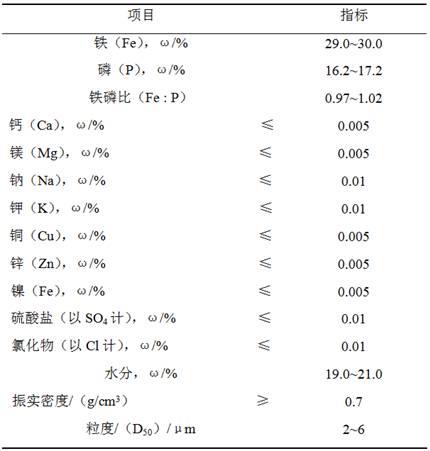
1.本发明属于废旧电池回收技术领域,具体涉及一种从废旧磷酸铁锂提锂废渣中回收制备电池级磷酸铁的方法。
背景技术:2.中国是全球锂电池使用数量最多的国家之一,每年的产量达到几十亿只,主要用于电子产品或便携式设备以及新型交通工具,如手机、笔记本电脑、电动汽车等。据资料显示,预计2020年我国新能源汽车数量将达到800万辆,2030年更可能达到9500万辆,而目前绝大部分新能源汽车使用的驱动源为磷酸铁锂电池。而磷酸铁锂电池的理论寿命仅为7~8年,如此大规模的消耗量必然产生数量庞大的废锂电池,预估到2023年中国约有9400吨磷酸铁锂电池废弃。锂电池的废弃堆积若得不到有效的处理,会造成巨大的环境污染和资源浪费。如何处理数量巨大的废旧锂电池,成为科研工作者及环保人士最关注的问题。寻找废旧锂离子电池的环境友好型处理方法,开发有效的创新性处理工艺,且考虑成本因素,在减少污染的同时获得经济价值,从而保证锂电池行业的可持续发展,推动废旧锂离子电池循环使用,已经成为推动电动车产业发展和经济社会进步的重要发展方向。
3.目前规模化回收磷酸铁锂存在的主要问题是只回收其中的锂,而剩余的大量磷酸铁还没有得到有效的回收便会做填埋处理或磷肥出售,挤占磷肥行业市场,并大大降低了其商业价值。而且提锂废料里的重金属元素会污染土壤环境,回收得到的磷酸铁纯度也并不能达到电池级标准,因此对于提锂废料里的磷酸铁进行有效回收是非常必要的。
技术实现要素:4.为了解决现有大量提锂废料存在的上述问题,本发明提供了一种利用废旧磷酸铁锂提锂废渣回收磷酸铁并提纯为电池级磷酸铁的方法。该方法操作简易,原料易得,且其酸用量少,不会造成环境污染,为大规模电池磷酸铁的回收提供了可行的生产工艺。
5.为实现上述目的,本发明采用如下技术方案:一种从废旧磷酸铁锂提锂废渣中回收制备电池级磷酸铁的方法,其包括以下步骤:(1)将废旧磷酸铁锂提锂后的废渣粉碎后与酸溶液混合,在搅拌和加热条件下浸出,过滤,得到滤液;(2)往步骤(1)所得滤液中加入一定量的水杨酸以降低钙铝离子的含量;(3)往步骤(2)所得混合溶液中滴加氢氧化钠溶液以调节ph值,使得磷酸铁沉出;(4)将步骤(3)所得磷酸铁按一定固液比加水配成浊液,然后加入酸性络合剂进行纯化,以进一步除去杂质离子,再经过滤,去离子水淋洗、105℃干燥,制得电池级磷酸铁。
6.进一步地,步骤(1)所述酸溶液是将酸和去离子水按体积比1:3~1:18混合制得,所述酸为硫酸、硝酸、柠檬酸、冰醋酸、盐酸中的任意一种。
7.进一步地,步骤(1)中所用废渣与酸溶液的重量比为1:1~1:10。
8.进一步地,步骤(1)中利用酸溶液进行浸出时的温度为30℃~80℃,时间为2~8h,搅拌速度为100~800rpm。
9.进一步地,步骤(2)中水杨酸的用量按其在混合溶液中的浓度为0.1~0.6wt.%进行换算。
10.进一步地,步骤(3)中所述氢氧化钠溶液的浓度为4~8mol/l,其加入量以使体系ph值达1.3~2.5为宜。
11.进一步地,步骤(4)中所述固液比为1:1~1:5。
12.进一步地,步骤(4)中所述酸性络合剂为聚乙烯吡咯烷酮,其加入量按在混合液中的浓度为0.1wt.%~0.9wt.%进行换算。
13.进一步地,步骤(4)中所述纯化的时间为2h~10h。
14.本发明先将废旧磷酸铁锂提锂后的废渣进行粉碎,以便提高后续酸浸步骤中有价金属的浸出率;然后采用水杨酸对其进行浸出处理,利用水杨酸与钙铝的络合能力优于铁、且所得络合物极为稳定的特性,带走浸出液中大量的钙铝杂质离子,从而将废渣粉末里的碳、硫酸钙和pvdf等与所需的磷酸铁进行有效分离,之后通过加入碱溶液调ph值到1.3~2.5范围内以得到粗制磷酸铁(磷酸铁在这一ph值范围内可以产生沉淀,当磷酸铁ph值低于1.3时,便会大量溶解于酸液之中,ph 值高于2.5时,铁离子会发生水解变为氢氧化铁胶体,无法有效回收磷酸铁),再将所得粗制磷酸铁进行纯化,使其中钙、铝、镁等杂质的含量均可达到电池级要求。
15.本发明具有如下有益效果:(1)本发明实现了废磷酸铁锂的二次利用,避免了资源浪费,对于环境保护起到积极的作用。
16.(2)本发明所用原料易得且价格低廉,且制备过程不会产生有害气体和有害废品,废料易于处理。
17.(3)本发明对于废旧磷酸铁锂中的磷酸铁着极高的回收率,且回收得到的磷酸铁的纯度可以达到行业电池级标准。
附图说明
18.图1为水杨酸浓度对钙元素含量的影响。
19.图2为水杨酸浓度对铝元素含量的影响。
20.图3为pvp浓度对钙、铝元素含量的影响。
21.图4为实施例3及对比例1-5所得磷酸铁中钙、铝元素含量的对比情况。
具体实施方式
22.一种从废旧磷酸铁锂提锂废渣中回收制备电池级磷酸铁的方法,其包括以下步骤:(1)将废旧磷酸铁锂提锂后的废渣粉碎后与酸溶液按重量比为1:1~1:10混合,在30℃~80℃、100~800rpm搅拌条件下浸出2~8h,过滤得到滤液;(2)往步骤(1)所得滤液中加入一定量水杨酸,使混合溶液中水杨酸浓度达0.1~0.6wt.%,以去除钙铝离子;
(3)往步骤(2)所得混合溶液中滴加4~8mol/l的氢氧化钠溶液以调节ph值至1.3~2.5,使得磷酸铁沉出;(4)将步骤(3)所得磷酸铁按固液比1:1~1:5加水配成浊液,然后加入酸性络合剂聚乙烯吡咯烷酮,使其在混合液中的浓度为0.1wt.%~0.9wt.%,纯化2h~10h以进一步除去杂质离子,再经过滤,并用去离子水淋洗3~5次,最后放入恒温鼓风干燥箱105℃恒温干燥,制得电池级磷酸铁。
23.其中,步骤(1)所述酸溶液是将酸和去离子水按体积比1:3~1:18混合制得,所述酸为硫酸、硝酸、柠檬酸、冰醋酸、盐酸中的任意一种。
24.图1为水杨酸浓度对钙元素含量的影响。由图1可知,随着水杨酸用量的提升,溶液中钙含量下降明显,在达到0.5wt.%时除钙效果趋于稳定。
25.图2为水杨酸浓度对铝元素含量的影响。由图2可知,随着水杨酸用量的提升,溶液中铝含量也有明显下降。
26.图3为pvp浓度对钙、铝元素含量的影响。由图3可知,随着体系中pvp浓度的提高,磷酸铁中钙、铝杂质含量明显下降,在pvp浓度达到0.9wt.%时,磷酸铁中钙、铝含量已经低于电池及磷酸铁杂质含量的国家标准。
27.下面结合具体实施例,进一步阐述本公开。应理解,这些实施例仅用于说明本公开而不用于限制本公开的范围。下列实施例中未注明具体条件的实验方法,通常按照常规条件或按照制造厂商所建议的条件。
28.除非另行定义,文中所使用的所有专业与科学用语与本领域熟练人员所熟悉的意义相同。本发明所使用的试剂或原料均可通过常规途径购买获得,如无特殊说明,本发明所使用的试剂或原料均按照本领域常规方式使用或者按照产品说明书使用。此外,任何与所记载内容相似或均等的方法及材料皆可应用于本发明方法中。文中所述的较佳实施方法与材料仅作示范之用。
29.需要注意的是,这里所使用的术语仅是为了描述具体实施方式,而非意图限制根据本公开的示例性实施方式。如在这里所使用的,除非上下文另外明确指出,否则单数形式也意图包括复数形式,此外,还应当理解的是,当在本说明书中使用术语“包含”和/或“包括”时,其指明存在特征、步骤、操作和/或它们的组合。
30.下面结合具体方式对本发明作进一步详细的说明。
31.实施例1(1)将废旧磷酸铁锂提锂后的废渣进行研磨后,称取50g置于400ml大烧杯中,加入150ml去离子水和20g硫酸,搅拌均匀后放置于水浴锅中,50℃、200rpm条件下恒温浸出3h,之后进行过滤处理得到滤液和滤渣,初步分离掉含pvdf、硫酸钙和炭黑的滤渣;(2)步骤(1)所得滤液中包含磷、三价铁、锂、钙、铝、镁、镍、铜等杂质元素,为防止在粗沉磷酸铁的同时将钙铝杂质裹挟在粗沉渣里,不利于后续吸附除杂,往所得滤液中加入0.90g水杨酸,使其在混合溶液中的浓度达0.6wt.%,从而将滤液里的钙铝杂质大部分带走;(3)往步骤(2)所得混合溶液中加入4mol/l的氢氧化钠溶液以调节ph至2.3,粗沉得到粗制磷酸铁;(4)将步骤(3)所得粗制磷酸铁按固液质量比1:3加水配成浊液,然后加入一定量
pvp,使其在溶液中的浓度为0.1wt.%,300rpm条件下常温搅洗5h,之后进行过滤,并用5倍体积的去离子水对滤渣淋洗3~5次,再放入105℃恒温鼓风干燥箱进行恒温烘干,得到电池级磷酸铁。
32.表1 实施例1所用废旧磷酸铁锂提锂废渣中杂质元素的含量分析表2 实施例1回收得到的磷酸铁中杂质元素的含量分析实施例2(1)将废旧磷酸铁锂提锂后的废渣进行研磨后,称取45g置于400ml大烧杯中,加入100ml去离子水和15g硫酸,搅拌均匀后放置于水浴锅中,70℃、400rpm条件下恒温浸出6h,之后进行过滤处理得到滤液和滤渣,初步分离掉含pvdf、硫酸钙和炭黑的滤渣;(2)步骤(1)所得滤液中包含磷、三价铁、锂、钙、铝、镁、镍、铜等杂质元素,为防止在粗沉磷酸铁的同时将钙铝杂质裹挟在粗沉渣里,不利于后续吸附除杂,往所得滤液中加入0.6g水杨酸,使其在混合溶液中的浓度达0.6wt.%,从而将滤液里的钙铝杂质大部分带走;(3)往步骤(2)所得混合溶液中加入4mol/l的氢氧化钠溶液以调节ph至1.8,粗沉得到粗制磷酸铁;(4)将步骤(3)所得粗制磷酸铁按固液质量比1:5加水配成浊液,然后加入一定量pvp,使其在溶液中的浓度为0.5wt.%,500rpm条件下常温搅洗6h,之后进行过滤,并用6倍体积的去离子水对滤渣淋洗3~5次,再放入105℃恒温鼓风干燥箱进行恒温烘干,得到电池级磷酸铁。
33.表3 实施例2废旧磷酸铁锂提锂废渣中杂质元素的含量分析表4 实施例2回收得到的磷酸铁中杂质元素的含量分析实施例3(1)将废旧磷酸铁锂提锂后的废渣进行研磨后,称取30g置于400ml大烧杯中,加入60ml去离子水和10g硫酸,搅拌均匀后放置于水浴锅中,40℃、600rpm条件下恒温浸出4h,之后进行过滤处理得到滤液和滤渣,初步分离掉含pvdf、硫酸钙和炭黑的滤渣;(2)步骤(1)所得滤液中包含磷、二价铁和三价铁、锂、钙、铝、镁、镍、铜等杂质元素,为防止在粗沉磷酸铁的同时将钙铝杂质裹挟在粗沉渣里,不利于后续吸附除杂,往所得
滤液中加入0.36g水杨酸,使其在混合溶液中的浓度达0.6wt.%,从而将滤液里的钙铝杂质大部分带走;(3)往步骤(2)所得混合溶液中加入4mol/l的氢氧化钠溶液以调节ph至2.0,粗沉得到粗制磷酸铁;(4)将步骤(3)所得粗制磷酸铁按固液质量比1:5加水配成浊液,然后加入一定量pvp,使其在溶液中的浓度为0.9wt.%,500rpm条件下常温搅洗6h,之后进行过滤,并用6倍体积的去离子水对滤渣淋洗3~5次,再放入105℃恒温鼓风干燥箱进行恒温烘干,得到电池级磷酸铁。
34.表5 实施例3废旧磷酸铁锂提锂废渣中杂质元素的含量分析表6 实施例3回收得到的磷酸铁中杂质元素的含量分析对比例1粗制磷酸铁的制备同实施例3步骤(1)-(3)。
35.将所得粗制磷酸铁按固液质量比1:3加水配成浊液,并利用硫酸控制其ph值在1.8,300rpm条件下常温搅洗6h,之后进行过滤,并用6倍体积的去离子水对滤渣淋洗3~5次,再放入105℃恒温鼓风干燥箱进行恒温烘干,得到纯化后的磷酸铁。
36.对比例2粗制磷酸铁的制备同实施例3步骤(1)-(3)。
37.将所得粗制磷酸铁按固液质量比1:3加水配成浊液,并利用盐酸控制其ph值在1.8,300rpm条件下常温搅洗6h,之后进行过滤,并用6倍体积的去离子水对滤渣淋洗3~5次,再放入105℃恒温鼓风干燥箱进行恒温烘干,得到纯化后的磷酸铁。
38.对比例3粗制磷酸铁的制备同实施例3步骤(1)-(3)。
39.将所得粗制磷酸铁按固液质量比1:3加水配成浊液,并利用硝酸控制其ph值在1.8,300rpm条件下常温搅洗6h,之后进行过滤,并用6倍体积的去离子水对滤渣淋洗3~5次,再放入105℃恒温鼓风干燥箱进行恒温烘干,得到纯化后的磷酸铁。
40.对比例4粗制磷酸铁的制备同实施例3步骤(1)-(3)。
41.将所得粗制磷酸铁按固液质量比1:3加水配成浊液,并利用醋酸控制其ph值在1.8,300rpm条件下常温搅洗6h,之后进行过滤,并用6倍体积的去离子水对滤渣淋洗3~5次,再放入105℃恒温鼓风干燥箱进行恒温烘干,得到纯化后的磷酸铁。
42.对比例5粗制磷酸铁的制备同实施例3步骤(1)-(3)。
43.将所得粗制磷酸铁按固液质量比1:3加水配成浊液,并利用硫酸控制其ph值在
1.8,300rpm条件下50℃恒温搅洗6h,之后进行过滤,并用6倍体积的去离子水对滤渣淋洗3~5次,再放入105℃恒温鼓风干燥箱进行恒温烘干,得到纯化后的磷酸铁。
44.图4为实施例3及对比例1-5所得磷酸铁中钙、铝元素含量的对比情况。由图中可见,常规采用硫酸、醋酸等酸性试剂进行除钙、除铝的效果不甚明显,而采用pvp进行纯化处理,可以使所得磷酸铁达到电池级磷酸铁的国家标准(如表7)。
45.表7 电池级磷酸铁的国家标准以上所述仅为本发明的较佳实施例,凡依本发明申请专利范围所做的均等变化与修饰,皆应属本发明的涵盖范围。