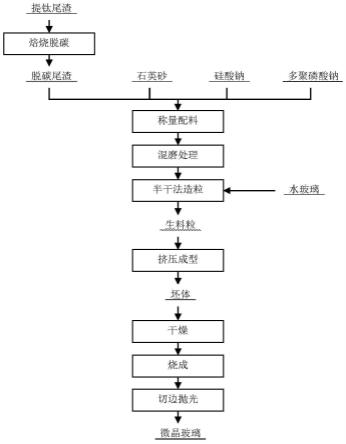
1.本发明涉及冶金固废技术领域,尤其涉及一种提钛尾渣制备微晶玻璃的方法。
背景技术:2.攀西地区每年产生含钛高炉渣700万吨以上。目前正在开展含钛高炉渣提钛工艺研究,已经建成了工程化示范线,有大量提钛尾渣产生,必须要走多途径建材资源化利用模式,才能实现整个高炉渣提钛工艺全流程绿色化、清洁化发展模式。提钛尾渣为150-400目的细粉状物料,硅(铝)钙玻璃体物相占85%以上,同时含有5~10%的tio2,软化温度1120℃,半球温度1254℃,流动温度1365℃。提钛尾渣适合作为微晶玻璃的原料使用,替代玻璃粉。同时尾渣中含有适量的钛氧化物,起到晶核剂作用,在烧成过程中可以形成枝状钙钛矿等微晶相,避免了晶核剂的另外加入。
3.微晶玻璃是指在基础玻璃中加入或者不加入晶核剂,在可控热处理的条件下,形成的一种玻璃相和微晶相共同存在的新型材料。因此,微晶玻璃既有玻璃的基本性能,又具有陶瓷的多晶特征,集中了玻璃和陶瓷的优点。目前存在利用含钛高炉渣作为主要原料开发微晶玻璃的相关技术研究,但由于制备过程要求高、产品效果不佳导致无法实现产业化应用。
4.因此,现有技术中存在对提钛尾渣制备微晶玻璃改进的技术需求。
技术实现要素:5.有鉴于此,本发明实施例的目的在于提出一种提钛尾渣制备微晶玻璃的方法,原料工艺简单,生产成本低,实现了对工业固体废物的高效资源化利用。
6.基于上述目的,本发明实施例的提供了一种提钛尾渣制备微晶玻璃的方法,该方法包括以下步骤:
7.对提钛尾渣进行高温脱碳处理以获得脱碳尾渣脱碳温度范围为600~750℃;
8.在脱碳尾渣中加入石英砂、硅酸钠、多聚磷酸钠以获得混料;
9.对混料依次进行混磨、制粒以及模压处理以获得坯体;
10.将坯体干燥后进行烧成处理,烧成处理包括梯度升温阶段、保温阶段、梯度降温阶段,对烧成后产物进行后处理以获得微晶玻璃。
11.在一些实施方式中,按重量百分比计,混料包括提钛尾渣30~40%,石英砂40~50%,硅酸钠8~10%,多聚磷酸钠3~5%。
12.在一些实施方式中,烧成处理包括:
13.(1)梯度升温阶段:以8℃/min的升温速率从室温升温至1000℃,再以5℃/min的升温速率升温至1100℃;
14.(2)保温阶段:以1100℃保温90min;
15.(3)梯度降温阶段:以10℃/min的降温速率降温至600℃,再以2℃/min的降温速率降至50℃。
16.在一些实施方式中,混磨处理为采用球磨机将混料球磨为粒度小于300目的细粉。
17.在一些实施方式中,制粒处理为采用半干法制粒工艺制备生料粒,制粒时采用水玻璃作为粘结剂,水玻璃的模数为2.0%,浓度为15%,按重量百分比计,水玻璃的添加量占混料量的4~6%。
18.在一些实施方式中,生料粒的粒度为0.2~1.0mm。
19.在一些实施方式中,模压处理的压力小于等于10mpa。
20.在一些实施方式中,坯体干燥的温度为150~300℃。
21.在一些实施方式中,后处理包括对烧成后产物进行切边、抛光以获得微晶玻璃。
22.在一些实施方式中,提钛尾渣为含钛高炉渣高温碳化-低温氯化提钛后的副产物,按重量百分比计,提钛尾渣包括氧化钙26~30%、二氧化硅24~28%、二氧化钛5~10%、三氧化二铝12~13%、氧化镁8~9%、氯离子2~4%、游离碳3~5%。
23.本发明至少具有以下有益技术效果:
24.(1)原料及工艺简单,充分利用了固废资源特点;
25.(2)采用一步法工艺,与传统两步法工艺相比能耗低,生产成本低;
26.(3)制备的微晶玻璃具有米黄色、形变小、烧成温度低、成瓷性好、强度高的特点;
27.(4)提钛尾渣利用率达到40%,开拓了提钛尾渣高值化利用途径。
附图说明
28.为了更清楚地说明本发明实施例或现有技术中的技术方案,下面将对实施例或现有技术描述中所需要使用的附图作简单地介绍,显而易见地,下面描述中的附图仅仅是本发明的一些实施例,对于本领域普通技术人员来讲,在不付出创造性劳动的前提下,还可以根据这些附图获得其他的实施例。
29.图1为本发明提供的提钛尾渣制备微晶玻璃的方法实施例的示意图。
具体实施方式
30.为使本发明的目的、技术方案和优点更加清楚明白,以下结合具体实施例,并参照附图,对本发明实施例进一步详细说明。
31.本发明的说明书和权利要求书及上述附图说明中的术语“包括”和“具有”以及它们的任何变形,意图在于覆盖不排他的包含;本发明的说明书和权利要求书或上述附图中的术语“第一”、“第二”等是用于区别不同对象,而不是用于描述特定顺序。“多个”的含义是两个或两个以上,除非另有明确具体的限定。
32.此外,在本文中提及“实施例”意味着,结合实施例描述的特定特征、结构或特性可以包含在本发明的至少一个实施例中。在说明书中的各个位置出现该短语并不一定均是指相同的实施例,也不是与其它实施例互斥的独立的或备选的实施例。本领域技术人员显式地和隐式地理解的是,本文所描述的实施例可以与其它实施例相结合。
33.提钛尾渣为深灰色细粉状物料,粒度150~400目,主要化学成分见下表所示(w%)。
34.caosio2al2o3mgotio2ccl26~3024~2812~138~95~103~52~4
35.提钛尾渣中硅(铝)钙玻璃体物相占85%以上,同时含有5~10%的tio2,软化温度1120℃,半球温度1254℃,流动温度1365℃。提钛尾渣适合作为微晶玻璃的原料使用,替代玻璃粉。同时尾渣中含有适量的钛氧化物,起到晶核剂作用,在烧成过程中可以形成枝状钙钛矿等微晶相,避免了晶核剂的另外加入。
36.如图1所示为本发明提供的一种提钛尾渣制备微晶玻璃的方法,该方法包括以下步骤:
37.(1)对提钛尾渣进行高温脱碳处理以获得脱碳尾渣;
38.(2)在脱碳尾渣中加入石英砂、硅酸钠、多聚磷酸钠以获得混料;
39.(3)对混料依次进行混磨、制粒以及模压处理以获得坯体;
40.(4)将坯体干燥后进行烧成处理,烧成处理包括梯度升温阶段、保温阶段、梯度降温阶段,对烧成后产物进行后处理以获得微晶玻璃。
41.进一步地,在步骤(1)中,脱碳温度范围控制在600-750℃,其中,当脱碳温度低于600℃,脱碳效果差,当脱碳温度超过750℃,提钛尾渣中玻璃体易转化为晶体,又称失玻,不利于烧结成型。
42.进一步地,在步骤(2)中,按重量百分比计,混料配比为提钛尾渣30~40%,石英砂40~50%,硅酸钠8~10%,多聚磷酸钠3~5%。石英砂采用天然石英砂,二氧化硅含量90%以上,硅酸钠采用工业纯,有效成分含量98%以上,多聚磷酸钠采用工业纯,有效成分含量95%以上。其中,加入硅酸钠的目的有三,其一是提供了足够的低熔点钠盐,易形成玻璃体,降低烧成温度;其二是有益补充了二氧化硅含量,控制微晶玻璃的生成物相在相图合理范围内;其三是硅酸钠本身具备塑性和粘结性能,通过添加硅酸钠,可以省去黏土的加入,同时可以作为粘结剂使用;加入多聚磷酸钠的目的有三,其一是提供了足够的低熔点钠盐,易形成玻璃体,降低烧成温度;其二是在体系中引入了磷酸盐结构体,有利于烧结制品强度结构的改善;其三是多聚磷酸钠具有分散剂作用,可以改善混料的分散及造粒效果。
43.进一步地,在步骤(3)中,采用球磨机将混料球磨为粒度小于300目的细粉;继而采用半干法制粒工艺制备生料粒,制粒时采用水玻璃作为粘结剂,水玻璃模数为2.0,浓度15%,按重量百分比计,水玻璃的添加量占混料量的4~6%,,其中,当添加量低于4%时,混料造粒性能差,挤压成型效果差,坯体强度低、易起粉;当添加量高于6%,挤压成型效果差,易粘模具,坯体强度低。在一些实施方式中,生料粒的粒度为0.2~1.0mm;继而将生料粒通入大吨位压机挤压成型,成型压力大于10mpa,形成坯体。
44.进一步地,在对坯体进行干燥时,干燥温度为150~300℃,干燥后在高温窑中烧成,烧成处理包括:
45.(1)梯度升温阶段:以8℃/min的升温速率从室温升温至1000℃,再以5℃/min的升温速率升温至1100℃;
46.(2)保温阶段:以1100℃保温90min;
47.(3)梯度降温阶段:以10℃/min的降温速率降温至600℃,该步骤为快速降温阶段,使烧结体保持较多玻璃体组分,再以2℃/min的降温速率降至50℃,该步骤为缓慢降温阶段,通过缓慢降温消除烧结体中的应力,提高烧结体的力学性能。
48.进一步地,步骤(4)中对烧成后产物进行后处理包括进行切边、抛光以获得微晶玻璃。
49.本发明的方法使用的原料及工艺简单,充分利用了固废资源特点,采用一步法工艺,生产成本低,产品性能好,提钛尾渣利用率达到40%,开拓了提钛尾渣高值化利用途径。
50.下面根据具体实施例进一步阐述本发明的具体实施方式。
51.实施例1
52.提钛尾渣30~40%,石英砂40~50%,硅酸钠8~10%,多聚磷酸钠3~5%。提钛尾渣经600~750℃热处理,渣中游离碳脱除到0.5%以下。石英砂采用天然石英砂,二氧化硅含量90%以上。硅酸钠采用工业纯,有效成分含量98%以上。多聚磷酸钠采用工业纯,有效成分含量95%以上。水玻璃模数2.0,浓度15%,添加量4~6%(占粉料重量百分比)。提钛尾渣经高温脱碳处理后,按比例配加石英砂、硅酸钠、多聚磷酸钠,进入球磨机磨制成粒度300目以下均匀细粉,采用半干法造粒工艺制成粒度0.2~1.0mm的生料粒,粘结剂采用水玻璃。生料粒通大吨位压机挤压成型,成型压力大于10mpa,形成坯体,经干燥箱中150~300℃干燥后,在高温窑中烧成,烧成温度1120℃,烧成制度如下:
53.室温~1000℃,升温速率8℃/min;
54.1000~1100℃,升温速率5℃/min;
55.1100℃,保温90min;
56.1120~600℃,降温速率10℃/min;
57.600~50℃,降温速率2℃/min;
58.烧成的微晶玻璃经切边、抛光后,形成微晶玻璃产品,使用本发明的方法制成的微晶玻璃产品的密度为2.58g/cm3,吸水率为0.5~0.8%,抗弯强度为48.5mpa,耐酸性为0.1%以及耐碱性为0.1%,该产品具有米黄色、形变小、烧结温度低、成瓷性好、强度高的特点。
59.以上是本发明公开的示例性实施例,但是应当注意,在不背离权利要求限定的本发明实施例公开的范围的前提下,可以进行多种改变和修改。根据这里描述的公开实施例的方法权利要求的功能、步骤和/或动作不需以任何特定顺序执行。此外,尽管本发明实施例公开的元素可以以个体形式描述或要求,但除非明确限制为单数,也可以理解为多个。
60.应当理解的是,在本文中使用的,除非上下文清楚地支持例外情况,单数形式“一个”旨在也包括复数形式。还应当理解的是,在本文中使用的“和/或”是指包括一个或者一个以上相关联地列出的项目的任意和所有可能组合。
61.上述本发明实施例公开实施例序号仅仅为了描述,不代表实施例的优劣。
62.所属领域的普通技术人员应当理解:以上任何实施例的讨论仅为示例性的,并非旨在暗示本发明实施例公开的范围(包括权利要求)被限于这些例子;在本发明实施例的思路下,以上实施例或者不同实施例中的技术特征之间也可以进行组合,并存在如上的本发明实施例的不同方面的许多其它变化,为了简明它们没有在细节中提供。因此,凡在本发明实施例的精神和原则之内,所做的任何省略、修改、等同替换、改进等,均应包含在本发明实施例的保护范围之内。