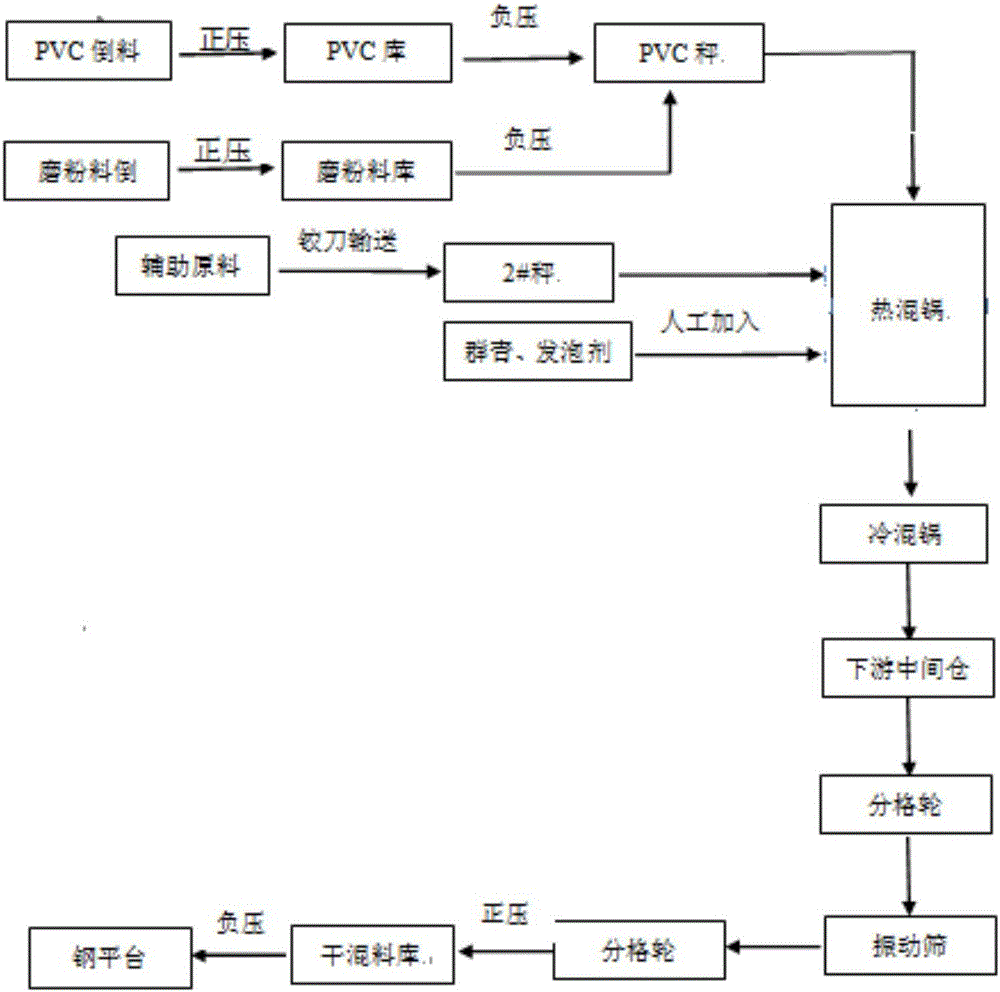
本发明属于建材领域,具体涉及一种采用钙锌稳定剂的树脂发泡转印门及其制备工艺。
背景技术:
:随着市场客户需求不断变化,人们对绿色环保、无甲醛等有害物质的装修材料日加青睐,在这轮装饰材料革命中,树脂发泡门以其环保、可循环利用、转印膜贴覆无甲醛等优势,及其其优良的隔音、隔热、防潮、可加工性能和装饰效果引领新一代的室内门潮流。优质的中空结皮PVC发泡门板及其木纹转印工艺赋予树脂发泡门绿色环保生态特性,并以优良的物理性能和多样化的产品设计,适合各类建筑风格,越来越深受市场欢迎,成为广大消费者的无毒环保室内门的首选。PVC发泡门板具有优良的加工性能,可进行钻、锯、钉、刨、粘等加工、可适用于热成型,加热弯曲及折叠加工、可根据一般塑料焊接程序焊接,也可与其他PVC材料粘接,与木板、胶合板相比有较强的优越性,产品使用寿命达到50年以上。现阶段在传统树脂发泡产品生产中,大多采用铅盐配方体系,而铅盐配方体系中含有一定量的铅等重金属,长时间使用有可能会析出,现阶段欧美等国大多环保稳定剂产品,长期以来由于知识产权与产供销的原因,在PVC树脂行业形成了欧洲主流配方先为铅系后为钙锌系,北美主流配方为有机锡系配方。有机锡系配方塑化能力、制品表面光泽、物理机械性能、稳定性、耐候性均优于铅系配方体系制品,但锡仍属重金属,环保性受质疑,且加工过程味道大,配方成本高;铅系配方含有毒重金属,易硫化污染,环保性能差,力学性能离散性大。钙锌系配方是欧洲国家近年来及未来发展的主流配方,随着技术的不断进步,现已趋于成熟,并成为绿色环保稳定剂的标准。但是目前,钙锌稳定剂生产中容易出现的析出、锌烧、转印时二次发泡等问题,同时发泡倍率和产品性能方面均满足不能满足相关检测要求。技术实现要素:本发明的目的在于提供一种采用钙锌稳定剂的树脂发泡转印门,无甲醛、不含有毒化学物质,绿色环保,解决了钙锌稳定剂生产中容易出现的析出、锌烧、转印时二次发泡等问题,同时发泡倍率和产品性能方面均满足相关检测要求。本发明还提供了一种采用钙锌稳定剂的树脂发泡转印门的制备工艺,配合配方中的原料特性,开发制造工艺和设计优化工艺参数,操作简单,稳定高效。本发明提供的一种采用钙锌稳定剂的树脂发泡转印门,含有以下重量份原料:所述PVC牌号为SG-7;本发明提供的一种采用钙锌稳定剂的树脂发泡转印门的制备工艺,包括以下步骤:1)、混料热混:按配方称取各组分,在300rpm转速下按照PVC--轻质碳酸钙--复合包--K718--AC发泡剂--NaHCO3的顺序下入热混锅后,然后转速控制在680-720rpm下高速搅拌,使原料温度在200秒以内提升至110℃以上,实现干混料的预塑化;所述复合包由配方量的PE蜡、双季戊四醇酯ST220/或F210、亚磷酸酯、乙酰丙酮锌、水滑石、沸石、K123、K385、内滑剂G60、ZnO、硬脂酸钙、硬脂酸锌、β-二酮锌和AC316A组成;2)混料冷混:经热混预塑化后,通过冷混的50rpm低速搅拌,将料温在350-400秒降至50℃以下,防止物料积热降解,同时消除高速搅拌产生的静电;3)挤出:物料塑化后挤压成型,然后冷却定型;4)下料,对门板按照客户需求尺寸进行切割;5)转印:通过温控加热转印设备,将转印膜贴覆在树脂发泡门基材上;门板转印工艺参数控制:收膜张力0.2±0.05N、牵引速度3-5m/min、面轮1温度(板材大面烫印轮)185±5℃、面轮2温度185±5℃、侧烫1温度170±5℃、侧烫2温度170±5℃和侧烫3温度130±5℃。进一步的,步骤1)中优选的,使原料温度提升至115-118℃;此温度下干混料预凝胶化程度最高;进一步的,步骤1)中物料在热混机中混合时间300-420秒,得到质量均匀、干流性好的干混料;步骤1)中优选的,混料量占800L热混锅锅体容积的65%-68%,混合料的预凝胶化效果最好,板材生产稳定。步骤1)中优选的,热混导流片侧边应距离锅壁3-5cm宽,此时物料在锅内翻腾效果最佳。步骤2)中优选的,冷混时间应该在330-420秒,同时下料温度应设置在45℃;进一步的,因钙锌生态门配方中含碳酸氢钠发泡剂,容易吸水分解,因此钙锌生态门配方储存时间不宜超过72小时,如长时间停机应提前将剩余干混料用完,否则易出现发泡倍率受影响,挤出负荷波动大等问题。步骤3)包括:第一阶段:塑化、即通过机筒温度与螺杆的作用,物料由颗粒状转变为具有一定流动性的均匀连续熔体的过程;第二阶段:成型、具有流动性的均匀熔体,利用螺杆的旋转挤压通过多孔板进入机头,并按口模和芯模成型为具有一定形状的型坯;第三阶段:冷却定型:即型坯在挤出压力和牵引作用下,经过真空冷却定型模后,形成具有一定强度、刚度和尺寸精度的制品。步骤3)中具体工艺参数为:螺杆转速16±2rpm、进料速度50±5rpm、牵引速度0.6±0.2m/min、挤出负荷40~70%、螺杆温度145±10℃、筒区1温度150±10℃、筒区2温度150±10℃、筒区3温度150±10℃、筒区4温度150±10℃、筒区5温度170±10℃、筒区6温度170±10℃、连接体1温度170±10℃、连接体2温度170±10℃、模具温度(1-11):190±10℃、模具温度(12-13):170±10℃、熔体温度180±10℃、芯模油温180±10℃、口模油温180±10℃、芯模水温60~80℃、口模水温30~50℃、冷却水温14~18℃、真空排湿负压-0.03~-0.07Mpa和干定型负压0~-0.06Mpa。步骤4)下料:由于发泡门下料尺寸精确度要求高,采用相对精确的横切锯按照客户要求进行切割小料;步骤5)中还包括门框材料转印工艺,具体参数控制:收膜张力0.2±0.05N、牵引速度3-7m/min、烫头1温度140±5℃、烫头2温度170±5℃和烫头3温度160±5℃。还包括步骤6)包装发运,按照《生态门包装管理规定》采用珍珠棉+纸盒的方式进行包装,并用胶带扎紧,按照装车规范进行订单运输。本发明中将钙锌稳定剂配方体系应用在树脂发泡产品中,采用的是中空低发泡结皮生产技术,对稳定剂热稳定体系、润滑体系要求高,在对所有钙锌原料作用机理充分研究和掌握的基础上,重新设计配方体系架构。在热稳定体系设计中,采用β-二酮锌和ST-220/F210作为核心稳定剂,辅以亚磷酸酯和乙酰丙酮锌进行稳定调节,使用硬脂酸钙和硬脂酸锌改善配方塑化性能,相关产品配方用量经过精确理论测算和实践验证,重点解决转印后二次发泡、模具锌烧问题满足产品相关材料性能满足要求。在润滑体系设计中,采用G60內滑剂和PE蜡外滑剂作为核心润滑剂,辅以氧化聚乙烯蜡进行内外滑协同,该体系必须契合树脂发泡门长期生产稳定性,在保证脱模性的情况下,减少析出,提高产品稳定性和生产周期。在发泡过程中通过配方中硬脂酸钙和硬脂酸锌调节塑化效果,使在不影响发泡量的情况下提高熔体强度,避免出现发泡门表面凹坑、通过调整AC发泡剂量和小苏打含量,调节产品米比重和发泡倍率,确保产品满足使用要求。在制备工艺中,由于钙锌配方体系和传统的铅盐体系在工艺控制方面的差异,整改生产工艺从混料-挤出-后期转印膜转印均有特定的工艺与其匹配,通过技术研发团队的摸索攻关,通过对配方各组分在各工序作业机理和温度等工艺控制要点分析,制定了一套适合该产品的工艺控制路线。在混料工艺方面根据配方中不同原料的性状、物理特性、预塑化要求等,调整热混混料时间等关键参数,提高预塑化效果。热混过程中物料形态发生的变化:(1)压实通常PVC树脂的表观密度仅为0.45~0.55g/ml。在高速混合机中由于相互摩擦产生的摩擦热,使物料温度不断上升,PVC颗粒和其它组分不断相互渗透,PVC粒子表面逐渐吸收稳定剂等各种助剂及已熔融的润滑剂等,使混合料的表观密度可增高至0.58~0.65g/ml。(2)均化在高速混合机中,各组分不仅能达到良好的机械混合,还可得到各组分间良好的稳定分散。随着温度不断升高,PVC粒子可不断吸收稳定剂、润滑剂等,逐渐被各组分所包覆,温度升至110~118℃时,可形成均匀、稳定的干混粉料。(3)排湿:当物料温度升至100℃左右时,包含在树脂及助剂组分中的湿气和其它易挥发物质很容易除去,避免了在挤出型材过程中产生气泡和缺陷。(4)预凝胶化:PVC的凝胶化是指在加工过程中树脂逐步熔融塑化,而后再结晶形成网络形态结构的过程,在高速热混合过程中,可见到PVC树脂既有颗粒细化、粒径均匀的形态变化,又表现出密度增大、部分凝胶化的特点。因此PVC物料高速热混合过程,也是PVC树脂均匀化、致密化及部分凝胶化的过程,物料凝胶化虽不是混料主要目的,但在混合过程中,已有部分PVC粒子出现凝胶化。有较大表面积的小粒子,易受到较大的摩擦,达到凝胶化状态,呈现出类似透明状,而在较高温度下小颗粒逐渐熔融,聚集在一起,变成较大的颗粒,表面凝胶化的PVC可以很好的吸收各种助剂,最终得到我们常见的均一性和干流性较好的干混料。(5)混合温度对混合料性能的影响:物料的混合温度是影响干混料性能最重要的因素之一,混料温度低于80℃时,物料的密实主要靠机械力密实,使各组分包围在PVC粒子周围。当温度至高于PVC树脂玻璃化温度Tg(约80℃)时,PVC颗粒开始软化,吸收其它组分,逐渐密实,温度升至110~120℃时,PVC粒子中较小的颗粒逐渐凝胶,我们通过原料性质设计研究,确定温度在115-118℃时,钙锌生态转印门配方混料效果最佳,干混料预凝胶化程度最高。(6)混合时间影响:物料在混合过程中经历的压实、均化、部分凝胶化过程,均需要一定时间完成。混料时间的延长有助于稳定剂及其他添加剂更加均匀地扩散到树脂中,以进一步提高物料稳定性和均匀程度。根据经验,物料在高速混合机中混合时间至少在300~420秒之间,才能得到质量均匀、干流性好的干混料。(7)高速混合机中加料量的影响:高速混合机中选择的加料量,应能在保证混合物料质量的前提下,有利于生产效率的提高。每批物料投料量过小,如物料体积仅为高速混合机的50%以下,物料翻腾较差,产生的摩擦热低,温升慢,耗时长,达到预设混合温度约要15min以上,同时也影响物料混合均匀。相反,投料量过大,电机负荷太高,主轴转速下降,同样影响物料的翻腾状况及混料质量,升温速度也不再明显提高。通常加料量在混合机容积60%~80%时,混合效果较好。本申请中混料量占锅体容积的65%-68%,钙锌配方混合料的预凝胶化效果最好,板材生产稳定。(8)热混导流片呈半椭圆弧面,因此导流片在混料锅中角度将直接影响物料在锅中翻腾效果,从而影响物料均化和预凝胶化效果,经过设计研究,本身器过中导流片侧边应距离锅壁1-23-5cm宽为宜,此时物料在锅内翻腾效果最佳。在挤出工艺方面通过降低前三筒区温度(温度控制在150±10℃),控制出料速度(0.6±0.2m/min)找出合理的产能区间等方式,防止出现锌烧等问题,并一定程度上降低了析出物的产生,提高了生产稳定性。本发明中挤出控制技术主要体现在温度控制上,一方面要在前期抑制过早发泡,同时筒区温度要与钙锌配方特点相匹配,同时通过研究对比,钙锌生态门挤出发泡工艺采用温度正向设置比采用温度抛物线设置和温度逆向设置出料均匀度,表面结皮效果更为理想。在转印工序方面尤其关注转印温度,在充分研究二次发泡引起的尺寸变化的情况下,设置合理的转印温度控制区间,对转印速度(板材控制在3-5m/min)、压辊压力标尺(控制在39.2mm),预热温度(185±5℃)等环节进行严格控制。与现有技术相比,本发明提供的采用钙锌稳定剂的树脂发泡转印门,钙锌基材与转印工艺都满足环保材料要求,基材不含重金属,转印材料不含甲醛;防腐、防潮、防虫蛀、不变形,由于所用主原料聚氯乙烯自身性能,受酸碱的影响较小;吸水率仅为0.5%;有效防止虫蛀。非常适用于南方潮湿的环境。加工安装便捷、板材内部采用中空结构和芯层发泡技术,使发泡产品的密度接近木材。类似木质的加工要求,比木质门的安装更加快捷,不需钉钉子、抹腻子、刷油漆等传统作业方式,工厂标准化生产,数控机床铣制合页、锁孔、装饰窗孔,尺寸标准精确,确保现场安装时整体严密。采用分件积木式结构,便于运输,现场安装方便,避免了在现场繁杂的手工加工制作过程,走工厂化流水线作业的道路,提高了门的制作安装效率。加工手段多样化,无需专业人员,所用加工工具通用性强。附图说明图1为树脂发泡转印门的制备工艺流程示意图;图2为混料的制备工艺示意图。具体实施方式本发明中原料品牌如下:PVC(SG-7):齐鲁石化SG-7;轻钙:江西大宇;硬脂酸钙和硬脂酸锌:南京金陵;ST220:味之素;;亚磷酸酯:无锡巨旺;水滑石和沸石:山东中铝;AC316A:霍尼韦尔;AC发泡剂:上海光裕;K385、K718:威海亿铭达;PE蜡:邦尼BN208。实施例1一种采用钙锌稳定剂的树脂发泡转印门,含有以下重量份原料:所述PVC牌号为SG-7。一种采用钙锌稳定剂的树脂发泡转印门的制备工艺,包括以下步骤:1)原料配料采用自动化称量设备对各组分原料进行精确称量,称量精度为0.01KG,称量完毕后通过程序控制以份为单位进入热混锅。2)混料热混混料热混:按配方称取各组分,在300rpm转速下按照PVC--轻质碳酸钙--复合包--K718--AC发泡剂--NaHCO3的顺序下入热混锅后,然后转速控制在680-720rpm下高速搅拌,使原料温度在200秒以内提升至110℃以上,实现干混料的预塑化;所述复合包由配方量的PE蜡、双季戊四醇酯ST220/或F210、亚磷酸酯、乙酰丙酮锌、水滑石、沸石、K123、K385、内滑剂G60、ZnO、硬脂酸钙、硬脂酸锌、β-二酮锌和AC316A组成;混料量占锅体容积的65%-68%,热混导流片侧边应距离锅壁3-5cm宽,通过底刀、中刀、扬角刀高速搅拌的协同作用,使原料温度逐步提升至115-118℃,此温度下干混料预凝胶化程度最高,在高速混合机中混合时间300-420秒;实现干混料的预塑化。3)混料冷混经热混预塑化后,通过冷混的低速搅拌,冷混时间应该在330-420秒之间,同时下料温度应设置在45℃,此时的物料含静电量和发泡剂分解比达到相对平衡最优的阶段,防止物料积热降解,发泡剂发泡分解,同时消除高速搅拌产生的静电。4)存放因钙锌生态门配方中含碳酸氢钠发泡剂,容易吸水分解,因此钙锌生态门配方储存时间不宜超过72小时,如长时间停机应提前将剩余干混料用完,否则易出现发泡倍率受影响,挤出负荷波动大等问题。5)挤出第一阶段:塑化。即通过机筒温度与螺杆的作用,物料由颗粒状转变为具有一定流动性的均匀连续熔体的过程。第二阶段:成型。具有流动性的均匀熔体,利用螺杆的旋转挤压通过多孔板进入机头,并按口模和芯模成型为具有一定形状的型坯。第三阶段:冷却定型。即型坯在挤出压力和牵引作用下,经过真空冷却定型模后,形成具有一定强度、刚度和尺寸精度的制品。挤出控制技术主要体现在温度控制上,一方面要在前期抑制过早发泡,同时筒区温度要与钙锌配方特点相匹配,同时通过研究对比,钙锌生态门挤出发泡工艺采用温度正向设置比采用温度抛物线设置和温度逆向设置出料均匀度,表面结皮效果更为理想。本申请工艺控制温度如下表1:表1挤出工艺参数控制5)下料:由于发泡门下料尺寸精确度要求高,采用相对精确的横切锯按照客户要求进行切割下料6)转印:通过温控加热转印设备,将转印膜贴覆在树脂发泡门基材上,此工序完全依靠热转印,不需使用胶水等含甲醛材料。转印工序尤其要注意温度控制,避免钙锌配方容易出现的二次发泡现象。对于门板转印工艺控制如下:收膜张力(0.2±0.05)N牵引速度:(3-5)m/min面轮1温度:(185±5)℃面轮2温度:(185±5)℃侧烫1温度:(170±5)℃侧烫2温度:(170±5)℃侧烫3温度:(130±5)℃对于辅材转印工艺控制如下:产品性能指标1)严格按照内控标准进行生产,各项性能满足用户使用要求。2)钙锌基材与转印工艺都满足环保材料要求,基材不含重金属,转印材料不含甲醛。3)防腐、防潮、防虫蛀、不变形,由于所用主原料聚氯乙烯自身性能,受酸碱的影响较小;吸水率仅为0.5%;有效防止虫蛀。非常适用于南方潮湿的环境。4)加工安装便捷、板材内部采用中空结构和芯层发泡技术,使发泡产品的密度接近木材。类似木质的加工要求,比木质门的安装更加快捷,不需钉钉子、抹腻子、刷油漆等传统作业方式,工厂标准化生产,数控机床铣制合页、锁孔、装饰窗孔,尺寸标准精确,确保现场安装时整体严密。采用分件积木式结构,便于运输,现场安装方便,避免了在现场繁杂的手工加工制作过程,走工厂化流水线作业的道路,提高了门的制作安装效率。加工手段多样化,无需专业人员,所用加工工具通用性强。当前第1页1 2 3