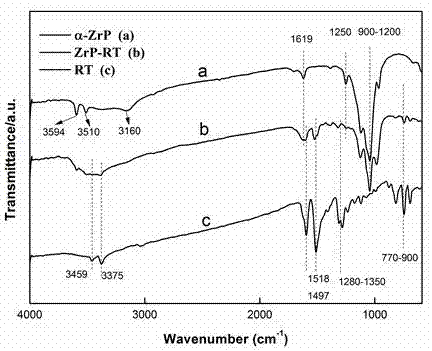
本发明涉及合成橡胶工业
技术领域:
,具体涉及一种基于功能磷酸锆改性的耐老化丁腈橡胶复合材料及制备方法。
背景技术:
:丁腈橡胶制品在运输、存储和使用过程中老化现象普遍,降低了使用寿命,增加了使用成本。丁腈橡胶的老化问题亟待解决,目前通常添加各类橡胶防老剂来改善丁腈橡胶的耐老化性能。但是橡胶防老剂绝大多数都是小分子,在生产和使用过程中容易从橡胶基体内部逸出。一方面使防老效应衰减,另一方面带来了环境污染问题。因此研发一种高效绿色环保的丁腈橡胶防老填料十分必要。针对普通小分子橡胶防老剂容易逸出的问题,已有文献报道了如下改进方法:(1)将小分子橡胶防老剂化学接枝到偶联剂(kh560)上,制备出防老偶联剂,然后将防老偶联剂接枝到无机粒子(纳米二氧化硅)的表面,制备出防老填料并将其添加到橡胶中,在提高橡胶耐老化性的同时抑制了防老剂的逸出。但是此方法工艺复杂,成本较高,不利于工业化生产;(2)将苯胺类橡胶防老剂接枝到碳类材料表面,将接枝改性后的碳类材料添加到橡胶中在提高橡胶耐老化性的同时抑制了防老剂的逸出。但是此方法原料成本高,工艺复杂,产量低,不利于工业化生产。(3)用对苯乙烯磺酸钠对水滑石插层,将插层后的填料加到橡胶中,不仅提高了橡胶的机械性能,耐老化性能也有所改善。但是水滑石的层板间带正电荷不利于具有防老功能的胺类插层改性,且其本身不耐酸,限制了应用领域。α-磷酸锆(α-zrp)是一类典型的层状材料,具有许多优异的性质,如具有大量的酸性羟基和活性位点、层间结构可设计、离子交换性、机械强度高、耐酸碱性、层板结构稳定、比表面积大和电荷密度高。因此,α-zrp有潜力成为一种性价比较高的可用于橡胶改性的填料。已有研究者将磷酸锆用于填充硅橡胶,显著提高了其阻燃性能。但片层间较强的分子间作用力使α-zrp易团聚,因此有必要对α-zrp进行有机功能化改性,减弱其团聚倾向,增加其在橡胶中的分散能力。α-zrp表面大量的酸性羟基和活性位点利于与具有防老功能的胺类物质插层改性。氨类防老剂(如n-苯基对苯二胺(rt))能有效抑制橡胶的热氧老化、臭氧老化和疲劳老化。氨类化合物能水解出带正电的铵根(-nh3+),而α-zrp层板带负电,这使得氨类化合物插层进入α-zrp的层间成为可能。氨类化合物插层能增大磷酸锆的层间距,有利于其在丁腈橡胶中的剥离和分散,形成良好的片层网络,阻碍氧气在基体中的扩散,达到物理防老的目的。此外,通过磷酸锆层板将氨类化合物“锁定”在丁腈橡胶基体内部,减少其逸出,延长化学防老的时间,减少对环境的污染,实现绿色防老。技术实现要素:本发明的目的在于克服现有技术的不足,提供一种基于功能磷酸锆改性的耐老化丁腈橡胶复合材料及制备方法,目的有如下几点:(1)、通过对磷酸锆的插层改性和功能化,可改善磷酸锆在丁腈橡胶基体中的分散程度;(2)、防老功能磷酸锆加入丁腈橡胶,提高机械性能的同时,能从物理防老和化学防老两方面协同提高丁腈橡胶的耐老化性能;(3)、防老功能磷酸锆能将氨类防老剂固定在磷酸锆层间,抑制防老剂溢出丁腈橡胶基体,降低对环境的危害,实现绿色防老。一种基于功能磷酸锆改性的耐老化丁腈橡胶复合材料及制备方法,该复合材料以丁腈橡胶生胶、助剂和防老功能磷酸锆为原料,所述的丁腈橡胶/防老功能磷酸锆复合材料的各组分含量如下:一种基于功能磷酸锆改性的耐老化丁腈橡胶复合材料及制备方法,所述的防老功能磷酸锆为苯胺类(对苯二胺,邻苯二胺,间苯二胺和对氨基二苯胺)、、萘胺类(1-萘胺-5-磺酸,4-硝基-1-萘胺和n-苯基-2-萘胺)化合物对α-磷酸锆(α-zrp)进行有机插层改性的产物。本发明提供的一种基于功能磷酸锆改性的耐老化丁腈橡胶复合材料及制备方法,所述丁腈橡胶生胶中丙烯腈的质量分数为18-46%。本发明提供的一种基于功能磷酸锆改性的耐老化丁腈橡胶复合材料及制备方法,所述的基础丁腈橡胶组分中邻苯二甲酸二辛酯含量为0~7份。本发明提供的一种基于功能磷酸锆改性的耐老化丁腈橡胶复合材料及制备方法,所述的基础丁腈橡胶组分中硬脂酸含量为0~4份。本发明提供的一种基于功能磷酸锆改性的耐老化丁腈橡胶复合材料及制备方法,所述的基础丁腈橡胶组分中氧化锌含量为1~9份。本发明提供的一种基于功能磷酸锆改性的耐老化丁腈橡胶复合材料及制备方法,所述的基础丁腈橡胶组分中促进剂含量为0~3份。本发明提供的一种基于功能磷酸锆改性的耐老化丁腈橡胶复合材料及制备方法,所述的基础丁腈橡胶组分中硫磺含量为0.5~5份。本发明提供的一种基于功能磷酸锆改性的耐老化丁腈橡胶复合材料及制备方法,所述的基础丁腈橡胶组分中防老功能磷酸锆含量为1~50份。本发明提供的一种基于功能磷酸锆改性的耐老化丁腈橡胶复合材料及制备方法,所述的基础丁腈橡胶组分中炭黑的含量为0~60份。工艺步骤如下:丁腈橡胶/防老功能磷酸锆复合材料可用机械或溶液共混制备,具体工艺如下:当采用机械共混法制备丁腈橡胶/防老功能磷酸锆复合材料时,通过机械剪切作用将丁腈橡胶生胶、助剂、防老功能磷酸锆混炼均匀后,用平板硫化机在140~160℃,10~20mpa的条件下对混炼胶硫化30~35分钟;当采用溶液共混法制备丁腈橡胶/防老功能磷酸锆复合材料时,用四氢呋喃(thf)、n,n-二甲基甲酰胺(dmf)、环己烷、丙酮中的一种作为丁腈橡胶生胶的溶剂,称取10~30g丁腈橡胶生胶,配制浓度为0.001~0.005g/ml的丁腈橡胶溶液,橡胶溶解后向其中加入1~50份(每100份丁腈橡胶生胶)防老功能磷酸锆,搅拌混合均匀后,用旋蒸仪及真空干燥箱除去溶剂制得丁腈橡胶/防老功能磷酸锆母胶,然后再通过机械剪切作用,将丁腈橡胶/防老功能磷酸锆母胶、助剂和还需补加的丁腈橡胶生胶混炼均匀,用平板硫化机在140~160℃,10~20mpa的条件下对混炼胶硫化30~35分钟。本发明所述丁腈橡胶/防老功能磷酸锆复合材料制品的加工方法如下:按照上述配方制备出丁腈橡胶/防老功能磷酸锆的混炼胶,然后根据需要,放入不同的模具进行硫化处理,得到不同规格的复合丁腈橡胶制品。在热氧条件下,此复合丁腈橡胶制品相较于普通的丁腈橡胶制品有更长的使用寿命。本发明具有以下有益效果:本发明所述方法选用材料易得,加工设备常规,成本较低,操作简单,便于产业化生产,制备出的丁腈橡胶/防老功能磷酸锆复合材料具有良好的机械性能和耐老化性能。本发明所述丁腈橡胶/防老功能磷酸锆复合材料,在基础丁腈橡胶的配方中添加了防老功能磷酸锆,良好分散的防老功能磷酸锆片层在丁腈橡胶基体中能提高丁腈橡胶的机械性能。并且磷酸锆片层结构在丁腈橡胶基体中能形成气体阻隔网络,有效阻止氧气在丁腈橡胶基体中扩散,从物理阻隔的角度抑制丁腈橡胶的热氧老化。另一方面,防老功能磷酸锆中的防老官能团能捕捉丁腈橡胶老化过程中产生的自由基,从化学防老的角度抑制丁腈橡胶的老化进程。此外,有机防老基团固定在磷酸锆的层间,其热稳定性相对较高,在生产和使用过程中防老基团不容易从橡胶基体内部逸出,防老效应相比普通防老剂更为持久,同时也减少对环境的污染,实现绿色防老。本发明所述橡胶/防老功能磷酸锆复合材料,根据丁腈橡胶制品性能的不同需求调节防老功能磷酸锆的添加量,适用范围广。附图说明:图1为防老功能磷酸锆复合粒子的红外谱图;图2为防老功能磷酸锆复合粒子的x射线衍射谱图;图3为防老功能磷酸锆复合粒子的的热重分析谱图。具体实施方式下面将结合本发明实施例对本发明实施例中的技术方案进行清楚、完整地描述,显然,所描述的实施例仅仅是本发明的一部分实施例,而不是全部的实施例。基于本发明中的实施例,本领域普通技术人员在没有做出创造性劳动前提下所获得的所有其他实施例,都属于本发明保护的范围。其中,所述的丁腈橡胶的氰基含量优选18~46%,更优选为20~45%,再优选为22~43%,最优选为25~40%;所述的丁腈橡胶中硬脂酸加入量优选为0~4份,更优选为1~4份,再优选为1~3份,最优选为1~2份;所述的丁腈橡胶中邻苯二甲酸二辛酯加入量优选为0~7份,更优选为1~6份,再优选为2~5份,最优选为2~4份;所述的丁腈橡胶中氧化锌加入量优选为1~9份,更优选为1~7份,再优选为3~6份,最优选为4~6份;所述的丁腈橡胶中促进剂加入量优选为0~3份,更优选为0~2份,再优选为0.3~1份,最优选为0.3~0.7份;所述的丁腈橡胶中硫磺加入量优选为0.5~5份,更优选为0~4份,再优选为1~3份,最优选为1~2份;所述的丁腈橡胶中炭黑加入量优选为0~60份,更优选为5~50份,再优选为10~40份,最优选为20~40份;所述的丁腈橡胶中防老功能磷酸锆占丁腈橡胶的质量比优选为1~50:100,更优选为3~40:100,再优选为5~30:100,最优选为10~30:100;所述的磷酸锆的防老改性剂优选为苯胺类、萘胺类化合物,更优选为对苯二胺,邻苯二胺、间苯二胺、1-萘胺-5-磺酸和4-硝基-1-萘胺和n-苯基-2-萘胺,再优选为对苯二胺、邻苯二胺、间苯二胺、1-萘胺-5-磺酸、4-硝基-1-萘胺和n-苯基-2-萘胺,最优选为苯二胺、邻苯二胺、间苯二胺。下面通过实施例对本发明所述丁腈橡胶/防老功能磷酸锆复合材料及其制备方法做进一步说明。以下实施例中所用的试剂均为市售。实施例1:用n-苯基对苯二胺(rt)对α-zrp进行插层改性制备zrp-rt复合粒子:将10g八水氯氧化锆(zrocl2.8h2o)缓慢滴加到不断搅拌的100ml一定浓度9mol/l的磷酸(h3po4)溶液,将所得的胶体在100℃下回流反应24h,产物洗涤离心,然后65℃干燥24h,研磨后得到α-zrp的白色粉末。将10g的rt溶解于400ml的无水乙醇中作为a液,然后将20g的α-zrp粉末超声分散在400ml的去离子水中作为b液。然后将a液缓慢滴入b液中得到混合溶液,混合溶液在80℃回流反应48h,产物洗涤离心,然后65℃干燥24h,研磨后得到灰色的zrp-rt粉末。利用红外光谱对实施例1中得到的zrp-rt复合粒子进行分析,得到其红外光谱图,如图1所示。由图1可知,傅里叶红外光谱图中,在波数为1250cm-1,900-1200cm-1处分别出现了p-o-h的弯曲振动吸收峰和-po4基团对称和不对称伸缩振动,说明经插层改性后zrp-rt依然保持了磷酸锆的基本结构。但是在波数为3594cm-1,3510cm-1和1619cm-1处水分子的吸收峰减弱,这说明经有机改性后zrp-rt表面和层间的水分子减少。此外,在波数为1497cm-1和1518cm-1分别为单取代苯环和双取代苯环的特征吸收峰,在1280-1350cm-1处为c-n伸缩振动。在700-900cm-1处为伯胺中的c-n面外变形振动吸收峰,3459cm-1处为伯胺(-nh2)对应的特征吸收峰,3375cm-1处为仲胺(-nh-)对应的特征吸收峰。zrp-rt相比于rt的红外谱图发现,zrp-rt在3459cm-1和700-900cm-1处的吸收峰明显减弱,这是因为rt在插层的过程中-nh2水解为-nh3+。利用x射线衍射仪对实施例1中得到的zrp-rt复合粒子进行分析,得到其x衍射谱图,如图2所示。由图2可以看到α-zrp前体以及不同ph值下插层改性后的zrp-rt的产物的x衍射图谱,从zrp-rt(ph=4)和zrp-rt(ph=7)的衍射图中可以发现存在两套插层系列峰,这表明rt分子在磷酸锆层间有单层和双层两种排列方式,分别对应的层间距为d(002)1=2.83nm和d(002)2=1.81nm。相比于α-zrp前体的层间距d(002)=0.75nm增加了2.08nm和1.06nm,这表明rt分子进入了磷酸锆层间,并且存在单层和双层的排列方式。此外,对比zrp-rt(ph=7)和zrp-rt(ph=4),发现zrp-rt(ph=7)中(002)1处的峰明显强于zrp-rt(ph=4),而zrp-rt(ph=4)中(002)2处的峰明显强于zrp-rt(ph=7),这说明zrp-rt(ph=7)中rt分子更多与双层排列,而zrp-rt(ph=4)中rt分子更多与单层排列。双层排列结构有利于zrp-rt在丁腈橡胶基体整剥离和分散,因此选择zrp-rt(ph=7)的产物作为橡胶的填料继续研究。利用热重分析仪对实施例1中得到的zrp-rt复合粒子进行分析,得到其tga谱图,如图3所示。由图3可知,第一个失重阶段在200℃范围内,质量损失在3%左右,主要是α-zrp中的吸附水和结合水脱除而造成的质量损失,生成α-zr(hpo4)2;在400~600℃为第二个失重阶段,对应于α-zr(hpo4)2层状结构中的p-oh发生脱水缩合反应生成zrp2o7,质量损失为7%左右。上面结果可以说明α-zrp在400℃以后才发生层状结构破坏的缩合反应,其分解温度比较高,表明α-zrp能在较高的温度下保持其层状结构的规整性,具有良好的热稳定性。而对于zrp-rt,在200℃以内几乎没有质量损失,主要因为经过rt有机改性后,层间水分子被有机改性剂取代以表面被疏水有机基团所覆盖,吸附水的的含量大大降低。从zrp-rt的失重曲线可以看出,其也存在两个明显的失重阶段,第一阶段失重主要发生在250℃-350℃之间,这是由于插层的有机产物开始受热分解,rt从zrp-rt的层间脱除,直到350℃左右rt已经完全脱除分解,此阶段的质量损失为25%左右,这也说明rt的插入量为25%左右,插层效果很显著。第二阶段发生在400-600℃之间,对应于α-zr(hpo4)2层状结构中的p-oh发生脱水缩合反应生成zrp2o7,质量损失为6%左右。以上结果表明,α-zrp的热稳定性较好,rt成功的插层进入磷酸锆的层间。实施例2:机械共混法制备丁腈橡胶/防老功能磷酸锆复合材料:丁腈橡胶/防老功能磷酸锆复合材料的制备采用机械共混,在双辊开炼机上将生胶、防老功能磷酸锆和助剂进行充分共混,得到混炼胶。各组分的配比如下:采用平板硫化机在150℃,10mpa的条件下对混炼胶进行硫化30min得到硫化胶。配方中添加0份防老功能磷酸锆的试样记为a0,配方中添加1份防老功能磷酸锆的试样记为a1,配方中添加3份防老功能磷酸锆的试样记为a2,配方中添加5份防老功能磷酸锆的试样记为a3,配方中添加10份防老功能磷酸锆的试样记为a4,配方中添加15份防老功能磷酸锆的试样记为a5。实施例3:机械共混法制备添加商用小分子防老剂的对比试样:对比试样的制备采用机械共混,在双辊开炼机上将生胶和助剂进行充分共混,得到混炼胶。各组分的配比如下:采用平板硫化机在150℃,10mpa的条件下对混炼胶进行硫化30min得到硫化胶,该对比试样记为a6。实施例4:本实施例对a0、a1、a2、a3、a4、a5和a6样品分别进行老化试验以及老化前后的强度测试。分别将样品a0、a1、a2、a3、a4、a5和a6置于热氧老化箱中,老化条件为90℃,96h,对比老化前后样品的拉伸强度,计算出老化前后拉伸强度的保留率。测试结果如表一所示:表一从表一可以看出,加入防老功能磷酸锆的丁腈橡胶复合橡胶与空白丁腈橡胶相比,其耐热氧老化性能和机械性能均具有明显提高,并且改性后的丁腈橡胶的防老性能高于添加商用小分子防老剂的试样。说明加入防老功能磷酸锆后,能明显提高丁腈橡胶的机械性能。并且良好分散的防老功能磷酸锆片层在丁腈橡胶基体中形成良好的气体阻隔网络,有效阻止氧气在丁腈橡胶基体中扩散,从物理阻隔角度抑制丁腈橡胶的热氧老化。另一方面,防老功能磷酸锆中的防老官能团能捕捉丁腈橡胶老化过程中产生的过氧自由基中间体,从化学角度抑制丁腈橡胶的老化进程。此外,有机防老基团被“锁定”在磷酸锆的层间,其热稳定性相对较高,在生产和使用过程中有机防老基团不容易从橡胶基体内部逸出,防老效应相比普通小分子防老剂更为持久,同时也减少对环境的污染。根据上述结果,防老功能磷酸锆的加入量优选为10份。实施例5:机械共混法制备丁腈橡胶/防老功能磷酸锆复合材料:丁腈橡胶/防老功能磷酸锆复合材料的制备采用机械共混,在双辊开炼机上将生胶、防老功能磷酸锆和助剂进行充分共混,得到混炼胶。各组分的配比如下:采用平板硫化机在150℃,10mpb的条件下对混炼胶进行硫化30min得到硫化胶。配方中添加0份邻苯二甲酸二辛酯的试样记为b1;配方中添加3份邻苯二甲酸二辛酯的试样记为b2;配方中添加7份邻苯二甲酸二辛酯的试样记为b3。对b1、b2、b3进行力学性能测试,测试结果分别为3.96mpb,3.80mpb,3.51mpb。通过对复合橡胶的力学强度、硬度以及加工性能分析,邻苯二甲酸二辛酯的加入量优选为3份。实施例6:机械共混法制备丁腈橡胶/防老功能磷酸锆复合材料:丁腈橡胶/防老功能磷酸锆复合材料的制备采用机械共混,在双辊开炼机上将生胶、防老功能磷酸锆和助剂进行充分共混,得到混炼胶。各组分的配比如下:采用平板硫化机在150℃,10mpa的条件下对混炼胶进行硫化30min得到硫化胶。配方中添加0份硬脂酸的试样记为c1;配方中添加1份硬脂酸的试样记为c2;配方中添加2份硬脂酸的试样记为c3;配方中添加3份硬脂酸的试样记为c4;配方中添加4份硬脂酸的试样记为c5。对c1、c2、c3、c4、c5进行力学性能测试,测试结果分别为3.94mpa,3.85mpa,3.79mpa,3.51mpa,3.09mpa。通过对复合橡胶的力学强度、硬度以及加工性能分析,硬脂酸的加入量优选为1份。实施例7:机械共混法制备丁腈橡胶/防老功能磷酸锆复合材料:丁腈橡胶/防老功能磷酸锆复合材料的制备采用机械共混,在双辊开炼机上将生胶、防老功能磷酸锆和助剂进行充分共混,得到混炼胶。各组分的配比如下:采用平板硫化机在150℃,10mpa的条件下对混炼胶进行硫化30min得到硫化胶。配方中添加1份氧化锌的试样记为d1;配方中添加3份氧化锌的试样记为d2;配方中添加5份氧化锌的试样记为d3;配方中添加7份氧化锌的试样记为d4;配方中添加9份氧化锌的试样记为d5。对d1、d2、d3、d4、d5进行力学性能测试,测试结果分别为3.57mpa,3.72mpa,3.85mpa,3.93mpa,4.05mpa。通过对复合橡胶的力学强度和正硫化时间分析,硬脂酸的加入量优选为5份。实施例8:机械共混法制备丁腈橡胶/防老功能磷酸锆复合材料:丁腈橡胶/防老功能磷酸锆复合材料的制备采用机械共混,在双辊开炼机上将生胶、防老功能磷酸锆和助剂进行充分共混,得到混炼胶。各组分的配比如下:采用平板硫化机在150℃,10mpa的条件下对混炼胶进行硫化30min得到硫化胶。配方中添加0份促进剂的试样记为e1;配方中添加0.5份促进剂的试样记为e2;配方中添加1份促进剂的试样记为e3;配方中添加3份促进剂的试样记为e4。对e1、e2、e3、e4进行力学性能测试,测试结果分别为3.81mpa,3.79mpa,3.85mpa,3.82mpa。用硫化仪测试了e1、e2、e3、e4的正硫化时间,测试结果分别为31min,30min,28min,25min。通过对复合橡胶的力学强度和正硫化时间分析,促进剂的加入量优选为0.5份。实施例9:机械共混法制备丁腈橡胶/防老功能磷酸锆复合材料:丁腈橡胶/防老功能磷酸锆复合材料的制备采用机械共混,在双辊开炼机上将生胶、防老功能磷酸锆和助剂进行充分共混,得到混炼胶。各组分的配比如下:采用平板硫化机在150℃,10mpa的条件下对混炼胶进行硫化30min得到硫化胶。配方中添加0份硫磺的试样记为f1;配方中添加1.5份硫磺的试样记为f2;配方中添加3份硫磺的试样记为f3;配方中添加5份硫磺的试样记为f4。对f1、f2、f3、f4进行力学性能测试,测试结果分别为1.78mpa,3.79mpa,4.16mpa,4.51mpa。通过对复合橡胶的力学强度和断裂伸长率分析,硫磺的加入量优选为1.5份。实施例10:机械共混法制备丁腈橡胶/防老功能磷酸锆复合材料:丁腈橡胶/防老功能磷酸锆复合材料的制备采用机械共混,在双辊开炼机上将生胶、防老功能磷酸锆和助剂进行充分共混,得到混炼胶。各组分的配比如下:采用平板硫化机在150℃,10mpa的条件下对混炼胶进行硫化30min得到硫化胶。配方中添加0份炭黑的试样记为g1;配方中添加20份炭黑的试样记为g2;配方中添加40份炭黑的试样记为g3;配方中添加60份炭黑的试样记为g4。对g1、g2、g3、g4进行力学性能测试,测试结果分别为2.84mpa,13.12mpa,23.56mpa,28.74mpa。通过对复合橡胶的力学强度和断裂伸长率分析,炭黑的加入量优选为40份。实施例11:通过对实施例2-10的测试结果的分析,优选的各组分配比如下:据此,用机械共混法和溶液共混法制备丁腈橡胶/防老功能磷酸锆复合材料:机械共混法:在双辊开炼机上分别加入丁腈橡胶生胶、助剂、炭黑、防老功能磷酸锆。采用平板硫化机在150℃,10mpa的条件下对混炼胶进行硫化,得到的复合橡胶记为g1。溶液共混法:先用四氢呋喃(thf)溶解10份丁腈橡胶生胶,溶解后向其中加入防老功能磷酸锆,在磁力搅拌器下搅拌均匀后,用旋蒸仪将溶剂蒸发后于干燥箱中干燥48h,即制得丁腈橡胶/防老功能磷酸锆母胶;在双辊开炼机上分别加入丁腈橡胶生胶、助剂、丁腈橡胶/防老功能磷酸锆母胶。采用平板硫化机在150℃,10mpa的条件下对混炼胶进行硫化,得到的复合橡胶记为g2。实施例12:机械共混法制备添加商用小分子防老剂的对比试样:对比试样的制备采用机械共混,在双辊开炼机上将生胶和助剂进行充分共混,得到混炼胶。各组分的配比如下:采用平板硫化机在150℃,10mpa的条件下对混炼胶进行硫化30min得到硫化胶,得到的对比试样记为g3。实施例13:本实施例对g1、g2、g3样品分别进行老化试验以及老化前后的强度测试。分别将样品g1、g2、g3置于热氧老化箱中,老化条件为90℃,96h,对比老化前后样品的拉伸强度,计算出老化前后拉伸强度的保留率。测试结果如表二所示:表二编号g1g2g3断裂强度(mpa)24.9825.7922.4190℃老化96小时后断裂强度(mpa)25.5726.5719.22断裂强度保留率(%)102.24103.0285.77从表二可以看出,用机械共混法和溶液共混法制备的加入防老功能磷酸锆的丁腈橡胶复合橡胶(g1、g2)与对比试样(g3)相比,其耐热氧老化性能和机械性能均具有明显提高;并且g2的改善效果更明显。说明加入防老功能磷酸锆后,能明显提高丁腈橡胶的机械性能,这与实施例4未加炭黑的复合橡胶的测试结果一致。防老功能磷酸锆在丁腈橡胶基体中的分散程度也对力学性能测试产生明显影响。通过溶液共混法制备的复合橡胶与机械共混法制备的复合橡胶相比,前者的力学性能和耐老化性能优于后者,说明防老功能磷酸锆在丁腈橡胶基体中分散程度更好,提高了其机械性能。并且更好的分散程度有利于形成更好的气体阻隔网络,有效阻止氧气在丁腈橡胶基体中扩散,提高其耐老化性能。当前第1页12