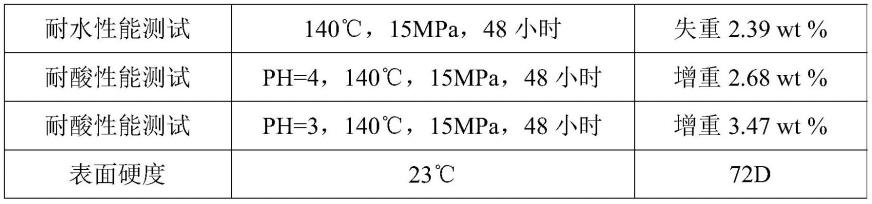
1.本发明属于油气开采射孔压裂技术领域,涉及一种耐水耐酸腐蚀固体推进剂、制备方法及其应用。
背景技术:2.复合射孔和高能气体压裂技术利用火药在井下点火燃烧后产生高压气体及释放热量做功,能够解除井筒及射孔孔道污染堵塞,并对地层压裂造缝,改善近井地带渗流能力,提高油气井产量,已经得到广泛的应用和认可。复合射孔和高能气体压裂施工时井筒中会有清水或井液,一般以酸性环境居多。现有复合射孔和高能气体压裂火药装药主要为单基、双基、复合固体推进剂,耐水、耐酸腐蚀性能差,在清水中会有一定程度氧化剂析出,在酸性井液中会有一定程度的酸液渗入,这两种情况都会导致点火失败或者燃烧不完全,影响施工作业安全和作业效果。
技术实现要素:3.本发明的目的是针对现有复合射孔和高能气体压裂火药装药的技术需求,发明一种耐水、耐酸腐蚀,生产工艺简单、绿色友好、无环境污染,生产效率高的固体推进剂、制备方法及其应用。
4.实现本发明的技术方案是:
5.一种耐水耐酸腐蚀固体推进剂,由主装药和包覆在主装药外的包覆层构成,按重量百分比计,主装药为93%~98%,包覆层为2%~7%;
6.所述主装药按重量分数组成为:粘结剂a10%~30%,稀释剂a1%~10%,工艺添加剂a1%~10%,氧化剂25%~65%,燃速催化剂1%~6%;
7.其中,所述粘结剂a为酚醛环氧树脂f51;
8.所述稀释剂a为环氧丙烷邻甲苯基醚或苯基缩水甘油醚;
9.所述工艺添加剂a为2-甲基戊二胺、1,3-戊二胺的一种或两种混合物。
10.所述氧化剂为硝酸钾、硝酸钡的一种或两种混合物;
11.所述燃速催化剂为乙基二茂铁胺、正丁基二茂铁的一种或两种混合物;
12.所述包覆层按重量分数组成为:粘结剂b85%~91%,稀释剂b4%~10%,工艺添加剂b5%~10%;
13.其中,所述粘结剂b为酚醛环氧树脂f51;
14.所述稀释剂b为环氧丙烷邻甲苯基醚或苯基缩水甘油醚;
15.所述工艺添加剂b为2-甲基戊二胺、1,3-戊二胺的一种或两种混合物。
16.具体地,所述固体推进剂采用如下方法制得:
17.首先将粘结剂a、稀释剂a、工艺添加剂a混合得到预混物,然后将氧化剂加入预混物中进行混合得到药浆,再将药浆浇注到模具中固化成型经退模得到主装药,随后将粘结剂b、稀释剂b、工艺添加剂b混合得到包覆层预混液,把包覆层预混液刷涂到主装药表面,固
化即得到成品。
18.具体地,按重量百分比计,主装药为95%,包覆层为5%;
19.所述主装药按重量分数组成为:粘结剂a30%,氧化剂55%,燃速催化剂3%,稀释剂a8%,工艺添加剂a4%;
20.所述包覆层按重量分数组成为:粘结剂b85%,稀释剂b10%,工艺添加剂b5%。
21.具体地,按重量百分比计,主装药为93%,包覆层为7%;
22.所述主装药按重量分数组成为:粘结剂a25%,氧化剂60%,燃速催化剂2%,稀释剂a7%,工艺添加剂a6%;
23.所述包覆层按重量分数组成为:粘结剂b90%,稀释剂b5%,工艺添加剂b5%。
24.本发明还公开一种耐水耐酸腐蚀固体推进剂的制备方法,所述制备方法用于制备权利要求1~4任一所述的耐水耐酸腐蚀固体推进剂,包括以下步骤:
25.步骤一,按配方比例将粘结剂a、稀释剂a、工艺添加剂a加入混合锅内预混,得到预混物;
26.步骤二,向混合锅内加入氧化剂,混合得到药浆;
27.步骤三,将药浆浇注到模具中,并将模具放入支架中,常温固化,固化后得到主装药;
28.步骤四,按配方比例将将粘结剂b、稀释剂b、工艺添加剂b加入混合锅内预混,得到包覆层预混液;
29.步骤五,把包覆层预混液刷涂到主装药表面,并把刷涂好包覆液的主装药放入支架,常温固化即得到产品。
30.具体地,所述步骤一中预混时间为10~20min,步骤二中混合时间为30~50min,步骤四中混合时间为10~20min。
31.具体地,步骤三中固化时间为16~24h,步骤五中固化时间为4~6h。
32.具体地,步骤四中预混10~20分钟。
33.本发明还公开一种耐水耐酸腐蚀固体推进剂的应用,采用本发明所述的耐水耐酸腐蚀固体推进剂或本发明所述的耐水耐酸腐蚀固体推进剂的制备方法制得的固体推进剂。
34.与现有技术相比,本发明的优点在于:
35.(1)本发明所设计的包覆层,固化后覆盖在主装药外表面,隔离主装药和井筒液体,有效避免在水或酸性环境液体中主装药所含氧化剂析出或环境液体渗入,确保推进剂性能稳定,点火正常,燃烧完全,施工安全可靠。
36.(2)本发明所设计的常温固化工艺,简化了生产工艺,提高了生产效率,降低了生产成本。
37.(3)本发明所设计的固体推进剂含有的稀释剂为活性稀释剂,在降低固化体系粘度,增加流动性,改善操作性的同时与工艺添加剂进行交链反应,形成网状结构,增加产品表面硬度,提高固化效果。
具体实施方式
38.以下给出本发明的具体实施例,需要说明的是本发明不限于并不局限于以下具体实施例,凡根据本发明的技术方案所做的等同变换,均属于本发明的保护范围。
39.本发明公开了一种耐水耐酸腐蚀固体推进剂,由主装药和包覆在主装药外的包覆层构成,按重量百分比计,主装药为95%~98%,包覆层为2%~5%;
40.所述主装药按重量分数组成为:粘结剂a10%~30%,氧化剂25%~65%,燃速催化剂1%~6%,稀释剂a1%~10%,工艺添加剂a1%~10%;
41.所述主装药按重量分数组成为:粘结剂a10%~30%,稀释剂a1%~10%,工艺添加剂a1%~10%,氧化剂25%~65%,燃速催化剂1%~6%;
42.其中,所述粘结剂a为酚醛环氧树脂f51;
43.所述稀释剂a为环氧丙烷邻甲苯基醚或苯基缩水甘油醚;
44.所述工艺添加剂a为2-甲基戊二胺、1,3-戊二胺的一种或两种混合物。
45.所述氧化剂为硝酸钾、硝酸钡的一种或两种混合物;
46.所述燃速催化剂为乙基二茂铁胺、正丁基二茂铁的一种或两种混合物;
47.所述包覆层按重量分数组成为:粘结剂b85%~91%,稀释剂b4%~10%,工艺添加剂b5%~10%;
48.其中,所述粘结剂b为酚醛环氧树脂f51;
49.所述稀释剂b为环氧丙烷邻甲苯基醚或苯基缩水甘油醚;
50.所述工艺添加剂b为2-甲基戊二胺、1,3-戊二胺的一种或两种混合物。
51.本发明中的固体推进剂采用如下方法制得:
52.首先将粘结剂a、稀释剂a、工艺添加剂a混合得到预混物,然后将氧化剂加入预混物中进行混合得到药浆,再将药浆浇注到模具中固化成型经退模得到主装药,随后将粘结剂b、稀释剂b、工艺添加剂b混合得到包覆层预混液,把包覆层预混液刷涂到主装药表面,固化即得到成品。
53.在本发明中,所用试剂均市售可得。
54.实施例一:
55.本实施例给出一种耐水耐酸腐蚀固体推进剂的制备方法,按重量百分比计,主装药为95%,包覆层为5%;
56.所述主装药按重量分数组成为:粘结剂a30%,氧化剂55%,燃速催化剂3%,稀释剂a8%,工艺添加剂a4%;
57.所述包覆层按重量分数组成为:粘结剂b85%,稀释剂b10%,工艺添加剂b5%。
58.在本实施例中,粘结剂a为酚醛环氧树脂f51,稀释剂a为环氧丙烷邻甲苯基醚,工艺添加剂a为2-甲基戊二胺,燃速催化剂为乙基二茂铁胺,氧化剂为硝酸钠和硝酸钾按重量比2:1的混合物。
59.粘结剂b为酚醛环氧树脂f51,稀释剂b为环氧丙烷邻甲苯基醚,工艺添加剂b为2-甲基戊二胺。
60.按照以下方法制备:
61.步骤一,按配方比例将粘结剂a(酚醛环氧树脂f51)、稀释剂a(环氧丙烷邻甲苯基醚)、工艺添加剂a(2-甲基戊二胺)加入立式混料机内预混15min,得到预混物;
62.步骤二,向立式混料机内加入氧化剂(硝酸钠和硝酸钾按重量比2:1的混合物),混合35min得到药浆;
63.步骤三,将药浆浇注到模具中,并将模具放入支架中,常温固化,固化24h,固化后
得到主装药;
64.步骤四,按配方比例将将粘结剂b(酚醛环氧树脂f51)、稀释剂b(环氧丙烷邻甲苯基醚)、工艺添加剂b(2-甲基戊二胺)加入混合锅内预混,得到包覆层预混液;
65.步骤五,把包覆层预混液刷涂到主装药表面,共刷涂3遍,每遍间隔1小时,并把刷涂好包覆液的主装药放入支架,常温固化6h即得到产品。
66.性能测试:
67.(1)耐水性能测试:的推进剂完全浸泡在自来水中,试验条件:140℃,15mpa,48小时。
68.(2)耐酸性能测试1:的推进剂完全浸泡在螯合酸中,试验条件:ph=4,140℃,15mpa,48小时。
69.(3)耐酸性能测试2:的推进剂完全浸泡在螯合酸中,试验条件:ph=3,140℃,15mpa,48小时。
70.(4)表面硬度测试:的推进剂常温下测试表面硬度。
71.本实施例的固体推进剂性能测试结果见表1。
72.表1实施例一的固体推进剂性能测试结果
73.测试项目试验条件试验结果耐水性能测试140℃,15mpa,48小时失重0.82wt%耐酸性能测试ph=4,140℃,15mpa,48小时增重0.93wt%耐酸性能测试ph=3,140℃,15mpa,48小时增重1.25wt%表面硬度22℃80d
74.从表1中可看出,该推进剂在自来水中氧化剂析出少,失重率为0.82%;在螯合酸中酸液渗入少,增重率低;固化效果好,表面硬度高80d。
75.实施例二:
76.在本实施例中,按重量百分比计,主装药为93%,包覆层为7%;
77.所述主装药按重量分数组成为:粘结剂a25%,氧化剂60%,燃速催化剂2%,稀释剂a7%,工艺添加剂a6%;
78.所述包覆层按重量分数组成为:粘结剂b90%,稀释剂b5%,工艺添加剂b5%。
79.在本实施例中,粘结剂a为酚醛环氧树脂f51,稀释剂a为苯基缩水甘油醚,工艺添加剂a为1,3-戊二胺,燃速催化剂为正丁基二茂铁,氧化剂为硝酸钾。
80.粘结剂b为酚醛环氧树脂f51,稀释剂b为环氧丙烷邻甲苯基醚,工艺添加剂b为2-甲基戊二胺。
81.按照以下方法制备:
82.步骤一,按配方比例将粘结剂a(酚醛环氧树脂f51)、稀释剂a(苯基缩水甘油醚)、工艺添加剂a(1,3-戊二胺)加入立式混料机内预混15min,得到预混物;
83.步骤二,向立式混料机内加入氧化剂(硝酸钾),混合35min得到药浆;
84.步骤三,将药浆浇注到模具中,并将模具放入支架中,常温固化,固化18h,固化后得到主装药;
85.步骤四,按配方比例将将粘结剂b(酚醛环氧树脂f51)、稀释剂b(环氧丙烷邻甲苯
基醚)、工艺添加剂b(2-甲基戊二胺)加入混合锅内预混15min,得到包覆层预混液;
86.步骤五,把包覆层预混液刷涂到主装药表面,共刷涂3遍,每遍间隔1小时,并把刷涂好包覆液的主装药放入支架,常温固化4h即得到产品。
87.性能测试:
88.(1)耐水性能测试:的推进剂完全浸泡在自来水中,试验条件:140℃,15mpa,48小时。
89.(2)耐酸性能测试1:的推进剂完全浸泡在螯合酸中,试验条件:ph=4,140℃,15mpa,48小时。
90.(3)耐酸性能测试2:的推进剂完全浸泡在螯合酸中,试验条件:ph=3,140℃,15mpa,48小时。
91.(4)表面硬度测试:的推进剂常温下测试表面硬度。
92.本实施例的固体推进剂性能测试结果见表2。
93.表2实施例二的固体推进剂性能测试结果
94.测试项目试验条件试验结果耐水性能测试140℃,15mpa,48小时失重0.75wt%耐酸性能测试ph=4,140℃,15mpa,48小时增重0.90wt%耐酸性能测试ph=3,140℃,15mpa,48小时增重1.15wt%表面硬度22℃83d
95.从表2中可看出,该推进剂在自来水中氧化剂析出少,失重率低,为0.75wt%;在螯合酸中酸液渗入少,增重率低;固化效果好,表面硬度高。
96.实施例三:
97.本实施例与实施例一相比不同的是,本实施例中按重量百分比计,主装药为98%,包覆层为2%;
98.所述主装药按重量分数组成为:粘结剂a25%,氧化剂50%,燃速催化剂5%,稀释剂a10%,工艺添加剂a10%;
99.所述包覆层按重量分数组成为:粘结剂b85%,稀释剂b8%,工艺添加剂b7%。
100.本实施例的固体推进剂耐酸性能测试所使用的酸液为盐酸。
101.本实施例的固体推进剂性能测试结果见表3。
102.表3实施例三的固体推进剂性能测试结果
103.测试项目试验条件试验结果耐水性能测试140℃,15mpa,48小时失重0.98wt%耐酸性能测试ph=4,140℃,15mpa,48小时增重0.99wt%耐酸性能测试ph=3,140℃,15mpa,48小时增重1.35wt%表面硬度23℃79d
104.从表3中可看出,该推进剂在自来水中氧化剂析出少,失重率低,为0.98wt%;在盐酸中酸液渗入少,增重率低;固化效果好,表面硬度高,为79d。
105.实施例四:
106.本实施例与实施例二相比不同的是,本实施例中按重量百分比计,主装药为96%,
包覆层为4%;
107.所述主装药按重量分数组成为:粘结剂a15%,氧化剂63%,燃速催化剂6%,稀释剂a8%,工艺添加剂a8%;
108.所述包覆层按重量分数组成为:粘结剂b87%,稀释剂b4%,工艺添加剂b9%。
109.本实施例的固体推进剂耐酸性能测试所使用的酸液为盐酸。
110.本实施例的固体推进剂性能测试结果见表3。
111.表4实施例四的固体推进剂性能测试结果
112.测试项目试验条件试验结果耐水性能测试140℃,15mpa,48小时失重0.90wt%耐酸性能测试ph=4,140℃,15mpa,48小时增重0.89wt%耐酸性能测试ph=3,140℃,15mpa,48小时增重1.05wt%表面硬度23℃83d
113.从表4中可看出,该推进剂在自来水中氧化剂析出少,失重率低,为0.90wt%;在盐酸中酸液渗入少,增重率低;固化效果好,表面硬度高,83d。
114.对比例1:
115.本对比例的主装药的重量分数组成和制备工艺与实施例2相同,与实施例2区别在于不采用包覆层。
116.本对比例的固体推进剂性能测试结果见表5。
117.表5对比例1的固体推进剂性能测试结果
[0118][0119][0120]
从表5中可看出,该推进剂在自来水中氧化剂析出多,失重率高,为2.39wt%;在盐酸中酸液渗入多,增重率2%以上。
[0121]
从实施例2的结果和本对比例的结果对比可以看出:在主装药重量分数组成相同的情况下,有包覆层的推进剂因为有包覆层的存在减少了氧化剂析出,失重率更低,为0.75wt%,而无包覆层的推进剂的失重率为2.39wt%;对比在酸液中因酸液渗入导致的增重率,有包覆层的推进剂因为有包覆层的存在减少了酸液渗入,与无包覆层的推进剂相比,增重率更低(小于2wt%)。
[0122]
对比固体推进剂的表面硬度,在有包覆层的情况下(实施例1~4),固体推进剂的表面硬度均大于80d,而对比例1中,不存在包覆层的情况下,固体推进剂的表面硬度为72d。说明包覆层的存在有利于提高固体推进剂的表面硬度,稀释剂为活性稀释剂,在降低固化体系粘度,增加流动性,改善操作性的同时与工艺添加剂进行交链反应,形成网状结构,增加产品表面硬度,提高固化效果。
[0123]
在有包覆层的情况下,对比不同包覆层含量的推进剂在自来水中因氧化剂析出导致的失重率以及在酸液中酸液渗入导致的增重率,随着包覆层含量升高,推进剂失重率和增长率均降低。
[0124]
以上测试结果表明:包覆层的存在,能有效降低推进剂主装药在水中氧化剂析出和推进剂在酸液中酸液渗入程度,使推进剂在水中或酸性溶液中保持性能稳定。
[0125]
该固体推进剂在火焰、金属射流或爆轰波等外界作用下燃烧生成大量气体,并释放热量。该固体推进剂耐水性能优异,在清水中浸泡48小时,失重率小于1%;在ph3-4的螯合酸性完井液中浸泡48小时,增重率小于2%。该固体推进剂有利于增强装药在井液中稳定性,确保可靠点火燃烧。该推进剂制备工艺简单,生产效率高,便于大规模生产应用。
[0126]
为了使本技术领域的人员更清楚的理解本发明中的技术方案,上面给出的实例是对本发明做出的详细阐述。显然,所描述的实施例只是本发明的一部分,不能理解为对本发明保护范围的限制。本领域的技术人员没有做出创造性劳动前提下所获得的其他实施例,都属于本发明的保护范围。