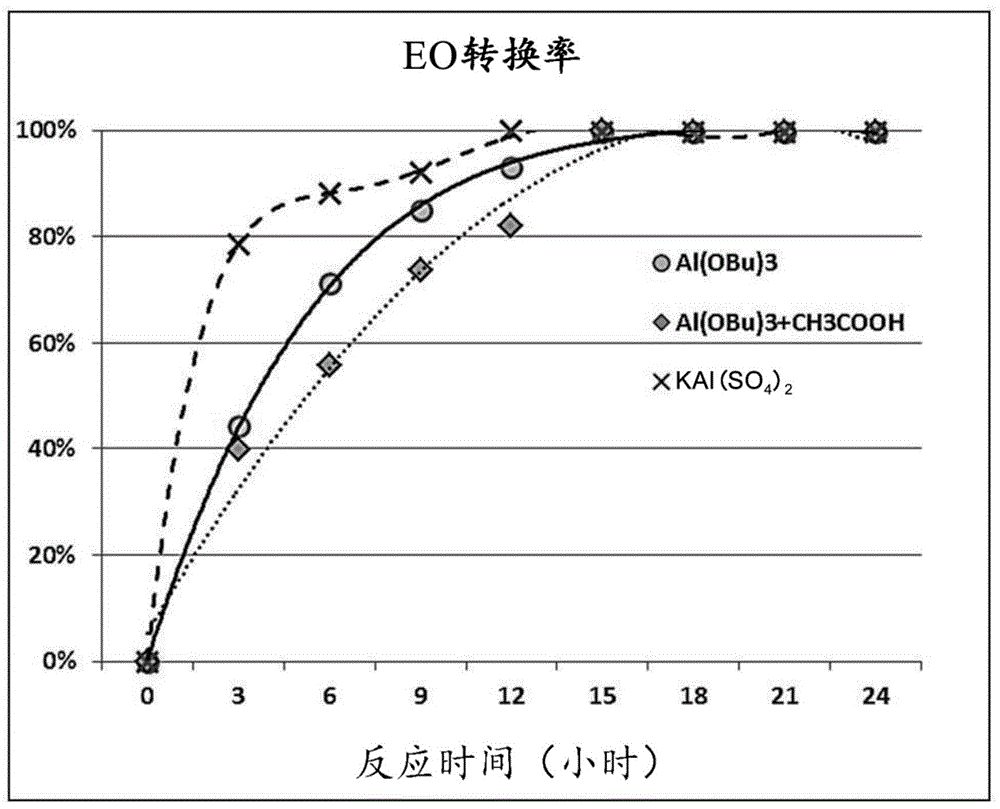
本发明涉及一种在新型铝系催化剂的存在下的烷基二甘醇(alkyldiglycol)的制备方法。更详细而言,本发明涉及一种具有nre(窄分布乙氧基化物narrowrangeethoxylate,窄摩尔分布)效果的同时增加反应速度的在新型铝系催化剂的存在下的烷基二甘醇的制备方法。
背景技术:
:本发明涉及一种由醇及环氧烷烃制备烷基二甘醇的方法。作为一例,由丁醇及环氧乙烷(eo)制备二乙二醇丁醚的反应如下所述。作为在上述反应中广泛使用的铝催化剂,已知有对2摩尔环氧烷烃(alkyleneoxide)的加成呈现选择性(nre效果)的mg-al催化剂。但是,由于该催化剂为复合氧化物形态的非均相催化剂,因此不适合连续生产工艺。此外,作为均相催化剂的烷醇铝催化剂呈现出nre效果,但具有反应速度明显慢的问题。因此,在由醇及环氧烷烃制备烷基二甘醇时,需要开发能够增加烷基二甘醇的生产率的催化剂。专利文献1:jp3174479b2技术实现要素:本发明的目的是提供一种新型铝系催化剂,其在由醇和环氧烷烃制备烷基二甘醇时,维持铝系催化剂所具有的对2摩尔环氧烷烃加成的选择性(nre效果)的同时改善反应速度。为了解决上述问题,本发明提供一种烷基二甘醇的制备方法,包括以下反应:在选自含碱金属及碱土金属的铝系化合物或其水合物的催化剂的存在下,使醇与环氧烷烃反应。根据一实现例,所述铝系催化剂可以是硫酸铝钾(aluminumpotassiumsulfate:kal(so4)2)或其水合物。根据一实现例,所述醇可以选自具有1至6个碳原子的烷基醇。根据一实现例,所述环氧烷烃可以选自具有2至4个碳原子的环氧烷烃。根据一实现例,可以在170℃至210℃的温度执行所述反应。根据一实现例,可以在3kg/cm2g至30kg/cm2g的压力下执行所述反应。根据一实现例,相对于所述醇可以以3:1至8:1的摩尔比使用所述环氧烷烃。根据一实现例,相对于醇重量可以使用20ppm至400ppm的所述催化剂。本发明的新型铝系催化剂发挥以下效果:在制备烷基二甘醇时,维持铝系催化剂所具有的对2摩尔环氧烷烃加成的选择性(nre效果)的同时改善反应速度。附图说明图1是表示关于在实施例及比较例中使用的催化剂的eo转换率的图表。具体实施方式本发明涉及一种烷基二甘醇的制备方法,包括以下反应:在选自铝系化合物或其水合物的铝系催化剂的存在下,使醇与环氧烷烃反应。根据一实现例,本发明提供一种二乙二醇丁醚(butyldiglycol)的制备方法,包括以下反应:在选自硫酸铝钾或其水合物的催化剂的存在下,使丁醇与环氧乙烷反应。所述铝系催化剂为含碱金属(化学周期表第1族金属)或碱土金属(化学周期表第2族金属)的铝系催化剂。根据一实现例,铝系催化剂为硫酸铝钾或其水合物。所述醇可以选自碳原子数为1至6的烷基醇。根据一实现例,所述醇为1-丁醇。所述环氧烷烃可以选自碳原子数为2至4的环氧烷烃。根据一实现例,所述环氧烷烃为环氧乙烷。相对于所述醇可以以3:1至8:1的摩尔比使用环氧烷烃。根据一实现例,环氧烷烃与所述醇的反应摩尔比为5:1至7:1。在脱离所述反应摩尔比范围的情况下,发生因高分子含量变多等理由而降低产品生产率的问题。相对于醇重量可以使用20ppm以上的所述含铝系催化剂。根据一实现例,相对于醇重量可以使用200ppm以上的所述催化剂。根据一实现例,相对于醇重量可以使用400ppm以下的所述催化剂。在所述催化剂的浓度脱离上述范围的情况下,有可能会发生高分子含量变多或反应率降低的问题。在本发明中,在铝系催化剂的存在下且在170℃至210℃的温度及3kg/cm2g至30kg/cm2g的压力下使醇和环氧烷烃反应。根据一实现例,所述温度为170℃至190℃。根据一实现例,所述压力为3kg/cm2g至10kg/cm2g。在本发明中使用铝系催化剂作为催化剂,从而能够提高环氧烷烃的转换率。下面,通过本发明的具体实施例对发明的作用及效果进行更具体说明。但是,该具体实施例是作为本发明的示例提出的,本发明的权利范围并非因该具体实施例而限定为某种含义。实施例实施例(单独使用硫酸铝钾催化剂)将500g的丁醇、0.1g的硫酸铝钾及50g的环氧乙烷加入到高压釜反应器中,并且在5kg/cm2g的压力及170℃的温度条件下搅拌24小时而使之反应。利用gc(50℃→10℃/min→300℃,hold)来分析获得的生成物,并且将随反应时间产生的生成物中的各成分的量示于下述表1。[表1][重量%]3小时6小时9小时12小时24小时bg93.192.392.291.991.7bdg6.637.307.377.747.82btg0.320.370.400.370.41b4g00.0400.020.02*bg:乙二醇丁醚*bdg:二乙二醇丁醚*btg:三乙二醇丁醚*b4g:四乙二醇丁醚比较例1(单独使用三丁氧基铝催化剂)除在上述实施例1中使用0.1g的三丁氧基铝代替0.1g的硫酸铝钾以外,执行与实施例1相同的反应。分析获得的生成物,并且将随反应时间产生的生成物中的各成分的量示于下述表2。[表2][重量%]3小时6小时9小时12小时24小时bg97.3395.8595.0794.5994.07bdg2.63.984.735.175.64btg0.070.130.170.200.23b4g00.050.040.050.06比较例2(混合使用三丁氧基铝催化剂和乙酸助催化剂)除在上述实施例1中使用0.1g的三丁氧基铝及0.1g的乙酸代替0.1g的硫酸铝钾以外,执行与实施例1相同的反应。分析获得的生成物,并且将随反应时间产生的生成物中的各成分的量示于下述表3。[表3][重量%]3小时6小时9小时12小时24小时bg97.7596.8796.1695.7995.02bdg2.23.063.724.024.74btg0.050.070.100.190.20b4g000.020.020.04反应结束时刻为在反应过程中压力未发生变化的时刻,该时刻为eo转换率为100%的时刻。在作为催化剂只单独使用三丁氧基铝的情况下,直至反应结束为止花费约18小时,但在使用本发明所涉及的硫酸铝钾催化剂的情况下,约在10小时完成反应,这表示硫酸铝钾催化剂的反应速度改善效果优异。在作为助催化剂追加乙酸的情况下,不存在反应速度改善效果,反而呈现出比单独使用三丁氧基铝时更低的速度。显示出相对于作为本发明的目的的对2摩尔的环氧烷烃的选择性,对1摩尔的环氧烷烃的选择性更高的结果。由上述结果可知,与作为现有的铝系催化剂众所周知的烷醇铝形态的催化剂相比较,在使用本发明的硫酸铝钾催化剂的情况下提高反应率。当前第1页12