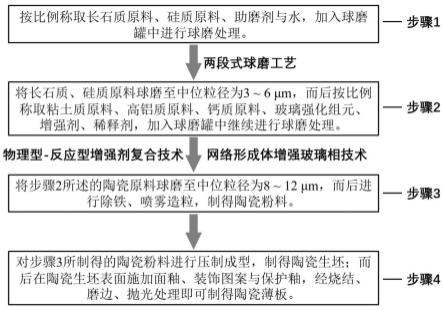
1.本发明涉及建筑陶瓷技术领域,具体涉及一种高强度陶瓷薄板及其制备方法。
背景技术:2.陶瓷薄板具有低吸水率、规格尺寸大、厚度薄、节能降耗、清洁环保、轻质高强等特点,建筑陶瓷薄型化制造是建筑陶瓷行业实现节约资源、节能减排的重要途径,符合国家“绿色低碳制造”的发展目标。然而,建筑陶瓷减薄之后,其承载能力(破坏强度)会显著减小,导致其服役安全性与可靠性降低。因此,提高建筑陶瓷板材的力学性能(开发力学强化技术)是实现“减薄不减质”的有效手段,也是目前生产建筑陶瓷薄板亟须解决的问题。
3.为提升建筑陶瓷的力学性能,国内外学者开展了大量研究,所开发的力学强化技术主要包括:颗粒弥散增强、基体强化、晶须/纤维增强、原位增强等。然而,目前所开发的力学强化方法主要是通过优化调控陶瓷结晶相组成、分布、含量、微观结构等来提升建筑陶瓷的力学性能,鲜见通过调控玻璃相组成与物理性能实现建筑陶瓷力学强化的研究报道。建筑陶瓷结晶相调控通常采用外掺或原位生成的方法:现有建筑陶瓷球磨分散与均化处理很难实现外掺增强相在陶瓷基体中的均匀分散;原位生成增强相组元通常需要对原料粉体进行一定的预处理(酸洗、碱活化等)或引入矿化剂,该强化方法需要较高的烧结温度或较长的保温时间,不利于陶瓷薄板的低碳制造,预处理也会带来一定的环境污染问题,且矿化剂的高温挥发对窑炉与产线工人健康均存在不利影响。
4.现有建筑陶瓷的力学强化主要是通过外掺或原位生成的方法在陶瓷中引入颗粒、晶须/纤维增强相实现的,例如:景德镇陶瓷大学通过掺加30%的α-al2o3微粉作为弥散增强相,有效提升了瓷坯的弯曲强度(提高大规格超薄建筑陶瓷砖瓷坯性能的研究[j]. 陶瓷学报, 2006, 27(3): 243-249);张电等人通过在建筑陶瓷中引入al2o3、zro2短纤维,实现陶瓷弯曲强度的提升(zro2短纤维增强体相变及对瓷质陶瓷性能的影响[j]. 建筑材料学报, 2017, 20(6): 909-913;al2o3短纤维增强薄型瓷质陶瓷的试验研究[j]. 建筑材料学报, 2018, 21(1): 174-178);刘一军等人以粉煤灰、铝矾土与叶腊石等为原料,以alf3为矿化剂,在陶瓷薄板中原位引入了针状/棒状莫来石微晶,成功制得了弯曲强度高达96 mpa的陶瓷薄板(高强度莫来石陶瓷微晶薄板的研究[j].人工晶体学报, 2010,39(s1): 156-159)。上述方法存在以下缺点:
①
实现外掺增强相在陶瓷基体中均匀分散的难度较大;
②
外掺增强相会导致陶瓷烧结温度增加,不利于陶瓷薄板的绿色制造;
③
为促使原位析晶,通常需要高温长时间烧结处理,会增加陶瓷的烧结能耗;
④
为提升原位增强效果,通常需要对原料粉体进行酸洗或碱活化处理,会带来一定的环境问题以及增加陶瓷企业废水处理难度;
⑤
为进一步促进原位析晶,通常需要引入一定量的矿化剂,矿化剂的高温挥发对窑炉与产线工人健康均存在不利影响。
技术实现要素:[0005]
针对上述五大缺点,本发明提出一种高强度陶瓷薄板及其制备方法,利用原料粉
体粒径与化学组成设计,基于玻璃相增强及其物理性能优化有效提升建筑陶瓷的力学强度,以及在不改变现有建筑陶瓷低温快烧工艺以及确保绿色低碳制造的前提下,大幅度提升陶瓷薄板的力学性能。
[0006]
第一方面,本发明提供一种高强度陶瓷薄板。所述高强度陶瓷薄板的原料组成包括:以质量百分比计,长石质原料10~18wt%、硅质原料20~30 wt%、粘土质原料30~40wt%、高铝质原料6~12wt%、钙质原料5~25wt%、玻璃强化组元3~15wt%;所述玻璃强化组元为硼质原料和磷质原料的混合物;硼质原料为硼酸锌、氧化硼、硼酸中的至少一种,占高强度陶瓷薄板的原料组成的1~5 wt%;磷质原料为磷酸钙、磷酸氢钙、磷酸铝、次磷酸铝、磷酸二氢铝中的至少一种,占高强度陶瓷薄板的原料组成的2~10 wt%。
[0007]
较佳地,长石质原料为钾砂、钠砂、钾铝砂、钾长石、钠长石中的至少一种;硅质原料为硅砂和/或硅微粉;粘土质原料为高岭土、球土、滑石泥、膨润土、伊利石的至少一种;高铝质原料为煅烧铝矾土、氧化铝、铝土矿中的至少一种;钙质原料为硅灰石、钙长石、方解石中的至少一种。
[0008]
第二方面,本发明提供一种高强度陶瓷薄板的制备方法。
[0009]
选用难溶于水的玻璃强化组元时,所述制备方法包括以下步骤:步骤1,称取长石质原料、硅质原料与水,进行第一球磨处理;步骤2,将长石质原料、硅质原料球磨至中位粒径为3~6 μm,而后加入称取的粘土质原料、高铝质原料、钙质原料、难溶于水的玻璃强化组元,继续进行第二球磨处理;步骤3,将步骤2的所有原料球磨至中位粒径为8~12 μm,而后进行除铁、喷雾造粒,制得陶瓷坯料;步骤4,对陶瓷坯料进行压制成型,制得陶瓷生坯,经烧成获得所述高强度陶瓷薄板。
[0010]
选用易溶于水的玻璃强化组元时,所述制备方法包括以下步骤:步骤1,称取长石质原料、硅质原料与水,进行第一球磨处理;步骤2,将长石质原料、硅质原料球磨至中位粒径为3~6 μm,而后加入称取的粘土质原料、高铝质原料、钙质原料,继续进行第二球磨处理;步骤3,将步骤2的所有原料球磨至中位粒径为8~12 μm,而后进行除铁、喷雾造粒,制得陶瓷粉料;步骤4,将陶瓷粉料和易溶于水的玻璃强化组元干混后制成陶瓷坯料,进行压制成型,制得陶瓷生坯,经烧成获得所述高强度陶瓷薄板。
[0011]
较佳地,所述陶瓷坯料的化学组成包括:以质量百分比计,sio
2 57~60%;al2o
3 19~21%;fe2o
3 0.5~1.1%;tio
2 0.2~0.6%;cao 4.5~7.3%;mgo 0.3~1.0%;k2o 1.2~2.0%;na2o 0.5~1.2%;zno 0.4~1.9%;b2o
3 0.5~2.4%;p2o
5 1.0~4.6%;烧失量 3~7%。
[0012]
较佳地,第一球磨处理时,除了长石质原料、硅质原料以外,还称取占长石质原料和硅质原料总质量的0.5~1.5%的助磨剂;所述助磨剂为聚磷酸钠、硅酸钠、聚磷酸铵中的至少一种。
[0013]
较佳地,第二球磨处理时,还称取占高强度陶瓷薄板的原料组成的0.3~1.5wt%的增强剂;所述增强剂为物理型-反应型复合增强剂,由物理型增强剂和酚醛树脂按照质量比为1:(0.5~1)组成,其中,物理型增强剂为黄糊精、纤维素醚、改性淀粉中的至少一种。
[0014]
较佳地,第二球磨处理时,还称取占高强度陶瓷薄板的原料组成的0.5~1.0wt%的稀释剂;所述稀释剂为水玻璃、腐殖酸钠、聚丙烯酸钠中的至少一种。
[0015]
较佳地,最高烧成温度为1110 ~ 1160 ℃,高温保火时间为15 ~ 30 min。
[0016]
较佳地,所述制备方法还包括:烧成前在陶瓷生坯表面施加面釉、装饰图案与施加保护釉的工序。
[0017]
有益效果
①
本发明通过对长石质原料、硅质原料进行两段式球磨处理以及硼质原料、磷质原料的引入,提升建筑陶瓷玻璃相中网络形成体(sio2、b2o3、p2o5)含量:一方面可提升玻璃相自身的力学强度;另一方面可降低玻璃相的热膨胀系数,从而增大玻璃相与结晶相之间的热失配,导致玻璃相中残余压应力增大,继而可进一步提升陶瓷薄板的力学性能;二者共同作用,有利于实现陶瓷薄板力学强度的大幅度提升。
[0018]
②
本发明采用物理型-反应型增强剂复合技术增加陶瓷颗粒粘结致密程度,从而降低淋釉或喷釉中水分向生坯的渗透速率,提升陶瓷薄板的湿坯强度,可减少陶瓷生坯在走线过程中的烂砖与暗裂,提升陶瓷薄板的良品率。
[0019]
③
本发明提出的网络形成体增强玻璃相技术,可解决高钙玻璃体系高温料性短的技术难题,从而可扩宽高钙陶瓷体系的烧成范围。利用cao取代断网能力强的k2o、na2o,可以增强玻璃网络的连接程度,有利于确保玻璃相自身较高的力学强度;而且钙质原料的析晶能力较强,可增加建筑陶瓷的结晶相含量;二者协同作用,有利于提升陶瓷薄板的力学强度。
附图说明
[0020]
为了更清楚地说明本发明实施例或现有技术中的技术方案,下面将对实施例或现有技术描述中所需要使用的附图作简单介绍。
[0021]
图1为本发明提供的一种高强度陶瓷薄板制备方法的工艺流程图。
具体实施方式
[0022]
通过下述实施方式进一步说明本发明,应理解,下述实施方式仅用于说明本发明,而非限制本发明。在没有特殊说明的情况下,各百分含量指质量百分含量。
[0023]
建筑陶瓷通常是以玻璃相/非晶相为主相,其含量通常≥60wt%,因此玻璃相本征强度对于建筑陶瓷的力学强化是至关重要的;且玻璃相物理性能的调控也会对颗粒弥散增强、基体强化效果产生影响。本发明利用玻璃相自身的强化,并调控玻璃相与结晶相(石英、莫来石)之间的热失配,基于复合强化和残余应力强化机制,通过二者的综合作用提升建筑陶瓷的力学性能。有鉴于此,本发明基于玻璃相组成设计,提出了一种高强度陶瓷薄板,可大幅度提升建筑陶瓷的力学性能。
[0024]
本发明所述高强度陶瓷薄板的原料组成包括:以质量百分比计,长石质原料10~18wt%、硅质原料20~30wt%、粘土质原料30~40wt%、高铝质原料6~12wt%、钙质原料5~25wt%、玻璃强化组元3~15wt%。
[0025]
长石质原料、硅质原料、粘土质原料、高铝质原料、钙质原料的选择不受限制,采用本领域的常用原料即可。以下仅为示例,长石质原料为钾砂、钠砂、钾铝砂、钾长石、钠长石
1160 ℃,高温保火时间为15~30 min。
[0035]
璃强化组元选取硼质原料(氧化硼、硼酸)和磷质原料(磷酸二氢铝),硼质原料和磷质原料均难溶于水,氧化硼、硼酸、磷酸二氢铝易溶于水,且溶于水后会改变陶瓷浆料的ph值,继而易导致陶瓷浆料触变,且难以解胶,因此不可直接将氧化硼/硼酸、磷酸二氢铝与陶瓷原料混合进行球磨处理。可将长石质原料、硅质原料、粘土质原料、高铝质原料、钙质原料等球磨处理后,进行喷雾造粒,而后通过干混的方式(干粉混料机)引入氧化硼/硼酸、磷酸二氢铝,继而将b2o3和p2o5引入至玻璃相中,实现陶瓷薄板的力学强化。但是,干混方法很难实现硼质原料、磷质原料在陶瓷基体中的均匀分散,会对陶瓷薄板的力学强化效果产生一定影响;且该方法增加了制造工序,会造成经济成本的提高。
[0036]
选用易溶于水的玻璃强化组元时,高强度陶瓷薄板的制备方法包括以下步骤:称取长石质原料、硅质原料与水,进行第一球磨处理。水的含量为陶瓷薄板原料的总质量的45~55wt%。将长石质原料、硅质原料球磨至中位粒径为3~6 μm,而后加入称取的粘土质原料、高铝质原料、钙质原料,继续进行第二球磨处理。将所有陶瓷原料球磨至中位粒径为8~12 μm,而后进行除铁、喷雾造粒,制得陶瓷粉料。将陶瓷粉料和易溶于水的玻璃强化组元干混后制成陶瓷坯料,进行压制成型,制得陶瓷生坯,经烧成获得所述高强度陶瓷薄板。陶瓷薄板的烧成温度为1110~1160 ℃,高温保火时间为15~30 min。
[0037]
本发明选用两段式球磨工艺,首先对长石质原料与硅质原料进行第一球磨处理(预球磨处理),而后加入粘土质原料、高铝质原料、钙质原料等进行第二球磨处理,且设计长石质原料与硅质原料第一球磨处理后的中位粒径小于所有陶瓷原料在第二球磨处理后的中位粒径。中位粒径(d
50
)表示样品的累计粒度分布百分数达到50%时所对应的粒径。
[0038]
利用两段式球磨工艺,仅对长石质原料与硅质原料进行深度球磨处理,而其他原料(粘土质原料、高铝质原料、钙质原料)仍保留建筑陶瓷生产常规细度,这样可避免全部原料深度球磨带来的能耗问题,同时也可确保陶瓷薄板的烧成收缩率不会明显增大。
[0039]
更加重要的是,由于长石质原料和硅质原料中均含有较多的石英,且石英在陶瓷烧结过程会熔解于非晶相,但是当石英颗粒较粗时,只能发生颗粒外缘局部熔解,导致玻璃相中sio2含量较低,网络形成体含量的减少也会导致玻璃相本征强度降低。因此,本发明通过第一球磨处理降低长石质原料和硅质原料中石英的细度,促进石英在非晶液相中的熔解,继而增加玻璃相中的sio2含量。增加玻璃相中的sio2含量也可以促进网络形成体的生成。这一方面,有利于增加网络形成体含量,提升玻璃相自身的力学强度;另一方面,有利于降低玻璃相的热膨胀系数,从而增大玻璃相与结晶相间的热失配,可优化玻璃相基体残余应力强化效果;二者的共同作用可提升陶瓷薄板的力学强度。
[0040]
不仅如此,长石质原料粒径的降低有利于降低建筑陶瓷的烧结温度,可实现建筑陶瓷薄板的绿色低碳制造。
[0041]
一些技术方案中,所述陶瓷坯料的化学组成包括:以质量百分比计,sio
2 57~60%;al2o
3 19~21%;fe2o
3 0.5~1.1%;tio
2 0.2~0.6%;cao 4.5~7.3%;mgo 0.3~1.0%;k2o 1.2~2.0%;na2o 0.5~1.2%;zno 0.4~1.9%;b2o
3 0.5~2.4%;p2o
5 1.0~4.6%;烧失量 3~7%。陶瓷原料的比例影响陶瓷粉料的化学组成。
[0042]
常规建筑陶瓷通常采用高钾低钠体系,这是因为高钾低钠体系玻璃料性长,建筑陶瓷的烧成范围较宽,且陶瓷砖形也易于调整。本发明选用的是高钙体系配方(cao含量高,
而k2o、na2o含量低),这是在传统建筑陶瓷领域鲜见的,其原因在于:cao含量较高的玻璃相的高温料性短,易导致陶瓷烧成范围较窄;而且,这会导致玻璃相的高温粘度显著降低,导致陶瓷坯体的抗变形能力比较差。本发明在上述高钙体系的基础上通过引入玻璃强化组元增加了陶瓷玻璃相中网络形成体(sio2、b2o3、p2o5)的含量,有利于延长玻璃相的高温料性。所以本发明选用了高钙体系熔剂,这将带来两方面的益处:
①ꢀ
cao对玻璃网络的断网能力弱于k2o、na2o,因此选用高钙体系熔剂可以增强玻璃网络的连接程度,有利于确保玻璃相自身较高的力学强度;
②ꢀ
钙质原料的析晶能力较强,可增加建筑陶瓷的结晶相含量,继而有利于提升陶瓷薄板的力学强度。
[0043]
一些技术方案中,第一球磨处理时,除了长石质原料、硅质原料以外,还称取占长石质原料和硅质原料总质量的0.5~1.5%的助磨剂。助磨剂包括但不限于聚磷酸钠、硅酸钠、聚磷酸铵中的至少一种。助磨剂优选聚磷酸铵,其不仅可提升长石质原料与硅质原料的球磨效率,而且可在陶瓷配方体系中引入玻璃网络形成体(p2o5)。
[0044]
一些技术方案中,第二球磨处理时,还称取占陶瓷薄板原料总质量的0.3~1.5 wt%的增强剂。所述增强剂为物理型-反应型复合增强剂。采用物理型-反应型增强剂复合技术提升建筑陶瓷生坯的力学强度,可减少陶瓷生坯在走线过程中的烂砖与暗裂,提升陶瓷薄板的良品率。物理型增强剂包括但不限于黄糊精、纤维素醚、改性淀粉中的至少一种。一些技术方案中,增强剂由物理型增强剂和酚醛树脂按照质量比为1:(0.5~1)组成。利用反应型增强剂(酚醛树脂)提升物理型增强剂分子链之间的缠绕和交联作用,增加陶瓷颗粒粘结致密程度,从而可有效降低淋釉或喷釉中水分向生坯的渗透速率,提升陶瓷薄板的湿坯强度,可提升陶瓷薄板产品的良品率。作为优选,物理型-反应型增强剂由黄糊精和酚醛树脂按照质量比为1:1组成。
[0045]
一些技术方案中,第二球磨处理时,还称取占陶瓷薄板原料总质量的0.5~1.0wt%的稀释剂;所述稀释剂为水玻璃、腐殖酸钠、聚丙烯酸钠中的至少一种。
[0046]
还可以在烧成后对陶瓷薄板进行磨边、抛光等常规处理。为了丰富陶瓷薄板的表面装饰,还可以在陶瓷生坯表面施加面釉、装饰图案与保护釉。面釉和保护釉的组成和施釉工艺采用本领域常规釉组成和施釉工艺即可。
[0047]
作为示例,高强度陶瓷薄板的制备方法包括以下步骤:按比例称取长石质原料、硅质原料、助磨剂与水,加入球磨罐中进行球磨处理。将长石质原料、硅质原料球磨至中位粒径为3~6 μm,而后按比例称取粘土质原料、高铝质原料、钙质原料、玻璃强化组元、增强剂、稀释剂,加入球磨罐中继续进行球磨处理。将陶瓷原料球磨至中位粒径为8~12 μm,而后进行除铁、喷雾造粒,制得陶瓷粉料;对制得的陶瓷粉料进行压制成型,制得陶瓷生坯;经烧结、磨边、抛光处理即可制得陶瓷薄板。
[0048]
综上,本发明基于原料粉体粒径与化学组成设计,采用一种简单有效的方法改变建筑陶瓷中玻璃相的组成与物理性能,基于玻璃相增强与残余应力强化,实现建筑陶瓷薄板的力学强化。而且,本发明通过对长石质原料和硅质原料进行了深度球磨处理,且设计以cao、zno为主要助熔剂的陶瓷配方,有利于降低高强度陶瓷薄板的烧结温度,继而可促进陶瓷薄板的绿色低碳制造。
[0049]
下面进一步列举实施例以详细说明本发明。同样应理解,以下实施例只用于对本发明进行进一步说明,不能理解为对本发明保护范围的限制,本领域的技术人员根据本发
明的上述内容作出的一些非本质的改进和调整均属于本发明的保护范围。下述示例具体的工艺参数等也仅是合适范围中的一个示例,即本领域技术人员可以通过本文的说明做合适的范围内选择,而并非要限定于下文示例的具体数值。
[0050]
下述实施例和对比例使用的陶瓷原料及其化学组成如下表1所示。
[0051]
表1 陶瓷原料种类及其化学组成(wt%)实施例1本技术实施例1提供了一种高强度陶瓷薄板及其制备方法,具体步骤如下:1、称取5质量份钾砂、3质量份钠砂、3质量份钾铝砂、10.5质量份硅砂、15质量份硅微粉、0.5质量份的聚磷酸铵与50质量份的自来水,加入球磨罐中,进行球磨处理,并随时监测长石质原料与硅质原料的球磨细度;2、当长石质原料与硅质原料球磨至中位粒径为3 μm时,停止球磨;称取8质量份高岭土、20质量份球土、3质量份滑石泥、3质量份膨润土、3质量份伊利石、10质量份煅烧铝矾土、9.5质量份硅灰石、5质量份硼酸锌、2质量份磷酸钙、0.5质量份水玻璃、0.15质量份黄糊精与0.15质量份酚醛树脂,加入球磨罐中,进行球磨处理,并随时监测原料的球磨细度;3、当步骤2的所有陶瓷原料球磨至中位粒径为12 μm时,停止球磨;除铁后,陈腐24 h;最后进行喷雾造粒,制得陶瓷坯料;所述陶瓷坯料的化学组成包括:以质量百分比计,sio
2 60.0%;al2o
3 20.0%;fe2o
3 0.7%;tio
2 0.3%;cao 4.5%;mgo 1.0%;k2o 1.7%;na2o 0.6%;zno 1.9%;b2o
3 2.4%;p2o
5 1.0%;烧失量 5.9%;4、对制得的陶瓷坯料进行干压成型制得陶瓷坯体;5、陶瓷坯体经喷涂面釉、喷墨打印装饰图案、喷涂保护釉后,在高温辊道窑中进行烧成,最高烧成温度为1110℃,高温保火时间为15 min;6、磨边、研磨抛光、分级、打包进仓。
[0052]
对所制得的陶瓷薄板进行切割加工,利用gb/t 3810.4-2016《陶瓷砖试验方法 第4部分:断裂模数和破坏强度的测定》测得陶瓷薄板试样的弯曲强度(断裂模数)为80.6
±
7.3 mpa。
[0053]
实施例2本技术实施例2提供了一种高强度陶瓷薄板及其制备方法,具体步骤如下:
1、称取5质量份钾砂、3质量份钠砂、3质量份钾铝砂、13质量份硅砂、15质量份硅微粉、0.5质量份的硅酸钠与50质量份的自来水,加入球磨罐中,进行球磨处理,并随时监测长石质原料与硅质原料的球磨细度;2、当长石质原料与硅质原料球磨至中位粒径为6 μm时,停止球磨;称取8质量份高岭土、20质量份球土、1质量份滑石泥、3质量份膨润土、3质量份伊利石、10质量份煅烧铝矾土、5质量份硅灰石、1质量份硼酸锌、10质量份磷酸钙、0.5质量份水玻璃、1.0质量份黄糊精与0.5质量份酚醛树脂,加入球磨罐中,进行球磨处理,并随时监测原料的球磨细度;3、当步骤2的所有陶瓷原料球磨至中位粒径为8 μm时,停止球磨;除铁后,陈腐24 h;最后进行喷雾造粒,制得陶瓷粉料;所述陶瓷粉料的化学组成包括:以质量百分比计,sio
2 57.7%;al2o
3 20.4%;fe2o
3 0.7%;tio
2 0.3%;cao 7.3%;mgo 0.5%;k2o 1.7 %;na2o 0.6 %;zno 0.4 %;b2o
3 0.5 %;p2o
5 4.6 %;烧失量 5.2%;4、对制得的陶瓷粉料进行干压成型制得陶瓷坯体;5、陶瓷坯体经喷涂面釉、喷墨打印装饰图案、喷涂保护釉后,在高温辊道窑中进行烧成,最高烧成温度为1160℃,高温保火时间为30 min;6、磨边、研磨抛光、分级、打包进仓。
[0054]
对所制得的陶瓷薄板进行切割加工,利用gb/t 3810.4-2016《陶瓷砖试验方法 第4部分:断裂模数和破坏强度的测定》测得陶瓷薄板试样的弯曲强度(断裂模数)为78.3
±
6.7 mpa。
[0055]
对比例1本对比例提供了一种制备普通建筑陶瓷的方法,所述制备工艺与实施例2基本相同,对比例1与实施例2的主要不同之处在于:实施例2中引入了硼酸锌、磷酸钙作为玻璃强化组元,而对比例1中未引入玻璃强化组元(即为传统的sio
2-al2o
3-k2o-na2o陶瓷体系)。对比例1的制备步骤如下:1、称取9质量份钾砂、11质量份钠砂、3质量份钾铝砂、10质量份硅砂、15质量份硅微粉、1.5质量份的硅酸钠与50质量份的自来水,加入球磨罐中,进行球磨处理,并随时监测长石质原料与硅质原料的球磨细度;2、当长石质原料与硅质原料球磨至中位粒径为6 μm时,停止球磨;称取8质量份高岭土、20质量份球土、3质量份滑石泥、3质量份膨润土、3质量份伊利石、10质量份煅烧铝矾土、5质量份硅灰石、0.5质量份水玻璃、1.0质量份黄糊精与0.5质量份酚醛树脂,加入球磨罐中,进行球磨处理,并随时监测原料的球磨细度;3、当步骤2的所有陶瓷原料球磨至中位粒径为8 μm时,停止球磨;除铁后,陈腐24 h;最后进行喷雾造粒,制得陶瓷粉料;所述陶瓷粉料的化学组成包括:以质量百分比计,sio
2 65.4%;al2o
3 21.9%;fe2o
3 0.7%;tio
2 0.3%;cao 2.0%;mgo 1.0%;k2o 2.1%;na2o 1.3%;p2o
5 0.05%;烧失量 5.1%;4、对制得的陶瓷粉料进行干压成型制得陶瓷坯体;5、陶瓷坯体经喷涂面釉、喷墨打印装饰图案、喷涂保护釉后,在高温辊道窑中进行烧成,最高烧成温度为1180℃,高温保火时间为30 min;6、磨边、研磨抛光、分级、打包进仓。
[0056]
对所制得的陶瓷薄板进行切割加工,利用gb/t 3810.4-2016《陶瓷砖试验方法 第
4部分:断裂模数和破坏强度的测定》测得陶瓷薄板试样的弯曲强度(断裂模数)为52.5
±
5.1 mpa。
[0057]
本对比例制得的陶瓷薄板的弯曲强度较实施例2制得陶瓷薄板的弯曲强度低33.0%,说明玻璃强化组元(硼酸锌、磷酸钙)的引入有利于大幅度提升陶瓷薄板的力学强度。
[0058]
对比例2本对比例2提供了一种建筑陶瓷薄板及其制备方法,所述制备工艺与实施例1基本相同,对比例2与实施例1的不同之处在于:实施例1中引入了硼酸锌、磷酸钙作为玻璃强化组元,而对比例2中仅引入硼酸锌作为玻璃强化组元,对比例2的制备步骤如下:1、称取5质量份钾砂、3质量份钠砂、3质量份钾铝砂、10.5质量份硅砂、15质量份硅微粉、0.5质量份的聚磷酸铵与50质量份的自来水,加入球磨罐中,进行球磨处理,并随时监测长石质原料与硅质原料的球磨细度;2、当长石质原料与硅质原料球磨至中位粒径为3 μm时,停止球磨;称取10质量份高岭土、20质量份球土、3质量份滑石泥、3质量份膨润土、3质量份伊利石、10质量份煅烧铝矾土、9.5质量份硅灰石、5质量份硼酸锌、0.5质量份水玻璃、0.15质量份黄糊精与0.15质量份酚醛树脂,加入球磨罐中,进行球磨处理,并随时监测原料的球磨细度;3、当步骤2的所有陶瓷原料球磨至中位粒径为12 μm时,停止球磨;除铁后,陈腐24 h;最后进行喷雾造粒,制得陶瓷坯料;所述陶瓷坯料的化学组成包括:以质量百分比计,sio
2 60.9%;al2o
3 20.8%;fe2o
3 0.7%;tio
2 0.3%;cao 3.4%;mgo 1.0%;k2o 1.7%;na2o 0.6%;zno 1.9%;b2o
3 2.4%;烧失量 6.2%;4、对制得的陶瓷坯料进行干压成型制得陶瓷坯体;5、陶瓷坯体经喷涂面釉、喷墨打印装饰图案、喷涂保护釉后,在高温辊道窑中进行烧成,最高烧成温度为1110℃,高温保火时间为15 min;6、磨边、研磨抛光、分级、打包进仓。
[0059]
对所制得的陶瓷薄板进行切割加工,利用gb/t 3810.4-2016《陶瓷砖试验方法 第4部分:断裂模数和破坏强度的测定》测得陶瓷薄板试样的弯曲强度(断裂模数)为67.5
±
5.9 mpa。
[0060]
本对比例2制得的陶瓷薄板的弯曲强度较实施例1制得陶瓷薄板的弯曲强度低16.2%,但仍较对比例1制得陶瓷的弯曲强度高28.9%,说明单独使用硼质原料也可提升陶瓷薄板强度,只是提升效果不及硼质原料和磷质原料组合使用。
[0061]
对比例3本技术对比例3提供了一种建筑陶瓷薄板及其制备方法,所述制备工艺与实施例1的区别在于:对比例3仅使用了单次球磨,未对长石质原料与硅质原料进行深度球磨处理。具体步骤如下:1、称取5质量份钾砂、3质量份钠砂、3质量份钾铝砂、10.5质量份硅砂、15质量份硅微粉、0.5质量份的聚磷酸铵、50质量份的自来水、8质量份高岭土、20质量份球土、3质量份滑石泥、3质量份膨润土、3质量份伊利石、10质量份煅烧铝矾土、9.5质量份硅灰石、5质量份硼酸锌、2质量份磷酸钙、0.5质量份水玻璃、0.15质量份黄糊精与0.15质量份酚醛树脂,加入球磨罐中,进行球磨处理,并随时监测原料的球磨细度;
2、当步骤1的所有陶瓷原料球磨至中位粒径为12 μm时,停止球磨;除铁后,陈腐24 h;最后进行喷雾造粒,制得陶瓷坯料;所述陶瓷坯料的化学组成包括:以质量百分比计,sio
2 60.0%;al2o
3 20.0%;fe2o
3 0.7%;tio
2 0.3%;cao 4.5%;mgo 1.0%;k2o 1.7%;na2o 0.6%;zno 1.9%;b2o
3 2.4%;p2o
5 1.0%;烧失量 5.9%;3、对制得的陶瓷坯料进行干压成型制得陶瓷坯体;4、陶瓷坯体经喷涂面釉、喷墨打印装饰图案、喷涂保护釉后,在高温辊道窑中进行烧成,最高烧成温度为1130℃,高温保火时间为15 min;5、磨边、研磨抛光、分级、打包进仓。
[0062]
对所制得的陶瓷薄板进行切割加工,利用gb/t 3810.4-2016《陶瓷砖试验方法 第4部分:断裂模数和破坏强度的测定》测得陶瓷薄板试样的弯曲强度(断裂模数)为63.8
±
6.1 mpa。
[0063]
本对比例3制得的陶瓷薄板的弯曲强度较实施例1制得陶瓷薄板的弯曲强度低20.8%,说明长石质原料与硅质原料的深度球磨处理有利于进一步提升建筑陶瓷的力学强度。
[0064]
对比例4本技术对比例4提供了一种建筑陶瓷薄板及其制备方法,其与实施例2最大的不同在于:二者第一球磨处理的原料种类不同;本对比例4对粘土质原料与高铝质原料进行了第一球磨处理,而实施例2是对长石质原料与硅质原料进行了第一球磨处理。具体步骤如下:1、称取8质量份高岭土、20质量份球土、1质量份滑石泥、3质量份膨润土、3质量份伊利石、10质量份煅烧铝矾土、0.5质量份的硅酸钠与50质量份的自来水,加入球磨罐中,进行球磨处理,并随时监测粘土质原料与高铝质原料的球磨细度;2、当粘土质原料与高铝质原料球磨至中位粒径为6 μm时,停止球磨;称取5质量份钾砂、3质量份钠砂、3质量份钾铝砂、13质量份硅砂、15质量份硅微粉、5质量份硅灰石、1质量份硼酸锌、10质量份磷酸钙、0.5质量份水玻璃、1.0质量份黄糊精与0.5质量份酚醛树脂,加入球磨罐中,进行球磨处理,并随时监测原料的球磨细度;3、当步骤2的所有陶瓷原料球磨至中位粒径为8 μm时,停止球磨;除铁后,陈腐24 h;最后进行喷雾造粒,制得陶瓷粉料;所述陶瓷粉料的化学组成包括:以质量百分比计,sio
2 57.7%;al2o
3 20.4%;fe2o
3 0.7%;tio
2 0.3%;cao 7.3%;mgo 0.5%;k2o 1.7%;na2o 0.6%;zno 0.4%;b2o
3 0.5%;p2o
5 4.6%;烧失量 5.2%;4、对制得的陶瓷粉料进行干压成型制得陶瓷坯体;5、陶瓷坯体经喷涂面釉、喷墨打印装饰图案、喷涂保护釉后,在高温辊道窑中进行烧成,最高烧成温度为1160℃,高温保火时间为30 min;6、磨边、研磨抛光、分级、打包进仓。
[0065]
对所制得的陶瓷薄板进行切割加工,利用gb/t 3810.4-2016《陶瓷砖试验方法 第4部分:断裂模数和破坏强度的测定》测得陶瓷薄板试样的弯曲强度(断裂模数)为65.6
±
4.9 mpa。
[0066]
本对比例4制得的陶瓷薄板的弯曲强度较实施例2制得陶瓷薄板的弯曲强度低16.2%,说明第一球磨处理的原料种类会影响建筑陶瓷的力学强化效果,且对长石质原料与硅质原料进行第一球磨处理有利于进一步提升建筑陶瓷的力学强度。