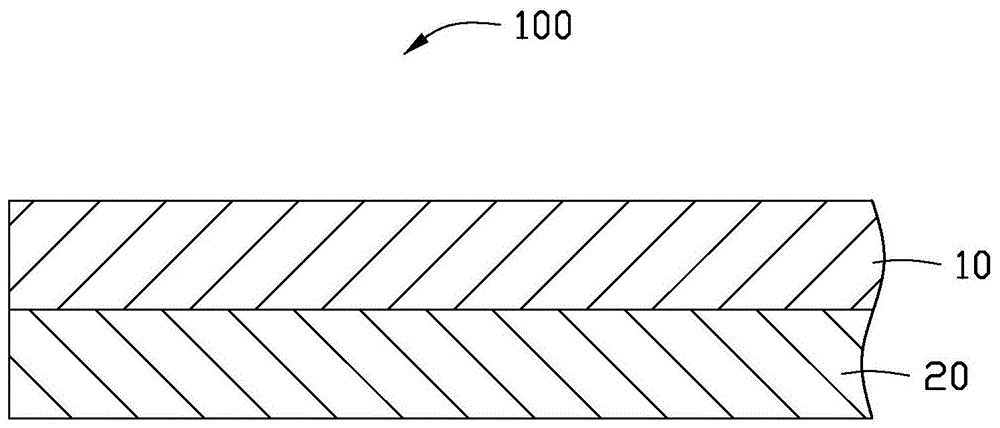
本发明涉及一种聚酰胺酸嵌段共聚物及其制备方法,由所述聚酰胺酸嵌段共聚物环化制得的聚酰亚胺覆铜板及应用所述聚酰亚胺覆铜板制得的电路板。
背景技术:
:近年来,印刷电路板被广泛应用于各种电子产品上。目前,用于制备印刷电路板的覆铜板通常包括铜箔、聚酰亚胺膜、及位于铜箔与聚酰亚胺膜之间用于将铜箔与聚酰亚胺膜结合在一起的胶粘层。然而,现有的聚酰亚胺膜与表面粗糙度较低的铜箔的结合力较低,使用表面粗糙度较低的铜箔制作覆铜板时,铜箔与聚酰亚胺膜的结合力较低。而且,现有的聚酰亚胺膜在热压中会出现较大的变形,且软化温度ts高,韧性差,不易压合。同时,现有的聚酰亚胺膜剥离强度差、介电损耗高等问题。技术实现要素:有鉴于此,有必要提供一种介电损耗低、剥离强度高、韧性好且易于压合的聚酰亚胺膜的聚酰胺酸嵌段共聚物的制备方法,以解决以上问题。另,还有必要提供一种由所述聚酰胺酸嵌段共聚物环化制得的聚酰亚胺覆铜板。另,还有必要提供一种应用所述聚酰亚胺覆铜板制得的电路板。一种聚酰胺酸嵌段共聚物的制备方法,包括步骤:提供第一种二酸酐单体和第二种二酸酐单体,所述第一种二酸酐单体和所述第二种二酸酐单体分别包括液晶性基团和柔性基团。提供第一种二胺单体和第二种二胺单体,所述第一种二胺单体和所述第二种二胺单体分别包括液晶性基团和柔性基团。混合所述第一种二酸酐单体和所述第二种二胺单体以使其缩合形成第一种酰胺链段。混合所述第二种二酸酐单体和所述第一种二胺单体以使其缩合形成第二种酰胺链段。混合所述第一种酰胺链段和所述第二种酰胺链段以使其发生共聚反应,从而得到所述聚酰胺酸嵌段共聚物。进一步地,所述液晶性基团包括多个芳香环及键接所述多个芳香环的桥键结构,所述芳香环包括中的至少一种;所述桥键结构包括中的至少一种。进一步地,含有所述液晶性基团的二酸酐单体为3,3',4,4'-联苯四羧酸二酐、对苯基二(偏苯三酸酯)二酸酐及环己烷-1,4-二基双(亚甲基)双(1,3-二氧代-1,3-二氢异苯并呋喃-5-羧酸乙酯)中的至少一种,其中,所述3,3',4,4'-联苯四羧酸二酐的结构式为所述对苯基二(偏苯三酸酯)二酸酐的结构式为所述环己烷-1,4-二基双(亚甲基)双(1,3-二氧代-1,3-二氢异苯并呋喃-5-羧酸乙酯)的结构式为:进一步地,含有所述液晶性基团的二胺单体为对氨基苯甲酸对氨基苯酯、1,4-双(4-氨基苯氧基)苯及对苯二甲酸二对氨基苯酯中的至少一种;其中,所述对氨基苯甲酸对氨基苯酯的结构式为:所述1,4-双(4-氨基苯氧基)苯的结构式为:所述对苯二甲酸二对氨基苯酯的结构式为:进一步地,所述柔性基团包括长链饱和脂肪烃基、长链不饱和脂肪烃基或醚基,所述长链是包括四个或四个以上碳原子的直链烃。进一步地,含有所述柔性基团的二酸酐单体为4,4'-氧双邻苯二甲酸酐、2,3,3',4'-二苯醚四甲酸二酐、3,3',4,4'-二苯甲酮四甲酸二酐、3,3,4,4-二苯基砜四羧酸二酸酐、六氟二酐及双酚a型二醚二酐中的至少一种;其中,所述4,4'-氧双邻苯二甲酸酐的结构式为:所述2,3,3',4'-二苯醚四甲酸二酐的结构式为:所述3,3',4,4'-二苯甲酮四甲酸二酐的结构式:为所述3,3,4,4-二苯基砜四羧酸二酸酐的结构式为:所述六氟二酐的结构式为:所述双酚a型二醚二酐的结构式为进一步地,含有所述柔性基团的二胺单体为4,4'-二氨基二苯醚、4,4'-二(4-氨基苯氧基)联苯、2,2'-双[4-(4-氨基苯氧基苯基)]丙烷、2,2-双[4-(4-氨基苯氧基)苯基]-1,1,1,3,3,3-六氟丙烷、1,3-双(4'-氨基苯氧基)苯及1,3-双(3-氨基苯氧基)苯中的至少一种;其中,所述4,4'-二氨基二苯醚的结构式为:所述4,4'-二(4-氨基苯氧基)联苯的结构式为:所述2,2'-双[4-(4-氨基苯氧基苯基)]丙烷的结构式为:所述2,2-双[4-(4-氨基苯氧基)苯基]-1,1,1,3,3,3-六氟丙烷的结构式为:所述1,3-双(4'-氨基苯氧基)苯的结构式为:所述1,3-双(3-氨基苯氧基)苯的结构式为:一种由上述备方法制备的聚酰胺酸嵌段共聚物,所述聚酰胺酸嵌段共聚物的分子链包括交替排列的第一种酰胺链段及第二种酰胺链段,所述第一种酰胺链段包括液晶性基团,所述第二种酰胺链段包括柔性基团。一种覆铜板,包括铜箔及结合于所述铜箔的表面的聚酰亚胺膜,所述聚酰亚胺膜由如上所述的聚酰胺酸嵌段共聚物涂布在所述铜箔的表面后环化形成。一种电路板,包括电路基板,所述电路基板包括聚酰亚胺膜及结合在所述聚酰亚胺膜至少一表面的导电线路层,所述聚酰亚胺膜由如上所述的聚酰胺酸嵌段共聚物涂布在所述导电线路层的表面后经环化形成。本发明提供的聚酰胺酸嵌段共聚物通过改变含柔性基团单体与含液晶性基团单体的聚合反应顺序从而提高聚酰亚胺膜的可加工性、剥离强度,同时还可以提高应电性。附图说明图1是本发明一较佳实施例的覆铜板的截面示意图。图2是由图1所示的覆铜板制得的电路板的截面示意图。主要元件符号说明聚酰亚胺覆铜板100铜箔10聚酰亚胺膜20电路板200电路基板201导电线路层2011覆盖膜202如下具体实施方式将结合上述附图进一步说明本发明。具体实施方式本发明实施方式提供一种聚酰胺酸嵌段共聚物的制备方法,包括步骤:步骤一:提供第一种二酸酐单体和第二种二酸酐单体,所述第一种二酸酐单体和所述第二种二酸酐单体分别包括液晶性基团和柔性基团。步骤二:提供第一种二胺单体和第二种二胺单体,所述第一种二胺单体和所述第二种二胺单体分别包括液晶性基团和柔性基团。步骤三:混合所述第一种二酸酐单体和所述第二种二胺单体以使其缩合形成第一种酰胺链段。步骤四:混合所述第二种二酸酐单体和所述第一种二胺单体以使其缩合形成第二种酰胺链段。步骤五:混合所述第一种酰胺链段和所述第二种酰胺链段以使其发生共聚反应,从而得到所述聚酰胺酸嵌段共聚物。在步骤一和步骤二中,第一种二酸酐单体和所述第一种二胺单体所包括的液晶性基团可以相同,也可以不同。所述第二种二酸酐单体和所述二胺单体所包括的柔性基团可以相同,也可以不同。在步骤三中,所述第一种二酸酐单体和所述第二种二胺单体在一溶剂中进行混合。所述溶剂为双极性的质子惰性溶剂。优选地,所述双极性的质子惰性溶剂选自为二甲基甲酰胺(dmf)、二甲基乙酰胺(dmac)、n-甲基吡咯烷酮(nmp)、二甲基亚砜(dmso)中至少一种。所述溶剂的重量占整体质量75%~85%。所述第一种二酸酐单体或所述第二种二胺单体的加入量为0.01~0.1mol。在步骤四中,所述第二种二酸酐单体或所述第一种二胺单体的加入量为0.01~0.1mol,且所述第一种二酸酐单体、第二种酸酐单体与所述第一种二胺单体、第二种二胺单体的摩尔比为1:1。进一步地,所述液晶性基团包括多个芳香环及键接所述多个芳香环的桥键结构,所述芳香环包括中的至少一种;所述桥键结构包括中的至少一种。进一步地,含有所述液晶性基团的二酸酐单体为3,3',4,4'-联苯四羧酸二酐、对苯基二(偏苯三酸酯)二酸酐及环己烷-1,4-二基双(亚甲基)双(1,3-二氧代-1,3-二氢异苯并呋喃-5-羧酸乙酯)中的至少一种,其中,所述3,3',4,4'-联苯四羧酸二酐的结构式为所述对苯基二(偏苯三酸酯)二酸酐的结构式为(p-phenylenebis(trimellitate)dianhydride,tahq),所述环己烷-1,4-二基双(亚甲基)双(1,3-二氧代-1,3-二氢异苯并呋喃-5-羧酸乙酯)的结构式为:进一步地,含有所述液晶性基团的二胺单体为对氨基苯甲酸对氨基苯酯、1,4-双(4-氨基苯氧基)苯及对苯二甲酸二对氨基苯酯中的至少一种;其中,所述对氨基苯甲酸对氨基苯酯的结构式为:(4-aminobenzoicacid4-aminophenylester,apab),所述1,4-双(4-氨基苯氧基)苯的结构式为:所述对苯二甲酸二对氨基苯酯的结构式为:进一步地,所述柔性基团包括长链饱和脂肪烃基、长链不饱和脂肪烃基或醚基,所述长链是包括四个或四个以上碳原子的直链烃。进一步地,含有所述柔性基团的二酸酐单体为4,4'-氧双邻苯二甲酸酐、2,3,3',4'-二苯醚四甲酸二酐、3,3',4,4'-二苯甲酮四甲酸二酐、3,3,4,4-二苯基砜四羧酸二酸酐、六氟二酐及双酚a型二醚二酐中的至少一种;其中,所述4,4'-氧双邻苯二甲酸酐的结构式为:(4,4′-oxydiphthalicanhydride,odpa),所述2,3,3',4'-二苯醚四甲酸二酐的结构式为:所述3,3',4,4'-二苯甲酮四甲酸二酐的结构式:为所述3,3,4,4-二苯基砜四羧酸二酸酐的结构式为:所述六氟二酐的结构式为:所述双酚a型二醚二酐的结构式为(4,4'-(4,4'-isopropylidenediphenoxy)bis-(phthalicanhydride),bpada)。进一步地,含有所述柔性基团的二胺单体为4,4'-二氨基二苯醚、4,4'-二(4-氨基苯氧基)联苯、2,2'-双[4-(4-氨基苯氧基苯基)]丙烷、2,2-双[4-(4-氨基苯氧基)苯基]-1,1,1,3,3,3-六氟丙烷、1,3-双(4'-氨基苯氧基)苯及1,3-双(3-氨基苯氧基)苯中的至少一种;其中,所述4,4'-二氨基二苯醚的结构式为:所述4,4'-二(4-氨基苯氧基)联苯的结构式为:(4,4'-bis(4-aminophenoxy)biphenyl,bapb),所述2,2'-双[4-(4-氨基苯氧基苯基)]丙烷的结构式为:(4,4'-(4,4'-isopropylidenediphenyl-1,1'-diyldioxy)dianiline,bapp),所述2,2-双[4-(4-氨基苯氧基)苯基]-1,1,1,3,3,3-六氟丙烷的结构式为:(2,2-bis[4-(4-aminophenoxy)phenyl]hexafluoropropane,hfbapp),所述1,3-双(4'-氨基苯氧基)苯的结构式为:所述1,3-双(3-氨基苯氧基)苯的结构式为:(1,3-bis(3-aminophenoxy)benzene,tpe-m)。本发明实施方式还提供一种由上述备方法制备的聚酰胺酸嵌段共聚物,所述聚酰胺酸嵌段共聚物的分子链包括交替排列的第一种酰胺链段及第二种酰胺链段,所述第一种酰胺链段包括液晶性基团,所述第二种酰胺链段包括柔性基团。本发明实施方式还提供一种聚酰胺酸嵌段共聚物的制备方法,包括步骤:步骤一:提供第一种二酸酐单体和第二种二酸酐单体,所述第一种二酸酐单体和所述第二种二酸酐单体分别包括液晶性基团和柔性基团。步骤二:提供第一种二胺单体和第二种二胺单体,所述第一种二胺单体和所述第二种二胺单体分别包括液晶性基团和柔性基团。步骤三:混合所述第一种二酸酐单体和所述第一种二胺单体以使其缩合形成第一种酰胺链段。步骤四:混合所述第二种二酸酐单体和所述第二种二胺单体以使其缩合形成第二种酰胺链段。步骤五:混合所述第一种酰胺链段和所述第二种酰胺链段以使其发生共聚反应,从而得到所述聚酰胺酸嵌段共聚物。在步骤一和步骤二中,第一种二酸酐单体和所述第一种二胺单体所包括的液晶性基团可以相同,也可以不同。所述第二种二酸酐单体和所述二胺单体所包括的柔性基团可以相同,也可以不同。在步骤三、步骤四及步骤五中,酸酐单体和二胺单体在一溶剂中进行混合。所述溶剂为双极性的质子惰性溶剂。优选地,所述双极性的质子惰性溶剂选自为二甲基甲酰胺(dmf)、二甲基乙酰胺(dmac)、n-甲基吡咯烷酮(nmp)、二甲基亚砜(dmso)中至少一种。所述溶剂的重量占整体质量75%~85%。在步骤三种,所述第一种二酸酐单体或所述第一种二胺单体的加入量为0.01~0.1mol。在步骤四中,所述第二种二酸酐单体或所述第二种二胺单体的加入量为0.01~0.1mol。进一步地,所述液晶性基团包括多个芳香环及键接所述多个芳香环的桥键结构,所述芳香环包括中的至少一种;所述桥键结构包括中的至少一种。进一步地,所述柔性基团包括长链饱和脂肪烃基、长链不饱和脂肪烃基或醚基,所述长链是包括四个或四个以上碳原子的直链烃。本发明实施方式还提供一种由上述制备方法制备的聚酰胺酸嵌段共聚物,所述聚酰胺酸嵌段共聚物的主链包括多个重复排列的酰胺链段,每一所述酰胺链段包括液晶性基团和柔性基团,在重复排列的所述酰胺链段上,所述液晶性基团及所述柔性基团交替排列。请结合参阅图1~2,一种聚酰亚胺覆铜板100,其用于制作电路板200。所述聚酰亚胺覆铜板100包括铜箔10及结合于所述铜箔10一表面的聚酰亚胺膜20。所述铜箔10的表面具有较低的粗糙度。其中,所述铜箔10的表面粗糙度在0.12um~2.1um之间。所述聚酰亚胺膜20通过将上述聚酰胺酸嵌段共聚物涂布在所述铜箔10的表面后经高温环化形成。其中,所述聚酰胺酸嵌段共聚物经高温环化形成所述聚酰亚胺膜20的原理为:因所述聚酰胺酸嵌段共聚物包括含有氮杂环的二胺单体,所述含有氮杂环的二胺单体中的氮杂环上的氮原子可与所述铜箔10产生配位作用,从而使得所述聚酰亚胺膜20与所述铜箔10之间具有较强的结合力。如此,可以使用表面粗糙度较低的铜箔10来制作聚酰亚胺覆铜板100,这样可以使在铜箔10表面所形成的聚酰亚胺膜20的表面较为平整,从而使得该聚酰亚胺膜20具有较高的透光度。其中,所述聚酰亚胺覆铜板100的所述铜箔10与所述聚酰亚胺膜20直接结合在一起,所述铜箔10与所述聚酰亚胺膜20之间未设置胶粘层,如此可以进一步提高所述聚酰亚胺膜20的透光度,并且可以节约成本。一种上述聚酰亚胺覆铜板100的制作方法:提供铜箔10,所述铜箔10的表面粗糙度在0.12μm~2.1μm之间。提供聚酰胺酸嵌段共聚物,将所述聚酰胺酸嵌段共聚物涂布在所述铜箔10的表面。高温环化,使所述铜箔10表面的聚酰胺酸嵌段共聚物高温下脱水而进行死循环,得到结合在铜箔10表面的聚酰亚胺膜20,即制得所述聚酰亚胺覆铜板100。其中,所述高温环化的温度范围大致为300~400℃。本发明还提供一种聚酰亚胺膜20,所述聚酰亚胺膜20通过将所述聚酰胺酸嵌段共聚物涂覆在基材的表面后经高温环化形成。其中,所述基材可以为离型膜、金属箔、树脂等常规应用于制备聚酰亚胺膜的基材。在高温环化过程中,所述聚酰胺酸嵌段共聚物会在高温下脱水而进行死循环,从而得到结合在基材表面的聚酰亚胺膜20。请参阅图2,一种电路板200,其应用于计算机、电子阅读器、平板计算机、智能手表等电子装置(图未示)上。该电路板200包括电路基板201及覆盖在该电路基板201至少一表面的覆盖膜202。该电路基板201包括所述聚酰亚胺膜20及结合在所述聚酰亚胺膜20至少一表面的导电线路层2011。所述导电线路层2011通过对聚酰亚胺覆铜板100的铜箔10图案化所形成。所述覆盖膜202结合于所述导电线路层2011的远离所述聚酰亚胺膜20的表面。下面通过具体实施例进一步对本发明的聚酰胺酸嵌段共聚物进行说明。实施例1于500ml反应瓶中分别加入nmp(211.10g)、apab(0.05mol,11.41g),待高速搅拌至溶解后,再加入odpa(0.05mol,15.51g)搅拌反应1小时后,再加入tpe-m(0.05mol,14.62g),待高速搅拌至溶解后,再加入tahq(0.05mol,22.93g)搅拌反应48小时,即配置完成聚酰胺酸嵌段共聚物。实施例2于500ml反应瓶中分别加入nmp(209.14g)、apab(0.05mol,11.41g),待高速搅拌至溶解后,再加入odpa(0.025mol,7.76g)、bpada(0.025mol,13.01g)搅拌反应1小时后,再加入tpe-m(0.05mol,14.62g),待高速搅拌至溶解后,再加入tahq(0.05mol,22.93g)搅拌反应48小时,即配置完成聚酰胺酸嵌段共聚物。实施例3于500ml反应瓶中分别加入nmp(224.91g)、apab(0.05mol,11.41g),待高速搅拌至溶解后,再加入bpada(0.05mol,26.02g)搅拌反应1小时后,再加入tpe-m(0.05mol,14.62g),待高速搅拌至溶解后,再加入tahq(0.05mol,22.93g)搅拌反应48小时,即配置完成聚酰胺酸嵌段共聚物。实施例4于500ml反应瓶中分别加入nmp(233.92g)、apab(0.025mol,5.71g)、bptp(0.025mol,8.71g),待高速搅拌至溶解后,再加入bpada(0.05mol,26.02g)搅拌反应1小时后,再加入tpe-m(0.05mol,14.62g),待高速搅拌至溶解后,再加入tahq(0.05mol,22.93g)搅拌反应48小时,即配置完成聚酰胺酸嵌段共聚物。实施例5于500ml反应瓶中分别加入nmp(235.43g)、apab(0.025mol,5.71g)、bapb(0.025mol,9.21g),待高速搅拌至溶解后,再加入bpada(0.05mol,26.02g)搅拌反应1小时后,再加入tpe-m(0.05mol,14.62g),待高速搅拌至溶解后,再加入tahq(0.05mol,22.93g)搅拌反应48小时,即配置完成聚酰胺酸嵌段共聚物。实施例6于500ml反应瓶中分别加入nmp(246.68g)、apab(0.025mol,5.71g)、hfbapp(0.025mol,12.96g),待高速搅拌至溶解后,再加入bpada(0.05mol,26.02g)搅拌反应1小时后,再加入tpe-m(0.05mol,14.62g),待高速搅拌至溶解后,再加入tahq(0.05mol,22.93g)搅拌反应48小时,即配置完成聚酰胺酸嵌段共聚物。比较例1于500ml反应瓶中分别加入nmp(260.76g)和hfbapp(0.10mol,41.05g),待高速搅拌至溶解后,再加入tahq(0.10mol,45.87g)搅拌反应48小时,即配置完成聚酰胺酸嵌段共聚物。比较例2于500ml反应瓶中分别加入nmp(227.29g)、apab(0.05mol,11.41g),待高速搅拌至溶解后,再加入tahq(0.05mol,22.93g)搅拌反应1小时后,再加入hfbapp(0.05mol,25.92g),待高速搅拌至溶解后,再加入odpa(0.05mol,15.51g)搅拌反应48小时,即配置完成聚酰胺酸嵌段共聚物。比较例3于500ml反应瓶中分别加入nmp(211.10g)、apab(0.05mol,11.41g),待高速搅拌至溶解后,再加入tahq(0.05mol,22.93g)搅拌反应1小时后,再加入bapp(0.05mol,20.53g),待高速搅拌至溶解后,再加入odpa(0.05mol,15.51g)搅拌反应48小时,即配置完成聚酰胺酸嵌段共聚物。比较例4于500ml反应瓶中分别加入nmp(211.10g)、apab(0.05mol,11.41g),待高速搅拌至溶解后,再加入tahq(0.05mol,22.93g)搅拌反应1小时后,再加入tpe-m(0.05mol,14.62g),待高速搅拌至溶解后,再加入odpa(0.05mol,15.51g)搅拌反应48小时,即配置完成聚酰胺酸嵌段共聚物。比较例5于500ml反应瓶中分别加入nmp(209.14g)、apab(0.05mol,11.41g),待高速搅拌至溶解后,再加入tahq(0.05mol,22.93g)搅拌反应1小时后,再加入tpe-m(0.05mol,14.62g),待高速搅拌至溶解后,再加入odpa(0.025mol,7.76g)、bpada(0.025mol,13.01g)搅拌反应48小时,即配置完成聚酰胺酸嵌段共聚物。比较例6于500ml反应瓶中分别加入nmp(224.91g)、apab(0.05mol,11.41g),待高速搅拌至溶解后,再加入tahq(0.05mol,22.93g)搅拌反应1小时后,再加入tpe-m(0.05mol,14.62g),待高速搅拌至溶解后,再加入bpada(0.05mol,26.02g)搅拌反应48小时,即配置完成聚酰胺酸嵌段共聚物。比较例7于500ml反应瓶中分别加入nmp(233.92g)、apab(0.025mol,5.71g)、bptp(0.025mol,8.71g),待高速搅拌至溶解后,再加入tahq(0.05mol,22.93g)搅拌反应1小时后,再加入tpe-m(0.05mol,14.62g),待高速搅拌至溶解后,再加入bpada(0.05mol,26.02g)搅拌反应48小时,即配置完成聚酰胺酸嵌段共聚物。比较例8于500ml反应瓶中分别加入nmp(235.43g)、apab(0.025mol,5.71g)、bapb(0.025mol,9.21g),待高速搅拌至溶解后,再加入tahq(0.05mol,22.93g)搅拌反应1小时后,再加入tpe-m(0.05mol,14.62g),待高速搅拌至溶解后,再加入bpada(0.05mol,26.02g)搅拌反应48小时,即配置完成聚酰胺酸嵌段共聚物。比较例9于500ml反应瓶中分别加入nmp(246.68g)、apab(0.025mol,5.71g)、hfbapp(0.025mol,12.96g),待高速搅拌至溶解后,再加入tahq(0.05mol,22.93g)搅拌反应1小时后,再加入tpe-m(0.05mol,14.62g),待高速搅拌至溶解后,再加入bpada(0.05mol,26.02g)搅拌反应48小时,即配置完成聚酰胺酸嵌段共聚物。由实施例1~6及比较例1~9制得的聚酰胺酸嵌段共聚物环化后形成聚酰亚胺膜的投料组分及含量如表一所示,聚酰亚胺膜在覆铜板的剥离强度、漂锡性、热性质、介电常数及介质损耗的测试结果如表二所示。表一:表二:通过分析表一及表二可知:(一)分析实施例1~6和对应的比较例4-9,可以发现,由实施例中1~6中聚酰胺酸嵌段共聚物制得的聚酰亚胺膜的剥离强度提高、软化温度(ts)降低、介电常数(dk)降低及介电损耗(df)也降低。即,通过改变含柔性基团单体与含液晶性基团单体的聚合反应顺序可以达到提高聚酰亚胺膜的可加工性、剥离强度,同时还可以提高应电性。(二)分析比较例1及比较例2~9,可以发现,聚酰亚胺膜的剥离强度、软化温度、介电常数及介电损耗均可通过改变单体的组分及比例来实现调节,从而可以生产出符合特定要求的聚酰亚胺膜。(三)实施例6及比较例9导入含f结构的hfbapp,介电常数较低,推测为hfbapp具有疏水性的f元素,及庞大的侧链基团所导致。(四)比较例6相较比较例4有较低的ts温度,推测为bpada相较odpa具有较多的醚基结构;其中比较例4相较比较例3有较低的软化温度,推测为bapp及tpe-m含醚基结构的比例较多,并且tpe-m为非线性结构,阻碍分子间的排列性,进而成功降低ts温度。另外,对于本领域的普通技术人员来说,可以根据本发明的技术构思做出其它各种相应的改变与变形,而所有这些改变与变形都应属于本发明权利要求的保护范围。当前第1页12