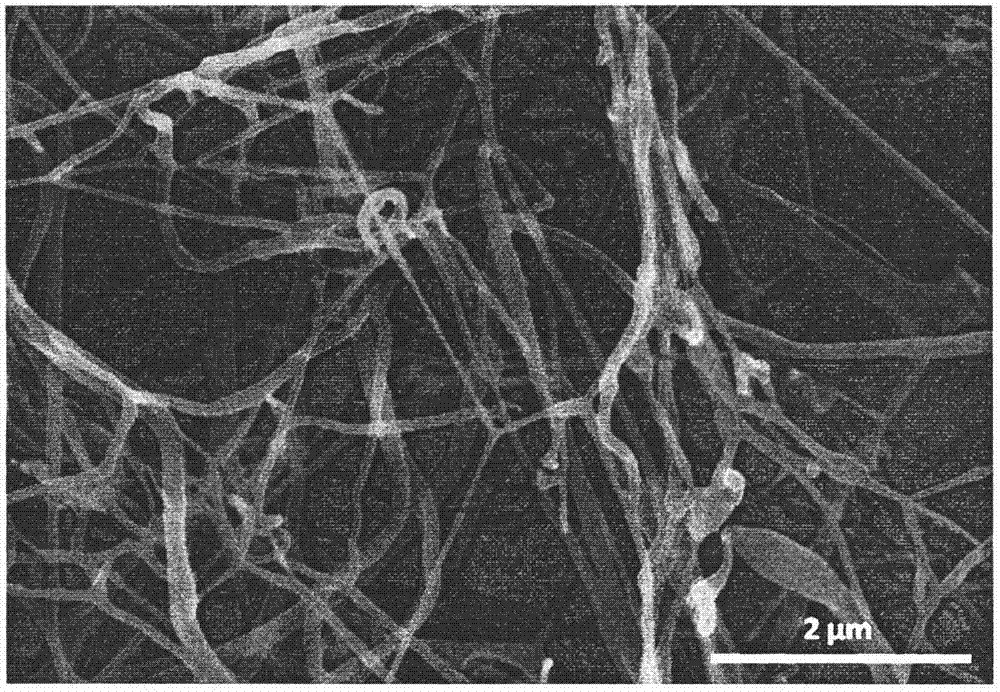
本发明属于纳米材料技术领域,具体涉及一种氨基甲酰乙基微纤化纤维素及其制备方法。
背景技术:
纳米纤维素作为新一代绿色功能材料已得到了业界的普遍关注。它由天然纤维素纤维制备而得,根据制备方法、尺寸和来源不同可大致分为:纤维素纳米晶须(nanocellulosecrystal,ncc),微纤化纤维素(microfibrillatedcellulose,mfc或nanofibrillatedcellulose,nfc)和细菌纤维素(bacterialcellulose,bc)。微纤化纤维素具有长径比大、自身强度高的特点,且原材料来源广泛、可持续获取,自身可生物降解、生物相容性良好,兼具纳米材料和天然有机高分子材料的双重特性。与钢材相比,微纤化纤维素的重量(比重1.6g/cm3)只有其五分之一,强度(弹性模量140gpa,明显高于高强玻璃纤维的90gpa)却是其五倍以上。此外,微纤化纤维素还具有热膨胀率低、磨损小等优点,在造纸、食品、化妆品、复合材料和生物医学领域具有巨大的潜在应用价值。
国内外微纤化纤维素的制备主要采用物理法,即通过研磨、高压均质、微射流、超声等机械处理将纤维素原料解离成微纤化纤维素,但该方法所需能耗高、效率低。将化学预处理与物理法相结合来制备微纤化纤维素,不仅可以降低机械解离能耗,还能够赋予微纤化纤维素特殊的官能团。常用的化学预处理方法包括tempo(2,2,6,6-四甲基哌啶氮氧化物)氧化法和羧甲基化法等。例如发明专利cn201710092572.0公开了一种采用tempo、高碘酸盐、次氯酸钠等氧化制备纳米纤维素的方法,而发明专利cn01711009627.3公开了一种羧甲基纳米纤维素的制备方法。前者所采用的tempo试剂价格极其昂贵,而后者需要用到异丙醇、乙醇等有机溶剂,成本较高,限制了微纤化纤维素的规模化生产。因此,开发一种低成本的微纤化纤维素及其制备方法具有重要的理论和实践意义。
技术实现要素:
有鉴于此,本发明提供了一种成本较低的氨基甲酰乙基微纤化纤维素制备方法。
本发明提供的氨基甲酰乙基微纤化纤维素的制备方法,其关键技术在于采用碱和丙烯酰胺以水为反应介质对纤维素原料进行化学预处理,解决了现有技术化学试剂昂贵、有机溶剂使用量大、设备负荷高的问题,降低了生产成本。
本发明还提供了一种氨基甲酰乙基微纤化纤维素产品,该产品表面富含氨基甲酰乙基官能团,氮元素含量在0.1-5.0wt%之间,羧基含量在0.1-2.0mmol/g之间,纤维直径在5nm-1um之间,纤维长度在500nm以上。
为实现上述目的,本发明采用的技术方案是:
(1)预浸渍:将纤维素原料加入醚化剂和催化剂的混合物,预浸渍后,进行浓缩;
(2)醚化:将浓缩物加热醚化;
(3)洗涤:将产物用水反复洗涤至中性;
(4)机械解离:将产物进行机械解离处理,得到氨基甲酰乙基微纤化纤维素
所述的纤维素原料为杨木、桉木、马尾松、落叶松、小麦秸秆、玉米秸秆、玉米芯、棉秸秆、竹子、芦苇、蔗渣的块状物、粉末、漂白或未漂白浆中的一种或多种混合,其中块状及粉末原料需粉碎至粒度为40-80目,优选为60-80目。
所述的醚化剂为丙烯酰胺,催化剂为氢氧化钠、氢氧化钾、氢氧化铵中的一种。
所述的预浸渍液的质量百分比组成为:醚化剂5-50%,优选为40-50%:催化剂0.1-10%,优选为3-6%;余量为水。
所述的预浸渍时间为1-30分钟,优选为5-20分钟;预浸渍温度为10-30℃;原料的预浸渍浓度为0.1-10%,优选为3-6%;浓缩后的物料质量浓度为1-30%,优选为15-25%。
所述的醚化温度为90-140℃,优选为110-130℃;醚化时间为1-120分钟,优选为5-60分钟。
所述的机械解离处理包括研磨处理、高压均质处理中的一种或两种组合;研磨处理的物料质量浓度为0.1-15%,优选为2-10%;双磨盘之间的间隙为-150-0μm,优选为-100--50μm;研磨时间为10分钟-5小时;高压均质处理的物料质量浓度为0.1-3%,优选为0.5-2%;处理压力为20-150mpa,优选为50-120mpa;处理时间10-60分钟。
所述的氨基甲酰乙基微纤化纤维素具有如下特征:氮元素(n)含量在0.1-5.0%之间,羧基含量在0.1-2.0mmol/g之间,纤维直径在5nm-1um之间,纤维长度在500nm以上。
本发明与现有技术相比,具有如下优点和有益效果:
1、该方法与直接采用物理机械法相比,减少了解离能耗,使机械处理时间从10-30小时,降低至5小时以内;与常用的tempo氧化法和羧甲基化法相比,具有药品价格低,反应介质为水,操作方便,工艺简单,生产成本低的优点,有利于实现微纤化纤维素的工业化生产。
2、本方法得到的氨基甲酰乙基微纤化纤维素含有氨基甲酰乙基官能团,通过控制反应条件,还可同时带有羧乙基官能团,且氨基甲酰乙基与羧乙基的比例可根据需要进行调控,有利于拓宽微纤化纤维素的应用范围。
3、本方法的适用范围广,可作用于阔叶木、针叶木以及非木材的块状、粉末、漂白浆、未漂白浆等形态的原料,并允许原料中含有半纤维素、木质素等除纤维素之外的其它组分,可实现原料组分的充分利用。
附图说明
附图是用来提供对本发明的进一步理解,并且构成说明书的一部分,但并不构成对本发明的限制。在附图中:
图1是氨基甲酰乙基微纤化纤维素的扫描电子显微镜图
图2是氨基甲酰乙基微纤化纤维素的傅里叶红外图谱
具体实施方式
下面结合具体实施例对本发明作进一步详细描述,但不作为对本发明的限定。
实施例1
一种氨基甲酰乙基微纤化纤维素的制备方法,包括如下步骤:
(1)取漂白硫酸盐杨木浆100克(绝干量),将其浸渍在2kg含50wt%丙烯酰胺和3wt%氢氧化钠的水溶液中,在25℃下浸渍10分钟后,将其浓缩至物料浓度为20wt%,浓缩液进行回用;
(2)将浓缩后的物料在125℃下反应30分钟,进行醚化;
(3)将醚化产物用水反复洗涤至中性;
(4)将洗涤后的产物用水稀释至5wt%的浓度,采用双磨盘研磨机在间隙为-100μm下研磨4小时,再将研磨后的物料用水稀释至1wt%的浓度,在压力为120mpa下进行高压均质,处理时间为10分钟。
所得氨基甲酰乙基微纤化纤维素的氮元素含量为4.8wt%,羧基含量为0.1mmol/g,纤维直径在60nm,纤维长度为3μm。
实施例2
(1)将玉米秸秆粉碎后,收集40-80目之间的粉末,取100克(绝干量)浸渍在1kg含10wt%丙烯酰胺和0.5wt%氢氧化钾的水溶液中,在10℃下浸渍30分钟后,将其浓缩至物料浓度为30wt%,浓缩液进行回用;
(2)将浓缩后的物料在140℃下反应120分钟,进行醚化;
(3)将醚化产物用水反复洗涤至中性;
(4)将洗涤后的产物用水稀释至12wt%的浓度,采用双磨盘研磨机在间隙为-50μm下研磨2小时,再将研磨后的浆料用水稀释至2wt%的浓度,在压力为100mpa下进行高压均质,处理时间为20分钟。
所得氨基甲酰乙基微纤化纤维素的氮元素含量为0.5wt%,羧基含量为0.2mmol/g,纤维直径在80nm,纤维长度为1μm。
实施例3
(1)取未漂白硫酸盐竹浆100克(绝干量),将其浸渍在3kg含40wt%丙烯酰胺和10wt%氢氧化铵的水溶液中,在30℃下浸渍20分钟后,将其浓缩至物料浓度为15wt%,浓缩液进行回用;
(2)将浓缩后的物料在110℃下反应60分钟,进行醚化;
(3)将醚化产物用水反复洗涤至中性;
(4)将洗涤后的产物用水稀释0.5wt%的浓度,在压力为120mpa下进行高压均质,处理时间为40分钟。
所得氨基甲酰乙基微纤化纤维素的氮元素含量为1.2wt%,羧基含量为0.5mmol/g,纤维直径在40nm,纤维长度为2μm。
实施例4
(1)将甘蔗渣粉碎后,收集40-80目之间的粉末,取100克(绝干量)浸渍在4kg含20wt%丙烯酰胺和8wt%氢氧化钠的水溶液中,在20℃下浸渍15分钟后,将其浓缩至物料浓度为10wt%,浓缩液进行回用;
(2)将浓缩后的物料在130℃下反应90分钟,进行醚化;
(3)将醚化产物用水反复洗涤至中性;
(4)将洗涤后的产物用水稀释至8wt%的浓度,采用双磨盘研磨机在间隙为-120μm下研磨2小时。
所得氨基甲酰乙基微纤化纤维素的氮元素含量为0.8wt%,羧基含量为1.0mmol/g,纤维直径在100nm,纤维长度为1.5μm。
实施例5
(1)取未漂白马尾松化机浆100克(绝干量)浸渍在1.25kg含30wt%丙烯酰胺和10wt%氢氧化钾的水溶液中,在15℃下浸渍25分钟后,将其浓缩至物料浓度为25wt%,浓缩液进行回用;
(2)将浓缩后的物料在120℃下反应20分钟,进行醚化;
(3)将醚化产物用水反复洗涤至中性;
(4)将洗涤后的产物用水稀释至6wt%的浓度,采用双磨盘研磨机在间隙为-90μm下研磨1.5小时,再将研磨后的浆料用水稀释至1.5wt%的浓度,在压力为110mpa下进行高压均质,处理时间为10分钟。
所得氨基甲酰乙基微纤化纤维素的氮元素含量为3.4wt%,羧基含量为1.2mmol/g,纤维直径在90nm,纤维长度为2.5μm。
以上实施例仅为本发明的示例性实施例,不用于限制本发明,本发明的保护范围由权利要求书限定。本领域技术人员可以在本发明的实质和保护范围内,对本发明做出各种修改或等同替换,这种修改或等同替换也应视为落在本发明的保护范围内。