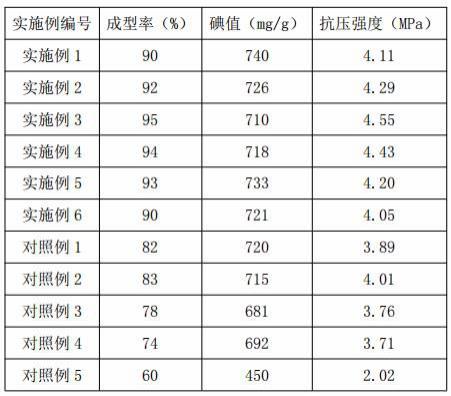
1.本发明涉及活性炭的技术领域,尤其涉及具有一定构型的活性炭的技术领域,具体而言,涉及活性炭、制备活性炭的原料和坯体以及坯体的制备方法。
背景技术:2.蜂窝状活性炭具有开孔率高、几何表面积大、耐磨损、抗粉尘能力强的优点,且床层压力损失小,吸附脱附速度快,可以很方便的用于气体净化、溶剂回收及作为催化剂的载体。目前,蜂窝状活性炭的制备方法包括涂载法与整体挤出法,其中涂载法由于容易发生涂层脱落的原因而很少使用,整体挤出法是目前国内使用最广泛的制备方法。整体挤出法的主要步骤是将煤质炭粉、粘结剂、水等原料进行混合、捏合和挤出成型,其中,原料及原料的配比是影响蜂窝状活性炭成型率、性能和应用的主要原因。
3.目前,传统配方和挤出工艺的蜂窝状活性炭的缺陷主要包括以下几方面:(1)煤的储备量有限且不可再生,开采受限,且价格上涨严重;(2)安全性较差,如以酚醛树脂为粘结剂时,内部含有甲醛,在高温下会产生危害性气体;(3)制备过程中常常需要经过陈化步骤,且还需加入专用润滑剂辅助成型,大幅度延长了蜂窝状活性炭的生产周期;(4)在生产过程容易出现蜂窝坯体不成型或成型率低,坯体湿度大导致蜂窝坯体变形等问题;(5)机械强度不足,碘值低,因此使用周期较短,无形中增加了运行成本。
技术实现要素:4.本发明的主要目的在于提供活性炭、制备活性炭的原料和坯体以及坯体的制备方法,以解决现有技术中煤质炭粉资源短缺、安全性差、生产周期长、成型率差和使用周期短的技术问题。
5.为了实现上述目的,根据本发明的第一个方面,提供了用于制备活性炭的原料,技术方案如下:用于制备活性炭的原料,包括按重量份数计的竹质炭粉55~70份、多孔黏土矿物20~50份、有机粘结剂3~8份、无机粘结剂5~10份、水22~50份。
6.作为本发明第一方面的进一步改进,所述竹质炭粉由楠竹在500~600℃炭化1~2h后得到;所述竹质炭粉的粒度≤200目。
7.作为本发明第一方面的进一步改进,所述多孔黏土矿物包括高岭土、海泡石、硅藻土中的一种或几种;所述有机粘结剂为羟丙基甲基纤维素;所述无机粘结剂为硅溶胶。
8.作为本发明第一方面的进一步改进,所述多孔黏土矿物包括高岭土5~30份、海泡石5~30份。
9.作为本发明第一方面的进一步改进,竹质炭粉和羟丙基甲基纤维素的重量比为
100:(5~10);炭粉、羟丙基甲基纤维素和多孔黏土矿物的总重量与硅溶胶的重量比为100:(6~8);竹质炭粉和水的重量比为100:(50~65)。
10.为了实现上述目的,根据本发明的第二个方面,提供了用于制备活性炭的坯体,技术方案如下:用于制备活性炭的坯体,包括上述第一方面所述的原料。
11.为了实现上述目的,根据本发明的第三个方面,提供了用于制备活性炭的坯体的制备方法,技术方案如下:用于制备活性炭的坯体的制备方法,由上述第一方面所述的原料经混合、捏合、挤出成型、干燥后得到。
12.作为本发明第三方面的进一步改进,所述混合为将竹质炭粉、有机粘结剂和多孔黏土矿物混合为预混料;所述捏合为将预混料、无机粘结剂和水混合为泥料;所述挤出成型为在10~20mpa的成型压力下将泥料挤出成型为具有蜂窝孔状结构的坯体。
13.为了实现上述目的,根据本发明的第四个方面,提供了活性炭,技术方案如下:活性炭,由上述第二方面所述的坯体或第三方面所述的制备方法制备得到的坯体经二次炭化和活化后得到。
14.作为本发明第四方面的进一步改进,二次炭化为在500~600℃炭化1~2h;活化为在850~950℃活化1~2h;活性炭呈蜂窝状。
15.为了实现上述目的,根据本发明的第五个方面,提供了活性炭的制备方法,技术方案如下:活性炭的制备方法,包括步骤:获取上述第二方面所述的坯体或第三方面所述的制备方法制备得到的坯体;对坯体进行二次炭化和活化,即得到活性炭。
16.本发明具有以下优点:由于竹材中富含有丰富的纤维素、半纤维素和木质素,这些物质热解后会形成丰富的孔道结构,因此竹质炭粉具备较高的比表面积,能够提升活性炭的应用效果;同时,竹材具有可再生特点,尤其是楠竹的生长周期较短,分布范围广,因此,采用竹质炭粉能够显著降低蜂窝状活性炭的生产成本。
17.有机粘结剂和无机粘结剂相互配合,不仅粘结效果好,而且粘结剂种类的选择范围更宽,有助于提升粘结剂的使用安全性。尤其是,当有机粘结剂为羟丙基甲基纤维素时,由于羟丙基甲基纤维素溶于水后具有较高的表面活性以及润滑性,同时还具有增稠能力、ph稳定性、保水性、稳定性、优良的成膜性以及分散性和粘结性等优点,使得不需要陈化等待便可使其在水分中分布非常均匀。当无机粘结剂为硅溶胶时,硅溶胶不仅可以发挥粘结作用,而且由于硅溶胶中胶体粒子的粒度非常小(一般为5~100nm),故有着相当大的比表面积,能很好的分散在物料中,同时,硅溶胶在加热后会脱去水分子,形成si-o-si键,该键形成的网状孔隙不仅可起到支撑骨架的作用,而且当硅溶胶和纤维素类物质共同使用时,其网状孔隙可以屏蔽残余的羟基,减少样品对水的敏感性从而起到增加耐水性的作用。
18.多孔黏土矿物的颗粒较细,具有较大的比表面积、独特的孔道结构和一定的吸附性能,与其它原料混合后具有较好的塑性,在捏合过程中可起到一定的辅助成型的作用,从而显著提升蜂窝状坯体的成型率;并且,多孔黏土矿物具有极高的热稳定性,在后续二次炭化和活化过程中可作为骨架结构对整体进行支撑,使得坯体的构型在高温煅烧下也不会发
生改变,从而确保活性炭的产品构型。尤其是当多孔黏土矿物为高岭土和海泡石的组合时,塑性和热稳定性最好,能够获得最优的成型率。
19.可见,本发明的蜂窝状活性炭采用的原料成本低,不使用有害性原料,无需陈化,显著缩短生产周期,制备蜂窝状活性炭的成型率高,无开裂及变形等缺陷,显著提升生产效率。经验证,所得蜂窝状活性炭的碘值和抗压强度高,具有较强的耐水性和耐水冲击性,可稳定应用于有水环境中,显著延长使用周期,具有极强的实用性。很明显,由于本发明在制备蜂窝状活性炭时具备优异的成型率,因此,除了制备蜂窝状构型之外,本发明的原料也可以用于制备其它构型的活性炭。
20.下面通过具体实施方式对本发明做进一步的说明。本发明附加的方面和优点将在下面的描述中部分给出,部分将从下面的描述中变得明显,或通过本发明的实践了解到。
具体实施方式
21.下面对本发明进行清楚、完整的说明。本领域普通技术人员在基于这些说明的情况下将能够实现本发明。在对本发明进行说明前,需要特别指出的是:本发明中在包括下述说明在内的各部分中所提供的技术方案和技术特征,在不冲突的情况下,这些技术方案和技术特征可以相互组合。
22.此外,下述说明中涉及到的本发明的实施例通常仅是本发明一部分的实施例,而不是全部的实施例。因此,基于本发明中的实施例,本领域普通技术人员在没有做出创造性劳动的前提下所获得的所有其他实施例,都应当属于本发明保护的范围。
23.关于本发明中术语和单位,本发明的说明书和权利要求书及有关的部分中的术语“包括”、“具有”以及它们的任何变形,意图在于覆盖不排他的包含。
24.术语“成型率”的含义是指在规定挤出坯体个数内,挤出后的完整蜂窝坯体个数与经过成型机成型的总的蜂窝坯体个数之比。术语“蜂窝状”是指沿坯体或活性炭的轴向间隔排列有孔道,孔道的横断面可以是圆形或矩形,坯体或活性炭的外形可以是圆形或棱柱形。
25.本发明的用于制备活性炭的原料的具体实施方式为由按重量份数计的竹质炭粉55~70份、多孔黏土矿物20~50份、有机粘结剂3~8份、无机粘结剂5~10份和水22~50份构成。其中,所述竹质炭粉由干燥的楠竹在600℃炭化2h后得到,炭化气氛为氮气,竹质炭粉的粒度为200目。所述多孔黏土矿物由高岭土和海泡石构成。所述有机粘结剂为羟丙基甲基纤维素(以下以“hpmc”表示)。所述无机粘结剂为硅溶胶。
26.所述多孔黏土矿物包括高岭土5~30份、海泡石5~30份,优选地,高岭土和海泡石的重量比为1:1。
27.竹质炭粉和羟丙基甲基纤维素的重量比(以下以“比例1”表示)为100:(5~10);炭粉、羟丙基甲基纤维素和多孔黏土矿物的总重量与硅溶胶的重量比(以下以“比例2”表示)为100:(6~8);竹质炭粉和水的重量比(以下以“比例3”表示)为100:(50~65)。
28.本发明的用于制备活性炭的坯体的具体实施方式为包括上述的原料或由以下的坯体的制备方法制备而成。
29.本发明的用于制备活性炭的坯体的制备方法的具体实施方式为由上述的原料经混合、捏合、挤出成型、干燥后得到,所述混合为将竹质炭粉、有机粘结剂和多孔黏土矿物在高速混合机中混合为预混料,所述捏合为将预混料、无机粘结剂和水在捏合机中混合为泥
料,所述挤出成型为在液压挤出机和15mpa的成型压力下将泥料挤出成型为具有蜂窝孔状结构的坯体,所述干燥为自然晾干24h以上。
30.本发明的活性炭的具体实施方式为由上述的坯体或上述的制备方法制备得到的坯体经二次炭化和活化后得到。
31.本发明的活性炭的制备方法的具体实施方式为包括步骤:获取上述的坯体或上述的制备方法制备得到的坯体;对坯体进行二次炭化和活化,即得到活性炭。
32.在上述的活性炭及其制备方法中,二次炭化为在600℃炭化2h,二次炭化气氛为氮气,活化为在850℃活化3h,活化气氛为二氧化碳。
33.所述的坯体和活性炭均呈蜂窝状,孔道的横断面为矩形,呈阵列状排列,外形为四棱柱形。呈蜂窝状的一种实施例为:四棱柱的长度为100mm,横断面为方形,边长为100mm,孔道的横断面为方形,孔道呈20*20排列。
34.以下通过具体的实施例来说明本发明的有益效果。
35.实施例1-6和对照例1-5的原料及其重量份数配比见表1。对照例1-2与实施例3的区别在于仅采用一种多孔黏土矿物。对照例3-4与实施例3的区别在于仅采用一种粘结剂。对照例5与实施例3的区别在于以30份淀粉代替多孔黏土矿物。
36.对应得到的蜂窝状活性炭的成型率、碘值和抗压强度见表2。
37.表1 表2
结合表1和表2可以看出,采用本发明的原料及其配比所制备得到的蜂窝状活性炭同时具备高成型率、高碘值和高抗压强度,说明其生产效率高,比表面积大,吸附性能好,抗压能力强,因此,具有极强的实用性。
38.通过对比实施例3、对照例1-2和对照例5可知,多孔黏土矿物尤其是由高岭土和海泡石组合而成的多孔黏土矿物能显著提升蜂窝状活性炭的成型率和抗压强度。
39.通过对比实施例3和对照例3-4可知,hpmc和硅溶胶的组合能显著提升蜂窝状活性炭的成型率和抗压强度。
40.所述的碘值采用“gb/t14296.8-2015 木质活性炭实验方法碘吸附值的测定”进行测试。
41.所述的抗压强度采用“gb/t 1964-1996多孔陶瓷压缩强度试验方法”进行测试。
42.以上对本发明的有关内容进行了说明。本领域普通技术人员在基于这些说明的情况下将能够实现本发明。基于本发明的上述内容,本领域普通技术人员在没有做出创造性劳动的前提下所获得的所有其他实施例,都应当属于本发明保护的范围。