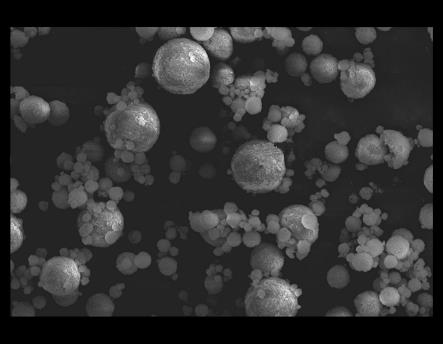
一种钠离子电池正极材料na3fe2(po4)p2o7的制备方法
技术领域
1.本发明属于钠离子电池正极材料技术领域,尤其涉及一种钠离子电池正极材料na3fe2(po4)p2o7的制备方法。
背景技术:2.能源是人类社会赖以生存和发展的重要物质基础,随着传统化石能源资源日益减少,世界各国开始大力发展新能源体系。锂离子电池作为当前综合性能最优异的二次电池代表,主导了便携式电子产品和电动汽车市场,并逐渐向储能领域拓展。但是,锂资源在地壳中的储量有限,据估算全球可开采锂资源的储量仅为25 m 吨,并且世界约73%的锂资源集中分布于南美洲少数国家,这种局势造成全球锂价格快速攀升,锂离子电池制造成本也随之升高。目前,锂资源的短缺和锂电池制备成本的提升使锂离子电池难以满足未来电动汽车和储能两大产业的需求。为了突破锂资源稀缺的掣肘,有必要开发一种更具优势的新一代储能电池。
3.钠与锂的物理化学性质非常相似,电极电势也较为接近,并且金属钠储量丰富,分布区域广泛,价格便宜,基于脱嵌机制构建的钠离子电池相较锂离子电池更具资源和成本优势。目前钠离子电池需要克服的技术难点就是开发低成本高性能的正极材料,在研究的正极材料包括氧化物类、普鲁士蓝类和聚阴离子类。其中,聚阴离子类化合物由于结构稳定、热稳定性好、循环寿命长、价格低廉,是储能钠离子电池的理想选择之一。
4.铁基聚阴离子型化合物na3fe2(po4)p2o7是目前研究最为广泛的钠离子电池正极材料之一,材料中的焦磷酸根与磷酸根能形成稳定的框架结构,使钠离子能够在其框架中可逆穿梭。并且在发生钠离子脱嵌过程中伴随着晶格畸变量小,因此该材料的电化学性能表现出极好的循环稳定性能及热稳定性能,同时该材料还兼顾安全、无毒、廉价等优势。但该材料理论比容量不高,同时电子导电率差,必须包覆一定导电性良好的材料,这使得该材料的理论放电比容量进一步减少。
5.目前关于制备高性能的na3fe2(po4)p2o7材料的研究报道较少,并且放电比容量始终无法突破120 mah/g,即使在进行改性研究后,倍率性能也没得到明显改善。基于此背景,本发明提供一种新工艺手段可制备得到高比容量,高倍率的na3fe2(po4)p2o7材料。
技术实现要素:6.本领域技术人员认为,在前驱体制备过程中,各元素分布均匀度是制备高电化学性能na3fe2(po4)p2o7材料的重要因素,直接影响材料的倍率性能及容量。常规的钠离子电池正极材料制备方法都是将原料直接混合研磨,先球磨再砂磨,尽量使原料中各元素混合均匀后再进行喷雾干燥造粒,烧结。通常情况下,研磨时长基本在15-20小时左右,耗能非常大,并且制备得到的材料放电比容量始终无法突破120 mah/g。
7.本发明技术人员认为,制备na3fe2(po4)p2o7粉体材料的原理是以固体磷酸铁为生长模板,使钠离子均匀附着在磷酸铁模板上,再通过喷雾干燥和烧结获得目标产物。从原理
可以看出,材料中的钠离子是否分布均匀是制备高电学性能na3fe2(po4)p2o7材料的最关键因素。但是,提供钠离子的磷酸钠盐非常容易结晶结块,直接研磨不仅降低研磨效率,也难以使钠离子均相分布在整个体系中。在此基础上,本发明技术人员并没有持续的将目光放在如何解决磷酸钠盐结晶结块的问题,而是将易结晶结块的磷酸钠盐直接制成溶液与其他原料混合进行研磨,确保体系中的钠离子非常均匀的分布在其他原料颗粒表面,使制备得到的na3fe2(po4)p2o7材料电化学性能更佳。
8.本发明包括如下技术方案:第一方面,本发明提供一种钠离子电池正极材料na3fe2(po4)p2o7的制备方法,所述方法包括如下步骤:(1)称取fepo4、磷酸钠盐、补充性铁源和碳源备用,钠元素、铁元素、磷元素摩尔比为3:2:3;(2)将磷酸钠盐溶于去离子水中形成浓度为0.1-1.5mol/l的水溶液;(3)将fepo4、补充性铁源、质量分数为30%-80%的碳源混匀后加入步骤(2)所述的水溶液,混合后利用砂磨机进行砂磨,直至颗粒粒径为0.1-2 μm,再加入剩余碳源;(4)将砂磨后的浆料进行喷雾干燥,得到前驱体颗粒;(5)将前驱体颗粒在惰性气氛下烧结得到na3fe2(po4)p2o7粉体。
9.本发明所述的磷酸钠盐选自磷酸钠(na3po4)、磷酸一氢钠(na2hpo4)、磷酸二氢钠(nah2po4)中的一种或两种以上的组合。
10.在本发明的最优选实施方式中,所述磷酸钠盐为磷酸一氢钠。
11.本发明所述的补充性铁源选自硝酸铁、乙酸铁、氯化铁、草酸亚铁、氢氧化亚铁、柠檬酸铁中的一种或两种以上的组合。
12.在本发明的优选实施方式中,所述补充性铁源为草酸亚铁。
13.优选的,所述步骤(2)中磷酸钠盐水溶液浓度为0.5-1.2mol/l。
14.本发明提供的将易结晶结块的磷酸钠盐先制成水溶液的形式,再加入其他原料进行研磨的制备工艺,可以直接省略球磨,只用砂磨处理即可达到要求,并且显著减少砂磨时间。本发明优选使用的砂磨机砂磨方式包括盘式、棒销式、涡轮式中的一种,在砂磨过程中可选择加入砂磨介质,所述砂磨介质包括天然砂石、玻璃珠、钢珠、氧化锆珠、硅酸锆珠、玛瑙珠中的一种或两种以上的组合。
15.优选的,所述砂磨机转速为1500-3500rpm,砂磨时间为0.5-2h。通过砂磨可以将磷酸铁和补充性铁源充分混匀。
16.本发明所述的喷雾干燥是将砂磨均匀的浆料进行雾化蒸发,得到颗粒尺寸均匀、形貌规整的前驱体颗粒。本发明对喷雾干燥仪器及参数不做特殊限定,是本领域技术人员的常规操作。
17.步骤(5)所述的惰性气氛包括氩气、氮气、氩气-氢气混合气、氮气-氢气混合气中的一种。在本发明的具体实施方式中,所述惰性气氛指氮气。
18.步骤(5)所述的烧结包括预烧和煅烧,预烧温度为200-350℃,预烧时间1-4h,煅烧温度为400-600℃,煅烧时间3-8h。
19.优选的,所述制备方法中碳源选自蔗糖、葡萄糖、淀粉、环糊精、柠檬酸中至少一种。
20.在本发明的具体实施方式中,所述碳源选自淀粉,淀粉加入量为磷源、铁源、钠源总质量的5%-20%。
21.更优选的,在砂磨前后分两次加入淀粉,砂磨前加入淀粉总量的50%-70%,砂磨后加入剩余的30%-50%。
22.本发明提供的钠离子电池正极材料na3fe2(po4)p2o7的制备方法,具有如下技术优势:1、本发明改变现有的将所有原材料直接混合进行球磨的工艺,通过将易结晶结块的磷酸钠盐优先溶解,制备成一定浓度的磷酸钠盐溶液再与其他原料混合作为浆料进行砂磨。所述技术方案不需要使用球磨装置,直接用砂磨即可,这样直接降低球磨工艺对原材料浪费以及各混合组分的配比影响,减少工艺流程,节约成本,利于实现工业化推进和批量化生产。
23.2、由于本发明将易结晶结块的磷酸钠盐优先溶解制备磷酸钠盐溶液,使钠元素均以离子形式存在,在砂磨过程中非常均匀的附着在其他原料颗粒表面,确保了在喷雾干燥后的前驱体颗粒中,钠离子存在于颗粒内部,缩短了在热处理过程中钠离子的扩散时间,减少烧结保温时间,降低能耗,节约生产成本。
24.3、常规的钠离子电池正极材料制备过程均是将铁源、钠源、磷源和碳源一起加入研磨装置中进行研磨,研磨装置尤其是球磨机,工作过程中会产生高温,会使碳源糊化,增加整个研磨浆料粘度,降低研磨效率,消耗能量。本发明技术人员预料不到的发现,砂磨之后再加入碳源不仅能显著降低砂磨浆料的粘度,降低能耗,同时对产品性能不会产生实质性影响。
25.4、通过本发明提供的改进工艺制备得到的na3fe2(po4)p2o7粉体材料,首次放电比容量不仅突破了120mah/g,并且在5c下的放电比容量大于100mah/g,1c倍率下循环500圈,比容量保持率仍大于98%。
附图说明
26.图1实施例4步骤s4得到的前驱体颗粒进行eds扫描点位图。
27.图2实施例4步骤s4得到的前驱体颗粒的eds能谱图。
28.图3实施例4步骤s4得到的前驱体颗粒的eds分层图像。
29.图4实施例4制备的na3fe2(po4)p2o7粉体xrd图。
30.图5实施例4制备的na3fe2(po4)p2o7粉体sem图。
31.图6实施例4制备的na3fe2(po4)p2o7粉体首次充放电曲线图。
32.图7实施例4制备的na3fe2(po4)p2o7粉体倍率图。
33.图8实施例4制备的na3fe2(po4)p2o7粉体在1c下500圈循环性能曲线图。
34.图9对比例1步骤s4得到的前驱体颗粒进行eds扫描点位图。
35.图10对比例1步骤s4得到的前驱体颗粒的eds能谱图。
36.图11对比例1步骤s4得到的前驱体颗粒的eds分层图像。
37.图12对比例1制备的na3fe2(po4)p2o7粉体xrd图。
38.图13实施例4制备的前驱体颗粒的eds能谱中元素占比数据图。
39.图14对比例1制备的前驱体颗粒的eds能谱中元素占比数据图。
40.图15na3fe2(po4)p2o7制备工艺耗能统计图。
41.图16na3fe2(po4)p2o7产品电化学性能图。
42.图17na3fe2(po4)p2o7制备工艺耗能及产品电化学性能图。
具体实施方式
43.下面将对本发明实施例中的技术方案进行清楚、完整地描述,显然,所描述的实施例仅是本发明的部分实施例,而不是全部。基于本发明中的实施例,本领域普通技术人员在没有做出创造性劳动前提下所获得的所有其他实施例,都属于本发明保护的范围。
44.钠离子电池正极材料na3fe2(po4)p2o7的制备原料为fepo4、na2hpo4、二水合草酸亚铁、淀粉,其中,fepo4为铁源、二水合草酸亚铁为补充性铁源,na2hpo4即是钠源又是磷源,淀粉是碳源。
45.制备过程的反应方程式为:4fec2o4·
2h2o+12fepo4+12na2hpo4+c6h
10
o5=8na3fe2(po4)p2o7+19h2o
↑
+9co2↑
+5c实施例1s1:称取226.5g fepo4(1.5mol,m=151)、213g na2hpo4(1.5mol,m=142)、90g二水合草酸亚铁(0.5mol,m=180)、56.6g淀粉备用;s2:将na2hpo4溶于15l去离子水中形成浓度为0.1mol/l的na2hpo4水溶液;s3:将fepo4、二水合草酸亚铁、淀粉混合均匀,向其中加入12l的na2hpo4水溶液,混匀,倒入砂磨机中,转速3500rpm条件下砂磨,直至颗粒粒径为0.3-2μm,砂磨结束后倒入剩余na2hpo4水溶液;s4:将砂磨浆料在喷雾干燥机中进行喷雾干燥,得到干燥均匀的前驱体颗粒;s5:将前驱体颗粒在氮气保护下,300℃预烧3h,500℃煅烧4h得到na3fe2(po4)p2o7粉体。
46.实施例2步骤s1同实施例1,步骤s2:将213g na2hpo4溶于5l去离子水中形成浓度为0.3mol/l的na2hpo4水溶液;步骤s3:将fepo4、二水合草酸亚铁、淀粉混合均匀,向其中加入4l的na2hpo4水溶液,混匀,倒入砂磨机中,转速3500rpm条件下砂磨,直至颗粒粒径为0.3-2μm,砂磨结束后倒入剩余na2hpo4水溶液,其他操作均与实施例1相同,制备得到na3fe2(po4)p2o7粉体。
47.实施例3步骤s1同实施例1,步骤s2:将213g na2hpo4溶于3l去离子水中形成浓度为0.5mol/l的na2hpo4水溶液;步骤s3:将fepo4、二水合草酸亚铁、淀粉混合均匀,向其中加入2.4l的na2hpo4水溶液,混匀,倒入砂磨机中,转速3500rpm条件下砂磨,直至颗粒粒径为0.3-2μm,砂磨结束后倒入剩余na2hpo4水溶液,其他操作均与实施例1相同,制备得到na3fe2(po4)p2o7粉体。
48.实施例4步骤s1同实施例1,步骤s2:将213g na2hpo4溶于1.5l去离子水中形成浓度为1mol/l的na2hpo4水溶液;步骤s3:将fepo4、二水合草酸亚铁、淀粉混合均匀,向其中加入1.2l的na2hpo4水溶液,混匀,倒入砂磨机中,转速3500rpm条件下砂磨,直至颗粒粒径为0.3-2μm,砂
磨结束后倒入剩余na2hpo4水溶液;步骤s4:将砂磨浆料在喷雾干燥机中进行喷雾干燥,得到干燥均匀的前驱体颗粒;其他操作均与实施例1相同,制备得到na3fe2(po4)p2o7粉体。
49.本实施例得到的前驱体颗粒的eds扫描点位图如图1所示,前驱体颗粒的eds能谱如图2所示,具体为谱图57,前驱体颗粒的eds分层图像如图3所示,其中,(a)表示eds面扫全图,(b)表示fe的eds分布图,(c)表示na的eds分布图,(d)表示p的eds分布图。eds能谱中各元素占比如图13所示,具体为谱图57中各元素占比。
50.实施例5步骤s1同实施例1,步骤s2:将213gna2hpo4溶于1.25l去离子水中形成浓度为1.2mol/l的na2hpo4水溶液;步骤s3:将fepo4、二水合草酸亚铁、淀粉混合均匀,向其中加入1l的na2hpo4水溶液,混匀,倒入砂磨机中,转速3500rpm条件下砂磨,直至颗粒粒径为0.3-2μm,砂磨结束后倒入剩余na2hpo4水溶液,其他操作均与实施例1相同,制备得到na3fe2(po4)p2o7粉体。
51.实施例6步骤s1同实施例1,步骤s2:将213gna2hpo4溶于1l去离子水中形成浓度为1.5mol/l的na2hpo4水溶液;步骤s3:将fepo4、二水合草酸亚铁、淀粉混合均匀,向其中加入0.8l的na2hpo4水溶液,混匀,倒入砂磨机中,转速3500rpm条件下砂磨,直至颗粒粒径为0.3-2μm,砂磨结束后倒入剩余na2hpo4水溶液,其他操作均与实施例1相同,制备得到na3fe2(po4)p2o7粉体。
52.对比例1s1:称取226.5gfepo4(1.5mol,m=151)、213gna2hpo4(1.5mol,m=142)、90g二水合草酸亚铁(0.5mol,m=180)、56.6g淀粉备用;s2:将na2hpo4(固体状态)、fepo4、二水合草酸亚铁、淀粉加入到1.5l去离子水中,混合均匀,以转速40rpm球磨5h;s3:再将浆料倒入砂磨机中,转速3500rpm砂磨10h,颗粒粒径达到0.3-2μm;s4:将砂磨浆料在喷雾干燥机中进行喷雾干燥,得到干燥均匀的前驱体颗粒;s5:将前驱体颗粒在氮气保护下,300℃预烧3h,500℃煅烧4h得到na3fe2(po4)p2o7粉体。
53.本实施例得到的前驱体颗粒的eds扫描电位图如图9所示,前驱体颗粒的eds能谱如图10所示,具体为谱图59,前驱体颗粒的eds分层图像如图11所示,其中,(a)表示eds面扫全图,(b)表示fe的eds分布图,(c)表示na的eds分布图,(d)表示p的eds分布图,eds能谱中各元素占比如图14所示,具体为谱图59中各元素占比。
54.效果例1砂磨工艺耗能在实际工业化生产中,工艺流程的耗能参数是技术人员重点关注的指标,耗能与产品制备成本密切相关,影响产品的市场接受度。本发明的一个目的也是提供一种耗能少的na3fe2(po4)p2o7制备工艺。
55.统计按照本发明实施例1-6,对比例1提供的工艺方法制备得到na3fe2(po4)p2o7粉体的总耗能,优选得到耗能较少的制备方法,结果如图15所示。
56.本发明实施例1-6的制备工艺是先将na2hpo4加水配制成水溶液,优选在砂磨前加入80%体积的na2hpo4水溶液,砂磨后再加入剩余的20%na2hpo4水溶液。从砂磨后浆体粘度数
据可以看出,随着na2hpo4水溶液浓度增加,向砂磨体系中加入的水溶液体积是逐渐减小的,导致砂磨后浆体粘度增大。但是,如实施例1-2所示,na2hpo4水溶液浓度小,体积大,导致浆体粘度小,就需要在喷雾干燥环节加大水的处理量,喷雾时间也更长,才能保证喷雾后的前驱体比较干燥。同时,技术人员还需要增大进风温度,使整个环节耗能更大。如实施例6所示,当浆料粘度过大,砂磨过程中流动性变差,砂磨更加困难。另一方面,在喷雾干燥时蠕动泵的转速就需要更大,增大了蠕动泵的负荷,耗能也会相应增加。而当浓度特别大时,甚至会堵塞进料口,导致制备工艺失败。
57.对比例1是现有技术公开的一种制备na3fe2(po4)p2o7粉体的工艺,没有将na2hpo4先制备成溶液,而是将所有原料与水混合,此时na2hpo4并没有溶解,大多以固体结晶状态存在,为了达到能砂磨的效果,必须增加球磨工艺,同时为了能降低砂磨粒度,必须延长砂磨时间,并且研磨浆料的粘度很大,不利于喷雾干燥,耗能也较大。
58.效果例2产品电化学性能检测试验目的:检测本发明实施例1-6,对比例1制备得到的na3fe2(po4)p2o7粉体的电化学性能,平行重复4组实验,取平均值。
59.试验方法:按照活性物质:导电剂:粘结剂=8:1:1制成正极浆料,并涂敷在铝箔上制备成正极,并以钠片作为负极,制成扣式半电池,在新威电化学测试仪上进行测试,标称比容量120mah/g,在0.1,0.2,0.5,1,2,5倍率下循环一圈,在1c下恒流恒压下进行循环,结果如图16所示。
60.从表中数据可以看出,本发明实施例3-5制备得到的na3fe2(po4)p2o7粉体首次放电比容量突破了120mah/g。实施例1-2制备过程中,由于na2hpo4水溶液浓度过低,在喷雾干燥过程中,钠离子更难找到合适的磷酸铁等固体附着点,使得雾化过程中的每个雾化珠中的元素混合度较低,直接影响其电化学性能;另一方面浓度低使得喷雾出来的前驱体更细,松装密度更大,影响后续的装钵烧结。实施例6制备过程中na2hpo4水溶液浓度过高,过高的浓度会使得在砂磨阶段更难以降低颗粒的尺寸,导致颗粒粒径过大,直接影响材料的倍率性能,同时也加剧了砂磨机的负荷。
61.通过分析实施例1-6制备工艺耗能量和产品电化学性能参数,技术人员发现,将na2hpo4在砂磨之前先进行溶解,与直接将na2hpo4和其他固体原料直接研磨相比(对比例1),不仅节省耗能,而且制备得到的na3fe2(po4)p2o7粉体电化学性能也更优。
62.技术人员分析认为,常规的固体混合球磨、砂磨、喷雾干燥、再进行煅烧的工艺难以达到各组分充分均匀的目的。因为磷酸钠盐易结晶结块,在不做任何预处理的情况下将其放入研磨装置中进行研磨,体系中的钠离子无法均匀附着在生长模板磷酸铁表面,导致该方法制备得到的粉体材料中容易存在无电化学活性的nafepo4相,影响产品电化学性能的表现。本发明将易结晶结块的磷酸钠盐溶于水制备成溶液,并且优选溶液浓度,使磷酸钠盐以水溶液的形式与其他原料混合进行研磨,体系中的钠离子均匀附着在生长模板磷酸铁表面。
63.从本发明提供的实施例4产品前驱体颗粒的eds能谱(图1和图2)和eds分层图像(图3)可以看出,在点扫测试和面扫测试上,实施例4制备的前驱体颗粒na、fe、p元素分布均比较均匀,并且从实施例4产品的sem图(图5)可以看出,该产品是由细小的一次颗粒团聚形成的疏松多孔的二次球,该结构具有较大的比表面积,给充放电过程中的钠离子提供了足
够的活性点位,保证正极材料能进行大电流充放电。图4是实施例4制备得到的产品xrd检测结果,pdf#89-0579和pdf#83-0225是购买的标准卡片,通过对比可以看出本发明制备的产品中不存在无电化学活性的nafepo4相,同样也不存在其他氧化物杂质相,因此也保证产品具备在充放电过程中钠离子的完全嵌入脱出。图6是实施例4制备的产品首次充放电曲线,从图中可以看出材料的首次放电比容量可以达到122.1 mah/g。图7是实施例4制备的na3fe2(po4)p2o7粉体倍率图,在5c下最优异的比容量是107.53 mah/g,并且当再次回到0.1c时,比容量是122.03 mah/g,与初始值差异不大,说明电池重复性能好。图8是实施例4制备的产品在1c下500圈循环性能曲线,可以看到性能较平稳。
64.相比之下,图12是对比例1制备得到的产品xrd检测结果,虽然对比例1的产品与标准品相比具有相同的衍射特征峰,但是峰强明显减弱。并且从对比例1产品前驱体的eds能谱(图9和图10)和eds分层图像(图11)可以看到各原子无论是在点或者面上都较杂乱,表明对比例1制备的产品结晶性较差,结构稳定性更差,因此循环性能也大打折扣。
65.此外,本发明技术人员预料不到的发现,碳源的加入时机也会显著影响制备工艺的耗能情况,与在砂磨前就加入碳源相比,在砂磨前后分批次加入碳源不仅能显著降低砂磨后浆料的粘度,降低能耗,同时对产品性能不会产生实质性影响。为此,发明人分别设置了实施例1-6的对比试验(实施例1a-6a),即均在砂磨前加入50%的淀粉,砂磨完成后再将剩余的淀粉与na2hpo4水溶液一起加入体系中搅拌均匀,其他操作与对应的实施例操作相同,制备得到na3fe2(po4)p2o7粉体。
66.例如,实施例1a的制备方法如下:s1:称取226.5g fepo4(1.5mol,m=151)、213g na2hpo4(1.5mol,m=142)、90g二水合草酸亚铁(0.5mol,m=180)、56.6g淀粉备用;s2:将na2hpo4溶于15l去离子水中形成浓度为0.1mol/l的na2hpo4水溶液;s3:将fepo4、二水合草酸亚铁、28.3g淀粉混合均匀,向其中加入12l的na2hpo4水溶液,混匀,倒入砂磨机中,转速3500rpm条件下砂磨,直至颗粒粒径为0.3-2μm,砂磨结束后倒入剩余的28.3g淀粉和na2hpo4水溶液充分搅拌均匀;s4:将砂磨浆料在喷雾干燥机中进行喷雾干燥,得到干燥均匀的前驱体颗粒;s5:将前驱体颗粒在氮气保护下,300℃预烧3h,500℃煅烧4h得到na3fe2(po4)p2o7粉体。
67.实施例2a-6a的淀粉加入方法同上,按照效果例1和效果例2的方法计算制备工艺耗能量,并且检测产品电化学性能,结果图17所示。
68.将图17的数据与图15和图16的数据进行比较可以发现,在砂磨前后分两次添加淀粉会显著减小砂磨后浆体粘度,因此降低了生产工艺的耗能。技术人员分析认为,na2hpo4水溶液中的磷酸氢根与淀粉混合后,能与淀粉羟基形成氢键,从而在各淀粉分子中起到架桥的作用,增加淀粉糊化程度,增加淀粉吸水能力,增加浆料的持水性,从而使浆料粘度增大。通过控制减少淀粉在砂磨过程中的含量能有效降低浆料粘度,并且为了不影响碳含量,在砂磨后补加剩余的淀粉,这样既保证了淀粉的均匀分布,粘度也得到了很好的控制,使得浆料在砂磨和喷雾中都减少了能耗,并且最终材料的电化学性能也没受到影响。
69.最后应说明的是:以上各实施例仅用以说明本发明的技术方案,而非对其限制;尽管参照前述各实施例对本发明进行了详细的说明,本领域的普通技术人员应当理解:其依
然可以对前述各实施例所记载的技术方案进行修改,或者对其中部分或者全部技术特征进行等同替换;而这些修改或者替换,并不使相应技术方案的本质脱离本发明各实施例技术方案的范围。