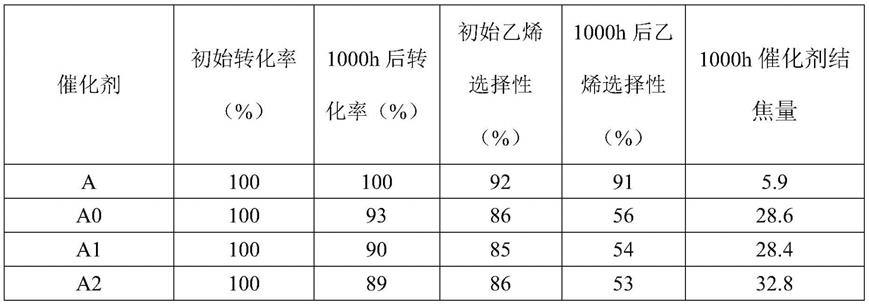
1.本发明涉及一种采用粗氢为氢源的碳二后加氢工艺的选择加氢方法。
背景技术:2.由石油烃蒸汽裂解得到的乙烯中含有质量分数0.5%~2.3%的乙炔。在用于聚合时,乙烯中的乙炔会降低聚合催化剂的活性,并影响聚合物的物理性能,因此必须将其脱除。目前工业上普遍采用选择加氢的方法脱除乙烯中的乙炔,采用的催化剂主要为pd,pt,au等贵金属催化剂。为了保证乙炔加氢生成的乙烯和原料中原有的乙烯不继续加氢生成乙烷,造成乙烯损失,必须保证催化剂的较高的加氢选择性,才能获得较好的经济效益。
3.碳二后加氢和前加氢是根据乙炔加氢反应器相对于脱甲烷塔的位置而言,加氢反应器位于脱甲烷塔之前为前加氢,加氢反应器位于脱甲烷塔之后为后加氢。后加氢工艺的优点是加氢过程控制手段多,不易飞温,操作方便,但工艺较复杂,需要单独配氢,碳二后加氢工艺由于加氢物料中氢气含量少,容易发生乙炔的加氢二聚反应,生成碳四馏分,碳四馏分进一步聚合生成分子量较宽的低聚物,俗称“绿油”。绿油吸附在催化剂表面,并进一步形成结焦,阻塞催化剂孔道,使反应物不能扩散到催化剂活性中心表面,从而导致催化剂活性下降。
4.对于以粗氢完全代替氢气的碳二后加氢工艺而言,一般采用一段加氢除炔工艺,少量装置采用两段加氢除炔工艺。由于粗氢中co含量高,更易发生甲酰化反应,形成含不饱和键的含氧物质,如醛和酮等,进一步聚合形成更大的绿油分子,而且该类含氧化合物在催化剂表面的滞留时间更长,对催化剂的影响更大。
5.贵金属催化剂活性较高,但在使用过程中易生成绿油,使催化剂发生结焦失活,影响催化剂稳定性和使用寿命。专利cn200810119385.8,发明了一种非贵金属负载型选择加氢催化剂及其制备方法和应用,包括载体以及负载在该载体上的主活性组分和助活性组分,其特征在于,所述的主活性组分为ni,所述的助活性组分选自mo、la、ag、bi、cu、nd、cs、ce、zn和zr中的至少一种,主活性组分和助活性组分均以非晶态形式存在,平均粒径<10nm,所述载体为不具氧化性的多孔材料;且所述的催化剂以微乳化法制备。
6.us4404124通过分步浸渍法制备了活性组分壳层分布的选择加氢催化剂,可应用于碳二馏分的选择加氢,以消除乙烯中的乙炔。us5587348以氧化铝为载体,添加助催化剂银与钯作用,加入与碱金属化学键合的氟制备了性能优良的碳二加氢催化剂。该催化剂具有减少绿油生成,提高乙烯选择性,减少含氧化合物生成量的特点。
7.专利cn1736589报道了一种采用完全吸附浸渍法制备的pd/γ-al2o3选择加氢催化剂,催化剂在使用过程中绿油生成量较大。专利cn200810114744.0了发明了一种不饱和烃选择加氢催化剂及其制备方法。该催化剂以氧化铝为载体,以钯为活性组分,通过加入稀土和碱土金属和氟提高催化剂抗杂质和抗结焦性能,但其催化剂选择性并不理想。
8.以上方法制备的催化剂均采用孔径单一分布的催化剂,在固定床反应过程中,受到内扩散的影响,催化剂的选择性较差。具有双峰孔分布的载体,在保证催化剂高活性的同
时,大孔的存在可以减少内扩散的影响,提高催化剂选择性。zl971187339公开了一种加氢催化剂,载体是一种蜂窝型载体,为大孔径载体,有效的提高了催化剂的选择性。cn1129606公开了一种烃类转化催化剂,其载体催化剂包括氧化铝、氧化镍、氧化铁等,该催化剂中包括两种孔,一种用于提高催化反应表面,另一种有利于扩散。专利cn101433842提供的一种加氢催化剂,其特征是催化剂具有双峰孔分布,小孔部分最可几半径为2~50nm,大孔部分最可几半径为100~500nm,由于催化剂为双峰孔分布,具有良好的加氢活性的同时,又有好的选择性,乙烯增量大。
9.在碳二加氢反应中,绿油的生成及催化剂的结焦是影响催化剂使用寿命的重要因素。催化剂的活性、选择性和使用寿命构成了催化剂的总体性能,以上所列出方法或对提高催化剂活性、选择性提出了较好的途径,却并没有解决催化剂容易结焦的问题,或者解决了催化剂易生成绿油和结焦的问题,却没有解决选择性的问题。具有大孔结构的载体虽然可以提高选择性,但是因聚合和链增长反应生成的较大分子也容易积留在载体大孔中,造成催化剂结焦失活,影响催化剂使用寿命。
10.zl201310114077.7,公开了了一种加氢催化剂,该催化剂中所述的活性组分有pd,ag,ni,其中pd,ag采用水溶液浸渍法负载,ni是采用w/o微乳液浸渍法负载的。采用该方法后,pd/ag与ni位于不同孔径的孔道中,反应生成的绿油在大孔中饱和加氢,催化剂结焦量降低。
11.但ni的还原温度往往要达到500℃左右,在该温度下还原态的pd原子极易聚集,使催化剂活性大幅度下降,需要大幅度增加活性组分等量以补偿活性损失,但又会引起选择性的下降。
技术实现要素:12.本发明的目的在于提供一种碳二馏分后加氢方法,尤其是一种可以采用粗氢为氢源的,可降低催化剂结焦的碳二馏分后加氢方法。
13.一种采用粗氢为氢源的碳二后加氢工艺的选择加氢方法,加氢物料为来自脱乙烷塔塔顶的碳二馏分,进入固定床反应器后进行气相加氢脱除乙炔,其特征在于加氢反应的所使用的氢气为粗氢,其中co含量为0.1~1v/v%,氢气含量为30~50v/v%。反应工艺条件为:反应器入口温度55~130℃,压力1.5~3.0mpa,气体体积空速1500~4000h-1
。催化剂载体为氧化铝或主要是氧化铝,具有双峰孔分布结构的氧化铝,其中小孔的孔径为15~50nm,大孔的孔径80~500nm,催化剂至少含有活性组分pd,ag,ni、cu,以催化剂的质量为100%计,pd的含量0.07~0.1%,ag的含量0.03-0.5%,ni含量0.5~5%,cu含量0.5~5%,ni和cu的总含量1~5.5%;其中pd的负载采用饱和浸渍法、微乳液法分两次浸渍;ni、cu采用微乳液法负载,控制微乳液粒径大于50nm小于500nm,使得ni、cu主要分布在载体的大孔中。微乳液法负载的pd的量是ni、cu总含量的1/100~1/200,微乳液法负载pd是在微乳液法负载ni、cu之后。
14.一种采用粗氢为氢源的碳二后加氢工艺的选择加氢方法,乙烯装置中来自脱乙烷塔塔顶的物料,与计量后的粗氢一起进入固定床碳二加氢反应器进行选择加氢,以脱除其中的炔烃。所述的加氢方法的特征在于所述的固定床反应器中装有含pd、ag、ni、cu组分的催化剂,该催化剂具有双峰孔径分布,所述的催化剂中ni、cu及部分pd采用微乳液法负载,
微乳液粒径大于小孔的孔径而小于大孔的最大孔径。
15.本发明中,先在小孔中先负载活性组分钯,而后在大孔中负载活性组分镍/铜及部分钯。乙炔等主要在小孔中发生选择性加氢反应,生成乙烯。而反应中生成的较大分子尺寸的副产物,主要为碳四至碳十六馏分,更容易进入大孔中,在大孔中的镍活性组分的作用下发生饱和加氢反应。由于这些分子被加氢饱和,其分子链不再增长,因而容易被物料带出反应器。铜的作用是与镍形成合金,可降低镍的还原温度,少量钯进入大孔还可以进一步大幅度降低镍的还原温度,使钯不至于在高温还原的过程中发生聚集。使催化剂的初期活性选择性不受还原过程的影响。
16.本发明使用是单段固定床反应器,反应器入口物料中氢炔比为2-3(v/v),反应器入口温度65~130℃。反应条件为:反应压力1.5~3.0mpa,气体体积空速1500~4000h-1
17.所述的粗氢中,co含量为0.1~1v/v%,氢气含量为30~50v/v%。
18.所述的加氢方法中,加氢原料为碳二馏分,其中乙烯70~93v/v%,乙炔0.6~1.3v/v%,碳三馏分0.01~0.5v/v%。
19.本发明人发现,由于催化剂抗结焦能力显著增强,碳三组分的含量在物料中的含量最高可达到0.5%,远远高于传统加氢方法对碳三馏分含量的限制。这就使得即使分离单元有较大幅度的波动,物料中重组分含量超标时,加氢单元仍然可以正常运行。
20.在该催化剂中,乙炔的选择加氢反应发生在ag,pd组成的主活中心;ni和cu以微乳液的形式将浸渍在载体的大孔中,反应中生成的绿油在cu与ni组成的活性中心上发生饱和加氢。
21.cu的作用是焙烧过程中形成ni/cu合金,在还原过程中有效降低了镍的还原温度,减少了pd在高温下的聚合。
22.对加氢反应而言,一般在催化剂应用前首先需要对加氢催化剂进行还原,保证活性组分以金属态存在,才能使催化剂具有加氢活性。因为催化剂制备过程中,活化是一个高温焙烧过程,在该过程中,金属盐分解为金属氧化物,氧化物会形成团簇,这种团簇一般是纳米尺寸的。不同的氧化物由于化学特性的不同,需要在不同的温度下进行还原。但对纳米尺寸的金属而言,200℃左右度是一个重要临界温度,超过该温度,金属粒子会有十分显著的产生聚集。因此,降低活性组分的还原温度,对加氢催化剂而言,有十分重要的意义。
23.本发明解决催化剂结焦的思路是:乙炔的选择加氢反应发生在ag、pd组成的主活性中心,反应中生产的绿油等大分子,容易进入催化剂的大孔中。在催化剂的大孔中,负载了ni/cu组分,其具有饱和加氢功能,绿油组分会在ni/cu组成的活性中心发生饱和加氢反应。由于双键被加氢饱和,绿油组分不能再发生聚合反应或聚合反应速率大大降低,其链增长反应终止或延缓,不能形成巨大分子量稠环化合物,容易被物料带出反应器,因此催化剂的表面的结焦程度会大大降低,催化剂的运行寿命会大幅度延长。
24.本发明中,大部分pd的浸渍采用过饱和浸渍法。在用过饱和浸渍法负载钯的过程中,由于小孔的虹吸作用,含有钯的溶液,更快地进入小孔中,钯是以氯钯酸离子的形式存在,由于该离子可以与载体表面的羟基形成化学键,使钯被快速的靶定,因此溶液进入孔道的速率越快,负载的速度就越快。所以在以过饱和浸渍法浸渍pd的过程中,更容易负载于小孔中。
25.本发明中控制ni/cu合金定位于催化剂大孔的方法是,ni/cu以微乳液的形式负
载,微乳液的粒径大于载体小孔孔径,而小于大孔的最大孔径。ni和cu金属盐包含在微乳液中,由于空间阻力的原因,难于进入尺寸较小的载体孔道中,因此ni和cu主要集中在大孔中。
26.本发明中,将cu与ni一起负载,可以降低ni的还原温度,因为要将nio完全还原,一般需要还原温度达到450~500℃,在该温度下会引起pd的团聚,而形成cu/ni合金后,其还原温度较纯ni的还原温度可以降低100℃以上,达到350℃。从而缓解还原过程中pd的团聚。
27.本发明并不特别限定以微乳液方式负载ni、cu、pd过程,只要是能形成大于50nm小于500nm微乳液粒径,都能使得ni、cu、pd分布在载体的大孔中。
28.该微乳液法负载过程包括:将前驱体盐溶于水中,加入油相、表面活性剂和助表面活性剂,充分搅拌形成微乳液,其中油相为烷烃或环烷烃,表面活性剂为离子型表面活性剂或非离子型表面活性剂,助表面活性剂为有机醇。
29.本发明推荐的油相为饱和烷烃或环烷烃,优选c6~c8饱和烷烃或环烷烃,优选环己烷、正己烷;表面活性剂为离子型表面活性剂或非离子型表面活性剂,优选非离子型表面活性剂,更优选是聚乙二醇辛基苯基醚或十六烷基三甲基溴化铵;助表面活性剂为有机醇,优选c4~c6醇类,更优选正丁醇或正戊醇。
30.微乳液中,最好水相和油相的重量比为2~3,表面活性剂和油相的重量比为0.15~0.6,表面活性剂和助表面活性剂的重量比为1~1.2。
31.本发明中,将少量pd负载在ni/cu合金的表面,还可以大幅度的降低ni的还原温度,可以达到200℃以下,最低到150℃。
32.因此,更佳的催化剂是pd主要存在于催化剂小孔中,ni/cu位于催化剂的大孔中,在大孔中ni/cu的表面还有少量pd。
33.该催化剂在制备过程中ni/cu以微乳液形态进行浸渍。pd以过饱和浸渍法及微乳液两种方法浸渍,ag的负载以饱和浸渍方法进行。
34.本发明推荐的催化剂更具体的制备方法,包括:
35.(1)将ni和cu的前驱体盐溶于水中,加入油相、表面活性剂和助表面活性剂,充分搅拌形成微乳液,控制微乳液粒径大于50nm小于500nm;将载体加入到制好的微乳液中浸渍0.5~4小时后,滤除余液,在80~120℃下干燥1~6小时,在300~600℃下焙烧2~8h,得到半成品催化剂a;
36.(2)将pd的前驱体盐溶于水,调ph为1.5~2.5,再将半成品催化剂a加入pd的盐溶液中,浸渍吸附0.5~4h后,80~120℃干燥1~4小时,400~550℃条件下焙烧2~6h,得到半成品催化剂b;
37.(3)ag的负载采用饱和浸渍法,即配制的ag盐的溶液是载体饱和吸水率的80~110%,调ph为1~5,半成品催化剂b负载ag之后在500~550℃之间进行焙烧,时间为4~6小时,得到半成品催化剂c;
38.(4)将pd前驱体盐溶于水中,加入油相、表面活性剂和助表面活性剂,充分搅拌形成微乳液,控制微乳液粒径大于50nm小于500nm;将半成品催化剂c加入到制好的微乳液中浸渍0.5~4小时后,滤除余液;在80~120℃下干燥1~6小时,在300~600℃下焙烧2~8h,得到半成品催化剂d。
39.(5)将半成品催化剂d置于固定床反应装置中,用n2:h2=1:1的混合气体,在150~
200℃下,还原处理4~8h得到成品催化剂e。
40.此催化剂具有以下特性:在加氢反应开始时,由于钯的加氢活性高,而且主要分布在小孔中,因而乙炔的选择性加氢反应主要发生在小孔中。随着催化剂运行时间的延长,催化剂表面生成了一部分分子量较大的副产物,这些物质由于分子尺寸较大,较多的进入大孔中,而且停留时间较长,会在镍催化剂的作用下,发生双键的加氢反应,而生成饱和烃或不含孤立双键的芳香烃,不再生成分子量更大的物质。本发明催化剂,制备过程还原温度低,还原温度为150~200℃。
41.采用本发明催化剂后,即使反应物中含较多重馏分,催化剂绿油生成量大幅增加,催化剂活性及选择性仍没有下降的趋势。鉴于该催化剂的优异性质,在采用粗氢为氢源的碳二后加氢工艺中,也可用于两段或三段加氢。
具体实施方式:
42.本发明催化剂在制备过程中用到以下表征方法:动态光散射粒径分析仪,在m286572动态光散射分析仪上分析ni/cu合金的微乳液粒径分布;在美国麦克公司9510型压汞仪上分析载体的孔体积、比表面积和孔径分布;在a240fs原子吸收光谱仪上,测定催化剂中pd、ag、ni和cu的含量。
43.实施例1
44.载体:采用市售双峰孔分布球形氧化铝载体,直径为4mm。经过1000℃焙烧4h后,双峰孔径分布范围在15~35nm和80~200mm,吸水率63%,比表面积为50m2/g。称取该载体100g。
45.催化剂制备:
46.(1)称取硝酸镍1.557g,硝酸铜14.767g,溶于69ml去离子水中,加环己烷23g,加triton x-100 3.45g,加正丁醇4.14g,充分搅拌形成微乳液,将称取的载体浸渍到所制备的微乳液中,摇动60min,滤除余液,在120℃下干燥1小时,在300℃下焙烧8h,称为半成品催化剂a-1。
47.(2)称取氯化钯0.075g,溶于100ml去离子水中,调ph为1.8,再将半成品催化剂a-1浸渍到已配制的pd盐溶液中,浸渍60min后,120℃干燥1小时,400℃条件下焙烧6小时,得到半成品催化剂a-2。
48.(3)称取硝酸银0.472g,溶于57ml去离子水中,调ph值为3,将步骤(2)制备的半成品催化剂a-2浸渍于所配制的配制含银的硝酸银溶液中,摇动,待溶液全部吸收后,120℃干燥1小时,在500℃焙烧6小时,得到半成品催化剂a-3。
49.(4)称取硝酸钯0.098g,溶于70ml去离子水中,加环己烷23g,加triton x-100 3.45g,加正丁醇4.14g,充分搅拌形成微乳液,将步骤(3)制备的半成品催化剂a-3浸渍到所制备的微乳液中,摇动60min,滤除余液,在120℃下干燥1小时,在300℃下焙烧8h得到半成品催化剂a-4。
50.(5)将步骤(4)得到的半成品催化剂a-4放置于固定床反应装置中,用摩尔比为n2:h2=1:1的混合气体,在190℃温度,还原处理5h,得到催化剂a。
51.动态光散射测定步骤(1)制备的微乳液乳液的粒径是53nm。
52.由原子吸收光谱法测定制备的催化剂,实施例1中,pd含量为0.10%,ni含量为
0.50%,cu含量为5.00%,ag含量为0.30%。
53.实施例2
54.载体:采用市售双峰孔分布圆柱形氧化铝载体,直径为3mm,长度为3mm。经过1030℃焙烧4h后,双峰孔径分布范围在18~38nm和85~270mm,吸水率61%,比表面积为43m2/g。称取该载体100g。
55.催化剂制备:
56.(1)称取氯化镍3.312g,氯化铜7.411g,溶于66ml去离子水中,加环己烷33g,加catb 9.90g,加正戊醇11.39g,充分搅拌形成微乳液,将称取的载体浸渍到所制备的微乳液中,摇动80min,滤除余液,在100℃下干燥4小时,在400℃下焙烧6h,称为半成品催化剂b-1。
57.(2)称取硝酸钯0.112g,溶于100ml去离子水中,调ph为1.8,再将半成品催化剂b-1浸渍到已配制的pd盐溶液中,浸渍60min后,100℃干燥4小时,450℃条件下焙烧4小时,得到半成品催化剂b-2。
58.(3)称取硝酸银0.394g,溶于57ml去离子水中,调ph值为3,将步骤(2)制备的半成品催化剂b-2浸渍于所配制的配制含银的硝酸银溶液中,摇动,待溶液全部吸收后,100℃干燥4小时,在530℃焙烧5小时,得到半成品催化剂b-3。
59.(4)称取氯化钯0.086g,溶于70ml去离子水中,加环己烷33g,加catb 9.90g,加正戊醇11.39g,充分搅拌形成微乳液,将步骤(3)制备的半成品催化剂b-3浸渍到所制备的微乳液中,摇动80min,滤除余液,在100℃下干燥4小时,在400℃下焙烧6h得到半成品催化剂b-4。
60.(5)将步骤(4)得到的半成品催化剂b-4放置于固定床反应装置中,用摩尔比为n2:h2=1:1的混合气体,在160℃温度,还原处理7h,得到成品催化剂b。
61.动态光散射测定步骤(1)制备的微乳液乳液的粒径是55nm。
62.由原子吸收光谱法测定制备的催化剂,实施例2中,pd含量为0.09%,ni含量为1.50%,cu含量为3.50%,ag含量为0.25%。
63.实施例3
64.载体:采用市售双峰孔分布三叶草形氧化铝载体,直径为2mm,长度为4mm。经过1060℃焙烧4h后,双峰孔径分布范围在20~42nm和90~360mm,吸水率58%,比表面积为37m2/g。称取该载体100g。
65.催化剂制备:
66.(1)称取硝酸镍8.095g,氯化铜4.658g,溶于62ml去离子水中,加正己烷30g,加catb 12.00g,加正戊醇13.20g,充分搅拌形成微乳液,将称取的载体浸渍到所制备的微乳液中,摇动70min,滤除余液,在110℃下干燥3小时,在500℃下焙烧3h,称为半成品催化剂c-1。
67.(2)称取硝酸钯0.109g,溶于100ml去离子水中,调ph为1.8,再将半成品催化剂c-1浸渍到已配制的pd盐溶液中,浸渍60min后,110℃干燥3小时,500℃条件下焙烧3小时,得到半成品催化剂c-2。
68.(3)称取硝酸银0.315g,溶于57ml去离子水中,调ph值为3,将步骤(2)制备的半成品催化剂c-2浸渍于所配制的配制含银的硝酸银溶液中,摇动,待溶液全部吸收后,110℃干燥3小时,在510℃焙烧6小时,得到半成品催化剂c-3。
69.(4)称取硝酸钯0.109g,溶于70ml去离子水中,加正己烷30g,加catb 12.00g,加正戊醇13.20g,充分搅拌形成微乳液,将步骤(3)制备的半成品催化剂c-3浸渍到所制备的微乳液中,摇动70min,滤除余液,在110℃下干燥3小时,在500℃下焙烧3h得到半成品催化剂c-4。
70.(5)将步骤(4)得到的半成品催化剂c-4置于固定床反应装置中,用摩尔比为n2:h2=1:1的混合气体,在170℃温度,还原处理6h,得到成品催化剂c。
71.动态光散射测定步骤(1)制备的微乳液乳液的粒径是62nm。
72.由原子吸收光谱法测定制备的催化剂,实施例3中,pd含量为0.08%,ni含量为2.60%,cu含量为2.20%,ag含量为0.20%。
73.实施例4
74.载体:采用市售双峰孔分布四叶草形氧化铝载体,直径为3mm,长度为3mm。经过1090℃焙烧4h后,双峰孔径分布范围在22~45nm和100~420mm,吸水率56%,比表面积为29m2/g。称取该载体100g。
75.催化剂制备:
76.(1)称取氯化镍8.611g,硝酸铜5.316g,溶于58ml去离子水中,加正己烷21g,加triton x-100 10.50g,加正丁醇11.03g,充分搅拌形成微乳液,将称取的载体浸渍到所制备的微乳液中,摇动90min,滤除余液,在90℃下干燥5小时,在600℃下焙烧2h,称为半成品催化剂d-1。
77.(2)称取氯化钯0.100g,溶于100ml去离子水中,调ph为1.8,再将半成品催化剂d-1浸渍到已配制的pd盐溶液中,浸渍60min后,90℃干燥5小时,550℃条件下焙烧2小时,得到半成品催化剂d-2。
78.(3)称取硝酸银0.142g,溶于57ml去离子水中,调ph值为3,将步骤(2)制备的半成品催化剂d-2浸渍于所配制的配制含银的硝酸银溶液中,摇动,待溶液全部吸收后,80℃干燥6小时,在540℃焙烧5小时,得到半成品催化剂d-3。
79.(4)称取氯化钯0.100g,溶于70ml去离子水中,加正己烷21g,加triton x-100 10.50g,加正丁醇11.03g,充分搅拌形成微乳液,将步骤(3)制备的半成品催化剂d-3浸渍到所制备的微乳液中,摇动90min,滤除余液,在90℃下干燥5小时,在600℃下焙烧2h得到半成品催化剂d-4。
80.(5)将步骤(4)得到的半成品催化剂d-4置于固定床反应装置中,用摩尔比为n2:h2=1:1的混合气体,在150℃温度,还原处理8h,得到成品催化剂d。
81.动态光散射测定步骤(1)制备的微乳液乳液的粒径是65nm。
82.由原子吸收光谱法测定制备的催化剂,实施例4中,pd含量为0.09%,ni含量为3.90%,cu含量为1.80%,ag含量为0.09%。
83.实施例5
84.载体:采用市售双峰孔分布球形氧化铝载体,直径为4mm。经过1130℃焙烧4h后,双峰孔径分布范围在25~50nm和110~500mm,吸水率50%,比表面积为20m2/g。称取该载体100g。
85.催化剂制备:
86.(1)称取硝酸镍15.567g,氯化铜2.117g,溶于50ml去离子水中,加正己烷25g,加
catb 15.00g,加正丁醇15.00g,充分搅拌形成微乳液,将称取的载体浸渍到所制备的微乳液中,摇动100min,滤除余液,在80℃下干燥6小时,在450℃下焙烧5h,称为半成品催化剂e-1。
87.(2)称取硝酸钯0.087g,溶于100ml去离子水中,调ph为1.8,再将半成品催化剂e-1浸渍到已配制的pd盐溶液中,浸渍60min后,80℃干燥6小时,450℃条件下焙烧4小时,得到半成品催化剂e-2。
88.(3)称取硝酸银0.047g,溶于57ml去离子水中,调ph值为3,将步骤(2)制备的半成品催化剂e-2浸渍于所配制的配制含银的硝酸银溶液中,摇动,待溶液全部吸收后,90℃干燥5小时,在550℃焙烧4小时,得到半成品催化剂e-3。
89.(4)称取硝酸钯0.087g,溶于70ml去离子水中,加正己烷25g,加catb 15.00g,加正丁醇15.00g,充分搅拌形成微乳液,将步骤(3)制备的半成品催化剂e-3浸渍到所制备的微乳液中,摇动100min,滤除余液,在80℃下干燥6小时,在450℃下焙烧5h得到半成品催化剂e-4。
90.(5)将步骤(4)得到的半成品催化剂e-4置于固定床反应装置中,用摩尔比为n2:h2=1:1的混合气体,在200℃温度,还原处理4h,得到成品催化剂e。
91.动态光散射测定步骤(1)制备的微乳液乳液的粒径是60nm。
92.由原子吸收光谱法测定制备的催化剂,实施例5中,pd含量为0.07%,ni含量为5.00%,cu含量为1.00%,ag含量为0.03%。
93.实施例6
94.使用与实施例5相同的载体,催化剂制备条件与实施例5相同,不同的是pd的负载均采用饱和浸渍法。各种组分含量相同。制备得到催化剂f。
95.对比例1
96.使用与实施例1相同的载体,催化剂制备条件与实施例1相同,区别是未负载cu。除cu外,其他组分的含量相同。制备得到催化剂a0。
97.对比例2
98.催化剂制备过程与实施例2相同,区别是未负载ni。除ni外,其他组分的含量相同。制备得到催化剂b0。
99.对比例3
100.使用与实施例3相同的载体,催化剂制备条件与实施例3相同,区别是cu是饱和浸渍法负载的。各种组分含量相同。制备得到催化剂c0。
101.对比例4
102.催化剂制备条件与对比例4相同,区别是第一步骤中采用饱和浸渍法负载cu和ni。各种组分含量相同。制备得到催化剂d0。
103.对比例5
104.与实施例1相比,区别是采用市售单峰孔分布载体,孔径分布范围在15~35nm,各类金属的负载均采用饱和浸渍法。各种组分含量相同。制备得到催化剂a1。
105.对比例6
106.与实施例1相比,区别是将实施例1中的cu替换为pb,其含量与实施例1中cu相同;其他组分含量及制备条件不变。制备得到催化剂a2。
107.对比例7
108.与实施例5相比,区别是将实施例5中的cu替换为pb,其含量与实施例1中cu相同;其他组分含量及制备条件不变。制备得到催化剂f0。
109.实施效果
110.催化剂应用于碳二后加氢反应的性能
111.实施例1、对比例1、对比例6、对比例7对比
112.加氢反应条件:催化剂在单段绝热固定床反应器的装填量为50ml,填料50ml,反应物料空速:4000/h,操作压力:1.5mpa,氢炔比2.0,反应器入口温度65℃。反应物料组成见下表1和表2。
113.表1物料组成:
114.反应物料c2h2h2c2h4c3co含量(v/v%)0.61.2930.30.03
115.表2运行结果:
[0116][0117]
与实施例1相比,对比例1中没有负载cu,虽然初始乙炔转化率及选择性与实施例1相比基本相同,但1000小时后,相比实施例1有明显降低。表明cu的负载或催化剂还原温度对提高抗结焦性能是重要的。或可能在200℃的还原温度下,具有饱和加氢功能的ni未能完全还原,没有发挥应有的作用。
[0118]
对比例6与实施例1相比,区别在于采用了市售单峰孔分布载体,孔径分布范围在15~35nm。其初始活性与实施例1相同,但其选择性远低于实施例1,运行1000h后,其活性选择性都有大幅下降,结焦量也远高于实施例1。其选择性低且结焦量大的原因是,载体不含大孔,反应生成物无法快速从小孔中输送出来,导致过度加氢,进而形成更大的绿油分子滞留在小孔中。
[0119]
对比例7与实施例1相比,区别在于未负载ni与cu,且pd、ag的负载均采用过饱和浸渍法。其初始活性较高,选择性差,运行1000h后结焦明显高于实施例1。选择性低原因可能是未含ni、cu,活性组分pd未能很好的分散,导致过度加氢;结焦量大的原因是不含具有饱和加氢功能的ni和cu,导致绿油生成量大。
[0120]
实施例2、对比例2对比
[0121]
加氢反应条件:催化剂在单段绝热固定床反应器的装填量为50ml,填料50ml,反应物料空速:3000/h,操作压力:1.7mpa,氢炔比2.2,反应器入口温度80℃。反应物料组成见下表3和表4。
[0122]
表3物料组成:
[0123]
反应物料c2h2h2c2h4c3co含量(v/v%)0.81.76880.20.044
[0124]
表4运行结果
[0125][0126]
与实施例2相比,对比例2中未负载ni,初始乙炔转化率及选择性与实施例2相同,但1000h后,相比实施例2有明显降低,且其结焦量明显高于实施例2。表明ni对提高催化剂抗结焦性能有重要的作用。
[0127]
实施例3、对比例3对比
[0128]
加氢反应条件:催化剂在单段绝热固定床反应器的装填量为50ml,填料50ml,反应物料空速:2500/h,操作压力:2.0mpa,氢炔比2.5,反应器入口温度90℃。反应物料组成见下表5和表6。
[0129]
表5物料组成:
[0130]
反应物料c2h2h2c2h4c3co含量(v/v%)12.5830.30.05
[0131]
表6运行结果
[0132][0133]
对比例3与实施例3相比,对比例3中cu的负载采用过饱和浸渍法,cu的分布主要在小孔中,没有起到有效降低还原温度的作用,在170℃的还原温度下,不能完全还原催化剂中的ni,导致其饱和加氢功能不能完全发挥,导致了催化剂绿油生成量大,进而形成大量结焦。结焦覆盖活性组分,导致催化剂转化率降低。
[0134]
实施例4、对比例4对比
[0135]
加氢反应条件1:催化剂在单段等温固定床反应器的装填量为50ml,填料50ml,反应物料空速:2000/h,操作压力:2.5mpa,氢炔比2.7,反应器入口温度130℃。反应物料组成见下表7和表8。
[0136]
表7物料组成:
[0137]
反应物料c2h2h2c2h4c3co含量(v/v%)1.23.24750.50.11
[0138]
表8运行结果
[0139][0140]
对比例4与实施例4相比,cu与ni的负载采用过饱和浸渍法,大部分cu与ni进入小孔,不能发挥其饱和加氢功能,1000小时后催化剂的结焦量大,催化剂性能下降。
[0141]
实施例5、对比例7对比
[0142]
加氢反应条件:催化剂在单段等温床反应器的装填量为50ml,填料50ml,反应物料空速:1500/h,操作压力:3.0mpa,氢炔比3.0,反应器入口温度110℃。反应物料组成见下表9和表10。
[0143]
表9物料组成:
[0144]
反应物料c2h2h2c2h4c3co含量(v/v%)1.33.9700.150.1
[0145]
表10运行结果
[0146][0147]
对比例5与实施例5相比,评价结果中结焦量大的原因可能是pb未能降低ni的还原温度,导致具有饱和加氢功能的ni未能发挥其功能,导致绿油生成量大,进而形成大量结焦。