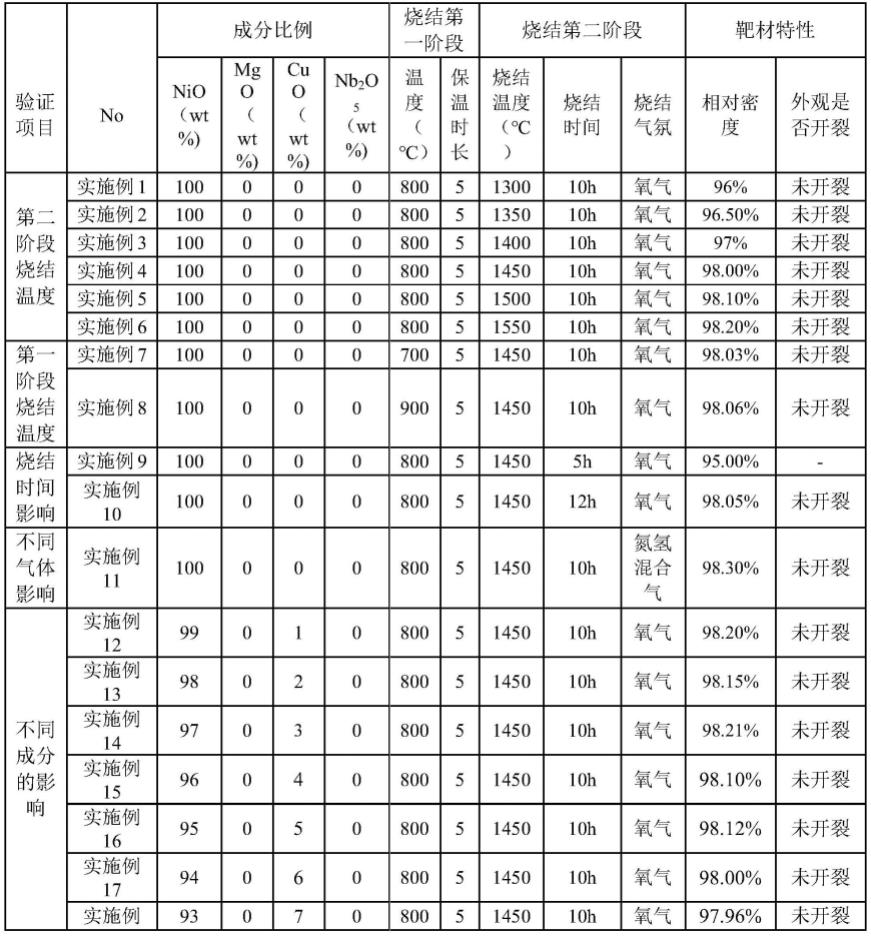
1.本发明涉及氧化物靶材技术领域,尤其是涉及一种氧化镍基靶材的制备方法与应用。
背景技术:2.相关技术中,为实现有机无机杂化钙钛矿太阳电池的光电转换效率迅速提升,大部分高性能器件都需要高质量的电子传输层和空穴传输层分别对光吸收层钙钛矿产生的电子和空穴进行有效传输。无机传输层材料由于具有高载流子迁移率和高稳定性等优势受到了广泛的关注,氧化镍料作为一种无机空穴传输层材料,具有载流子迁移率高,稳定性好,光学透过率高,功函数与钙钛矿能级相对匹配以及制备方法简单等优势。氧化镍空穴传输层多被用在p-i-n型平面钙钛矿太阳电池中,但氧化镍基钙钛矿太阳电池的光电转换效率相对于pedot:pss基钙钛矿太阳电池仍然较低,主要原因是氧化镍薄膜导电性不高,同时采用旋涂或溶胶凝胶等低温成膜方式使得氧化镍衬底与钙钛矿薄膜的界面接触较差以及氧化镍衬底上生长的钙钛矿薄膜结晶性和质量较差。
3.针对基于氧化镍空穴传输层的p-i-n型钙钛矿太阳电池开路电压和短路电流较低的问题,相关技术中通常采用离子掺杂或调节nio中的镍/氧比的方法来改善nio的电学性能,氧含量的改变可以使nio中的镍/氧比发生变化,一个ni
2+
空位可以产生两个ni
3+
离子,而ni
3+
离子的形成则决定了nio的p型特性,通过物理气相沉积(pvd)低温成膜可获得结晶性好,与钙钛矿薄膜的界面接触好的氧化镍薄膜,并通过退火过程中的调整氧含量对于提高倒置钙钛矿太阳能电池效率具有重要的意义。然而,由于氧化镍存在多种分子式,不同的分子式的氧含量存在差异,且各种不同的成分的密度存在差异,在烧结过程中,如果存在成分变化,则会造成烧结后的靶材开裂,从而无法得到满足磁控溅射的靶材的要求。
4.因此,亟需寻求一种氧化镍基靶材,其具有较好的烧结密度,且在烧结后靶材不易开裂。
技术实现要素:5.本发明旨在至少解决现有技术中存在的技术问题之一。为此,本发明提出了一种氧化镍基靶材的制备方法与应用,能够解决靶材在冷却后易出现开裂的问题。
6.本发明还提出一种氧化镍基靶材。
7.本发明还提出上述氧化镍基靶材在制备钙钛矿太阳能电池中的应用。
8.本发明的第一方面,提供一种氧化镍基靶材的制备方法,包括以下制备步骤:
9.步骤s1、将氧化镍基粉末材料、分散剂、粘结剂和水制成浆料,经喷雾造粒后得到球型氧化镍基颗粒;
10.步骤s2、将所述球型氧化镍基颗粒进行模压成型、冷等静压后得毛坯靶材;
11.步骤s3、将所述毛坯靶材进行脱胶处理,然后经分段烧结后降温即得。
12.根据本发明实施例的钙钛矿太阳能电池用氧化镍基靶材的制备方法,至少具有如
下有益效果:本发明通过采用分段烧结方法解决了氧化镍基靶材在烧结后降温过程中易开裂的技术问题,本发明的氧化镍基靶材制备方法简单,易于工业化生产。
13.在本发明的一些实施方式中,步骤s1中,所述浆料的d
50
小于250nm。
14.在本发明的一些实施方式中,步骤s1中,所述浆料的d
90
小于500nm。
15.在本发明的一些实施方式中,步骤s1中,所述球型氧化镍基颗粒的d
50
小于25μm。
16.在本发明的一些实施方式中,步骤s1中,所述球型氧化镍基颗粒的d
90
小于48μm。
17.在本发明的一些实施方式中,步骤s1中,所述球型氧化镍基颗粒的d
50
小于25μm。
18.在本发明的一些实施方式中,步骤s1中,所述球型氧化镍基颗粒的d
90
小于48μm。
19.在本发明的一些实施方式中,步骤s1中,所述氧化镍基粉末材料还掺杂了氧化镁、氧化铜和氧化铌中的至少一种氧化物。
20.在本发明的一些实施方式中,步骤s1中,所述氧化物镍基粉末材料中,氧化镍的质量分数不小于90%。
21.在本发明的一些实施方式中,步骤s1中,所述分散剂为日本中京油脂celuna d-305。
22.在本发明的一些实施方式中,步骤s1中,所述浆料中分散剂的质量百分比为0.5%~1%。
23.在本发明的一些实施方式中,步骤s1中,所述粘结剂为聚乙烯乙酸酯。
24.在本发明的一些实施方式中,步骤s1中,所述浆料中粘结剂的质量百分比为1.5%~3%。
25.在本发明的一些实施方式中,步骤s2中,所述模压成型的压力为0.1mpa~0.8mpa。
26.在本发明的一些实施方式中,步骤s2中,所述冷等静压的压力为250mpa~300mpa。
27.在本发明的一些实施方式中,步骤s3中,所述脱胶的温度为400℃~500℃。
28.在本发明的一些实施方式中,步骤s3中,所述分段烧结包括第一阶段烧结和第二阶段烧结,其中:
29.所述第一阶段烧结的烧结温度为700℃~900℃,保温时长为5h~10h,真空度为0.08mpa~0.1mpa;
30.所述第二阶段烧结的烧结温度为1300℃~1500℃,烧结时间为5h~12h,并在到达第二阶段烧结温度后的0.8~1.2h后通入氧气或氮氢混合气。
31.在本发明中,延迟通入氧气或氮氢混合气的时间有利于提高烧结质量。
32.在本发明的一些实施方式中,所述第二阶段烧结的烧结压力为0.05mpa~0.1mpa。
33.在本发明的一些实施方式中,所述第一阶段烧结的烧结温度升至所述第二阶段的烧结温度时的升温速率为0.5℃/min~1.5℃/min。
34.在本发明中,第一阶段的烧结温度升至第二阶段的烧结温度时的升温速率太高也会影响靶材的质量,有导致靶材开裂的风险。
35.在本发明的一些实施方式中,所述氮氢混合气中氮气与氢气的体积比为98~100:2。
36.优选地,所述氮氢混合气中氮气与氢气的体积比为98:2。
37.在烧结过程中通入氧气或氮氢混合气的目的是控制成分不发生变化,当通入氧气时,靶材成分可以维持富氧状态,即全是ni2o3的成分,不会产生缺氧成分的存在,即不会造
成靶材不同成分的密度差,也就不会产生开裂的情况;当通入氮氢混合气体(n2/h2=98/2wt%)时,靶材成分处于缺氧状态,成分全是nio,即不存在富氧成分,因此也不会造成靶材不同成分的密度差,进而也不会产生开裂的情况。
38.在本发明的一些实施方式中,步骤s3中,所述降温的过程中的压力为0.1mpa~0.5mpa。
39.在本发明的一些实施方式中,步骤s3中,所述降温的过程中的气氛为氧气或氮氢混合气;
40.优选地,所述氮氢混合气中氮气与氢气的体积比为98:2。
41.在降温过程中氧气或氮氢混合气可作为保护气体,有利于降低靶材开裂。
42.本发明的第二方面,提供一种氧化镍基靶材,其采用上述制备方法制得。
43.根据本发明实施例的氧化镍基靶材,至少具有如下有益效果:采用本发明制备方法获得的氧化镍基靶材相对密度高(大于95%),且不易开裂,可广泛应用于太阳能电池的制备。
44.本发明的第三方面,提供一种氧化镍基靶材在制备钙钛矿太阳能电池中的应用。
45.将本发明制得的氧化镍基靶材应用于钙钛矿太阳能电池中,有利于提高光电转化效果。
46.本发明的其它特征和优点将在随后的说明书中阐述,并且,部分地从说明书中变得显而易见,或者通过实施本发明而了解。
具体实施方式
47.以下将结合实施例对本发明的构思及产生的技术效果进行清楚、完整地描述,以充分地理解本发明的目的、特征和效果。显然,所描述的实施例只是本发明的一部分实施例,而不是全部实施例,基于本发明的实施例,本领域的技术人员在不付出创造性劳动的前提下所获得的其他实施例,均属于本发明保护的范围。
48.本发明的描述中,参考术语“一个实施例”、“一些实施例”、“示意性实施例”、“示例”、“具体示例”、或“一些示例”等的描述意指结合该实施例或示例描述的具体特征、结构、材料或者特点包含于本发明的至少一个实施例或示例中。在本说明书中,对上述术语的示意性表述不一定指的是相同的实施例或示例。而且,描述的具体特征、结构、材料或者特点可以在任何的一个或多个实施例或示例中以合适的方式结合。
49.在本发明实施方式中,分散剂为中京油脂celunad-305,有效成分含量40wt%,粘度(25℃)为50cps。
50.粘结剂为国药集团化学试剂有限公司生产的分析纯pva。
51.在本发明实施方式中未注明具体条件者,按照常规条件或制造商建议的条件进行。所用试剂或仪器未注明生产厂商者,均为可以通过市售购买获得的常规产品。
52.在本发明实施方式中钙钛矿太阳能电池用氧化镍基靶材的制备方法如下:
53.(1)按照比例称取氧化粉体材料、去离子水、分散剂、粘结剂和球磨用氧化锆球进行研磨处理,研磨时间为6~10h,研磨至浆料的d
50
小于250nm,d
90
小于500nm,然后将所得浆料进行喷雾造粒,得到d
50
小于25μm,d
90
小于48μm的球型氧化镍基颗粒。
54.(2)将球型氧化镍基颗粒在0.1mpa~0.8mpa的压力下进行模压成型,并对其进行
压力为250mpa~300mpa的冷等静压,得到毛坯靶材。
55.(3)将上述毛坯靶材置于400℃~500℃下进行脱胶处理,然后进行分段烧结,其中第一阶段的烧结温度为700℃~900℃,保温时长为5h~10h,真空度为0.08mpa~0.1mpa;第二阶段的烧结温度为1300℃~1500℃,烧结时间为5h~12h,烧结气氛为氧气或氮氢混合气;
56.第一阶段的烧结温度和第二阶段的烧结温度中间升温速率为0.5℃/min~1.5℃/min,烧结完成后保持气氛压力降温至室温,即得钙钛矿太阳能电池用氧化镍基靶材。
57.实施例1
58.一种氧化镍基靶材,其制备方法包括以下步骤:
59.(1)氧化镍基颗粒的制备:称取氧化镍基粉体材料(表面积为7m2/g~10m2/g)、去离子水、分散剂、粘结剂和球磨用氧化锆球进行球磨处理,其中氧化镍基粉体材料为氧化镍粉末,占比为20%;球磨用氧化锆球(粒径为0.5mm)占比50%,去离子水占比28%,分散剂占比0.5%,粘结剂占比1.5%。在砂磨机中研磨8h,直至浆料的d
50
小于250nm,d
90
小于500nm,将得到的浆料在喷雾塔中进行喷雾,得到d
50
小于25μm,d
90
小于48μm的球型氧化镍颗粒。
60.(2)毛坯靶材的制备:将上述所得的球型氧化镍颗粒在压力0.1mpa~0.8mpa的压力下进行模压成型,并对其进行压力为300mpa的冷等静压,得到毛坯靶材;
61.(3)脱胶烧结处理:将上述毛坯靶材置于450℃下进行脱胶处理,然后进行分段烧结,其中第一阶段烧结的烧结温度为800℃,保温时长为5h,真空度为0.09mpa;第一阶段烧结完成后,以1℃/min升温速率升温至第二阶段的烧结温度1300℃,在到达第二阶段烧结温度时1h后通入氧气,维持烧结压力在0.05mpa~0.1mpa之间,并继续烧结,第二阶段总烧结时间为10h,烧结完成后保持气氛压力(氧气,0~0.5mpa)降温至室温,即得氧化镍基靶材。
62.采用阿基米德法对上述氧化镍基靶材进行了相对密度测定,结果表明其相对密度为96%,外观无开裂现象。
63.实施例2
64.本实施例制备了一种氧化镍基靶材,与实施例1的差异在于:步骤(3)中第二阶段的烧结温度为1350℃。
65.采用阿基米德法对本实施例制得的氧化镍基靶材进行了相对密度测定,结果表明其相对密度为96.5%,外观无开裂现象。
66.实施例3
67.本实施例制备了一种氧化镍基靶材,与实施例1的差异在于:步骤(3)中第二阶段的烧结温度为1400℃。
68.采用阿基米德法对本实施例制得的氧化镍基靶材进行了相对密度测定,结果表明其相对密度为97%,外观无开裂现象。
69.实施例4
70.本实施例制备了一种氧化镍基靶材,与实施例1的差异在于:步骤(3)中第二阶段的烧结温度为1450℃。
71.采用阿基米德法对本实施例制得的氧化镍基靶材进行了相对密度测定,结果表明其相对密度为98%,外观无开裂现象。
72.实施例5
73.本实施例制备了一种氧化镍基靶材,与实施例1的差异在于:步骤(3)中第二阶段的烧结温度为1500℃。
74.采用阿基米德法对本实施例制得的氧化镍基靶材进行了相对密度测定,结果表明其相对密度为98.1%,外观无开裂现象。
75.实施例6
76.本实施例制备了一种氧化镍基靶材,与实施例1的差异在于:步骤(3)中第二阶段的烧结温度为1550℃。
77.采用阿基米德法对本实施例制得的氧化镍基靶材进行了相对密度测定,结果表明其相对密度为98.2%,外观无开裂现象。
78.实施例7
79.本实施例制备了一种氧化镍基靶材,与实施例4的差异在于:步骤(3)中第一阶段的烧结温度为700℃。
80.采用阿基米德法对本实施例制得的氧化镍基靶材进行了相对密度测定,结果表明其相对密度为98.03%,外观无开裂现象。
81.实施例8
82.本实施例制备了一种氧化镍基靶材,与实施例4的差异在于:步骤(3)中第一阶段的烧结温度为900℃。
83.采用阿基米德法对本实施例制得的氧化镍基靶材进行了相对密度测定,结果表明其相对密度为98.06%,外观无开裂现象。
84.实施例9
85.本实施例制备了一种氧化镍基靶材,与实施例4的差异在于:步骤(3)中第二阶段的烧结时间为5h。
86.采用阿基米德法对本实施例制得的氧化镍基靶材进行了相对密度测定,结果表明其相对密度为95%,外观无开裂现象。
87.实施例10
88.本实施例制备了一种氧化镍基靶材,与实施例4的差异在于:步骤(3)中第二阶段的烧结时间为12h。
89.采用阿基米德法对本实施例制得的氧化镍基靶材进行了相对密度测定,结果表明其相对密度为98.05%,外观无开裂现象。
90.实施例11
91.本实施例制备了一种氧化镍基靶材,与实施例4的差异在于:步骤(3)中第二阶段的烧结气氛为氮氢混合气体。
92.采用阿基米德法对本实施例制得的氧化镍基靶材进行了相对密度测定,结果表明其相对密度为98.3%,外观无开裂现象。
93.实施例12
94.本实施例制备了一种氧化镍基靶材,与实施例4的差异在于:步骤(1)中的氧化镍基粉体材料为bet在7m2/g~10m2/g的氧化镍粉体与bet在7m2/g~10m2/g的氧化镁粉体,其中氧化镍粉体与氧化镁粉体的重量比为99:1。
95.采用阿基米德法对本实施例制得的氧化镍基靶材进行了相对密度测定,结果表明
其相对密度为98.2%,外观无开裂现象。
96.实施例13
97.本实施例制备了一种氧化镍基靶材,与实施例4的差异在于:步骤(1)中的氧化镍基粉体材料为bet在7m2/g~10m2/g的氧化镍粉体与bet在7m2/g~10m2/g的氧化镁粉体,其中氧化镍粉体与氧化镁粉体的重量比为98:2。
98.采用阿基米德法对本实施例制得的氧化镍基靶材进行了相对密度测定,结果表明其相对密度为98.15%,外观无开裂现象。
99.实施例14
100.本实施例制备了一种氧化镍基靶材,与实施例4的差异在于:步骤(1)中的氧化镍基粉体材料为bet在7m2/g~10m2/g的氧化镍粉体与bet在7m2/g~10m2/g的氧化镁粉体,其中氧化镍粉体与氧化镁粉体的重量比为97:3。
101.采用阿基米德法对本实施例制得的氧化镍基靶材进行了相对密度测定,结果表明其相对密度为98.21%,外观无开裂现象。
102.实施例15
103.本实施例制备了一种氧化镍基靶材,与实施例4的差异在于:步骤(1)中的氧化镍基粉体材料为bet在7m2/g~10m2/g的氧化镍粉体与bet在7m2/g~10m2/g的氧化镁粉体,其中氧化镍粉体与氧化镁粉体的重量比为96:4。
104.采用阿基米德法对本实施例制得的氧化镍基靶材进行了相对密度测定,结果表明其相对密度为98.10%,外观无开裂现象。
105.实施例16
106.本实施例制备了一种氧化镍基靶材,与实施例4的差异在于:步骤(1)中的氧化镍基粉体材料为bet在7m2/g~10m2/g的氧化镍粉体与bet在7m2/g~10m2/g的氧化镁粉体,其中氧化镍粉体与氧化镁粉体的重量比为95:5。
107.采用阿基米德法对本实施例制得的氧化镍基靶材进行了相对密度测定,结果表明其相对密度为98.12%,外观无开裂现象。
108.实施例17
109.本实施例制备了一种氧化镍基靶材,与实施例4的差异在于:步骤(1)中的氧化镍基粉体材料为bet在7m2/g~10m2/g的氧化镍粉体与bet在7m2/g~10m2/g的氧化镁粉体,其中氧化镍粉体与氧化镁粉体的重量比为94:6。
110.采用阿基米德法对本实施例制得的氧化镍基靶材进行了相对密度测定,结果表明其相对密度为98%,外观无开裂现象。
111.实施例18
112.本实施例制备了一种氧化镍基靶材,与实施例4的差异在于:步骤(1)中的氧化镍基粉体材料为bet在7m2/g~10m2/g的氧化镍粉体与bet在7m2/g~10m2/g的氧化镁粉体,其中氧化镍粉体与氧化镁粉体的重量比为93:7。
113.采用阿基米德法对本实施例制得的氧化镍基靶材进行了相对密度测定,结果表明其相对密度为97.96%,外观无开裂现象。
114.实施例19
115.本实施例制备了一种氧化镍基靶材,与实施例4的差异在于:步骤(1)中的氧化镍
基粉体材料为bet在7m2/g~10m2/g的氧化镍粉体与bet在7m2/g~10m2/g的氧化镁粉体,其中氧化镍粉体与氧化镁粉体的重量比为92:8。
116.采用阿基米德法对本实施例制得的氧化镍基靶材进行了相对密度测定,结果表明其相对密度为98.07%,外观无开裂现象。
117.实施例20
118.本实施例制备了一种氧化镍基靶材,与实施例4的差异在于:步骤(1)中的氧化镍基粉体材料为bet在7m2/g~10m2/g的氧化镍粉体与bet在7m2/g~10m2/g的氧化镁粉体,其中氧化镍粉体与氧化镁粉体的重量比为91:9。
119.采用阿基米德法对本实施例制得的氧化镍基靶材进行了相对密度测定,结果表明其相对密度为98.09%,外观无开裂现象。
120.实施例21
121.本实施例制备了一种氧化镍基靶材,与实施例4的差异在于:步骤(1)中的氧化镍基粉体材料为bet在7m2/g~10m2/g的氧化镍粉体与bet在7m2/g~10m2/g的氧化镁粉体,其中氧化镍粉体与氧化镁粉体的重量比为90:10。
122.采用阿基米德法对本实施例制得的氧化镍基靶材进行了相对密度测定,结果表明其相对密度为98.12%,外观无开裂现象。
123.实施例22
124.本实施例制备了一种氧化镍基靶材,与实施例4的差异在于:步骤(1)中的氧化镍基粉体材料为bet在7m2/g~10m2/g的氧化镍粉体与bet在7m2/g~10m2/g的氧化铜粉体,其中氧化镍粉体与氧化铜粉体的重量比为99:1。
125.采用阿基米德法对本实施例制得的氧化镍基靶材进行了相对密度测定,结果表明其相对密度为98.01%,外观无开裂现象。
126.实施例23
127.本实施例制备了一种氧化镍基靶材,与实施例4的差异在于:步骤(1)中的氧化镍基粉体材料为bet在7m2/g~10m2/g的氧化镍粉体与bet在7m2/g~10m2/g的氧化铜粉体,其中氧化镍粉体与氧化铜粉体的重量比为98:2。
128.采用阿基米德法对本实施例制得的氧化镍基靶材进行了相对密度测定,结果表明其相对密度为98.12%,外观无开裂现象。
129.实施例24
130.本实施例制备了一种氧化镍基靶材,与实施例4的差异在于:步骤(1)中的氧化镍基粉体材料为bet在7m2/g~10m2/g的氧化镍粉体与bet在7m2/g~10m2/g的氧化铜粉体,其中氧化镍粉体与氧化铜粉体的重量比为97:3。
131.采用阿基米德法对本实施例制得的氧化镍基靶材进行了相对密度测定,结果表明其相对密度为98.10%,外观无开裂现象。
132.实施例25
133.本实施例制备了一种氧化镍基靶材,与实施例4的差异在于:步骤(1)中的氧化镍基粉体材料为bet在7m2/g~10m2/g的氧化镍粉体与bet在7m2/g~10m2/g的氧化铜粉体,其中氧化镍粉体与氧化铜粉体的重量比为96:4。
134.采用阿基米德法对本实施例制得的氧化镍基靶材进行了相对密度测定,结果表明
其相对密度为98.14%,外观无开裂现象。
135.实施例26
136.本实施例制备了一种氧化镍基靶材,与实施例4的差异在于:步骤(1)中的氧化镍基粉体材料为bet在7m2/g~10m2/g的氧化镍粉体与bet在7m2/g~10m2/g的氧化铜粉体,其中氧化镍粉体与氧化铜粉体的重量比为95:5。
137.采用阿基米德法对本实施例制得的氧化镍基靶材进行了相对密度测定,结果表明其相对密度为98.02%,外观无开裂现象。
138.实施例27
139.本实施例制备了一种氧化镍基靶材,与实施例4的差异在于:步骤(1)中的氧化镍基粉体材料为bet在7m2/g~10m2/g的氧化镍粉体与bet在7m2/g~10m2/g的氧化铜粉体,其中氧化镍粉体与氧化铜粉体的重量比为94:6。
140.采用阿基米德法对本实施例制得的氧化镍基靶材进行了相对密度测定,结果表明其相对密度为98.09%,外观无开裂现象。
141.实施例28
142.本实施例制备了一种氧化镍基靶材,与实施例4的差异在于:步骤(1)中的氧化镍基粉体材料为bet在7m2/g~10m2/g的氧化镍粉体与bet在7m2/g~10m2/g的氧化铜粉体,其中氧化镍粉体与氧化铜粉体的重量比为93:7。
143.采用阿基米德法对本实施例制得的氧化镍基靶材进行了相对密度测定,结果表明其相对密度为97.99%,外观无开裂现象。
144.实施例29
145.本实施例制备了一种氧化镍基靶材,与实施例4的差异在于:步骤(1)中的氧化镍基粉体材料为bet在7m2/g~10m2/g的氧化镍粉体与bet在7m2/g~10m2/g的氧化铜粉体,其中氧化镍粉体与氧化铜粉体的重量比为92:8。
146.采用阿基米德法对本实施例制得的氧化镍基靶材进行了相对密度测定,结果表明其相对密度为98.02%,外观无开裂现象。
147.实施例30
148.本实施例制备了一种氧化镍基靶材,与实施例4的差异在于:步骤(1)中的氧化镍基粉体材料为bet在7m2/g~10m2/g的氧化镍粉体与bet在7m2/g~10m2/g的氧化铜粉体,其中氧化镍粉体与氧化铜粉体的重量比为91:9。
149.采用阿基米德法对本实施例制得的氧化镍基靶材进行了相对密度测定,结果表明其相对密度为98.14%,外观无开裂现象。
150.实施例31
151.本实施例制备了一种氧化镍基靶材,与实施例4的差异在于:步骤(1)中的氧化镍基粉体材料为bet在7m2/g~10m2/g的氧化镍粉体与bet在7m2/g~10m2/g的氧化铜粉体,其中氧化镍粉体与氧化铜粉体的重量比为90:10。
152.采用阿基米德法对本实施例制得的氧化镍基靶材进行了相对密度测定,结果表明其相对密度为98.09%,外观无开裂现象。
153.实施例32
154.本实施例制备了一种氧化镍基靶材,与实施例4的差异在于:步骤(1)中的氧化镍
基粉体材料为bet在7m2/g~10m2/g的氧化镍粉体与bet在7m2/g~10m2/g的氧化铌粉体,其中氧化镍粉体与氧化铌粉体的重量比为99:1。
155.采用阿基米德法对本实施例制得的氧化镍基靶材进行了相对密度测定,结果表明其相对密度为98%,外观无开裂现象。
156.实施例33
157.本实施例制备了一种氧化镍基靶材,与实施例4的差异在于:步骤(1)中的氧化镍基粉体材料为bet在7m2/g~10m2/g的氧化镍粉体与bet在7m2/g~10m2/g的氧化铌粉体,其中氧化镍粉体与氧化铌粉体的重量比为98:2。
158.采用阿基米德法对本实施例制得的氧化镍基靶材进行了相对密度测定,结果表明其相对密度为98.50%,外观无开裂现象。
159.实施例34
160.本实施例制备了一种氧化镍基靶材,与实施例4的差异在于:步骤(1)中的氧化镍基粉体材料为bet在7m2/g~10m2/g的氧化镍粉体与bet在7m2/g~10m2/g的氧化铌粉体,其中氧化镍粉体与氧化铌粉体的重量比为97:3。
161.采用阿基米德法对本实施例制得的氧化镍基靶材进行了相对密度测定,结果表明其相对密度为98.10%,外观无开裂现象。
162.实施例35
163.本实施例制备了一种氧化镍基靶材,与实施例4的差异在于:步骤(1)中的氧化镍基粉体材料为bet在7m2/g~10m2/g的氧化镍粉体与bet在7m2/g~10m2/g的氧化铌粉体,其中氧化镍粉体与氧化铌粉体的重量比为96:4。
164.采用阿基米德法对本实施例制得的氧化镍基靶材进行了相对密度测定,结果表明其相对密度为98.07%,外观无开裂现象。
165.实施例36
166.本实施例制备了一种氧化镍基靶材,与实施例4的差异在于:步骤(1)中的氧化镍基粉体材料为bet在7m2/g~10m2/g的氧化镍粉体与bet在7m2/g~10m2/g的氧化铌粉体,其中氧化镍粉体与氧化铌粉体的重量比为95:5。
167.采用阿基米德法对本实施例制得的氧化镍基靶材进行了相对密度测定,结果表明其相对密度为98.20%,外观无开裂现象。
168.实施例37
169.本实施例制备了一种氧化镍基靶材,与实施例4的差异在于:步骤(1)中的氧化镍基粉体材料为bet在7m2/g~10m2/g的氧化镍粉体与bet在7m2/g~10m2/g的氧化铌粉体,其中氧化镍粉体与氧化铌粉体的重量比为94:6。
170.采用阿基米德法对本实施例制得的氧化镍基靶材进行了相对密度测定,结果表明其相对密度为97.89%,外观无开裂现象。
171.实施例38
172.本实施例制备了一种氧化镍基靶材,与实施例4的差异在于:步骤(1)中的氧化镍基粉体材料为bet在7m2/g~10m2/g的氧化镍粉体与bet在7m2/g~10m2/g的氧化铌粉体,其中氧化镍粉体与氧化铌粉体的重量比为93:7。
173.采用阿基米德法对本实施例制得的氧化镍基靶材进行了相对密度测定,结果表明
其相对密度为98.06%,外观无开裂现象。
174.实施例39
175.本实施例制备了一种氧化镍基靶材,与实施例4的差异在于:步骤(1)中的氧化镍基粉体材料为bet在7m2/g~10m2/g的氧化镍粉体与bet在7m2/g~10m2/g的氧化铌粉体,其中氧化镍粉体与氧化铌粉体的重量比为92:8。
176.采用阿基米德法对本实施例制得的氧化镍基靶材进行了相对密度测定,结果表明其相对密度为98.17%,外观无开裂现象。
177.实施例40
178.本实施例制备了一种氧化镍基靶材,与实施例4的差异在于:步骤(1)中的氧化镍基粉体材料为bet在7m2/g~10m2/g的氧化镍粉体与bet在7m2/g~10m2/g的氧化铌粉体,其中氧化镍粉体与氧化铌粉体的重量比为91:9。
179.采用阿基米德法对本实施例制得的氧化镍基靶材进行了相对密度测定,结果表明其相对密度为98.13%,外观无开裂现象。
180.实施例41
181.本实施例制备了一种氧化镍基靶材,与实施例4的差异在于:步骤(1)中的氧化镍基粉体材料为bet在7m2/g~10m2/g的氧化镍粉体与bet在7m2/g~10m2/g的氧化铌粉体,其中氧化镍粉体与氧化铌粉体的重量比为90:10。
182.采用阿基米德法对本实施例制得的氧化镍基靶材进行了相对密度测定,结果表明其相对密度为98.17%,外观无开裂现象。
183.对比例1
184.本对比例制备了一种氧化镍基靶材,与实施例4的差异在于:步骤(3)中第一阶段的烧结温度为650℃。
185.对上述制得的氧化镍基靶材进行了外观观察,结果表明其出现了开裂现象。
186.对比例2
187.本对比例制备了一种氧化镍基靶材,与实施例4的差异在于:步骤(3)中第一阶段的烧结温度为950℃。
188.对上述制得的氧化镍基靶材进行了外观观察,结果表明其出现了开裂现象。
189.对比例3
190.本对比例制备了一种氧化镍基靶材,与实施例4的差异在于:步骤(3)中第二阶段的无烧结气氛(即真空)。
191.对上述制得的氧化镍基靶材进行了外观观察,结果表明其出现较为严重的开裂现象。
192.对比例4
193.本对比例制备了一种氧化镍基靶材,与实施例4的差异在于:步骤(3)中第二阶段的烧结气氛为空气。
194.对上述制得的氧化镍基靶材进行了外观观察,结果表明其出现较为严重的开裂现象。
195.为了方便理解本发明的技术要点,对本发明实施例1~41和对比例1~4制得的氧化镍基靶材的制备要点和所得靶材性能进行了统计,具体如表1所示。
196.表1:本发明实施例1~41和对比例1~4制得的靶材性能测试结果
197.[0198][0199][0200]
从上述表1中,根据实施例1~6记载分析可知,采用本发明的氧化镍基靶材制备方
法进行烧结,在1300℃~1550℃的烧结温度下均不会出现靶材开裂现象,且随着烧结温度的提高靶材的相对密度也得到进一步提高。
[0201]
进一步的,对比本发明实施例6~7和对比例1~2可知,采用本发明方法进行分段煅烧,当烧结第一阶段的煅烧温度为700~900℃时,能够获得高相对密度的靶材,且未出现开裂现象;而当烧结第一阶段的煅烧温度低于600℃或高于900℃时,如对比例1和对比例2所示,其所制得的靶材出现了较为严重的开裂现象。
[0202]
对比本发明实施例4、9和10可知,提高烧结第二阶段的烧结时间也有利于提高靶材的相对密度。
[0203]
对比本发明实施例4、11和对比例3、4可知,在烧结过程中烧结气氛对提高靶材的质量至关重要,当烧结气氛为氧气或者氮氢混合气时,其制备获得的靶材密度高、无开裂现象,具体如本发明实施例4和11所示,而当将烧结过程中不通入任何气氛或将烧结气氛改为空气时,其靶材出现了显著的开裂现象,这主要是因为当通入氧气时,靶材成分可以维持富氧状态,即全是ni2o3的成分,不会产生缺氧成分的存在,即不会造成靶材不同成分的密度差,也就不会产生开裂的情况,当通入氮氢混合气体(n2/h2=98/2wt%)时,靶材成分处于缺氧状态,成分全是nio,即不存在富氧成分,因此也不会造成靶材不同成分的密度差,进而也不会产生开裂的情况。
[0204]
根据本发明实施例12~21、实施例22~31和实施例32~41记载可知,采用本发明的制备方法,当掺杂适量氧化镁、氧化铜或氧化铌时,其获得的靶材仍具有较高的密度,且掺杂之后有利于改善开裂情况,这主要是由于不同的掺杂物会形成少量的不同密度的成分,可以在靶材密度存在变化时作为缓冲,释放一定量的应力,减少开裂的风险。
[0205]
综上可见,本发明的氧化镍基靶材制备方法简单,采用该方法制得氧化镍基靶材密度高,且烧结完成后降温不易开裂。
[0206]
上面对本发明实施例作了详细说明,但是本发明不限于上述实施例,在所属技术领域普通技术人员所具备的知识范围内,还可以在不脱离本发明宗旨的前提下作出各种变化。此外,在不冲突的情况下,本发明的实施例及实施例中的特征可以相互组合。