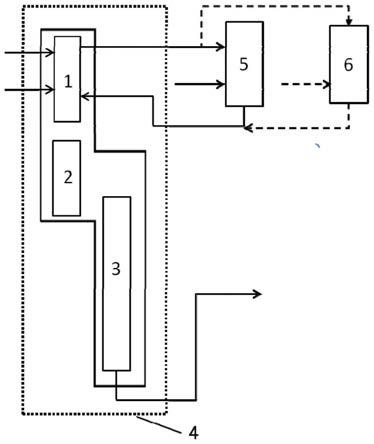
1.本发明涉及低碳烯烃制备领域,尤其涉及一种原油制备低碳烯烃的方法与系统。
背景技术:2.众所周知,裂解反应是生产乙烯、丙烯等极其重要工业原料的主要手段。本领域的哪怕一点点改进,都能够带来巨大的经济效益和社会效益。现阶段主流的裂解装置是采用馏分油、炼油装置富产的轻烃、采油装置伴生的轻烃、页岩气页岩油开采中伴生的轻烃,在高温条件下,并在水蒸气存在的气氛下发生自由基反应来实现的。而不经蒸馏处理的原油中包含沸点超过560℃的高分子量的非挥发性组分,这些非挥发性组分在常规的裂解炉的对流段进行预热时,有小部分未被气化,未被气化的非挥发性组分会在对流段管壁结焦沉积,造成对流段炉管压降增加,甚至堵塞对流段炉管,影响裂解炉的正常运行。
3.cn101583697a公开了一种用于裂解合成原油原料的方法,该方法采用常规裂解原料,如石脑油、加氢尾油等,作为稀释剂,改善原油的裂解性能,从而提高烯烃的转化率。但该方法受限于现有的乙烯生产原料来源限制,不能有效利用大量原油进行低碳烯烃的生产。
4.cn1957068a公开了一种含盐和/或微粒物质的原油的蒸汽裂解方法,该方法采用闪蒸分离器将其分离成蒸汽相和液相,不挥发性组分和盐留在液相中,然后将蒸汽相进行裂解以获得低碳烯烃。us3617493也公开了一种和上述方法相似的采用蒸汽裂解原油的方法。采用以上方法对原料进行裂解处理,其均采用闪蒸罐处理经过裂解炉对流段的原油,实现气液分离,气相进入辐射段进行裂解。但原料经过闪蒸后,仍至少有5%的烃原料留在液体中,影响低碳烯烃的收率,而且,分离后的液相直接用作燃料油,造成了原料浪费。
5.cn104593039a公开了减少裂解炉对流段结焦的工艺方法,裂解炉产生的裂解气经急冷、油洗后进入水洗塔,水洗塔釜工艺水进入工艺水汽提塔,工艺水汽提塔塔釜的水进入工艺水萃取塔,与萃取剂接触,工艺水萃取塔釜水进入稀释蒸汽发生器产生稀释蒸汽。该方法主要是解决现有技术中无法脱除稀释蒸汽夹带高聚物的问题。
6.cn1247887a公开了一种抑制乙烯裂解装置结焦的方法,主要是采用注入结焦抑制剂以减少炉管结焦和急冷锅炉结焦;cn1546609a公开了一种抑制和减缓乙烯裂解炉结焦的方法,主要是对炉管进行气氛处理和合金化处理,形成氧化层以抑制和减缓结焦;cn101724827a公开了一种减少乙烯裂解炉管结焦的方法,是在炉管内形成一种陶瓷涂层的方法以减少炉管内壁的焦炭沉积。
7.上述专利采用多种方法抑制裂解炉的结焦,但不幸的是,上述种种方法虽然都有一定的效果,但都无法完全避免裂解炉的结焦,尤其是原油作为裂解原料后,对流段的结焦情况将会愈发严重,因此如何在对流段结焦的情况下仍然能够保证裂解炉的正常运行将是一个严峻的问题。
技术实现要素:8.本发明的目的是为了克服现有技术中存在的原油汽化不充分、在裂解过程中容易结焦、低碳烯烃的产率低的问题,提供一种原油制备低碳烯烃的方法及系统,该方法能够提高原油原料的裂解效率,提高系统在线率,并同时提高产品中低碳烯烃的收率。
9.本发明的目的之一在于提供一种原油制备低碳烯烃的方法,包括以下步骤:
10.步骤1、将原油送入裂解炉的对流段第一管组进行预热,并部分汽化,得到预热后原油;
11.步骤2、将所述预热后原油送入汽化单元,与(过热)蒸汽混合进行汽化,得到汽化混合物;
12.步骤3、将所述汽化混合物送入裂解炉的对流段第二管组,加热至横跨温度后送入辐射段;
13.步骤4、在辐射段进行裂解得到裂解气,所述裂解气经分离得到低碳烯烃。
14.在本发明中,所述裂解炉采用现有技术公开的裂解炉,优选包括对流段第一管组、对流段第二管组和辐射段。
15.在一种优选的实施方式中,在步骤1中,所述预热后的原油的流出温度为120~280℃,优选为150~250℃,优选为180~240℃。
16.本发明利用蒸汽与原油混合,利用蒸汽显热及降低原油分压的目的来达到原油完全汽化的,因此采用首先要部分汽化,其次化学计量的过热蒸汽只能使原油气化后达到一个比较低的温度。
17.在一种优选的实施方式中,在步骤1中,所述预热后原油的最大汽化量不超过20wt%,优选不超过10wt%。
18.在一种优选的实施方式中,在步骤2中,所述原油与蒸汽之重量比为(0.1-2):1,优选为(0.4-1.5):1。
19.在进一步优选的实施方式中红,所述原油与蒸汽的混合方式可以为一次性或多次混合,优选采用2-5次分比例多次混合的方式。
20.在更进一步优选的实施方式中,在步骤2中,经过汽化后的汽化混合物的温度为500℃以下、200℃以上,优选为450以下、300℃以上,例如400℃。
21.在本发明中,“以上”、“以下”包括本数。
22.本发明步骤2所述蒸汽为过热蒸汽,对其温度没有严格限定,只要能够在汽化后使汽化混合物的温度达到500℃以下、200℃以上,优选450以下、300℃以上即可。
23.在一种优选的实施方式中,步骤3所述横跨温度为450-700℃,优选为480-600℃。
24.在一种优选的实施方式中,步骤4所述辐射段的出口温度为780-950℃,优选为800-900℃。
25.在一种优选的实施方式中,步骤4所述裂解的停留时间为0.05-1s,优选为0.1-0.7s。
26.在一种优选的是实施方式中,步骤4所述裂解的水油比为(0.1-2):1,优选为(0.4-1.5):1。
27.在一种优选的实施方式中,所述汽化单元包括至少两个汽化装置。
28.在进一步优选的实施方式中,其中一个汽化装置为工作状态,其它为备用状态,轮
流切换使用;优选地,当汽化过程中压降超过设定值,则将工作状态的汽化装置切出,将备用状态的汽化装置切入进行汽化处理;更优选地,所述设定值为0.1~0.2~mpag,例如0.1mpag。
29.在更进一步优选的实施方式中,切出的汽化装置烧焦后继续使用,同时烧焦尾气可以但不限于进入裂解炉的清焦罐。
30.其中,两个或多个汽化装置的轮流切换操作,保证汽化装置的在线清焦,也延长了装置的在线率,从而提高原油的裂解效率,提高产品中低碳烯烃的收率。
31.在一种优选的实施方式中,所述原油包括轻石脑油、石脑油、柴油、加氢尾油、轻质原油、终馏点高于600℃且低于700℃的原油和经过脱水脱盐处理的脱后原油。
32.在进一步优选的实施方式中,所述原油包括柴油、加氢尾油、轻质原油、经过脱水脱盐处理的脱后原油和终馏点高于600℃且低于700℃的原油。
33.本发明目的之二在于提供一种原油制备低碳烯烃的系统,优选用于进行本发明目的之一所述方法,所述系统包括裂解炉和汽化单元,所述裂解炉包括对流段第一管组、对流段第二管组和辐射段,所述对流段第一管组与汽化单元的物料入口连接,所述汽化单元的轻相组分出口与对流段第二管组连接。
34.在一种优选的实施方式中,所述汽化单元包括至少两个汽化装置,其中一个汽化装置为工作状态,其它为备用状态,轮流切换使用。
35.在进一步优选的实施方式中,当汽化过程中压降超过设定值,则将工作状态的汽化装置切出,将备用状态的汽化装置切入进行汽化处理;更优选地,所述设定值为0.1~0.2mpa。
36.在一种优选的实施方式中,切出的汽化装置烧焦后继续使用,同时烧焦尾气可以但不限于进入裂解炉的清焦罐。
37.在本发明中,控制裂解炉对流段于低温下进行部分汽化,这样,低温下不会导致裂解炉的对流段出现结焦现象。而将大部分的汽化过程于所述汽化单元内进行,在汽化过程中即使高温下出现结焦现象,由于两个以上汽化装置的设置,可以在线烧焦,保证运行中的汽化装置是无结焦堆积的状态,这样大大延长了系统的运行周期。
38.在本发明中,(1)将原油送入裂解炉的对流段第一管组进行预热,并部分汽化,得到预热后原油;(2)将所述预热后原油送入汽化装置,与过热蒸汽混合后汽化,得到汽化混合物;(3)将所述汽化混合物送入裂解炉的对流段第二管组,加热至横跨温度后送入辐射段;(4)在辐射段进行裂解得到裂解气,所述裂解气经分离得到低碳烯烃。
39.与现有技术相比,本发明具有如下有益效果:
40.(1)本发明中原油经过对流段预热后进入汽化单元进行汽化,然后再返回对流段,再进入辐射段进行裂解获得低碳烯烃。其中两个或多个汽化装置的轮流切换操作,保证汽化装置的在线清焦,也延长了装置的在线率,从而提高原油的裂解效率,提高产品中低碳烯烃的收率;
41.(2)克服了现有技术存在的原油汽化不充分、在裂解过程中容易结焦,低碳烯烃产率低的问题;
42.(3)利用本发明所述方法不仅能够提高产品的产率,而且能够明显延长系统的运行周期。
附图说明
43.图1示出本发明所述系统的结构示意图。
44.在图1中,1-对流段第一管组,2-对流段第二管组,3-辐射段,4-裂解炉,5-第一汽化装置,6-第二汽化装置。
45.在图1中,所述对流段第一管组1与汽化装置5的物料入口连接、所述第一汽化装置5的轻相组分出口与对流段第二管组2连接,所述第一汽化装置5与第二汽化装置6为一开一备,轮流切换使用。
具体实施方式
46.下面结合具体实施例对本发明进行具体的描述,有必要在此指出的是以下实施例只用于对本发明的进一步说明,不能理解为对本发明保护范围的限制,本领域技术人员根据本发明内容对本发明做出的一些非本质的改进和调整仍属本发明的保护范围。
47.另外需要说明的是,在以下具体实施方式中所描述的各个具体技术特征,在不矛盾的情况下,可以通过任何合适的方式进行组合。为了避免不必要的重复,本发明对各种可能的组合方式不再另行说明。
48.本发明实施例和对比例采用的裂解炉为cbl-iii型裂解炉(购自中国石化工集团公司)。
49.以下实施例和对比例中所用的原油的组成如表1所示,该组成根据astm d5307方法测得。
50.表1
51.分析项目astm d5307ip,℃6910%,℃19220%,℃27230%,℃33740%,℃39350%,℃44660%,℃50870%,℃59575%,℃65380%,℃-90%,℃-ep,℃-52.实施例1
53.本实施例用于提供一种采用原油制备低碳烯烃的方法,该方法包括:
54.(1)将经过脱水脱盐的原油在裂解炉4的对流段第一管组1中,利用对流段烟气热量对管组中的原油进行预热,预热后温度达到150℃(预热后的原油发生部分汽化,最大汽化量不超过5wt%)。
55.(2)预热后的原油的温度为150℃,将其送入带有多排管束的汽化装置5。通过分四
次进一步向所述汽化装置内注入过热蒸汽将原油完全汽化至400℃,压力为≤0.6mpa,其中,原油与过热蒸汽之重量比为1.0:1。
56.(3)汽化后原油再次进入裂解炉的对流段进行混合原料过热,加热至横跨温度(600℃)后直接送入辐射段3进行裂解得到裂解气,该辐射段3的操作参数为炉管出口温度为840℃,停留时间为0.22s,其中,裂解的水油比为1.0:1;
57.(4)将裂解气经过急冷器和裂解气分离系统(采用lummus的顺序分离流程),分离得到氢气,低碳烯烃和裂解汽油、裂解柴油和裂解燃料油;
58.(5)汽化装置各排管束均采用压力监控,当气化过程中压降超过设定值0.10mpa,则将汽化装置5切出,采用汽化装置6进行汽化;
59.(6)切出后的汽化装置5,经吹扫后采用蒸汽/空气进行烧焦,烧焦气进入裂解炉的清焦罐处理后,达到环保要求后排放;
60.裂解气经过分离获得低碳烯烃,其中乙烯收率为25.20wt%,丙烯的收率为13.88wt%,1,3-丁二烯的收率为4.49wt%,上述三烯的总收率为43.57wt%。运行周期为50天。
61.由上可以看出,采用本发明所述方法或系统可以使运行周期达到50天之久,主要是因为重质的原油作为裂解原料时,首先部分原油在对流段发生汽化,达到了回收对流段热量的作用,而大部分原油是在外设的气化单元完成汽化,避免了重质原料导致的对流段结焦无法在线清除,而汽化单元采用两个装置,实现在线烧焦,延长了运行周期。
62.实施例2
63.本实施例用于提供一种采用原油制备低碳烯烃的方法,该方法包括:
64.(1)将经过脱水脱盐的原油在裂解炉4的对流段第一管组1中,利用对流段烟气热量对管组中的原油进行预热,预热后温度达到120℃(预热后的原油发生部分汽化,最大汽化量不超过4wt%)。
65.(2)预热后的原油的温度为120℃,将其送入带有多排管束的汽化装置5。通过分三次进一步向所述汽化装置内注入过热蒸汽将原油完全汽化至450℃,其中,原油与过热蒸汽之重量比为1.5:1。
66.(3)汽化后原油再次进入裂解炉的对流段进行混合原料过热,加热至横跨温度(480℃)后直接送入辐射段3进行裂解得到裂解气,该辐射段3的操作参数为炉管出口温度为780℃,停留时间为0.7s,其中,裂解的水油比为1.5:1;
67.(4)将裂解气经过急冷器和裂解气分离系统(采用lummus的顺序分离流程),分离得到氢气,低碳烯烃和裂解汽油、裂解柴油和裂解燃料油;
68.(5)汽化装置各排管束均采用压力监控,当气化过程中压降超过设定值0.10mpa,则将汽化装置5切出,采用汽化装置6进行汽化;
69.(6)切出后的汽化装置5,经吹扫后采用蒸汽/空气进行烧焦,烧焦气进入裂解炉的清焦罐处理后,达到环保要求后排放;
70.裂解气经过分离获得低碳烯烃,其中乙烯收率为25.18wt%,丙烯的收率为13.87wt%,1,3-丁二烯的收率为4.50wt%,上述三烯的总收率为43.55wt%。运行周期为50天。
71.由上可以看出,采用本发明所述方法或系统可以使运行周期达到50天之久,主要
是因为重质的原油作为裂解原料时,首先部分原油在对流段发生汽化,达到了回收对流段热量的作用,而大部分原油是在外设的气化单元完成汽化,避免了重质原料导致的对流段结焦无法在线清除,而汽化单元采用两个装置,实现在线烧焦,延长了运行周期。
72.实施例3
73.本实施例用于提供一种采用原油制备低碳烯烃的方法,该方法包括:
74.(1)将经过脱水脱盐的原油在裂解炉4的对流段第一管组1中,利用对流段烟气热量对管组中的原油进行预热,预热后温度达到280℃(预热后的原油发生部分汽化,最大汽化量不超过10wt%)。
75.(2)预热后的原油的温度为280℃,将其送入带有多排管束的汽化装置5。通过分五次进一步向所述汽化装置内注入过热蒸汽将原油完全汽化至500℃,其中,原油与过热蒸汽之重量比为0.4:1。
76.(3)汽化后原油再次进入裂解炉的对流段进行混合原料过热,加热至横跨温度(700℃)后直接送入辐射段3进行裂解得到裂解气,该辐射段3的操作参数为炉管出口温度为900℃,停留时间为0.1s,其中,裂解的水油比为0.4:1;
77.(4)将裂解气经过急冷器和裂解气分离系统(采用lummus的顺序分离流程),分离得到氢气,低碳烯烃和裂解汽油、裂解柴油和裂解燃料油;
78.(5)汽化装置各排管束均采用压力监控,当气化过程中压降超过设定值0.10mpa,则将汽化装置5切出,采用汽化装置6进行汽化;
79.(6)切出后的汽化装置5,经吹扫后采用蒸汽/空气进行烧焦,烧焦气进入裂解炉的清焦罐处理后,达到环保要求后排放;
80.裂解气经过分离获得低碳烯烃,其中乙烯收率为25.21wt%,丙烯的收率为13.90wt%,1,3-丁二烯的收率为4.52wt%,上述三烯的总收率为43.63wt%。运行周期为50天。
81.由上可以看出,采用本发明所述方法或系统可以使运行周期达到50天之久,主要是因为重质的原油作为裂解原料时,首先部分原油在对流段发生汽化,达到了回收对流段热量的作用,而大部分原油是在外设的气化单元完成汽化,避免了重质原料导致的对流段结焦无法在线清除,而汽化单元采用两个装置,实现在线烧焦,延长了运行周期。
82.对比例1
83.该对比例采用常规的裂解炉进行裂解。
84.脱水脱盐的原油直接送入裂解炉中,经过对流段后,直接进入辐射段,进行裂解。裂解气采用lummus的顺序分离流程。对蒸汽裂解反应产物进行分析得知,乙烯的收率为21.49wt%,丙烯的收率为13.29wt%,1,3-丁二烯的收率为4.03wt%,三烯收率为38.81wt%。运行周期为5天。
85.对比例2
86.重复实施例1的过程,区别在于:没有控制步骤(1)中预热后的最大汽化量,预热后温度达315℃。
87.裂解气经过分离获得低碳烯烃,其中该系统的运行周期为40天,明显低于本申请的运行周期。分析原因在于,在该对比例中于裂解炉的对流段高温下汽化,容易使对流段出现结焦现象而影响运行周期。
88.对比例3
89.重复实施例1的过程,区别在于:只采用一个汽化装置。
90.裂解气经过分离获得低碳烯烃,乙烯收率为25.00wt%,丙烯的收率为13.79wt%,1,3-丁二烯的收率为4.25wt%,上述三烯的总收率为43.04wt%。可以看出,在对比例3中,运行周期明显降低,仅为30天。
91.对比例4
92.将经过脱水脱盐的原油注入裂解炉,在蒸汽裂解炉的对流段第一管组进行预热,预热后的原油温度为380℃,压力为0.15mpa。
93.将预热后的原油送入带有内构件的导叶式旋风分离器,内构件为顶部撇液筒、下部隔离板和防涡器,进行气液分离。旋风分离器的入口液相含量在0.04%(v/v),其中液相密度为800kg/m3,气相密度为0.85kg/m3。旋风分离器的分离效率为98%,经过分离后的蒸气相中的液相为200mg/m3。
94.将步骤2中分离出的蒸气相送入蒸汽裂解炉的对流段第二管组预热至横跨温度(510℃)后进入辐射段,进行裂解。该辐射段的操作参数为水油比0.75,炉管出口温度为840℃,停留时间0.21s。裂解产物中的乙烯收率为23.37wt%,丙烯的收率为12.12wt%,1,3-丁二烯的收率为4.43wt%,三烯收率为39.92wt%。运行周期为38天。
95.可以看出,该对比例4采用的是汽液分离,不同于实施例所述汽化处理,其汽化不充分,导致产率降低,另一个原因也在于,该对比例中于裂解炉的对流段高温下汽化,容易使对流段出现结焦现象而影响产率和运行周期。