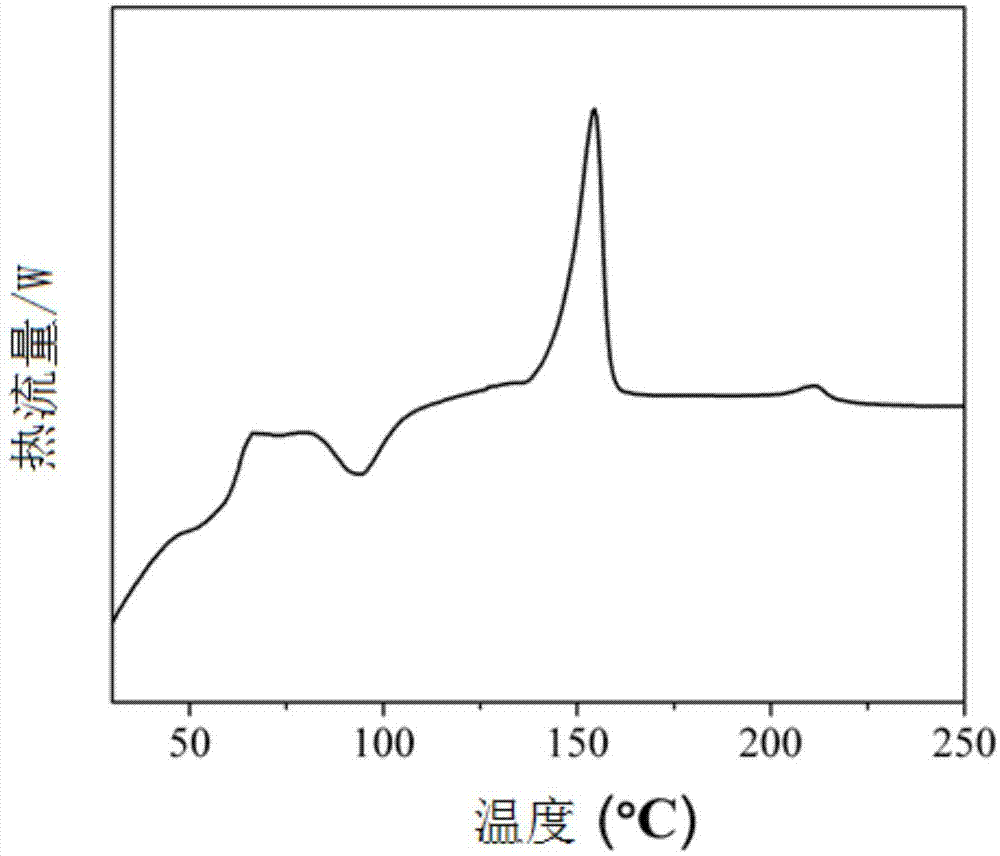
本发明属于聚合物材料加工和微孔发泡
技术领域:
,具体涉及一种全生物基聚乳酸发泡材料及其制备方法。
背景技术:
:发泡塑料是一种以聚合物为基体,内部含有大量气体的微孔材料,可以看做是一种特殊的聚合物/气体复合材料。由于气体相的存在,发泡塑料兼有气体和聚合物的性能特点。与未发泡材料相比,发泡塑料具有质轻、比强度高、高冲击强度、隔音、隔热和强吸收能力等特点,在包装、汽车、运输业、日用品、运动器材及建筑等行业都具有广泛的应用。然而,目前在工业生产中广泛应用的发泡材料以聚乙烯、聚苯乙烯和聚氨酯等软质和硬质泡沫塑料为主,这些传统的发泡塑料都是石油基塑料,以不可再生的石油资源为来源,使用后在自然环境中几乎不会分解,焚烧处理后又产生大量有毒有害物质,难回收,容易对环境造成“白色污染”。为解决上述问题,亟待找寻一种可完全生物降解同时与传统发泡塑料具有类似性能的生物发泡塑料。其中,聚乳酸发泡塑料是最重要的一种生物发泡塑料。聚乳酸(polylactide,pla)是一种热塑性脂肪族聚酯,来源于可再生资源如小麦、玉米、谷物、稻秆等中的淀粉和糖类。聚乳酸具有良好的机械和加工性能,同时在自然环境中可自然降解,最终分解产物为二氧化碳和水,不会对环境产生任何污染。由于与石油基发泡塑料具有类似的基本物性,聚乳酸发泡材料成为微孔发泡材料领域研究的热点,有望广泛的用于日用品和包装等领域,取代传统的石油基泡沬塑料。但是,由于聚乳酸分子链的半刚性,导致其熔融后熔体强度低、结晶速率慢,难以直接用于发泡,故在发泡前需要对聚乳酸进行增强改性。传统的改性聚乳酸发泡性能的主要方法有以下三种,一是改变聚乳酸分子链结构,如通过加入扩链剂和交联剂交联,cn200610117069公开了一种吸塑用聚乳酸泡沫塑料片材及制备方法,特点在于由挤出机挤出发泡、成型得到。但是,该技术采用化学发泡剂发泡,同时加入扩链剂、增塑剂等添加剂,小分子物质残留不仅会影响聚乳酸发泡材料的力学性能,也限制了其在食品包装方面的应用。cn201210032907公布了一种聚乳酸可降解发泡及其制备方法,该技术采用传统的化学发泡剂,同时利用交联剂来改善聚乳酸的熔体强度,然而化学发泡剂分解后无机物质的残留会影响聚乳酸发泡材料的应用范围,同时交联剂的加入让聚乳酸交联难于回收利用,损害了利用其作为生物可降解材料的初衷。二是加入另外一种聚合物形成聚合物共混物,cn201210163071和cn201010231424等,第二组分的加入会在一定程度上改善聚乳酸的发泡性能,但是由于不同聚合物之间的相容性较低,所得共混物的性能均匀性和力学性能一般都较差,而各种相容剂的加入不仅会增加操作过程的复杂性和生产成本,同时也会损害聚乳酸的生物可降解性,难以工业化生产。三是加入填料,如微米级颗粒碳酸钙、纳米级颗粒纳米黏土和碳基纳米材料,是一种有效的改善聚乳酸发泡能力的手段,同时填料的加入能增强聚乳酸发泡材料的机械性能。如cn201310528798公开了一种利用纳米黏土来改善聚乳酸发泡能力的方法,得到了高发泡倍率的聚乳酸发泡制品。然而,纳米粒子的引入也存在一些挑战,比如难于分散和增加产品的价格。同时,在生产和使用过程中,纳米颗粒的逸出会影响生产人员的身体健康。此外,这些填料还会影响聚乳酸材料的生物特性。技术实现要素:针对现有技术存在的问题,本发明目的在于提供一种全生物基聚乳酸发泡材料及其制备方法,该制备工艺简单,原料完全为生物降解材料,并且所得聚乳酸发泡材料泡孔尺寸小、泡孔密度高、发泡倍率高。本发明的技术方案如下:一种全生物基聚乳酸发泡材料的制备方法,其步骤如下:(1)将干燥后的左旋聚乳酸和右旋聚乳酸进行混合,然后将混合物加入双螺杆挤出机中熔融共混、干燥,得到含有立构复合晶体的聚乳酸;(2)将聚乳酸放入挤出发泡机中使其熔融,再将发泡剂气体由挤出发泡机上的注气口计量泵输入螺杆内,与聚乳酸熔体混合均匀,形成单相聚合物/气体熔液;(3)降低注气口至机头处螺杆的温度,使机头处熔体的温度为110-140℃,机头处压力为6-20mpa,最后通过口模挤出发泡并经冷却定型后得到聚乳酸发泡材料。进一步方案,步骤(1)中左旋聚乳酸的质量百分比为90-99%,右旋聚乳酸为余量。进一步方案,步骤(1)中,所述双螺杆挤出机的螺杆温度为140-180℃,螺杆转速为50-150rpm;熔融区域温度为140-200℃。进一步方案,所述左旋聚乳酸和右旋聚乳酸的重均分子量均为15-40万;所述左旋聚乳酸中d-旋光异构体的质量含量为1-10%;所选右旋聚乳酸中l-旋光异构体的质量含量为1-10%。进一步方案,步骤(2)中发泡剂气体为超临界氮气或超临界二氧化碳,其加入量为聚乳酸质量的0.5-10%。进一步方案,步骤(2)中,所述挤出发泡机的温度为140-200℃进一步方案,步骤(1)中左旋聚乳酸和右旋聚乳酸的干燥,是指经60-80℃干燥6-8h,以除去其中水分,防止在挤出机中受热降解。进一步方案,所述挤出发泡机为双螺杆挤出机、单螺杆挤出机或二者的串联挤出机;其中口模为平口模、圆形口模或环形口模。本发明的另一个发明目的是提供一种如上述的制备方法所制备的全生物基聚乳酸发泡材料,其发泡倍率15-45,平均泡孔直径不大于40μm,泡孔密度为108-109个/cm3。本发明将干燥后的左旋聚乳酸和右旋聚乳酸进行混合,以除去其中水分,防止在挤出机中受热降解。然后将混合物加入双螺杆挤出机中熔融共混、干燥,得到含有立构复合晶体的聚乳酸;双螺杆挤出机的螺杆温度为140-180℃、熔融区域温度为140-200℃,由于左旋聚乳酸(plla)和右旋聚乳酸(pdla)在熔融共混的过程中,分子链可以紧密的排列形成特殊的聚乳酸立构复合晶体,其熔点高于聚乳酸同质晶体50℃左右。然后在挤出发泡过程中,可以利用立构复合晶体作为聚乳酸的成核剂和发泡剂,从而改善聚乳酸的熔体性能和结晶速率,最终改善聚乳酸的发泡能力。另外,熔融区域温度为140-200℃,为了达到让立构复合晶体充当聚乳酸成核剂的目的,熔融区温度范围选择是关键,该温度应小于立构复合晶体的熔融温度,同时又高于聚乳酸同质晶体的熔融温度,因而立构复合晶体可以以类固体颗粒形式存在,从而极大提高聚乳酸的熔体强度和结晶速率。本发明的有益效果:(1)由于左旋聚乳酸和右旋聚乳酸同属于聚乳酸,解决了传统聚合物共混物中相容性差的问题。(2)本发明利用低温熔融加工方法得到了含有立构复合晶体的聚乳酸材料,从而改善聚乳酸的熔体性能和结晶速率,最终改善聚乳酸的发泡能力;并且生产过程中无环境污染,生产方法安全,制备过程简单,适合于大批量生产。(3)由于左旋聚乳酸和右旋聚乳酸在熔融共混的过程中形成聚乳酸立构复合晶体,能显著提高聚乳酸的熔体强度和结晶性能,因而所得聚乳酸发泡材料质量稳定、泡孔尺寸均匀、泡孔密度高、发泡倍率高,适合工业规模化生产。(4)该方法制得的全生物基聚乳酸发泡材料,泡孔尺寸、泡孔密度和发泡倍率都可以由左旋聚乳酸与右旋聚乳酸质量比、发泡剂的含量和发泡温度来调控,具有高度可调控性,能满足不同的要求。(5)本发明所得的全生物基聚乳酸发泡材料具有高度可控的发泡倍率和孔结构,发泡倍率15-45,平均泡孔直径不大于40μm,泡孔密度高达109个/cm3。附图说明:图1为左旋聚乳酸与右旋聚乳酸共混后的熔融曲线,图2为实施例四制得的全生物基聚乳酸生物发泡材料的扫描电镜图。具体实施方式以下实施例只是几种典型的实施方式,并不能限制本发明的作用,本领域的技术人员可以参照实施例对技术方案进行合理的设计,同样能够获得本发明的结果。本发明中熔融曲线、发泡倍率、泡孔密度的测试方法如下:熔融曲线:用差示扫描量热法(dsc)仪器分析聚乳酸的熔融曲线,将5-7mg左右的样品放入dsc仪器中,以10℃/min的升温速率,从30℃加热到250℃,即可得到样品的熔融曲线。发泡倍率:按照gb/t6343-2009标准分别测试发泡材料和未发泡材料的表观密度,对于发泡样品采用排水法测量,然后计算得到最终微孔发泡材料的发泡倍率。发泡倍率(φ)=ρpolymer/ρfoam,其中ρpolymer为未发泡材料的密度,ρfoam为发泡材料的密度。泡孔密度:将微孔发泡材料经液氮淬断,断面喷金后,采用扫描电子显微镜(sem)观察发泡材料内部的泡孔结构。采用imagej软件测量泡孔尺寸并计算出泡孔密度。其中泡孔密度n(单位:个/cm3)=(n/a)3/2×φ,n为所选扫描电镜照片上的泡孔数目,a为扫描照片的实际面积(单位:cm2),φ为发泡倍率。具体实施方式中的份数均为重量百分数。以下各实施例按下面方法制备:一种全生物基聚乳酸发泡材料的制备方法,其步骤如下:(1)先将左旋聚乳酸和右旋聚乳酸经60-80℃干燥6-8h,然后将干燥后的左旋聚乳酸和右旋聚乳酸按质量比为90-99:10-1进行混合,最后将混合物加入双螺杆挤出机中熔融共混、干燥,得到含有立构复合晶体的聚乳酸;双螺杆挤出机的螺杆温度为140-180℃,螺杆转速为50-150rpm;熔融区域温度为140-200℃;(2)将聚乳酸放入140-200℃的挤出发泡机中使其熔融,再将发泡剂气体由挤出发泡机上的注气口计量泵输入螺杆内,与聚乳酸熔体混合均匀,形成单相聚合物/气体熔液;(3)降低注气口至机头处螺杆的温度,使机头处熔体的温度为110-140℃,机头处压力为6-8mpa,最后通过口模挤出发泡并经冷却定型后得到聚乳酸发泡材料。进一步方案,所述左旋聚乳酸和右旋聚乳酸的重均分子量均为15-40万;所述左旋聚乳酸中d-旋光异构体的质量含量为1-10%;所选右旋聚乳酸中l-旋光异构体的质量含量为1-10%。进一步方案,步骤(2)中发泡剂气体为超临界氮气或超临界二氧化碳,其加入量为聚乳酸质量的0.5-10%。进一步方案,所述挤出发泡机为双螺杆挤出机、单螺杆挤出机或二者的串联挤出机;其中口模为平口模、圆形口模或环形口模。实施例1(1)将干燥后的左旋聚乳酸和右旋聚乳酸按照质量比为99:1共混,其中二者重均分子量均为15,对应的另一种异构体含量为1%,通过双螺杆挤出机熔融共混,螺杆温度为140-180℃,螺杆转速为50rpm,得到含有立构复合晶体的聚乳酸。(2)将干燥后的含有立构复合晶体的聚乳酸放入挤出发泡机中使其熔融,温度为140-200℃。同时将占聚乳酸质量0.5%的超临界氮气由挤出机上的注气口计量泵输入螺杆内,与聚合物熔体混合均匀,形成单相聚合物/气体溶液。(3)降低注气口至机头处螺杆温度,使机头处熔体温度为110℃,机头处压力为8mpa,最后通过口模挤出发泡并经冷却定型后得到聚乳酸发泡材料。图1为本实施例制得的聚乳酸的熔融曲线,从图中可以看到在210℃左右出现了一个小峰,说明体系中形成了立构复合晶体。如图2为实施例四制得的全生物基聚乳酸生物发泡材料的扫描电镜图,其发泡倍率为31,泡孔直径27μm、泡孔密度1.1×109个/cm3。实施例2-9的制备方法同实施例1,其原料与发泡条件见表1。对比例1-2中的原料仅为纯的左旋聚乳酸,其原料与发泡条件如表1所示,发泡工艺参数见表1。实施例1-9和对比例1-2制备的聚乳酸发泡材料的性能测试见表2所示。表1:实施例1-9对比例1-2中的原料与发泡条件表2:性能测试发泡倍率泡孔直径(μm)泡孔密度(个/cm3)实施例136222.3×109实施例238194.1×109实施例327374.7×108实施例431271.1×109实施例539213.1×109实施例645224.5×109实施例726354.2×108实施例828336.1×108实施例915392.3×108对比例1132004.1×106对比例2173003.6×106从上表2可看出,本发明制备的全生物基聚乳酸发泡材料具有高度可控的发泡倍率和孔结构,其发泡倍率为15-45,平均泡孔直径不大于40μm,泡孔密度高达109个/cm3。而对比例中泡孔直径达到200-300μm,泡孔密度仅为106个/cm3。应当理解的是,对本领域普通技术人员来说,可以根据上述说明加以改进或变换,而所有这些改进和变换都应属于本发明的保护范围。当前第1页12