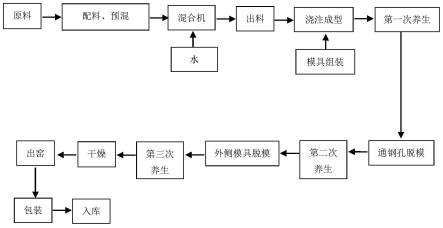
1.本发明涉及中间包用耐火材料技术领域,尤其涉及一种振动成型的中间包吸渣过滤分离器及其制备方法。
背景技术:2.连铸中间包是炼钢生产流程的中间环节,是钢夜凝固之前所经过的最后一个耐火材料容器,对提高钢质量有重要作用。中间包应尽可能排除掉钢水中的非金属夹杂物,防止钢夜吸收空气及耐火材料中的氧,避免二次氧化,以满足洁净钢的品质要求。
3.目前国内钢厂的连铸中间包内普遍都设置了挡渣墙,挡渣墙的设置不仅能改善钢水流动的轨迹,使钢水沿钢渣界面流动,缩短夹杂物上浮距离,有利于渣的吸收;而且还增加了钢水在中间包内停留时间,提高了夹杂物的分离率。但实际生产中,中间包底部存在钢水不活跃的停滞区,夹杂物上浮很困难,因此中间包内即使设置了挡渣墙,底部夹杂物仍然很难消除,导致铸坯质量还是很难得到保证。为了解决上述问题,目前国内一些钢厂在连铸中间包内除了设置传统的挡渣墙外,还在包底位置设置了吸渣过滤分离器,与挡渣墙配套使用。设置吸渣过滤分离器后,中包內钢水由吸渣过滤分离器上的通钢孔从冲击区流向浇钢区,由于减缓了钢水流动速度,所以更加延长钢水在中包內停留时间,为停滞在包底钢水中夹杂物的去除提供了更多的反应和吸附时间,能够有效提高钢水的洁净度和铸坯质量。
4.现有技术的中间包吸渣过滤分离器普遍采用等静压成型,等静压成型不仅设备昂贵,而且生产工艺比较复杂,泥料一般需要造粒和干燥,泥料装模后一般还需要抽真空,坯体一般外形不够规整需要打磨处理,热处理过程需要干燥和烧成两个环节,生产周期较长而且涉及的设备较多,投资较大。并且由于等静压成型特点,泥料极限粒径较小,高温下抗冲性能较差,导致中间包吸渣过滤分离器通钢孔扩孔较严重。
5.发明专利cn202010282507.6的专利文献公开了一种复合质中间包吸渣过滤器及生产方法,由滤筒和本体两部分复合而成,整个生产方法分成先后两步进行,第一步是制作滤筒,滤筒是等静压成型后经过预烧、还原气氛烧成而制得;第二步是制作吸渣过滤器,经过滤筒安装、浇注料浇注成型、养护、脱模、干燥等工序制作。该发明不足之处:生产工艺比较繁琐,所需设备较多,尤其需要使用等静压设备,设备投入成本较高,生产工序多,生产周期长,生产成本较高。
技术实现要素:6.本发明的目的在于提供一种振动成型的中间包吸渣过滤分离器及其制备方法,本发明通过开发一种中间包吸渣过滤分离器浇注料,混合均匀后将其浇注在模具内通过振动成型,以及合理的养生、干燥制度,制备出振动成型的中间包吸渣过滤分离器。本发明生产的中间包吸渣过滤分离器,生产场地环境要求低、生产设备简易、设备资金投入较少、生产工艺简单、生产周期短、生产效率高,产品外形好、强度大、通钢孔扩孔程度较轻且不易堵塞,通钢孔扩孔率降低30%以上,通钢孔堵塞率降低40%以上,生产成本可降低20%以上。
7.为了达到上述目的,本发明采用以下技术方案实现:
8.一种振动成型的中间包吸渣过滤分离器,所述中间包吸渣过滤分离器是由下列重量份数的原料制备而成:粒径8~0mm的废旧刚玉碳化硅砖再生料50~70份、粒径3~0mm合成镁钙砂5~20份、电熔白刚玉粉8~20份、复配氧化铝微粉2~8份、纯铝酸钙水泥3~10份、硅微粉1~6份、球状沥青2~8份、复合添加剂2~6份、高效减水剂0.1~0.6份、防爆裂纤维0.05~0.5份、不锈钢纤维0.5~3份。
9.所述的复合添加剂为金属铝粉、金属硅粉、金属铬粉中一种或几种。
10.所述的复配氧化铝微粉为活性氧化铝微粉、煅烧氧化铝微粉、双峰氧化铝微粉中一种或几种。
11.所述的高效减水剂为聚丙烯酸盐、聚羧酸盐中一种或几种。
12.所述的防爆裂纤维为长度为2mm~6mm的聚丙烯纤维。
13.所述吸渣过滤分离器通钢孔入钢口直径φ1=90mm~120mm,出钢口直径φ2=75mm~110mm,且通钢孔入钢口直径φ1大于出钢口直径φ2。
14.所述的废旧刚玉碳化硅砖中al2o3≥82%,sic≥5%。
15.浇注料中主要原料化学成分见表1;
16.表1主要原料化学成分
[0017][0018]
一种振动成型的中间包吸渣过滤分离器的制备方法,包括如下方法步骤:
[0019]
1)吸渣过滤分离器模具组装,并在模具内壁及模芯上均匀涂刷脱模油;
[0020]
2)按照吸渣过滤分离器浇注料各种原料加入比例进行浇注料配料,并将复配氧化铝微粉与复合添加剂、纯铝酸钙水泥、球状沥青、硅灰粉、高效减水剂进行预混合,制成预混粉备用;
[0021]
3)使用行星式混合机进行浇注料混练,先加入骨料、粉料,混合1~5分钟后,再加入预混粉混合1~5分钟,然后再分散加入防爆裂纤维和不锈钢纤维混合1~5分钟后,最后加水进行泥料混练3~8分钟;
[0022]
4)浇注料浇注施工,将模具放置在台式振动器上,然后将浇注料均匀加入模具内,浇注料高度达到模具高度1/4~1/3时,启动振动器设置振幅为35~50hz进行振动,然后边振动边继续在模具内布料,直至浇注料高度与模具上沿平齐,然后将振动器振幅调整为10~25hz继续振动2~5分钟,直至浇注料表面均匀返浆,充分排出气体为止;
[0023]
5)使用塑料薄膜将浇注体连同模具覆盖包裹以实现保证浇注体周围环境湿度的目的,进行第一次自然养生,养生时间3~5小时;
[0024]
6)进行中间包吸渣过滤分离器l型通钢孔模芯进行脱模;
[0025]
7)通钢孔模芯脱模后继续将模具放入养生窑内进行第二次养生,养生温度35~60℃,养生时间15~24小时;
[0026]
8)进行浇注体外侧模具脱模;
[0027]
9)将脱模后的产品继续放入养生窑内进行第三次养生,养生时间24~48小时;
[0028]
10)将养生后产品放入梭式干燥窑内进行干燥,干燥温度280~450℃,干燥时间45~65小时;
[0029]
11)出窑,包装。
[0030]
与现有技术相比,本发明的有益效果是:
[0031]
1)本发明的中间包吸渣过滤分离器采用振动成型,与传统的等静压设备成型相比,具有生产工艺简单、生产效率高、设备成本投入低、产品外形好、不需要后续机械加工等优点,生产成本可降低20%以上。
[0032]
2)本发明吸渣过滤分离器是振动成型,相比等静压成型产品,其原料种类及极限粒度可选择范围更宽,所以可以通过合适的原料选择来增强其对钢水中夹杂物的吸附过滤能力,并通过加大浇注料极限粒度等方法,来提高吸渣过滤分离器的高温强度和抗冲刷、抗侵蚀性等高温性能,有效避免了使用过程中通钢孔扩孔和堵塞现象,通钢孔扩孔率可降低40%以上,通钢孔堵塞率可降低30%以上。
[0033]
3)本发明振动成型中间包吸渣过滤分离器生产周期较短,一般生产周期为5-7天,而等静压成型生产周期较长,一般生产周期为10-12天,由于生产周期显著缩短,所以生产效率大幅提高。
[0034]
4)本发明振动成型中间包吸渣过滤分离器干燥后即可使用,而等静压产品一般干燥后还需要高温烧成,相比之下本发明能源消耗较低,不仅可以降低生产成本,还有利于节能减排,保护环境。
[0035]
5)本发明通过添加合成镁钙砂引入mgo和cao,由于游离cao可以与钢水中al2o3、s、p等夹杂物的反应生成低熔点化合物上浮到钢夜表面被覆盖剂吸收,有效减少了刚液中的夹杂物,对钢水起到净化作用。同时mgo与刚玉中al2o3反应生产原位尖晶石,极大地提高了吸渣过滤分离器高温下抗侵蚀性能和抗渗透性能,减少了钢水和耐材之间的互溶,提高钢水的洁净度。
[0036]
6)本发明采用废旧刚玉碳化硅砖再生料,不仅降低了产品的原材料成本,而且开发了废旧耐火材料的再生利用技术,符合国家循环经济、节能减排的产业政策,具有较好的经济和社会效益。
附图说明
[0037]
图1是本发明的生产工艺流程图。
[0038]
图2是本发明中间包吸渣过滤分离器的结构示意图。
[0039]
图中:1-通钢孔、2-通钢孔出钢口2、3-出钢面、4-入钢面、5-通钢孔出钢口1。
具体实施方式
[0040]
下面结合实施例对本发明的具体实施方式作进一步的说明:
[0041]
本发明的一种振动成型的中间包吸渣过滤分离器,是在组装好的模具内浇注混练均匀的浇注料,并通过振动成型、通钢孔模芯脱模、本体模具脱模、养生干燥等生产工序进行制备,生产工艺流程见图1。
[0042]
本发明在某钢铁集团公司65吨中间包和50吨中间包上分别使用,通钢孔扩孔率和堵塞率都明显降低,使用性能显著提高。
[0043]
具体实施例:
[0044]
本发明提供了一种在组装好的模具内浇注混合均匀的中间包吸渣过滤分离器浇注料,并通过振动成型、通钢孔模芯脱模、外侧模具脱模、养生干燥、包装等生产工序,制备一种振动成型的中间包吸渣过滤分离器。
[0045]
中间包吸渣过滤分离器浇注料由下述原料按重量份配比组成见表2。
[0046]
表2吸渣过滤分离器浇注料配比组成
[0047]
原料名称粒径,mm加入比例,份废旧刚玉碳化硅砖再生料8-055合成镁钙砂3-010电熔白刚玉粉 12.5复配氧化铝微粉 4纯铝酸钙水泥 6硅微灰粉 3球状沥青 4复合添加剂 3.6高效减水剂 0.2防爆裂纤维 0.2不锈钢纤维 1.5
[0048]
浇注料中主要原料化学成分见表3。
[0049]
表3主要原料化学成分
[0050][0051][0052]
浇注料中复合添加剂由金属铝粉和金属硅粉组成。
[0053]
复配氧化铝微粉有活性氧化铝微粉和煅烧氧化铝微粉组成。
[0054]
高效减水剂为聚丙烯酸钠减水剂。
[0055]
浇注料中防爆裂纤维为长度为4mm的聚丙烯纤维。
[0056]
吸渣过滤分离器通钢孔入钢口直径φ1=100mm,出钢口直径φ2=90mm。
[0057]
一种浇注成型的中间包吸渣过滤分离器,其制备过程如下:
[0058]
1)吸渣过滤分离器模具组装,并在模具内壁及模芯上均匀涂刷脱模油;
[0059]
2)按照吸渣过滤分离器浇注料各种原料加入比例进行浇注料配料,并将复配氧化铝微粉与复合添加剂、纯铝酸钙水泥、球状沥青、硅灰粉、高效减水剂进行预混合,制成预混粉备用;
[0060]
3)使用行星式混合机进行浇注料混练,先加入骨料、粉料,混合1分钟后,加入复合添加剂预混料混合2分钟,最后加入防爆裂纤维和不锈钢纤维混合3分钟后,加水进行泥料混练5分钟;
[0061]
4)浇注料浇注施工,将模具放置在台式振动器上,然后将浇注料均匀加入模具内,浇注料高度达到模具高度1/3时,启动振动器设置振幅为45hz进行振动,然后边振动边继续在模具内布料,直至浇注料高度与模具上沿平齐,然后将振动器振幅调整为15hz继续振动3分钟,直至浇注料表面均匀返浆,充分排出气体为止;
[0062]
5)使用塑料薄膜将浇注体连同模具覆盖包裹以实现保证浇注体周围环境湿度的目的,进行一次自然养生1,养生时间3.5小时;
[0063]
6)进行中间包吸渣过滤分离器l型通钢孔模芯进行脱模;
[0064]
7)通钢孔模芯脱模后继续将模具放入养生窑内进行二次养生2,养生温度45℃,养生时间20小时;
[0065]
8)进行浇注体外侧模具脱模;
[0066]
9)将脱模后的产品继续放入养生窑内进行三次养生3,养生时间30小时;
[0067]
10)将养生后产品放入梭式干燥窑内进行干燥,干燥温度320℃,干燥时间52小时;
[0068]
11)出窑,包装。一种振动成型的中间包吸渣过滤分离器制备完成。
[0069]
在某钢铁集团公司使用本实施例前、后中间包吸渣过滤分离器通钢孔扩孔率、堵塞率情况统计见表4、表5。
[0070]
表4使用本发明前后中间包吸渣过滤分离器通钢孔扩孔率情况
[0071][0072]
表5使用本发明前后中间包吸渣过滤分离器通钢堵塞率情况
[0073][0074]
本发明中间包吸渣过滤分离器采用振动成型,振动成型生产方式设备简单,设备较少且价格较低,总体投资较少,操作方便,易于维护。并且通过合理选择工艺参数和振动成型参数,便可获得密度较高且比较均匀、气孔率较低、强度较高、外形规整棱角完好的坯体,且坯体废品率低,生产效率高。采用振动成型对模具的压力和摩擦力都很小,对模具材
质材质要求不高,故模具成本较低且使用寿命较长,能够有效降低生产制造成本。
[0075]
本发明中间包吸渣过滤分离器通钢孔形状设计先进,采用入钢水口φ1和出钢水口φ2不等径的孔径设计方式,在满足中间包内钢水流场需要的前提下,将钢水入钢口φ1直径尺寸设计成比钢水流出口φ2的直径尺寸大5-20mm,此设计能够适当延长钢水在通钢孔内停留时间,为吸渣过滤分离器吸附钢水中的夹杂物提供了更加充足时间,增强了中间包吸渣过滤分离器对钢水的净化作用,提高了钢水的洁净化程度。
[0076]
本发明对生产厂房要求不严格,在简易厂房内也可生产,本发明探索了一套在厂房保湿效果不好的情况下,保证产品生产质量的有效方法,即为了给浇注体提供良好的湿度环境,本发明采用了一种简易的保湿方法,即产品振动成型后进行第一次自然养生时,使用塑料薄膜将浇注体连同模具覆盖包裹,以此营造一个恒湿环境,为浇注料中水泥硬化反应提供充足时间,保证了浇注体内部和外部硬化强度的均匀性。采用此方法进行浇注体保湿养生,不仅效果良好,而且成本较低,降低了对生产厂房环境的要求。
[0077]
本发明中通过加入刚玉碳化硅废料引入sic,碳化硅的加入可以大幅提高吸渣过滤分离器的热震稳定性、何种软化温度、耐磨性和抗侵蚀性等,有效降低了吸渣过滤分离器上通钢孔的扩孔度,大幅提高了其使用寿命。