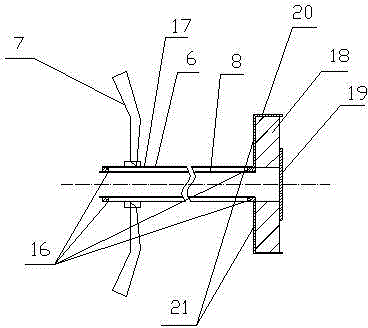
本发明涉及一种由戊糖溶液生产糠醛的方法,特别是一种采用高效混合反应器生产糠醛并同时副产甲酸和醋酸的方法。
背景技术:
糠醛,又名呋喃甲醛。由于糠醛分子结构中存在醛基、双烯、环醚等官能团,所以它兼具醛、醚、二烯和芳香烃化合物的性质,可参与多种不同类型的反应,合成多种化工产品,广泛应用于食品、医药、合成树脂、铸造等多个生产领域。
目前生产糠醛的原料是以富含戊聚糖的植物纤维,如玉米芯、甘蔗渣、玉米秆、稻壳等。其原理是戊聚糖首先被水解为戊糖,然后戊糖脱水环化生成糠醛。
根据戊聚糖水解和戊糖脱水这两步反应是否在同一个反应器中,可将糠醛生产方法分为一步法和两步法。一步法的优点是设备简单、操作简单,但其主要缺点是蒸汽消耗量大,生产1吨糠醛消耗18~24吨的蒸汽,糠醛收率低,只有45%左右,产生大量废水废渣,生产1吨糠醛产生24吨高污染废水,原料利用率低,生产1吨糠醛,消耗玉米芯11吨,废渣发黑,纤维素和木质素破坏严重。两步法生产糠醛技术由于戊聚糖水解和戊糖脱水在两个反应器中进行,能够解决现有糠醛生产的原料利用率低、原料来源窄、糠醛收率低、工艺废水难处理、糠醛渣难以继续利用等难题,该法被认为是最具前景的糠醛生产新方法。
目前“两步法”生产糠醛技术中的第一步,即生物质原料水解制取戊糖技术已经成熟,在较温和的反应条件下,生物质中的半纤维素即可水解主要生成戊糖,同时半纤维分子侧链上的乙酰基和甲酰基被氧化生成醋酸和甲酸,因此戊糖溶液中也含有一定量的甲酸和醋酸。然而由戊糖制取糠醛过程,由于糠醛容易与其前体物发生副反应从而导致糠醛收率很低,这也成为“两步法”生成糠醛技术未能工业应用的根本原因。
只有在戊糖反应生成糠醛的同时快速把反应生成的糠醛快速转移出反应体系才能从根本上降低副反应提高糠醛收率。反应萃取制取糠醛技术被认为是最具工业前景的戊糖制取糠醛技术。反应萃取制取糠醛技术是指在戊糖反应生成糠醛过程加入一种与水不互溶而对糠醛具有高选择性的溶剂,靠溶剂不断把糠醛从水相反应体系萃取到溶剂相,从而大大降低副反应提高糠醛收率。
CN101486695A公开了一种反应萃取制备糠醛的方法和装置。该发明以超临界二氧化碳为萃取剂,以固体酸为催化剂,超临界二氧化碳与戊糖溶液在填料萃取塔中逆流接触反应,在反应温度为200 ℃、木糖浓度30%(wt)、超临界二氧化碳压力为7 MPa时,糠醛收率为70%。
CN102627618A公开了一种反应萃取制取糠醛的方法。该发明利用有机溶剂与戊糖溶液在填料萃取塔内逆流接触反应,在反应温度为200 ℃、戊糖浓度1.56%(wt)、溶剂比3:1时,糠醛收率为70%。
采用反应萃取工艺制备糠醛的过程中,戊糖溶液与萃取剂能否高效的混合接触以促使反应生成的糠醛足够快速的传质到萃取相是制约糠醛收率高低的最关键因素。上述专利中萃取剂和戊糖溶液均是在填料萃取塔内逆流接触反应,但填料塔混合效果较差,副反应严重导致糠醛收率较低,最高只有70%;副反应生成的缩合产物还会累积在填料的表面引起填料堵塞,使得生产过程无法长时间进行;另外上述发明方法无法同时回收戊糖溶液的醋酸和甲酸,反应完的水溶液如果直接排放不仅会造成严重的环境污染,还会造成宝贵资源的浪费。
撞击流是实现快速混合的一种十分有效的方法。它利用两股高速流体相向撞击,在反应器中形成一个高度湍动的撞击区,能够有效降低传递过程中的外部阻力,促进混合,强化传质传热。撞击流反应器已经广泛用于吸收、混合、传热、结晶等化工过程。开发高效的适用于反应萃取工艺制备糠醛过程的撞击流反应器是提高糠醛收率的有效手段。
20世纪90年代以来,撞击流领域的研究明显转向以液体连续相撞击流(Liquid-continuous Impinging Streams,LIS)为重点。专利CN 100364656C在反应器壳体中设置两个正对的导流筒,液体通过泵的驱动作用分别流经两侧导流筒后,在中心处发生相向撞击。这种反应器虽然结构简单,但是只注重了两端导流筒流体的撞击效果,未考虑液体撞击后在反应器中的流动状况,容易造成反应器两侧存在死区。如果两撞击流体中存在固相催化剂,则容易造成催化剂沉降、滞留,直接影响反应深度和产品质量。
专利CN 102989404 A在导流筒中设置螺旋桨,利用两螺旋桨的驱动作用使得反应器中液体在中心处发生撞击,同时利用导流筒和导流片的作用,解决了撞击区外的混合的问题。但螺旋桨需要动力驱动,因此需要外设电机,增加了反应器的整体造价;另外,安装螺旋桨的电机轴在反应器壁上需要安装轴封结构,长期运转易造成损坏,影响反应器的长周期运行。
技术实现要素:
针对现有技术的不足,本发明提供一种高效生产糠醛并同时回收副产物甲酸和醋酸的新方法,以及一种特别适用于该工艺的撞击流反应器,它不仅能够强化撞击流的撞击效果,而且可以实现撞击区外液体的高效、充分混合,并克服了带螺旋桨撞击流反应器的轴封问题,具有结构简单,运行可靠的优点。
本发明提供了一种高效生产糠醛并同时回收副产物甲酸和醋酸的新方法,包括以下内容:
(1)提供一种撞击流液相反应器,其包括反应器壳体,在反应器壳体内沿水平方向设置两个正对的导流筒,每个所述的导流筒均包括内筒和外筒,在外筒靠近碰撞面的一端固定连接有自旋叶轮;所述的自旋叶轮为一体式结构,其包括罩筒、环板、叶片和中心板四个部分;罩筒和环板相连,两者用于导流液体,环板与外筒相连;叶片固定于环板上,与导流筒轴向成夹角;
(2)以戊糖溶液为原料,将戊糖溶液与萃取剂通过输送设备分别通入步骤(1)的撞击流反应器,反应所用催化剂为甲酸和/或醋酸,在戊糖脱水生成糠醛的反应条件下进行混合接触反应;
(3)步骤(2)得到的反应流出物进行冷却静置分层,上层为水相,含有微量的糠醛、醋酸、甲酸及微量的未反应的戊糖,下层为萃取相,主要含有糠醛、醋酸、甲酸以及微量的水分;
(4)步骤(3)得到的萃取相进入萃取剂再生塔进行分离,塔顶产物经分相得到再生的萃取剂和少量的水,塔釜得到不含水的糠醛、醋酸和甲酸的混合物;
(5)步骤(4)中塔釜所得糠醛、醋酸和甲酸的混合物进入糠醛成品塔进行分离,塔釜得到糠醛,塔顶得到醋酸和甲酸混合物;
(6)步骤(5)中塔顶得到的醋酸和甲酸混合物进入醋酸精制塔,塔顶得到甲酸,塔釜得到醋酸。
本发明的方法中,步骤(1)所述的撞击流反应器,在靠近反应器两端的位置设置有一对螺旋桨。所述的螺旋桨分成两个部分:靠近外筒的部分,又称垂直部分;远离外筒的部分,又称弯曲部分。垂直部分与外筒垂直,用于驱动水流沿轴向流动;弯曲部分与垂线方向有一定夹角,驱动水流向斜上方流动,以便与来自第一撞击面的水流形成二次撞击;螺旋桨可对反应器两侧产生扰动,避免死区的形成。所述螺旋桨通过固定轴承与外筒连接。螺旋桨的桨叶(桨片)为向前弯曲结构,倾斜角为15°~60°,可朝前弯方向转动也可向后转动,螺旋桨叶片设计成向液体流入侧弯曲的结构,其倾斜角为5°~60°。
本发明的方法中,步骤(1)所述撞击流反应器的壳体的顶部与底部空间内还设置有分配筒,用来对反应器内的液体进行分配和导流。所述分配筒的两端、中间以及撞击面对应处均开孔。液体可以由撞击面处开孔进入分配筒,而由分配筒两端以及中间的开孔流出,从而实现液体在反应器的导流和分配。
本发明的方法中,步骤(1)所述反应器可以为立式或卧式。反应器的形状一般可以为圆筒形、方形或管型,优选圆筒形。所述反应器左侧与右侧为对称结构。
本发明的方法中,所述撞击流反应器的反应器壳体上设有进料口和卸料口。出料口优选位于撞击平面正下方位置。可以只在中间设立出料口,或者在三个撞击面下方均设立出料口。
本发明的方法中,步骤(1)所述的撞击流反应器中,所述导流筒分布于反应器两侧呈横向对称分布,或分布于上下两端呈纵向对称分布,并处于中央位置。如选择卧式反应器壳体,导流筒宜与反应器的轴线重合。
所述的导流筒中,所述的自旋叶轮和外筒为固定连接。如自旋叶轮可以通过螺纹连接、卡扣联接、法兰连接或其他的固定连接方式固定在外筒上。其中外筒的直径一般约为反应器或撞击面直径的1/10~2/3,优选1/4~1/2。外筒与自旋叶轮直径的比例一般为1/5~1/1,优选1/3~1/1。所述的两个自旋叶轮实际运转时,可设计成同向或异向转动。
进一步,所述的自旋叶轮与外筒构成一体式结构。外筒通过旋转轴承与内筒连接。
本发明的方法中,进一步,所述的撞击流反应器中,分配筒(上分配筒,下分配筒)在撞击面处开孔方向与液体流动方向相同,设计为水平方向开孔,中间开孔设计为垂直方向开孔。
根据本发明的方法,其中戊糖脱水生成糠醛反应温度一般为150~280℃,优选为180~220℃;反应停留时间为0.1~2 h。
本发明的方法中,撞击流反应器内的反应压力应大于反应温度下水相泡点压力以保证反应在液相状态下进行。所述反应压力范围一般为2~10 MPa,优选为2~6 MPa。
本发明的方法中,进一步地,所用萃取剂优选为复合萃取剂。复合萃取剂包括苯、醋酸乙酯和沸点小于甲酸沸点的氯代烃,以复合萃取剂的重量为基准,其中各组分的含量为:苯10wt%~60wt%,醋酸乙酯10wt%~30wt%,氯代烃10wt%~60wt%。优选组成为:苯20~40wt%,醋酸乙酯15~25wt%,氯代烃20~40wt%。所述的氯代烃为三氯甲烷、三氯乙烯、1,1,1-三氯乙烷、1,1,2-三氯乙烷中的一种或几种的混合物。
本发明的方法中,其中使用的复合萃取剂同时还可以起到共沸剂的作用,在萃取剂再生塔中萃取剂与水形成共沸物把糠醛和羧酸混合物中的水分带到塔顶。
本发明的方法中,所述戊糖溶液中还可以添加一定量的无机盐。无机盐具体可以选自是硫酸钠、硫酸钙、氯化钠和硝酸钠中的一种或几种,优选为硫酸钠和/或氯化钠。所述无机盐用量为戊糖溶液的1wt%~5wt%。
本发明的方法中,戊糖脱水反应的催化剂为本技术领域中的常规催化剂,优选为醋酸和甲酸。所述催化剂用量为戊糖溶液的1wt%~5wt%。
本发明的方法中,可以根据装置的规模和操作条件确定撞击流反应器的规模。为提高撞击流反应器的混合效果,可以在撞击流反应器出口与入口之间建立物料循环。将所得到反应流出物的一部分与戊糖溶液原料混合后,循环回撞击流反应器,其中循环物料量为新鲜进料量的5%~500%。
与现有技术相比较,本发明的方法具有以下有益效果:
1、本发明采用的撞击流液相反应器中,液体从自旋叶轮流出后发生首次撞击,撞击后的液体流动方向发生改变后与螺旋桨驱动的液体发生二次撞击,因此在反应器中形成了一个一次撞击面和两个二次撞击面,这种设计大大增强了液体的微观混合效果;内筒中液体驱动自旋叶轮旋转,并通过外筒带动螺旋桨旋转,取消了电机驱动,消除了轴承密封带来的一系列问题(如装置长时间运行易造成轴承密封损毁,影响到装置操作的连续性和长周期性);在反应器两端设置螺旋桨,消除了反应器两端形成死区的可能性,使得反应器中液体的混合更加均匀,更加充分;螺旋桨叶片设计为向前弯曲结构,加强了反应器两端的扰动效果,并使得反应器中液体有整体逆时针或顺势针旋转的趋势,强化了撞击区外的液体混合;分配筒起导流液体的作用,可对反应器顶部和底部的液体进行再分配,选择在两端、二次撞击面和中间开孔有利于增强反应器中液体的循环流动性。本发明的撞击流强化了液液撞击流反应器的撞击效果,使反应器的微观混合效果大大增强,混合的时间大大缩短,提高了生产效率,强化了撞击区外的混合,避免了死区的存在,使得化学反应在反应器空间各位置的同步性提高,有助于提高产品质量;取消了常规螺旋桨反应器的外用电机驱动,消除了轴封带来的许多问题,大大降低了设备投资,保证了设备的长周期运行,具有良好的经济效益。
2、本发明采用所述的撞击流反应器作为反应萃取制取糠醛工艺的反应器,极大的强化了微观混合和微观传质,使糠醛在萃取剂和水两相瞬间达到分配平衡,提高了生产效率,降低了副反应,提高了糠醛收率。解决了因萃取剂和戊糖溶液混合效果差,反应体系呈两相,糠醛在水相反应体系浓度远高于两相平衡时糠醛浓度而造成的副反应严重、糠醛收率低及反应器堵塞等问题。
3、本发明方法中采用了复合溶剂作为萃取剂,其中,醋酸乙酯对甲酸、醋酸和糠醛均具有很高的选择性,苯和氯代烃对糠醛都具有很高的选择性,苯和氯代烃几乎不溶于水且对醋酸乙酯具有很高的选择性,能够使醋酸乙酯几乎不溶于水,解决了醋酸乙酯因在水中溶解度大而不能作为萃取剂的问题;氯代烃同时还能起到调节复合萃取剂密度和粘度的作用;该复合萃取剂对糠醛、醋酸和甲酸均具有很高的选择性,能够在反应萃取制取糠醛的同时回收副产物甲酸和醋酸,糠醛收率大于80%,醋酸和甲酸回收率大于90%,反应完的水相可作为系统回用水。
4、本发明方法中所采用的复合萃取剂中苯和醋酸乙酯能够均与水形成共沸物,因此复合萃取剂还可以起到脱水的共沸剂作用,这使得本发明脱水过程不必添加其他的共沸剂,所以本发明工艺流程简单,而且分离得到的糠醛和醋酸产品纯度高。
5、本发明方法中通过在水相中添加一定量的无机盐,大大降低了高温下萃取剂与水相的互溶度,解决了在高温下因萃取剂与水互溶度大而导致萃取剂损失严重,最终导致反应萃取工艺无法在工业上应用这一关键技术问题;另外无机盐既对戊糖脱水反应有较强的催化活性,又大大提高了萃取剂对糠醛、甲酸和醋酸的选择性,有助于降低副反应提高糠醛收率。
6、本发明方法与设备,大大提高了戊糖制取糠醛的收率和生产效率,简化了工艺流程、降低了生产成本和设备投资,保证了设备的长周期运行。生产过程中无废液排放,是一项绿色环保工艺方法。
附图说明
图1为反应器的结构示意图。
图2为反应器导流筒的结构示意图。
图3为自旋叶轮的结构示意图。
图4为螺旋桨的结构示意图。
图5为本发明工艺流程图。
具体实施方式
以下结合具体附图对本发明的液相撞击流反应器做更详细的说明。
如图1所示,本发明的一种液相撞击流反应器包括反应器壳体11。反应器壳体11的两端设置进料口15和进料口9,在反应器壳体11 的底部设置有卸料口12。在反应器壳体11内设置两个正对的导流筒17。导流筒17由内筒8和外筒6组成。所述的内筒8用于导流液体,外筒6通过两个或两个以上的轴承与内筒8相连。在外筒6靠近碰撞面的一端设置有自旋叶轮3和4。自旋叶轮3、4和外筒6构成一体式结构,二者可采用焊接或铸造方式制备。
如图2所示,以自旋叶轮4为例,其中自旋叶轮4由罩筒20、环板21、叶片18和中心板19构成,罩筒20与环板21连接,环板21与外筒6连接,中心板19置于罩筒20的中心,若干叶片18均布在中心板与罩筒、以及环板之间的环形空间内,叶片的一侧与环板连接。叶片18与内筒8轴线成一定夹角,该夹角一般为5°~85°,当流体流过时,流体对其做功,在推力作用下发生旋转。中心板19用于减小液体流通截面积,增强自旋动力。液体由内筒8导入后,流经自旋叶轮4驱动叶轮旋转,流出叶轮后在中心区域发生撞击,形成撞击面13。
如图1和图2所示,本发明的撞击流反应器还包括螺旋桨7。所述的螺旋桨7通过固定轴承(连接)与外筒6相连。当自旋叶轮4在水力驱动下旋转时,将带动外筒6旋转进而带动螺旋桨7旋转。
如图1、2和4所示,螺旋桨7包括两个部分,垂直部分和弯曲部分。垂直部分与外筒垂直,用于驱动水流沿轴向流动;弯曲部分与垂线方向有一定夹角,驱动水流向斜上方流动,与来自撞击面13的水流形成二次撞击,形成另外两个撞击面5和14。螺旋桨7设计成在导流筒轴向垂面内弯曲的一种结构,用于搅动反应器两端易于形成死区的地方。
如图1所示,在反应器中还可以设置两个用于导流液体的分配筒—上分配筒1和下分配筒10。分配筒1和分配筒10分别通过焊接或铆接2固定在反应器壳体的内部。分配筒1和分配筒10可以在两侧、中间以及撞击面5和撞击面14处开孔,撞击后的液体由撞击面开孔处流入,由两侧和中间开孔流出。撞击混合、反应后的流体经出料口12排出。
根据本发明的撞击流反应器,所述反应器11壳体为对称结构,其可以采用立式或卧式结构。反应器壳体11的形状可以为圆柱体形或长方体形,优选圆柱体形。所述导流筒17分布于反应器两侧或上下两端,并处于中央位置。外筒6的直径一般约为反应器或撞击面直径的1/10~2/3,优选1/4~1/2。外筒6与自旋叶轮4直径的比例一般为1/5~1/1,优选1/3~1/1。所述的自旋叶轮3和自旋叶轮4实际运转时,可设计成同向或异向转动。所述螺旋桨直径一般可以为反应器或撞击面直径的1/8~1/1,螺旋桨为向前弯曲结构,其倾斜角一般为15°~60°,可朝前弯方向转动也可向后转动。螺旋桨叶片设计成向液体流入侧弯曲的结构,倾斜角一般可以为5°~60°。所述分配筒(上分配筒,下分配筒)撞击面处开孔方向与液体流动方向相同,设计为水平方向开孔,中间开孔设计为垂直方向开孔。所述的出料口12位于撞击平面正下方位置,可以只在中间设立或在三个撞击面下方同时设立。
结合图1,本发明提供的液相撞击流反应器的工作原理或工作过程为:两股液体分别经进料口15和9进入反应器,并流经导流筒中的内筒8。液体经内筒8末端流出,驱动自旋叶轮3和4旋转。自旋叶轮3和4喷出的液体发生撞击,撞击后的液体向上下两端或者向反应器的两端流动,部分循环的液体进入反应器上下设置的分配筒1,经过分配筒1的重新分配后,流向反应器的两端。而自旋叶轮3和4的旋转,带动外筒6也进行旋转,从而带动固定在外筒6一端的螺旋桨7随之旋转。螺旋桨7的旋转,一方面对反应器壳体内部两端的区域进行搅拌,不致形成死区;另一方面,螺旋桨7也同时推动位于反应器两端的液体向反应器的中心流动,并与碰撞后流向两端的液体流再次发生碰撞,并形成新的碰撞面,从而进一步增加了反应器的液相混合效果。而反应后的液体可以经由放料口12排出。
以下结合具体附图对本发明工艺做更详细的说明。
如图5所示,按照化学计量比将参加反应的物料萃取剂22和戊糖溶液23,分别用泵或其他液体输送设备把物料输入到中间罐24中,进行预混合,然后通过泵或其他液体输送设备,输入到撞击流反应器11的进料口9、15,原料物流在压力作用下高速经导流筒流向容器中心,并在中心处相向撞击,经过撞击后的物料从出口12流向中间罐24,再通过泵输入到撞击流反应器的进料口9、15,进行再次撞击,通过压力调节器37来控制反应器压力。从压力调节器37排出的反应物料直接进入分相罐25进行冷却静置分层,上层为反应完的水相26,水相26可作为半纤维素水解用水,下层为富含糠醛、醋酸和甲酸的萃取相27,下层萃取相27直接进入萃取剂再生塔28进行分离,塔顶产物29为再生的萃取剂和少量的水,萃取剂可循环使用,塔底产物30为不含水的糠醛和羧酸混合物,塔底产物30然后直接进入糠醛成品塔31进行分离,塔底得到糠醛产品32,纯度大于99.5%,塔顶产物33为甲酸和醋酸混合物,塔顶产物33进入醋酸精制塔34进行分离,塔顶得到甲酸产品35,其纯度大于99.5%,塔底得到醋酸产品36,其纯度大于99.5%。
下面通过实施例进一步说明本发明的方法和效果。涉及的百分含量为质量百分含量。
实施例中戊糖转化率、糠醛收率以及酸回收率通过下式进行计算。
。
实施例1
原料戊糖溶液中,糠醛、醋酸、甲酸浓度分别为4.9wt%、3.1wt%、0.6wt%,硫酸钠浓度3wt%。
萃取剂为苯、醋酸乙酯、1,1,1-三氯乙烷混合溶剂,其中,苯占40wt%,醋酸乙酯占20wt%,1,1,1-三氯乙烷占40wt%。
萃取剂与戊糖溶液进料比为3:1(体积比),萃取剂与戊糖溶液的进料速率等于撞击流反应器体积(即进料体积空速为1 h-1,也即反应时间为1 h),将萃取剂和戊糖溶液分别用泵打入撞击流反应器内,与循环物料在撞击流反应器中快速混合发生反应-萃取过程,循环物料速率为进料量的200%。控制反应温度为200 ℃,反应压力为3 MPa。
实验结果表明戊糖转化率为97.4%,糠醛收率为82.6%,醋酸回收率为91.3%,甲酸回收率为90.5%。
实施例2
按照实施例1的方法,不同之处为进料速率为撞击流反应器容积的2倍,即反应时间为0.5 h。
实验结果表明戊糖转化率为78.1%,糠醛收率为61.9%,醋酸回收率为94.5%,甲酸回收率为91.8%。
实施例3
按照实施例1的方法,不同之处为进料速率为撞击流反应器容积的0.67倍,即反应时间为1.5 h。
实验结果表明戊糖转化率为99%,糠醛收率为83.5%,醋酸回收率为94.3%,甲酸回收率为91.5%。
实施例4
按照实施例1的方法,不同之处为循环物流为进料量的100%。
实验结果表明戊糖转化率为96.8%,糠醛收率为82.9%,醋酸回收率为92.8%,甲酸回收率为91.5%。
实施例5
按照实施例1的方法,不同之处为循环物流为进料量的300%。
实验结果表明戊糖转化率为96.1%,糠醛收率为81.8%,醋酸回收率为93.9%,甲酸回收率为91.9%。
实施例6
按照实施例1的方法,不同之处为反应温度变为180℃。
实验结果表明戊糖转化率为45.5%,糠醛收率为39.4%,醋酸回收率为95.3%,甲酸回收率为93.1%。
实施例7
按照实施例1的方法,不同之处为反应温度变为220℃。
实验结果表明戊糖转化率为99.5%,糠醛收率为84.8%,醋酸回收率为94.2%,甲酸回收率为91.9%。
实施例8
按照实施例1的方法,不同之处为硫酸钠浓度变为零。
实验结果表明戊糖转化率为94.1%,糠醛收率为76.9%,醋酸回收率为83.1%,甲酸回收率为81.9%。
实施例9
按照实施例1的方法,不同之处为硫酸钠浓度变为5%。
实验结果表明戊糖转化率为97.8%,糠醛收率为84.1%,醋酸回收率为94.6%,甲酸回收率为93.7%。
实施例13
按照实施例1的方法,不同之处为萃取剂与戊糖溶液进料比变为1:1。
实验结果表明戊糖转化率为97.9%,糠醛收率为78.1.3%,醋酸回收率为84.1%,甲酸回收率为80.5%。
实施例14
按照实施例1的方法,不同之处为萃取剂与戊糖溶液进料比变为5:1。
实验结果表明戊糖转化率为97.5%,糠醛收率为85.9%,醋酸回收率为94.8%,甲酸回收率为93.3%。
实施例15
按照实施例1的方法,不同之处为复合萃取剂组成变为:苯、醋酸乙酯、1,1,1-三氯乙烷质量比3:1:1。
实验结果表明戊糖转化率为97.7%,糠醛收率为77.9%,醋酸回收率为86.2%,甲酸回收率为83.3%。
实施例16
按照实施例1的方法,不同之处为复合萃取剂组成变为:苯、醋酸乙酯、1,1,1-三氯乙烷质量比1:1:3。
实验结果表明戊糖转化率为97.8%,糠醛收率为83.5%,醋酸回收率为82.2%,甲酸回收率为80.3%。
实施例17
按照实施例1的方法,不同之处为复合萃取剂组成变为:苯、醋酸乙酯、1,1,1-三氯乙烷质量比1:0:1。
实验结果表明戊糖转化率为97.8%,糠醛收率为83.9%,醋酸回收率为72.8%,甲酸回收率为71.8%。
实施例18
按照实施例1的方法,不同之处为复合萃取剂组成变为:苯、醋酸乙酯、1,1,1-三氯乙烷质量比0:1:1。
实验结果表明戊糖转化率为97.7%,糠醛收率为74.5%,醋酸回收率为93.2%,甲酸回收率为90.4%。
实施例19
按照实施例1的方法,不同之处为复合萃取剂组成变为:苯、醋酸乙酯、1,1,1-三氯乙烷质量比1:1:0。
实验结果表明戊糖转化率为97.8%,糠醛收率为76.9%,醋酸回收率为89.9%,甲酸回收率为86.7%。
实施例20
按照实施例1的方法,不同之处为复合萃取剂组成变为:苯、醋酸乙酯、1,1,1-三氯乙烷质量比1:0:0。
实验结果表明戊糖转化率为97.8%,糠醛收率为56.9%,醋酸回收率为39.9%,甲酸回收率为36.7%。
实施例21
按照实施例1的方法,不同之处为复合萃取剂组成变为:苯、醋酸乙酯、1,1,1-三氯乙烷质量比0:1:0。
实验结果表明戊糖转化率为97.8%,糠醛收率为58.2%,醋酸回收率为91.2%,甲酸回收率为88.9%。
比较例1
使用常规的撞击流反应器,如CN 102989404 A中介绍的撞击流反应器,其他同实施例1。
实验结果表明戊糖转化率为97.4%,糠醛收率为80.9%,醋酸回收率为88.6%,甲酸回收率为87.9%。