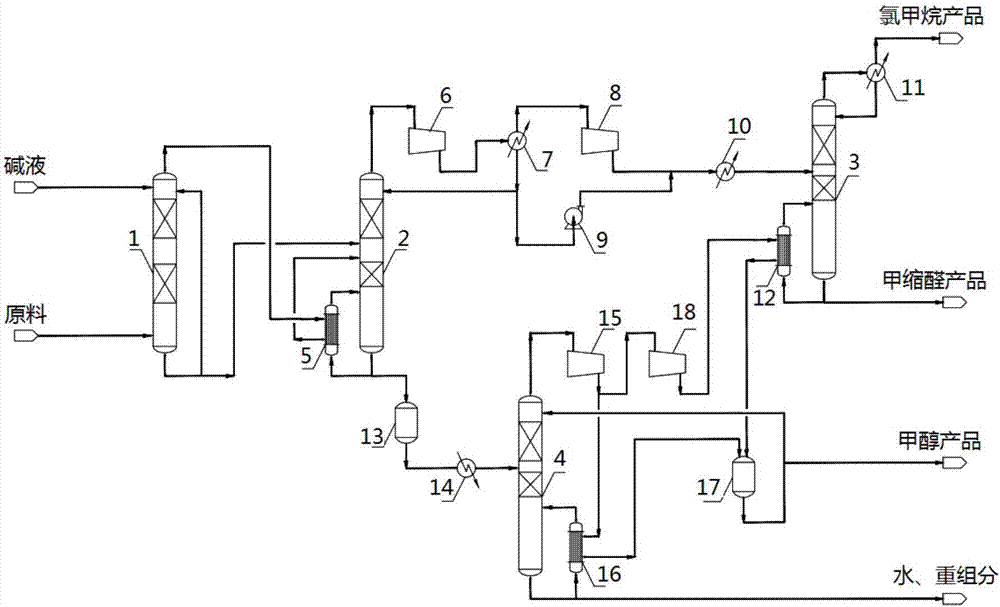
本发明属于化工领域,涉及用于草甘膦溶剂及副产物回收的方法。
背景技术:
:草甘膦是一种高效、低毒、低残留、广谱性、与环境相容性好的除草剂,因其性能优越而成为目前世界范围内使用最广泛的除草剂品种。草甘膦的生产方法有多种,目前国内主要采用以甘氨酸和亚磷酸二甲酯为主要原料的烷基酯法生产。该方法以甲醇为反应溶剂,在催化剂三乙胺的存在下,甘氨酸首先和聚甲醛反应形成n,n-二羟甲基甘氨酸,再与亚磷酸二甲酯反应后加盐酸水解生成草甘膦以及副产物甲缩醛和氯甲烷。水解过程中产生大量蒸汽,主要成分为甲醇、甲缩醛、氯甲烷、水和少量氯化氢气体。传统的回收工艺是对水解蒸汽进行冷凝,其中沸点相对较高的甲醇、甲缩醛、水和少量氯化氢气体冷凝成为液相,称为稀甲醇;氯甲烷为气相,经水洗、碱洗、硫酸干燥达到净化目的后得到氯甲烷气体,经压缩、冷凝后得到氯甲烷产品。冷凝得到的稀甲醇加碱中和,通过两个精馏塔分别回收其中的甲醇和甲缩醛,甲醇作为溶剂回用至草甘膦合成环节,甲缩醛作为副产品。草甘膦生成过程中水解和溶剂回收两个工序是最主要的蒸汽消耗工序,其中溶剂回收工序的蒸汽消耗约占整个草甘膦生产过程蒸汽消耗的50%。现有工艺中,大量甲醇、甲缩醛、水等物料先被冷凝成液态,在进入精馏塔后又需耗用大量蒸汽加热成汽态,不仅浪费了水解蒸汽的热量,还额外消耗了大量生蒸汽,造成了极大的热量浪费。现有技术中,公开号为cn106748637a的发明专利公开了一种草甘膦水解尾气回收方法,水解尾气以气体形态进入精馏塔,并通过二级冷凝的方式将水解气体冷凝分离为甲醇和甲缩醛的混合凝液以及甲缩醛和氯甲烷的混合凝液,并分别进行精馏提纯得到甲醇、甲缩醛、氯甲烷产品。该方法能耗较传统工艺有所降低,但仍需要消耗一定量的生蒸汽作为精馏塔再沸器的热源。由于氯甲烷的沸点较低,使用冷却水无法将其冷凝,因此在二级冷凝器中需要使用大量冷冻盐水来进行冷却。而与冷却水相比,制备提供相同冷量的冷冻盐水要消耗更多的能源、成本也更高,因此,冷冻盐水的使用大大增加了生产成本,也削弱了汽相进料所带来的降低工艺能耗的作用。公开号为cn101225030b的发明专利公开了一种草甘膦连续合成中热能利用的方法,将草甘膦生产过程中水解产生的蒸汽经预热进塔,塔内中和或塔外气相中和,经脱水,塔顶馏出蒸汽再预热到过热状态,送入第二精馏塔分离,得甲缩醛和甲醇产品。虽然有效利用了水解蒸汽的热能,但在加热精馏塔再沸器时仍需消耗一定量的生蒸汽。此外,在第二精馏塔塔顶馏出甲缩醛并分离出不凝气体氯甲烷,塔釜排出精甲醇产品。塔顶部分冷凝,由于氯甲烷的存在,导致第二精馏塔塔顶冷凝温度降低,无法使用冷却水达到冷凝目的,因此必须使用大量冷冻盐水进行冷却,也同样削弱了汽相进料所带来的降低工艺能耗的作用,大大增加了生产成本。因此,亟需一种具有很好的节能降耗效果的草甘膦溶剂及副产物回收的方法。技术实现要素:有鉴于此,本发明的目的在于提供一种用于草甘膦溶剂及副产物回收的方法,具有很好的节能降耗效果,草甘膦溶剂及副产物回收率高,产品质量高,应用前景广。为达到上述目的,本发明提供如下技术方案:用于草甘膦溶剂及副产物回收的方法,其特征在于,包括如下步骤:将草甘膦生产过程中水解产生的蒸汽通入汽相中和塔,使用碱液进行中和,中和得到的汽相为预精馏塔再沸器供热后通入预精馏塔中,中和得到的液相一部分循环回汽相中和塔,一部分通入预精馏塔;通入的汽相和液相在预精馏塔精馏,塔顶得到含有甲缩醛和氯甲烷的轻组分,塔底得到含有甲醇、水和重组分的混合物,得到的含有甲缩醛和氯甲烷的轻组分经压缩机ⅰ压缩后通入预精馏塔冷凝器进行部分冷凝,部分冷凝得到的汽相经压缩机ⅱ压缩后通入轻组分冷却器,部分冷凝得到的液相经加压泵加压后通入轻组分冷却器,再由轻组分冷却器通入轻组分精制塔;将通入轻组分精制塔的含有甲缩醛和氯甲烷的轻组分经过精馏处理,塔顶得到氯甲烷产品,塔底得到甲缩醛产品;含有甲醇、水和重组分的混合物通入中间缓冲罐缓冲,经中间加热器加热后通入甲醇精制塔精馏处理,处理后塔底得到含重组分的水,塔顶得到精甲醇蒸汽,得到的甲醇蒸汽经甲醇压缩机加压提高能量品位后用作轻组分精制塔再沸器和甲醇精制塔再沸器的热源,换热冷凝后用甲醇凝液收集罐收集得到精甲醇产品。作为本发明优选的方案,将甲醇精制塔塔顶得到的精甲醇蒸汽经甲醇压缩机压缩提高能量品位后一部分用作甲醇精制塔再沸器的热源,另一部分经二级甲醇压缩机压缩后用作轻组分精制塔再沸器的热源。作为本发明优选的方案,将甲醇精制塔塔顶得到的精甲醇蒸汽经甲醇压缩机压缩提高能量品位后一部分用作中间再沸器的热源,另一部分进入二级甲醇压缩机,经压缩提高品位后一部分用作甲醇精制塔再沸器的热源,另一部分经三级甲醇压缩机压缩后用作轻组分精制塔再沸器的热源。更优选的,所述中间加热器使用所述甲醇精制塔塔底出料废水作为热源。更优选的,所述草甘膦生产过程中水解产生的蒸汽包括如下组分:质量分数为20%~60%的甲醇,质量分数为5%~30%的氯甲烷,质量分数为1%~20%的甲缩醛和质量分数为20%~45%的水;还包括必要的杂质,如少量氯化氢、空气、二甲醚等。更优选的,所述碱液为碱金属氢氧化物的水溶液或甲醇溶液,碱液用量以中和后塔顶出料ph达到7.0为准。更优选的,所述碱液在温度为40~90℃、常压条件下进行中和。更优选的,所述预精馏塔在压力为0.07~0.1mpa,塔顶回流比为0.3~2条件下精馏。更优选的,所述轻组分精制塔在压力为0.75~1.1mpa、塔顶回流比为0.8~3条件下精馏。更优选的,所述甲醇精制塔在常压,塔顶回流比为0.5~2.5条件下精馏。本发明的有益效果在于:(1)甲醇精制塔采用了热泵精馏,将塔顶的低品位热能转化为高品位热能,为甲醇精制塔和轻组分精制塔的再沸器供热,合理利用热量,代替了低压或中压蒸汽的使用,且预精馏塔再沸器使用汽相中和塔中和得到的汽相作为热源,中间加热器使用出料废水作为热源,因此装置正常运行时完全不需要消耗生蒸汽,大大降低了工艺能耗,达到了节能降耗的目的;(2)使用压缩机对轻组分进行加压,提高了轻组分的冷凝温度,使得预精馏塔和轻组分精制塔的塔顶出料能够使用冷却水进行冷却,避免使用成本更高的冷冻盐水,降低了生产成本,提高了工艺的经济性;(3)本发明的草甘膦溶剂及副产物回收方法对各组分的分离能力较强,溶剂甲醇以及副产物甲缩醛和氯甲烷的回收率高、纯度高、质量好;(4)汽相中和塔、预精馏塔、甲醇精制塔均在常压或负压条件下操作,避免了原料中盐碱等不挥发杂质对设备的腐蚀,降低了对设备材质的耐腐蚀要求,从而节约了设备投资。附图说明为了使本发明的目的、技术方案和有益效果更加清楚,本发明提供如下附图进行说明:图1为草甘膦溶剂及副产物回收工艺流程示意图。图2为草甘膦溶剂及副产物回收优选工艺流程示意图。图3为草甘膦溶剂及副产物回收最优选工艺流程示意图。1-汽相中和塔;2-预精馏塔;3-轻组分精制塔;4-甲醇精制塔;5-预精馏塔再沸器;6-压缩机ⅰ;7-预精馏塔冷凝器;8-压缩机ⅱ;9-加压泵;10-轻组分冷却器;11-轻组分精制塔冷凝器;12-轻组分精制塔再沸器;13-中间缓冲罐;14-中间加热器;15-甲醇压缩机;16-甲醇精制塔再沸器;17-甲醇凝液收集罐;18-二级甲醇压缩机;19-三级甲醇压缩机;20-中间再沸器。具体实施方式下面将结合附图,对本发明的优选实施例进行详细的描述。实施例1本发明提供了一种用于草甘膦溶剂及副产物回收的方法,具有很好的节能降耗效果,草甘膦溶剂及副产物回收率高,产品质量高,应用前景广,具体工艺路线如图1所示,具体方法如下:将草甘膦生产过程中水解产生的蒸汽通入汽相中和塔1,使用碱液进行中和,中和得到的汽相为预精馏塔再沸器5供热后通入预精馏塔2中,中和得到的液相一部分循环回汽相中和塔1,一部分通入预精馏塔2;通入的汽相和液相在预精馏塔2塔顶得到含有甲缩醛和氯甲烷的轻组分,塔底得到含有甲醇、水和重组分的混合物,得到的含有甲缩醛和氯甲烷的轻组分经压缩机ⅰ6压缩后通入预精馏塔冷凝器7进行部分冷凝,部分冷凝得到的汽相经压缩机ⅱ8通入轻组分冷却器10,部分冷凝得到的液相经加压泵9加压后通入轻组分冷却器10,再由轻组分冷却器10通入轻组分精制塔3;将通入轻组分精制塔3的含有甲缩醛和氯甲烷的轻组分经过精馏处理,塔顶得到氯甲烷产品,塔底得到甲缩醛产品;过程中用压缩机ⅰ6和压缩机ⅱ8对轻组分蒸汽进行加压,其目的是提高其冷凝温度,使轻组分能够用循环水冷却、避免使用成本更高的冷冻盐水;含有甲醇、水和重组分的混合物通入甲醇精制塔4,为避免汽相进料波动对甲醇精制塔4热泵系统的稳定操作造成影响,在甲醇精制塔4前设置一个中间缓冲罐13。中间缓冲罐13中的物料通过中间加热器14加热后再通入甲醇精制塔4,精馏处理后,塔底得到含重组分的水,塔顶得到精甲醇蒸汽,得到的甲醇蒸汽经甲醇压缩机15加压提高能量品位后用作轻组分精制塔再沸器12和甲醇精制塔再沸器16的热源,换热冷凝后用甲醇凝液收集罐17收集得到精甲醇产品。为充分利用流股热量,使用出料废水作为中间加热器14的热源,使用加压后的甲醇作为中间加热器14的补充热源。本发明中,草甘膦生产过程中水解产生的蒸汽各组分含量如下:质量含量为20%~60%的甲醇,5%~30%的氯甲烷,1%~20%的甲缩醛,20%~45%的水以及少量氯化氢、空气、二甲醚等杂质。汽相中和塔1为常压操作,操作温度为40~90℃。预精馏塔2操作压力为0.07~0.1mpa(绝压),塔顶回流比选择范围为0.3~2。轻组分精制塔3操作压力为0.75~1.1mpa(绝压),塔顶回流比选择范围为0.8~3。甲醇精制塔4为常压操作,塔顶回流比选择范围为0.5~2.5。压缩机所需动力可由变频电机提供,也可由背压式汽轮机提供,汽轮机排出的背压蒸汽可用作各精馏塔再沸器的补充热源,也可作为中间加热器的供热介质,使工艺流程更节能。采用该方法氯甲烷产品中氯甲烷质量含量达到85%以上,其余成分主要为氮、氧等;甲缩醛产品中甲缩醛质量含量达到85%以上,其余成分主要为甲醇,达到市售商品含量要求;甲醇产品中甲醇质量含量达到99.7%以上;甲醇精制塔塔底出料中水的质量含量大于98.5%,其余成分主要为中和产物盐类即碱金属的氯化物,有机物含量低于0.1%;整个草甘膦溶剂及副产物回收工艺,精甲醇回收率≥96.9%,总甲醇回收率≥99.9%,甲缩醛回收率≥99.9%,氯甲烷的回收率≥99.9%。实施例2实施例2为实施例1的优选方案,甲醇压缩机采用二级压缩方案,能进一步降低工艺能耗,具体工艺如图2所示,其工艺与实施例1相同,区别是甲醇精制塔4的塔顶蒸汽经甲醇压缩机15一级压缩提高能量品位后一部分用作甲醇精制塔再沸器16的热源,另一部分经二级甲醇压缩机18压缩后用作轻组分精制塔再沸器12的热源。由于轻组分精制塔3的塔釜温度高于甲醇精制塔4的塔釜温度,因此在实施例1的一级压缩方案中,需将所有甲醇精制塔4塔顶甲醇蒸汽加压提高品位至能够为轻组分精制塔再沸器12供热的程度。而本实施例由于采用甲醇二级压缩方案,为甲醇精制塔再沸器16供热的这部分蒸汽不需要加压提高品位至能够为轻组分精制塔再沸器12供热的程度,甲醇压缩机15可设置相对低的出口压力,与实施例1的方案相比,减少了压缩这部分蒸汽需要消耗的电能,达到降低工艺能耗的目的。本实施例中,原料进料流量为15000kg/hr,组成见表1所示,碱液为质量分数为30%的氢氧化钠水溶液,流量为70kg/hr。各精馏塔的操作参数见表2,甲醇压缩机采用电驱动、二级压缩方案,得到产品组成见表3、表4、表5。表1、原料组成(质量分率,%)甲醇水甲缩醛氯甲烷氯化氢氧氮二甲醚0.4250.3680.09110.09930.001270.003010.009970.00235表2、各精馏塔操作参数表3、甲醇产品组成(质量分率,%)甲醇水甲缩醛氯甲烷二甲醚≥0.99977ppm7ppm痕量痕量表4、甲缩醛产品组成(质量分率,%)甲缩醛甲醇水氯甲烷二甲醚≥0.8500.1490.000127痕量痕量表5、氯甲烷产品组成(质量分率,%)氯甲烷氧氮二甲醚甲醇水甲缩醛0.8690.02570.08510.020167ppm20ppm13ppm将本实施例的能耗数据与现有工艺进行对比,包括加热汽耗、冷却水耗、冷冻水耗、压缩机电耗及由此计算得到的能源单耗折合标煤,结果如表6所示。表6、能耗对比由表6可知,本实施例的工艺与现有工艺相比可节能61.2%以上。实施例3实施例3为实施例1的优选方案,能进一步降低工艺能耗,具体工艺如图3所示,其工艺与实施例1相同,区别在于为甲醇精制塔4增加一个中间再沸器20,甲醇压缩机采用三级压缩方案,具体为:甲醇精制塔4的塔顶蒸汽经甲醇压缩机15一级压缩提高能量品位后一部分用作中间再沸器20的热源,另一部分进入二级甲醇压缩机18,经压缩提高品位后一部分用作甲醇精制塔再沸器16的热源,另一部分经三级甲醇压缩机19压缩后用作轻组分精制塔再沸器12的热源。由于甲醇精制塔4的温度分布是从塔底到塔顶逐渐降低的,且塔底和塔顶的温差较大,设置中间再沸器20,可分担部分甲醇精制塔再沸器16的热负荷,而中间再沸器20可用较低品位的热源加热,因此可相应降低甲醇压缩机15的出口压力,减少甲醇压缩机15的电耗。而二级甲醇压缩机18的压缩目的是为甲醇精制塔再沸器供热,因此同样也可相应降低二级甲醇压缩机18的出口压力,减少二级甲醇压缩机18的电耗。最终仅有一部分的甲醇蒸汽需要加压提高品位至能够为轻组分精制塔再沸器12供热的程度。因此本实施例的方案在实施例2方案的基础上,更进一步降低了工艺能耗,达到了更优的节能降耗效果。本实施例中,原料进料流量为8000kg/hr,组成见表7,碱液为32%的氢氧化钠水溶液,流量为69kg/hr;各精馏塔的操作参数见表8,甲醇压缩机采用电驱动、三级压缩方案,得到产品组成见表9、表10、表11。表7、原料组成(质量分率,%)甲醇水甲缩醛氯甲烷氯化氢氧氮二甲醚0.4080.3820.1030.08820.002500.003150.01050.00265表8、各精馏塔操作参数精馏塔名称塔顶压/kpa塔压降/kpa回流比预精馏塔85100.5轻组分精制塔1100201.7甲醇精制塔102101.0表9、甲醇产品组成(质量分率,%)甲醇水甲缩醛氯甲烷二甲醚≥0.9980.001705ppm痕量痕量表10、甲缩醛产品组成(质量分率,%)甲缩醛甲醇水氯甲烷二甲醚0.8520.1470.00095619ppm25ppm表11、氯甲烷产品组成(质量分率,%)氯甲烷氧氮二甲醚甲醇水甲缩醛0.8620.02700.08860.022355ppm9ppm36ppm将本实施例的能耗数据与现有工艺进行对比,包括加热汽耗、冷却水耗、冷冻水耗、压缩机电耗及由此计算得到的能源单耗折合标煤,结果如表12所示。表12、能耗对比由表12可知,本实施例的工艺与现有工艺相比可节能68.0%以上。综上所述,使用本发明的方法回收草甘膦溶剂及副产物,具有很好的节能效果,因此可以用于工业化生产草甘膦中溶剂和副产物的回收。最后说明的是,以上优选实施例仅用以说明本发明的技术方案而非限制,尽管通过上述优选实施例已经对本发明进行了详细的描述,但本领域技术人员应当理解,可以在形式上和细节上对其作出各种各样的改变,而不偏离本发明权利要求书所限定的范围。当前第1页12