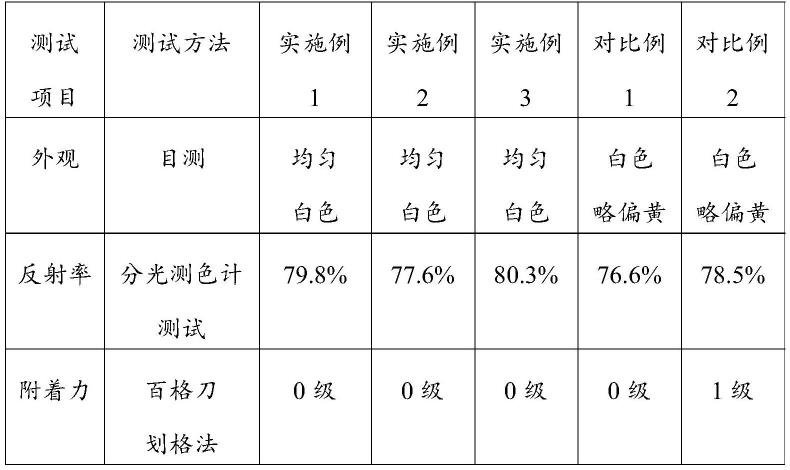
1.本发明属于油墨技术领域,具体涉及一种釉料、光伏背板玻璃及其制备方法。
背景技术:2.随着技术的进步,双玻组件逐渐进入人们的视野。双玻组件采用高反射镀釉背板玻璃代替传统的背板,高反射镀釉背板玻璃利用电池片与电池片之间的空隙进行镀釉涂白,将透过太阳能电池片间隙的太阳光反射到太阳能电池片的表面,使太阳光能够二次利用,提升双玻光伏组件对光的吸收能力,达到阻光反射提升组件功率的效果。结合perc、hjt、pert、topcon等双面电池技术,镀釉双玻组件可以实现双面发电,但没有明显的成本增加,同时在系统端实现10~30%的发电增益。因此,各组件厂商均在大规模导入网格化高反射镀釉玻璃。
3.由于光伏背板镀釉技术发展的时间较短,对于光伏组件用镀釉背板玻璃的性能标准还没有形成国家标准,目前市场对镀釉玻璃的性能要求指标主要包括反射率、附着力、耐候性、eva粘结强度、抗电势诱导衰减(pid)性能。国内针对光伏背板用白色高反射釉料研究厂家较少,目前应用的大部分光伏高反射釉料的反射率都可以做到75%以上,附着力0~1级,满足客户的基本需求。
4.但随着镀釉背板玻璃的广泛应用,最近组件厂一直有反馈镀釉背板玻璃应用过程中存在一些问题,例如镀釉背板玻璃机械载荷低,抗击异物砸落能力差,甚至容易自爆。
5.因此,提高光伏背板玻璃的抗冲击性能和反射率具有重要意义。
技术实现要素:6.目前的镀釉背板玻璃机械载荷低,抗击异物砸落能力差,甚至容易自爆。这是因为在光伏背板玻璃上丝印白色网格高反射釉料,在随玻璃钢化时镀制白色网格高反射釉料的区域与没有镀制白色高反射釉料的区域吸收的热量不同,同时目前大部分的白色高反射釉料所用玻璃熔剂膨胀系数与基材玻璃的膨胀系数不匹配,导致高反射釉层处的强度低于无釉层区,表现为整块玻璃应力不均匀及应力偏低,玻璃的平整度和弯曲度会偏大,从而使得镀釉玻璃在使用过程中抗机械载荷低,容易自爆。
7.本发明旨在至少解决上述现有技术中存在的技术问题之一。为此,本发明提出一种釉料,能够制备抗冲击性能优异的釉层,并提高光伏背板玻璃的抗冲击性能。
8.本发明还提出所述釉料的制备方法。
9.本发明还提出一种光伏背板玻璃。
10.根据本发明的一个方面,提出了一种釉料,包括以下重量份的组分:水性调墨油20~30份,颜填料30~45份,玻璃熔剂55~70份;所述玻璃熔剂在30~300℃的热膨胀系数为70
×
10-7
~80
×
10-7
/k。
11.具体地,由于光伏玻璃在30~300℃的膨胀系数一般在85
×
10-7
~91
×
10-7
/k,因此本发明设计的玻璃熔剂的热膨胀系数比光伏玻璃的膨胀系数略小,这样加上颜填料后,
使得釉料的膨胀系数会适当变大,与玻璃基材的膨胀系数就会非常匹配,使制备的釉层与玻璃基材完美结合,从而提高光伏背板玻璃的抗冲击性能。
12.在本发明的一些实施方式中,所述水性调墨油由水溶性丙烯酸树脂、分散助剂、醇、醚和水组成。
13.在本发明的一些优选的实施方式中,所述水性调墨油由水溶性丙烯酸树脂、聚乙烯醇0388(pva0388)、乙醇、乙二醇、二乙二醇单丁醚和水组成。
14.在本发明的一些优选的实施方式中,所述水性调墨油由如下重量百分比的组分组成:5~25%的水溶性丙烯酸树脂,1~5%的pva0388,10~18%的乙醇,5~20%的乙二醇,15~30%的二乙二醇单丁醚,余量为水。
15.在本发明的一些实施方式中,所述颜填料为钛白粉。
16.在本发明的一些实施方式中,所述钛白粉为金红石型钛白粉。
17.具体地,所述钛白粉为氯化法制备得到的金红石型钛白粉,且使用氧化硅和氧化铝进行无机包膜处理。该法制备的钛白粉杂质含量低,且使用氧化硅和氧化铝进行包膜处理,可堵塞二氧化钛在紫外照射条件下引起的晶格缺陷,遮蔽其表面的光活化点,提高抗电势诱导衰减(pid)性能。
18.在本发明的一些实施方式中,所述玻璃熔剂为无铅镉环保低熔点玻璃粉,粒径大小为5~10μm。
19.在本发明的一些实施方式中,所述玻璃熔剂的成分体系为硅铝硼锌锆钛系,包括氧化硅(sio2)、氧化硼(b2o3)、氧化铝(al2o3)、氧化钠(na2o)、氧化钾(k2o)、氧化锌(zno)、氧化钛(tio2)、氧化锆(zro2)。
20.在本发明的一些实施方式中,所述玻璃熔剂中,各组分的质量百分数如下:氧化硅36~45%,氧化硼18~20%,氧化铝1~5%,氧化钠8~10%,氧化钾1~5%,氧化锌12~15%,氧化钛3~5%,氧化锆1~3%。
21.在本发明的一些优选的实施方式中,所述玻璃熔剂中,所述氧化硅的质量百分数为40~45%。
22.具体地,所述氧化硅的质量百分数大于40%,会使制备的玻璃的网络结构稳定性更强,化学稳定性更好,耐水性、耐酸碱性、电绝缘性能和机械强度更好;所述氧化硅的质量百分数要小于45%,因为过高的氧化硅含量会造成软化温度、完全熔融温度偏高,从而影响制备的釉层的附着力及耐候性能。
23.在本发明的一些实施方式中,所述玻璃熔剂还包括其他组分。所述其他组分中不含铅镉。
24.在本发明的一些实施方式中,所述玻璃熔剂中的所述其他组分的质量百分数为1~3%。
25.在本发明的一些实施方式中,所述玻璃熔剂的软化温度为450~550℃。
26.具体地,软化点太低,会造成所述水性调墨油来不及完全气化,从而导致制备的釉层偏黄、偏黑,影响釉层的耐候性能。因此,所述玻璃熔剂的软化温度在上述范围内较合适。
27.在本发明的一些实施方式中,所述玻璃熔剂的完全熔融温度为600~670℃。
28.具体地,玻璃熔剂的完全熔融温度在上述范围内时,可以使所述釉料在680~720℃的钢化温度范围内短时间完全熔融。熔融流动性能更好,才能对钛白粉有更好的包覆性,
进而保证了制备的釉层的高附着力及耐候性能。
29.在本发明的一些实施方式中,所述釉料还包括分散剂和触变防沉剂。
30.在本发明的一些实施方式中,所述分散剂为润湿分散剂,选自tego dispers 735w、tego surten 404e中的至少一种。
31.在本发明的一些实施方式中,所述釉料中,所述分散剂的重量份为1~2份。
32.在本发明的一些实施方式中,所述触变防沉剂包括聚酰胺蜡、气相二氧化硅或有机膨润土中的至少一种。
33.在本发明的一些实施方式中,所述釉料中,所述触变防沉剂的重量份为1~2份。
34.在本发明的一些实施方式中,所述釉料还包括稀释剂。
35.在本发明的一些实施方式中,所述稀释剂包括二乙二醇甲醚、二乙二醇丁醚、三丙二醇甲醚、三丙二醇丁醚、二丙二醇丁醚、二丙二醇甲醚中的至少一种。
36.具体地,所述稀释剂的含量根据需要添加,不作具体限定。
37.根据本发明的第二个方面,提出了所述釉料的制备方法,包括以下步骤:
38.s1:将水性调墨油、颜填料、玻璃熔剂混合进行分散,得混合浆料;
39.s3:研磨所述混合浆料至细度<10μm,即得所述釉料。
40.在本发明的一些实施方式中,步骤s1先将所述水性调墨油与分散剂混合进行分散,得分散液;再将所述颜填料、所述玻璃熔剂和触变防沉剂加入所述分散液中进行分散,得所述混合浆料。
41.在本发明的一些实施方式中,所述颜填料为钛白粉。
42.在本发明的一些实施方式中,步骤s1所述分散的转速为500~1500rpm。
43.在本发明的一些实施方式中,步骤s1所述分散的时间为10~90min。
44.在本发明的一些实施方式中,步骤s1得到所述混合浆料后,根据需要加入稀释剂,以调节所述混合浆料的粘度为60000~100000mpa
·
s。
45.根据本发明的第三个方面,提出了一种光伏背板玻璃,所述光伏背板玻璃包括背板玻璃和设置于所述背板玻璃表面的釉层,所述釉层为将所述釉料印刷在所述背板玻璃表面形成的釉层。
46.在本发明的一些实施方式中,所述釉料经150~200目丝网印刷在所述背板玻璃表面形成所述釉层。
47.在本发明的一些实施方式中,所述釉层为对印刷在所述背板玻璃表面的所述釉料进行固化和钢化处理后得到的釉层。
48.在本发明的一些实施方式中,所述固化的温度为180~250℃。
49.在本发明的一些实施方式中,所述固化的时间为2~5min。
50.在本发明的一些实施方式中,所述钢化的温度为680~720℃。
51.经所述固化和钢化处理后,得到的所述光伏背板玻璃具有优异的抗冲击性能。
52.在本发明的一些实施方式中,所述釉料印刷在所述背板玻璃表面形成的所述釉层的厚度为15~25μm。
53.相对于现有技术,本发明的有益效果如下:
54.本发明设计的玻璃熔剂的热膨胀系数比光伏玻璃的膨胀系数略小,加上钛白粉等颜填料后,制备的釉料的膨胀系数会适当变大,与玻璃基材的膨胀系数非常匹配,使制得的
釉层与玻璃基材完美结合,从而大大提高了光伏背板玻璃的抗冲击性能。同时,本发明设计的玻璃熔剂的软化温度为450~550℃,完全熔融温度为600~670℃,使釉料在680~720℃的钢化温度范围内短时间完全熔融,熔融流动性能更好,对钛白粉有更好的包覆性,进而保证了釉层的高附着力及耐候性能。
具体实施方式
55.以下将结合实施例对本发明的构思及产生的技术效果进行清楚、完整地描述,以充分地理解本发明的目的、特征和效果。显然,所描述的实施例只是本发明的一部分实施例,而不是全部实施例,基于本发明的实施例,本领域的技术人员在不付出创造性劳动的前提下所获得的其他实施例,均属于本发明保护的范围。实施例中所使用的试验方法如无特殊说明,均为常规方法;所使用的材料、试剂等,如无特殊说明,均可从商业途径得到的试剂和材料。
56.下述实施例中采用的玻璃熔剂,包括如下质量百分数的组分:氧化硅42%,氧化硼18.3%,氧化铝4.7%,氧化钠8.8%,氧化钾2.2%,氧化锌14.6%,氧化钛4.1%,氧化锆3%,其他组分2.3%。
57.玻璃熔剂的制备方法如下:
58.(1)原料混合:按上述质量百分数,将氧化硅、氧化硼、氧化铝、氧化钠、氧化钾、氧化锌、氧化钛、氧化锆等加入混料机中混合均匀,得到混合料;
59.(2)熔炼:将步骤(1)得到的混合料放入电炉中先进行预热,预热温度为570℃,预热时间20min,预热后再加热进行熔炼得到玻璃液,加热至1050℃,熔炼60min;
60.(3)球磨:将步骤(2)得到的玻璃液进行水淬得到玻璃熔块,再放入球磨机中进行球磨,球磨时间为3h,使粉料粒径等于5μm,得到低熔点玻璃熔剂。
61.下述水性调墨油由如下重量百分比的组分组成:15%的水溶性丙烯酸树脂,3%的pva0388,15%的乙醇,10%的乙二醇,20%的二乙二醇单丁醚,余量为水。
62.实施例1
63.本实施例制备了釉料1和光伏背板玻璃1,具体过程为:
64.1.制备釉料1:
65.(1)将80g水性调墨油加入分散缸中,开启机械搅拌机,搅拌速度为500rpm,边搅拌边将4g的tego dispers 735w分散剂加入其中进行分散,分散时间为10min;
66.(2)将104g钛白粉、216g玻璃熔剂(30~300℃的热膨胀系数为75.9
×
10-7
/k)、4g聚酰胺蜡依次加入分散缸中继续于1500rpm下高速分散50min,得混合浆料;加入稀释剂二乙二醇甲醚调整混合浆料的粘度在60000mpas左右;
67.(3)将上述混合浆料倒入三辊研磨机(辊速:慢辊19.1r/min,中辊54.5r/min,快辊155.3r/min;功率:7.5kw)中扎墨,检测细度使其<10μm,即得釉料1。
68.2.制备光伏背板玻璃1:
69.将上述釉料1用200目丝网印刷在背板玻璃表面,控制形成的釉层的厚度为15μm,经250℃固化3min,再经695~700℃烧结钢化,即得光伏背板玻璃1。
70.实施例2
71.本实施例制备了釉料2和光伏背板玻璃2,具体过程为:
72.1.制备釉料2:
73.(1)将80g水性调墨油加入分散缸中,开启机械搅拌机,搅拌速度为500rpm,边搅拌边将3g的tego dispers 735w分散剂加入其中进行分散,分散时间为10min;
74.(2)将96g钛白粉、224g玻璃熔剂(30~300℃的热膨胀系数为79.6
×
10-7
/k)、5g聚酰胺蜡依次加入分散缸中继续于1500rpm下高速分散50min,得混合浆料;加入稀释剂三丙二醇甲醚调整混合浆料的粘度在80000mpas左右;
75.(3)将上述混合浆料倒入三辊研磨机(辊速:慢辊19.1r/min,中辊54.5r/min,快辊155.3r/min;功率:7.5kw)中扎墨,检测细度使其<10μm,即得釉料2。
76.2.制备光伏背板玻璃2:
77.将上述釉料2用200目丝网印刷在背板玻璃表面,控制形成的釉层的厚度为25μm,经250℃固化3min,再经700~705℃烧结钢化,即得光伏背板玻璃2。
78.实施例3
79.本实施例制备了釉料3和光伏背板玻璃3,具体过程为:
80.1.制备釉料3:
81.(1)将80g水性调墨油加入分散缸中,开启机械搅拌机,搅拌速度为500rpm,边搅拌边将5g的tego dispers 735w分散剂加入其中进行分散,分散时间为10min;
82.(2)将112g钛白粉、208g玻璃熔剂(30~300℃的热膨胀系数为70.4
×
10-7
/k)、3g聚酰胺蜡依次加入分散缸中继续于1500rpm下高速分散50min,得混合浆料;加入稀释剂二乙二醇丁醚调整混合浆料的粘度在75000mpas左右;
83.(3)将上述混合浆料倒入三辊研磨机(辊速:慢辊19.1r/min,中辊54.5r/min,快辊155.3r/min;功率:7.5kw)中扎墨,检测细度使其<10μm,即得釉料3。
84.2.制备光伏背板玻璃3:
85.将上述釉料3用200目丝网印刷在背板玻璃表面,控制形成的釉层的厚度为20μm,经250℃固化3min,再经705~710℃烧结钢化,即得光伏背板玻璃3。
86.对比例1
87.本对比例制备了釉料a和光伏背板玻璃a,与实施例2的区别在于,对比例1中选用了玻璃熔剂d245,在30~300℃的热膨胀系数为110
×
10-7
/k。具体过程为:
88.1.制备釉料a:
89.(1)将80g水性调墨油加入分散缸中,开启机械搅拌机,搅拌速度为500rpm,边搅拌边将3g的tego dispers 735w分散剂加入其中进行分散,分散时间为10min;
90.(2)将128g钛白粉、192g玻璃熔剂d245(30~300℃的热膨胀系数为110
×
10-7
/k)、5g聚酰胺蜡依次加入分散缸中继续于1500rpm下高速分散50min,得混合浆料;加入稀释剂三丙二醇甲醚调整混合浆料的粘度在80000mpas左右;
91.(3)将上述混合浆料倒入三辊研磨机(辊速:慢辊19.1r/min,中辊54.5r/min,快辊155.3r/min;功率:7.5kw)中扎墨,检测细度使其<10μm,即得釉料a。
92.2.制备光伏背板玻璃a:
93.将上述釉料a用200目丝网印刷在背板玻璃表面,控制形成的釉层的厚度为25μm,经250℃固化3min,再经690~695℃烧结钢化,即得光伏背板玻璃a。
94.对比例2
95.本对比例制备了釉料b和光伏背板玻璃b,与实施例2的区别在于,对比例2中选用了玻璃熔剂d255,在30~300℃的热膨胀系数为95
×
10-7
/k。具体过程为:
96.1.制备釉料b:
97.(1)将80g水性调墨油加入分散缸中,开启机械搅拌机,搅拌速度为500rpm,边搅拌边将3g的tego dispers 735w分散剂加入其中进行分散,分散时间为10min;
98.(2)将120g钛白粉、200g玻璃熔剂d255(30~300℃的热膨胀系数为95
×
10-7
/k)、5g聚酰胺蜡依次加入分散缸中继续于1500rpm下高速分散50min,得混合浆料;加入稀释剂三丙二醇甲醚调整混合浆料的粘度在80000mpas左右;
99.(3)将上述混合浆料倒入三辊研磨机(辊速:慢辊19.1r/min,中辊54.5r/min,快辊155.3r/min;功率:7.5kw)中扎墨,检测细度使其<10μm,即得釉料b。
100.2.制备光伏背板玻璃b:
101.将上述釉料b用200目丝网印刷在背板玻璃表面,控制形成的釉层的厚度为25μm,经250℃固化3min,再经690~695℃烧结钢化,即得光伏背板玻璃b。
102.试验例
103.本试验例测试了实施例1~3和对比例1~2制备的光伏背板玻璃的性能。其中:
104.反射率采用konica minolta的分光测色计cm-26dg/26d/25d测试。
105.附着力采用szzw-bgd-001的百格刀,参照标准gb/t 9286测试。
106.抗冲击强度采用227g钢球砸非丝网印刷面釉条交叉点进行测试,参照标准《gb/t34328-2017轻质物理强化玻璃》执行。
107.测试结果如表1所示。
108.表1
109.[0110][0111]
从表1可以看出,在进行抗冲击强度测试时,实施例1~3的釉条在800mm或900mm时才会破裂,而对比例1和2的釉条在300mm或400mm时就会破裂,即实施例1~3的光伏背板玻璃的抗冲击强度显著大于对比例1和2的光伏背板玻璃的抗冲击强度,显示本发明制备的光伏背板玻璃具有优异的抗冲击性能。这是由于本发明实施例制备釉料时使用的玻璃熔剂在30~300℃的热膨胀系数在70
×
10-7
~80
×
10-7
/k之间,比背板玻璃的膨胀系数略小,加上钛白粉等颜填料后,使得釉料的热膨胀系数适当变大,与背板玻璃的膨胀系数非常匹配,使制备的釉层与背板玻璃完美结合,从而提高了光伏背板玻璃的抗冲击性能。而对比例1和2制备釉料时使用的玻璃熔剂的热膨胀系数大于本发明中玻璃熔剂的热膨胀系数,使得釉料的热膨胀系数与背板玻璃的膨胀系数不匹配,导致制备的釉层与背板玻璃不能很好地结合,从而使得光伏背板玻璃的抗冲击性能较差。
[0112]
上面对本发明实施例作了详细说明,但是本发明不限于上述实施例,在所属技术领域普通技术人员所具备的知识范围内,还可以在不脱离本发明宗旨的前提下作出各种变化。此外,在不冲突的情况下,本发明的实施例及实施例中的特征可以相互组合。