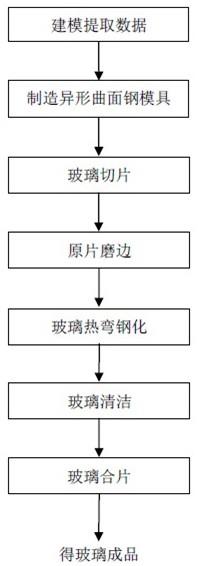
1.本发明涉及玻璃加工领域,具体涉及一种异形曲面玻璃的加工方法。
背景技术:2.在一些公共建筑中,为了打造地标性建筑和突出设计的与众不同,通常会采用一些流线型线条、单曲面、双曲面、甚至多曲面手法进行设计组合,借此来表现出更为优美、曲线更为突出、更具有代表性的建筑。特别是异形建筑中,异形曲面玻璃幕墙,由于异形曲面玻璃幕墙不仅对施工提出较高要求和标准,对异形曲面玻璃加工同样也提出了较高的要求和标准。
3.由于异形曲面玻璃不像普通玻璃方正且构造简单,易于确定坐标点、下料尺寸和加工尺寸。而且也不能使用常规热弯模具进行造型,和在和片过程中由于异形,也增加了玻璃和片和pvb施工难度,那么如何保证异形曲面幕墙玻璃的顺利加工,满足现场施工需求,成为了急需解决的问题。
技术实现要素:4.基于此,本发明提供了一种异形曲面玻璃的加工方法,该方法降低了异形曲面玻璃成形,合片过程的施工难度,保证了曲面玻璃幕墙的质量。
5.为实现上述目的,本发明提供了以下技术方案:本发明提供了一种异形曲面玻璃的加工方法,包括以下加工步骤:s1、建模提取数据:利用bim建模软件建立3d模型,提取玻璃加工下料和加工尺寸、数量及定位坐标等数据;s2、制造异形曲面钢模具:用网格式空间模形确定玻璃下料尺寸,在制作时按网格横线条的曲度将钢管弯曲成形,每间隔100mm放置一根曲形钢管并按网格的竖向线条曲度拼接成异形曲面钢模具;s3、玻璃切片:将步骤s1提取的三维坐标数据转换成平面坐标数据,按照常规普通玻璃加工方法进行原片切割;s4、原片磨边:用磨边机进行原片磨边,磨削量控制:玻璃厚度在8mm以下时,磨削量﹤2.5mm,玻璃厚度在10~19mm以下时,磨削量﹤1.5mm;进料速度控制:玻璃厚度在8mm以下时,速度﹤2.5m,玻璃厚度在10~19mm以下时,速度﹤1.5m;s5、玻璃热弯钢化:利用加热设备将玻璃原片加热至700℃软化后用公母模具进行压制;s6、玻璃清洁:用手动清洁方式将玻璃表面的异物擦除;s7、玻璃合片:真空夹胶合片,真空装袋进釜烧制,冷却排气得玻璃成品。
6.本发明提供的一种异形曲面玻璃的加工方法,具体加工步骤可选的还包括喷绘彩釉。
7.进一步地,所述步骤s2中异形曲面钢模具分为公母模具;所述公母模具尺寸预留
有玻璃热弯钢化回弹尺寸余量,曲面偏差
±
2.5mm,外形尺寸偏差
±
3mm。
8.进一步地,所述步骤s6中手动清洁方式为通过粘辊把玻璃表面的异物通过粘结的方式移除。
9.进一步地,所述步骤s6中手动清洁方式为利用无水乙醇将玻璃表面异物擦除。
10.进一步地,所述步骤s7中真空夹胶合片包括:用设备抽出真空,将两片玻璃以及置于夹层中的pvb胶片在10kg的压力下进行合片,用拉弯机把铝格条进行拉弯,在进行中空后充入氦气。
11.进一步地,所述pvb胶片含水率<0.2%;所述pvb胶片储存环境温度为22~28℃,湿度<28%。
12.进一步地,所述步骤s7中真空装袋进釜烧制包括:合片完成后在玻璃边缘包裹一层百里布,在百里布外面包裹一层毡布,并用高温胶带固定防止脱落,然后将弯夹层玻璃放入装有气嘴的耐高温真空袋内,预抽真空,预抽完成后将夹层玻璃放置高压釜内,摆放间隙》100mm,进釜烧制。
13.进一步地,所述预抽真空时长》30min,真空压力-0.03mpa/
㎡
。
14.进一步地,所述进釜烧制过程中烧釜温度为135-145℃,压力为12.5-13 bar,烧釜时间为90-120min。
15.进一步地,所述步骤s7中冷却排气包括:烧制完成后,对釜降温,降温速率≥3.3℃/min,当釜内温度<45℃时,进行排气得玻璃成品。
16.基于上述技术方案,本发明实施例至少可以产生如下技术效果:(1)本发明提供的一种异形曲面玻璃的加工方法,还提供了异形曲面钢模具制造的步骤,能使玻璃烧制成形的曲面偏差在
±
2.5mm之内,外形尺寸偏差在
±
3mm之内,能够最大限度的满足夹层玻璃的产品质量。
17.(2)本发明提供的一种异形曲面玻璃的加工方法,在真空合片过程中,玻璃产品受热均匀,烧制结束后能够快速降温,防止受热不均而形成透光度不均。
18.(3)本发明提供的一种异形曲面玻璃的加工方法,在排气过程中,保持降温速率≥3.3℃/min,温度<45℃,温度过高、过早排气会降低玻璃产品的透光度,增加产品雾度,影响产品质量。
19.(3)本发明提供的一种异形曲面玻璃的加工方法,该方法操作简便,成形的玻璃产品质量高,更符合施工现场的要求和标准,具有良好的推广前景。
附图说明
20.图1是本发明实施例的流程图;图2是本发明实施例的流程图。
具体实施方式
21.以下结合实施例对本发明作进一步说明,实施例是用于说明本发明,而不是用于限制本发明的范围。本领域技术人员可以确定本发明的基本特征,并且在不偏离本发明精神和范围的情况下,可以对本发明做出各种修改和改变,以使其使用各种用途和条件。
22.一种异形曲面玻璃的加工方法,包括以下加工步骤:
s1、建模提取数据:利用bim建模软件建立3d模型,提取玻璃加工下料和加工尺寸、数量及定位坐标等数据;s2、制造异形曲面钢模具:用网格式空间模形确定玻璃下料尺寸,在制作时按网格横线条的曲度将钢管弯曲成形,每间隔100mm放置一根曲形钢管并按网格的竖向线条曲度拼接成异形曲面钢模具;s3、玻璃切片:将步骤s1提取的三维坐标数据转换成平面坐标数据,按照常规普通玻璃加工方法进行原片切割;s4、原片磨边:用磨边机进行原片磨边,磨削量控制:玻璃厚度在8mm以下时,磨削量﹤2.5mm,玻璃厚度在10~19mm以下时,磨削量﹤1.5mm;进料速度控制:玻璃厚度在8mm以下时,速度﹤2.5m,玻璃厚度在10~19mm以下时,速度﹤1.5m;s5、玻璃热弯钢化:利用加热设备将玻璃原片加热至700℃软化后用公母模具进行压制;s6、玻璃清洁:用手动清洁方式将玻璃表面的异物擦除;s7、玻璃合片:真空夹胶合片,真空装袋进釜烧制,冷却排气得玻璃成品。
23.本发明提供的一种异形曲面玻璃的加工方法,可选的步骤还包括喷绘彩釉。
24.进一步地,所述步骤s2中异形曲面钢模具分为公母模具;所述公母模具尺寸预留有玻璃热弯钢化回弹尺寸余量,曲面偏差
±
2.5mm,外形尺寸偏差
±
3mm。
25.进一步地,所述步骤s6中手动清洁方式为通过粘辊把玻璃表面的异物通过粘结的方式移除。
26.进一步地,所述步骤s6中手动清洁方式为利用无水乙醇将玻璃表面异物擦除。
27.进一步地,所述步骤s7中真空夹胶合片包括:用设备抽出真空,将两片玻璃以及置于夹层中的pvb胶片在10kg的压力下进行合片,用拉弯机把铝格条进行拉弯,在进行中空后充入氦气。
28.进一步地,所述pvb胶片含水率<0.2%;所述pvb胶片储存环境温度为22~28℃,湿度<28%。
29.进一步地,所述步骤s7中真空装袋进釜烧制包括:合片完成后在玻璃边缘包裹一层百里布,在百里布外面包裹一层毡布,并用高温胶带固定防止脱落,然后将弯夹层玻璃放入装有气嘴的耐高温真空袋内,预抽真空,预抽完成后将夹层玻璃放置高压釜内,摆放间隙》100mm,进釜烧制。
30.进一步地,所述预抽真空时长》30min,真空压力-0.03mpa/
㎡
。
31.进一步地,所述进釜烧制过程中烧釜温度为135-145℃,压力为12.5-13 bar,烧釜时间为90-120min。
32.进一步地,所述步骤s7中冷却排气包括:烧制完成后,对釜降温,降温速率≥3.3℃/min,当釜内温度<45℃时,进行排气得玻璃成品。
33.实施例1 异形曲面玻璃成形制作s1、建模提取数据:根据异形曲面玻璃的施工设计图纸,在计算机上利用bim建模软件建立3d模型,并提取玻璃加工下料和加工尺寸、数量及定位坐标等数据,通过 bim 技术对主体钢结构框架进行数据提取,建立双曲面模型。再通过 revit 参数化的异形曲面玻璃模型导入 rhino(犀牛)软件中,采用gh插件提取玻璃板块翘曲值 、尺寸等一系列空间定
位参数,形成每块曲面玻璃加工单,提交到加工厂;s2、制造异形曲面钢模具:用网格式空间模形确定玻璃下料尺寸,在制作时按网格横线条的曲度将钢管弯曲成形,每间隔100mm放置一根曲形钢管并按网格的竖向线条曲度拼接成异形曲面钢模具,并预留出玻璃在烧制过程中回弹尺寸余量,保证玻璃的曲面偏差在
±
2.5mm之内,外形尺寸偏差在
±
3mm之内,模具分公母模具,能够最大限度的满足夹层玻璃的产品质量,模型的吻合度直接决定弯夹层的质量,甚至影响到弯夹层产品的后期使用寿命。
34.s3、玻璃切片:将步骤s1利用bim建立3d模型提取的三维坐标数据转换成平面坐标数据,按照常规普通玻璃加工方法进行原片切割,原片切割完成后进行原片磨边。
35.s4、原片磨边:所述磨边机采用的是四川锦泰宏威玻璃机械研发生产的jh-3000型中型磨边机;使用前检查磨边机磨轮是否松动、磨损程度、循环水是否清洁等,例行检查无误后,将磨边机预热开机,进行试磨削。
36.试磨削后,将玻璃原片用磨边机进行原片磨边处理,控制玻璃原片进料速度为2.5m,控制磨削量为2.5mm;磨削量是指玻璃在切割的时候损失量。
37.s5、玻璃热弯钢化:利用加热设备将玻璃原片加热至700℃软化后,用公母模具进行压制,成型后采用3d扫描仪扫描检查是否与设计图纸相符,合格后,放入钢化炉进行钢化,热弯钢化后再次采用3d扫描仪扫描检测产品是否合格。
38.s6、玻璃清洁:对检测合格的玻璃产品进行清洁,用手动清洁方式将玻璃表面的异物去除,用无尘布和无水乙醇来清洁擦拭,待无水乙醇挥发后方可进行下一步铺pvb胶片的操作,防止乙醇部分残留在pvb膜层内形成蒸汽泡,降低pvb胶片与玻璃的粘结性能。
39.s7、玻璃合片:真空夹胶合片,取出pvb胶片,所述pvb胶片储存环境温度为28℃,湿度27%,pvb胶片含水率0.2%,将pvb胶片铺与两片玻璃的夹层,一同放入合片装置内;用设备抽出装置内真空,将两片玻璃以及置于夹层中的pvb胶片在10kg的压力下进行合片,用拉弯机把铝格条进行拉弯,在进行中空后充入氦气。
40.真空装袋进釜烧制,合片完成后在玻璃边缘包裹一层百里布,在百里布外面包裹一层毡布,并用高温胶带固定防止脱落,然后将弯夹层玻璃放入装有气嘴的耐高温真空袋内,大于3m2的玻璃装装入有2个气嘴的耐高温真空袋内,装车进釜前,需要进行预抽真空,预抽真空时长》30min,真空压力-0.03mpa/
㎡
,预抽完成后将夹层玻璃放置高压釜内,摆放间隙》100mm,以利于热循环风在釜内均匀流通,保证产品在高压釜内均匀受热,及保温结束后能够快速降温,防止受热不均而形成透光度不均,进釜烧制,在烧釜前检查真空袋是否抽紧,有无漏气现象,如有漏气现象需及时处理,烧釜开始后,持续真空直至开釜,釜内温度控制为140℃,压力为12.5bar,烧制时间100min。
41.冷却排气得玻璃成品,烧制完成后,对釜降温,降温速率≥3.3℃/min,当釜内温度<45℃时,进行冷却排气,取出玻璃进行修边处理得到玻璃成品,并挑选出不合格品进行返工。
42.最后异形曲面玻璃送粘框加工厂进行玻框粘接,玻框事先在拉弯厂进行拉弯成异形曲面,粘完框检查质量合格后,再送施工现场。
43.实施例2 异形曲面彩釉玻璃成形制作
s1、建模提取数据:根据异形曲面玻璃的施工设计图纸,在计算机上利用bim建模软件建立3d模型,并提取玻璃加工下料和加工尺寸、数量及定位坐标等数据,通过 bim 技术对主体钢结构框架进行数据提取,建立双曲面模型。再通过 revit 参数化的异形曲面玻璃模型导入 rhino(犀牛)软件中,采用gh插件提取玻璃板块翘曲值 、尺寸等一系列空间定位参数,形成每块曲面玻璃加工单,提交到加工厂;s2、制造异形曲面钢模具:用网格式空间模形确定玻璃下料尺寸,在制作时按网格横线条的曲度将钢管弯曲成形,每间隔100mm放置一根曲形钢管并按网格的竖向线条曲度拼接成异形曲面钢模具,并预留出玻璃在烧制过程中回弹尺寸余量,保证玻璃的曲面偏差在
±
2.5mm之内,外形尺寸偏差在
±
3mm之内,模具分公母模具,能够最大限度的满足夹层玻璃的产品质量,模型的吻合度直接决定弯夹层的质量,甚至影响到弯夹层产品的后期使用寿命。
44.s3、玻璃切片:将步骤s1利用bim建立3d模型提取的三维坐标数据转换成平面坐标数据,按照常规普通玻璃加工方法进行原片切割,原片切割完成后进行原片磨边。
45.s4、原片磨边:所述磨边机采用的是川锦泰宏威玻璃机械研发生产的jh-3000型中型磨边机;使用前检查磨边机磨轮是否松动、磨损程度、循环水是否清洁等,例行检查无误后,将磨边机预热开机,进行试磨削。
46.试磨削后,将玻璃原片用磨边机进行原片磨边处理,控制玻璃原片进料速度为1.5m,控制磨削量为1.5mm;磨削量是指玻璃在切割的时候损失量。
[0047] s5、喷绘彩釉:采用特殊设备进行高温喷绘彩釉,超白镀膜玻璃原片分为一面镀膜,一面不镀膜,彩釉面做在不镀膜面。玻璃进行彩釉处理后再进行玻璃热弯钢化,异行玻璃彩釉及镀膜工艺后在进入弯钢炉过程中,彩釉面和low-e膜需位于玻璃凹面,但本工程立面玻璃存在外突曲型玻璃和内凹曲型玻璃,为保证彩釉和low-e膜效果一致,对于内凹曲型玻璃由于彩釉面和镀膜面需位于玻璃的凸面,此种做法直接进入弯钢炉弯钢时会刮花彩釉和low-e膜面,所以内凹曲型玻璃需单独开模进入特殊弯钢炉。
[0048] s6、玻璃热弯钢化:利用加热设备将玻璃原片加热至700℃软化后,用公母模具进行压制,成型后采用3d扫描仪扫描检查是否与设计图纸相符,合格后,放入钢化炉进行钢化,热弯钢化后再次采用3d扫描仪扫描检测产品是否合格。
[0049]
s7、玻璃清洁:对检测合格的玻璃产品进行清洁,用手动清洁方式将玻璃表面的异物去除,用无尘布和无水乙醇来清洁擦拭,待无水乙醇挥发后方可进行下一步铺pvb胶片的操作,防止乙醇部分残留在pvb膜层内形成蒸汽泡,降低pvb胶片与玻璃的粘结性能。
[0050]
s8、玻璃合片:真空夹胶合片,取出pvb胶片,所述pvb胶片储存环境温度为28℃,湿度27%,pvb胶片含水率0.2%,将pvb胶片铺与两片玻璃的夹层,一同放入合片装置内用设备抽出装置内真空,将两片玻璃以及置于夹层中的pvb胶片在10kg的压力下进行合片,用拉弯机把铝格条进行拉弯,在进行中空后充入氦气。
[0051]
真空装袋进釜烧制,合片完成后在玻璃边缘包裹一层百里布,在百里布外面包裹一层毡布,并用高温胶带固定防止脱落,然后将弯夹层玻璃放入装有气嘴的耐高温真空袋内,大于3m2的玻璃装装入有2个气嘴的耐高温真空袋内,装车进釜前,需要进行预抽真空,预抽真空时长》30min,真空压力-0.03mpa/
㎡
,预抽完成后将夹层玻璃放置高压釜内,摆放
间隙》100mm,以利于热循环风在釜内均匀流通,保证产品在高压釜内均匀受热,及保温结束后能够快速降温,防止受热不均而形成透光度不均,进釜烧制,在烧釜前检查真空袋是否抽紧,有无漏气现象,如有漏气现象需及时处理,烧釜开始后,持续真空直至开釜,釜内温度控制为140℃,压力为12.5bar,烧制时间100min。
[0052]
冷却排气得玻璃成品,烧制完成后,对釜降温,降温速率≥3.3℃/min,当釜内温度<45℃时,取出玻璃进行修边处理得到玻璃成品,并挑选出不合格品进行返工。
[0053]
最后异形曲面玻璃送粘框加工厂进行玻框粘接,玻框事先在拉弯厂进行拉弯成异形曲面,粘完框检查质量合格后,再送施工现场。
[0054]
以上所述,仅为本发明的具体实施方式,但本发明的保护范围并不局限于此,任何熟悉本技术领域的技术人员在本发明揭露的技术范围内,可轻易想到变化或替换,都应涵盖在本发明的保护范围之内。