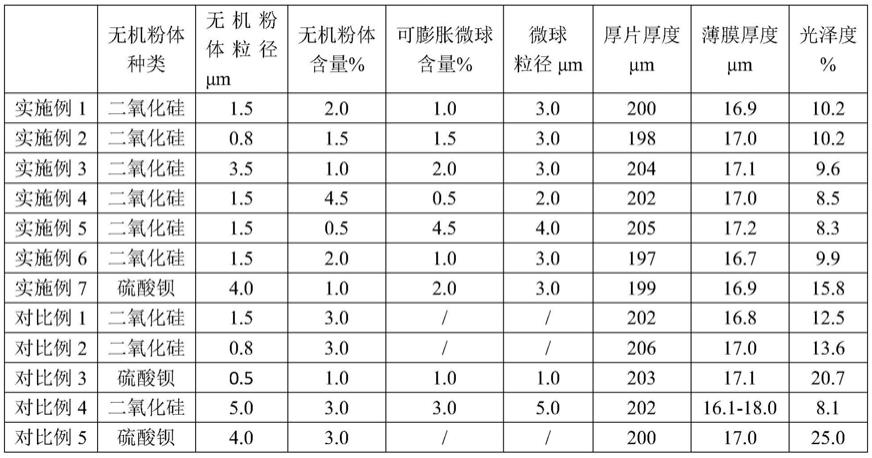
1.本发明涉及聚酯薄膜及其制备方法,尤其涉及一种低光泽度亚光聚酯薄膜及其制备方法。
背景技术:2.亚光薄膜具有表面光泽度低的特点,视感舒适,亚光薄膜一般由亚光聚酯母粒和主料经熔融挤出、双向拉伸制备而成。当平行光线照射到薄膜表面时,光线可分为三部分:一部分被吸收;另一部分被薄膜表面反射,当表面平整时形成了正反射光,表面不平整时形成了漫反射;第三部分是进入薄膜表面的平行光线。对于亚光薄膜而言,其低光泽度的特点是由表面正反射光、漫反射光以及内部的散射发射光的共同作用的结果。
3.为降低亚光薄膜的光泽度,申请号为cn201610979775.7的中国专利公开了一种单面亚光聚酯薄膜,采用6%~10%无机添加剂的聚酯母粒与基料共混成为亚光膜层,将亚光膜层与基膜层进行共挤成型,其光泽度小于80%,若亚光膜层中添加剂的含量过高会导致后道拉伸性能变差。现有技术还通过复配纳米级、亚纳米级、微米级添加剂的方式制备复配添加剂,然而纳米级、亚纳米级、微米级的粉体共混时难以均匀分散。申请号为cn01810763160.x的中国专利公开了一种亚光双向拉伸聚酯薄膜及其制备方法,采用三层共挤的方式制备亚光薄膜,将芯层设计为消光层,表层设计为亚光层,虽然选用不同粒径的二氧化硅代替单一粒径的二氧化硅,可以改善散射效果、赋予亚光膜更低的光泽度,但二氧化硅0.2-0.8μm和1-6μm两种粒径差异过大,难以混合均匀。申请号为cn201010185433.0的中国专利公开了一种高透明厚型聚酯薄膜,聚酯薄膜由低结晶速率的共聚酯经双向拉伸得到,薄膜中含有纳米级、亚纳米级和微米级的添加剂,虽然可以制备得到满足光学性能要求较高的薄膜,但仅限于制备厚型亚光膜(大于125μm),难以制备薄型高亚薄膜。
技术实现要素:4.发明目的:针对以上问题,本发明提出一种亚光聚酯薄膜,该亚光聚酯薄膜的散射效果得到改善,具有更低的光泽度,且厚度较薄。本发明的另一目的是提供该亚光聚酯薄膜的制备方法,制备过程拉伸容易。
5.技术方案:本发明所述的低光泽度亚光聚酯薄膜,所述聚酯薄膜主要由有光聚酯粉末和复合添加剂组成的共混物经熔融塑化、铸片、拉伸处理得到;所述复合添加剂包括尺寸相近的无机粉体和可膨胀微球。
6.作为优选,所述复合添加剂的用量为有光聚酯粉末质量的3%~5%。复合添加剂添加量过少会导致薄膜的亚光效果不明显,添加量过多则会使加工难度变大,薄膜厚度均匀性变差。
7.所述无机粉体选自二氧化硅、二氧化钛、硫酸钡、高岭土、碳酸钙、蒙脱土或滑石。优选二氧化硅。
8.作为优选,所述无机粉体为亚微米级或微米级无机粉体,其粒径中值为0.7~4.0μ
m。
9.所述可膨胀微球的外壳包括但不限于由腈系、酰胺类或丙烯酸酯类单体聚合制备的热塑性高聚物;所述可膨胀微球的芯层为膨胀剂,其组分包括但不限于脂肪族类化合物。
10.作为优选,所述可膨胀微球的粒径中值为2.0~4.0μm。
11.所述聚酯薄膜为三层亚光聚酯薄膜或单层亚光聚酯薄膜。优选三层亚光聚酯薄膜。
12.本发明所述的制备上述低光泽度亚光聚酯薄膜的制备方法,包括如下步骤:将常规亚光聚酯粉末、有光聚酯粉末和无机粉体共混,作为亚光膜芯层共混物料,将有光聚酯粉末和复合添加剂共混,作为亚光膜表层共混物料,亚光膜芯层共混物料和亚光膜表层共混物料经三层共挤挤出机熔融塑化、铸片,得到三层亚光聚酯厚片,再将厚片进行双向拉伸工艺处理,得到三层亚光聚酯薄膜;或将有光聚酯粉末和复合添加剂共混,共混物料经结晶干燥、熔融塑化、铸片,得到单层亚光聚酯厚片,再将厚片进行双向拉伸工艺处理,得到单层亚光聚酯薄膜。熔融挤出、双向拉伸工艺与常规亚光聚酯薄膜制备工艺相同。
13.相比于现有技术制备低光泽度聚酯薄膜采用单一种类的添加剂,本发明采用复合添加剂,亚微米或微米级的无机粉体(0.7~4.0μm)与可膨胀微球(2.0~4.0μm)的尺寸相近,能较为均匀的混合。经熔融挤出后,亚光膜表层中的可膨胀微球膨胀后的尺寸为8.0~12.0μm,尺寸较小的无机粉体与尺寸大的可膨胀微球使得薄膜表面变的粗糙,产生更强的漫反射,从而可以有效降低薄膜光泽度。另外,为了获得更低光泽度的聚酯薄膜,现有技术通常采用增加添加剂加入量的方法,然而添加剂的加入量过多会导致拉伸困难,本发明复合添加剂的用量仅为有光聚酯粉末质量的3%~5%,通过在原位聚合法加入改性组分的方式,可以有效改善亚光聚酯薄膜后道加工拉伸较难的问题,具有潜在的经济和应用前景。
14.有益效果:与现有技术相比,本发明的显著优点是:与相同含量的常规亚光薄膜相比,本发明加入复合添加剂的亚光薄膜光泽度能降低20%以上,其光泽度为8.3%;本发明复合添加剂的用量仅为有光聚酯粉末质量的3%~5%,在保证低光泽度的同时,还能有效改善亚光聚酯薄膜后道加工拉伸困难的问题。
具体实施方式
15.下面结合实施例对本发明作进一步的说明。
16.实施例1
17.采用aba三层共挤挤出机制备三层亚光聚酯薄膜
18.将二氧化硅含量为3.0%的常规亚光聚酯与有光聚酯按照1:1比例进行混合,制备成含有1.5%二氧化硅含量的亚光膜芯层共混物料。
19.将干燥后的有光聚酯进行粉碎制成粉末,称取1000g有光聚酯粉末、20g粒径均值为1.5μm的二氧化硅粉体、10g粒径均值为3.0μm的可膨胀微球粉体,将三种粉体在高速混合机中混合20min制成共混物料,作为亚光膜表层共混物料,表层中使用二氧化硅粉体与可膨胀微球作为复合添加剂,表层中复合添加剂的含量为3.0%(复合添加剂占有光聚酯粉末的质量百分比)。需要说明的是,本发明所用可膨胀微球的外壳包括但不限于由腈系、酰胺类或丙烯酸酯类单体聚合制备的热塑性高聚物;可膨胀微球的芯层为膨胀剂,其组分包括但不限于脂肪族类化合物。
20.采用aba三层共挤挤出机将亚光膜表层共混物料、亚光膜芯层共混物料分别加料后熔融塑化、铸片,制备得到厚度为200μm的三层亚光聚酯厚片。将厚片放置一天后,在双向拉伸机进行拉伸处理,厚片的拉伸条件为预热温度100℃,时间为30s,拉伸速率为100%*100%,厚片的拉伸倍率为3.5*3.5,得到厚度为16.9μm的三层亚光聚酯薄膜。
21.实施例2
22.采用与实施例1相同的方法制备三层亚光聚酯薄膜,所不同的是,表层中使用的二氧化硅粉体与可膨胀微球粉体的加入量均为15g,二氧化硅粉体粒径中值为0.8μm。
23.制备的厚片厚度为198μm,薄膜厚度为17.0μm。
24.实施例3
25.采用与实施例1相同的方法制备三层亚光聚酯薄膜,所不同的是,表层中使用的二氧化硅粉体与可膨胀微球粉体的加入量分别为10g、20g,二氧化硅粉体粒径中值为3.5μm。
26.制备的厚片厚度为204μm,薄膜厚度为17.1μm。
27.实施例4
28.采用与实施例1相同的方法制备三层亚光聚酯薄膜,所不同的是,表层中使用的二氧化硅粉体与可膨胀微球粉体的加入量分别为45g、5g,可膨胀微球的粒径均值为2.0μm。
29.制备的厚片厚度为202μm,薄膜厚度为17.0μm。
30.实施例5
31.采用与实施例1相同的方法制备三层亚光聚酯薄膜,所不同的是,表层中使用的二氧化硅粉体与可膨胀微球粉体的加入量分别为5g、45g,可膨胀微球的粒径均值为4.0μm。
32.制备的厚片厚度为205μm,薄膜厚度为17.2μm。
33.实施例6
34.采用单层挤出机制备单层亚光聚酯薄膜
35.将干燥后的有光聚酯进行粉碎制成粉末,称取1000g有光聚酯粉末、20g粒径均值为1.5μm的二氧化硅粉体、10g粒径均值为3.0μm的可膨胀微球粉体,将三种粉体在高速混合机中混合20min制成共混物料,采用此共混物料经预结晶干燥后,熔融塑化、铸片,制备得到厚度为197μm的单层亚光聚酯厚片。将厚片放置一天后,在双向拉伸机进行拉伸处理,厚片的拉伸条件为预热温度100℃,时间为30s,拉伸速率为100%*100%,厚片的拉伸倍率为3.5*3.5,得到厚度为16.7μm的单层亚光聚酯薄膜。
36.实施例7
37.采用与实施例1相同的方法制备三层亚光聚酯薄膜,所不同的是,表层中使用的是硫酸钡粉体与可膨胀微球粉体,其加入量分别为10g、20g,硫酸钡粉体粒径中值为4.0μm。
38.制备的厚片厚度为199μm,薄膜厚度为16.9μm。
39.对比例1
40.采用与实施例1相同的方法制备三层亚光聚酯薄膜,所不同的是,表层中使用的添加剂为30g二氧化硅粉体。
41.制备的厚片厚度为202μm,薄膜厚度为16.8μm。
42.对比例2
43.采用与实施例2相同的方法制备亚光薄膜,所不同的是,表层中使用的添加剂为30g二氧化硅粉体。
44.制备的厚片厚度为206μm,薄膜厚度为17.0μm。
45.对比例3
46.采用与实施例1相同的方法制备三层亚光聚酯薄膜,所不同的是,表层中使用的是硫酸钡粉体与可膨胀微球粉体,其加入量分别为10g、10g,两种添加剂粒径中值分别为0.5um、1.0μm。
47.制备的厚片厚度为203μm,薄膜厚度为17.1μm。
48.对比例4
49.采用与实施例2相同的方法制备亚光薄膜,所不同的是,表层中使用的是硫酸钡粉体与可膨胀微球粉体,其加入量分别为30g、30g,两种添加剂粒径中值均为5.0μm。
50.制备的厚片厚度为202μm,在双向拉伸成膜过程中因添加剂含量高拉伸成功率低于其他样品,薄膜厚度为16.1μm~18.1μm,其厚度均匀性差。
51.对比例5
52.采用与实施例7相同的方法制备亚光薄膜,所不同的是,表层中使用的是硫酸钡粉体加入量为30g。
53.制备的厚片厚度为200μm,薄膜厚度为17.0μm。
54.实施例与对比例原料组成及聚酯薄膜的性能参数见表1。
55.表1实施例与对比例原料组成及聚酯薄膜的性能参数
[0056][0057]
由表1可看出,本发明在亚光聚酯薄膜的制备原料中加入复合添加剂,因无机粉体与可膨胀微球的尺寸相近,可以使得物料在共混过程中能够较为均匀的混合,共混物料经熔融挤出后,可膨胀微球受热,达到构成壳体的热可塑性高分子材料的玻璃化温度,外壳软化,具有可塑性,由于微球内的低沸点芯层受热产生压强,从而引起微球外壳的膨胀,可膨胀微球由原先2.0~4.0μm的尺寸膨胀为8.0~12.0μm的大尺寸。尺寸较小的无机粉体0.7~4.0μm与尺寸大的可膨胀微球8.0~12.0μm使得薄膜表面变的粗糙,产生更强的漫反射,得到具有较低光泽度的亚光聚酯薄膜(8.3%~10.2%)。
[0058]
对比例3薄膜中复合添加剂的含量为2%,小于本发明限定的含量3%~5%,硫酸钡粉体和可膨胀微球的中值粒径分别为为0.5μm、1.0μm,也均低于本发明的粒径尺寸限定
值(无机粉体0.7~4.0μm、可膨胀微球2.0~4.0μm),制备得到的薄膜光泽度高达20.7%,可见复合添加剂含量过少、粒径过小时,薄膜的亚光效果不明显。分析对比例4,薄膜中复合添加剂含量为6%,高于本发明的限定值,虽然可以得到较好的亚光效果,其光泽度为8.1%,但由于复合添加剂含量过多,相当于在薄膜基体内部存在大量粒径相差较大的杂质组分,这导致了加工过程中拉伸难度增大,而且使薄膜的厚度均匀性变差(16.1~18.0μm)。
[0059]
比较实施例3和实施例7,当无机粉体选择硫酸钡时,其亚光效果不如二氧化硅,因此,本发明的无机粉体优选二氧化硅。
[0060]
相比于现有技术制备的厚度大于125μm的厚型亚光膜,本发明制备的聚酯薄膜厚度为16.7~17.2μm,为薄型高亚薄膜。
[0061]
在其他配方及工艺条件相同的前提下,在添加剂加入量相同的前提下,对比例1和2仅在制备原料中添加了无机粉体,其光泽度为12.5%~13.6%,明显高于实施例1~6中添加有复合添加剂的聚酯薄膜(8.3%~10.2%);当选择硫酸钡作为无机粉体时,对比例5薄膜光泽度高达25.0%,明显高于实施例7中添加有复合添加剂的聚酯薄膜15.8%。可见,在使用相同无机粉体的情况下,与仅加入无机粉体、添加剂含量相同的亚光薄膜相比,加入了可膨胀微球的亚光薄膜的光泽度降低20%以上。