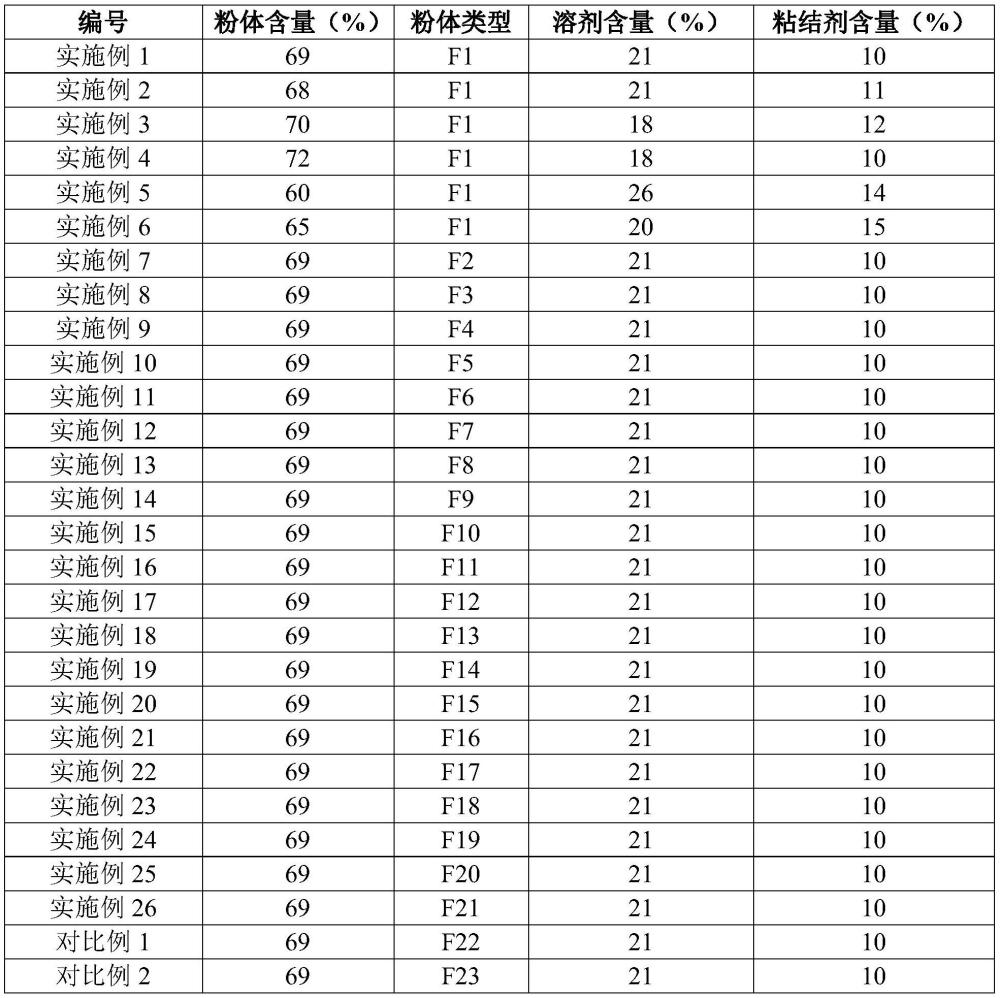
本发明涉及陶瓷领域,具体涉及一种陶瓷基板及其制备方法和应用。
背景技术:
1、陶瓷基板因其具有薄、耐高温、电绝缘性能高、介质损耗低、化学稳定性好等优点,被广泛应用在电子信息行业中的集成电路封装、led照明、散热基板、压力传感器等领域。通过烧结得到的陶瓷基板,在烧结过程中会受到生坯中氧杂质的影响,热导率不能得到稳定的控制,而导致不同程度的变形,表面不平整。要得到表面平整的陶瓷基板,需要采用打磨或研磨的方式进行加工,增加了额外成本,另外使用大水磨研磨容易在陶瓷基板产品表面留下齿轮痕迹,后期铸铁磨很难磨平,导致产品的厚薄不均、平面度差。
技术实现思路
1、为了克服上述现有技术存在的至少一个技术问题,本发明的目的之一在于提供一种陶瓷基板。
2、本发明的目的之二在于提供上述陶瓷基板的制备方法。
3、本发明的目的之三在于提供上述陶瓷基板在电子产品或散热基板中的应用。
4、为了实现上述目的,本发明所采取的技术方案是:
5、本发明的第一个方面提供了一种陶瓷基板,所述陶瓷基板的原料包括粉体,所述粉体包括以下质量百分数的组分:陶瓷粉95~97%,烧结助剂3~5%;所述烧结助剂包括硼酸镁和氢氧化镁。硼酸镁的熔点低,在低温下变成粘流态,在毛细管压力下可以促进陶瓷基板生坯中粉体颗粒的重新排列达到致密化;氢氧化镁中的-oh提高静电斥力,使粉体分散性更均匀,堆积更紧密;通过硼酸镁和氢氧化镁的协同作用,使陶瓷基板具有较高的表面平整度,表面厚度差异不超过0.01mm,且具有较高的致密度。
6、优选地,所述陶瓷粉的质量百分数为96~97%。
7、优选地,所述烧结助剂的质量百分数为3~4%。
8、优选地,所述陶瓷基板包括以下质量百分数的原料:粉体60~72%,粘结剂10~15%,溶剂18~30%。
9、优选地,所述粉体的质量百分数为68~70%。
10、优选地,所述粘结剂的质量百分数为10~12%。
11、优选地,所述溶剂的质量百分数为18~26%;进一步优选地,所述溶剂的质量百分数为20~26%。
12、优选地,以所述烧结助剂的总质量百分数为100%计,所述硼酸镁和氢氧化镁的总质量百分数为37%-52%。硼酸镁和氢氧化镁主要在烧结前期起到主要作用,因此硼酸镁和氢氧化镁占烧结助剂的含量不易过高。
13、优选地,所述硼酸镁和氢氧化镁的质量比为(0.5-5.5):1;进一步优选地,所述硼酸镁和氢氧化镁的质量比为(1.2-2.3):1;更优选地,所述硼酸镁和氢氧化镁的质量比为(1.2-1.5):1。当硼酸镁和氢氧化镁的质量比在上述范围内时,制得的陶瓷基板的致密度较优,一方面,可以避免生成硼酸玻璃,提高陶瓷基板的强度,体系中过量的硼酸镁会容易生成硼酸玻璃,硼酸玻璃的存在会导致陶瓷基板脆性,强度降低。另一方面,可以避免氢氧化镁中的羟基腐蚀生产设备,提高生产设备的使用寿命,氢氧化镁含量高会使体系呈现碱性对生产设备有一定腐蚀作用,氢氧化镁含量过低,粉体颗粒之间斥力较小,粉体容易团聚,陶瓷基板中容易存在力学薄弱点,导致陶瓷基板强度降低。
14、优选地,所述烧结助剂还包括选自氧化锰、氧化铬、氧化镁、氧化硅中至少一种的化合物;本发明中的烧结助剂包括硼酸镁、氢氧化镁和选自氧化锰、氧化铬、氧化镁、氧化硅中至少一种的化合物;进一步优选地,所述烧结助剂包括硼酸镁、氢氧化镁和氧化锰。
15、优选地,所述硼酸镁的用量小于所述氧化锰的用量。
16、优选地,所述陶瓷粉包括ɑ-氧化铝、氧化锆增韧氧化铝陶瓷粉(zta)、氧化锆中的至少一种。
17、优选地,所述陶瓷粉的粒径为6-8μm。
18、优选地,所述溶剂选自二甲苯、乙酸乙酯、甲苯、丙酮、异丙醇中的至少一种;进一步优选地,所述溶剂选自二甲苯和乙酸乙酯;更优选地,所述二甲苯和乙酸乙酯的质量比为(2~3):1。
19、优选地,所述粘结剂选自聚乙烯醇、聚丙烯酸铵、聚乙烯醇缩丁醛中的至少一种。
20、优选地,所述陶瓷基板的密度大于3.6cm2/g。
21、本发明的第二个方面提供了本发明第一个方面提供的陶瓷基板的制备方法,包括以下步骤:
22、s1:将陶瓷粉进行第一次球磨,得到陶瓷粉体;
23、s2:将所述陶瓷粉体与烧结助剂混合后进行第二次球磨,得到粉体;
24、s3:将所述粉体、溶剂、粘合剂混合后进行第三次球磨,得到混合浆料;
25、s4:将所述混合浆料涂覆,压制成型,然后烧结,制得所述陶瓷基板;
26、所述第一次球磨步骤中,研磨球的粒径为10~18μm,球磨总时间为18~30h,研磨球的加入质量为陶瓷粉加入质量的30~40%,球磨转速为40~70r/min;
27、所述第二次球磨步骤中,研磨球的粒径为2~4μm,球磨总时间为10~20h,研磨球的加入质量为粉体质量的30~40%,球磨转速为35~55r/min;
28、所述第三次球磨步骤中,球磨总时间为15~20h,球磨转速为30~40r/min。
29、在本发明的制备方法中,第一次研磨步骤中,需要控制研磨球的加入量,如果研磨球加入量偏少只能研磨到部分粉体,研磨不均匀,容易出现研磨后的粉体粒径分布不均匀。如果研磨球加入量过大,研磨球之间摩擦大,损耗大,容易产生杂质。此外,研磨球的粒径要大于陶瓷粉的粒径才能起到研磨的作用,但是研磨球粒径过大时,研磨球之间的空隙较大,研磨效率降低。
30、第二次研磨步骤中,控制研磨球的加入量的目的主要是为了使粉体混合均匀。第二次球磨需要更换较小粒径的研磨球,目的是将第一次研磨之后较大的颗粒进一步研磨,使得粉体间粒径变得均匀。
31、优选地,所述混合浆料的粉体的晶粒尺寸为3~4μm。
32、优选地,所述第一次球磨为分段球磨,具体步骤为:先在转速为40~50r/min下搅拌1~3h;然后在68~70r/min下搅拌1~3h,再在转速为55~60r/min下搅拌至出料。
33、优选地,所述第二次球磨为分段球磨,具体步骤为:先在转速为35~38r/min下搅拌1~3h;然后在50~55r/min下搅拌1~3h,再在转速为40~45r/min下搅拌至出料。
34、优选地,所述第三次球磨为分段球磨,具体步骤为:先在转速为30~33r/min下搅拌1~3h;然后在38~40r/min下搅拌至出料。
35、优选地,第一次球磨和第二次球磨均采用不同转速分三段球磨的方式,其原因为:慢速搅拌是先将颗粒混合均匀,快速搅拌是研磨掉大的颗粒,然后中速搅拌是使颗粒粒径均匀化。
36、优选地,第三次球磨采用不同转速分两段球磨的方式,其原因为:第三步球磨是对完成第二步球磨的浆料进行颗粒均匀化,所以采用的研磨转速较第二步球磨的慢;先慢速混合均匀,再增加转速是使颗粒粒径均匀化。
37、优选地,所述压制成型步骤为冲压成型。
38、优选地,所述烧结温度为1500-1700℃。
39、优选地,所述烧结时间为15-20h。
40、本发明的第三个方面提供了本发明第一个方面提供的陶瓷基板在电子产品或散热基板中的应用。
41、优选地,所述电子产品包括集成电路、led、压力传感器。
42、本发明的有益效果是:本发明中的陶瓷基板的表面平整性好,厚度极差不超过0.01mm,烧结后得到的陶瓷基板无需打磨或研磨加工,可以简化陶瓷基板的加工步骤,降低生产成本;陶瓷基板还具有较高的力学强度和较高的致密度,具体为:韦伯强度超过400mpa,冲击强度超过420mpa,密度大于3.6cm2/g,满足高性能、高致密度、高强度陶瓷基板的使用要求。
43、本发明中的制备方法通过控制研磨球的粒径以及加入量、研磨转速、研磨时间等参数,制得的混合浆料中的粉体晶粒较小,晶粒较小的粉体具有比表面积大、活性高,采用该混合浆料烧结后制得成瓷粒径小,晶粒堆积致密,表面平整度高的陶瓷基板,该陶瓷基板无需再进行后续的大水磨研磨,生产效率高,成本较低,可以大批量工业化生产。