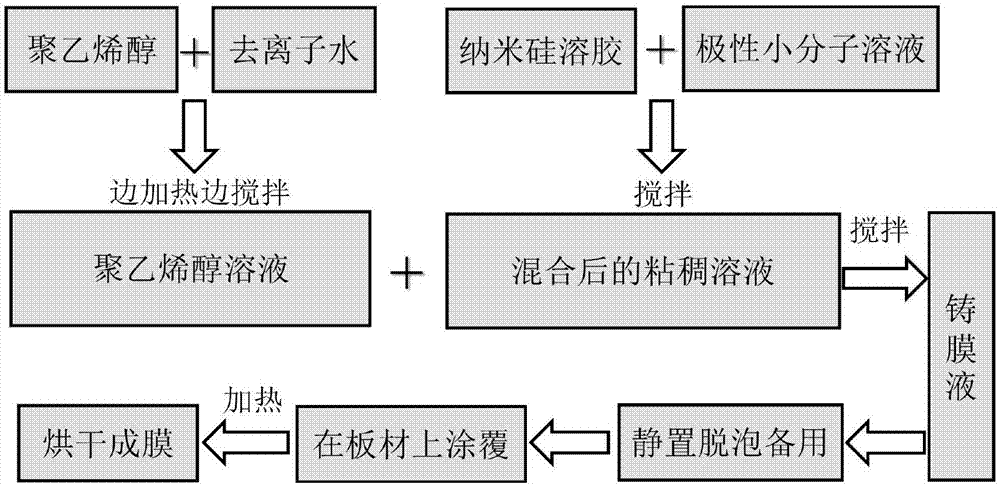
本发明属于高分子膜化学改性技术领域,特别涉及一种基于纳米硅溶胶延缓小分子析出的聚乙烯醇膜制备方法。
背景技术
聚乙烯醇是一种具有优良的机械、物理和化学性能的水溶性聚合物,其在薄膜材料中占有非常重要的地位。在聚乙烯醇膜制品中常需要添加无机小分子以改善其性能,如山梨醇、尿素、乙酰胺等增塑剂,用以提高聚乙烯醇膜的柔韧性、弹性及耐低温等性能,如氯化锂、氯化钙等极性小分子,用以提高聚乙烯醇的吸/脱附性能。但在长期使用过程中,聚乙烯醇膜中的小分子因不断向周围环境迁移而使制品性能变差,从而严重影响制品的使用性能与寿命。
为了抑制聚乙烯醇膜中小分子的迁移,通常需要对其进行表面处理,如采用电子束发射、低温等离子辐射、紫外线照射等。但上述方法的制备工艺相当复杂、且成本较高,限制了它们的应用。近年来,随着纳米技术的研究与发展,为抑制聚乙烯醇膜中极性小分子的迁移问题提供了一种新的思路与方法。本发明提出了一种基于纳米硅溶胶延缓小分子析出的聚乙烯醇膜制备方法,利用纳米粒子表面原子与极性小分子的强作用力,实现抑制小分子向聚乙烯醇膜表面迁移的目的。
与现有技术相比,本发明具有以下优点:本发明可改善聚乙烯醇膜中极性小分子的析出现象,且成本低、简单易操作。
技术实现要素:
本发明提出一种基于纳米硅溶胶延缓小分子析出的聚乙烯醇膜制备方法。纳米硅溶胶中纳米粒子表面的原子具有较高的活性及不稳定性,容易与极性小分子产生较强的作用力;此外,纳米粒子在聚合物中是相对稳定的。因此,纳米硅溶胶能抑制极性小分子向聚乙烯醇膜表面迁移。
本发明是通过以下技术方案实现的,具体操作步骤为:
步骤一,将聚乙烯醇分散于去离子水中,并在去离子水中添加消泡剂,充分搅拌制成聚乙烯醇溶液;
步骤二,将极性小分子分散于去离子水中,制得极性小分子溶液;
步骤三,将步骤二制成的极性小分子溶液与纳米硅溶胶混合,充分搅拌制成粘稠的溶液;
步骤四,将步骤三制成的粘稠溶液加入聚乙烯醇溶液中,充分搅拌制成铸膜液;
步骤五,将步骤四制成的铸膜液静置脱泡;
步骤六,将步骤五脱泡后的铸膜液平铺于板材上,并置于烘箱中加热促使铸膜液中的水分蒸发,制备成聚乙烯醇膜。
进一步地,步骤一中所述聚乙烯醇溶解是指在96-100℃条件下搅拌聚乙烯醇与去离子水的混合溶液,直至聚乙烯醇全部溶解为止;所述消泡剂是指有机硅消泡剂、聚醚消泡剂、矿物油消泡剂中的任意一种或几种。
进一步地,步骤二中所述极性小分子是指氯化锂、氯化钙中的任意一种或几种。
进一步地,步骤三中所述纳米硅溶胶是指浓度为20%-40%的粒径为10-20nm的硅溶胶;所述充分搅拌制成粘稠的溶液是指在室温条件下搅拌1-5min,直至溶液变得粘稠,停止搅拌。
进一步地,步骤四中所述将纳米硅溶胶和极性小分子制成的粘稠溶液加入聚乙烯醇溶液中是为了使纳米硅溶胶与极性小分子先反应,这样才能起到限制极性小分子在聚乙烯醇膜中迁移的作用;所述充分搅拌制成铸膜液是指在室温条件下搅拌,时间为10-30min;所述铸膜液的原料,按重量份数计,去离子水含量为110份,聚乙烯醇含量为10-12份,极性小分子含量为1-3份、纳米硅溶胶含量为10-30份。
进一步地,步骤五中所述静置脱泡是指在将铸膜液放置于室温条件下5-10h。
进一步地,步骤六中所述烘箱中加热是指烘箱的温度设为40-70℃,加热持续时间为8-16h。
相比于现有技术,本发明的有益效果为:本发明利用纳米粒子表面原子与极性小分子的强作用力,实现抑制小分子向聚乙烯醇膜表面迁移的目的,可改善聚乙烯醇膜中极性小分子的析出现象,且成本低、简单易操作。
附图说明
图1基于纳米硅溶胶延缓小分子析出的聚乙烯醇膜制备方法的工艺流程图;
图2是实施例1制备的聚乙烯醇膜放置于室内三个月后的实物图;
图3是对比例1制备的聚乙烯醇膜放置于室内三个月后的实物图;
图4是对比例2制备的聚乙烯醇膜放置于室内三个月后的实物图。
具体实施方式
下面列出本发明的具体实施方案,但本发明的保护范围不限于所列出的实施方案。
实施例1
(1)取100g去离子水,将10g聚乙烯醇分散于去离子水中,并在去离子水中添加3滴有机硅消泡剂,在96℃的条件下采用搅拌器搅拌,直至聚乙烯醇完全溶解,得聚乙烯醇溶液;
(2)将1g氯化锂分散于10g去离子水中,制得氯化锂溶液;
(3)将步骤(2)的氯化锂溶液与10g浓度为20%的纳米硅溶胶混合,在室温条件下搅拌1min,制得粘稠溶液;
(4)将步骤(3)制得的粘稠溶液加入到步骤(1)制得的聚乙烯醇溶液中,在室温条件下搅拌10min制成铸膜液;
(5)将步骤(4)的铸膜液置于室温条件下5h脱泡备用;
(6)将步骤(5)脱泡后的铸膜液涂覆于板材上,之后,将板材置于温度设为40℃的烘箱中16h,促使铸膜液中的水分蒸发,制备成膜。
将实施例1的聚乙烯醇膜置于室内,经观察,三个月后未发现膜表面有白色物质,如附图2所示,表明聚乙烯醇膜的稳定性较好,氯化锂小分子未析出。
实施例2
(1)取100g去离子水,将11g聚乙烯醇分散于去离子水中,并在去离子水中添加4滴聚醚型消泡剂,在98℃的条件下采用搅拌器搅拌,直至聚乙烯醇完全溶解,得聚乙烯醇溶液;
(2)将2g氯化锂分散于10g去离子水中,制得氯化锂溶液;
(3)将步骤(2)的氯化锂溶液与20g浓度为30%的纳米硅溶胶混合,在室温条件下搅拌3min,制得粘稠溶液;
(4)将步骤(3)制得的粘稠溶液加入到步骤(1)制得的聚乙烯醇溶液中,在室温条件下搅拌20min制成铸膜液;
(5)将步骤(4)的铸膜液置于室温条件下7.5h脱泡备用;
(6)将步骤(5)脱泡后的铸膜液涂覆于板材上,之后,将板材置于温度设为55℃的烘箱中12h,促使铸膜液中的水分蒸发,制备成膜。
将实施例2的聚乙烯醇膜置于室内,经观察,三个月后未发现膜表面有白色物质,表明聚乙烯醇膜的稳定性较好,氯化锂小分子未析出。
实施例3
(1)取100g去离子水,将12g聚乙烯醇分散于去离子水中,并在去离子水中添加5滴矿物油消泡剂,在100℃的条件下采用搅拌器搅拌,直至聚乙烯醇完全溶解,得聚乙烯醇溶液;
(2)将3g氯化钙分散于10g去离子水中,制得氯化钙溶液;
(3)将步骤(2)的氯化钙溶液与30g浓度为40%的纳米硅溶胶混合,在室温条件下搅拌5min,制得粘稠溶液;
(4)将步骤(3)制得的粘稠溶液加入到步骤(1)制得的聚乙烯醇溶液中,在室温条件下搅拌30min制成铸膜液;
(5)将步骤(4)的铸膜液置于室温条件下10h脱泡备用;
(6)将步骤(5)脱泡后的铸膜液涂覆于板材上,之后,将板材置于温度设为70℃的烘箱中8h,促使铸膜液中的水分蒸发,制备成膜。
将实施例3的聚乙烯醇膜置于室内,经观察,三个月后未发现膜表面有白色物质,表明聚乙烯醇膜的稳定性较好,氯化钙小分子未析出。
对比例1
(1)取100g去离子水,将10g聚乙烯醇分散于去离子水中,并在去离子水中添加3滴有机硅消泡剂,在96℃的条件下采用搅拌器搅拌,直至聚乙烯醇完全溶解,得聚乙烯醇溶液;
(2)将1g氯化锂分散于10g去离子水中,制得氯化锂溶液;
(3)将步骤(2)的氯化锂溶液加入到步骤(1)制得的聚乙烯醇溶液中,在室温条件下搅拌10min制成铸膜液;
(4)将步骤(3)的铸膜液置于室温条件下5h脱泡备用;
(5)将步骤(4)脱泡后的铸膜液涂覆于板材上,之后,将板材置于温度设为40℃的烘箱中16h,促使铸膜液中的水分蒸发,制备成膜。
将对比例1的聚乙烯醇膜置于室内,经观察,三个月后聚乙烯醇膜表面呈现颗粒状白色物质,如附图3所示,表明不含纳米硅溶胶的聚乙烯醇膜的稳定性差,氯化锂小分子易析出。氯化锂小分子的析出,一方面会影响聚乙烯醇膜的表面形貌,另一方面会降低聚乙烯醇膜的吸湿能力。
对比例2
(1)取100g去离子水,将10g聚乙烯醇分散于去离子水中,并在去离子水中添加3滴有机硅消泡剂,在96℃的条件下采用搅拌器搅拌,直至聚乙烯醇完全溶解,得聚乙烯醇溶液;
(2)将1g氯化锂分散于10g去离子水中,制得氯化锂溶液;
(3)将步骤(2)的氯化锂溶液与10g浓度为20%的纳米硅溶胶同时加入到步骤(1)制得的聚乙烯醇溶液中,在室温条件下搅拌10min制成铸膜液;
(4)将步骤(3)的铸膜液置于室温条件下5h脱泡备用;
(5)将步骤(4)脱泡后的铸膜液涂覆于板材上,之后,将板材置于温度设为40℃的烘箱中16h,促使铸膜液中的水分蒸发,制备成膜。
将对比例2的聚乙烯醇膜置于室内,经观察,三个月后聚乙烯醇膜表面呈现少许白色物质。相比于对比例1的聚乙烯醇膜,对比例2的聚乙烯醇膜的氯化锂析出现象有所改善,但抑制氯化锂析出的效果不及实施例1。对比例2达不到本发明的技术要求。
虽然本发明是结合以上方案进行描述的,但本发明并不被限制与上述实施方案,而只受所附权力的限定。其他的任何未背离本发明实质构思下所作的改变、替代、组合、简化,均应为等效的置换方式,都包含在本发明的保护范围之内。