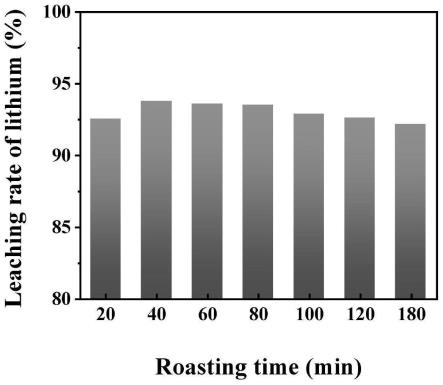
1.本发明涉及二次资源回收再利用技术领域,具体涉及一种利用废旧锂离子电池回收锂的方法。
背景技术:2.锂离子电池主要由外壳、正极、负极、电解液与隔膜所组成,内部主要采用卷绕式或叠片结构,电池的外壳通常由铝塑膜壳、不锈钢或镀镍钢壳制成,正极是通过起粘结作用的pvdf(聚偏氟乙烯)将磷酸铁锂、钴酸锂或镍钴锰酸锂等粉末均匀涂布于铝箔集流体表面构成,负极则由无定形碳(石墨)涂覆于铜箔集流体表面构成;有机电解液一般采用六氟磷酸锂(lipf6)溶于有机溶剂如碳酸酯类溶剂)制备而成;隔膜则常用对锂离子具有选择透过性的聚烯微孔膜pp、pe等。锂离子电池大量应用于手机、笔记本电脑、电动工具、电动车、路灯备用电源、航灯以及家用小电器上。锂电池广泛应用的同时也会产生大量废弃的锂离子电池。
3.由于锂矿资源的不可再生性和稀缺性,回收废旧锂离子电池中的锂具有重要的意义。回收废旧锂离子电池的常用方法为湿法冶金或火法冶金。火法冶金法的主要工艺为:将经过预处理(放电、破碎)的废旧锂电池通过高温焙烧去除锂电池中粘合剂,材料中的金属变成熔融态的合金,实现锂电池组成材料的分离。湿法治金法工艺主要通过溶液浸出(酸浸或碱浸)的方式对锂电池物料中的贵重金属进行溶解,然后通过沉淀法、电沉积法、络合法、萃取法、盐析法和离子交换法对不同金属进行分离、最后获得高纯度的锂、钻等贵重金属。其中,酸浸采用的浸出剂通常为h2so4、hno3、hcl等无机酸,并在其中添加h2o2作为还原剂来提高锂的回收率。然而,传统的湿法冶金回收锂过程中,分离有价金属后得到的残余液体中的锂含量较低,并且存在许多难以处理的杂质,导致锂的回收率低且纯度低;火法冶金回收锂过程中锂经常作为副产物在炉渣中损失或在高温过程中蒸发,也导致锂的回收率低。
技术实现要素:4.有鉴于此,本发明的目的在于提供一种利用废旧锂离子电池回收锂的方法,本发明提供的方法锂回收率高且得到的碳酸锂的纯度高。
5.为了实现上述发明目的,本发明提供以下技术方案:
6.本发明提供了一种利用废旧锂离子电池回收锂的方法,包括以下步骤:
7.将废旧锂离子电池的正极极片依次进行碱浸和焙烧,得到正极活性物质;
8.将所述正极活性物质与废弃生物质混合,在保护气氛进行还原焙烧,得到焙烧含锂料;
9.将所述焙烧含锂料在碳酸水溶液中进行碳酸水浸后干燥,得到回收碳酸锂;所述焙烧含锂料与碳酸水溶液的固液比为10~30g:1l。
10.优选地,所述废弃生物质与正极活性物质的质量比为1:0.1~2。
11.优选地,所述还原焙烧的温度为500~800℃,保温时间为20~180min。
12.优选地,所述碳酸水浸的温度为20~80℃,时间为1~5h。
13.优选地,所述碳酸水浸为:将焙烧含锂料与水混合,通入二氧化碳进行碳酸水浸。
14.优选地,所述二氧化碳通入流速为50~200ml/min。
15.优选地,所述焙烧的温度为700~800℃,保温时间为3~5h。
16.优选地,所述碱浸用碱液为无机强碱液;
17.优选地,所述无机强碱液的浓度为1~5mol/l。
18.优选地,所述正极极片由废旧锂离子电池进行放电处理后拆解得到;所述废旧锂离子电池包括废旧钴酸锂电池、废旧三元电池和废旧高镍电池中的至少一种。
19.本发明提供了一种利用废旧锂离子电池回收锂的方法,包括以下步骤:将废旧锂离子电池的正极极片依次碱浸和焙烧,得到正极活性物质;将所述正极活性物质与废弃生物质混合,在保护气氛进行还原焙烧,得到焙烧含锂料;将所述焙烧含锂料在碳酸水溶液中进行碳酸水浸后干燥,得到回收碳酸锂;所述焙烧含锂料与碳酸水溶液的固液比为10~30g:1l。本发明以废弃生物质作为还原剂,在还原焙烧过程中产生还原性气体(一氧化碳、氨气、甲烷、氢气等)和生物炭,对正极活性物质的分解(产物为碳酸锂、氧化镍、氧化钴、二氧化锰)起到促进作用,提高了锂的回收率;在高固液比条件下进行碳酸水浸能够实现碳酸锂的高效回收,不仅提高了锂的回收率与回收产品纯度,解决了传统湿法和火法回收过程中锂回收率低、回收的锂纯度不够、杂质过多等问题;并且减少了在蒸发结晶过程中能量的消耗,提高了废旧锂离子电池正极材料的再利用附加值与回收效益。
20.而且,本发明以废弃生物质作为还原剂,产生了还原性气体(一氧化碳、氨气、甲烷、氢气等),该还原性气体在室温下就可以发生还原反应,所以在焙烧过程中,低温下产生的还原性气体会直接还原三元材料分解后产生的金属氧化物,进而能够降低还原焙烧温度,还能够减少还原剂的用量,进一步降低了回收锂的成本;本发明以废弃生物质作为还原剂变废为宝,减少了废弃生物质对环境的污染,且无需添加h2o2作为还原剂,显著降低了回收锂的成本。本发明以碳酸水浸代替传统的h2so4、hno3、hcl等无机酸浸,酸浸过程中产生的气体为二氧化碳,不产生no3、so2、cl2等有毒有害气体,绿色环保且锂的回收成本低。
附图说明
21.图1为回收锂的流程图;
22.图2为废弃生物质豆渣的实物图;
23.图3为正极活性物质粉末的实物图;
24.图4为还原焙烧时间对回收率的影响;
25.图5为还原焙烧温度对回收率的影响;
26.图6为正极活性物质粉末与豆渣粉末的质量比对回收率的影响;
27.图7为实施例1制备得到的焙烧含锂料的x射线衍射图;
28.图8为实施例1制备得到的回收碳酸锂的x射线衍射图;
29.图9为实施例1制备得到的回收碳酸锂的扫描电镜图;
30.图10为碳酸水浸回收装置图。
具体实施方式
31.本发明提供了一种利用废旧锂离子电池回收锂的方法,包括以下步骤:
32.将废旧锂离子电池的正极极片依次碱浸和焙烧,得到正极活性物质;
33.将所述正极活性物质与废弃生物质混合,在保护气氛进行还原焙烧,得到焙烧含锂料;
34.将所述焙烧含锂料在碳酸水溶液中进行碳酸水浸后干燥,得到回收碳酸锂;所述焙烧含锂料与碳酸水溶液的固液比为10~30g:1l。
35.在本发明中,若无特殊说明,所有的原料组分均为本领域技术人员熟知的市售商品。
36.本发明将废旧锂离子电池的正极极片依次碱浸和焙烧,得到正极活性物质。
37.在本发明中,所述正极极片优选由废旧锂离子电池进行放电处理后拆解得到。在本发明中,所述废旧锂离子电池优选包括废旧钴酸锂电池、废旧三元电池和废旧高镍电池中的至少一种。在本发明中,所述放电处理优选包括盐溶液浸泡放电、液氮冷冻放电、石墨粉短路放电和充放电机放电中的至少一种;本发明对于所述盐溶液浸泡放电、液氮冷冻放电、石墨粉短路放电和充放电机放电没有特殊限定,放电至废旧锂离子电池的电压≤2v即可。本发明对于所述拆解没有特殊限定,采用本领域技术人员熟知的拆解方式即可。
38.在本发明中,所述碱浸用碱液优选为无机强碱液,更优选为碱金属氢氧化物,更优选为氢氧化钠水溶液和/或氢氧化钾水溶液;所述碱液的浓度优选为2~3mol/l,更优选为2.5mol/l;所述碱浸的目的是除去铝箔。
39.完成所述碱解后,本发明优选还包括将所得碱浸液进行固液分离,将所得固体组分水洗后干燥;本发明对于所述固液分离的方式没有特殊限定,采用本领域技术人员熟知的固液分离方式即可,具体如过滤;本发明对于所述水洗的次数没有特殊限定,水洗至洗液为中性即可;所述干燥的温度优选为80~90℃,更优选为80~85℃;所述干燥的时间优选为12~15h,更优选为8h。
40.在本发明中,所述焙烧的温度优选为700~800℃,更优选为750℃;所述焙烧的保温时间优选为3~5h,更优选为4h;所述焙烧的气氛优选为空气;所述焙烧的目的是除去正极极片中的粘结剂(如pvdf)和导电剂(如炭黑)。
41.得到正极活性物质后,本发明将所述正极活性物质与废弃生物质混合,在保护气氛进行还原焙烧,得到焙烧含锂料。
42.在本发明中,所述废弃生物质优选包括豆渣、秸秆粉和木屑粉中的至少一种,更优选为豆渣;所述废弃生物质在使用前优选先依次进行水浸泡-洗涤和干燥。所述浸泡-洗涤的温度优选为室温,所述浸泡-洗涤的次数优选为3~5次,单次浸泡-洗涤的时间优选为10~30min,更优选为20min。在本发明中,所述干燥的温度优选为110~120℃,更优选为110~115℃;本发明对于所述干燥的时间没有特殊限定,干燥至恒重即可,具体如干燥12~15h。
43.在本发明中,所述废弃生物质与正极活性物质的质量比优选为1:0.1~2,更优选为1:0.2~1,进一步优选为1:0.3~1。
44.在本发明中,所述混合优选为研磨混合,所述研磨混合的温度优选为室温,所述研磨混合的时间优选为2~10min,更优选为5min。
45.在本发明中,所述还原焙烧的温度优选为500~800℃,更优选为550~750℃,进一
步优选为650~750℃,最优选为700℃;温度由室温升至所述还原焙烧的温度的升温速率优选为5~10℃/min,更优选为8~10℃/min;所述还原焙烧的保温时间优选为20~180min,更优选为40~120min,进一步优选为40~100min,最优选为40~80min。在本发明中,所述还原焙烧过程中,废弃生物质产生还原性气体和生物炭,对正极活性物质的分解起到促进作用,从而降低还原焙烧温度,减少还原剂的用量,并且在还原焙烧过程中产生的气体为二氧化碳、氮气以及水蒸气,不会对环境造成污染,绿色环保。
46.完成所述还原焙烧后,本发明优选还包括将所得焙烧产物进行研磨,得到焙烧含锂料。在本发明中,所述研磨的温度优选为室温,所述研磨的时间优选为2~10min,更优选为5min。
47.得到焙烧含锂料后,本发明将所述焙烧含锂料在碳酸水溶液中进行碳酸水浸后干燥,得到回收碳酸锂;所述焙烧含锂料与碳酸水溶液的固液比为10~30g:1l。
48.在本发明中,所述焙烧含锂料与碳酸水浸用碳酸水溶液的固液比为10~30g:1l,优选为15~25g:1l,更优选为20~25g:1l。
49.在本发明中,所述碳酸水浸的温度优选为20~80℃,更优选为40~70℃,进一步优选为50~65℃;所述碳酸水浸的时间优选为1~5h,更优选为2~4h,进一步优选为3h。在本发明中,所述碳酸水浸优选为:将焙烧含锂料与水混合,通入二氧化碳进行碳酸水浸。在本发明中,所述二氧化碳通入流速优选为50~200ml/min,更优选为50~150ml/min,进一步优选为100~150ml/min。在本发明中,所述碳酸水浸优选在图10所示的碳酸水浸回收装置中进行,所述碳酸水浸回收装置优选包括广口瓶、胶塞、玻璃管、导气胶管和二氧化碳气瓶。
50.完成所述碳酸水浸后,本发明优选还包括将所得碳酸水浸反应液依次进行固液分离,将得到的液体组分进行浓缩,将所得浓缩液进行水洗。本发明对于所述固液分离的方式没有特殊限定,采用本领域技术人员熟知的固液分离方式即可,具体如过滤。本发明对于所述浓缩的方式没有特殊限定,采用本领域技术人员熟知的浓缩方式即可;所述浓缩的温度优选为90~110℃,更优选为100℃;本发明对于所述浓缩的时间没有特殊限定,浓缩至所述浓缩液的体积占碳酸水浸反应液体积的15~20%即可。在本发明中,所述水洗优选为沸水洗。
51.在本发明中,所述干燥的温度优选为80~90℃,更优选为80~85℃;所述干燥的时间优选为12~15h,更优选为8h。
52.下面将结合本发明中的实施例,对本发明中的技术方案进行清楚、完整地描述。显然,所描述的实施例仅仅是本发明一部分实施例,而不是全部的实施例。基于本发明中的实施例,本领域普通技术人员在没有做出创造性劳动前提下所获得的所有其他实施例,都属于本发明保护的范围。
53.实施例1
54.按照图1所示的工艺流程图和图10所示碳酸水浸回收装置制备回收碳酸锂,具体步骤如下:
55.(1)将废弃生物质豆渣用去离子水浸泡-洗涤3次,然后在110℃真空烘箱中干燥12h,得到豆渣粉末(实物图如图2所示)。
56.(2)将废旧三元523锂离子电池浸泡于5wt%nacl溶液中放电处理至电压≤2v,手动拆解,除去铝壳、正负极端子、密封圈、盖板、负极极片和隔膜,得到正极极片;
57.(3)将所述正极极片浸泡于2.5mol/lnaoh溶液中以去除铝箔,过滤,将得到的滤渣用去离子水洗涤至无钠离子,在80℃条件下干燥12h,然后在700℃、空气气氛条件下焙烧3h以去除pvdf和炭黑,得到正极活性物质粉末(实物图如图3所示);
58.(4)将所述正极活性物质粉末与豆渣粉末按1:0.3的质量比(记为填样比例)加入到玛瑙研钵中,在室温条件下研磨20min,在氩气气氛下以10℃/min的升温速率升温至700℃后还原焙烧40min,置于玛瑙研钵中在室温条件下研磨5min,得到焙烧含锂料;
59.(5)将所述焙烧含锂料加入到碳酸水浸回收装置中,加入去离子水并持续通入二氧化碳,在65℃条件下碳酸水浸3h,将所得碳酸水浸液进行过滤,将所得滤液在100℃条件下浓缩至碳酸水浸液体积的20%,过滤,将所得滤渣沸水洗涤1次,在100℃条件下干燥至恒重,得到回收碳酸锂;其中,焙烧含锂料和去离子水的固液比为25g:1l,二氧化碳流速为135ml/min;碳酸水浸回收装置由广口瓶、胶塞、玻璃管、导气胶管和二氧化碳气瓶组成。
60.实施例2~21
61.按照实施例1的方法制备回收碳酸锂,实施例2~21的回收条件如表1所示,其他回收条件与实施例1相同:
62.表1实施例1~21的回收条件和锂回收率实验结果
63.[0064][0065]
实施例1~21中锂回收率如图4~图6和表2所示,其中,图4为还原焙烧时间(实施例1~7)对锂回收率的影响图;图5为还原焙烧温度(实施例8~14)对对锂回收率的影响图,图6为正极活性物质粉末与豆渣粉末质量比(实施例15~21)对锂回收率的影响图,由表2和图4~图6可知,随着还原焙烧温度的升高,锂回收率先升高后降低,这是由于为温度提升,还原反应速度加快,但是较高的温度会导致碳酸锂分解。随着豆渣粉末用量的增加,锂回收率先升高后降低,这是由于豆渣粉末的用量过少,产生的还原气体和co2的量不够,进而导致li的不完全还原和浸出速率的降低,豆渣粉末的用量过多,产生过量的生物炭会封装li2co3,迫使它在随后的回收过程中无法与水和co2接触。还原焙烧时间对于焙烧时间对锂回收率的影响不大。本发明提供的方法的锂回收率在84.1%以上,当正极活性物质粉末与豆渣粉末的质量比为1:0.3、还原焙烧温度为700℃时,锂的回收率达到最大值。
[0066]
实施例1制备得到的焙烧含锂料的x射线衍射图如图7所示,由图7可知,焙烧含锂料主要由ni、co、mno以及li2co3组成。
[0067]
实施例1制备得到的碳酸锂的x射线衍射图如图8所示,其中内插图为碳酸锂的实物图。由图8可知,只有碳酸锂的衍射峰,证明最终回收产物为高纯度碳酸锂(纯度为99.79%)。
[0068]
实施例1制备得到的碳酸锂的扫描电镜图如图9所示,由图9可知,碳酸锂呈现棒状,为碳酸锂的典型形貌,且无其他杂质存在,说明回收的碳酸锂纯度高。
[0069]
本发明采用响应面和中心复合设计优化的碳酸水浸过程,能够在高固液比的情况下实现碳酸锂的高效回收,不仅提高了锂的回收率与回收产品纯度,解决了传统湿法和火法回收过程中锂回收率低、回收的锂纯度不够、杂质过多等问题;并且减少了在蒸发结晶过程中能量的消耗,提高了锂离子电池正极材料的再利用附加值与回收效益。
[0070]
以上所述仅是本发明的优选实施方式,应当指出,对于本技术领域的普通技术人员来说,在不脱离本发明原理的前提下,还可以做出若干改进和润饰,这些改进和润饰也应视为本发明的保护范围。