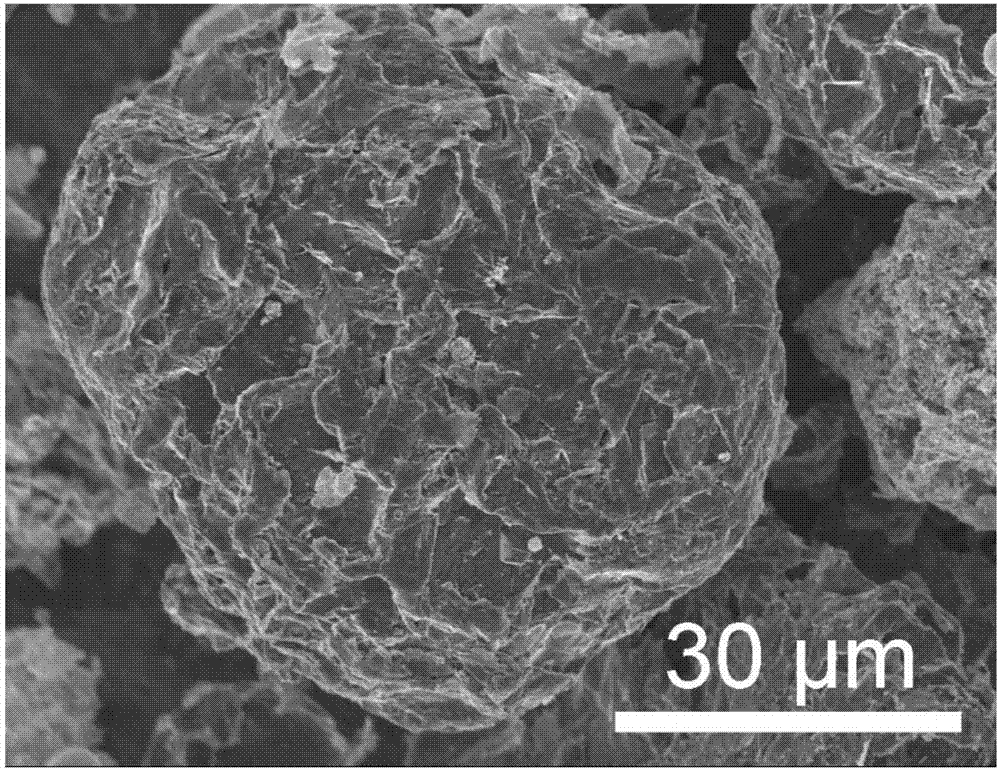
本发明涉及尼龙复合材料及其制备领域,具体涉及一种石墨烯复合尼龙粉末材料及其制备方法和在3d打印中的应用。
背景技术:
增材制造技术(也称“3d打印”)是基于计算机三维cad模型,采用逐层堆积的方式直接制造三维物理实体的方法。增材制造技术可以在一台设备上快速精密地制造出任意复杂形状和结构的零部件,从而实现“自由制造”。其中,激光烧结技术采用高分子粉末材料为原料,不需要支撑结构即可直接制造三维复杂结构,解决传统制造工艺难以甚至无法加工的制造难题。目前,国际上可供3d打印用高分子材料是目前应用最广的3d打印材料,包括pa12、peek等不超过30种,与上万种注塑成型高分子材料相比,还远远不能达到工业应用的水平。
聚酰胺俗称尼龙(nylon),由于它独特的低比重、高抗拉强度、耐磨、自润滑性好、冲击韧性优异、具有刚柔兼备的性能,可广泛代替铜和合金用于制作耐磨零件、传动结构件等耐磨损件。但是,3d打印尼龙材料的机械性能还不够完善,特别是韧性和断裂伸长率明显低于传统注塑件。此外,目前使用的尼龙粉末材料具有较大的体积收缩率,零件在激光烧结过程中特别容易翘曲,这进一步导致其综合性能难以满足工程应用的需要。为了提高尼龙材料在低温和干燥状况下机械特性和几何特性,通常需要加入各种改性剂。
石墨烯是目前已知强度最高的材料,其强度约为结构钢的100倍。同时,石墨烯还具有重量轻、柔韧性好等特性,使用3d打印技术直接加工石墨烯复合材料将能够制造具有高强度、重量轻、以及柔韧性俱佳的零部件或产品。除此之外,石墨烯最重要的性质之一就是它独特的载流子特性和无质量的狄拉克费米子属性,这赋予其优良的导热和导电性。
目前,有人尝试采用液相共沉淀法制备激光烧结用石墨烯复合尼龙粉体,具体是将石墨烯粉末与尼龙加入有机溶剂中,经加压、加热,尼龙溶解并与石墨烯混合均匀后降温异相结晶,得石墨烯增强型尼龙3d打印粉体材料。这种制备方法得到的粉体材料需要石墨烯在尼龙基体中均匀分散、并且与尼龙基体有较好的结合力,为达到上述效果,需要采用单层石墨烯。而单层石墨烯的制备工艺复杂,价格昂贵,很难在导热、导电和大型零部件上应用。多层石墨烯在层数增加到几十到数百层左右也就是约几十纳米到几百纳米厚度左右,其性质与一般石墨已经接近,通过上述的液相共沉淀法方法将难以获得预期的增强效果。另外,为保证3d打印构件的表面精度和力学性能,所用粉末材料粒径需要在20~120微米之间,优选45微米左右。而单层悬浮石墨烯稳定尺寸最大可达20微米,多层石墨烯约几十纳米到几百纳米厚度左右,而直径通常几百微米。由于石墨烯颗粒的异相成核作用,通过上述液相共沉淀法制备的石墨烯复合尼龙粉体通常在上百微米以上,不仅无法满足激光烧结系统的要求,而且3d打印构件表面粗糙,还需要大量的后处理工作。
因此,开发出适合导热、导电和大尺寸构件领域应用的低成本石墨烯复合尼龙3d打印粉体,将会促进增材制造技术的广泛推广和石墨烯复合材料在航空航天、汽车、半导体和先进制造业方面的应用。
技术实现要素:
为克服现有3d打印用石墨烯/尼龙复合粉体在性能和成本方面的不足,本发明提供了一种石墨烯复合尼龙粉末材料及其制备方法,该方法对石墨烯的片层结构没有特殊要求,显著降低了制造成本;以该石墨烯复合尼龙粉末材料为原料经激光烧结技术制备的产品具有高的导热、导电性能,并兼具优异的抗冲击特性。
具体技术方案如下:
一种石墨烯复合尼龙粉末材料,原料组成包括尼龙和石墨烯,所述的石墨烯为粉末状的石墨烯微片,片径≤100微米,厚度≤30微米;
所述石墨烯复合尼龙粉末材料中,石墨烯以片状存在于尼龙粉末表面。
作为优选,以原料总质量计,所述石墨烯的质量分数为0.1~5%。
所述的石墨烯可由本领域人员所熟知的机械剥离法、氧化还原法、sic外延生长法、化学气相沉积法(cvd)等方法获得。作为优选,所述的石墨烯选自纯石墨烯微片、氧化石墨烯微片、有机改性石墨烯微片中的至少一种。
由于完整结构的石墨烯化学稳定性高,表面呈惰性状态。可以通过对石墨烯有机改性进一步提高石墨烯与尼龙颗粒表面的相互作用。本发明所述的有机改性石墨烯微片包括表面经硅烷化、酰胺化、吸附含有芳香结构的小分子和聚合物得到的有机功能化石墨烯微片。
作为优选,所述的尼龙选自尼龙-6、尼龙-66、尼龙-610、尼龙11、尼龙12中的至少一种。所述的尼龙还包括由上述尼龙中的至少两种组成的热塑性共聚物。
作为优选,原料组成还包括防粘剂,进一步优选酰胺类防粘剂。
本发明公开了所述的石墨烯复合尼龙粉末材料的制备方法,步骤如下:
(1)将石墨烯超声分散于有机溶剂a中,得到石墨烯分散液;
(2)将尼龙、可选择性加入的防粘剂与有机溶剂b混合后置于高压反应釜中,初次升温至150~230℃直至尼龙完全溶解,解除高压后,降温至60~90℃,得到尼龙微米颗粒悬浮液;
(3)将步骤(1)制备的石墨烯分散液与步骤(2)制备的尼龙微米颗粒悬浮液混合得混合液,再次升温至120~150℃,反应后再经后处理得到所述的石墨烯复合尼龙粉末材料。
本发明制备得到的石墨烯复合尼龙粉末材料,与现有技术中采用液相共沉淀法制备的石墨烯复合尼龙粉体相比,存在两点显著不同:
1、结构不同:液相共沉淀法制备得到的石墨烯复合尼龙粉体,石墨烯是均匀分布在尼龙基体内部,而本发明制备得到的产物,石墨烯以片状均匀包覆于尼龙粉末表面。
2、原料不同:液相共沉淀法对原料石墨烯的片层结构有着特殊的要求,其片层厚度必须在几百纳米以下,而本发明中,对于石墨烯的片层结构没有特殊要求,即使是片层厚度达到100微米的石墨烯微片也能保证复合材料及制备得到的产品构件具有良好的导热、导电等物理性能。
作为优选,步骤(1)中,所述的有机溶剂a选自乙醇、乙二醇、正丙醇、异丙醇、正丁醇、乙腈、甲酸、n,n-二甲基甲酰胺中的至少一种;
所述的石墨烯分散液的质量百分比浓度为20~65%。
本发明中,步骤(2)中尼龙原料的溶解是关键。通常地,尼龙类缩聚物由于具有较高的结晶度,在常温下难以溶解。一般地,只有硫酸、酚类溶剂、含氯溶剂和少数含氟溶剂才能使之完全溶解。本发明中,尼龙的溶解过程是在高压反应釜内进行,溶解过程中伴随高速搅拌,溶解过程的温度、时间需根据具体采用的尼龙种类进行适应性调整。
作为优选,步骤(2)中,所述的有机溶剂b选自乙醇、乙二醇、正丙醇、异丙醇、正丁醇、乙腈、甲酸、n,n-二甲基甲酰胺中的至少一种。
为防止超细粉末粘结结块,可选择性的加入防粘剂,是否添加防粘剂,取决于粒径的大小。通常对3d打印构件表明精度要求较高时需要小颗粒尼龙粉体,但由于表面能较大易于团聚,而大颗粒尼龙粉体抗粘性较好。优选地,d50小于50微米时建议添加防粘剂。作为优选,所述的防粘剂选自油酸酰胺、芥酸酰胺、乙醇双硬脂酰胺、乙醇双月桂酰胺中的至少一种。防粘剂的用量通常为尼龙质量的0.1~1%。
步骤(2)中的降温过程对于保证所制备的石墨烯复合尼龙粉末材料具有优异的性能具有关键作用。由于尼龙溶液处于过饱和状态,如果降温速度太快,反应釜内温度不均,导致较冷区域尼龙首先成核结晶,随后可发生二次成核,粒径分布不均或颗粒快速长大;如果降温速度过慢,尼龙在某个温度发生快速成核,从而形成大量小颗粒,难以满足3d打印设备需求。作为优选,本发明所述降温的速率为4~10℃/min,采用该降温速率,可以保证在加入石墨烯前形成10~120微米尺度的球形尼龙颗粒悬浮液。经试验发现,上述降温速率可保证制备的尼龙粉体在后续激光烧结成型过程具有最佳的粉体流动性和打印构件力学性能。
步骤(3)中,所述的后处理包括固液分离和干燥处理,固液分离可采用离心、过滤、加热挥发、减压蒸馏等本领域技术人员熟知的分离方法。
本发明还公开了由上述方法制备得到的石墨烯复合尼龙粉末材料在3d打印中应用,所述的3d打印采用选择性激光烧结技术。
与现有技术相比,本发明具有如下优点:
(1)本发明的石墨烯复合尼龙材料通过在尼龙粉末表面掺杂低成本的石墨烯微片,从而在3d打印构件中形成均匀的石墨烯网络,有利于提高3d打印尼龙构件的机械强度和物理性能,特别是在不采用单层石墨烯的条件下,即可获得较高的抗冲击强度、抗变型特性及优异的导热导电性能。有利于解决由于激光烧结成型过程热应力集中导致的严重的翘曲变形现象,并提高打印件的韧性和应用领域。
(2)本发明的石墨烯复合尼龙粉末制备方法,采用了双液相合成方法,石墨烯主要分布于尼龙粉末颗粒表面,不仅尼龙粉末的粒径分布比较均匀,还解决了由于石墨烯成核作用导致尼龙材料结晶度降低、尺寸难以满足3d打印要求的问题。
(3)本发明的制备方法不需要石墨烯在尼龙基体中均匀分散,因此无论单层石墨烯还是大尺寸石墨烯颗粒,均能通过本方法获得满足3d打印的粉体材料,能够大幅度降低制备成本,且对环境友好。
附图说明
图1为实施例1制备得到的未加入石墨烯的尼龙粉末的sem图;
图2为实施例1制备得到的石墨烯复合尼龙粉末材料的sem图。
具体实施方式
为进一步阐明本发明的目的、技术方案和优点,以下结合具体实施例,对本发明作进一步的详细说明,但并不因此而限制本发明的保护范围。
实施例1
(1)将直径约40μm,厚度约25μm高纯石墨烯微片在200℃烘箱中干燥24h,取1g干燥后的石墨烯微片用超声波仪(功率900w,频率2.45ghz)分散在100g异丙醇中1min,制得石墨烯分散液。
(2)将90g尼龙12颗粒与900g乙醇和乙烯-双硬脂酰胺混合物(乙烯-双硬脂酰胺质量分数为1%)加入高压反应釜中,通入氮气加压至1mpa,并高速搅拌(630rpm)。将温度升至145℃,保温1h至尼龙12完全溶解。完全溶解后解除高压,以4℃/min的速度将温度降至68℃,得到35~72微米尺度的尼龙微米颗粒悬浮液,sem图见附图1所示。
(3)将石墨烯分散液加入置于高压反应釜内的尼龙微米颗粒悬浮液中,升温至140℃,加压至1mpa,恒速搅拌1h后,降至常温常压(即101kpa)。通过真空过滤器将析出粉末分离,经酒精洗涤后在100℃真空烘箱中彻底干燥10h,得到颗粒尺寸42~98微米石墨烯增强尼龙复合粉末,sem图见附图2所示。
本实施例制备得到的石墨烯复合尼龙粉末材料中,较大粒径的石墨烯微片通过140℃热处理,均匀吸附在预先形成的尼龙12粉体表面,即防止了3d打印铺粉过程中由于石墨烯与尼龙颗粒比重不同而发生分相,也有利于提高打印机铺粉速度。
对比例1
本对比例采用石墨烯和尼龙材料共沉淀的制备方法,为提高石墨烯微片与尼龙基体的结合力,需要先氧化制成氧化石墨烯,具体包括以下步骤:
(1)将1.0g直径约40μm,厚度约25μm的高纯石墨烯微片浸入69%浓硝酸溶液中,升温至83℃进行表面化学预处理3h。然后将片晶用去离子水浸洗2h,并在200℃烘箱中干燥24h以除去残留的酸和水,随后加入到十八烷基三甲基氯化铵的乙醇溶液中得到改性氧化石墨烯微片;
(2)将改性氧化石墨烯微片、90g尼龙12颗粒和900g乙醇和乙烯-双硬脂酰胺混合物(乙烯-双硬脂酰胺质量分数为1%)一起加入高压反应釜中,通入氮气加压至1mpa,并高速搅拌(630rpm)。将温度升至145℃,保温1h至尼龙12完全溶解。完全溶解后解除高压,温度降至68℃形成尼龙粉体悬浮液。
(3)通过真空过滤器将析出粉末分离,经酒精洗涤后在100℃真空烘箱中彻底干燥10h,得到石墨烯增强尼龙复合粉末。
本对比例所得氧化石墨烯增强尼龙材料中,氧化石墨烯均匀分布在尼龙基体中,并与尼龙形成化学结合。
对比例2
本对比例采用石墨烯和尼龙粉体材料机械混合的制备方法,具体包括以下步骤:
(1)将90g尼龙12颗粒与900g乙醇和乙烯-双硬脂酰胺混合物(乙烯-双硬脂酰胺质量分数为1%)加入高压反应釜中通入氮气加压至1mpa,并高速搅拌(630rpm)。将温度升至145℃,保温1h至尼龙12完全溶解。完全溶解后解除高压,温度降至68℃形成尼龙粉体悬浮液。
(2)通过真空过滤器将析出粉末分离,经酒精洗涤后在100℃真空烘箱中彻底干燥10h。最后通过筛分得到直径小于100μm的尼龙粉末。
(3)将1.0g直径约40μm,厚度约25μm的高纯石墨烯微片与尼龙粉末机械混合,得到石墨烯复合尼龙12复合粉末。
本对比例所得氧化石墨烯增强尼龙材料中,氧化石墨烯与尼龙颗粒均匀混合在一起,但之间无化学或物理结合。
将实施例1、对比例1和对比例2所得石墨烯复合尼龙12粉体材料用于选择性激光烧结系统,粉体粒径及所制造的产品性能如表1所示。
表1
由表1可知,本发明实施例1所制备的石墨烯复合尼龙12材料粒径较小,在冲击强度、导热性和导电性这三个性能指标上都比传统共沉淀法明显提高,其中,冲击强度提高达39.2%,热导提高1.9倍,电导提高达3个数量级。而对比例3所示的机械混合法,无论机械性能还是导热导电性能均较上述两者低。这说明本发明通过在粉体颗粒表面添加少量石墨烯颗粒就可达到较好的效果。
实施例2
制备工艺与实施例1中的相同,区别仅在于所采用的高纯石墨烯微片的直径约130μm,厚度约102μm。得到135~170微米尺度的石墨烯增强尼龙复合粉末。
本实施例所得石墨烯增强尼龙粉体材料颗粒较大,在激光烧结过程中铺粉性能较好,但打印件表面具有较大的粗糙度,拉伸强度稍低于实例1,可达到50.7mpa。但z方向热导为0.92w/mk、z方向电导1.68e-07s/cm,均与实施例1接近,说明本实施例采用的石墨烯微片可覆盖在颗粒表面并能在3d打印构件中形成有效的导热导电网络。
实施例3
制备工艺与实施例1中的相同,区别仅在于步骤(2)中的降温速率为10℃/min。得到75~140微米尺度的石墨烯增强尼龙复合粉末。
本实施例所得石墨烯增强尼龙粉体材料经激光烧结得到的打印件,力学性能与导电、导热性能均于实施例1制备得到的打印件相当。
经试验发现,进一步提高降温速率,所得石墨烯增强尼龙粉体材料颗粒较大,并且颗粒分布呈多分散状态,导致激光烧结构件孔隙偏多,边角明显变形,拉伸强度明显低于实例1。
实施例4
制备工艺与实施例1中的相同,区别仅在于步骤(2)中的降温速率为2℃/min。得到10~60微米尺度的石墨烯增强尼龙复合粉末。
本实施例所得石墨烯增强尼龙粉体材料颗粒尺寸明显降低,导致颗粒间粘度较大,激光烧结过程铺粉少量结块,打印件拉伸强度42.1mpa。打印件孔隙较多。进一步降低降温速率,对性能影响不大,但耗时较长。
实施例5
(1)将羧基化石墨烯微片在200℃烘箱中干燥24h以除去吸附水,得到石墨烯微片直径约3μm,厚度约27μm。取0.1g石墨烯微片用超声波仪(功率900w,频率5.8ghz)分散在100g异丙醇中1min,制得石墨烯分散液。
(2)将99.9g尼龙6颗粒与1000g乙二醇加入反应釜中,通入氩气加压至1mpa,并高速搅拌(650rpm)。将温度升至220℃,保温4.5h至尼龙6完全溶解。完全溶解后解除高压,温度降至68℃加入石墨烯分散液,得到混合液。
(3)将高压反应釜升温至150℃,加压至1mpa,恒速搅拌1h后,降至常温常压(即101kpa)。通过真空过滤器将析出粉末分离,经酒精洗涤后在100℃真空烘箱中彻底干燥10h。最后通过筛分得到直径小于100μm的纳米复合粉末。
实施例6
(1)石墨烯分散液制法与实施例1相同。本实施例中的石墨烯微片为氮掺杂石墨烯。
(2)将45g尼龙6颗粒,45g尼龙12颗粒,1000gn,n-二甲基甲酰胺和9g乙醇双月桂酰胺加入反应釜中,通入氮气加压至1mpa,并高速搅拌(650rpm)。将温度升至210℃,保温4.5h至尼龙完全溶解。完全溶解后解除高压,温度降至60℃加入石墨烯分散液,得到混合液。此步骤注意回收利用n,n-二甲基甲酰胺溶剂。
(3)将高压反应釜升温至130℃,恒速搅拌1h后,降至常温常压。通过真空过滤器将析出粉末分离,经酒精洗涤后在100℃真空烘箱中彻底干燥10h。最后通过筛分得到直径小于50~100um的纳米复合粉末。
实施例7
(1)将质量比为1:1的高纯石墨烯微片与氮掺杂石墨烯微片浸入69%浓硝酸溶液中,升温至83℃进行表面化学预处理3h。然后将片晶用去离子水浸洗2h,并在200℃烘箱中干燥24h以除去残留的酸和水。得到石墨烯微片直径约3μm,厚度约25μm。取1g微片用超声波仪(功率900w,频率2.45ghz)分散在100g异丙醇中1min,制得石墨烯分散液。
(2)将19g尼龙66颗粒,100g甲酸与n,n-二甲基甲酰胺混合物(混合比例为4:1)加入高压反应釜中,常压条件下高速搅拌(650rpm)。将温度升至255℃,保温4.5h至尼龙66完全溶解。完全溶解后温度降至60℃加入石墨烯分散液,得到混合液。此步骤注意回收利用n-二甲基甲酰胺溶剂。
(3)将高压反应釜升温至130℃,恒速搅拌1h后,降至常温常压。通过真空过滤器将析出粉末分离,经酒精洗涤后在100℃真空烘箱中彻底干燥10h。最后通过筛分得到直径小于50~100um的纳米复合粉末。
以上所述,仅为本发明的具体实施方式,并不构成对本专利保护范围的限制,任何熟悉本技术领域的技术人员在本发明揭示的技术范围内,可轻易想到变化或替换,都应涵盖在本发明的保护范围之内。