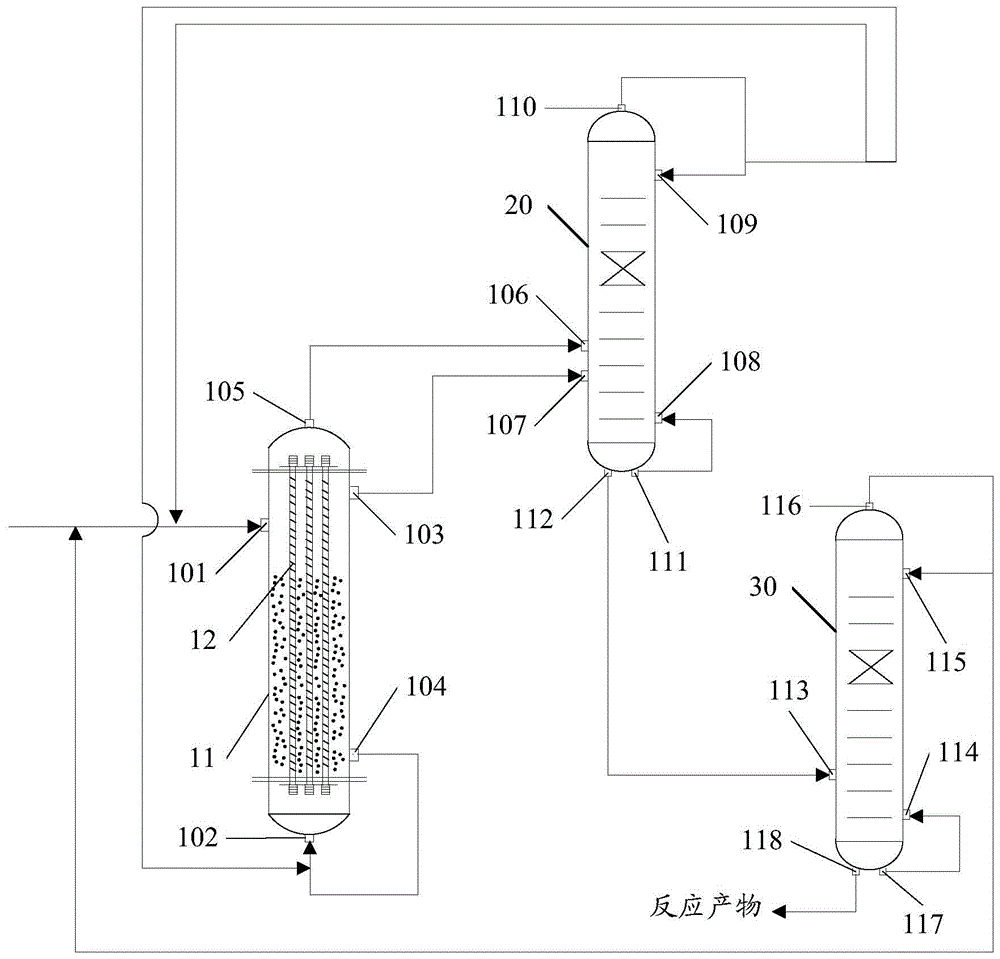
本发明涉及石油化工
技术领域:
。特别涉及一种以混合碳四为原料生产二异丁烯的方法及装置。
背景技术:
:异丁烯是一种重要的化工原料,主要用于合成mtbe(methyltert-butylether,甲基叔丁基醚)。mtbe由于具有较高的辛烷值,目前常用作汽油添加剂。并且,mtbe的抗震爆性好。但国家相关部门规定,未来将推广使用乙醇汽油,乙醇汽油中除乙醇外,其他有机含氧化合物含量不大于0.5%且不得人为加入,因此,mtbe作为有机含氧化合物,将不再被添加至汽油中。这种情况下,异丁烯的出路成为行业关注的焦点。经研究发现,异丁烯可以通过二聚反应生成二聚物二异丁烯,二异丁烯不是有机含氧化合物,且可以直接作为汽油添加剂,或者将二异丁烯加氢生成异辛烷,将异辛烷作为汽油添加剂。而如何通过异丁烯合成二异丁烯成为人们亟需解决的问题。相关技术如cn201711235599.7中主要是以混合碳四为原料通过加入抑制剂合成二异丁烯,混合碳四为含有四个碳原子的烃类混合物,除包括异丁烯外,还包括其他烃类如1-丁烯、2-丁烯等。相关技术中以混合碳四为原料生产二异丁烯的装置主要包括催化蒸馏塔、萃取塔、回收塔和两台反应器。其中,第一反应器和催化蒸馏塔连接,催化蒸馏塔分别与第二反应器和萃取塔连接,萃取塔和回收塔连接。混合碳四和抑制剂进入第一反应器,最后通过萃取塔输出二聚物二异丁烯。但相关技术中以混合碳四为原料生产二异丁烯的装置所用的设备较多,占地面积较大,导致生产成本高,投入大。技术实现要素:本发明实施例提供了一种以混合碳四为原料生产二异丁烯的方法及装置,能够解决以混合碳四为原料生产二异丁烯的装置所用设备较多,生产成本高,投入大的问题。具体技术方案如下:一方面,本发明实施例提供了一种以混合碳四为原料生产二异丁烯的装置,所述装置包括:管壳程叠合反应器、催化蒸馏塔、回收塔;所述管壳程叠合反应器包括管程反应器和壳程反应器,所述管程反应器位于所述壳程反应器内;所述壳程反应器一侧的中上部设有第一进料口,所述管程反应器的底部设有第二进料口,所述壳程反应器另一侧的中上部设有第一出料口,所述壳程反应器另一侧的中下部设有第二出料口,所述管程反应器的顶部设有第三出料口,所述第二进料口和所述第二出料口连接;所述催化蒸馏塔一侧的中下部设有第三进料口和第四进料口,所述催化蒸馏塔另一侧的下部设有第五进料口,所述催化蒸馏塔另一侧的上部设有第六进料口,所述催化蒸馏塔的顶部设有第四出料口,所述催化蒸馏塔的底部设有第五出料口和第六出料口;所述第四出料口分别与所述第一进料口、所述第二进料口和所述第六进料口连接,所述第五进料口和所述第五出料口连接;所述第一出料口和所述第四进料口连接,所述第三进料口和所述第三出料口连接;所述回收塔一侧的中下部设有第七进料口,所述回收塔另一侧的中下部设有第八进料口,所述回收塔另一侧的中上部设有第九进料口,所述回收塔的顶部设有第七出料口,所述回收塔的底部设有第八出料口和第九出料口;所述第七进料口和所述第六出料口连接,所述第八进料口和所述第八出料口连接,所述第七出料口分别与所述第一进料口和所述第九进料口连接;所述第一进料口用于输入第一反应物料,所述第九出料口用于输出反应产物,所述第一反应物料包括第一混合碳四、第二混合碳四和抑制剂,所述反应产物主要包括二异丁烯。在一种可能的实现方式中,所述装置还包括:原料预热器和产物冷却器;所述原料预热器的一端和所述第一进料口连接,所述原料预热器的另一端和第一输入管道连接;所述第一输入管道用于输入所述第一反应物料,所述原料预热器用于对所述第一混合碳四加热;所述产物冷却器的一端和所述第九出料口连接,所述产物冷却器的另一端和第一输出管道连接;所述第一输出管道用于输出所述反应产物。在另一种可能的实现方式中,所述装置还包括:壳程冷却器和壳程升压泵;所述壳程升压泵的一端和所述第二出料口连接,所述壳程升压泵的另一端和所述壳程冷却器的一端连接;所述壳程冷却器的另一端和所述第二进料口连接。在另一种可能的实现方式中,所述装置还包括:第一重沸器和第二重沸器;所述第一重沸器的一端和所述第五进料口连接,所述第一重沸器的另一端和所述第五出料口连接;所述第二重沸器的一端和所述第八进料口连接,所述第二重沸器的另一端和所述第八出料口连接。在另一种可能的实现方式中,所述装置还包括:第一冷凝器、第二冷凝器、第一回流泵、第二回流泵、第一回流罐和第二回流罐;所述第一冷凝器的一端和所述第四出料口连接,所述第一冷凝器的另一端和所述第一回流罐的一端连接,所述第一回流罐的另一端和所述第一回流泵的一端连接,所述第一回流泵的另一端分别与所述第一进料口、所述第二进料口、所述第六进料口和第二输出管道连接;所述第二冷凝器的一端和所述第七出料口连接,所述第二冷凝器的另一端和所述第二回流罐的一端连接,所述第二回流罐的另一端和所述第二回流泵的一端连接,所述第二回流泵的另一端分别与所述第一进料口和所述第九进料口连接;其中,所述第一回流泵的另一端通过第一调节阀和所述第一进料口连接;所述第一回流泵的另一端通过所述第二调节阀和所述第二进料口连接;所述第一调节阀用于调节进入所述第一进料口中第二混合碳四的进料量;所述第二调节阀用于调节进入所述第二进料口中第三混合碳四的进料量;所述第二混合碳四为经所述第一冷凝器、所述第一回流罐和所述第一回流泵输送至所述第一进料口的混合碳四;所述第三混合碳四为经所述第一冷凝器、所述第一回流罐经和所述第一回流泵输送至所述第二进料口的混合碳四;所述第二输出管道用于输出剩余混合碳四产品。在另一种可能的实现方式中,所述壳程反应器中装填有第一催化剂;所述管程反应器包括多个反应管,所述多个反应管在所述管程反应器中呈三角形排列,相邻两个反应管的管心之间的距离为100~500mm;对于每个反应管,所述反应管的高度为1000~15000mm,所述反应管的直径为50~250mm,所述反应管中装填有第二催化剂;所述反应管的两端设有筛网,所述筛网的筛缝尺寸小于所述第二催化剂颗粒的粒径;所述筛网的筛缝对应的流通面积不小于所述反应管的出口管对应的横截面积的两倍。在另一种可能的实现方式中,所述催化蒸馏塔包括第一精馏段、第一反应段和第一提馏段;所述第一精馏段包括15~25块塔板,所述第一提馏段包括25~35块塔板;所述回收塔包括第二精馏段和第二提馏段;所述第二精馏段包括10~15块塔板,所述第二提馏段包括20~30块塔板。另一方面,本发明实施例提供了一种以混合碳四为原料生产二异丁烯的方法,所述方法包括:将第一反应物料输送至管壳程叠合反应器中的壳程反应器,所述第一反应物料在第一催化剂存在的条件下发生二聚反应,得到第一混合物;所述第一反应物料包括第一混合碳四、第二混合碳四和抑制剂;所述第一混合物中包括反应产物和所述抑制剂;所述反应产物中主要包括二异丁烯;将第二反应物料输送至所述管壳程叠合反应器中的管程反应器,所述第二反应物料在第二催化剂存在的条件下发生二聚反应,得到第二混合物,所述第二反应物料包括所述第一混合物和第三混合碳四,所述第二混合物包括所述反应产物、所述抑制剂和第四混合碳四,所述第四混合碳四为所述第二反应物料在所述管程反应器中未反应的混合碳四;分别将所述第二混合物自第三出料口经第三进料口、所述第一反应物料在所述壳程反应器因汽化而产生的未反应的气相混合碳四自第一出料口经第四进料口输送至催化蒸馏塔中,所述第一反应物料在壳程反应器因汽化而产生的未反应的气相混合碳四以及所述第四混合碳四在所述催化蒸馏塔中发生二聚反应,得到第三混合物,所述第三混合物包括所述反应产物、抑制剂和第五混合碳四,所述第五混合碳四为经所述催化蒸馏塔的第一反应段未反应的混合碳四;所述第三混合物中的反应产物和抑制剂在所述催化蒸馏塔中与所述第五混合碳四分离,将分离后的所述第三混合物中的反应产物和所述抑制剂输送至回收塔;所述反应产物和所述抑制剂在所述回收塔中分离,所述反应产物作为产品输出,所述抑制剂循环使用,与所述第一混合碳四和所述第二混合碳四混合后作为所述第一反应物料输送至所述壳程反应器。在一种可能的实现方式中,所述方法还包括:将所述第五混合碳四分为四部分混合碳四,第一部分混合碳四回流至所述催化蒸馏塔中,第二部分混合碳四作为所述第二混合碳四,输送至所述壳程反应器,第三部分混合碳四作为所述第三混合碳四,输送至所述管程反应器,第四部分混合碳四作为剩余混合碳四产品输出。在另一种可能的实现方式中,所述分别将所述第二混合物自第三出料口经第三进料口、所述第一反应物料在所述壳程反应器因汽化而产生的气相混合碳四自第一出料口经第四进料口输送至催化蒸馏塔中,包括:将所述第二混合物自所述第三出料口经所述第三进料口输送至所述催化蒸馏塔第一提馏段的第4~10块塔板;将所述第一反应物料在所述壳程反应器因汽化而产生的未反应的气相混合碳四自所述第一出料口经所述第四进料口输送至所述催化蒸馏塔第一提馏段的第6~12块塔板。在另一种可能的实现方式中,所述壳程反应器中的反应压力为0.5~0.9mpa,反应温度为70~90℃,所述第一催化剂在所述壳程反应器中的空速为0.5~1h-1;所述管程反应器中的反应压力为1.5~2.5mpa,反应温度不大于120℃,所述第二催化剂在所述管程反应器中的空速为1~3h-1,且所述第二催化剂的装填量为所述管程反应器体积的65%~85%;所述催化蒸馏塔中第一反应段空速为1~3h-1,反应温度为60~80℃,反应压力为0.6~1.0mpa;所述回收塔中塔顶温度为60~90℃,塔底温度为160~190℃,操作压力为0.5~1.0mpa。在另一种可能的实现方式中,所述抑制剂和所述第一混合碳四中异丁烯的摩尔比为0.01~0.1:1;所述抑制剂为叔丁醇。在另一种可能的实现方式中,所述第一反应物料中第二混合碳四的质量为所述第一混合碳四质量的15%~75%;所述第二反应物料中第三混合碳四的质量为所述第一混合碳四质量的15%~75%。本发明实施例提供的技术方案带来的有益效果是:本发明实施例提供的以混合碳四为原料生产二异丁烯的装置,包括管壳程叠合反应器、催化蒸馏塔和回收塔;在生产二异丁烯时,通过第一进料口输入第一反应物料,第一反应物料包括第一混合碳四、第二混合碳四和抑制剂,通过第九出料口输出反应产物,该反应产物主要包括二异丁烯。该装置主要通过一台反应器和两台塔器生产二异丁烯,减少了生产二异丁烯所用的设备,减少了占地面积,降低了生产成本和投入。附图说明图1是本发明实施例提供的一种以混合碳四为原料生产二异丁烯的装置的示意图;图2是本发明实施例提供的另一种以混合碳四为原料生产二异丁烯的装置的示意图;图3是本发明实施例提供的一种以混合碳四为原料生产二异丁烯的方法的流程图。附图标记分别表示:10-管壳程叠合反应器,11-管程反应器,12-壳程反应器,20-催化蒸馏塔,30-回收塔,101-第一进料口,102-第二进料口,103-第一出料口,104-第二出料口,105-第三出料口,106-第三进料口,107-第四进料口,108-第五进料口,109-第六进料口,110-第四出料口,111-第五出料口,112-第六出料口,113-第七进料口,114-第八进料口,115-第九进料口,116-第七出料口,117-第八出料口,118-第九出料口,40-原料预热器,50-产物冷却器,60-壳程冷却器,70-壳程升压泵,80-第一重沸器,90-第二重沸器,201-第一冷凝器,202-第二冷凝器,203-第一回流泵,204-第二回流泵,205-第一回流罐,206-第二回流罐,207-第一调节阀,208-第二调节阀。具体实施方式为使本发明的技术方案和优点更加清楚,下面对本发明实施方式作进一步地详细描述。本发明实施例提供了一种以混合碳四为原料生产二异丁烯的装置,参见图1,该装置包括:管壳程叠合反应器10、催化蒸馏塔20和回收塔30;管壳程叠合反应器10包括管程反应器11和壳程反应器12,管程反应器11位于壳程反应器12内;壳程反应器12一侧的中上部设有第一进料口101,管程反应器11的底部设有第二进料口102,壳程反应器12另一侧的中上部设有第一出料口103,壳程反应器12另一侧的中下部设有第二出料口104,管程反应器11的顶部设有第三出料口105,第二进料口102和第二出料口104连接;催化蒸馏塔20一侧的中下部设有第三进料口106和第四进料口107,催化蒸馏塔20另一侧的下部设有第五进料口108,催化蒸馏塔20另一侧的上部设有第六进料口109,催化蒸馏塔20的顶部设有第四出料口110,催化蒸馏塔20的底部设有第五出料口111和第六出料口112;第四出料口110分别与第一进料口101、第二进料口102和第六进料口109连接,第五进料口108和第五出料口111连接;第一出料口103和第四进料口107连接,第三进料口106和第三出料口105连接;回收塔30一侧的中下部设有第七进料口113,回收塔30另一侧的中下部设有第八进料口114,回收塔30另一侧的中上部设有第九进料口115,回收塔30的顶部设有第七出料口116,回收塔30的底部设有第八出料口117和第九出料口118;第七进料口113和第六出料口112连接,第八进料口114和第八出料口117连接,第七出料口116分别与第一进料口101和第九进料口115连接;第一进料口101用于输入第一反应物料,第九出料口118用于输出与混合物中的叔丁醇分离的反应产物,第一反应物料包括第一混合碳四、第二混合碳四和抑制剂,反应产物主要包括二异丁烯。其中,壳程反应器12和管程反应器11用于异丁烯发生二聚反应,生成反应产物。催化蒸馏塔20用于将反应产物和抑制剂与混合碳四分离。第一出料口103用于输出第一反应物料因汽化而产生的未反应的气相第一混合碳四和未反应的气相第二混合碳四的混合物,第四进料口107用于输入未反应的气相混合碳四,该未反应的气相混合碳四包括未反应的气相第一混合碳四和未反应的气相第二混合碳四,第二出料口104用于输出壳程反应器12中反应得到的反应产物,第二进料口102用于输入壳程反应器12中反应得到的反应产物和第三混合碳四,即第二反应物料,第三出料口105用于输出第二混合物,第二混合物包括第四混合碳四、抑制剂和管程反应器11中反应得到的反应产物,第四混合碳四为第二反应物料在管程反应器中未反应的混合碳四,第三进料口106用于向催化蒸馏塔20中输入第二混合物。第四出料口110用于输出第五混合碳四,第五混合碳四为经催化蒸馏塔反应段未反应的混合碳四,第五出料口111用于输出反应产物与叔丁醇的混合物,第五进料口108用于将第五出料口111输出的混合物循环至催化蒸馏塔20中,第六出料口112用于输出反应产物和抑制剂的混合物,第七进料口113用于将第六出料口112输出的反应产物和抑制剂的混合物输入至回收塔30中,回收塔30用于将混合物中的反应产物和抑制剂分离。第五混合碳四为经催化蒸馏塔反应段未反应的混合碳四,第五混合碳四可以分为四部分混合碳四,第一部分混合碳四回流至催化蒸馏塔中,第二部分混合碳四作为第二混合碳四,输送至壳程反应器,第三部分混合碳四作为第三混合碳四,输送至管程反应器,第四部分混合碳四作为剩余混合碳四产品输出。第六进料口109用于将第五混合碳四中的第一部分混合碳四回流至催化蒸馏塔20中,第七出料口116用于输出与二异丁烯分离的叔丁醇,第八出料口117输出的二异丁烯及少量叔丁醇的混合物为液相,经第二重沸器90加热为气液两相后经第八进料口114返回回收塔30。第九进料口115用于将与二异丁烯分离的一部分叔丁醇回流至回收塔30中。第一混合碳四和第二混合碳四中不仅包括异丁烯,还包括其他烃类如1-丁烯、2-丁烯等。其中,第一混合碳四可以为蒸汽裂解产生的混合碳四,也可以为催化裂化产生的混合碳四。在本发明实施例中,对此不作具体限定。需要说明的一点是,二异丁烯易与叔丁醇形成共沸物,如果直接将二异丁烯和叔丁醇的共沸物作为产品输出,导致生成的二异丁烯纯度较低。并且,gb18351《车用乙醇汽油(e10)》与gb22030《车用乙醇汽油调合组分油》标准规定,乙醇汽油中除乙醇外,其他有机含氧化合物含量不大于0.5%且不得人为加入,而叔丁醇属于有机含氧化合物,不可直接添加到汽油中,因此,应将二异丁烯与叔丁醇分离。在本发明实施例中,通过本发明实施例提供的生产二异丁烯的装置,将从催化蒸馏塔20的第六出料口112输出的二异丁烯与叔丁醇的混合物输入至回收塔30中,在回收塔30中将该混合物分离,其中,二异丁烯作为产品从回收塔30的塔底输出,叔丁醇从回收塔30的塔顶输出,其中,一部分叔丁醇与第一混合碳四和第二混合碳四混合后作为第一反应物料循环使用,一部分叔丁醇回流至回收塔30中。从而实现了二异丁烯与叔丁醇的分离,提高了二异丁烯的纯度。另外,相关技术cn201711235599.7中在生产二异丁烯时,至少需要两台反应器。而在本发明实施例中,将壳程反应器12和管程反应器11整合为一个反应器,即管壳程叠合反应器10,从而可以减少设备的占地面积,降低生产成本和投入。在一种可能的实现方式中,进料口和出料口的位置可以根据需要进行选择并更改,进料口和出料口的尺寸也可以根据需要进行选择并更改,在本发明实施例中,对此不作具体限定。本发明实施例提供的以混合碳四为原料生产二异丁烯的装置,包括管壳程叠合反应器10、催化蒸馏塔20和回收塔30;在生产二异丁烯时,通过第一进料口101输入第一反应物料,第一反应物料包括第一混合碳四、第二混合碳四和抑制剂,通过第九出料口118输出反应产物,该反应产物主要包括二异丁烯。该装置主要通过一台反应器和两台塔器生产二异丁烯,减少了生产二异丁烯所用的设备,减少了占地面积,降低了生产成本和投入。在一种可能的实现方式中,参见图2,该装置还包括原料预热器40和产物冷却器50;原料预热器40的一端和第一进料口101连接,原料预热器40的另一端和第一输入管道连接;第一输入管道用于输入第一反应物料,原料预热器40用于对第一混合碳四加热;产物冷却器50的一端和第九出料口118连接,产物冷却器50的另一端和第一输出管道连接;第一输出管道用于输出反应产物。在本发明实施例中,第一混合碳四在进入壳程反应器12之前,通过原料预热器40加热,加热后的第一混合碳四通过第一输入管道进入壳程反应器12中,壳程反应器12中装填有第一催化剂,第一反应物料在第一催化剂的催化作用下发生反应。其中,第一混合碳四为从该装置外部输入的反应物料,第二混合碳四和抑制剂均为该装置循环利用的反应物料。产物冷却器50用于冷却反应产物,第一输出管道用于输出冷却后的反应产物。需要说明的一点是,异丁烯生成二异丁烯的反应为放热反应,因此,在反应过程中,通过控制壳程反应器12中的压力,使第一反应物料在相应压力的沸点下发生反应,反应热使第一反应物料呈气液混合状态,部分第一混合碳四和部分第二混合碳四因反应热而汽化,未反应的气相混合碳四从第一出料口103通过催化蒸馏塔20的第四进料口107进入催化蒸馏塔20中。未反应的气相混合碳四包括第一反应物料中因反应热而汽化的未反应的气相第一混合碳四和未反应的气相第二混合碳四。由于反应热用于第一反应物料的汽化,壳程反应器中反应温度基本保持不变,从而不需要单独在壳程反应器12外设置循环取热装置;而管程反应器11中的第二反应物料的反应热也被壳程反应器12中第一反应物料的汽化所吸收,也不需要单独在管程反应器11外设置循环取热装置;这样就消除了相关技术如申请(专利)号cn201711235599.7中固定床反应器外设置循环取热装置,循环的反应产物经外部冷却器冷却后返回反应器入口造成二聚物在反应器中浓度增加,以及随二聚物浓度增加,副产物三聚物、四聚物增多的弊端,可大幅度提高第一催化剂、第二催化剂床层的利用率,与固定床反应器装置相比可减少第一催化剂用量30%~40%。在一种可能的实现方式中,该装置还包括:壳程冷却器60和壳程升压泵70;壳程升压泵70的一端和第二出料口104连接,壳程升压泵70的另一端和壳程冷却器60的一端连接;壳程冷却器60的另一端和第二进料口102连接。在一种可能的实现方式中,壳程反应器12中的温度和压力与管程反应器11中的温度和压力不同。因此,第一混合物在进入管程反应器11中之前,可以通过壳程升压泵70和壳程冷却器60进行升压和降温。壳程升压泵70用于将第一混合物的压力升高至第一预设压力,壳程冷却器60用于将第一混合物的温度冷却至第一预设温度。在一种可能的实现方式中,该装置还包括:第一重沸器80和第二重沸器90;第一重沸器80的一端和第五进料口108连接,第一重沸器80的另一端和第五出料口111连接;第二重沸器90的一端和第八进料口114连接,第二重沸器90的另一端和第八出料口117连接。第五出料口111中输出的物料为液相物料,通过第一重沸器80加热汽化,当该物料的汽化率达到第一预设汽化率时,将该物料重新输送至催化蒸馏塔20中,为第一混合物与混合碳四的分离提供能量。相应的,第八出料口117中输出的物料也为液相物料,通过第二重沸器90加热汽化,当该物料达到第二预设汽化率时,将该物料重新输送至回收塔30中继续反应,为反应产物与抑制剂的分离提供能量。在一种可能的实现方式中,管程反应器11中包括多个反应管,多个反应管在管程反应器11中呈三角形排列,相邻两个反应管的管心之间的距离为100~500mm;对于每个反应管,反应管的高度为1000~15000mm,反应管的直径为50~250mm,反应管中装填有第二催化剂;反应管的两端设有筛网,筛网的筛缝尺寸小于第二催化剂颗粒的粒径;筛网的筛缝对应的流通面积不小于反应管的出口管对应的横截面积的两倍。其中,反应管的两端设有筛网可以防止催化剂从反应管两端泄漏,筛网的筛缝尺寸小于第二催化剂颗粒的粒径可以防止第二催化剂从筛缝中漏出。筛网的筛缝对应的流通面积较大,可有效地降低反应物料在反应管内压降,确保反应正常进行。需要说明的一点是,在本发明实施例中,筛网还可以承受整个第二催化剂床层的重量,从而避免在反应过程中第二催化剂漏出。并且,筛网的最大压降为0.1mpa。筛缝的尺寸可以根据需要进行设置并更改,在本发明实施例中,对筛缝的尺寸不作具体限定。例如,第二催化剂的最小颗粒直径为0.25mm,则筛缝的尺寸可以为0.15~0.16mm;第二催化剂的最小颗粒直径为0.23mm,则筛缝的尺寸可以为0.12~0.13mm。筛缝的形状可以根据需要进行设置并更改,例如,筛缝的尺寸可以为圆形、条形。在本发明实施例中,筛缝的尺寸为条形。第一混合物和第三混合碳四,也即第二反应物料在管程反应器11中进一步发生二聚反应,管程反应器11的反应管中装填有第二催化剂,在第二催化剂的催化作用下,第二反应物料在抑制剂的作用下进一步发生二聚反应。由于壳程反应器12位于管程反应器11外部,因此,管程反应器11中的反应热可以被壳程反应器12中的第一反应物料吸收。相较于相关技术固定床反应器循环取热所用的外循环泵和外循环冷却器,本发明实施例提供的装置可以减少设备数量,降低操作费用。在一种可能的实现方式中,该装置还包括:第一冷凝器201、第二冷凝器202、第一回流泵203、第二回流泵204、第一回流罐205和第二回流罐206;第一冷凝器201的一端和第四出料口110连接,第一冷凝器201的另一端和第一回流罐205的一端连接,第一回流罐205的另一端和第一回流泵203的一端连接,第一回流泵203的另一端分别与第一进料口101、第二进料口102、第六进料口109和第二输出管道连接;第二冷凝器202的一端和第七出料口116连接,第二冷凝器202的另一端和第二回流罐206的一端连接,第二回流罐206的另一端和第二回流泵204的一端连接,第二回流泵204的另一端分别与第一进料口101和第九进料口115连接;其中,第一回流泵203的另一端通过第一调节阀207和第一进料口101连接;第一回流泵203的另一端通过第二调节阀208和第二进料口102连接;第一调节阀207用于调节进入第一进料口101中第二混合碳四的进料量;第二调节阀208用于调节进入第二进料口102中第三混合碳四的进料量;第二混合碳四为经第一冷凝器、第一回流罐和第一回流泵输送至第一进料口的混合碳四;第三混合碳四为经第一冷凝器、第一回流罐和第一回流泵输送至第二进料口的混合碳四;第二输出管道用于输出剩余混合碳四产品。其中,可以通过循环水冷凝第四出料口110的物料以及第七出料口116的物料。第一进料口101和第一回流泵203之间可以通过一输送管道连接,在该输送管道上设置有第一调节阀207。其中,第一调节阀207用于调节进入第一进料口101中第二混合碳四的进料量,当壳程反应器12中第一反应物料的汽化量增大或异丁烯的转化率降低时,可以调大第一调节阀207,增大第二混合碳四的进料量;当第一反应物料的汽化量减少或异丁烯的转化率增大,生成副产物较多时,可以调小第一调节阀207,减少第二混合碳四的进料量。相应的,第二进料口102和第一回流泵203之间可以通过另一输送管道连接,在该输送管道上设置有第二调节阀208。其中,第二调节阀208用于调节进入第二进料口102中第三混合碳四的进料量,当管程反应器11的温度差增大或异丁烯的转化率降低时,可以调大第二调节阀208,增大第三混合碳四的进料量;当管程反应器11的温度差减少或异丁烯的转化率增大,生成副产物较多时,可以调小第二调节阀208,减少第三混合碳四的进料量。在一种可能的实现方式中,催化蒸馏塔20包括第一精馏段、第一反应段和第一提馏段;第一精馏段包括15~25块塔板,第一提馏段包括25~35块塔板;回收塔30包括第二精馏段和第二提馏段;第二精馏段包括10~15块塔板,第二提馏段包括20~30块塔板。壳程反应器12中未反应的气相混合碳四进入催化蒸馏塔20中第一提馏段的第6~12块塔板;管程反应器11中反应得到的第二混合物进入催化蒸馏塔20中第一提馏段的第4~10块塔板。在一种可能的实现方式中,未反应的气相混合碳四与第二混合物可以进入同一块塔板,也可以进入不同的塔板。在本发明实施例中,对此不作具体限定。例如,当未反应的气相混合碳四与第二混合物进入同一块塔板时,该塔板可以为第一提馏段的第6块塔板、第7块塔板或者第10块塔板。需要说明的一点是,在本发明实施例中,涉及的塔板的序号为自上而下排列时塔板对应的序号。在本发明实施例中,通过将相关技术如申请(专利)号cn201711235599.7中的第一反应器、第二反应器、第一反应器外循环泵以及外循环冷却器、第二反应器外循环泵以及外循环冷却器等多台设备整合为一台设备,即管壳程叠合反应器10,不但大幅度降低了设备和操作费用,还减少了设备占地面积。本发明实施例提供的以混合碳四为原料生产二异丁烯的装置,包括管壳程叠合反应器10、催化蒸馏塔20和回收塔30;在生产二异丁烯时,通过第一进料口101输入第一反应物料,第一反应物料包括第一混合碳四、第二混合碳四和抑制剂,通过第九出料口118输出反应产物,该反应产物主要包括二异丁烯。该装置主要通过一台反应器和两台塔器生产二异丁烯,减少了生产二异丁烯所用的设备,减少了占地面积,降低了生产成本和投入。本发明实施例提供了一种以混合碳四为原料生产二异丁烯的方法,参见图3,该方法包括:步骤301:将第一反应物料输送至管壳程叠合反应器中的壳程反应器,第一反应物料在第一催化剂存在的条件下发生二聚反应,得到第一混合物。第一反应物料包括第一混合碳四、第二混合碳四和抑制剂,第一混合物包括反应产物和抑制剂,反应产物中主要包括二异丁烯。第一混合碳四和第二混合碳四中的异丁烯发生二聚反应生成二异丁烯,但异丁烯在发生二聚反应时,可能还会发生三聚反应甚至四聚反应,生成三聚物甚至四聚物,导致反应产物中不仅包括二异丁烯,可能还包括少量的三聚物或者四聚物。而在本发明实施例中,通过抑制剂抑制异丁烯生成三聚物、四聚物,提高异丁烯生成二异丁烯的选择性,从而提高二异丁烯的产率。在一种可能的实现方式中,温度为30~40℃、压力为0.60~1.40mpa的第一混合碳四通过第一输入管道输入,通过原料预热器预热,经预热后第一混合碳四的温度为50~70℃。预热后的第一混合碳四、从催化蒸馏塔中输出且循环的、温度为45~55℃、压力为0.60~1.40mpa的第二混合碳四和从回收塔中输出且循环的、温度为45~55℃、压力为0.60~1.40mpa的抑制剂在第一输入管道中混合均匀后,通过第一进料口进入壳程反应器中。壳程反应器中的反应压力为0.5~0.9mpa,反应温度为70~90℃,壳程反应器中装填有第一催化剂,第一催化剂在壳程反应器中的空速为0.5~1h-1,第一混合碳四、第二混合碳四和抑制剂在第一催化剂的催化作用下发生二聚反应。其中,第一催化剂可以为大孔阳离子交换树脂催化剂,在本发明实施例中,对此不作具体限定。该空速可以为体积空速也可以为质量空速,在本发明实施例中,对此不作具体限定。在本发明实施例中,第二混合碳四可循环利用,第二混合碳四循环至壳程反应器中,可以调节壳程反应器中第一反应物料的汽化量或异丁烯的转化率。当壳程反应器中第一反应物料的汽化量增大或异丁烯的转化率降低时,可以增大第二混合碳四的循环量;当壳程反应器中第一反应物料的汽化量降低或异丁烯的转化率增大,生成副产物较多时,可以减少第二混合碳四的循环量。其中,第二混合碳四的循环质量为第一混合碳四质量的15%~75%。需要说明的一点是,异丁烯生成二异丁烯的反应为放热反应,在反应过程中,部分反应物料会吸收反应热汽化,因此,第一反应物料在壳程反应器中反应时,处于气液混合状态。在本发明实施例中,通过控制壳程反应器中的压力为0.5~0.9mpa,使反应在相应压力的沸点下进行。反应过程中,第一反应物料中部分混合碳四因吸收反应热而汽化,未反应的气相混合碳四从壳程反应器中的第一出料口进入催化蒸馏塔,从而使反应温度基本保持恒定,并且可大幅度提高催化剂的利用率。其中,未反应的气相混合碳四进入催化蒸馏塔时,进入催化蒸馏塔第一提馏段的第6~12块塔板。其中,未反应的气相混合碳四包括未反应的气相第一混合碳四和第二混合碳四。第一反应物料在壳程反应器中发生反应,得到第一混合物,第一混合物为液相物料,从壳程反应器下部的第二出料口输出,进入管程反应器中,在管程反应器中进一步发生二聚反应,从而提高异丁烯的转化率,提高二异丁烯的产率。相应的,在执行完步骤301后,执行步骤302。步骤302:将第二反应物料输送至管壳程叠合反应器中的管程反应器,第二反应物料在第二催化剂存在的条件下发生二聚反应,得到第二混合物。第二反应物料包括第一混合物和第三混合碳四,第二混合物包括反应产物、抑制剂和第四混合碳四,第四混合碳四为第二反应物料在管程反应器中未反应的混合碳四。壳程反应器中的温度和压力与管程反应器中的温度和压力不同,因此,第一混合物在进入管程反应器之前,可以先将其压力升高至第一预设压力,将其温度冷却至第一预设温度。经升压和冷却后的第一混合物与从催化蒸馏塔中输出的第三混合碳四一起自管程反应器的底部进入管程反应器的反应管中,在反应管中第二催化剂的催化作用下进一步发生二聚反应。在一种可能的实现方式中,第一混合物在壳程反应器中的压力为0.5~0.9mpa、温度为70~90℃。第一混合物在进入管程反应器之前,先将其压力升高至1.5~2.5mpa,再将其温度冷却至50~60℃。管程反应器中发生的二聚反应的反应热可以被壳程反应器中的第一反应物料吸收,从而可以避免单独设置外循环泵和外循环冷却器,降低设备和操作费用。在一种可能的实现方式中,管程反应器中的反应压力可以为1.5~2.5mpa,反应温度不大于120℃,且保证第一混合物和第三混合碳四,也即第二反应物料不在管程反应器中汽化。其中,可以通过控制管程反应器中的反应压力、壳程反应器中第一反应物料吸收管程反应器中的反应热,以及增加第三混合碳四的循环量实现第一混合物和第三混合碳四,也即第二反应物料不在管程反应器中汽化。管程反应器中包括多个反应管,每个反应管中装填有第二催化剂,第二催化剂在反应管中的空速1~3h-1,且第二催化剂的装填量为管程反应器体积的65%~85%。其中,第一混合物和第三混合碳四,也即第二反应物料在第二催化剂的催化作用下进一步发生二聚反应。在反应过程中,第二催化剂床层处于膨胀状态,第二催化剂颗粒有不规则的自转和轻微扰动,整个第二催化剂床层压降小且恒定,第二催化剂床层径向温度分布均匀,不存在局部热点,从而有利于抑制副产物的生成。第一催化剂和第二催化剂可以相同或者不同。例如,第一催化剂和第二催化剂相同。当第一催化剂和第二催化剂相同时,第一催化剂和第二催化剂可以均为大孔阳离子交换树脂催化剂。需要说明的一点是,第三混合碳四可循环利用,第三混合碳四循环作为反应物料,可以调节管程反应器中的温度差或异丁烯的转化率。当管程反应器中的温度差增大或异丁烯的转化率降低时,可以增大第三混合碳四的循环量;当管程反应器中的温度差降低或异丁烯的转化率增大,生成副产物较多时,可以减少第三混合碳四的循环量。其中,第三混合碳四的质量为第一混合碳四质量的15%~75%。步骤303:分别将第二混合物自第三出料口经第三进料口、第一反应物料在壳程反应器因汽化而产生的未反应的气相混合碳四自第一出料口经第四进料口输送至催化蒸馏塔中,第一反应物料在壳程反应器因汽化而产生的未反应的气相混合碳四以及该第四混合碳四在催化蒸馏塔中发生二聚反应,得到第三混合物。第三混合物包括反应产物、抑制剂和第五混合碳四,第五混合碳四为经催化蒸馏塔的第一反应段未反应的混合碳四。在一种可能的实现方式中,第二混合物可以自第三出料口经第三进料口输送至催化蒸馏塔中第一提馏段的第4~10块塔板,第一反应物料在壳程反应器因汽化而产生的未反应的气相混合碳四自第一出料口经第四进料口输送至催化蒸馏塔中第一提馏段的第6~12块塔板。其中,第二混合物、未反应的气相混合碳四在催化蒸馏塔中可以同时发生反应和分离,抑制剂和反应产物中的二聚物、三聚物等可以从催化蒸馏塔的塔底排出,进入回收塔。其中,催化蒸馏塔的催化蒸馏作用可以将反应热直接用于反应产物、抑制剂与第五混合碳四的分离,从而降低能耗;并且,容易控制反应温度,没有明显的局部热点,不需要额外增加冷却设备。另外,还可以使反应产物二聚物及时从第一反应段分离,降低了副产物的生成,提高了二聚物的产率。在一种可能的实现方式中,催化蒸馏塔中第一反应段空速为1~3h-1,反应温度为60~80℃,反应压力为0.6~1.0mpa,通过控制催化蒸馏塔的反应温度和反应压力可以使反应产物、抑制剂与未反应的混合碳四分离。在一种可能的实现方式中,第五混合碳四在催化蒸馏塔中经催化蒸馏后,可以分为四部分混合碳四;第一部分混合碳四回流至催化蒸馏塔中,第二部分混合碳四作为第二混合碳四,输送至壳程反应器,第三部分混合碳四作为第三混合碳四,输送至管程反应器,第四部分混合碳四作为剩余混合碳四产品输出。在另一种可能的实现方式中,催化蒸馏塔塔底的部分液相物料可以通过第一重沸器加热,达到第一预设汽化率时,返回催化蒸馏塔中为上述分离提供能量。第一预设汽化率可以根据需要进行设置并更改,例如第一预设汽化率可以为0.15~0.35之间的任一值。在本发明实施例中,对此不作具体限定。步骤304:第三混合物中的反应产物和抑制剂在催化蒸馏塔中与第五混合碳四分离,将分离后的第三混合物中的反应产物和抑制剂输送至回收塔;反应产物和抑制剂在回收塔中分离,反应产物作为产品输出,抑制剂循环使用,与第一混合碳四和第二混合碳四混合后作为第一反应物料输送至壳程反应器。反应产物和抑制剂进入回收塔后,在回收塔中分离,其中反应产物从回收塔塔底输出,抑制剂从回收塔塔顶输出分为两部分,一部分抑制剂回流至回收塔中,另一部分抑制剂与第一混合碳四和第二混合碳四混合后作为第一反应物料,循环利用。反应产物中主要包括二聚物二异丁烯,还包括副产物三聚物、四聚物等。输出的反应产物可以输入至汽油加氢脱硫装置,在加氢饱和后作为高辛烷值汽油添加剂输出装置;或者,输入至催化裂化主分馏塔进行二聚物、三聚物以及四聚物的分离,其中,二聚物、三聚物作为汽油添加剂、四聚物作为柴油添加剂输出装置;或者,输入至新建的烯烃加氢饱和装置,在加氢饱和后得到异辛烷,异辛烷作为高辛烷值汽油添加剂输出装置。在本发明实施例中,可根据具体情况进行选择,对此不作具体限定。在一种可能的实现方式中,回收塔中塔顶温度为60~90℃,塔底温度为160~190℃,操作压力为0.5~1.0mpa。塔底物料经产物冷却器冷却至40~45℃后输出。抑制剂从回收塔塔顶输出,经第二冷凝器冷却至45~55℃后,进入第二回流罐,再经第二回流泵升压至0.60~1.40mpa后分为两部分。在一种可能的实现方式中,回收塔塔底的部分液相物料可以通过第二重沸器加热,达到第二预设汽化率时,返回回收塔中为上述分离提供能量。第二预设汽化率可以根据需要进行设置并更改,例如第二预设汽化率可以为0.15~0.35之间的任一值。在本发明实施例中,对此不作具体限定。需要说明的一点是,抑制剂对异丁烯的转化率具有很大的影响。随着抑制剂的增加,其覆盖第一催化剂或第二催化剂活性中心的比例相应增加,从而降低了三聚物、四聚物的生成,提高了二聚物的产率。但过量的抑制剂会降低异丁烯的转化率,因此,在本发明实施例中,抑制剂与第一混合碳四中异丁烯的摩尔比可以为0.01~0.1:1。并且,抑制剂可以根据需要进行选择并更改,在本发明实施例中,对此不作具体限定。例如,抑制剂可以为叔丁醇。本发明实施例提供的以混合碳四为原料生产二异丁烯的方法,以混合碳四为原料发生二聚反应,在反应过程中通过抑制剂抑制副产物的生成,提高二异丁烯的产率,并且通过将二异丁烯和抑制剂分离,将二异丁烯作为产品输出,添加到汽油中,不仅解决了异丁烯的出路,还生成了高辛烷值的汽油添加剂。以下将通过具体实施例对本发明的技术方案进行详细说明。实施例1温度为40℃、压力为0.80mpa、进料量为20000kg/h的第一混合碳四通过第一输入管道输入,通过原料预热器预热至65℃。预热后的第一混合碳四、从催化蒸馏塔中输出且循环的,温度为50℃、压力为0.80mpa、进料量为10000kg/h的第二混合碳四和从回收塔中输出且循环的,温度为50℃、压力为0.80mpa、进料量为700kg/h的叔丁醇这三股物料作为第一反应物料混合均匀后,进入壳程反应器中。壳程反应器中装填有大孔阳离子交换树脂催化剂,大孔阳离子交换树脂催化剂在壳程反应器中的空速为0.75h-1。壳程反应器中的反应压力为0.7mpa,反应温度为72℃,反应热使第一反应物料呈气液混合状态,未反应的第一混合碳四和第二混合碳四从壳程反应器的第一出料口进入催化蒸馏塔第一提馏段的第8块塔板。温度为72℃、压力为0.7mpa的第一混合物经壳程升压泵升压至1.8mpa,由壳程冷却器冷却至60℃。经升压、冷却后的第一混合物与温度为50℃、压力为1.8mpa、进料量为10000kg/h的第三混合碳四这两股物料作为第二反应物料一起自管程反应器的底部进入管程反应器中。其中,管程反应器中包括96根反应管,每根反应管的高度为14000mm、直径为200mm,从管程反应器的横截面上看呈正三角形排布。每根反应管中装填有大孔阳离子交换树脂催化剂,大孔阳离子交换树脂催化剂在管程反应器中的空速为2.0h-1。第二反应物料在大孔阳离子交换树脂催化剂的作用下进一步发生二聚反应。催化蒸馏塔中的第一精馏段设有17块塔板,第一反应段空速为2h-1,反应温度为80℃,反应压力为0.8mpa;第一提馏段设有28块塔板。温度为95℃、压力为1.75mpa、进料量为38950kg/h的第二混合物进入催化蒸馏塔第一提馏段的第5块塔板。叔丁醇和反应产物中的二聚物、三聚物等从催化蒸馏塔的塔底排出,进入回收塔。未反应的第一混合碳四和第二混合碳四,以及未反应的第三混合碳四移动至催化蒸馏塔的第一精馏段,然后离开催化蒸馏塔塔顶,经第一冷凝器冷凝至50℃后进入催化蒸馏塔第一回流罐,经第一回流泵升压至1.9mpa后分为四部分混合碳四;第一部分混合碳四进料量为10000kg/h,回流至催化蒸馏塔中,第二部分混合碳四进料量为10000kg/h,输送至壳程反应器作为第二混合碳四,第三部分混合碳四进料量为10000kg/h,输送至管程反应器作为第三混合碳四,第四部分混合碳四进料量为14200kg/h,作为剩余混合碳四产品输出。回收塔塔底温度为195℃、操作压力为0.85mpa,总进料量为6500kg/h的反应产物和叔丁醇同时进入回收塔中,在回收塔中分离。回收塔中的第二精馏段设有12块塔板、第二提馏段设有24块塔板。塔顶温度为87℃、塔底温度为166℃,操作压力为0.6mpa。回收塔塔底输出的反应产物出料量为5800kg/h,经产物冷却器冷却至40℃后进入汽油加氢脱硫装置,加氢饱和后作为高辛烷值汽油添加剂输出装置。叔丁醇从回收塔塔顶输出,经第二冷凝器冷却至50℃后进入第二回流罐,由第二回流泵升压至0.90mpa,分为两部分;第一部分进料含叔丁醇5500kg/h,回流至回收塔中,第二部分进料含叔丁醇700kg/h作为第一反应物料循环至壳程反应器。对比例温度为40℃、压力为0.80mpa、进料量为20000kg/h的第一混合碳四和温度为50℃、压力为0.80mpa、进料量为700kg/h的叔丁醇在第一固定床反应器中进行反应,反应产物一部分进入催化蒸馏塔,另一部分通过换热器移除反应热后返回至第一固定床反应器;经催化蒸馏后,催化蒸馏塔中反应产物进入第二固定床反应器,在第二固定床反应器中反应后回流至催化蒸馏塔中,催化蒸馏塔塔底的反应产物进入萃取塔。经萃取后,萃取塔塔顶的反应产物可以进行后续处理,萃取塔塔底的萃取剂和叔丁醇进入回收塔;经回收后,叔丁醇返回至第一固定床反应器。需要说明的一点是,实施例和对比例中所用物料的性质和工程条件完全相同,要求的产品性质也完全相同。以下从工程消耗、所需设备情况、相对占地面积以及投入等方面对实施例和对比例进行比较,参见表1。表1序号项目实施例对比例一能量消耗对比蒸汽消耗量4.46t/h4.97t/h循环水消耗量267t/h281t/h二所需主要设备情况对比管壳程叠合反应器1台0壳程升压泵1台0壳程冷却器1台0第一固定床反应器01台第一固定床反应器外循环泵01台第一固定床反应器外循环冷却器01台催化蒸馏塔1台1台第二固定床反应器01台回收塔1台1台萃取塔01台三占地面积对比相对占地面积1.01.21四投入对比相对投入1.01.16从表1中可以看出:实施例中的蒸汽消耗量与循环水消耗量均小于对比例。对于所用主要设备,实施例中仅需要1台反应器,而对比例需要2台反应器;实施例中需要2台塔器,而对比例需要3台塔器。另外,从占地面积和投入方面来看,实施例也小于对比例。综上所述,本发明实施例提供的以混合碳四为原料生产二异丁烯的装置所用设备较少,占地面积也较少,投入较少。以上所述仅是为了便于本领域的技术人员理解本发明的技术方案,并不用以限制本发明。凡在本发明的精神和原则之内,所作的任何修改、等同替换、改进等,均应包含在本发明的保护范围之内。当前第1页12