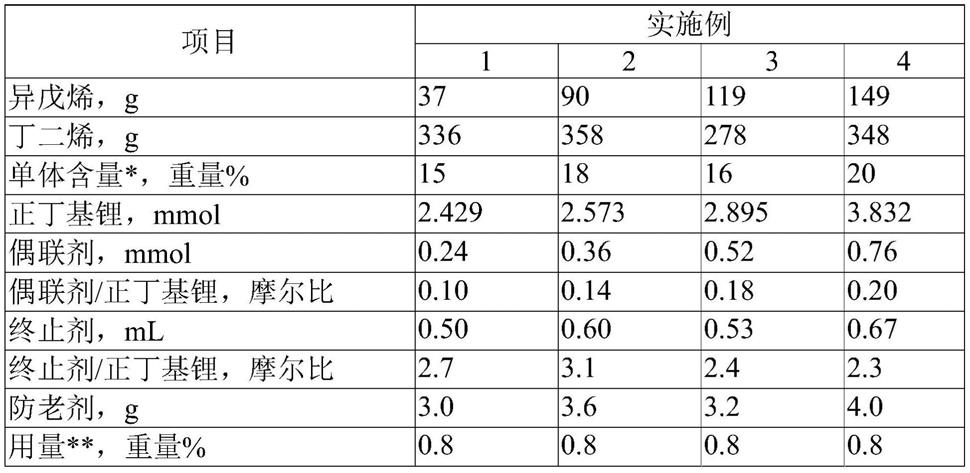
1.本发明涉及丁二烯-异戊二烯共聚物制备领域,具体地,涉及一种无规丁二烯-异戊二烯共聚物的合成方法,该合成方法制得的无规丁二烯-异戊二烯共聚物以及包含该共聚物的低滚阻汽车轮胎胎面胶。
背景技术:2.从丁戊橡胶(丁二烯-异戊二烯共聚物)产品的性能特点来看,具有无规分布的丁戊橡胶是一类有特点的产品。当汽车轮胎的胎侧胶中加入丁戊橡胶后,胎侧胶的抗裂口增长性能有所提高;丁戊橡胶用于组成汽车轮胎的胎面胶时,又可以提高胎面较的耐疲劳性并且可以降低滚动阻力。
3.无规度是丁二烯-异戊二烯共聚物合成方法的重要研究方面。无规共聚是指两单体聚合时随机的在共聚分子主链上排布,分子链上不存在某种单体所形成的较长的嵌段,这样分子间的对称性和分子链的化学规整性会被破坏,从而可以降低共聚物的结晶能力甚至形成完全不结晶共聚物,这样有利于低温耐寒的性能。
4.目前,无规丁二烯-苯乙烯共聚物的合成方法通常是加入结构调节剂或者采用稀土催化体系条件下进行聚合。
5.us20050004333公开了一种制备丁二烯和异戊二烯无规共聚物的方法,包括在丁二烯和异戊二烯存在下与催化体系的反应,特征在于其包括:使用一种体系作为催化体系,该体系基于至少:一种共轭的二烯单体,一种或多种稀土金属的有机磷酸盐,包含分子式为alr3或halr2的烷基铝的烷基化试剂,和包含卤化烷基铝的卤素给体,所述盐为在至少一种惰性、饱和的和脂肪族或脂环族烃溶剂的悬浮液中,该溶剂包含在所述催化体系中,且“烷基化试剂∶稀土盐”的摩尔比为1至8,和在惰性烃聚合反应溶剂或没有该溶剂下进行共聚合反应。
6.us20050222348公开了具有1,4-反式结构的无规丁二烯-异戊二烯共聚物,具有丁二烯/异戊二烯的摩尔组成范围为从98/2至32/68,上述共聚物为结晶或无定型取决于异戊二烯含量。合成的方法包括通过在一种或多种溶剂和催化系统存在下进行1,3-丁二烯和异戊二烯共聚,其特征在于:上述催化体系包括:(a)第一成分由钒化合物选自:(a1)化合物具有通式(ia)的vo(l)
n
(x)
m
其中n是从1至3的整数和m为从零至2,n+m等于2或3;(a2)化合物具有通式(ib)v(l)
p
(x)
q
其中p为从1至4的整数,q范围从零至3,p+q的总和等于3或4;其中l是二齿配位体,和x是卤素,优选为氯;(b)选自铝氧烷和相关衍生物的第二成分。用稀土催化体系合成高顺式或高反式的丁二烯-异戊二烯无规共聚物。
7.cn1269371a公开了一种共轭二烯和/或单乙烯基芳烃聚合物的制备方法,该方法包括在下列通式(a)所示的结构调节剂存在下,以有机锂为引发剂,在惰性溶剂中,于0-150℃温度范围内,引发聚合共轭二烯和/或单乙烯基芳烃得聚合物,
其中:r1,r2,r3相互之间可以相同或不同,并各自独立地为烷基;n为1-4的正整数;其中结构调节剂与有机锂的摩尔比范围为0.01∶1-40∶1。
8.以上技术是通过改进催化剂或者加入结构调节剂的技术措施实现合成具有无规分布的丁二烯-异戊二烯共聚物,需要另外开发专用催化剂或结构调节剂,技术难度和研制成本较高,工业生产不方便。而且现有工业中,单体进料的浓度只能达到10-13重量%,生产效率较低。因此,需要一种更有效的生产方法。
技术实现要素:9.本发明的目的是为了解决如何提高丁二烯与异戊二烯共聚时单体进料含量,以及改进获得丁二烯-异戊二烯共聚物无规分布的问题,提供了无规丁二烯-异戊二烯共聚物及其合成方法和低滚阻汽车轮胎胎面胶。采用该共聚物制备的汽车轮胎胎面胶具有滚动阻力低的特点。
10.为了实现上述目的,本发明第一方面提供一种无规丁二烯-异戊二烯共聚物的合成方法,包括:
11.(1)在氮气保护且无调节剂的条件下,向惰性溶剂和有机锂引发剂的混料中加入丁二烯单体与异戊二烯单体的混合物进行共聚反应,控制所述混合物在10-40min内完成所述加入,然后再经过5-40min完成所述共聚反应;
12.其中,以惰性溶剂、有机锂引发剂和所述混合物的总重量为基准,所述共聚反应中所述混合物的含量为15-20重量%;
13.(2)将步骤(1)得到的活性丁戊聚合产物进行偶联和终止,并加入防老剂,得到无规丁二烯-异戊二烯共聚物。
14.本发明第二方面提供一种本发明的合成方法制得的无规分布丁二烯-异戊二烯共聚物。
15.本发明第三方面提供了一种低滚阻汽车轮胎胎面胶,所述胎面胶包含本发明的无规分布丁二烯-异戊二烯共聚物。
16.通过上述技术方案,本发明改进加料方式,将单体混合物加入含有催化剂的溶剂中,并控制单体混合物的进料时间,使得实现单体总量的含量达到15-18重量%仍可以进行丁二烯和异戊二烯的共聚反应。并且可以实现不使用结构调节剂且无需更换催化剂体系即可制备获得具有无规分布(异戊二烯嵌段在链段中含量低)的丁二烯-异戊二烯共聚物,该共聚物用于汽车轮胎胎面胶可以具有低滚阻的性能。
17.本发明的其它特征和优点将在随后的具体实施方式部分予以详细说明。
具体实施方式
18.在本文中所披露的范围的端点和任何值都不限于该精确的范围或值,这些范围或值应当理解为包含接近这些范围或值的值。对于数值范围来说,各个范围的端点值之间、各个范围的端点值和单独的点值之间,以及单独的点值之间可以彼此组合而得到一个或多个
新的数值范围,这些数值范围应被视为在本文中具体公开。
19.本发明第一方面提供一种无规丁二烯-异戊二烯共聚物的合成方法,包括:
20.(1)在氮气保护且无调节剂的条件下,向惰性溶剂和有机锂引发剂的混料中加入丁二烯单体与异戊二烯单体的混合物进行共聚反应,控制所述混合物在10-40min内完成所述加入,然后再经过5-40min完成所述共聚反应;
21.其中,以惰性溶剂、有机锂引发剂和所述混合物的总重量为基准,所述共聚反应中所述混合物的含量为15-20重量%;
22.(2)将步骤(1)得到的活性丁戊聚合产物进行偶联和终止,并加入防老剂,得到无规丁二烯-异戊二烯共聚物。
23.本发明中,在共聚反应的加料方式上采取了先将丁二烯单体与异戊二烯单体混合成混合物,然后加入含有催化剂的惰性溶剂中,并且控制该含有单体的混合物原料进行加入的时间,该时间从该混合物开始通入含有催化剂的惰性溶剂中算起,到完成所述混合物全部投料结束。上述单体加料完成后,共聚反应再继续进行5-40min后结束。优选地,所述丁二烯单体与异戊二烯单体在20-30min内完成进料,再经过10-30min完成所述共聚反应。
24.在本发明的具体实施方式中,所述共聚反应的过程从单体混合物完成所述加入开始,先进行第一反应阶段达到最高温度;然后从最高温度开始至共聚反应结束完成第二反应阶段。共聚反应的时间相应地从所述加入丁二烯单体与异戊二烯单体的混合物完成后开始计时,控制完成第一反应阶段的时间-i,再控制在共聚反应达到最高温度后继续完成第二反应阶段的时间-ii,所述共聚反应的时间包括从加完单体混合物开始计时到共聚反应结束,具体包括时间-i和时间-ii,总和在5-40min,优选10-30min内。结束共聚反应的同时取样测丁二烯和异戊二烯单体的转化率。
25.根据本发明,优选地,步骤(1)中,所述丁二烯单体与异戊二烯单体的质量比为70:30-90:10。
26.根据本发明,在所述共聚反应过程中,如前所述的加料方式和控制所述混合物的加入时间,丁二烯单体与异戊二烯单体的共聚反应逐渐进行,反应过程的温度可以有效控制,可以有效实现无规丁二烯-异戊二烯共聚物的获得。共聚反应过程中存在自放热现象,本发明中优选限定引发开始共聚反应时的温度,优选地,所述共聚反应的引发温度为25-120℃;优选为55-95℃。
27.根据本发明,优选限定开始进行共聚反应时的表压压力,优选地,所述共聚反应的表压压力为0.1-0.5mpa。
28.根据本发明提供的方法,实现所述共聚反应过程中提高单体原料的加入浓度。即共聚反应体系中,单体总量的含量可以相较于现有技术提高,从而提高反应效率。所述混合物的含量是指所述丁二烯单体与异戊二烯单体的重量总和,在惰性溶剂、有机锂引发剂、丁二烯单体与异戊二烯单体的重量总和中所占的重量百分含量。优选地,步骤(1)中,所述共聚反应中所述混合物的含量为15-18重量%。
29.根据本发明,优选地,当所述有机锂引发剂选自正丁基锂和/或仲丁基锂。
30.根据本发明,优选地,所述有机锂引发剂的用量以li计为0.1-5mmol/100g单体总量,所述单体总量为所述丁二烯单体与异戊二烯单体的总和。
31.本发明中,所述惰性溶剂可以选自环己烷、环戊烷、正己烷、正庚烷等。所述惰性溶
剂可以是含有两种以上溶剂的混合溶剂。优选地,所述惰性溶剂进行除水。所述除水的方式可以为所述惰性溶剂中加入除水剂。所述除水剂的种类为本领域技术人员公知,例如可以为购自大连康宇化工有限公司的5a分子筛。
32.根据本发明,优选地,所述偶联的过程为:将所述活性丁戊聚合产物与偶联剂进行偶联反应;其中,所述偶联剂选自烷基卤化物,偶联反应时间为5-40min,偶联反应温度为60-80℃。
33.优选地,所述偶联剂的用量满足所述偶联剂与所述有机锂引发剂中锂的摩尔比为0.05-0.25:1,优选为0.1-0.2:1。
34.根据本发明,优选地,所述终止的过程为:将所述偶联得到的产物与终止剂进行终止反应;其中,所述终止剂选自水或醇类;终止反应时间为5-30min,终止反应温度为50-80℃。
35.优选地,所述终止剂的用量满足所述终止剂与所述有机锂引发剂中锂的摩尔比为0.5-5:1。
36.根据本发明,所述防老剂可以为本领域的常规选择。优选地,步骤(3)中,所述防老剂选自酚类防老剂和/或磷酸酯类防老剂。所述防老剂的用量也可以为本领域的常规用量。例如,以所述终止步骤得到的聚合物的重量为基准,所述防老剂的用量可以为所述活性丁戊聚合物产物的0.1-2重量%,优选为0.2-1重量%。
37.本发明中,在加入防老剂后,得到的产物可以通过纯化沉淀、离心分离、过滤、倾析、热水凝聚等方法从溶液中沉淀出来,也可以采用气提法将反应体系中的溶剂去除,对此本领域技术人员均能知悉,在此不再赘述。
38.本发明第二方面提供一种本发明的合成方法制得的无规分布丁二烯-异戊二烯共聚物。
39.根据本发明,优选地,以所述共聚物的总量为基准,所述共聚物中,异戊二烯嵌段的含量低于0.5重量%。
40.本发明提供的无规分布丁二烯-异戊二烯共聚物优选数均分子量为28万-36万。
41.本发明第三方面提供了一种低滚阻汽车轮胎胎面胶,所述胎面胶包含本发明的无规分布丁二烯-异戊二烯共聚物。
42.根据本发明,优选地,所述胎面胶在动态黏弹谱60℃时的损耗因子tanδ低于0.075。
43.以下将通过实施例对本发明进行详细描述。
44.共聚物中异戊二烯嵌段含量采用瑞士bruker公司avance drx 400mhz核磁振动波谱仪测定,样品在常温下用氘代氯仿(内含1%的tms)溶解配制成2-3%(w/v)溶液,以tms为零定标计算化学位移,室温下测试。
45.共聚物的数均分子量通过gpc(日本东曹公司的hlc-8320型凝胶渗透色谱仪)测试。
46.以下实施例和对比例按照表1所列条件制备丁二烯-异戊二烯共聚物产品。
47.实施例1
48.将混合惰性溶剂(环己烷和正己烷,重量比为88:12)用5a分子筛(购自大连康宇化工有限公司,预先在500℃下烘5h)浸泡1周。
49.(1)在高纯氮气保护下,先依次向5升聚合釜中加入混合溶剂2100g、正丁基锂溶液20ml(正丁基锂的浓度为0.1437mol/l),然后将聚合釜升温至共聚反应的温度为60℃,共聚反应的表压压力0.1mpa;
50.然后将37g异戊二烯与336g丁二烯的混合物(丁二烯:异戊二烯的质量比约为90:10)缓慢向聚合釜内进料,控制加料速度,在30min内加完该混合物,再继续共聚反应10min;达到最高温度为77℃,反应压力为0.35mpa,并在达到最高温度后继续共聚反应10min至结束,同时取样测丁二烯和异戊二烯单体的转化率均大于99.9%;共聚反应的时间共为20min,得到活性丁戊聚合产物;
51.(2)在反应压力为0.20mpa,将四氯化硅溶液10ml(0.043mol/l)加入反应釜内与聚合产物接触在72℃下进行偶联反应10min;
52.再加入0.5ml异丙醇在62℃下进行终止反应,搅拌15min后,加入3.0g防老剂2,6-二叔丁基对甲基苯酚(活性丁戊聚合产物的0.8重量%)。
53.得到的聚合反应胶液经过水蒸汽凝聚后,经开炼机干燥后得到丁二烯-异戊二烯共聚物产品。将产品进行结构测试,结果见表3。
54.实施例2
55.将混合惰性溶剂(环己烷和正己烷,重量比为88:12)用5a分子筛(购自大连康宇化工有限公司,预先在500℃下烘5小时)浸泡1周。
56.(1)在高纯氮气保护下,先依次向5升聚合釜中加入混合溶剂2100g、正丁基锂溶液24ml(正丁基锂的浓度为0.1437mol/l),然后将聚合釜升温至共聚反应的温度为50℃,共聚反应的表压压力为0.2mpa;
57.然后将90g异戊二烯与358g丁二烯的混合物(丁二烯:异戊二烯的质量比约为80:20)缓慢向聚合釜内进料,控制加料速度,在30min内加完该混合物,再继续共聚反应20min;达到最高温度为80℃,反应压力为0.37mpa,并在达到最高温度后继续共聚反应10min至结束,同时取样测丁二烯和异戊二烯单体的转化率均大于99.9%;共聚反应的时间为30min,得到活性丁戊聚合产物;
58.(2)在反应压力为0.21mpa,将四氯化硅溶液12ml(0.043mol/l)加入反应釜内与聚合产物接触在75℃下进行偶联反应5min;
59.再加入0.6ml异丙醇在65℃下进行终止反应,搅拌15min后,加入3.6g防老剂2,6-二叔丁基对甲基苯酚(活性丁戊聚合产物的0.8重量%)。
60.得到的聚合反应胶液经过水蒸汽凝聚后,经开炼机干燥后得到丁二烯-异戊二烯共聚物产品。将产品进行结构测试,结果见表3。
61.实施例3
62.将混合惰性溶剂(环己烷和正己烷,重量比为88:12)用5a分子筛(购自大连康宇化工有限公司,预先在500℃下烘5小时)浸泡1周。
63.(1)在高纯氮气保护下,先依次向5升聚合釜中加入混合溶剂2100g、正丁基锂溶液21ml(正丁基锂的浓度为0.1437mol/l),然后将聚合釜升温至共聚反应的温度55℃,共聚反应的表压压力为0.1mpa;
64.然后将119g异戊二烯与278g丁二烯的混合物(丁二烯:异戊二烯的质量比约为70:30)缓慢向聚合釜内进料,控制加料速度,在25min内加完该混合物,再继续共聚反应10min;
达到最高温度为76℃,反应压力为0.28mpa,并在达到最高温度继续共聚反应20min至结束,同时取样测丁二烯和异戊二烯单体的转化率均大于99.9%;共聚反应的时间共为30min,得到活性丁戊聚合产物;
65.(2)在反应压力为0.18mpa,将四氯化硅溶液11ml(0.043mol/l)加入反应釜内与聚合产物接触在71℃下进行偶联反应10min;
66.再加入0.53ml异丙醇在61℃下进行终止反应,搅拌15min后,加入3.2g防老剂2,6-二叔丁基对甲基苯酚(活性丁戊聚合产物的0.8重量%)。
67.得到的聚合反应胶液经过水蒸汽凝聚后,经开炼机干燥后得到丁二烯-异戊二烯共聚物产品。将产品进行结构测试,结果见表3。
68.实施例4
69.将混合惰性溶剂(环己烷和正己烷,重量比为88:12)用5a分子筛(购自大连康宇化工有限公司,预先在500℃下烘5小时)浸泡1周。
70.(1)在高纯氮气保护下,先依次向5升聚合釜中加入混合溶剂2100g、正丁基锂溶液27ml(正丁基锂的浓度为0.1437mol/l),然后将聚合釜升温至共聚反应的温度为45℃,共聚反应的表压压力为0.3mpa;
71.然后将149g异戊二烯与348g丁二烯的混合物缓慢向聚合釜内进料,控制加料速度,在10min内加完该混合物,再继续共聚反应5min;达到最高温度为80℃,反应压力为0.24mpa,并在达到最高温度后继续共聚反应10min至结束,同时取样测丁二烯和异戊二烯单体的转化率均大于99.8%;共聚反应的时间共15min,得到活性丁戊聚合产物;
72.(2)在反应压力为0.16mpa,将四氯化硅溶液13ml(0.043mol/l)加入反应釜内与聚合产物接触在75℃下进行偶联反应10min;
73.再加入0.67ml异丙醇在65℃下进行终止反应,搅拌15min后,加入4.0g防老剂2,6-二叔丁基对甲基苯酚(活性丁戊聚合产物的0.8重量%)。
74.得到的聚合反应胶液经过水蒸汽凝聚后,经开炼机干燥后得到丁二烯-异戊二烯共聚物产品。将产品进行结构测试,结果见表3。
75.对比例1
76.将混合惰性溶剂(环己烷和正己烷,重量比为88:12)用5a分子筛(购自大连康宇化工有限公司,预先在500℃下烘5小时)浸泡1周。
77.(1)在高纯氮气保护下,先依次向5升聚合釜中加入混合溶剂2100g、异戊二烯37g,丁二烯336g;然后将聚合釜升温至共聚引发温度为55℃,反应压力为0.2mpa;
78.然后再加入正丁基锂溶液20ml(正丁基锂的浓度为0.1437mol/l)引发进行共聚反应。聚合反应15min反应压力为0.45mpa,达到最高温度106℃后再继续进行反应10min至结束,同时取样测丁二烯和异戊二烯单体的转化率均大于99.9%,共聚反应时间共为25min;
79.(2)在反应压力为0.25mpa,将四氯化硅溶液10ml(0.043mol/l)加入反应釜内与聚合产物接触在82℃下进行偶联反应10min;
80.再加入0.5ml异丙醇在72℃下进行终止反应,搅拌15min后,加入3.0g防老剂2,6-二叔丁基对甲基苯酚(活性丁戊聚合产物的0.8重量%)。
81.得到的聚合反应胶液经过水蒸汽凝聚后,经开炼机干燥后得到丁二烯-异戊二烯共聚物产品。将产品进行结构测试,结果见表3。
82.对比例2
83.将混合惰性溶剂(环己烷和正己烷,重量比为88:12)用5a分子筛(购自大连康宇化工有限公司,预先在500℃下烘5小时)浸泡1周。
84.(1)在高纯氮气保护下,先依次向5升聚合釜中加入混合溶剂2500g、异戊二烯75g,丁二烯298g;然后将聚合釜升温至共聚引发温度为60℃,反应压力为0.2mpa;
85.然后再加入正丁基锂溶液20ml(正丁基锂的浓度为0.1437mol/l)引发进行共聚反应。聚合反应14min反应压力为0.39mpa,达到最高温度100℃后,再继续进行反应10min至结束,同时取样测丁二烯和异戊二烯单体的转化率均大于99.9%,共聚反应时间共为24min;
86.(2)在反应压力为0.26mpa,将四氯化硅溶液10ml(0.043mol/l)加入反应釜内与聚合产物接触在85℃下进行偶联反应10min;
87.再加入0.5ml异丙醇在75℃下进行终止反应,搅拌15min后,加入3.0g防老剂2,6-二叔丁基对甲基苯酚(活性丁戊聚合产物的0.8重量%)。
88.得到的聚合反应胶液经过水蒸汽凝聚后,经开炼机干燥后得到丁二烯-异戊二烯共聚物产品。将产品进行结构测试,结果见表3。
89.对比例3
90.将混合惰性溶剂(环己烷和正己烷,重量比为88:12)用5a分子筛(购自大连康宇化工有限公司,预先在500℃下烘5小时)浸泡1周。
91.(1)在高纯氮气保护下,先依次向5升聚合釜中加入混合溶剂2500g、异戊二烯112g,丁二烯261g;然后将聚合釜升温至共聚引发温度为50℃,反应压力为0.18mpa;
92.然后再加入正丁基锂溶液20ml(正丁基锂的浓度为0.1437mol/l)引发进行共聚反应。聚合反应20min反应压力为0.28mpa,达到最高温度90℃后,再继续进行反应10min至结束,同时取样测丁二烯和异戊二烯单体的转化率均大于99.9%,共聚反应时间共为30min;
93.在反应压力为0.20mpa,将四氯化硅溶液10ml(0.043mol/l)加入反应釜内与聚合产物接触在78℃下进行偶联反应10min;
94.再加入0.5ml异丙醇在69℃下进行终止反应,搅拌15min后,加入3.0g防老剂2,6-二叔丁基对甲基苯酚(活性丁戊聚合产物的0.8重量%)。
95.得到的聚合反应胶液经过水蒸汽凝聚后,经开炼机干燥后得到丁二烯-异戊二烯共聚物产品。将产品进行结构测试,结果见表3。
96.表1
[0097][0098][0099]
*单体含量:丁二烯单体与异戊二烯单体的混合物在惰性溶剂、有机锂引发剂和所述混合物的总重量中所占重量百分含量;
[0100]
**用量:防老剂的用量为活性丁戊聚合产物的重量百分数,重量%。
[0101]
表1(续)
[0102][0103][0104]
注:混合溶剂(环己烷和正己烷,质量比为88:12),单体占总量13%(质量比)加入2100g,单体占总量15%(质量比)加入2500g
[0105]
测试例
[0106]
将实施例1-5和对比例1-3分别制得的丁二烯-异戊二烯共聚物产品制备为胎面胶,并测定胎面胶的滚动阻力性能。
[0107]
胎面胶混炼配方表2所示:
[0108]
表2
[0109]
组分用量,质量份丁二烯-异戊二烯共聚物137.5高耐磨炭黑10白炭黑60硬脂酸1氧化锌2.5
防老剂40202cz1.4dpg1.5si696硫磺1.4
[0110]
按照表2配制原料并加入哈克密炼机进行热处理,条件:150℃
×
7min、转速30rpm。
[0111]
得到的汽车轮胎胎面胶采用美国ta-dma2980型动态力学分析仪测定滚动阻力性能:频率2hz,升温速率5℃/min,测试温度范围-120℃至+100℃。结果见表3。
[0112]
表3
[0113][0114][0115]
从表1-3的结果可以看出,采用本发明提供的方法,控制单体在限定时间范围内完成加入,有利于实现以高单体含量下进行共聚反应,并且得到的共聚物产品中嵌段含量低,表明异戊二烯在共聚物链段中分散均匀,接近无规分布的特点,进一步制成的汽车轮胎胎面胶的60℃时的损耗因子tanδ低于0.075,滚动阻力性能优异。
[0116]
对比例采用现有技术的方法进行共聚反应。对比例1中,共聚反应时单体的浓度为15重量%,反应最高温度达到106℃,反应过程不易控温,同样浓度下的实施例1-4中,反应最高温度能够小于100℃。对比例2、3中,共聚反应时单体的浓度为13重量%,但反应过程最高温度也要达到100℃、90℃,相比实施例仍属于不易控制。因此,对比例中共聚反应的投料方式不同,无法控制单体原料的加料时间,不仅制得的共聚物制备的胎面胶滚动阻力大,而且共聚反应时单体的浓度不能高于15重量%,否则共聚反应容易造成温升过高或者飞温爆聚,反应过程难以控制。
[0117]
以上详细描述了本发明的优选实施方式,但是,本发明并不限于此。在本发明的技术构思范围内,可以对本发明的技术方案进行多种简单变型,包括各个技术特征以任何其它的合适方式进行组合,这些简单变型和组合同样应当视为本发明所公开的内容,均属于本发明的保护范围。