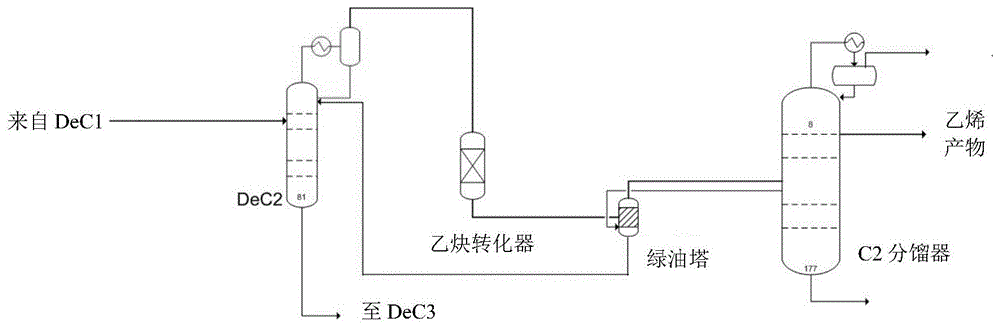
本申请要求于2017年06月08日提交的韩国专利申请no.10-2017-0071315的优先权的权益,该申请的全部公开内容通过引用并入本说明书中。本发明涉及一种从包含乙炔、乙烷、乙烯和c3+的混合物中分离乙烯的工艺,更具体地,涉及一种具有提高的工艺效率的乙烯分离工艺。
背景技术:
:乙烯是用于制造各种化学物质的原料,并且在工业上通过在存在蒸汽的裂化炉中烃的热解来生产。通常将含有各种成分的裂化炉流出流净化、干燥以除去水、压缩并且通过烯烃回收区以从其它轻质烃如乙烷、丙烯、丙烷等中分离乙烯。从裂化炉流出物中分离混合物的顺序可以由脱甲烷塔(dec1)、脱乙烷塔(dec2)或脱丙烷塔(dec3)开始。例如,在脱甲烷塔第一分馏工艺中,将来自裂化炉的流出物冷却,挤出,然后引入到脱甲烷塔中以除去甲烷和轻质化合物。将脱甲烷塔的底部流出物进料至脱乙烷塔。脱乙烷塔将脱甲烷塔的底部流出物分离为含有从脱乙烷塔的顶部作为蒸汽流出的c2和轻质化合物的馏分,和含有从脱乙烷塔的底部流出的重质化合物的馏分。处理脱乙烷塔的底部来分离重质化合物。可以将塔顶c2输送至乙炔转化器(ac转化器)以将乙炔转化为乙烷和乙烯,或者输送至乙炔回收单元以从乙烷和乙烯中分离乙炔。可以将反应器或回收单元的流出物进料至c2分离器(c2分流器或c2分馏器)并且分离为乙烯和乙烷。做了许多努力来提高c2分离器中的乙烯产量。然而,存在由于现有设备的限制而经常存在制约,并且改变现有设备的成本高的问题。例如,在乙炔转化器位于脱甲烷塔的上游的情况下,使用通过在脱乙烷塔上提供第二脱乙烷塔来将含有较高纯度的乙烯的流出物供应至乙烯分离器的高级dec2工艺。然而,该工艺存在的问题在于难以使用,因为在乙炔转化器设置在脱乙烷塔的下游的情况下,乙炔转化器不能从乙烯产物中分离乙炔。技术实现要素:技术问题本发明的一个目的是提供一种乙烯分离工艺,该工艺可以在乙炔转化器位于脱乙烷塔的下游的工艺中在不改变现有设备的情况下经济地提高乙烯产量。技术方案为了解决上述技术问题,本发明提供一种从包含乙炔、包含乙烷和乙烯的c2流和包含丙烯的c3流的原料流中分离乙烯的工艺,该分离乙烯的工艺包括以下步骤:将包含c2流和c3流的原料流进料至第一脱乙烷塔(dec2)中,以在第一脱乙烷塔的顶部排出第一c2流并且在底部排出c3流;将在脱乙烷塔的顶部排出的第一c2流的一部分进料至第二脱乙烷塔中,以排出第二c2流;将第二脱乙烷塔的底部物流再次引入到所述第一脱乙烷塔中,以充当所述第一脱乙烷塔的回流;将所述第二c2流供应至第一乙炔转化器中,以将所述第二c2流中含有的乙炔转化为乙烯并且排出第一乙烯流;将在脱乙烷塔的顶部排出的第一c2流的其余物流供应至第二乙炔转化器中,以将所述第一c2流中含有的乙炔转化为乙烯并且排出第二乙烯流;和将所述第一乙烯流和所述第二乙烯流进料至乙烯分离塔中以得到乙烯。根据一个实施方案,所述第一乙烯流可以进料至乙烯分离塔的中间,所述第二乙烯流可以进料至所述乙烯分离塔的底部。根据一个实施方案,所述第一脱乙烷塔的顶部的回流比可以与不存在所述第二脱乙烷塔的回流比相同。根据一个实施方案,在所述第一脱乙烷塔的顶部排出的第一c2流的乙烯纯度可以为65%至85%。根据一个实施方案,从所述第二脱乙烷塔排出的第二c2流的乙烯纯度为96%至99%,并且通过第一乙炔转化器之后的所述第一乙烯流的乙烯纯度可以为97%以上。根据一个实施方案,通过第二乙炔转化器之后的所述第二乙烯流的乙烯纯度可以为65%至85%。根据一个实施方案,所述第二脱乙烷塔可以具有30至100之间的塔板数。根据一个实施方案,所述乙烯分离塔可以具有150至200之间的塔板数,其中,可以将所述第一乙烯流进料至所述乙烯分离塔的塔板50至塔板110之间,并且可以将第二乙烯流进料至比第一乙烯流低30至100的塔板中。根据一个实施方案,与不存在所述第二脱乙烷塔的回流比相比,乙烯分离塔的顶部的回流比可以降低。有益效果本发明提供一种通过在常规脱乙烷塔上添加第二脱乙烷塔和乙炔转化器,通过乙烯预分离工艺而得到的效果,并且通过将得到的具有99%以上的高纯度的第一乙烯流进料至乙烯分离塔的中间,而能够提高每单位体积的乙烯产量。本发明可以应用于乙炔转化器位于脱乙烷塔的下游的任意设备,使得可以经济地提高乙烯的产量。附图说明图1是乙炔转化器位于脱乙烷塔的下游的常规脱乙烷和乙烯分离工艺的示意性工艺流程图;图2是根据本发明的乙烯分离工艺的示意性工艺流程图;图3是根据常规工艺(基本)的dec2工艺的流程图;图4是根据本发明的一个实施方案的在乙烯分离塔的上游添加高级dec2工艺的工艺的流程图(预分离);图5比较了根据比较例(基本)和实施例(预分离)的工艺的液体载荷;图6是根据本发明的一个实施方案的在脱乙烷塔上具有第二脱乙烷塔的工艺(高级dec2)的工艺流程图;图7示出了在根据图6的工艺中高级dec2流的根据流速的乙烯纯度;图8是根据本发明的一个实施方案的将99%的乙烯引入到乙烯分离塔中的工艺的流程图;图9示出了在根据图8的工艺中乙烯分离塔的根据99%的乙烯的进料量的回流速率和回流比;图10是示出根据本发明的实施方案的工艺中的通过进料塔板数的回流速率,和经过乙炔转化器之后的预期乙烯组成的图。具体实施方式如本文中所使用,“c#烃”或“c#”(其中,#是正整数)意在描述具有#个碳原子的所有烃。此外,术语“c#+烃”或“c#+”意在描述碳数大于或等于#的所有烃分子。例如,术语“c3+烃”或“c3+”意在描述具有三个以上碳原子的烃的混合物。因此,术语“c3+烷烃”是指具有三个以上碳原子的烷烃。因此,术语“c#减号烃”或“c#减号”意在描述含有氢与多达#个碳原子的烃的混合物。例如,术语“c2-”或“c2减号”是指乙烷、乙烯、乙炔、甲烷和氢气的混合物。在本发明中,提供乙烯分离工艺,其中,在脱乙烷塔(dec2)的下游设置乙炔转化器,并且在脱乙烷塔上进一步设置第二脱乙烷塔(高级dec2)和乙炔转化器,以通过预分馏塔的效果提高乙烯产量。根据本发明的乙烯分离工艺是用于从包含含有乙炔、乙烷和乙烯的c2流和含有丙烯的c3流的原料流分离乙烯的工艺,该分离乙烯的工艺包括以下步骤:将包含c2流和c3流的原料流进料至第一脱乙烷塔(dec2)中,以在第一脱乙烷塔的顶部排出第一c2流并且在底部排出c3流;将在脱乙烷塔的顶部排出的第一c2流的一部分进料至第二脱乙烷塔中,以排出第二c2流;将所述第二c2流供应至第一乙炔转化器中,以将第二c2流中含有的乙炔转化为乙烯并且排出第一乙烯流;将在所述脱乙烷塔的顶部排出的第一c2流的其余物流供应至第二乙炔转化器中,以将第一c2流中含有的乙炔转化为乙烯并且排出第二乙烯流;和将所述第一乙烯流和所述第二乙烯流进料至乙烯分离塔中以得到乙烯。在本发明中,在第一脱乙烷塔的下游另外设置第二脱乙烷塔来产生高纯乙烯流,并且将高纯乙烯流引入到乙烯分离塔的中间来进一步提高乙烯产量。使用另外设置的第二脱乙烷塔的脱乙烷工艺充当乙烯流的预分馏步骤,使得与常规乙烯分离工艺相比,每单位体积的乙烯产量可以增加。根据一个实施方案,第一乙烯流可以进料至乙烯分离塔的中间,第二乙烯流可以进料至乙烯分离塔的底部。根据一个实施方案,第一脱乙烷塔的顶部的回流比可以与不存在第二脱乙烷塔的回流比相同。根据一个实施方案,在第一脱乙烷塔的顶部排出的第一c2流的乙烯纯度可以为65%至85%,优选为80%至85%。根据一个实施方案,从第二脱乙烷塔排出的第二c2流的乙烯纯度为96%至99%,并且通过第一乙炔转化器之后的第一乙烯流的乙烯纯度可以为97%以上。第二c2流的乙烯纯度远高于第一c2流的乙烯纯度。根据一个实施方案,通过第二乙炔转化器之后的第二乙烯流的乙烯纯度可以为65%至85%。根据一个实施方案,第二脱乙烷塔可以具有30至100,优选地为30至80,更优选地为30至60之间的塔板数。具有上述塔板数,可以使高纯第一乙烯流的效率最大化。根据一个实施方案,乙烯分离塔可以具有150至200之间的塔板数,其中,可以将第一乙烯流进料至乙烯分离塔的塔板50至塔板110,优选地为塔板80至塔板110,更优选地为塔板90至塔板105之间,并且可以将第二乙烯流进料至比第一乙烯流低30至100的塔板中。通过上述塔板数,可以使高纯第一乙烯流的效率最大化。根据一个实施方案,与不存在第二脱乙烷塔的回流比相比,乙烯分离塔的顶部的回流比可以降低。因此,可以提高每单位体积的乙烯产率。乙炔转化器使得c2流中含有的乙炔能够与氢气接触,引起乙炔向乙烯的转化。因此,乙烯流形成贫乙炔流或基本无乙炔流。根据一个实施方案,所述原料流可以是由脱丙烷塔、脱甲烷塔、脱丁烷塔或脱甲烷塔的汽提塔得到的产物流、裂化炉流出物、催化反应器流出物或它们的组合。第一脱乙烷塔、第二脱乙烷塔和乙烯分离塔可以配备有冷凝器,并且该冷凝器可以冷凝并且收集分离的乙烯流。如本文中所使用的乙烯分离塔包括“精馏器”,它指包括多个塔板的分馏蒸馏区。该区使得来自原料流的蒸汽能够与乙烷相对贫的液体接触,导致上部乙烯流贫乙烷,并且不为来自由进料塔板收集的液体的乙烯提供再沸或汽提。乙烯分离塔的底部可以进料,根据需要,在热交换器中加热或冷却的具有相对低纯度的乙烯的第二乙烯流。本发明还提供一种乙烯分离系统,用于从包含乙炔、包含乙烷和乙烯的c2流和包含丙烯的c3流的原料流分离乙烯。根据本发明的乙烯分离系统包括:第一脱乙烷塔(dec2)塔,在其中进料c2流和c3流,并且在顶部排出c2流并且在底部排出c3流;设置在所述第一脱乙烷塔上的第二脱乙烷塔(高级dec2)塔,用于从第一脱乙烷塔排出的第一c2流的一部分进一步除去乙烷;第一乙炔转化器,用于将从第二脱乙烷塔排出的第二c2流中含有的乙炔转化为乙烯以除去乙炔;第二乙炔转化器,用于将除了进料至第二脱乙烷塔中的第一c2流之外的其余的第一c2流中含有的乙炔转化为乙烯以除去乙炔;和乙烯分离塔,向其中进料第一乙烯流和第二乙烯流以分离乙烯。根据一个实施方案,从第一乙炔转化器排出的高纯第一乙烯流可以进料至乙烯分离塔的中间。根据一个实施方案,从第二乙炔转化器排出的低纯第二乙烯流可以进料至乙烯分离塔的底部。第二乙烯流可以进料至比第一乙烯流低30至100的塔板中。通过上述塔板数,可以使高纯第一乙烯流的效率最大化。下文中,将详细描述本发明的实施例,使得本领域技术人员可以容易地实施本发明。然而,本发明可以以许多不同的形式实施,并且不应理解为局限于本文中阐述的实施方案。下文中,缩写和符号表示以下内容。da401:第一脱乙烷塔da412/1412:乙烯分离塔da403:脱甲烷塔<比较例1和实施例1>图3和图4分别示出了常规dec2工艺(比较例)和根据本发明的高级dec2工艺(实施例)。每个图中的物流中所示的四个数字表示温度(℃)、压力(kg/cm2g)、流速(kg/hr)和从顶部至底部的气体分数。工艺操作条件如下。进料性能:100%的气体第一脱乙烷塔的塔板数:81塔板第二脱乙烷塔的塔板数:50塔板(仅例示)乙烯分离塔的塔板数:215塔板(da1412100塔板/da412115塔板)第一乙烯流的纯度和进料塔板:99%,塔板100(仅例示)第二乙烯流的纯度和进料塔板:-比较例:82%,塔板151-实施例:80%,塔板151在表1中比较根据比较例和实施例的工艺的产量、回流、冷凝器和再沸器的负荷,以及乙烯分离塔的液体载荷。[表1]项目比较例(基本)实施例(预分离)原料总量59.1ton/hr17.3+41.8=59.1ton/hr产量48.4ton/hr50.7ton/hr回流速率174.3ton/hr157.7ton/hr冷凝器的负荷15.048gcal/hr13.508gcal/hrda412液体载荷133.5ton/hr108.3ton/hr如表1中所示,在包括使用第二脱乙烷塔的预分离工艺的情况下,显而易见的是,液体载荷降低,这在图5中更详细地示出。在根据本发明的工艺中,塔板10至塔板100的范围内的液体载荷减少21.5ton/hr,塔板101以下的液体载荷也减少25.2ton/hr,引起6ton/hr的乙烯的附加产量。在根据本发明的工艺中,回流比(rr)从3.597降低至3.114,回流速率降低18.4ton/hr,冷凝器负荷总共降低1.9gcal/hr,并且再沸器负荷总共降低2.02gcal/hr。可以确认,通过包括使用第二脱乙烷塔的预分离工艺,分离工艺所需要的能量降低。<实施例2:根据原料流速的乙烯纯度>图7示出了当在图6中所示的操作条件下操作时,根据第二脱乙烷塔的流速的乙烯纯度。由于所述工艺用于通过乙炔转化器之前的乙烯纯度,因此,乙炔存在于物流中。因此,乙烯的纯度表现出98.9%的极限,并且直至排出17ton/hr的乙烯,组成才改变。<实施例3:根据高纯乙烯流的进料量的回流速率和回流比>上文中,可以确认,通过根据本发明的使用第二脱乙烷塔的预分馏可以得到约99%的乙烯流。根据99%的乙烯流的进料量测量乙烯分离塔的回流速率和回流比的变化。如图8中所示,将99%的乙烯流直接进料至da402(乙烯分离塔)的塔板40。在改变乙烯流的进料量的同时测量回流速率和rr(回流比)的变化。结果示于图9和表2中。[表2]99%c2-回流速率rr产量冷凝器负荷再沸器负荷03473874.027586253-29.3910.401000349410.54.005387237.92-29.5610.492000351467.73.983988222.58-29.7410.593000353559.83.963489207.13-29.9110.6850003578553.924991175.86-30.2810.886000360061.23.906992160.04-30.4610.987000362308.43.889893144.1-30.6511.098000364598.23.873494128.03-30.8511.209000366932.23.857995111.83-31.0411.3210000369311.93.843296095.5-31.2411.4412000374214.43.816198062.45-31.6611.6913000376740.13.803799045.73-31.8711.8215000381946.63.7812101011.9-32.3112.1016000384629.83.7711101994.8-32.5412.2417000387367.43.7617102977.6-32.7712.3918000390160.33.7530103960.3-33.0112.55190003930093.7450104942.9-33.2512.7020000395913.73.7377105925.3-33.4912.8721000398874.83.7310106907.7-33.7413.04220004018923.7250107890-34.0013.2123000404964.93.7196108872.2-34.2613.39240004080933.7149109854.3-34.5213.5725000411275.53.7107110836.4-34.7913.7626000414511.23.7070111818.5-35.0613.9527000417798.93.7039112800.4-35.3414.1528000421137.13.7012113782.4-35.6214.3529000424524.23.6991114764.4-35.9114.5530000427958.23.6974115746.3-36.2014.7631000431437.33.6961116728.3-36.4914.9732000434959.33.6952117710.2-36.7915.1933000438522.23.6946118692.2-37.0915.4134000442123.73.6944119674.3-37.4015.63结果示出,随着高纯乙烯流增加,回流速率增加并且rr降低。可以示出,回流速率与进料量成比例地增加,并且rr(=l/d)可以表达为回流速率/产物量。随着回流速率增加,产物量增加。随着乙烯的量增加,rr降低,因为产物量的增量大于回流速率的增量。<实施例4:乙烯分离塔根据进料塔板的效果>在将通过第一乙炔转化器之后的第一乙烯流进料至乙烯分离塔的步骤中,检查乙烯分离塔根据进料塔板的效果。图10示出了根据进料塔板的回流速率和回流比。经过乙炔转化器之前的乙烯流的组成为98.9%。经过乙炔转化器之后的第一乙烯原料流的预期组成为99.4%,并且根据乙炔转化器的反应可以确定为99.0%至99.7%。参照图10的曲线图,可以看出,考虑到乙烯流的组成可以高于99.4%和回流模式改变的可能性,在80与100之间的进料塔板具有最高的预分离效果。如果进料塔板高于塔板80,则在塔顶产生的乙烯产物的为99.96%的纯度会受到不利影响,如果进料塔板低于塔板100,则乙烯在塔底部泄漏的可能性增加,这会导致回流速率增加,产量减少并且能源效率降低。虽然已经参照附图和实施方案具体示出并描述了本发明,但是本领域普通技术人员应当理解的是,本发明的范围不受其限制,并且可以在其中进行各种改变和修改。因此,本发明的实际范围将由所附权利要求书及其等同物限定。当前第1页12