0.65~0.75mpa;在步骤s3中,球磨机的球磨介质为氧化锆球,氧化锆球与石英复合粉体的重量比为1∶0.9~1.3,球磨机转速为400~500r/min。
20.进一步的,在步骤三中,双面顶压机处理素坯时的高压为3.5gpa,温度为1800℃;在步骤s2中,采用螺旋式气流粉碎机进行粉碎处理,空气耗量为9m3/min,空气压力为0.65mpa;在步骤s3中,球磨机的球磨介质为氧化锆球,氧化锆球与石英复合粉体的重量比为1∶0.9,球磨机转速为400r/min。
21.进一步的,在步骤三中,双面顶压机处理素坯时的高压为3.6gpa,温度为1850℃;在步骤s2中,采用螺旋式气流粉碎机进行粉碎处理,空气耗量为10m3/min,空气压力为0.70mpa;在步骤s3中,球磨机的球磨介质为氧化锆球,氧化锆球与石英复合粉体的重量比为1∶1.1,球磨机转速为450r/min。
22.本发明的技术效果和优点:
23.1、采用本发明中的原料配方和方法所制备出的高强度高致密性石英坩埚,结构强度更高,且自身致密性较佳,可有效避免石英坩埚发生破损;在步骤一中,称取合适分量的石英注浆浆料,用于后续制备加工;在步骤二中,将石英注浆浆料注入模具中,施加静压处理,可有效将石英注浆浆料进行快速压缩成型,得到素坯,可有效加强素坯的内部结构压缩效果更佳,进而有效加强石英坩埚的高致密度;在步骤三中,将素坯使用双面顶压机进行高温高压处理,可快速对素坯进行压紧和烧结处理,高压下原子的扩散速率显著降低,使得高温烧结过程中晶粒的异常生长受到抑制,合成压力越大,对晶粒生长的抑制作用越强,所得样品的晶粒尺寸越小,合成压力的升高有利于减少材料的孔洞缺陷,提升复合材料样品的致密度,有效加强石英坩埚的高强度和高致密性;在步骤s2中,对硼化锆微粉、碳化锆微粉、氧化镧、氧化钇、聚乙烯亚胺、熔融石英砂共混后进行粉碎处理,使得石英复合粉体共混更加均匀,便于后续石英注浆浆料的混匀性;在步骤s3中,将石英复合粉体、黏结剂和溶剂进
行球磨处理,可有效加强石英注浆浆料的混匀效果,加强石英注浆浆料的稳定性;
24.2、本发明石英坩埚原料中的石英复合粉体、黏结剂和溶剂相互配合,制成石英注浆浆料,可有效保证石英坩埚的基础性能;石英复合粉体中的熔融石英砂作为石英坩埚中的基础组成物质,保证石英坩埚的基础性能;石英复合粉体中的硼化锆微粉和碳化锆微粉相互配合,碳化锆作为硼化锆的烧结助剂,可有效加强提高引入碳化锆可以有效地阻碍硼化锆晶粒长大,并且在烧结过程中形成稳定的硼锆玻璃相,进一步提高材料的高致密性、力学性能和抗烧蚀性能;石英复合粉体中的聚乙烯亚胺可作为碳化锆的分散剂,在机械球磨处理下,聚乙烯亚胺可有效吸附在碳化锆粉末表面提高颗粒团聚的阻力进而有效提高碳化锆粉体的分散性,从而进一步加强石英坩埚致密性和高强度;石英复合粉体中的氧化镧与氧化钇相互配合,氧化镧对氧化钇进行补充调节,可有效降低石英坩埚的开孔率,提高石英坩埚和高致密性。
具体实施方式
25.下面将结合本发明实施例中的技术方案进行清楚、完整地描述,显然,所描述的实施例仅仅是本发明一部分实施例,而不是全部的实施例。基于本发明中的实施例,本领域普通技术人员在没有做出创造性劳动前提下所获得的所有其他实施例,都属于本发明保护的范围。
26.实施例1:
27.本发明提供了高强度高致密性石英坩埚的制备工艺,具体制备步骤如下:
28.步骤一:称取石英注浆浆料;所述石英注浆浆料按照重量百分比计算包括:57.8%的石英复合粉体、5.78%的黏结剂、余量为溶剂;所述石英复合粉体按照重量百分比计算包括:7.6%的硼化锆微粉、0.8%的碳化锆微粉、0.8%的氧化镧、9.6%的氧化钇、2.7%的聚乙烯亚胺,余量为熔融石英砂;所述黏结剂为聚乙烯醇缩丁醛,所述溶剂为乙醇溶液,所述乙醇溶液的浓度为75%;
29.所述石英注浆浆料的制备方法如下:
30.s1:按照上述重量百分比称取黏结剂、溶剂和石英复合粉体原料中的硼化锆微粉、碳化锆微粉、氧化镧、氧化钇、聚乙烯亚胺、熔融石英砂;
31.s2:将步骤s1中的硼化锆微粉、碳化锆微粉、氧化镧、氧化钇、聚乙烯亚胺、熔融石英砂进行共混送入到气流粉碎机中进行粉碎处理,得到石英复合粉体;采用螺旋式气流粉碎机进行粉碎处理,空气耗量为9m3/min,空气压力为0.65mpa;
32.s3:将步骤s2中制得的石英复合粉体和步骤s1中的黏结剂、溶剂加入到球磨机中进行球磨处理3小时,得到石英注浆浆料;球磨机的球磨介质为氧化锆球,氧化锆球与石英复合粉体的重量比为1∶0.9,球磨机转速为400r/min;
33.步骤二:将步骤一中的石英注浆浆料向模具中进行注浆后,施加270mpa静压4min,开模,得到素坯;
34.步骤三:将步骤二中制得的素坯放入到双面顶压机中,进行高温高压处理13min,得到高强度高致密性石英坩埚;双面顶压机处理素坯时的高压为3.5gpa,温度为1800℃。
35.实施例2:
36.与实施例1不同的是,所述石英注浆浆料按照重量百分比计算包括:59.8%的石英
复合粉体、5.98%的黏结剂、余量为溶剂;所述石英注浆浆料按照重量百分比计算包括:59.8%的石英复合粉体、5.98%的黏结剂、余量为溶剂;所述石英复合粉体按照重量百分比计算包括:8.6%的硼化锆微粉、1.2%的碳化锆微粉、1.2%的氧化镧、10.6%的氧化钇、3.7%的聚乙烯亚胺,余量为熔融石英砂。
37.实施例3:
38.与实施例1-2均不同的是,所述石英注浆浆料按照重量百分比计算包括:58.8%的石英复合粉体、5.88%的黏结剂、余量为溶剂;所述石英注浆浆料按照重量百分比计算包括:58.8%的石英复合粉体、5.88%的黏结剂、余量为溶剂;所述石英复合粉体按照重量百分比计算包括:8.1%的硼化锆微粉、1.0%的碳化锆微粉、1.0%的氧化镧、10.1%的氧化钇、3.2%的聚乙烯亚胺,余量为熔融石英砂。
39.实施例4:
40.与实施例3不同的是,高强度高致密性石英坩埚的制备工艺,具体制备步骤如下:
41.步骤一:称取石英注浆浆料;所述石英注浆浆料的制备方法如下:
42.s1:按照上述重量百分比称取黏结剂、溶剂和石英复合粉体原料中的硼化锆微粉、碳化锆微粉、氧化镧、氧化钇、聚乙烯亚胺、熔融石英砂;
43.s2:将步骤s1中的硼化锆微粉、碳化锆微粉、氧化镧、氧化钇、聚乙烯亚胺、熔融石英砂进行共混送入到气流粉碎机中进行粉碎处理,得到石英复合粉体;采用螺旋式气流粉碎机进行粉碎处理,空气耗量为11m3/min,空气压力为0.75mpa;
44.s3:将步骤s2中制得的石英复合粉体和步骤s1中的黏结剂、溶剂加入到球磨机中进行球磨处理3小时,得到石英注浆浆料;球磨机的球磨介质为氧化锆球,氧化锆球与石英复合粉体的重量比为1∶1.3,球磨机转速为500r/min;
45.步骤二:将步骤一中的石英注浆浆料向模具中进行注浆后,施加270mpa静压4min,开模,得到素坯;
46.步骤三:将步骤二中制得的素坯放入到双面顶压机中,进行高温高压处理13min,得到高强度高致密性石英坩埚;双面顶压机处理素坯时的高压为3.7gpa,温度为1900℃。
47.实施例5:
48.与实施例3不同的是,高强度高致密性石英坩埚的制备工艺,具体制备步骤如下:
49.步骤一:称取石英注浆浆料;所述石英注浆浆料的制备方法如下:
50.s1:按照上述重量百分比称取黏结剂、溶剂和石英复合粉体原料中的硼化锆微粉、碳化锆微粉、氧化镧、氧化钇、聚乙烯亚胺、熔融石英砂;
51.s2:将步骤s1中的硼化锆微粉、碳化锆微粉、氧化镧、氧化钇、聚乙烯亚胺、熔融石英砂进行共混送入到气流粉碎机中进行粉碎处理,得到石英复合粉体;采用螺旋式气流粉碎机进行粉碎处理,空气耗量为10m3/min,空气压力为0.70mpa;
52.s3:将步骤s2中制得的石英复合粉体和步骤s1中的黏结剂、溶剂加入到球磨机中进行球磨处理3小时,得到石英注浆浆料;球磨机的球磨介质为氧化锆球,氧化锆球与石英复合粉体的重量比为1∶1.1,球磨机转速为450r/min;
53.步骤二:将步骤一中的石英注浆浆料向模具中进行注浆后,施加270mpa静压4min,开模,得到素坯;
54.步骤三:将步骤二中制得的素坯放入到双面顶压机中,进行高温高压处理13min,
得到高强度高致密性石英坩埚;双面顶压机处理素坯时的高压为3.6gpa,温度为1850℃。
55.对比例1:
56.与实施例5不同的是,所述石英复合粉体为熔融石英砂。
57.对比例2:
58.与实施例5不同的是,所述石英注浆浆料按照重量百分比计算包括:58.8%的石英复合粉体、5.88%的黏结剂、余量为溶剂;所述石英复合粉体按照重量百分比计算包括:1.0%的碳化锆微粉、1.0%的氧化镧、10.1%的氧化钇、3.2%的聚乙烯亚胺,余量为熔融石英砂。
59.对比例3:
60.与实施例5不同的是,所述石英注浆浆料按照重量百分比计算包括:58.8%的石英复合粉体、5.88%的黏结剂、余量为溶剂;所述石英复合粉体按照重量百分比计算包括:8.1%的硼化锆微粉、1.0%的碳化锆微粉、10.1%的氧化钇、3.2%的聚乙烯亚胺,余量为熔融石英砂。
61.对比例4:
62.与实施例5不同的是,所述石英注浆浆料按照重量百分比计算包括:58.8%的石英复合粉体、5.88%的黏结剂、余量为溶剂;所述石英复合粉体按照重量百分比计算包括:8.1%的硼化锆微粉、1.0%的碳化锆微粉、1.0%的氧化镧、10.1%的氧化钇,余量为熔融石英砂。
63.对比例5:
64.与实施例5不同的是,所述石英注浆浆料的制备方法如下:
65.s1:按照上述重量百分比称取黏结剂、溶剂和石英复合粉体原料中的硼化锆微粉、碳化锆微粉、氧化镧、氧化钇、聚乙烯亚胺、熔融石英砂;
66.s2:将步骤s1中的黏结剂、溶剂和石英复合粉体原料中的硼化锆微粉、碳化锆微粉、氧化镧、氧化钇、聚乙烯亚胺、熔融石英砂加入到球磨机中进行球磨处理3小时,得到石英注浆浆料;球磨机的球磨介质为氧化锆球,氧化锆球与石英复合粉体的重量比为1∶1.1,球磨机转速为450r/min。
67.硼化锆微粉采购自湖北成丰化工有限公司、工业级、执行质量标准:国标;碳化锆微粉采购自湖北成丰化工有限公司、工业级、货号:002;氧化镧采购自西格玛奥德里奇(上海)贸易有限公司、货号:l4000;氧化钇采购自西格玛奥德里奇(上海)贸易有限公司、货号:774022;聚乙烯亚胺采购自武汉曙尔生物科技有限公司、货号:294321;熔融石英砂采购自石家庄欧美亚矿产品有限公司的超白高含量电熔熔融石英砂、等级:一级;聚乙烯醇缩丁醛采购自广州市新稀冶金化工有限公司、型号:shgl-101;75%浓度乙醇溶液采购自济南文竹化工有限公司、型号:wz-75乙醇。
68.分别取上述实施例和对比例中的高强度高致密性石英坩埚,按照gb2977-82标准对实施例和对比例中高强度高致密性石英坩埚的气孔率进行检测,按照gb/t4740 99标准对实施例和对比例中高强度高致密性石英坩埚的抗压强度进行检测,抗折强度按照gb/t3001-2008标准对实施例和对比例中高强度高致密性石英坩埚的抗折强度进行检测,测试结果如表一所示:
69.表一:
[0070][0071][0072]
由表一可知,本发明中制得的高强度高致密性石英坩埚,结构强度更高,且自身致密性较佳,可有效避免石英坩埚发生破损;
[0073]
在步骤一中,称取合适分量的石英注浆浆料,用于后续制备加工;在步骤二中,将石英注浆浆料注入模具中,施加静压处理,可有效将石英注浆浆料进行快速压缩成型,得到素坯,可有效加强素坯的内部结构压缩效果更佳,进而有效加强石英坩埚的高致密度;在步骤三中,将素坯使用双面顶压机进行高温高压处理,可快速对素坯进行压紧和烧结处理,高压下原子的扩散速率显著降低,使得高温烧结过程中晶粒的异常生长受到抑制,合成压力越大,对晶粒生长的抑制作用越强,所得样品的晶粒尺寸越小,合成压力的升高有利于减少材料的孔洞缺陷,提升复合材料样品的致密度,有效加强石英坩埚的高强度和高致密性;石英坩埚原料中的石英复合粉体、黏结剂和溶剂相互配合,制成石英注浆浆料,可有效保证石英坩埚的基础性能;石英复合粉体中的熔融石英砂作为石英坩埚中的基础组成物质,保证石英坩埚的基础性能;石英复合粉体中的硼化锆微粉和碳化锆微粉相互配合,碳化锆作为硼化锆的烧结助剂,可有效加强提高引入碳化锆可以有效地阻碍硼化锆晶粒长大,并且在烧结过程中形成稳定的硼锆玻璃相,进一步提高材料的高致密性、力学性能和抗烧蚀性能;石英复合粉体中的聚乙烯亚胺可作为碳化锆的分散剂,在机械球磨处理下,聚乙烯亚胺可有效吸附在碳化锆粉末表面提高颗粒团聚的阻力进而有效提高碳化锆粉体的分散性,从而进一步加强石英坩埚致密性和高强度;石英复合粉体中的氧化镧与氧化钇相互配合,氧化镧对氧化钇进行补充调节,可有效降低石英坩埚的开孔率,提高石英坩埚和高致密性;在步骤s2中,对硼化锆微粉、碳化锆微粉、氧化镧、氧化钇、聚乙烯亚胺、熔融石英砂共混后进行粉碎处理,使得石英复合粉体共混更加均匀,便于后续石英注浆浆料的混匀性;在步骤s3中,将石英复合粉体、黏结剂和溶剂进行球磨处理,可有效加强石英注浆浆料的混匀效果,加强石英注浆浆料的稳定性。
[0074]
需要说明的是,在本文中,诸如第一和第二等之类的关系术语仅仅用来将一个实体或者操作与另一个实体或操作区分开来,而不一定要求或者暗示这些实体或操作之间存在任何这种实际的关系或者顺序。而且,术语“包括”、“包含”或者其任何其他变体意在涵盖非排他性的包含,从而使得包括一系列要素的过程、方法、物品或者设备不仅包括那些要
素,而且还包括没有明确列出的其他要素,或者是还包括为这种过程、方法、物品或者设备所固有的要素。
[0075]
最后应说明的是:以上所述仅为本发明的优选实施例而已,并不用于限制本发明,尽管参照前述实施例对本发明进行了详细的说明,对于本领域的技术人员来说,其依然可以对前述各实施例所记载的技术方案进行修改,或者对其中部分技术特征进行等同替换。凡在本发明的精神和原则之内,所作的任何修改、等同替换、改进等,均应包含在本发明的保护范围之内。