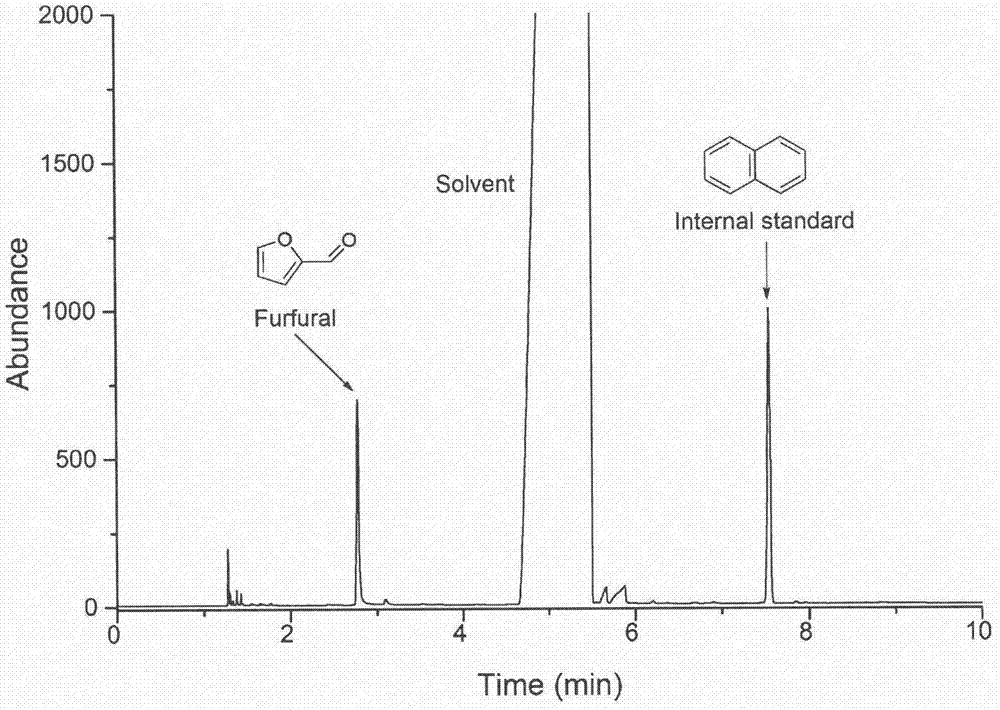
本发明涉及有机化合物合成领域,尤其涉及催化生物质转化制备糠醛的方法。
背景技术:
发展生物质资源的高效转化利用对于能源和化学品工业的可持续发展具有重要的意义。在从生物质转化得到的众多有机化学品中,糠醛是一种重要的化工产品,在树脂、医药、农药、能源及化工等领域中具有广泛的应用前景。糠醛分子结构中的醛基、烯烃和环醚等官能团的存在,使其具有较高的反应活性,通过加氢、氧化、酯化等反应可以衍生出一系列呋喃基化学品和溶剂,例如糠醇、四氢呋喃、环戊酮、γ-戊内酯和乙酰丙酸酯等。中国是糠醛工业大国,占世界糠醛总产量的70%以上。在现有的工业生产方法下糠醛得率普遍较低,并且生产过程中会产生大量的废气废液,造成严重的环境污染。有鉴于此,发展一种高效、环保的反应工艺来制备高产率的糠醛产品就具有重要意义。工业上,糠醛主要由戊糖含量高的半纤维素原料在稀酸催化水解下得到,应用最多的是硫酸和盐酸。受多种条件的限制,工业上糠醛的最高产率只能达到理论产率的45%~55%。为了解决糠醛产率低的问题,国内外众多学者对现有的生产工艺进行了全面的革新,主要的研究方向是开发新型催化剂(金属盐或固体酸催化剂)和溶剂体系(双相体系)。例如stein等在水和2-甲基四氢呋喃的双相体系中,测试了一系列金属氯化盐在木糖制备糠醛反应中的催化活性,当使用fecl3作为催化剂时,糠醛收率为31%。在加入nacl提高糠醛在有机相中的分配比后,糠醛的收率可由31%提高到71%(chemsuschem[j].2011,4,1592.)。bhaumik等利用合成的sapo-44分子筛,在水/甲苯双相体系中高效催化不同半纤维素原料转化,糠醛得率均在60%以上。反应过程产生的糠醛可以被快速萃取到有机相中,有效抑制了副反应的发生,从而提高了糠醛的选择性(acscatal.[j].2013,3,2299.)。但是目前使用的金属盐均为金属氯化物,其催化效率仍然较低,并且需要添加大量的nacl来产生“盐析”效应以降低糠醛在水中的溶解性。而固体酸催化剂的酸性往往比无机酸差很多,并且固体酸高成本也是其目前在工业上难以替代无机酸的主要原因。因此,针对现有的催化体系存在的缺点,开发反应条件更加温和、工艺更加简单、催化效率更高、成本更低的催化体系就成为了生物质制备糠醛工艺中亟待解决的问题。技术实现要素:本发明的目的在于提供一种简单高效的由生物质制备糠醛的新方法,本发明提供的方法能够高产率地制备糠醛,同时具有反应成本低,环境友好,产物易分离,催化剂易回收等优点。本发明采用的技术方案如下:本发明提供了一种制备糠醛的方法,包括以下步骤:将生物质原料和金属硫酸盐加入到有机溶剂/水双相反应体系中,在110-150℃温度下加热反应10-300min,糠醛的收率在19%-90%之间变动。上述的制备方法中,任何可脱水(或水解、脱水)得到糠醛的生物质原料均可作为本发明的原料,包括但不限于木糖、木聚糖、秸秆、玉米芯、甘蔗渣和木粉等生物质。上述的制备方法中,所述金属硫酸盐的金属阳离子为al3+、cr3+或fe3+中的至少一种。上述的制备方法中,采用的反应体系为有机溶剂/水双相反应体系,所述的有机溶剂为γ-戊内酯、四氢呋喃、2-甲基四氢呋喃、甲基异丁基甲酮、甲苯或丁醇以及它们任意比例的混合物,且有机溶剂占整个双相体系体积比为0-100%。上述的制备方法中,所述的加热方式为微波加热或油浴加热。在微波加热条件下,反应时间为10-50min。在油浴加热条件下,反应时间为60-300min。上述的制备方法中,所述金属硫酸盐催化剂和所述生物质原料的质量比为1∶(1~10);所述生物质原料在所述双相体系中的质量浓度为1%~30%。上述反应可在空气中进行,但优选在氮气、氩气的惰性气体氛围中进行。反应结束后,离心,生成的糠醛被有效地萃取到上层有机相中,催化剂被留存在下层水相中,通过对上相进行减压蒸馏即可得到高纯度的糠醛,而下层水相可以直接用于下次催化反应。本发明未提及的技术均参照现有技术。本发明提供了一种由生物质制备糠醛的方法,具有以下优点:利用廉价的金属硫酸盐作为催化剂,成本低、催化活性高、能够将生物质原料高产率地转化为糠醛,同时无需添加氯化钠就可以使有机溶剂和水有效分离,并提高了糠醛在有机相中的分配比。本发明提供的方法,不仅反应条件温和、反应时间短、催化剂易回收、重复利用性好、无腐蚀、无污染,同时还能高收率的获得糠醛产品。附图说明图1为本发明实施例1所得糠醛的气相色谱测试图。图2为本发明实施例1、4、5所得反应体系。具体实施方式以下以实施例来具体说明本发明的内容,但本发明的保护范围不仅限于此:催化剂种类:实施例1将250mg木聚糖(质量浓度为2.5%)、2ml水、8mlγ-戊内酯以及0.2mmolal2(so4)3(al3+为0.4mmol,金属盐与木聚糖的质量比为1∶3.65)加入到聚四氟乙烯反应釜中,在空气氛围下,以400w微波功率加热升温1min至130℃,反应30min。反应产物通过气质联用分析以及与糠醛的标准品进行对比证实主要产物确为糠醛。以萘作为内标,通过气相色谱的定量分析,得到糠醛的产率为87.8%。实施例2与实施例1基本相同,所不同的是:采用0.2mmolfe2(so4)3代替实施例1中的0.2mmolal2(so4)3,检测结果为,本发明实施例得到糠醛的产率为84.2%。实施例3与实施例1基本相同,所不同的是:采用0.2mmolcr2(so4)3代替实施例1中的0.2mmolal2(so4)3,检测结果为,本发明实施例得到糠醛的产率为70.5%。实施例4与实施例1基本相同,所不同的是:采用0.4mmolalcl3代替实施例1中的0.2mmolal2(so4)3,检测结果为,本发明实施例得到糠醛的产率为51.5%。实施例5与实施例4基本相同,所不同的是:添加12mmolnacl到反应体系中,检测结果为,本发明实施例得到糠醛的产率为64.2%。微波反应时间:实施例6与实施例1基本相同,所不同的是:采用10min反应时间代替实施例1中的30min反应时间,检测结果为,本发明实施例得到糠醛的产率为23.3%。实施例7与实施例1基本相同,所不同的是:采用20min反应时间代替实施例1中的30min反应时间,检测结果为,本发明实施例得到糠醛的产率为65.3%。实施例8与实施例1基本相同,所不同的是:采用40min反应时间代替实施例1中的30min反应时间,检测结果为,本发明实施例得到糠醛的产率为84.6%。实施例9与实施例1基本相同,所不同的是:采用50min反应时间代替实施例1中的30min反应时间,检测结果为,本发明实施例得到糠醛的产率为81.1%。微波加热反应温度:实施例10与实施例1基本相同,所不同的是:采用110℃的反应温度代替实施例1中的130℃反应温度,检测结果为,本发明实施例得到糠醛的产率为35.9%。实施例11与实施例1基本相同,所不同的是:采用120℃的反应温度代替实施例1中的130℃反应温度,检测结果为,本发明实施例得到糠醛的产率为62.7%。实施例12与实施例1基本相同,所不同的是:采用140℃的反应温度代替实施例1中的130℃反应温度,检测结果为,本发明实施例得到糠醛的产率为84.2%。实施例13与实施例1基本相同,所不同的是:采用150℃的反应温度代替实施例1中的130℃反应温度,检测结果为,本发明实施例得到糠醛的产率为78.2%。木聚糖的质量浓度:实施例14与实施例1基本相同,所不同的是:采用100mg糠醛(在双相体系中的质量浓度1%)的反应物料代替实施例1中的250mg反应物料,检测结果为,本发明实施例得到糠醛的产率为90.1%。实施例15与实施例1基本相同,所不同的是:采用500mg糠醛(在双相体系中的质量浓度5%)的反应物料代替实施例1中的250mg反应物料,检测结果为,本发明实施例得到糠醛的产率为82.8%。实施例16与实施例1基本相同,所不同的是:采用1g糠醛(在双相体系中的质量浓度10%)的反应物料代替实施例1中的250mg反应物料,检测结果为,本发明实施例得到糠醛的产率为71.7%。实施例17与实施例1基本相同,所不同的是:采用2g糠醛(在双相体系中的质量浓度20%)的反应物料代替实施例1中的250mg反应物料,检测结果为,本发明实施例得到糠醛的产率为60.1%。实施例18与实施例1基本相同,所不同的是:采用3g糠醛(在双相体系中的质量浓度30%)的反应物料代替实施例1中的250mg反应物料,检测结果为,本发明实施例得到糠醛的产率为49.2%。实施例19与实施例1基本相同,所不同的是:采用3g糠醛(在双相体系中的质量浓度30%)的反应物料代替实施例1中的250mg反应物料,并延长反应时间至50min,检测结果为,本发明实施例得到糠醛的产率为79.2%。催化剂用量:实施例20与实施例1基本相同,所不同的是:采用0.073mmol催化剂用量(金属硫酸盐和木聚糖的质量比为1∶10)代替实施例1中的0.2mmol催化剂用量,检测结果为,本发明实施例得到糠醛的产率为52.1%。实施例21与实施例1基本相同,所不同的是:采用0.146mmol催化剂用量(金属硫酸盐和木聚糖的质量比为1∶5)代替实施例1中的0.2mmol催化剂用量,检测结果为,本发明实施例得到糠醛的产率为81.6%。实施例22与实施例1基本相同,所不同的是:采用0.365mmol催化剂用量(金属硫酸盐和木聚糖的质量比为1∶2)代替实施例1中的0.2mmol催化剂用量,检测结果为,本发明实施例得到糠醛的产率为83.1%。实施例23与实施例1基本相同,所不同的是:采用0.731mmol催化剂用量(金属盐和纤维素物质的量比为1∶1)代替实施例1中的0.2mmol催化剂用量,检测结果为,本发明实施例得到糠醛的产率为74.1%。γ-戊内酯的含量:实施例24与实施例1基本相同,所不同的是:采用0ml水的用量代替实施例1中的2ml水的用量,同时采用10mlγ-戊内酯的用量代替实施例1中8mlγ-戊内酯的用量(γ-戊内酯的体积百分浓度100%),检测结果为,本发明实施例得到糠醛的产率为49.8%。实施例25与实施例1基本相同,所不同的是:采用1ml水的用量代替实施例1中的2ml水的用量,同时采用9mlγ-戊内酯的用量代替实施例1中8mlγ-戊内酯的用量(γ-戊内酯的体积百分浓度90%),检测结果为,本发明实施例得到糠醛的产率为68.1%。实施例26与实施例1基本相同,所不同的是:采用3ml水的用量代替实施例1中的2ml水的用量,同时采用7mlγ-戊内酯的用量代替实施例1中8mlγ-戊内酯的用量(γ-戊内酯的体积百分浓度70%),检测结果为,本发明实施例得到糠醛的产率为82.9%。实施例27与实施例1基本相同,所不同的是:采用4ml水的用量代替实施例1中的2ml水的用量,同时采用6mlγ-戊内酯的用量代替实施例1中8mlγ-戊内酯的用量(γ-戊内酯的体积百分浓度60%),检测结果为,本发明实施例得到糠醛的产率为74.9%。实施例28与实施例1基本相同,所不同的是:采用10ml水的用量代替实施例1中的2ml水的用量,同时采用0mlγ-戊内酯的用量代替实施例1中8mlγ-戊内酯的用量(γ-戊内酯的体积百分浓度0%),检测结果为,本发明实施例得到糠醛的产率为60.2%。有机溶剂的种类:实施例29与实施例1基本相同,所不同的是:采用四氢呋喃代替实施例1中的γ-戊内酯,检测结果为,本发明实施例得到糠醛的产率为53.9%。实施例30与实施例1基本相同,所不同的是:采用2-甲基四氢呋喃代替实施例1中的γ-戊内酯,检测结果为,本发明实施例得到糠醛的产率为50.1%。实施例31与实施例1基本相同,所不同的是:采用甲基异丁基甲酮代替实施例1中的γ-戊内酯,检测结果为,本发明实施例得到糠醛的产率为71.1%。实施例32与实施例1基本相同,所不同的是:采用甲苯代替实施例1中的γ-戊内酯,检测结果为,本发明实施例得到糠醛的产率为63.1%。实施例33与实施例1基本相同,所不同的是:采用丁醇代替实施例1中的γ-戊内酯,检测结果为,本发明实施例得到糠醛的产率为64.2%。生物质的种类:实施例34将250mg木糖(质量浓度为2.5%)、2ml水、8mlγ-戊内酯以及0.2mmolal2(so4)3加入到100ml聚四氟乙烯反应釜后,充入氮气保护气,密封反应器,以400w微波功率加热升温1min至130℃,反应30min后。分液分离上层有机相,加入萘作为内标,用气相色谱进行定量分析,得到糠醛的产率为89.7%实施例35与实施例1基本相同,所不同的是:采用秸秆代替实施例1中的木聚糖,检测结果为,本发明实施例得到糠醛的产率为13.3%。实施例36与实施例1基本相同,所不同的是:采用玉米芯代替实施例1中的木聚糖,检测结果为,本发明实施例得到糠醛的产率为24.2%。实施例37与实施例1基本相同,所不同的是:采用甘蔗渣代替实施例1中的木聚糖,检测结果为,本发明实施例得到糠醛的产率为14.3%。实施例438与实施例1基本相同,所不同的是:采用秸秆代替实施例1中的木聚糖,检测结果为,本发明实施例得到糠醛的产率为13.3%。催化剂复配:实施例39与实施例1基本相同,所不同的是:采用0.1mmolal2(so4)3和0.1mmolfe2(so4)3代替实施例1中的0.2mmolal2(so4)3,检测结果为,本发明实施例糠醛的产率为87.9%。实施例40与实施例1基本相同,所不同的是:采用0.1mmolal2(so4)3和0.1mmolcr2(so4)3代替实施例1中的0.2mmolal2(so4)3,检测结果为,本发明实施例得到糠醛的产率为81.2%。实施例41与实施例1基本相同,所不同的是:采用0.1mmolcr2(so4)3和0.1mmolfe2(so4)3代替实施例1中的0.2mmolal2(so4)3,检测结果为,本发明实施例得到糠醛的产率为77.4%。不同气体氛围:实施例42与实施例1基本相同,所不同的是:采用氮气分为代替实施例1中的空气氛围,检测结果为,本发明实施例得到糠醛的产率为89.9%。常规加热:实施例43将250mg木聚糖、0.2mmolal2(so4)3、8mlγ-戊内酯以及2ml水加入到100ml耐压管中,再将耐压管置于130℃的油浴中加热,反应240min。反应产物通过气相色谱分析并以萘作为内标,得到糠醛的产率为81.3%。实施例44与实施例43基本相同,所不同的是:将反应时间替换为60min,检测结果为,本发明实施例得到糠醛的产率为19.3%。实施例45与实施例43基本相同,所不同的是:将反应时间替换为120min,检测结果为,本发明实施例得到糠醛的产率为40.7%。实施例46与实施例43基本相同,所不同的是:将反应时间替换为180min,检测结果为,本发明实施例得到糠醛的产率为65.1%。实施例47与实施例43基本相同,所不同的是:将反应时间替换为300min,检测结果为,本发明实施例得到糠醛的产率为76.7%。常规加热反应温度:实施例48与实施例43基本相同,所不同的是:采用110℃的反应温度代替实施例45中的130℃反应温度,检测结果为,本发明实施例得到糠醛的产率为37.7%。实施例49与实施例43基本相同,所不同的是:采用120℃的反应温度代替实施例45中的130℃反应温度,检测结果为,本发明实施例得到糠醛的产率为63.9%。实施例50与实施例43基本相同,所不同的是:采用140℃的反应温度代替实施例45中的130℃反应温度,检测结果为,本发明实施例得到糠醛的产率为76.1%。实施例51与实施例43基本相同,所不同的是:采用150℃的反应温度代替实施例45中的130℃反应温度,检测结果为,本发明实施例得到糠醛的产率为69.6%。催化剂循环使用:将实施例1反应后得到的混合物离心,上层有机相用针筒小心抽出,下层水相重新加入到反应器内,同时加入8mlγ-戊内酯和250mg木聚糖,密封反应器。加热到130℃后反应30min。待反应体系冷却至室温后,抽取上层有机相,并用气相色谱检修;之后的循环采用同样的方法,并连续循环5次,结果如图表1所示:实施例序号催化剂循环次数糠醛产率(%)1087.852187.153286.354385.955485.756584.4通过以上的实施例可以看出,本发明提供了一种高效环保的金属硫酸盐催化剂,在水/有机溶剂的双相体系中,实现了一系列生物质原料到糠醛产品的高效率转化。该方法反应条件温和、绿色环保、催化剂成本低并且活性较高、产物与催化剂容易分离,具有十分重要的工业应用前景。当前第1页12