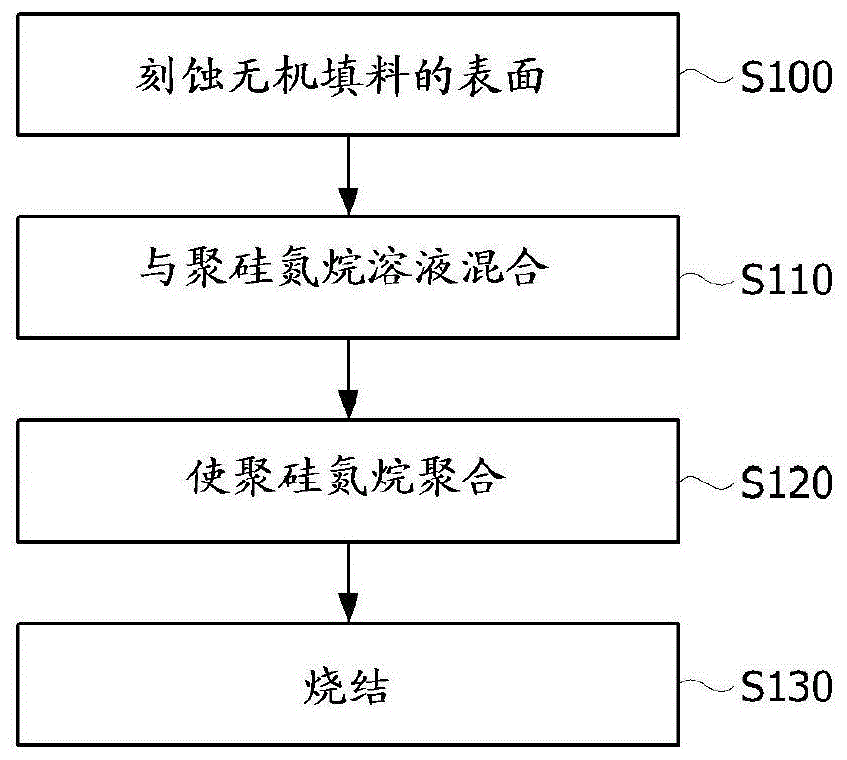
本发明涉及无机填料,更具体地,涉及包含在环氧树脂组合物中的无机填料。
背景技术:
:包含发光元件(例如发光二极管(led))的发光器件用于多种类型的光源中。根据半导体技术的发展,大功率发光元件的发展正在加速。为了稳定地与从这样的发光元件散发出的大量的光和热相符合,需要发光元件的辐射性能。此外,根据高度集成的和大功率电子部件的趋势,对其上安装有电子部件的印刷电路板的辐射的关注日益增加。通常,对于发光元件或印刷电路板的绝缘层,可使用包含环氧化合物、固化剂和无机填料的环氧树脂组合物。这里,无机填料可包括陶瓷基无机填料例如氮化硼、碳化硅、氧化铝或氮化铝或者碳基无机填料例如碳纳米管、石墨或石墨烯。根据包含在环氧树脂组合物中的无机填料的类型和含量,可改变环氧树脂组合物的分散性、绝缘性和热导率。虽然无机填料之一氮化硼具有非常高的热导率,但与环氧化合物的润湿性低、分散性低、对基底的粘合强度低以及加工性低。此外,面状氮化硼具有优良的热导率,但具有各向异性的热导率。为了解决这种问题,可使用面状氮化硼的团聚体,但是由于团聚体中的空隙,热导率可能降低,并且由于面状氮化硼之间的结合强度弱,团聚体容易断裂。技术实现要素:技术问题本发明旨在提供包含在环氧树脂组合物中的无机填料。技术方案根据本发明的一个示例性实施方案的无机填料包含形成在其表面上的涂层,并且涂层包含氧碳氮化硅(sicno)。无机填料可包含碳化硅(sic)、氮化硼(bn)、氧化铝(al2o3)和氮化铝(aln)中的至少一种。形成在碳化硅的表面上的涂层的厚度可以为50nm至200nm。形成在氮化硼的表面上的涂层的厚度可以为50nm至150nm。形成在氧化铝的表面上的涂层的厚度可以为10nm至100nm。形成在氮化铝的表面上的涂层的厚度可以为40nm至150nm。涂层可由聚硅氮烷(psz)形成。所述涂层可通过使无机填料的表面上的聚硅氮烷聚合并烧结聚合的产物而形成。根据本发明的一个示例性实施方案的环氧树脂组合物包含3重量%至40重量%的环氧化合物、0.5重量%至10重量%的固化剂和50重量%至95重量%的无机填料,并且所述无机填料包含其中表面涂覆有包含选自c、n和o中至少两种元素的陶瓷的氮化硼。陶瓷可包含氧碳氮化硅(sicno)或包含烷氧基团的金属氧化物。金属氧化物可包括氧化铝、氧化硅和氧化钛中的至少一种。金属氧化物可由铝醇盐、硅醇盐和钛醇盐中的至少一种形成。氮化硼可包含其中面状氮化硼发生团聚的团聚体。相对于环氧树脂组合物,可包含30重量%至39重量%的氮化硼。无机填料还可包含氧化铝和氮化铝中的至少一种。相对于10重量份的氮化硼,可包含7.4至9.7重量份的氮化铝,以及可包含5.6至7.4重量份的氧化铝。环氧化合物可包括结晶环氧化合物、非晶环氧化合物和硅环氧化合物中的至少一种,固化剂可包括基于胺的固化剂和基于酸酐的固化剂中的至少一种。环氧树脂组合物可具有14w/mk或更大的热导率和0.7kgf/cm或更大的剥离强度。环氧树脂组合物可具有16w/mk或更大的热导率和1kgf/cm或更大的剥离强度。根据本发明的一个示例性实施方案的印刷电路板包含基底、形成在基底上的绝缘层和形成在绝缘层上的电路图案,并且绝缘层包含环氧树脂组合物,环氧树脂组合物包含3重量%至40重量%的环氧化合物、0.5重量%至10重量%的固化剂和50重量%至95重量%的无机填料。这里,无机填料包含其中表面涂覆有包含选自c、n和o中至少两种元素的陶瓷的氮化硼。根据本发明的一个示例性实施方案的发光元件模块包含基底、在基底上形成的绝缘层、在绝缘层上形成的电路图案和在绝缘层上形成的发光元件,并且绝缘层包含环氧树脂组合物,环氧树脂组合物包含3重量%至40重量%的环氧化合物、0.5重量%至10重量%的固化剂和50重量%至95重量%的无机填料。这里,无机填料包含其中表面涂覆有包含选自c、n和o中至少两种元素的陶瓷的氮化硼。根据本发明的一个示例性实施方案的无机填料包含其中面状无机颗粒发生团聚的团聚体,并且在团聚体的空隙中形成有包含选自c、n和o中至少两种元素的陶瓷。面状无机颗粒可包含石墨和氮化硼(bn)中的至少一种。陶瓷可包含氧碳氮化硅(sicno)或碳氮化硅(sicn)。氧碳氮化硅或碳氮化硅可由聚硅氮烷(psz)形成。陶瓷可包含氧化铝、氧化硅和氧化钛中的至少一种,其各自均包含烷氧基团。烷氧基团可选自c1~c6烷基。陶瓷可由铝醇盐、硅醇盐和钛醇盐中的至少一种形成。根据本发明的一个示例性实施方案的环氧树脂组合物包含环氧化合物和包含其中面状无机颗粒发生团聚的团聚体的无机填料。这里,在团聚体的空隙中形成有包含选自c、n和o中至少两种元素的陶瓷。相对于10体积份的环氧化合物,可包含10至60体积份的其中氮化硼发生团聚的团聚体。相对于10体积份的环氧化合物,可包含15至55体积份的其中氮化硼发生团聚的团聚体。相对于10体积份的环氧化合物,可包含45至55体积份的其中氮化硼发生团聚的团聚体。环氧化合物可包含选自结晶环氧化合物、非晶环氧化合物和硅环氧化合物中的至少一种。根据本发明的一个示例性实施方案的发光元件模块包含基底、形成在基底上的绝缘层、形成在绝缘层上的电路图案和形成在绝缘层上的发光元件,并且绝缘层包含环氧树脂组合物,环氧树脂组合物包含环氧化合物和包含其中面状无机颗粒发生团聚的团聚体的无机填料。这里,在团聚体的空隙中形成有包含选自c、n和o中至少两种元素的陶瓷。根据本发明的一个示例性实施方案的无机填料包含形成在其表面上的涂层,并且涂层包含含有选自c、n和o中至少两种元素的陶瓷,并且在涂层的表面上形成有羟基(-oh)。无机填料可包含碳化硅(sic)、氮化硼(bn)、石墨、氧化铝(al2o3)和氮化铝(aln)中的至少一种。陶瓷可包含氧碳氮化硅(sicno)或碳氮化硅(sicn)。羟基可结合至氧碳氮化硅或碳氮化硅的si。无机填料可包含其中面状无机颗粒发生团聚的团聚体。无机颗粒可包含氮化硼和石墨中的至少一种。陶瓷可填充在团聚体的空隙中。根据本发明的一个示例性实施方案的环氧树脂组合物包含环氧化合物和包含形成在其表面上的涂层的无机填料。这里,涂层包含含有选自c、n和o中至少两种元素的陶瓷,并且在涂层的表面上形成有羟基(-oh)。可以以10∶10至50的体积比包含环氧化合物和无机填料。陶瓷可包含氧碳氮化硅(sicno)或碳氮化硅(sicn),并且羟基可结合至氧碳氮化硅或碳氮化硅的si。有益效果根据本发明的一个示例性实施方案,可获得应用于印刷电路板或发光元件的包含在环氧树脂组合物中的无机填料。因此,可获得具有良好分散性、优异的绝缘性、粘合强度和加工性、高剥离强度和高热导率的环氧树脂组合物,并且可增加印刷电路板或发光元件的热辐射特性和可靠性。此外,可获得具有优异的各向同性热导率的无机填料。附图说明图1和图2示出了根据本发明的一个示例性实施方案涂覆无机填料的表面的方法;图3至图8是例示了逐步涂覆无机填料的表面的扫描电子显微镜(sem)图像;图9和图10例示了根据本发明的一个示例性实施方案用陶瓷填充其中面状无机颗粒发生团聚的团聚体的空隙的方法;图11示出了氮化硼团聚体1200的形态;图12示出了其中空隙填充有sicno的氮化硼团聚体的形态;图13和图14例示了根据本发明的一个示例性实施方案处理无机填料的表面的方法;图15是根据本发明的一个示例性实施方案的印刷电路板的截面图;和图16是根据本发明的一个示例性实施方案的发光元件模块的截面图。具体实施方式可以以多种形式修改和实施本发明,因此,将仅详细地描述具体的实施方案。然而,本发明并不限于具体的公开内容,且应理解本发明覆盖包括在本发明的技术思想和范围内的所有修改方案、等同方案和替代方案。术语“第一”和“第二”可用于解释多种部件,但是部件不应受这些术语限制。这些术语仅用于将一个部件与另一个部件区分开。例如,在不脱离本发明的范围的情况下,第一部件可被称为第二部件,类似地,第二部件可被称为第一部件。术语“和/或”包括本文的多个相关项目中的任何一个或其组合。本发明中使用的术语仅用于解释具体的实施例,而不是限制本发明。,除非上下文中另有明确说明,否则单数表述包括复数指示物。本文使用的术语“包含/包括”和“具有”表明存在本说明书中描述的特征、数字、步骤、操作、组分、部件或其组合,并不意味着预先排除一种或更多种其他特性、数目、步骤、操作、组分、部件或其组合的存在或添加的可能性。除非另有限定,否则包括技术和科学术语的所有术语具有本领域技术人员通常理解的相同含义。除非在本发明中清楚地对其限定,否则一般的术语,例如在字典中定义的术语应当根据相关技术的上下文来解释,不应理解为具有理想的或过于形式化的含义。当一个部分例如层、膜、区域或板存在于另一部分“上”时,这意味着该部分“直接”存在于另一部分“上”,且还意味着第三部分存在于它们之间。相反,当一个部分“直接”存在于另一部分“上”时,这意味着它们之间没有任何东西。在下文中,将参考附图详细地描述示例性实施方案,且无论图上的标记为何,相同的附图标记代表相同的或相应的部件,并且其重复说明将被省略。在本说明书中,wt%可替换为重量份。i.其中形成有涂层的无机填料根据本发明的一个示例性实施方案的环氧树脂组合物包含环氧化合物、固化剂和其中表面涂覆有包含选自c、n和c中至少两种元素的陶瓷的无机填料。根据本发明的一个示例性实施方案的无机填料包含形成在其表面上的涂层,并且涂层包含含有选自c、n和o中至少两种元素的陶瓷,例如氧碳氮化硅(sicno)。当无机填料的表面涂覆有sicno时,与环氧化合物的润湿性增加,因此分散性、绝缘性和热导率可能增加。这里,无机填料可包含碳化硅(sic)、氮化硼(bn)、氧化铝(al2o3)和氮化铝(aln)中的至少一种,并且可以是球形。此外,涂层可由式1的聚硅氮烷(psz)形成。[式1]这里,r1、r2和r3各自可选自h、c1~c3烷基、c2~c3烯烃和c2~c3炔烃,并且n是正整数。图1和图2示出了根据本发明的一个示例性实施方案涂覆无机填料的表面的方法。参考图1和图2,对无机填料200,例如碳化硅(sic)、氮化硼(bn)、氧化铝(al2o3)和氮化铝(aln)的表面进行蚀刻(s100)。这里,碳化硅、氮化硼、氧化铝和氮化铝可以是球形或面状。这里,可使用基于氟化氢(hf)的溶液进行蚀刻。当对无机填料的表面蚀刻时,与聚硅氮烷的反应性可能增加。此外,将蚀刻的无机填料210与聚硅氮烷溶液混合(s110)。这里,聚硅氮烷溶液是稀释在溶剂中的聚硅氮烷单体。聚硅氮烷和溶剂的稀释比可以是例如10∶90的重量比,但本发明不受限制。聚硅氮烷和溶剂的稀释比可取决于涂层厚度。此外,使聚硅氮烷在无机填料210的表面上聚合(s120)。为此,可将无机填料210和聚硅氮烷溶液混合,然后在160℃下处理18小时。因此,可使聚硅氮烷单体交联并且可将聚合的聚硅氮烷涂覆在无机填料220的表面上。此外,将聚硅氮烷涂覆的无机填料烧结(s130)。为此,可将无机填料220在800℃下热解3小时。通过热解,可获得散发聚硅氮烷聚合物的ch4、c2h4、c2h6和nh3且在其表面上具有sicno陶瓷涂层的无机填料230。图3至图8是例示了逐步涂覆无机填料的表面的sem图像。图3和图4示出了碳化硅的未处理表面。图5和图6示出了涂覆有聚硅氮烷聚合物的碳化硅的表面。此外,图7和图8示出了涂覆有sicno的碳化硅的表面。参考图7和图8,可注意到,与图5和图6所示的涂覆有聚硅氮烷聚合物相比,无机填料的表面被均匀地涂覆。在下文中,将描述根据本发明的一个示例性实施方案测量无机填料的分散性、绝缘性和热导率的结果。首先,将描述通过改变无机填料的类型和涂层厚度来测量分散性的结果。涂层厚度可以根据图1的s110中使用的聚硅氮烷和溶剂的稀释比来控制。根据图1和图2所示的方法,将具有形成在其表面上的sicno涂层的碳化硅、氮化硼、氧化铝和氮化铝各5g分散在20g的甲基乙基酮(mek)中,然后观察分散性24小时。表1[表1]无机填料0nm5nm10nm20nm40nm50nm100nm200nm碳化硅xxxxpppp氮化硼xxxxxppp氧化铝pppppppp氮化铝xxxppppp参考表1,可注意到,当形成在碳化硅的表面上的sicno涂层的厚度为40nm或更大时,获得良好的分散性,且当形成在氮化硼的表面上的sicno涂层的厚度为50nm或更大时,可获得良好的分散性。此外,可注意到,当形成在氮化铝的表面上的sicno涂层的厚度为20nm或更大时,获得良好的分散性。当无机填料具有良好的分散性时,可获得具有均匀质量的环氧树脂组合物。此后,将描述根据无机填料的类型和涂层厚度测量电导率和热导率的结果。为此,制备具有多种类型和涂层厚度的无机填料的环氧树脂组合物。首先,为了制备环氧树脂组合物,将5g的结晶环氧化合物(4,4’-双酚醚二缩水甘油醚)、2.5g的式2的非晶环氧化合物、2.5g的式3的硅环氧化合物、1.25g的4,4’-二氨基二苯砜和1.25g的式4的基于酸酐的固化剂混合并溶解在30g的mek中20分钟。[式2][式3]这里,r1至r6可各自选自h、cl、br、f、c1~c3烷基、c1~c3烯烃、c1~c3炔烃和芳基。[式4]此外,将不同类型的无机填料各自添加到其中完成溶解的透明溶液中以具有不同的厚度,并搅拌2小时。将其中完成搅拌的溶液均匀地涂覆在铜板上,并在150℃下以恒定压力固化一个半小时,然后测量导电率和热导率。表2示出了测量导电率的结果,而表3示出了测量热导率的结果。在表3中,热导率的单位是w/mk。表2[表2]无机填料0nm5nm10nm20nm40nm50nm100nm200nm碳化硅0.1e-11.1e-12.8e-27.8e-50.4e-7溢出溢出溢出氮化硼3.6e-71.7e-83.2e-84.5e-9溢出溢出溢出溢出氧化铝溢出溢出溢出溢出溢出溢出溢出溢出氮化铝2.5e-74.5e-88.5e-83.1e-9溢出溢出溢出溢出表3[表3]参考表2,当形成在碳化硅的表面上的sicno涂层的厚度为50nm或更大时,或者形成在氮化硼的表面上的sicno涂层的厚度为40nm或更大时,无机填料可具有适合用作绝缘层的绝缘性。此外,可注意到,当形成在氮化铝的表面上的sicno涂层的厚度为40nm或更大时,无机填料可具有适于用作绝缘层的绝缘性。参考表3,可注意到,与没有涂层的无机填料(0nm)的热导率相比,当在无机填料的表面上形成有sicon涂层时,热导率显著增加。根据无机填料的类型,可注意到,当形成在碳化硅的表面上的sicno涂层的厚度为40nm至200nm时,无机填料的热导率为10w/mk或更大,而当形成在碳化硅表面上的sicno涂层的厚度为50nm至150nm时,无机填料的热导率为11w/mk或更大。此外,可注意到,当形成在氮化硼表面上的sicno涂层的厚度为5nm至150nm时,无机填料的热导率为15w/mk或更大,而当形成在氮化硼表面上的sicno涂层的厚度为50nm至100nm时,无机填料的热导率为16w/mk或更大。此外,可注意到,当形成在氧化铝表面上的sicno涂层的厚度为10nm至100nm时,无机填料的热导率为9w/mk或更大。此外,可注意到,当形成在氮化铝的表面上的sicno涂层的厚度为10nm至150nm时,无机填料的热导率为11w/mk或更大,并且当形成在氮化铝的表面上的sicno涂层的厚度为50nm至100nm时,无机填料的热导率为12w/mk或更大。根据表1至3中所示的测量分散性、绝缘性和热导率的结果的综合分析,形成在碳化硅的表面上的涂层的厚度可以是50nm至200nm,且优选50nm至150nm。形成在氮化硼的表面上的涂层的厚度可以是50nm至150nm,且优选50nm至100nm。形成在氧化铝的表面上的涂层的厚度可以是10nm至100nm,优选50nm至60nm。此外,形成在氮化铝的表面上的涂层的厚度可以是40nm至150nm,优选50nm至100nm。ii.包含其中形成有涂层的无机填料的环氧树脂组合物在下文中,将详细地描述根据本发明的一个示例性实施方案的包含无机填料的环氧树脂组合物。根据本发明的示例性实施方案的环氧树脂组合物包含环氧化合物、固化剂和无机填料,无机填料包含其中表面涂覆有包含选自c、n和o中至少两种元素的陶瓷的氮化硼。这里,r可选自c1~c6烷基。更具体地,根据本发明的示例性实施方案的环氧树脂组合物可包含3重量%至40重量%,优选3重量%至20重量%,且更优选9重量%至18重量%的环氧化合物,0.5重量%至10重量%,优选0.5重量%至5重量%,更优选0.5重量%至2重量%的固化剂;以及50重量%至95重量%,优选75重量%至95重量%,且更优选81重量%至90重量%的包含其中表面涂覆有包含选自c、n和o中至少两种元素的陶瓷的氮化硼的无机填料。当环氧树脂组合物包含3重量%至40重量%,优选3重量%至20重量%,更优选9重量%至18重量%的环氧化合物时,由于良好的硬度,获得优异的内聚特性(cohesiveproperty),且厚度易于控制。此外,当环氧树脂组合物包含0.5重量%至10重量%,优选0.5重量%至5重量%,更优选0.5重量%至2重量%的固化剂时,易于进行固化,并且由于良好的硬度,获得优异的内聚特性。此外,当环氧树脂组合物包含50重量%至95重量%,优选75重量%至95重量%,更优选81重量%至90重量%的其中表面涂覆有包含选自c、n和o中至少两种元素的陶瓷的氮化硼的无机填料时,获得优异的粘合强度和热导率以及低电导率,还获得低的热膨胀特性、高耐热性和优异的可塑性。这里,环氧化合物可包括结晶环氧化合物、非晶环氧化合物和硅环氧化合物中的至少一种。结晶环氧化合物可包括介晶(mesogen)结构。介晶是液晶的基本单元且包含刚性结构。介晶可包括例如(a)至(e)中所示的刚性结构之一。(a)(b)(c)(d)(e)包含介晶结构的结晶环氧化合物可包括但不限于:例如4,4’-双酚醚二缩水甘油醚,即se-4280。根据本发明的一个示例性实施方案,结晶环氧化合物可包括例如式5至式16中所示的化合物中的至少一种。[式5][式6][式7][式8][式9][式10][式11][式12][式13][式14][式15][式16]此外,根据本发明的一个示例性实施方案的环氧树脂组合物还可包含非晶环氧化合物。相对于10重量份的结晶环氧化合物,可包含3重量份至40重量份的非晶环氧化合物。当以上述比例包含结晶环氧化合物和非晶环氧化合物时,可提高室温稳定性。非晶环氧化合物可以是分子中具有至少两个环氧基团的常规非晶环氧化合物。非晶环氧化合物可以是衍生自以下中一种的缩水甘油醚化合物:二元酚,例如双酚a、双酚f、3,3’,5,5’-四甲基-4,4’-二羟基二苯基甲烷、4,4’-二羟基二苯砜、4,4’-二羟基二苯硫醚、4,4’-二羟基二苯酮、双酚芴、4,4’-双酚、3,3’5,5’-四甲基-4,4’-二羟基二苯基、2,2’-双酚、间苯二酚、邻苯二酚、叔丁基邻苯二酚、对苯二酚、叔丁基对苯二酚、1,2-二羟基萘、1,3-二羟基萘、1,4-二羟基萘、1,5-二羟基萘、1,6-二羟基萘、1,7-二羟基萘、1,8-二羟基萘、2,3-二羟基萘、2,4-二羟基萘、2,5-二羟基萘、2,6-二羟基萘、2,7-二羟基萘、2,8-二羟基萘、二羟基萘的烯丙基化化合物或多烯丙基化化合物、烯丙基化双酚a、烯丙基化双酚f和烯丙基化苯酚酚醛清漆;三元或更多元酚例如苯酚酚醛清漆、双酚a酚醛清漆、邻甲酚酚醛清漆、间甲酚酚醛清漆、对甲酚酚醛清漆、二甲酚酚醛清漆、聚对羟基苯乙烯、三-(4-羟基苯基)甲烷、1,1,2,2-四(4-羟基苯基)乙烷、氟代乙醇胺(fluoroglycinol)、邻苯三酚、叔丁基邻苯三酚、烯丙基化邻苯三酚、多烯丙基化邻苯三酚、1,2,4-苯三酚、2,3,4-三羟基二苯甲酮、苯酚芳烷基树脂、萘酚芳烷基树脂和基于二环戊二烯的树脂;卤代双酚例如四溴双酚a及其混合物。双酚a型环氧化合物的实例在式2中示出。[式2]此外,根据本发明的一个示例性实施方案的环氧树脂组合物还可包含硅环氧化合物。相对于10重量份的结晶环氧化合物,可包含3重量份至40重量份的硅环氧化合物。当以上述比例包含结晶环氧化合物和硅环氧化合物时,可提高热导率和耐热性。硅环氧化合物的实例在式3中示出。[式3]这里,r1至r6可各自选自h、cl、br、f、c1~c3烷基、c2~c3烯烃、c2~c3炔烃和芳基。此外,根据本发明的一个示例性实施方案包含在环氧树脂组合物中的固化剂可包括基于胺的固化剂、基于酚的固化剂、基于酸酐的固化剂、基于多硫醇的固化剂、基于聚氨基酰胺的固化剂、基于异氰酸酯的固化剂和基于嵌段异氰酸酯的固化剂。基于胺的固化剂可以是例如4,4’-二氨基二苯砜。式17示出了二氨基二苯砜的实例。[式17]基于胺的固化剂的其他实例可包括脂肪族胺、聚醚多胺、脂环族胺和芳香族胺。对于脂肪族胺,可使用乙二胺、1,3-二氨基丙烷、1,4-二氨基丙烷、六亚甲基二胺、2,5-二甲基六亚甲基二胺、三甲基六亚甲基二胺、二亚乙基三胺、亚氨基双丙胺、双(六亚甲基)三胺、三亚乙基四胺、四亚乙基五胺、五亚乙基六胺、n-羟乙基亚乙基二胺或四(羟乙基)亚乙基二胺。聚醚多胺可以是以下中的一种:三乙二醇二胺、四乙二醇二胺、二乙二醇双(丙胺)、聚氧丙烯二胺、聚氧丙烯三胺及其混合物。对于脂环族胺,可使用异佛尔酮二胺、孟烷二胺(metacendiamine)、n-氨乙基哌嗪、双(4-氨基-3-甲基二环己基)甲烷、双(氨甲基)环己烷、3,9-双(3-氨丙基)2,4,8,10-四氧杂螺(5,5)十一烷或降冰片烯二胺。芳香族胺可以是四氯对亚二甲苯基胺、间亚二甲苯基二胺、对亚二甲苯基二胺、间苯二胺、邻苯二胺、对苯二胺、2,4-二氨基苯甲醚、2,4-甲苯二胺、2,4-二氨基二苯甲烷、4,4’-二氨基二苯甲烷、4,4’-二氨基-1,2-二苯乙烷、2,4-二氨基二苯砜、间氨基苯酚、间氨基苄胺、苄基二甲胺、2-(二甲基氨基甲基)苯酚、三乙醇胺、甲基苄胺、α-(间氨基苯基)乙胺、α-(对氨基苯基)乙胺、二氨基二乙基二甲基二苯基甲烷、α,α′-双(4-氨基苯基)-对-二异丙基苯及其混合物。基于酚的固化剂可以是例如以下中的一种:双酚a、双酚f、4,4’-二羟基二苯甲烷、4,4’-二羟基二苯醚、1,4-双(4-羟基苯氧基)苯、1,3-双(4-羟基苯氧基)苯、4,4’-二羟基二苯基硫醚、4,4’-二羟基二苯基酮、4,4’-二羟基二苯砜、4,4’-二羟基二苯基酯、4,4’-二羟基二苯基、2,2’-二羟基二苯基、10-(2,5-二羟基苯基)-10h-9-氧杂-10-磷杂菲-10-氧化物、苯酚酚醛清漆、双酚a酚醛清漆、邻甲酚酚醛清漆、间甲酚酚醛清漆、对甲酚酚醛清漆、二甲苯酚酚醛清漆、聚对羟基苯乙烯、对苯二酚、间苯二酚、邻苯二酚、叔丁基邻苯二酚、叔丁基对苯二酚、氟代乙醇胺、邻苯三酚、叔丁基邻苯三酚、烯丙基化邻苯三酚、多烯丙基化邻苯三酚、1,2,4-苯三酚、2,3,4-三羟基二苯甲酮、1,2-二羟基萘、1,3-二羟基萘、1,4-二羟基萘、1,5-二羟基萘、1,6-二羟基萘、1,7-二羟基萘,1,8-二羟基萘、2,3-二羟基萘、2,4-二羟基萘、2,5-二羟基萘、2,6-二羟基萘、2,7-二羟基萘、2,8-二羟基萘、二羟基萘的烯丙基化或多烯丙基化化合物、烯丙基化双酚a、烯丙基化双酚f、烯丙基化苯酚酚醛清漆、烯丙基化邻苯三酚及其混合物。基于酸酐的固化剂可包括例如式4的化合物。[式4]此外,基于酸酐的固化剂可以是例如以下中的一种:十二碳烯基琥珀酸酐、聚(己二酸酐)、聚(壬二酸酐)、聚(癸二酸酐)、聚(乙基十八烷二酸)酸酐、聚(苯基十六烷二酸)酸酐、甲基四氢邻苯二甲酸酐、甲基六氢邻苯二甲酸酐、六氢邻苯二甲酸酐、甲基纳迪克酸酐(methylhimicanhydride)、四氢邻苯二甲酸酐、三烷基四氢邻苯二甲酸酐、甲基环己烯二羧酸酐、甲基环己烯四羧酸酐、邻苯二甲酸酐、偏苯三酸酐、均苯四酸酐、二苯甲酮四羧酸酐、乙二醇双偏苯三酸酯、氯菌酸酐、纳迪克酸酐(nadicanhydride)、甲基纳迪克酸酐、5-(2,5-二氧代四氢-3-呋喃基)-3-甲基-3-环己烷-1,2-二羧酸酐、3,4-二羧基-1,2,3,4-四氢-1-萘琥珀酸二酸酐、1-甲基-二羧基-1,2,3,4-四氢-1-萘琥珀酸二酐及其混合物。根据本发明的一个示例性实施方案,可以混合至少两种类型的固化剂。根据本发明的一个示例性实施方案的环氧树脂组合物还可包含固化促进剂。固化促进剂可以是例如胺固化促进剂、咪唑固化促进剂、有机膦固化促进剂或路易斯酸固化促进剂,具体地,叔胺例如1,8-二氮杂双环(5,4,0)十一碳烯-7,三亚乙基二胺、苄基二甲胺、三乙醇胺、二甲基氨基乙醇或三(二甲基氨基甲基)苯酚,咪唑例如2-甲基咪唑、2-苯基咪唑、2-苯基-4-甲基咪唑或2-十七烷基咪唑,有机膦例如三丁基膦、甲基二苯基膦、三苯基膦、二苯基膦或苯基膦,四取代的·四取代的硼酸盐例如四苯基·四苯基硼酸盐、四苯基·乙基三苯基硼酸盐或四丁基·四丁基硼酸盐或者四苯基硼酸酯例如2-乙基-4-甲基咪唑·四苯基硼酸酯或n-甲基吗啉.四苯基硼酸酯。这里,相对于环氧树脂组合物的总重量,可包含30重量%至39重量%,优选32重量%至37重量%的其中表面涂覆有包含选自c、n和o中至少两种元素的陶瓷或者包含烷氧(-or)基团的金属氧化物的氮化硼。当以上述范围包含经涂覆的氮化硼时,环氧树脂组合物可具有16w/mk或更大的的热导率和1kgf/cm或更大的剥离强度。这里,氮化硼可以是其中面状氮化硼发生团聚的氮化硼团聚体。氮化硼团聚体可具有0.3g/cm3至0.4g/cm3的密度。当包含氮化硼团聚体作为无机填料时,可提高穿过平面的热导率,因此可获得比面状氮化硼更高的热导率。这里,当氮化硼团聚体具有大于0.4g/cm3的密度时,分散性可能降低。此外,当氮化硼团聚体具有小于0.3g/cm3的密度时,可能无法获得比面状氮化硼的热导率更高的热导率。此外,包含sicno的涂层可以由如上所述的式1的聚硅氮烷(psz)形成。包含烷氧(-or)基团的金属氧化物(例如氧化铝、氧化硅或氧化钛)可分别通过式18的铝醇盐(al醇盐)、式19的硅醇盐(si醇盐)或式20的钛醇盐(ti醇盐)的脱水缩合形成。[式18]这里,r1至r3各自可选自h和c1~c6烷基。[式19]这里,r1至r4各自可选自h和c1~c6烷基。[式20]这里,r1至r4各自可选自h和c1~c6烷基。从硅醇盐形成包含烷氧基团的氧化硅的机理示于以下反应式中。涂覆氮化硼的表面的方法如上所述在图1和图2中示出。这里,当氮化硼是其中面状氮化硼发生团聚的氮化硼团聚体时,团聚体中的空隙可以用sicno填充。同样,当团聚体中的空隙用陶瓷填充时,可进一步提高热传导性能。此外,根据本发明的一个示例性实施方案,无机填料还可包含氧化铝和氮化铝中的至少一种。例如,相对于10重量份的其中表面涂覆有sicno或金属氧化物的氮化硼,可包含7.4至9.7重量份的氮化铝,可包含5.6至7.4重量份的氧化铝。当进一步包含氧化铝和氮化铝时,可进一步提高热导率和剥离强度。当以上述比例包含氧化铝、氮化铝和氮化硼时,环氧树脂组合物可具有16w/mk或更大的热导率和1kgf/cm或更大的剥离强度。根据本发明的一个示例性实施方案的环氧树脂组合物还可包含催化剂、添加剂和溶剂。催化剂可包括例如式21中所示的基于咪唑的添加剂。[式21]当根据本发明的一个示例性实施方案的环氧树脂组合物包含式21的催化剂时,可提高与金属的粘合特性。因此,由于绝缘层和由铜构成的电路图案之间的粘合强度提高,以及脱离可能性和分离可能性降低,印刷电路板易于加工且印刷电路板的可靠性提高。在下文中,将参考实施例和比较例进一步详细地描述本发明。<实施例ii-1>将11重量%的结晶环氧化合物(4,4’-双酚醚二缩水甘油醚)、4重量%的式2的非晶环氧化合物、4重量%的其中r为苯基的式3的硅环氧化合物、0.5重量%的4,4’-二氨基二苯砜和0.5重量%的式4的基于酸酐的固化剂溶解在mek中20分钟,并将29重量%的其中表面涂覆有sicno的氮化硼[这里,其中表面涂覆有sicno(涂层厚度:100nm)的氮化硼通过以下制备:使用基于氢氟酸(hf)的溶液对其中面状氮化硼发生团聚的氮化硼团聚体的表面进行蚀刻,将蚀刻的所得物与聚硅氮烷溶液混合并将所得混合物在160℃下处理18小时,并使所得产物在800℃下热分解3小时]、29重量%的氮化铝和22重量%的氧化铝搅拌2小时。将其中完成搅拌的溶液涂覆在铜板上,并在150℃下压一个半小时,从而获得实施例ii-1的环氧树脂组合物。<实施例ii-2>将10重量%的结晶环氧化合物(4,4’-双酚醚二缩水甘油醚)、4重量%的式2的非晶环氧化合物、4重量%的其中r为苯基的式3的硅环氧化合物、0.5重量%的4,4’-二氨基二苯砜和0.5重量%的式4的基于酸酐的固化剂溶解在mek中20分钟,并将30重量%的其中表面涂覆有sicno的氮化硼[这里,其中表面涂覆有sicno(涂层厚度:100nm)的氮化硼通过以下制备:使用基于hf的溶液对其中面状氮化硼发生团聚的氮化硼团聚体的表面进行蚀刻,将蚀刻的所得物与聚硅氮烷溶液混合并将所得混合物在160℃下处理18小时,并使所得产物在800℃下热分解3小时]、29重量%的氮化铝和22重量%的氧化铝搅拌2小时。将其中完成搅拌的溶液涂覆在铜板上,在150℃下压一个半小时,从而获得实施例ii-2的环氧树脂组合物。<实施例ii-3>将5重量%的结晶环氧化合物(4,4’-双酚醚二缩水甘油醚)、4重量%的式2的非晶环氧化合物、4重量%的其中r为苯基的式3的硅环氧化合物、0.5重量%的4,4’-二氨基二苯砜和0.5重量%的式4的基于酸酐的固化剂溶解在mek中20分钟,并将35重量%的其中表面涂覆有sicno的氮化硼[这里,其中表面涂覆有sicno(涂层厚度:100nm)的氮化硼通过以下制备:使用基于hf的溶液对其中面状氮化硼发生团聚的氮化硼团聚体的表面进行蚀刻,将蚀刻的所得物与聚硅氮烷溶液混合并将所得混合物在160℃下处理18小时,并使所得产物在800℃下热分解3小时]、29重量%的氮化铝和22重量%的氧化铝搅拌2小时。将其中完成搅拌的溶液涂覆在铜板上,在150℃下压一个半小时,从而获得实施例ii-3的环氧树脂组合物。<实施例ii-4>将5重量%的结晶环氧化合物(4,4’-双酚醚二缩水甘油醚)、2重量%的式2的非晶环氧化合物、2重量%的其中r为苯基的式3的硅环氧化合物、0.5重量%的4,4’-二氨基二苯砜和0.5重量%的式4的基于酸酐的固化剂溶解在mek中20分钟,并将39重量%的其中表面涂覆有sicno的氮化硼[这里,其中表面涂覆有sicno(涂层厚度:100nm)的氮化硼通过以下制备:使用基于hf的溶液对其中面状氮化硼发生团聚的氮化硼团聚体的表面进行蚀刻,将蚀刻的所得物与聚硅氮烷溶液混合并将所得混合物在160℃下处理18小时,并使所得产物在800℃下热分解3小时]、29重量%的氮化铝和22重量%的氧化铝搅拌2小时。将其中完成搅拌的溶液涂覆在铜板上,在150℃下压一个半小时,从而获得实施例ii-4的环氧树脂组合物。<买施例ii-5>将4重量%的结晶环氧化合物(4,4’-双酚醚二缩水甘油醚)、2重量%的式2的非晶环氧化合物、2重量%的其中r为苯基的式3的硅环氧化合物、0.5重量%的4,4’-二氨基二苯砜和0.5重量%的式4的基于酸酐的固化剂溶解在mek中20分钟,并将40重量%的其中表面涂覆有sicno的氮化硼[这里,其中表面涂覆有sicno(涂层厚度:100nm)的氮化硼通过以下制备:使用基于hf的溶液对其中面状氮化硼发生团聚的氮化硼团聚体的表面进行蚀刻,将蚀刻的所得物与聚硅氮烷溶液混合并将所得混合物在160℃下处理18小时,并使所得产物在800℃下热分解3小时]、29重量%的氮化铝和22重量%的氧化铝搅拌2小时。将其中完成搅拌的溶液涂覆在铜板上,在150℃下压一个半小时,从而获得实施例ii-5的环氧树脂组合物。<实施例ii-6>将11重量%的结晶环氧化合物(4,4’-双酚醚二缩水甘油醚)、4重量%的式2的非晶环氧化合物、4重量%的其中r为苯基的式3的硅环氧化合物、0.5重量%的4,4’-二氨基二苯砜和0.5重量%的式4的基于酸酐的固化剂溶解在mek中20分钟,并将29重量%的其中表面涂覆有具有-or基团(其中r为c1烷基)的氧化铝的氮化硼[这里,经涂覆的氮化硼通过以下制备:使用基于hf的溶液对其中面状氮化硼发生团聚的氮化硼团聚体的表面进行蚀刻,将蚀刻的所得物与铝醇盐溶液(-or,其中r是c1)混合并将所得混合物在160℃下处理18小时,并使所得产物在800℃下热解3小时]、29重量%的氮化铝和22重量%的氧化铝搅拌2小时。将其中完成搅拌的溶液涂覆在铜板上,在150℃下压一个半小时,从而获得实施例ii-6的环氧树脂组合物。<实施例ii-7>将10重量%的结晶环氧化合物(4,4’-双酚醚二缩水甘油醚)、4重量%的式2的非晶环氧化合物、4重量%的其中r为苯基的式3的硅环氧化合物、0.5重量%的4,4’-二氨基二苯砜和0.5重量%的式4的基于酸酐的固化剂溶解在mek中20分钟,并将30重量%的其中表面涂覆有具有-or基团(其中r为c1烷基)的氧化铝的氮化硼[这里,经涂覆的氮化硼通过以下制备:使用基于hf的溶液对其中面状氮化硼发生团聚的团聚体的表面进行蚀刻,将蚀刻的所得物与铝醇盐溶液(-or,其中r是c1)混合并将所得混合物在160℃下处理18小时,并使所得产物在800℃下热解3小时]、29重量%的氮化铝和22重量%的氧化铝搅拌2小时。将其中完成搅拌的溶液涂覆在铜板上,在150℃下压一个半小时,从而获得实施例ii-7的环氧树脂组合物。<实施例ii-8>将5重量%的结晶环氧化合物(4,4’-双酚醚二缩水甘油醚)、4重量%的式2的非晶环氧化合物、4重量%的其中r为苯基的式3的硅环氧化合物、0.5重量%的4,4’二氨基二苯砜和0.5重量%的式4的基于酸酐的固化剂溶解在mek中20分钟,并将35重量%的其中表面涂覆有具有-or基团(其中r为c1烷基)的氧化铝的氮化硼[这里,经涂覆的氮化硼通过以下制备:使用基于hf的溶液对其中面状氮化硼发生团聚的氮化硼团聚体的表面进行蚀刻,并将蚀刻的所得物与铝醇盐溶液(-or,其中r是c1)混合并将所得混合物在160℃下处理18小时,并使所得产物在800℃下热解3小时]、29重量%的氮化铝和22重量%的氧化铝搅拌2小时。将其中完成搅拌的溶液涂覆在铜板上,在150℃下压一个半小时,从而获得实施例ii-8的环氧树脂组合物。<实施例ii-9>将5重量%的结晶环氧化合物(4,4’-双酚醚二缩水甘油醚)、2重量%的式2的非晶环氧化合物、2重量%的其中r为苯基的式3的硅环氧化合物、0.5重量%的4,4’-二氨基二苯砜和0.5重量%的式4的基于酸酐的固化剂溶解在mek中20分钟,并将39重量%的其中表面涂覆有具有-or基团(其中r为c1烷基)的氧化铝的氮化硼[这里,经涂覆的氮化硼通过以下制备:使用基于hf的溶液对其中面状氮化硼发生团聚的氮化硼团聚体的表面进行蚀刻,并将蚀刻的所得物与铝醇盐溶液(-or,其中r是c1)混合并将所得混合物在160℃下处理18小时,并使所得产物在800℃下热解3小时]、29重量%的氮化铝和22重量%的氧化铝搅拌2小时。将其中完成搅拌的溶液涂覆在铜板上,在150℃下压一个半小时,从而获得实施例ii-9的环氧树脂组合物。<实施例ii-10>将4重量%的结晶环氧化合物(4,4’-双酚醚二缩水甘油醚)、2重量%的式2的非晶环氧化合物、2重量%的其中r为苯基的式3的硅环氧化合物、0.5重量%的4,4’-二氨基二苯砜和0.5重量%的式4的基于酸酐的固化剂溶解在mek中20分钟,并且将40重量%的其表面涂覆有具有-or基团(其中r为c1烷基)的氧化铝的氮化硼[这里,经涂覆的氮化硼通过以下进行制备:使用基于hf的溶液对其中面状氮化硼发生团聚的氮化硼团聚体的表面进行蚀刻,将蚀刻所得物与铝醇盐溶液(-or,其中r是c1)混合并将所得混合物在160℃下处理18小时,并使所得产物在800℃下热解3小时]、29重量%的氮化铝和22重量%的氧化铝搅拌2小时。将其中完成搅拌的溶液涂覆在铜板上,在150℃下压一个半小时,从而获得实施例ii-10的环氧树脂组合物。<比较例ii-1>将11重量%的结晶环氧化合物(4,4’-双酚醚二缩水甘油醚)、4重量%的式2的非晶环氧化合物、4重量%的其中r为苯基的式3的硅环氧化合物、0.5重量%的4,4’-二氨基二苯砜和0.5重量%的式4的基于酸酐的固化剂溶解在mek中20分钟,并将29重量%的氮化硼(这里,氮化硼包含其中面状氮化硼发生团聚的氮化硼团聚体)、29重量%的氮化铝和22重量%的氧化铝搅拌2小时。将其中完成搅拌的溶液涂覆在铜板上,在150℃下压一个半小时,从而获得比较例ii-1的环氧树脂组合物。<比较例ii-2>将6重量%的结晶环氧化合物(4,4’-双酚醚二缩水甘油醚)、3.5重量%的式2的非晶环氧化合物、3.5重量%的其中r为苯基的式3的硅环氧化合物、0.5重量%的4,4’-二氨基二苯砜和0.5重量%的式4的基于酸酐的固化剂溶解在mek中20分钟,并将35重量%的氮化硼(这里,氮化硼包含其中面状氮化硼发生团聚的氮化硼团聚体)、29重量%的氮化铝和22重量%的氧化铝搅拌2小时。将其中完成搅拌的溶液涂覆在铜板上,在150℃下压一个半小时,从而获得比较例ii-2的环氧树脂组合物。<比较例ii-3>将4重量%的结晶环氧化合物(4,4’-双酚醚二缩水甘油醚)、2重量%的式2的非晶环氧化合物、2重量%的其中r为苯基的式3的硅环氧化合物、0.5重量%的4,4’-二氨基二苯砜和0.5重量%的式4的基于酸酐的固化剂溶解在mek中20分钟,并将40重量%的氮化硼(这里,氮化硼包含其中面状氮化硼发生团聚的氮化硼团聚体)、29重量%的氮化铝和22重量%的氧化铝搅拌2小时。将其中完成搅拌的溶液涂覆在铜板上,在150℃下压一个半小时,从而获得比较例ii-3的环氧树脂组合物。<实验例>将实施例ii-1至实施例ii-10和比较例ii-1至比较例ii-3中得到的组合物固化,然后使用lfa447nanoflash(由netzsch制造)通过瞬态热线法测量热导率。此外,使用由ymtech制造的装置在垂直方向上在50mm/分钟的速率条件下并使用厚度为62.5mm的铜层测量剥离强度。测量结果示于表4和表5。表4[表4]表5[表5]参考表4和5,可注意到,包含环氧化合物、固化剂和其中表面涂覆有氧碳氮化硅的氮化硼作为无机填料的实施例ii-1至实施例ii-5和包含环氧化合物、固化剂和其中表面涂覆有包含-or的陶瓷的氮化硼作为无机填料的实施例ii-6和实施例ii-10,满足这样的条件:热导率为14w/mk或更大,剥离强度为0.7kgf/cm或更大。相反,可注意到,其中无机填料的类型和含量相同但氮化硼的表面未涂覆有陶瓷的比较例ii-1至比较例ii-3具有小于12w/mk的低热导率以及0.4kgf/cm或更低的相当低的剥离强度。此外,可注意到,相对于环氧树脂组合物的总重量,包含30重量%至39重量%的其中表面涂覆有陶瓷的氮化硼作为无机填料,以及相对于10重量份的氮化硼,包含7.4重量份至9.7重量份的氮化铝和5.6重量份至7.4重量份的氧化铝的实施例ii-2至实施例ii-4和实施例ii-7至实施例ii-9的组合物具有16w/mk或更大的热导率以及1kgf/cm或更大的剥离强度。iii.无机填料,其是具有填充有陶瓷的空隙的团聚体同时,根据本发明的一个示例性实施方案的环氧树脂组合物中包含的无机填料可包含其中面状无机颗粒发生团聚的团聚体并且在团聚体中的空隙中可形成有包含选自c、n和o中至少两种元素的陶瓷。同样地,当无机填料包含其中面状无机颗粒发生团聚的团聚体时,可获得在各个方向上表现出均匀热导率的各向同性导热特性,并且分散性和绝缘性也可提高。特别地,当团聚体中的空隙被填充时,由于团聚体中的空气层被最小化,所以可提高热导率,并且可提高形成团聚体的面状无机颗粒之间的结合强度从而防止团聚体破裂。这里,面状无机颗粒可包含石墨和氮化硼(bn)中的至少一种。此外,面状无机颗粒可包含其中石墨和氮化硼中的每一个存在于平面上的混合填料。同时,在团聚体中的空隙中填充的陶瓷可包含氧碳氮化硅(sicno)或碳氮化硅(sicn)。这里,sicno或sicn可由如上所述的式1的聚硅氮烷(psz)形成。或者,填充在团聚体的空隙中的陶瓷可包含含有烷氧基团的氧化铝、含有烷氧基团的氧化硅和含有烷氧基团的氧化钛中的至少一种。这里,如上所述,氧化铝可通过铝醇盐(al醇盐)的水解和脱水缩合形成,氧化硅可以通过硅醇盐的水解和脱水缩合形成,氧化钛可通过钛醇盐的水解和脱水缩合形成。图9和图10例示了根据本发明的一个示例性实施方案填充其中面状无机颗粒发生团聚的团聚体的空隙的方法。为了便于说明,假设面状无机颗粒是面状氮化硼并且陶瓷是sicno来对该方法进行描述,但是本发明不限于此。参考图9和图10,将氮化硼团聚体1200与聚硅氮烷混合(s110)。图11示出了氮化硼团聚体1200的形态。当通过edx分析测定图11的氮化硼团聚体1200的表面时,包含75.33重量%的b以及包含24.67重量%的n,以及当通过edx分析测定其截面时,包含73.58重量%的b以及包含26.42a重量%的n。例如,聚硅氮烷可以是单体或低聚物,可将30g的聚硅氮烷和30g的氮化硼团聚体1200搅拌5分钟,然后用溶剂(例如丙酮)洗涤。为此,可使用基于hf的溶液预先对氮化硼团聚体1200进行蚀刻。当氮化硼团聚体1200被蚀刻后,可提高对聚硅氮烷的反应性。因此,液体聚硅氮烷可填充在空隙中以及氮化硼团聚体1210的表面上。随后,使氮化硼团聚体1210的空隙中和表面上的液体聚硅氮烷聚合(s1110)。为此,可将氮化硼团聚体1210在160℃至180℃下处理18至24小时。因此,聚硅氮烷单体或低聚物可通过脱水缩合而交联以填充氮化硼团聚体1220的空隙或涂覆氮化硼团聚体1220的表面。此外,将氮化硼团聚体1220烧结(s1120)。为此,可将氮化硼团聚体1220在700℃至800℃下热解2至3小时。随着热解,释放出聚硅氮烷聚合物的ch4、c2h4、c2h6和nh3,并且可获得其中空隙和表面填充有sicno陶瓷的氮化硼团聚体1230。图12示出了其中空隙填充有sicno的氮化硼团聚体的形态。当通过edx分析测定图12的氮化硼团聚体的表面时,包含50.23重量%的b、9.00重量%的c、7.56重量%的n、4.69重量%的o、28.53重量%的si,以及当通过edx分析测定图12的氮化硼团聚体的截面时,包含53.40重量%的b、9.16重量%的c、12.14重量%的n、5.93重量%的o、19.38重量%的si。当在氮气气氛中进行s1120中描述的热解时,可用包含sicn的陶瓷填充空隙。同样,当将液体陶瓷前体(例如聚硅氮烷、铝醇盐、硅醇盐或钛醇盐)与氮化硼团聚体混合并加热时,液体陶瓷前体渗透到氮化硼团聚体的空隙中,然后被烧结成陶瓷,因此易于填充空隙。根据本发明的一个示例性实施方案的环氧树脂组合物还可包含选自氧化铝、氮化铝、氧化镁和氮化硼中的至少一种。这里,根据本发明的一个示例性实施方案的环氧树脂组合物可包含3体积%至40体积%,优选3体积%至20体积%的环氧化合物,0.5体积%至10体积%,优选0.5体积%至5体积%的固化剂以及50体积%至95体积%,优选75体积%至95体积%的包含其中面状无机颗粒发生团聚的团聚体的无机填料,并且在团聚体中的空隙中形成有包含选自c、n和o中至少两种元素的陶瓷。当以上述比例包含环氧化合物、固化剂和无机填料时,环氧树脂组合物可具有良好的热导率、室温稳定性和分散性。特别地,当包含大于95体积%的无机填料时,环氧化合物的含量可能相对降低,并且在无机填料和环氧化合物之间可形成微小的空隙,因此反而降低了热导率。此外,当包含小于50体积%的无机填料时,热导率也可能降低。这里,相对于10体积份的环氧化合物,可包含10体积份至60体积份,优选15体积份至55体积份,更优选45体积份至55体积份的其中面状无机颗粒发生团聚的团聚体。当环氧化合物和团聚体满足上述比例时,环氧树脂组合物可具有高的热导率和剥离强度。特别地,当相对于10体积份的环氧化合物,包含小于10体积份的团聚体时,热导率可能降低。此外,当相对于10体积份的环氧化合物包含大于60体积份的团聚体时,环氧树脂组合物的脆性可能增加,因此剥离强度可能降低。这里,环氧化合物可包括结晶环氧化合物、非晶环氧化合物和硅环氧化合物中的至少一种。结晶环氧化合物可包括介晶结构。介晶是液晶的基本单元且包含刚性结构。此外,非晶环氧化合物可以是分子中具有至少两个环氧基团的常规非晶环氧化合物,例如衍生自双酚a或双酚f的缩水甘油醚化合物。相对于10体积份的结晶环氧化合物,可包含3体积份至40体积份的非晶环氧化合物。当以上述比例包含结晶环氧化合物和非晶环氧化合物时,可提高室温稳定性。此外,相对于10体积份的结晶性环氧化合物,可包含3体积份至40体积份的硅环氧化合物。当以上述比例包含结晶环氧化合物和硅环氧化合物时,可提高热导率和耐热性。此外,根据本发明的一个示例性实施方案包含在环氧树脂组合物中的固化剂可包括基于胺的固化剂、基于酚的固化剂、基于酸酐的固化剂、基于多硫醇的固化剂、基于聚氨基酰胺的固化剂、基于异氰酸酯的固化剂和基于嵌段异氰酸酯的固化剂中的至少一种以及其至少两种的混合物。在下文中,将参考实施例和比较例进一步详细地描述本发明。<实施例iii-1>将3.75体积%的结晶环氧化合物(即,4,4’-双酚醚二缩水甘油醚)、1.875体积%的式2的非晶环氧化合物和1.875体积%的式3的硅环氧化合物、1.25体积%的4,4’-二氨基二苯砜和1.25体积%的式4的基于酸酐的固化剂混合。[式2][式3]这里,r1至r6各自可选自:h、cl、br、f、c1~c3烷基、c1~c3烯烃、c1~c3炔烃和芳基。这里,r1至r6可以是苯基。[式4]此外,添加26体积%的氧化铝和64体积%的其中空隙填充有sicno的氮化硼(这里,其中空隙填充有sicno的氮化硼通过以下制备:将其中面状氮化硼发生团聚的氮化硼团聚体与聚硅氮烷混合,将所得混合物在180℃下处理24小时,并在700℃下进行热解2小时,平均密度为2.246g/cm3,空隙率为1%或更低),搅拌2小时。将其中完成搅拌的溶液均匀地涂覆在铜板上,并在150℃下于恒定压力下固化一个半小时。<实施例iii-2>将3.75体积%的结晶环氧化合物(即,4,4’-双酚醚二缩水甘油醚)、1.875体积%的式2的非晶环氧化合物和1.875体积%的式3的硅环氧化合物、1.25体积%的4,4’-二氨基二苯砜和1.25体积%的式4的基于酸酐的固化剂混合。此外,添加35体积%的氧化铝和55体积%的其中空隙填充有sicno的氮化硼(这里,其中空隙填充有sicno的氮化硼通过以下制备:将其中面状氮化硼发生团聚的氮化硼团聚体与聚硅氮烷混合,将所得混合物在180℃下处理24小时,并在700℃下进行热解2小时,平均密度为2.246g/cm3,空隙率为1%或更低),搅拌2小时。将其中完成搅拌的溶液均匀地涂覆在铜板上,并在150℃下于恒定压力下固化一个半小时。<实施例iii-3>将3.75体积%的结晶环氧化合物(即,4,4’-双酚醚二缩水甘油醚)、1.875体积%的式2的非晶环氧化合物和1.875体积%的式3的硅环氧化合物、1.25体积%的4,4’-二氨基二苯砜和1.25体积%的式4的基于酸酐的固化剂混合。此外,添加50体积%的氧化铝和40体积%的其中空隙填充有sicno的氮化硼(这里,其中空隙填充有sicno的氮化硼通过以下制备:将其中面状氮化硼发生团聚的氮化硼团聚体与聚硅氮烷混合,将所得混合物在180℃下处理24小时,并在700℃下进行热解2小时,平均密度为2.246g/cm3,空隙率为1%或更低),搅拌2小时。将其中完成搅拌的溶液均匀地涂覆在铜板上,并在150℃下于恒定压力下固化一个半小时。<实施例iii-4>将3.75体积%的结晶环氧化合物(即,4,4’-双酚醚二缩水甘油醚)、1.875体积%的式2的非晶环氧化合物和1.875体积%的式3的硅环氧化合物、1.25体积%的4,4’-二氨基二苯砜和1.25体积%的式4的基于酸酐的固化剂混合。此外,添加58体积%的氧化铝和32体积%的其中空隙填充有sicno的氮化硼(这里,其中空隙填充有sicno的氮化硼通过以下制备:将其中面状氮化硼发生团聚的氮化硼团聚体与聚硅氮烷混合,将所得混合物在180℃下处理24小时,并在700℃下进行热解2小时,平均密度为2.246g/cm3,空隙率为1%或更低),搅拌2小时。将其中完成搅拌的溶液均匀地涂覆在铜板上,并在150℃下于恒定压力下固化一个半小时。<实施例iii-5>将3.75体积%的结晶环氧化合物(即,4,4’-双酚醚二缩水甘油醚)、1.875体积%的式2的非晶环氧化合物和1.875体积%的式3的硅环氧化合物、1.25体积%的4,4’-二氨基二苯砜和1.25体积%的式4的基于酸酐的固化剂混合。此外,添加66体积%的氧化铝和24体积%的其中空隙填充有sicno的氮化硼(这里,其中空隙填充有sicno的氮化硼通过以下制备:将其中面状氮化硼发生团聚的氮化硼团聚体与聚硅氮烷混合,将所得混合物在180℃下处理24小时,并在700℃下进行热解2小时,平均密度为2.246g/cm3,空隙率为1%或更低),搅拌2小时。将其中完成搅拌的溶液均匀地涂覆在铜板上,并在150℃下于恒定压力下固化一个半小时。<实施例iii-6>将3.75体积%的结晶环氧化合物(即,4,4’-双酚醚二缩水甘油醚)、1.875体积%的式2的非晶环氧化合物和1.875体积%的式3的硅环氧化合物、1.25体积%的4,4’-二氨基二苯砜和1.25体积%的式4的基于酸酐的固化剂混合。此外,添加75体积%的氧化铝和16体积%的其中空隙填充有sicno的氮化硼(这里,其中空隙填充有sicno的氮化硼通过以下制备:将其中面状氮化硼发生团聚的氮化硼团聚体与聚硅氮烷混合,将所得混合物在180℃下处理24小时,并在700℃下进行热解2小时,平均密度为2.246g/cm3,空隙率为1%或更低),搅拌2小时。将其中完成搅拌的溶液均匀地涂覆在铜板上,并在150℃下于恒定压力下固化一个半小时。<实施例iii-7>将3.75体积%的结晶环氧化合物(即,4,4′-双酚醚二缩水甘油醚)、1.875体积%的式2的非晶环氧化合物和1.875体积%的式3的硅环氧化合物、1.25体积%的4,4’-二氨基二苯砜和1.25体积%的式4的基于酸酐的固化剂混合。此外,添加82体积%的氧化铝和8体积%的其中空隙填充有sicno的氮化硼(这里,其中空隙填充有sicno的氮化硼通过以下制备:将其中面状氮化硼发生团聚的氮化硼团聚体与聚硅氮烷混合,将所得混合物在180℃下处理24小时,并在700℃下进行热解2小时,平均密度为2.246g/cm3,空隙率为1%或更低),搅拌2小时。将其中完成搅拌的溶液均匀地涂覆在铜板上,并在150℃下于恒定压力下固化一个半小时。<比较例iii-1>将3.75体积%的将结晶环氧化合物(即,4,4’-双酚醚二缩水甘油醚)、1.875体积%的式2的非晶环氧化合物和1.875体积%的式3的硅环氧化合物、1.25体积%的4,4’-二氨基二苯砜和1.25体积%的式4的基于酸酐的固化剂混合。此外,添加26体积%的氧化铝、64体积%的氮化硼(这里,氮化硼是其中面状氮化硼发生团聚的氮化硼团聚体,平均密度为2.075g/cm3,空隙率为8%),搅拌2小时。将其中完成搅拌的溶液均匀地涂覆在铜板上,并在150℃下于恒定压力下固化一个半小时。<比较例iii-2>将3.75体积%的将结晶环氧化合物(即,4,4’-双酚醚二缩水甘油醚)、1.875体积%的式2的非晶环氧化合物和1.875体积%的式3的硅环氧化合物、1.25体积%的4,4’-二氨基二苯砜和1.25体积%的式4的基于酸酐的固化剂混合。此外,添加35体积%的氧化铝和55体积%的氮化硼(这里,氮化硼是其中面状氮化硼发生团聚的氮化硼团聚体,平均密度为2.075g/cm3,空隙率为8%),搅拌2小时。将其中完成搅拌的溶液均匀地涂覆在铜板上,并在150℃下于恒定压力下固化一个半小时。<比较例iii-3>将3.75体积%的结晶环氧化合物(即,4,4’-双酚醚二缩水甘油醚)、1.875体积%的式2的非晶环氧化合物和1.875体积%的式3的硅环氧化合物、1.25体积%的4,4’二氨基二苯砜和1.25体积%的式4的基于酸酐的固化剂混合。此外,添加50体积%的氧化铝为和40体积%的氮化硼(这里,氮化硼是其中面状氮化硼发生团聚的团聚体,平均密度为2.075g/cm3,空隙率为8%),搅拌2小时。将其中完成搅拌的溶液均匀地涂覆在铜板上,并在150℃下于恒定压力下固化一个半小时。<比较例iii-4>将3.75体积%的结晶环氧化合物(即,4,4’-双酚醚二缩水甘油醚)、1.875体积%的式2的非晶环氧化合物和1.875体积%的式3的硅环氧化合物、1.25体积%的4,4’-二氨基二苯砜和1.25体积%的式4的基于酸酐的固化剂混合。此外,添加58体积%的氧化铝和32体积%的氮化硼(这里,氮化硼是其中面状氮化硼发生团聚的氮化硼团聚体,平均密度为2.075g/cm3,空隙率为8%),搅拌2小时。将其中完成搅拌的溶液均匀地涂覆在铜板上,并在150℃于恒定压力下固化一个半小时。<比较例iii-5>将3.75体积%的结晶环氧化合物(即,4,4’-双酚醚二缩水甘油醚)、1.875体积%的式2的非晶环氧化合物和1.875体积%的式3的硅环氧化合物、1.25体积%的4,4’-二氨基二苯砜和1.25体积%的式4的基于酸酐的固化剂混合。此外,添加66体积%的氧化铝和24体积%的氮化硼(这里,氮化硼是其中面状氮化硼发生团聚的氮化硼团聚体,平均密度为2.075g/cm3,空隙率为8%),搅拌2小时。将其中完成搅拌的溶液均匀地涂覆在铜板上,并在150℃下于恒定压力下固化一个半小时。<比较例iii-6>将3.75体积%的结晶环氧化合物(即,4,4’-双酚醚二缩水甘油醚)、1.875体积%的式2的非晶环氧化合物和1.875体积%的式3的硅环氧化合物、1.25体积%的4,4’-二氨基二苯砜和1.25体积%的式4的基于酸酐的固化剂混合。此外,添加74体积%的氧化铝和16体积%的氮化硼(这里,氮化硼是其中面状氮化硼发生团聚的氮化硼团聚体,平均密度为2.075g/cm3,空隙率为8%),搅拌2小时。将完成搅拌的溶液均匀地涂覆在铜板上,并在150℃下于恒定压力下固化一个半小时。<比较例iii-7>将3.75体积%的结晶环氧化合物(即,4,4’-双酚醚二缩水甘油醚)、1.875体积%的式2的非晶环氧化合物和1.875体积%的式3的硅环氧化合物、1.25体积%的4,4’-二氨基二苯砜和1.25体积%的式4的基于酸酐的固化剂混合。此外,添加82体积%的氧化铝和8体积%的氮化硼(这里,氮化硼是其中面状氮化硼发生团聚的氮化硼团聚体,平均密度为2.075g/cm3,空隙率为8%),搅拌2小时。将其中完成搅拌的溶液均匀地涂覆在铜板上,并在150℃下于恒定压力下固化一个半小时。<实验例>将在实施例iii-1至实施例iii-7和比较例iii-1至比较例iii-7中得到的环氧树脂组合物固化,然后使用lfa447nanoflash(由netzsch制造)通过瞬态热线法测量热导率。为此,将环氧树脂组合物制成直径为0.5英寸的圆形,然后通过将组合物的上表面暴露于具有247电压的激光脉冲并测量在底部达到平衡的时间来计算热导率。此外,将实施例iii-1至实施例iii-7和比较例iii-1至比较例iii-7中得到的环氧树脂组合物固化,并粘附厚度为62.5mm的铜层,然后使用由ymtech制造的装置通过以50mm/分钟的速率在垂直方向(以90度的角度)提升铜层来测量剥离强度。结果示于表6中。表6[表6]参考表1,可注意到,与包含其中空隙未填充sicno的氮化硼团聚体作为无机填料的比较例iii-1的环氧树脂组合物相比,包含其中空隙填充有sicno的氮化硼团聚体作为无机填料的实施例iii-1的环氧树脂组合物具有更高的热导率和更高的剥离强度。同样,可注意到,与包含相同含量的其中空隙未填充sicno的氮化硼团聚体作为无机填料的比较例iii-2至iii-7的环氧树脂组合物相比,包含其中空隙填充有sicno的氮化硼团聚体作为无机填料的实施例iii-2至iii-7的环氧树脂组合物具有更高的热导率和更高的剥离强度。特别地,可注意到,相对于10体积份的环氧化合物,包含其中空隙填充有10体积份至60体积份的sicno的氮化硼团聚体的实施例iii-3至实施例iii-7与相同含量的比较例iii-3至比较例iii-7相比,热导率提高8%或更高。此外,可注意到,根据其中相对于10体积份的环氧化合物,包含其中空隙填充有45至55体积份的sicno的氮化硼团聚体的实施例iii-3,可获得热导率为21w/mk或更大,剥离强度为0.6kgf/cm或更大的环氧树脂组合物。iv.其中在涂层的表面上形成有羟基的无机填料同时,根据本发明的一个示例性实施方案的包含在环氧树脂组合物中的无机填料可包含形成在其表面上的涂层,涂层可包含含有选自c、n和o中至少两种元素的陶瓷,并且在涂层的表面上可形成有羟基(-oh)。同样地,当无机填料的表面涂覆有包含选自c、n和o中至少两种元素的陶瓷时,可提高分散性、绝缘性和热导率。特别地,当在涂层的表面上形成有羟基(-oh)时,可增加环氧树脂和无机填料之间的粘合强度,从而增加分散性、热导率和剥离强度。这里,无机填料可包含碳化硅(sic)、氮化硼(bn)、石墨、氧化铝(al2o3)和氮化铝(aln)中的至少一种。这里,无机填料可包含其中面状氮化硼或面状石墨发生团聚的团聚体,并且在团聚体的空隙中可形成有包含选自c、n和o中至少两种元素的陶瓷。同时,包含选自c、n和o中至少两种元素的陶瓷可由如上所述的式1的聚硅氮烷(psz)形成。此外,陶瓷可包含含有烷氧基团(-or)的氧化铝、含有烷氧基团的氧化硅和含有烷氧基团的氧化钛中的至少一种。这里,如上所述,氧化铝可通过铝醇盐(al醇盐)的水解和脱水缩合形成,氧化硅可通过硅醇盐的水解和脱水缩合形成,以及氧化钛可通过钛醇盐的水解和脱水缩合形成。图13至图14例示了根据本发明的一个实施例处理无机填料的表面的方法。为了便于说明,将假设无机填料是面状氮化硼的团聚体且陶瓷是sicno来对本发明进行描述,但是本发明不限于此。图13和图14的s1100至s1120与图9和图10的那些相同。因此,重复描述将被省略。参照图13和图14,将在s1120中烧结的氮化硼团聚体1230在naoh溶液中热解20至40小时(s1130)。因此,可获得其中在表面上形成有羟基的氮化硼团聚体1240。也就是说,在氮化硼团聚体1230(类似图14的氮化硼团聚体1230)的表面上形成有sicno。sicno是非晶陶瓷并以-si-o-si-的结构结合。这里,当在naoh溶液中处理氮化硼团聚体时,oh-破坏si和o之间的键并与si反应,由此形成si-oh的键。根据这种方法,在涂覆有sicno的氮化硼聚团聚体的表面上可形成有羟基。这里,在根据本发明的一个示例性实施方案的环氧树脂组合物中,可以以10∶10至50,优选10∶25至50,且更优选10∶40至50的体积比包含环氧化合物和无机填料。当相对于10体积份的环氧化合物,包含小于10体积份的无机填料时,热导率可能降低。此外,当相对于10体积份的环氧化合物,包含大于50体积份的无机填料时,环氧树脂组合物的脆性可能增加,因此剥离强度可能降低。这里,环氧化合物可包括结晶环氧化合物、非晶环氧化合物和硅环氧化合物中的至少一种。结晶环氧化合物可包括介晶结构。介晶是液晶的基本单元且包含刚性结构。此外,非晶环氧化合物可以是在分子中具有至少两个环氧基团的常规非晶环氧化合物,并且可以是例如衍生自双酚a或双酚f的缩水甘油醚化合物。相对于10体积份的结晶性环氧化合物,可包含3体积份至40体积份的非晶环氧化合物。当以上述比例包含结晶环氧化合物和非晶环氧化合物时,可提高室温稳定性。此外,相对于10体积份的结晶性环氧化合物,可包含3体积份至40体积份的硅环氧化合物。当以上述比例包含结晶环氧化合物和硅环氧化合物时,可提高热导率和耐热性。此外,根据本发明的一个示例性实施方案的环氧树脂组合物还可包含固化剂。相对于环氧树脂组合物的总体积可包含0.5体积%至5体积%的固化剂。根据本发明的一个示例性实施方案的环氧树脂组合物中包含的固化剂可包括基于胺的固化剂、基于酚的固化剂、基于酸酐的固化剂、基于多硫醇的固化剂、基于聚氨基酰胺的固化剂、基于异氰酸酯的固化剂和基于嵌段异氰酸酯的固化剂中的至少一种以及其至少两种的混合物。根据本发明的一个示例性实施方案的环氧树脂组合物可应用于印刷电路板。图15是根据本发明的示例性实施方案的印刷电路板的截面图。参考图15,印刷电路板100包含基底110、绝缘层120和电路图案130。基底110可由铜、铝、镍、金、铂及其合金组成。由根据本发明的示例性实施方案的环氧树脂组合物构成的绝缘层120形成在基底110上。电路图案130形成在绝缘层120上。电路图案130可由金属(例如铜或镍)构成。绝缘层120使金属板110与电路图案130之间绝缘。根据本发明的示例性实施方案的包含无机填料的环氧树脂组合物还可应用于发光元件模块。图16是根据本发明的一个示例性实施方案的发光元件模块的截面图。参考图16,发光元件模块400包含基底410、形成在基底410上的绝缘层420、形成在绝缘层420上的电路图案430和形成在绝缘层420上的发光元件440。基底410可由铜、铝、镍、金、铂及其合金组成。绝缘层420可包含根据本发明的一个示例性实施方案的包含无机填料的环氧树脂组合物。尽管在图16中未示出,但是为了提高绝缘层420和电路图案430之间的粘合强度,可在绝缘层420和电路图案430之间形成籽晶层。下文中,将参照示实施例和比较例更详细地描述本发明。首先,使用相同含量比但具有不同类型的无机填料的环氧化合物和无机填料制备环氧树脂组合物。<实施例iv-1>将8.75体积%的结晶环氧化合物(即,4,4’-双酚醚二缩水甘油醚)、4.375体积%的式2的非晶环氧化合物和4.375体积%的式3的硅环氧化合物、1.25体积%的4,4’-二氨基二苯砜和1.25体积%的式4的基于酸酐的固化剂混合。[式2][式3]这里,r1至r6各自可选自h、cl、br、f、c1~c3烷基、c1~c3烯烃、c1~c3炔烃和芳基。这里,r1至r6可以是苯基。[式4]此外,将包含sicno的涂层涂覆在sic的表面上至厚度为100nm,添加80体积%的在naoh中处理了36小时的无机填料并搅拌2小时。将其中完成搅拌的溶液均匀地涂覆在铜板上,并在150℃下于恒定压力下固化一个半小时。<实施例iv-2>将8.75体积%的结晶环氧化合物(即,4,4′-双酚醚二缩水甘油醚)、4.375体积%的式2的非晶环氧化合物和4.375体积%的式3的硅环氧化合物、1.25体积%的4,4’-二氨基二苯砜和1.25体积%的式4的基于酸酐的固化剂混合。此外,将包含sicno的涂层涂覆在bn(其中面状bn发生团聚的团聚体,平均密度为2.246g/cm3,空隙率为8%或更低)的表面上至厚度为100nm,添加80体积%在naoh中处理了36小时的无机填料并搅拌2小时。将其中完成搅拌的溶液均匀地涂覆在铜板上,并在150℃下于恒定压力下固化一个半小时。<实施例iv-3>将8.75体积%的结晶环氧化合物(即,4,4’-双酚醚二缩水甘油醚)、4.375体积%的式2的非晶环氧化合物和4.375体积%的式3的硅环氧化合物、1.25体积%的4,4’-二氨基二苯砜和1.25体积%的式4的基于酸酐的固化剂混合。此外,将包含sicno的涂层涂覆在al2o3的表面上至厚度为100nm,添加80体积%的在naoh中处理了36小时的无机填料并搅拌2小时。将其中完成搅拌的溶液均匀地涂覆在铜板上,并在150℃下在恒定压力下固化一个半小时。<实施例iv-4>将8.75体积%的结晶环氧化合物(即,4,4’-双酚醚二缩水甘油醚)、4.375体积%的式2的非晶环氧化合物和4.375体积%的式3的硅环氧化合物、1.25体积%的4,4′-二氨基二苯砜和1.25体积%的式4的基于酸酐的固化剂混合。此外,将包含sicno的涂层涂覆在aln的表面上至厚度为100nm,添加80体积%的在naoh中处理了36小时的无机填料并搅拌2小时。将其中完成搅拌的溶液均匀地涂覆在铜板上,并在150℃下在恒定压力下固化一个半小时。<比较例iv-1>将8.75体积%的结晶环氧化合物(即,4,4’-双酚醚二缩水甘油醚)、4.375体积%的式2的非晶环氧化合物和4.375体积%的式3的硅环氧化合物、1.25体积%的4,4’-二氨基二苯砜和1.25体积%的式4的基于酸酐的固化剂混合。此外,添加80体积%的通过将包含sicno的涂层涂覆在sic的表面至厚度为100nm而形成的无机填料并搅拌2小时。将其中完成搅拌的溶液均匀地涂覆在铜板上,并在150℃下在恒定压力下固化一个半小时。<比较例iv-2>将8.75体积%的结晶环氧化合物(即,4,4’-双酚醚二缩水甘油醚)、4.375体积%的式2的非晶环氧化合物和4.375体积%的式3的硅环氧化合物、1.25体积%的4,4’-二氨基二苯砜和1.25体积%的式4的基于酸酐的固化剂混合。此外,添加80体积%的通过将包含sicno的涂层涂覆在bn(其中面状bn发生团聚的团聚体,平均密度为2.246g/cm3,空隙率为8%或更低)的表面至厚度为100nm而形成的无机填料,并搅拌2小时。将其中完成搅拌的溶液均匀地涂覆在铜板上,并在150℃下在恒定压力下固化一个半小时。<比较例iv-3>将8.75体积%的结晶环氧化合物(即,4,4’双酚醚二缩水甘油醚)、4.375体积%的式2的非晶环氧化合物和4.375体积%的式3的硅环氧化合物、1.25体积%的4,4’-二氨基二苯砜和1.25体积%的式4的基于酸酐的固化剂混合。此外,添加80体积%的通过将包含sicno的涂层涂覆在al2o3的表面至厚度为100nm而形成的无机填料,并搅拌2小时。将其中完成搅拌的溶液均匀地涂覆在铜板上,并在150℃下在恒定压力下固化一个半小时。<比较例iv-4>将8.75体积%的结晶环氧化合物(即,4,4’-双酚醚二缩水甘油醚)、4.375体积%的式2的非晶环氧化合物和4.375体积%的式3的硅环氧化合物、1.25体积%的4,4’-二氨基二苯砜和1.25体积%的式4的基于酸酐的固化剂混合。此外,添加80体积%的通过将包含sicno的涂层涂覆在aln的表面至厚度为100nm而形成的无机填料,并搅拌2小时。将其中完成搅拌的溶液均匀地涂覆在铜板上,并在150℃下在恒定压力下固化一个半小时。然后,使用与实施例iv-2中所用的相同类型的无机填料和不同含量比的环氧化合物和无机填料来制备环氧树脂组合物。<实施例iv-5>将18.75体积%的结晶环氧化合物(即,4,4’-双酚醚二缩水甘油醚)、9.375体积%的式2的非晶环氧化合物和9.375体积%的式3的硅环氧化合物、1.25体积%的4,4’-二氨基二苯砜和1.25体积%的式4的基于酸酐的固化剂混合。此外,将包含sicno的涂层涂覆在bn(其中面状bn发生团聚的团聚体,平均密度为2.246g/cm3,空隙率为8%或更低)的表面上至厚度为100nm,添加60体积%在naoh中处理了36小时的无机填料并搅拌2小时。将其中完成搅拌的溶液均匀地涂覆在铜板上,并在150℃下在恒定压力下固化一个半小时。<实施例iv-6>将13.75体积%的结晶环氧化合物(即,4,4′-双酚醚二缩水甘油醚)、6.875体积%的式2的非晶环氧化合物和6.875体积%的式3的硅环氧化合物、1.25体积%的4,4’-二氨基二苯砜和1.25体积%的式4的基于酸酐的固化剂混合。此外,将包含sicno的涂层涂覆在bn(其中面状bn发生团聚的团聚体,平均密度为2.246g/em3,空隙率为8%或更低)的表面上至厚度为100nm,添加70体积%在naoh中处理了36小时的无机填料并搅拌2小时。将其中完成搅拌的溶液均匀地涂覆在铜板上,并在150℃下在恒定压力下固化一个半小时。<实施例iv-7>将11.25体积%的结晶环氧化合物(即,4,4’-双酚醚二缩水甘油醚)、5.625体积%的式2的非晶环氧化合物和5.625体积%的式3的硅环氧化合物、1.25体积%的4,4’-二氨基二苯砜和1.25体积%的式4的基于酸酐的固化剂混合。此外,将包含sicno的涂层涂覆在bn(其中面状bn发生团聚的团聚体,平均密度为2.246g/cm3,空隙率为8%或更低)的表面上至厚度为100nm,添加75体积%在naoh中处理了36小时的无机填料并搅拌2小时。将其中完成搅拌的溶液均匀地涂覆在铜板上,并在150℃下在恒定压力下固化一个半小时。<比较例iv-5>将38.75体积%的结晶环氧化合物(即,4,4’-双酚醚二缩水甘油醚)、19.375体积%的式2的非晶环氧化合物和19.375体积%的式3的硅环氧化合物、1.25体积%的4,4’-二氨基二苯砜和1.25体积%的式4的基于酸酐的固化剂混合。此外,将包含sicno的涂层涂覆在bn(其中面状bn发生团聚的团聚体,平均密度为2.246g/cm3,空隙率为8%或更低)的表面上至厚度为100nm,添加20体积%在naoh中处理了36小时的无机填料并搅拌2小时。将其中完成搅拌的溶液均匀地涂覆在铜板上,并在150℃下在恒定压力下固化一个半小时。<比较例iv-6>将33.75体积%的结晶环氧化合物(即,4,4’-双酚醚二缩水甘油醚)、16.875体积%的式2的非晶环氧化合物和16.875体积%的式3的硅环氧化合物、1.25体积%的4,4’-二氨基二苯砜和1.25体积%的式4的基于酸酐的固化剂混合。此外,将包含sicno的涂层涂覆在bn(其中面状bn发生团聚的团聚体,平均密度为2.246g/cm3,空隙率为8%或更低)的表面上至厚度为100nm,添加30体积%在naoh中处理了36小时的无机填料并搅拌2小时。将其中完成搅拌的溶液均匀地涂覆在铜板上,并在150℃下在恒定压力下固化一个半小时。<比较例iv-7>将28.75体积%的结晶环氧化合物(即,4,4’-双酚醚二缩水甘油醚)、14.375体积%的式2的非晶环氧化合物和14.375体积%的式3的硅环氧化合物、1.25体积%的4,4’-二氨基二苯砜和1.25体积%的式4的基于酸酐的固化剂混合。此外,将包含sicno的涂层涂覆在bn(其中面状bn发生团聚的团聚体,平均密度为2.246g/cm3,空隙率为8%或更低)的表面上至厚度为100nm,添加40体积%在naoh中处理了36小时的无机填料并搅拌2小时。将其中完成搅拌的溶液均匀地涂覆在铜板上,并在150℃下在恒定压力下固化一个半小时。<比较例iv-8>将3.75体积%的结晶环氧化合物(即,4,4’-双酚醚二缩水甘油醚)、1.875体积%的式2的非晶环氧化合物和1.875体积%的式3的硅环氧化合物、1.25体积%的4,4’二氨基二苯砜和1.25体积%的式4的基于酸酐的固化剂混合。此外,将包含sicno的涂层涂覆在bn(其中面状bn发生团聚的团聚体,平均密度为2.246g/cm3,空隙率为8%或更低)的表面上至厚度为100nm,添加90体积%在naoh中处理了36小时的无机填料并搅拌2小时。将其中完成搅拌的溶液均匀地涂覆在铜板上,并在150℃下在恒定压力下固化一个半小时。<比较例iv-9>将6.25体积%的结晶环氧化合物(即,4,4’-双酚醚二缩水甘油醚)、3.125体积%的式2的非晶环氧化合物和3.125体积%的式3的硅环氧化合物、1.25体积%的4,4’-二氨基二苯砜和1.25体积%的式4的基于酸酐的固化剂混合。此外,将包含sicno的涂层涂覆在bn(其中面状bn发生团聚的团聚体,平均密度为2.246g/cm3,空隙率为8%或更低)的表面上至厚度为100nm,添加85体积%在naoh中处理了36小时的无机填料并搅拌2小时。将其中完成搅拌的溶液均匀地涂覆在铜板上,并在150℃下在恒定压力下固化一个半小时。<实验例>将实施例iv-1至实施例iv-7和比较例iv-1至比较例iv-9中得到的环氧树脂组合物固化并制成直径为0.5英寸的圆形,然后通过将组合物的上表面暴露于具有247电压的激光脉冲并测量在底部达到平衡的时间来计算热导率。此外,将实施例iv-1至实施例iv-5和比较例iv-1至比较例iv-8中得到的环氧树脂组合物固化,并粘附厚度为62.5mm的铜层,通过以50mm/分钟的速率在垂直方向(以90度的角度)提升铜层测量剥离强度。结果示于表7至11中。表7[表7]测试号热导率(w/mk)剥离强度(kgf/cm2)实施例iv-114.561.69比较例iv-113.631.42表8[表8]表9[表9]表10[表10]表11[表11]参考表7,可注意到,与包含与实施例iv-1相同含量的其中表面涂覆有sicno而未在naho溶液中进行处理的无机填料的比较例iv-1相比,包含其中表面涂覆有sicno且在naoh溶液中处理以添加羟基的无机填料的实施例iv-1表现出更高的热导率和剥离强度。同样,参考表8至10,可注意到,与包含分别与实施例iv-2至实施例iv-4相同含量的其中表面涂覆有sicno且在naho溶液中进行处理的比较例iv-2至比较例iv-4相比,包含其中表面涂覆有sicno且在naoh溶液中处理以添加羟基的无机填料的实施例iv-2至实施例iv-4表现出更高的热导率和剥离强度。同时,参考表11,如实施例iv-2和实施例iv-5至实施例iv-7中所述,可注意到,当以10∶10至10∶50的体积比包含根据本发明的一个示例性实施方案的环氧化合物和无机填料时,可获得具有高热导率和剥离强度的环氧树脂组合物。也就是说,如比较例iv-5至比较例iv-7中所述,可注意到,当相对于10体积份的环氧化合物包含小于10体积份的无机填料时,剥离强度高但热导率相当低。此外,如比较例iv-8至比较例iv-9所述,可注意到,当相对于10体积份的环氧化合物包含大于50体积份的无机填料时,热导率优异,但由于脆性,剥离强度非常低。特别地,如实施例iv-2中所述,可注意到,当以10∶40至50的体积比包含根据本发明的一个示例性实施方案的环氧化合物和无机填料时,可获得具有1kgf/cm或更高的剥离强度和17w/mk或更高的热导率的环氧树脂组合物。对于本领域技术人员明显的是,在不脱离本发明的精神或范围的情况下,可以对本发明的上述示例性实施方案进行多种修改。因此,只要这样的修改落入所附权利要求及其等同物的范围内,则本发明旨在覆盖所有这样的修改。当前第1页1 2 3