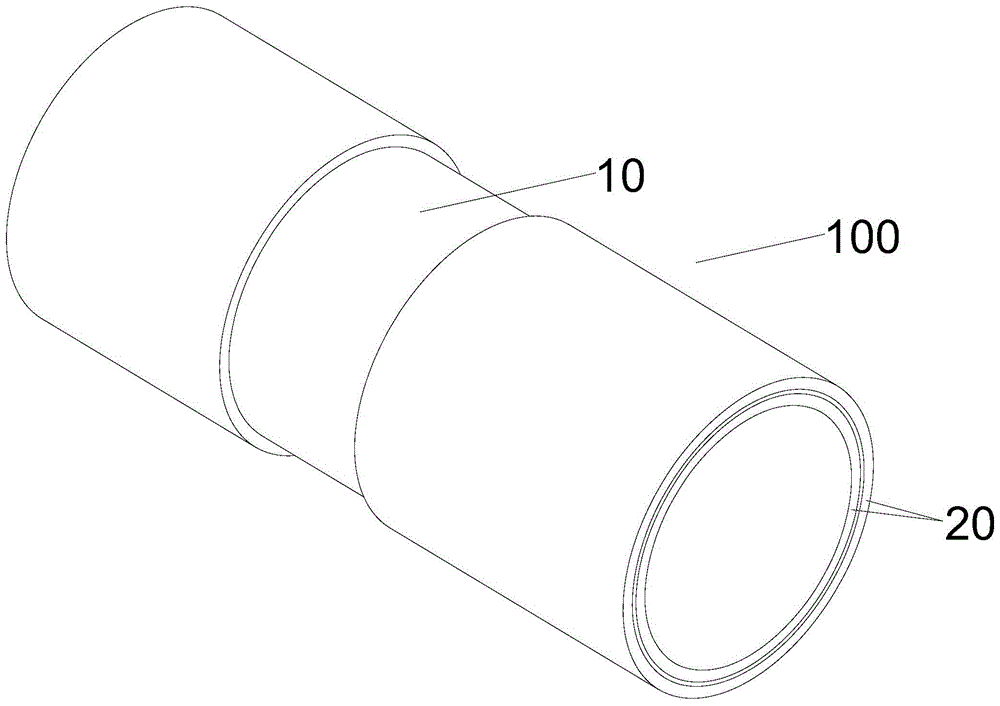
本发明涉及材料领域,具体涉及一种气密性聚氨酯材料及管道修复用内衬管。
背景技术:
地下排水管道、排污管道、燃气管道等市政管道(简称管道)是人们生活中必不可少的基础设施。由于地基不牢固、管道腐蚀等原因,市政管道使用时间过久就会出现老化、腐蚀、裂缝和坍塌等损坏现象,给正常的生产和生活带来不利影响,需要及时对其进行维修。维修管道的技术总的来说有两种:一种是挖开损坏处的路面,对管道损坏处进行修补施工。另一种是在破损管道内设置修复管道对管道进行修复;
前一种修复方式需要挖开一段路面,从而会对交通、环境、周边建筑基础以及居民的正常生活和工作秩的带来破坏和不良影响;
后一种方式则对各方面影响小,且实施方便、费用低,是较好的修复方法,但是该方式对修复用的管道的要求也非常高,特别是用在修复燃气管道中时,需要保证足够的气密性。
技术实现要素:
本发明要解决的技术问题是提供一种气密性聚氨酯材料及管道修复用内衬管,其具有气密性好的特点。
为了解决上述技术问题,本发明采用的技术方案如下:一种气密性聚氨酯材料,包括聚氨酯、蒙脱土、炭黑、内润滑剂、热稳定剂、偶联剂和增韧剂,各组分的质量比为70~80:15~30:5~10:0.5~1.5:0.5~1:3~5:0.5~1.5。
进一步的,优选地,所述聚氨酯为聚醚型聚氨酯,硬度为75~90a。
优选地,所述蒙脱土为硅烷改性蒙脱土,目数为5000~10000目,所述炭黑的微观形貌为球形,目数为2000~5000目。
优选地,所述内润滑剂为长链多官能团酯,所述热稳定剂为有机锡类热稳定剂。
优选地,还包括质量比为0.5~1.5的外润滑剂,所述外润滑剂包括质量比为1:1的聚乙烯蜡和硬脂酸钙。
优选地,还包括质量比为0.5~1.5的抗氧剂,所述抗氧剂由质量比为1:1的抗氧剂1010和抗氧剂168组成。
优选地,所述增韧剂为sebs。
一种气密性聚氨酯材料制备方法,在混合室混合时加料的顺序为:
(1)在低转速下,将聚氨酯加入混合室;
(2)在40~80℃,高转速下,加入热稳定剂及聚乙烯蜡;
(3)在60~90℃,高转速下,加入偶联剂、抗氧剂和硬脂酸钙;
(4)在80~120℃,高转速下,加入内润滑剂;
(5)在90~130℃,高转速下,加入蒙脱土、炭黑及增韧剂;
(6)在110℃~120℃,低转速下排出物料,送入冷混机中;
(7)冷混至料温为50℃以下,排出、过筛。
一种管道修复用内衬管,包括pet纤维层,所述pet纤维层的内外层均通过涂覆所述气密性聚氨酯材料形成气密性聚氨酯层。
一种管道修复方法,包括:(1)在待修复管道上开设两个开口;(2)将如权利要求11所述内衬管从所述一个开口塞入所述待修复管道并从所述另一个开口拉出;(3)堵住所述内衬管的一端口,从另一端口吹入压缩空气使所述内衬管完全紧密贴附在所述待修复管道的内壁上。
本发明的有益效果:本发明具有能够保持较低的硬度,从而满足管道的长距离收卷,同时阻隔气体效果好,耐寒性能好,性价比高。
附图说明
图1是本发明的内衬管的结构示意图;
图2是本发明的内衬管的呈u型的示意图。
具体实施方式
下面结合附图和具体实施例对本发明作进一步说明,以使本领域的技术人员可以更好地理解本发明并能予以实施,但所举实施例不作为对本发明的限定。
实施例一:
一种气密性聚氨酯材料制备方法,在混合室混合时加料的顺序为:
(1)在低转速下,将6260份聚氨酯加入混合室;
(2)在40~80℃,高转速下,加入45份热稳定剂;
(3)在60~90℃,高转速下,加入447份偶联剂;
(4)在80~120℃,高转速下,加入45份内润滑剂;
(5)在90~130℃,高转速下,加入2711份蒙脱土、447份炭黑及45份增韧剂;
(6)在110℃~120℃,低转速下排出物料,送入冷混机中;
(7)冷混至料温为50℃以下,排出、过筛;
其中,所述低转速为0~200r/min,所述高转速为200~2000r/min。
所述聚氨酯为聚醚型聚氨酯,硬度为75~90a,该硬度下的聚氨酯中加入上述各无机填料后的复合材料也能够保持较低的硬度,能够满足长距离管材的扁平收卷;所述蒙脱土为硅烷改性蒙脱土,目数为5000~10000目,硅烷改性的蒙脱土能够提高有机相和无机相的相容性,能够较好的分散于有机相中,蒙脱土的片层结构,均匀分散在有机相中,起到了较好的阻隔气体的作用;所述炭黑的微观形貌为球形,球形的比表面积大,与其他材料的接触面也大,从而增强了气密性,目数为2000~5000目;所述内润滑剂为长链多官能团酯,相比较常用的石蜡,硬脂酸、硬脂酸钙等,不会出现吐霜等问题,有很高的性价比;所述热稳定剂为有机锡类热稳定剂;所述增韧剂为sebs(氢化苯乙烯-丁二烯嵌段共聚物),耐寒性能好;所述偶联剂为硅烷偶联剂,提高有机相和无机相的相容性;气密性聚氨酯材料中还包括用于调色的色母;
取三组不同厚度的气密性聚氨酯和普通80a聚氨酯进行气体渗透性测试:
(1)测试标准:gb/t1038-2000;
(2)测试条件:测试温度40℃,测试气体为甲烷;
(3)样品数量:共2组,每组3个;
(4)测试设备:压差法气体渗透仪vac-v2;
测试结果如下:
由上述表格可知,气密性聚氨酯的气密性远好于普通80a聚氨酯。
如图1所示,一种管道修复用内衬管100,包括pet纤维层10,所述pet纤维层10的内外层均通过涂覆所述气密性聚氨酯材料形成气密性聚氨酯层20,该气密性聚氨酯层20通过将各组分混合,造粒,得到的粒子涂覆挤出在pet纤维层10的内外层形成,同时需要注意的是采用混合机混合各组分时,混合机的加料量控制在混合室空容积的50%~70%,该内衬管100的使用年限为40年;
一种管道修复方法,包括:(1)在待修复管道上开设两个开口;(2)将所述内衬管100从所述一个开口塞入所述待修复管道并从所述另一个开口拉出,如图2所示,内衬管100提前通过压成u型呈扁平化收卷在收卷架上,同时通过压成u型可以减小与待修复管道的接触面积,方便拖动,通过牵引机对内衬管100进行牵引从而穿过待修复管道;(3)堵住所述内衬管100的一端口,进一步的采用气囊堵住内衬管100的一端口,从另一端口吹入压缩空气使所述内衬管100完全紧密贴附在所述待修复管道的内壁上,之后切掉多余部分,修复完成;原来步骤(1)中开挖的两个开口则通过焊接或者连接新管道进行连接。
实施例二:
一种气密性聚氨酯材料制备方法,在混合室混合时加料的顺序为:
(1)在低转速下,将6400份聚氨酯加入混合室;
(2)在40~80℃,高转速下,加入55份热稳定剂及22.5份聚乙烯蜡;
(3)在60~90℃,高转速下,加入490份偶联剂、45份抗氧剂和22.5份硬脂酸钙,45份抗氧剂由质量比为1:1的抗氧剂1010和抗氧剂168组成;
(4)在80~120℃,高转速下,加入65份内润滑剂;
(5)在90~130℃,高转速下,加入2360份蒙脱土、560份炭黑及70份增韧剂;
(6)在110℃~120℃,低转速下排出物料,送入冷混机中;
(7)冷混至料温为50℃以下,排出、过筛;
其中,所述低转速为0~200r/min,所述高转速为200~2000r/min。
所述聚氨酯为聚醚型聚氨酯,硬度为75~90a,该硬度下的聚氨酯中加入上述各无机填料后的复合材料也能够保持较低的硬度,能够满足长距离管材的扁平收卷;所述蒙脱土为硅烷改性蒙脱土,目数为5000~10000目,硅烷改性的蒙脱土能够提高有机相和无机相的相容性,能够较好的分散于有机相中,蒙脱土的片层结构,均匀分散在有机相中,起到了较好的阻隔气体的作用;所述炭黑的微观形貌为球形,球形的比表面积大,与其他材料的接触面也大,从而增强了气密性,目数为2000~5000目;所述内润滑剂为长链多官能团酯,相比较常用的石蜡,硬脂酸、硬脂酸钙等,不会出现吐霜等问题,有很高的性价比;所述热稳定剂为有机锡类热稳定剂;所述增韧剂为sebs(氢化苯乙烯-丁二烯嵌段共聚物),耐寒性能好;所述偶联剂为硅烷偶联剂,提高有机相和无机相的相容性;气密性聚氨酯材料中还包括用于调色的色母。
取三组不同厚度的气密性聚氨酯和普通80a聚氨酯进行气体渗透性测试:
(1)测试标准:gb/t1038-2000;
(2)测试条件:测试温度40℃,测试气体为甲烷;
(3)样品数量:共2组,每组3个;
(4)测试设备:压差法气体渗透仪vac-v2;
测试结果如下:
由上述表格可知,气密性聚氨酯的气密性远好于普通80a聚氨酯。
如图1所示,一种管道修复用内衬管100,包括pet纤维层10,所述pet纤维层10的内外层均通过涂覆所述气密性聚氨酯材料形成气密性聚氨酯层20,该气密性聚氨酯层20通过将各组分混合,造粒,得到的粒子涂覆挤出在pet纤维层10的内外层形成,同时需要注意的是采用混合机混合各组分时,混合机的加料量控制在混合室空容积的50%~70%,该内衬管100的使用年限为45年;
一种管道修复方法,包括:(1)在待修复管道上开设两个开口;(2)将所述内衬管100从所述一个开口塞入所述待修复管道并从所述另一个开口拉出,如图2所示,内衬管100提前通过压成u型呈扁平化收卷在收卷架上,同时通过压成u型可以减小与待修复管道的接触面积,方便拖动,通过牵引机对内衬管100进行牵引从而穿过待修复管道;(3)堵住所述内衬管100的一端口,进一步的采用气囊堵住内衬管100的一端口,从另一端口吹入压缩空气使所述内衬管100完全紧密贴附在所述待修复管道的内壁上,之后切掉多余部分,修复完成;原来步骤(1)中开挖的两个开口则通过焊接或者连接新管道进行连接。
实施例三:
一种气密性聚氨酯材料制备方法,在混合室混合时加料的顺序为:
(1)在低转速下,将6700份聚氨酯加入混合室;
(2)在40~80℃,高转速下,加入67份热稳定剂及43.5份聚乙烯蜡;
(3)在60~90℃,高转速下,加入357份偶联剂、87份抗氧剂和43.5份硬
脂酸钙,87份抗氧剂由质量比为1:1的抗氧剂1010和抗氧剂168组成;
(4)在80~120℃,高转速下,加入87份内润滑剂;
(5)在90~130℃,高转速下,加入2020份蒙脱土、670份炭黑及99份增韧剂;
(6)在110℃~120℃,低转速下排出物料,送入冷混机中;
(7)冷混至料温为50℃以下,排出、过筛;
其中,所述低转速为0~200r/min,所述高转速为200~2000r/min。
所述聚氨酯为聚醚型聚氨酯,硬度为75~90a,该硬度下的聚氨酯中加入上述各无机填料后的复合材料也能够保持较低的硬度,能够满足长距离管材的扁平收卷;所述蒙脱土为硅烷改性蒙脱土,目数为5000~10000目,硅烷改性的蒙脱土能够提高有机相和无机相的相容性,能够较好的分散于有机相中,蒙脱土的片层结构,均匀分散在有机相中,起到了较好的阻隔气体的作用;所述炭黑的微观形貌为球形,球形的比表面积大,与其他材料的接触面也大,从而增强了气密性,目数为2000~5000目;所述内润滑剂为长链多官能团酯,相比较常用的石蜡,硬脂酸、硬脂酸钙等,不会出现吐霜等问题,有很高的性价比;所述热稳定剂为有机锡类热稳定剂;所述增韧剂为sebs(氢化苯乙烯-丁二烯嵌段共聚物),耐寒性能好;所述偶联剂为硅烷偶联剂,提高有机相和无机相的相容性;气密性聚氨酯材料中还包括用于调色的色母。
取三组不同厚度的气密性聚氨酯和普通80a聚氨酯进行气体渗透性测试:
(1)测试标准:gb/t1038-2000;
(2)测试条件:测试温度40℃,测试气体为甲烷;
(3)样品数量:共2组,每组3个;
(4)测试设备:压差法气体渗透仪vac-v2;
测试结果如下:
由上述表格可知,气密性聚氨酯的气密性远好于普通80a聚氨酯。
如图1所示,一种管道修复用内衬管100,包括pet纤维层10,所述pet纤维层10的内外层均通过涂覆所述气密性聚氨酯材料形成气密性聚氨酯层20,该气密性聚氨酯层20通过将各组分混合,造粒,得到的粒子涂覆挤出在pet纤维层10的内外层形成,同时需要注意的是采用混合机混合各组分时,混合机的加料量控制在混合室空容积的50%~70%,该内衬管100的使用年限为50年;
一种管道修复方法,包括:(1)在待修复管道上开设两个开口;(2)将所述内衬管100从所述一个开口塞入所述待修复管道并从所述另一个开口拉出,如图2所示,内衬管100提前通过压成u型呈扁平化收卷在收卷架上,同时通过压成u型可以减小与待修复管道的接触面积,方便拖动,通过牵引机对内衬管100进行牵引从而穿过待修复管道;(3)堵住所述内衬管100的一端口,进一步的采用气囊堵住内衬管100的一端口,从另一端口吹入压缩空气使所述内衬管100完全紧密贴附在所述待修复管道的内壁上,之后切掉多余部分,修复完成;原来步骤(1)中开挖的两个开口则通过焊接或者连接新管道进行连接。
实施例四:
一种气密性聚氨酯材料制备方法,在混合室混合时加料的顺序为:
(1)在低转速下,将6930份聚氨酯加入混合室;
(2)在40~80℃,高转速下,加入75份热稳定剂及65份聚乙烯蜡;
(3)在60~90℃,高转速下,加入310份偶联剂、130份抗氧剂和65份硬脂酸钙,130份抗氧剂由质量比为1:1的抗氧剂1010和抗氧剂168组成;
(4)在80~120℃,高转速下,加入115份内润滑剂;
(5)在90~130℃,高转速下,加入1675份蒙脱土、780份炭黑及115份增韧剂;
(6)在110℃~120℃,低转速下排出物料,送入冷混机中;
(7)冷混至料温为50℃以下,排出、过筛;
其中,所述低转速为0~200r/min,所述高转速为200~2000r/min。
所述聚氨酯为聚醚型聚氨酯,硬度为75~90a,该硬度下的聚氨酯中加入上述各无机填料后的复合材料也能够保持较低的硬度,能够满足长距离管材的扁平收卷;所述蒙脱土为硅烷改性蒙脱土,目数为5000~10000目,硅烷改性的蒙脱土能够提高有机相和无机相的相容性,能够较好的分散于有机相中,蒙脱土的片层结构,均匀分散在有机相中,起到了较好的阻隔气体的作用;所述炭黑的微观形貌为球形,球形的比表面积大,与其他材料的接触面也大,从而增强了气密性,目数为2000~5000目;所述内润滑剂为长链多官能团酯,相比较常用的石蜡,硬脂酸、硬脂酸钙等,不会出现吐霜等问题,有很高的性价比;所述热稳定剂为有机锡类热稳定剂;所述增韧剂为sebs(氢化苯乙烯-丁二烯嵌段共聚物),耐寒性能好;所述偶联剂为硅烷偶联剂,提高有机相和无机相的相容性;气密性聚氨酯材料中还包括用于调色的色母。
取三组不同厚度的气密性聚氨酯和普通80a聚氨酯进行气体渗透性测试:
(1)测试标准:gb/t1038-2000;
(2)测试条件:测试温度40℃,测试气体为甲烷;
(3)样品数量:共2组,每组3个;
(4)测试设备:压差法气体渗透仪vac-v2;
测试结果如下:
由上述表格可知,气密性聚氨酯的气密性远好于普通80a聚氨酯。
如图1所示,一种管道修复用内衬管100,包括pet纤维层10,所述pet纤维层10的内外层均通过涂覆所述气密性聚氨酯材料形成气密性聚氨酯层20,该气密性聚氨酯层20通过将各组分混合,造粒,得到的粒子涂覆挤出在pet纤维层10的内外层形成,同时需要注意的是采用混合机混合各组分时,混合机的加料量控制在混合室空容积的50%~70%,该内衬管100的使用年限为45年;
一种管道修复方法,包括:(1)在待修复管道上开设两个开口;(2)将所述内衬管100从所述一个开口塞入所述待修复管道并从所述另一个开口拉出,如图2所示,内衬管100提前通过压成u型呈扁平化收卷在收卷架上,同时通过压成u型可以减小与待修复管道的接触面积,方便拖动,通过牵引机对内衬管100进行牵引从而穿过待修复管道;(3)堵住所述内衬管100的一端口,进一步的采用气囊堵住内衬管100的一端口,从另一端口吹入压缩空气使所述内衬管100完全紧密贴附在所述待修复管道的内壁上,之后切掉多余部分,修复完成;原来步骤(1)中开挖的两个开口则通过焊接或者连接新管道进行连接。
实施例五:
一种气密性聚氨酯材料制备方法,在混合室混合时加料的顺序为:
(1)在低转速下,将7159份聚氨酯加入混合室;
(2)在40~80℃,高转速下,加入45份热稳定剂;
(3)在60~90℃,高转速下,加入268份偶联剂;
(4)在80~120℃,高转速下,加入130份内润滑剂;
(5)在90~130℃,高转速下,加入1330份蒙脱土、894份炭黑及130份增韧剂;
(6)在110℃~120℃,低转速下排出物料,送入冷混机中;
(7)冷混至料温为50℃以下,排出、过筛;
其中,所述低转速为0~200r/min,所述高转速为200~2000r/min。
所述聚氨酯为聚醚型聚氨酯,硬度为75~90a,该硬度下的聚氨酯中加入上述各无机填料后的复合材料也能够保持较低的硬度,能够满足长距离管材的扁平收卷;所述蒙脱土为硅烷改性蒙脱土,目数为5000~10000目,硅烷改性的蒙脱土能够提高有机相和无机相的相容性,能够较好的分散于有机相中,蒙脱土的片层结构,均匀分散在有机相中,起到了较好的阻隔气体的作用;所述炭黑的微观形貌为球形,球形的比表面积大,与其他材料的接触面也大,从而增强了气密性,目数为2000~5000目;所述内润滑剂为长链多官能团酯,相比较常用的石蜡,硬脂酸、硬脂酸钙等,不会出现吐霜等问题,有很高的性价比;所述热稳定剂为有机锡类热稳定剂;所述增韧剂为sebs(氢化苯乙烯-丁二烯嵌段共聚物),耐寒性能好;所述偶联剂为硅烷偶联剂,提高有机相和无机相的相容性;气密性聚氨酯材料中还包括用于调色的色母。
取三组不同厚度的气密性聚氨酯和普通80a聚氨酯进行气体渗透性测试:
(1)测试标准:gb/t1038-2000;
(2)测试条件:测试温度40℃,测试气体为甲烷;
(3)样品数量:共2组,每组3个;
(4)测试设备:压差法气体渗透仪vac-v2;
测试结果如下:
由上述表格可知,气密性聚氨酯的气密性远好于普通80a聚氨酯。
如图1所示,一种管道修复用内衬管100,包括pet纤维层10,所述pet纤维层10的内外层均通过涂覆所述气密性聚氨酯材料形成气密性聚氨酯层20,该气密性聚氨酯层20通过将各组分混合,造粒,得到的粒子涂覆挤出在pet纤维层10的内外层形成,同时需要注意的是采用混合机混合各组分时,混合机的加料量控制在混合室空容积的50%~70%,该内衬管100的使用年限为40年;
一种管道修复方法,包括:(1)在待修复管道上开设两个开口;(2)将所述内衬管100从所述一个开口塞入所述待修复管道并从所述另一个开口拉出,如图2所示,内衬管100提前通过压成u型呈扁平化收卷在收卷架上,同时通过压成u型可以减小与待修复管道的接触面积,方便拖动,通过牵引机对内衬管100进行牵引从而穿过待修复管道;(3)堵住所述内衬管100的一端口,进一步的采用气囊堵住内衬管100的一端口,从另一端口吹入压缩空气使所述内衬管100完全紧密贴附在所述待修复管道的内壁上,之后切掉多余部分,修复完成;原来步骤(1)中开挖的两个开口则通过焊接或者连接新管道进行连接。
以上所述实施例仅是为充分说明本发明而所举的较佳的实施例,本发明的保护范围不限于此。本技术领域的技术人员在本发明基础上所作的等同替代或变换,均在本发明的保护范围之内。本发明的保护范围以权利要求书为准。