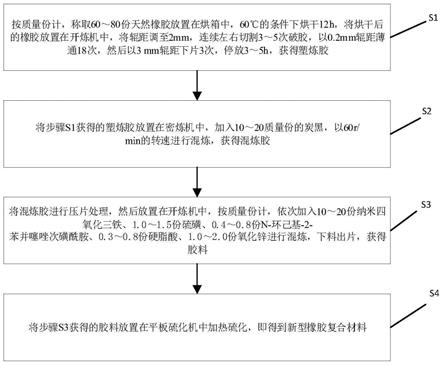
1.本发明涉及橡胶制备技术领域,尤其涉及一种新型橡胶复合材料的制备方法。
背景技术:2.天然橡胶为一种可再生自然资源,因其优异的综合性能,如高强度、高弹性、高伸长率和耐磨性等,广泛地应用于航空航天、国防军工、交通运输、医用弹性体等领域。由于橡胶本身的分子间作用力较小,自由体积较大,结晶能力较弱,所以大多橡胶材料需要经过物理改性或者化学改性之后才能应用到实际制品中。而填充改性则是物理改性中非常重要的一类。纳米级填料在提高橡胶材料综合性能上表现出极好的效果。与传统复合材料及微米复合材料相比,纳米级填料的增强具有其特异性,如宏观量子隧道效应、量子尺寸效应、表面界面效应和小尺寸效应等。正是由于纳米填料的这些特性,使得纳米复合材料能够具有一些特殊性能,比如抗老化性能、高耐磨性和抗辐射性能等。
技术实现要素:3.有鉴于此,本发明提供了一种工艺简单的新型橡胶复合材料的制备方法,制备得到的新型橡胶复合材料性能优异。
4.本发明提供一种新型橡胶复合材料的制备方法,包括以下步骤:
5.s1,将天然橡胶放置在烘箱中,60℃的条件下烘干12h,将烘干后的橡胶放置在开炼机中,将辊距调至2mm,连续左右切割3~5次破胶,以0.2mm辊距薄通18次,然后以3mm辊距下片3次,停放3~5h,获得塑炼胶;
6.s2,将步骤s1获得的塑炼胶放置在密炼机中,加入炭黑,以60r/min的转速进行混炼,获得混炼胶;
7.s3,将混炼胶进行压片处理,然后放置在开炼机中,依次加入纳米四氧化三铁、硫磺、n-环己基-2-苯并噻唑次磺酰胺、硬脂酸、氧化锌进行混炼,下料出片,获得胶料;
8.s4,将步骤s3获得的胶料放置在平板硫化机中加热硫化,即得到新型橡胶复合材料。
9.进一步地,所述新型橡胶复合材料的各原料的质量份为:天然橡胶60~80份,炭黑10~20份,纳米四氧化三铁10~20份,硬脂酸0.3~0.8份,氧化锌1.0~2.0份,n-环己基-2-苯并噻唑次磺酰胺0.4~0.8份,硫磺1.0~1.5份。
10.进一步地,所述新型橡胶复合材料的各原料的质量份为:天然橡胶65份,炭黑12份,纳米四氧化三铁15份,硬脂酸0.5份,氧化锌1.2份,n-环己基-2-苯并噻唑次磺酰胺0.6份,硫磺1.2份。
11.进一步地,所述新型橡胶复合材料的各原料的质量份为:天然橡胶70份,炭黑18份,纳米四氧化三铁18份,硬脂酸0.6份,氧化锌1.5份,n-环己基-2-苯并噻唑次磺酰胺0.5份,硫磺1.4份。
12.进一步地,所述纳米四氧化三铁的粒径为80nm或300nm。
13.进一步地,所述纳米四氧化三铁为经硅烷偶联剂改性后的纳米四氧化三铁。
14.本发明提供的技术方案带来的有益效果是:本发明提供的制备方法利用纳米氧化铁作为填料制得一种新型橡胶复合材料,提升了橡胶的力学性能,试验表明,该新型橡胶复合材料的300%定伸应力、拉伸强度和撕裂强均有所增大。
附图说明
15.图1是本发明一种新型橡胶复合材料的制备方法的工艺流程图。
具体实施方式
16.为使本发明的目的、技术方案和优点更加清楚,下面将结合附图对本发明实施方式作进一步地描述。
17.请参考图1,本发明的实施例提供了一种新型橡胶复合材料的制备方法,包括以下步骤:
18.步骤s1,按质量份计,称取60~80份天然橡胶放置在烘箱中,60℃的条件下烘干12h,将烘干后的橡胶放置在开炼机中,将辊距调至2mm,连续左右切割3~5次破胶,以0.2mm辊距薄通18次,然后以3mm辊距下片3次,停放3~5h,获得塑炼胶;
19.步骤s2,将步骤s1获得的塑炼胶放置在密炼机中,加入10~20质量份的炭黑,以60r/min的转速进行混炼,获得混炼胶;
20.步骤s3,将混炼胶进行压片处理,然后放置在开炼机中,按质量份计,依次加入10~20份纳米四氧化三铁、1.0~1.5份硫磺、0.4~0.8份n-环己基-2-苯并噻唑次磺酰胺、0.3~0.8份硬脂酸、1.0~2.0份氧化锌进行混炼,下料出片,获得胶料;纳米四氧化三铁为经硅烷偶联剂改性后的纳米四氧化三铁,其粒径为80nm或300nm;
21.步骤s4,将步骤s3获得的胶料放置在平板硫化机中加热硫化,硫化温度为145~155℃,硫化时间为10~15min,硫化压力为12mpa,即得到新型橡胶复合材料。
22.下面结合实施例对本发明提供的新型橡胶复合材料的制备方法进行详细说明。
23.实施例1:
24.称取650g天然橡胶放置在烘箱中,60℃的条件下烘干12h,将烘干后的橡胶放置在开炼机中,将辊距调至2mm,连续左右切割4次破胶,以0.2mm辊距薄通18次,然后以3mm辊距下片3次,停放4h,获得塑炼胶;将获得的塑炼胶放置在密炼机中,加入120g炭黑,以60r/min的转速进行混炼,获得混炼胶;将混炼胶进行压片处理,然后放置在开炼机中,依次加入150g纳米四氧化三铁、12g硫磺、6gn-环己基-2-苯并噻唑次磺酰胺、5g硬脂酸、12g氧化锌进行混炼,下料出片,获得胶料;将获得的胶料放置在平板硫化机中,在12mpa、150℃的条件下加热硫化12min,即得到新型橡胶复合材料。
25.实施例1中,每10g为一份。
26.对实施例1制得的新型橡胶复合材料进行力学性能测试,实施例1制得的新型橡胶复合材料的拉伸强度为26.5mpa,撕裂强度为61.14kn/m,100%定伸应力为1.68mpa,300%定伸应力为6.94mpa,拉断伸长率为568%,邵尔硬度为54度。
27.实施例2:
28.称取700g天然橡胶放置在烘箱中,60℃的条件下烘干12h,将烘干后的橡胶放置在
开炼机中,将辊距调至2mm,连续左右切割4次破胶,以0.2mm辊距薄通18次,然后以3mm辊距下片3次,停放3h,获得塑炼胶;将获得的塑炼胶放置在密炼机中,加入180g炭黑,以60r/min的转速进行混炼,获得混炼胶;将混炼胶进行压片处理,然后放置在开炼机中,依次加入180g纳米四氧化三铁、14g硫磺、5gn-环己基-2-苯并噻唑次磺酰胺、6g硬脂酸、15g氧化锌进行混炼,下料出片,获得胶料;将获得的胶料放置在平板硫化机中,在12mpa、155℃的条件下加热硫化12min,即得到新型橡胶复合材料。
29.实施例2中,每10g为一份。
30.对实施例2制得的新型橡胶复合材料进行力学性能测试,实施例2制得的新型橡胶复合材料的拉伸强度为27.5mpa,撕裂强度为62.28kn/m,100%定伸应力为1.68mpa,300%定伸应力为6.85mpa,拉断伸长率为564%,邵尔硬度为54度。
31.在不冲突的情况下,本文中上述实施例及实施例中的特征可以相互结合。
32.以上所述仅为本发明的较佳实施例,并不用以限制本发明,凡在本发明的精神和原则之内,所作的任何修改、等同替换、改进等,均应包含在本发明的保护范围之内。