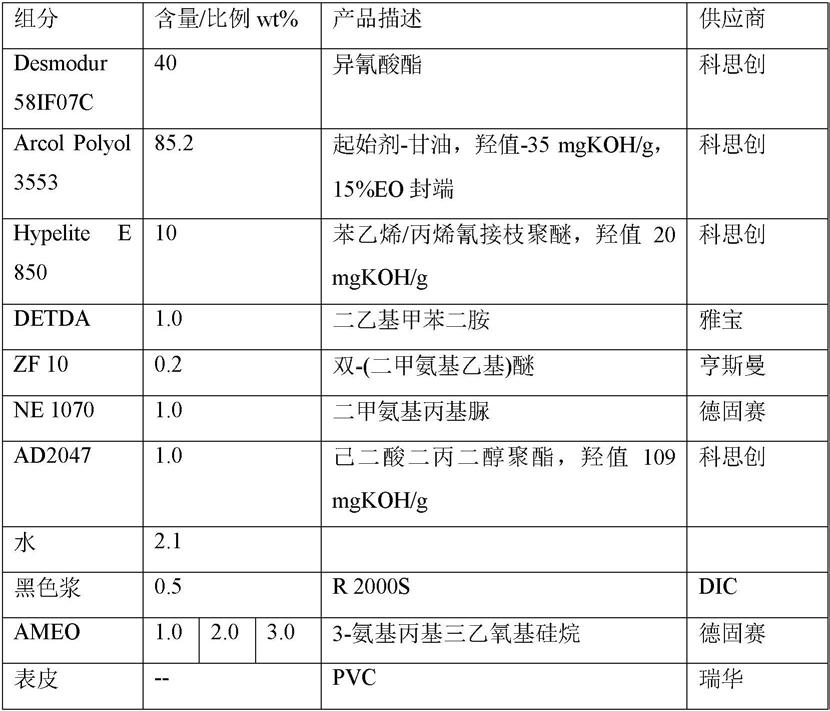
1.本发明涉及一种制备聚氨酯半硬质泡沫的方法,该方法所制得的聚氨酯半硬质泡沫及其用途。
背景技术:2.作为一种非常重要的化工原料,聚氨酯被广泛的应用于工业生产和日常生活中。在需要使用表皮制备聚氨酯复合材料/板的时候,为了改善表皮的韧性、舒适性和美观等,表皮材料中通常会加入大量塑化剂。但是,塑化剂会降低表皮材料的极性,影响聚氨酯泡沫与表皮材料的粘接。此外,由于表皮材料一般采用搪塑工艺生产,因成型工艺需要,制备表皮的材料中必须加入内脱模剂,而内脱模剂在搪塑工艺中会析出并迁移至表皮表面,对剥离强度产生不利影响。怎样获得剥离强度好的聚氨酯泡沫,而又不影响聚氨酯泡沫的其他性能,是业内亟待解决的问题。
3.cn110078891a公开了一种低密度半硬质聚氨酯材料,其由a组分和b组分经发泡工艺制得,按重量份计,所述的a组分包括如下原料:以甘油为起始剂、数均分子量为350~450的聚醚35~45份;以甘油为起始剂、数均分子量为5000~6000的聚醚40~50份;水8~12份;助剂3~7份;其中,所述的聚醚的聚合单体为环氧乙烷、1,2-环氧丙烷中的一种或两种;所述的b组分为异氰酸酯。本发明在不改变生产设备和工艺的条件下,通过对配方组分的整体优化,使得生产处的聚氨酯泡沫具有密度低、泡孔细腻均匀、透气性佳、阻燃性好、声学性能好等优点,有利于汽车的轻量化与减噪。
4.cn101541850a公开了一种可以在不导致尺寸稳定性下降的情况下实现低密度化的硬质聚氨酯泡沫塑料的制造方法及硬质聚氨酯泡沫塑料。使羟值为200~800mgkoh/g的多元醇和多异氰酸酯化合物在氨基改性硅氧烷、催化剂、发泡剂和泡沫稳定剂的存在下反应来制造硬质聚氨酯泡沫塑料。
5.cn106146875a公开了一种高倍率热塑性聚氨酯微孔发泡板材,包括以下组分:70~100重量份的tpu、0~30重量份的聚二甲基硅氧烷;该发明的优点:由于超临界流体在聚二甲基硅氧烷具有较大的溶解度和聚二甲基硅氧烷具有较低的界面张力,在tpu中混入的少量聚二甲基硅氧烷,极大地加速了超临界流体在tpu中的扩散速度,缩短了超临界流体在tpu中的扩散平衡时间;模腔体积稍大于tpu板材体积,并且模具表面铺有透气金属材料的模具,使超临界流体可以通过tpu板材的上下两个表面同时扩散进入tpu板材,相比于超临界流体只能通过上表面扩散进入tpu板材,扩散距离缩短,缩短了扩散平衡时间,提高了生产效率;另外,该文献还提供一种高倍率热塑性聚氨酯微孔发泡板材的生产方法。
6.尽管有以上公开,市场仍然急需具有更优良品质的、高物理性质的硬质聚氨酯半硬质泡沫,以满足汽车、家私等行业的需求。
技术实现要素:7.本发明的第一个方面,是提供一种制备聚氨酯半硬质泡沫的方法,其为使包括如
下组分的聚氨酯反应体系反应制得所述聚氨酯半硬质泡沫:
8.组分a,一种或多种多异氰酸酯;
9.组分b,包括:
10.b1)至少一种重均分子量为5000-12000g/mol,优选5000-6000g/mol(测试方法参照gb/t 21863-2008)的eo封端的,基于b1)组分总重量计氧亚乙基单元含量为10-20wt%的聚醚多元醇,其含量为70-90wt%,优选75-90wt%,基于组分b总重量计;
11.b2)至少一种重均分子量为150-400g/mol,优选180-350g/mol(测试方法参照gb/t 21863-2008)的氨基硅烷,其含量为0.3-4.8wt%,优选0.3-4.5wt%,更优选0.5-3.5wt%,特别优选0.5-2.5wt%,基于组分b总重量计;
12.b3)重均分子量为1000-2000g/mol(测试方法参照gb/t 21863-2008)的聚醚多元醇,其含量为5-15wt%,优选5-10wt%,基于组分b总重量计;
13.b4)至少一种胺类催化剂;和
14.b5)至少一种发泡剂。
15.优选的,所述氨基硅烷选自三乙氧基丙基硅烷、三甲氧基氨基丙基硅烷或其组合。
16.优选的,所述组分b还包括b6)重均分子量为8000-9000g/mol(测试方法参照gb/t 21863-2008)的苯乙烯/丙烯氰接枝聚醚,其含量为0-15wt%,优选owt%,基于组分b总重量计。
17.优选的,所述b5)发泡剂为水,其含量为1.5-3.0wt%,优选1.5-2.5wt%,基于组分b总重量计。
18.优选的,所述催化剂含量为0.1-2wt%,优选0.2-1.5wt%,基于所述组分b总重量计。
19.优选的,所述组分b还可选的包括b7)一种表面活性剂,所述表面活性剂优选硅油,其含量为0-1.2wt%,优选0-0.7wt%,基于组分b总重量计。
20.通过实验,我们意外的发现,本发明的制备聚氨酯半硬泡的方法,能够克服聚氨酯复合材料表皮粘接强度不够的缺陷,在保证各项物理性质满意的同时,极大的增强了粘接强度。使得其可以与更多种类的表皮材料完美结合,大大提高了其适用性。
21.业内通常添加苯乙烯/丙烯氰接枝聚醚以改善聚氨酯泡沫的物理性质例如粘接强度。苯乙烯/丙烯氰接枝聚醚的存在,可以让聚氨酯半硬泡的粘接/剥离强度得到提高。若不含苯乙烯/丙烯氰接枝聚醚,所制得的聚氨酯半硬质泡沫的粘接性能/剥离强度会急剧下降,测试时无泡沫残留,即剥离强度<1n/m,不可测量。然而,本领域技术人员知悉,挥发性有机物voc(volatile organic compound),是影响室内/车内空气品质的一种严重污染物。汽车内饰用品需要严格控制voc,以满足安全性和舒适性的要求。由于苯乙烯/丙烯氰接枝聚醚是由苯乙烯/丙烯氰于聚醚中悬浮聚合而成,有游离的苯乙烯/丙烯氰,会造成voc增加。
22.意外的,我们发现本发明的方案,在不含苯乙烯/丙烯氰接枝聚醚的时候,不仅仍然可以制得具有满意剥离强度的聚氨酯半硬质泡沫,还能避免使用会造成voc释放、污染环境的苯乙烯/丙烯氰接枝聚醚。
23.本发明的反应体系优选不含苯乙烯/丙烯氰接枝聚醚,即,优选的,本发明的反应体系中组分b所含苯乙烯/丙烯氰接枝聚醚的量为owt%,基于所述组分b总重量计。本发明
优选的方案,不仅可以制得物理性质优良、剥离强度/粘接性能卓越的聚氨酯半硬质泡沫,还减少了voc,减少了污染,更加健康、环保。
24.本发明的另一个方面,是提供一种聚氨酯半硬质泡沫,由本发明的制备聚氨酯半硬质泡沫的方法制得。
25.优选的,所述聚氨酯半硬质泡沫的平均剥离强度较未添加b2)氨基硅烷所制备的聚氨酯半硬质泡沫的平均剥离强度增加>15%,优选增加>40%,更优选增加>100%。
26.优选的,所述聚氨酯半硬质泡沫的平均剥离强度(测试方法参照pv2034)≥4n/5cm,优选≥6n/5cm。
27.优选的,所述聚氨酯半硬质泡沫的密度为100-240kg/m3,优选150-200kg/m3。
28.本发明的半硬质泡沫与现有技术中的半硬质泡沫相比,粘接强度得到了很大的提高。从而可以适应更多种类的表皮材料,制得更加结实、美观、性能卓越的聚氨酯复合材料/板。
29.本发明的再一个方面,是提供一种本发明的方法制备的聚氨酯半硬质泡沫在汽车装饰,优选汽车内饰方面的用途。
30.本发明的再一个方面,是提供一种制备聚氨酯复合板的方法,包括:
31.将至少一表皮置于一模具中,向所述模具中引入包括如下组分的聚氨酯反应体系,发泡后脱模得到所述聚氨酯复合板:
32.组分a,一种或多种多异氰酸酯;
33.组分b,包括:
34.b1)至少一种重均分子量为5000-12000g/mol,优选5000-6000g/mol(测试方法参照gb/t 21863-2008)的eo封端的,基于b1)组分总重量计氧亚乙基单元含量为10-20wt%的聚醚多元醇,其含量为70-90wt%,优选75-90wt%,基于组分b总重量计;
35.b2)至少一种重均分子量为150-400g/mol,优选180-350g/mol(测试方法参照gb/t 21863-2008)的氨基硅烷,其含量为0.3-4.8wt%,优选0.3-4.5wt%,更优选0.5-3.5wt%,特别优选0.5-2.5wt%,基于组分b总重量计;
36.b3)重均分子量为1000-2000g/mol(测试方法参照gb/t 21863-2008)的聚醚多元醇,其含量为5-15wt%,优选5-10wt%,基于组分b总重量计;
37.b4)至少一种胺类催化剂;和
38.b5)至少一种发泡剂。
39.优选的,所述至少一表皮为两层表皮,所述表皮材料选自pvc、san、聚氨酯、ps、pmi和pet。
40.本发明的再一个方面,是提供一种聚氨酯产品,包括本发明的制备聚氨酯半硬质泡沫的方法制备的聚氨酯半硬质泡沫。
41.优选的,所述聚氨酯产品选自聚氨酯复合板,优选汽车门板扶手、座椅扶手、门板上装和仪表板。
具体实施方案
42.现在对本发明的各方面进行详细说明。
43.聚氨酯半硬质泡沫反应体系各组分
44.多异氰酸酯组分
45.任何有机多异氰酸酯都可用于制备本发明的半硬质聚氨酯泡沫,包括芳族、脂族和脂环族多异氰酸酯和它们的组合。所述多异氰酸酯可用通式r(ngo)n表示,其中r表示含2-18个碳原子的脂肪族烃基、含6-15个碳原子的芳烃基、含8-15个碳原子芳脂族烃基,n=2-4。
46.可用的多异氰酸酯包括,优选但不限于,乙烯基二异氰酸酯、四亚甲基1,4-二异氰酸酯、己二异氰酸酯(hdi)、十二烷基1,2-二异氰酸酯、环丁烷-1,3-二异氰酸酯、环己烷-1,3-二异氰酸酯、环己烷-1,4-二异氰酸酯、1-异氰酸酯基-3,3,5-三甲基-5-异氰酸酯基甲基环己烷、六氢甲苯-2,4-二异氰酸酯、六氢苯基-1,3-二异氰酸酯、六氢苯基-1,4-二异氰酸酯、全氢化-二苯甲烷2,4-二异氰酸酯、全氢化-二苯甲烷4,4-二异氰酸酯、亚苯基1,3-二异氰酸酯、亚苯基1,4-二异氰酸酯、二苯乙烯1,4-二异氰酸酯、3,3-二甲基4,4-二苯基二异氰酸酯、甲苯-2,4-二异氰酸酯(tdi)、甲苯-2,6-二异氰酸酯(tdi)、二苯甲烷-2,4
’-
二异氰酸酯(mdi)、二苯甲烷-2,2
’-
二异氰酸酯(mdi)、二苯甲烷-4,4
’-
二异氰酸酯(mdi)、二苯基甲烷二异氰酸酯和/或具有更多环的二苯基甲烷二异氰酸酯同系物的混合物、多苯基甲烷多异氰酸酯(聚合mdi)、亚萘基-1,5-二异氰酸酯(ndi)、它们的异构体、它们与它们的异构体之间的任意混合物。
47.可用的多异氰酸酯,还包括用碳化二胺、脲基甲酸酯、或异氰酸酯改性所得的异氰酸酯,优选但不限于,二苯基甲烷二异氰酸酯、碳化二胺改性的二苯甲烷二异氰酸酯、它们的异构体、它们与它们的异构体之间的混合物。
48.当用于本发明时,多异氰酸酯包括异氰酸酯二聚体、三聚体、四聚体或其组合。
49.在本发明优选的实施例中,多异氰酸酯组分选用聚合mdi。
50.本发明的优选的实施例中,多异氰酸酯组分组分包括:a1)基于组分a计,0-10wt%,优选0.1-8wt%的2,2
’-
二苯甲烷二异氰酸酯;a2)基于组分a计,0-30wt%,优选10-25wt%的2,4
’-
二苯甲烷二异氰酸酯;和a3)基于组分a计,25-75wt%,优选35-55wt%的4,4
’-
二苯甲烷二异氰酸酯。
51.本发明的有机多异氰酸酯的nco含量为20-33wt%,优选25-32wt.%,特别优选30-32wt%。nco含量通过gb/t 12009.4-2016测得。
52.有机多异氰酸酯还可以以多异氰酸酯预聚物形式使用。这些多异氰酸酯预聚物可以通过使过量的上述有机多异氰酸酯与具有至少两个异氰酸酯反应性的基团的化合物在例如30-100℃,优选约80℃的温度下反应获得。本发明多异氰酸酯预聚物的nco含量为20-33wt%,优选25-32wt.%。nco含量通过gb/t 12009.4-2016测得。
53.多元醇组分
54.本发明所述多元醇,优选多种聚醚多元醇和/或它们的混合物。其中至少一种聚醚多元醇是甘油起始的多元醇。聚醚多元醇的官能度为2-4,其羟值为20-600,优选50-500,特别优选300-400。
55.所述聚醚多元醇可以通过已知的工艺过程制备。通常是将环氧乙烷或环氧丙烷与乙二醇、1,2-丙二醇、1,3-丙二醇、二甘醇、丙三醇、三羟甲基丙烷、季戊四醇、三乙醇胺、甲苯二胺、山梨醇和蔗糖混合,并以甘油或丙二醇为起始剂进行制备。
56.此外,所述聚醚多元醇还可以在催化剂的存在下通过将至少一种含有2-4个碳原
子的亚烷基的烯烃氧化物与含有2-8个,优选但不限于,3-8个活泼氢原子的化合物或者其它反应性的化合物反应来制备。
57.所述催化剂的例子有碱金属氢氧化物如氢氧化钠、氢氧化钾,或碱金属的醇盐例如甲醇钠、乙醇钠或乙醇钾或异丙醇钾。
58.可用的烯烃氧化物包括,优选但不限于,四氢呋喃、环氧乙烷、1,2-环氧丙烷、1,2-环氧丁烷、2,3-环氧丁烷、氧化苯乙烯及它们的任意混合物。
59.可用的含活泼氢原子的化合物包括多羟基化合物,优选但不限于,水、乙二醇、1,2-丙二醇、1,3-丙二醇、二甘醇、三羟甲基丙烷、它们的任意混合物,更优选多元、特别是三元或更多元醇,如丙三醇、三羟甲基丙烷、季戊四醇、山梨醇和蔗糖。可用的含活泼氢原子的化合物还包括,优选但不限于,有机二元羧酸如琥珀酸、己二酸、邻苯二甲酸和对苯二甲酸,或芳族或脂族取代的二胺如乙二胺、二亚乙基三胺、三亚乙基四胺、丙二胺、丁二胺、己二胺或甲苯二胺。
60.当用于本发明时,术语“环氧烷化合物”通常是指具有如下通式(i):
[0061][0062]
其中r1和r2独立地选自h、c
1-c6直链和支链烷基以及苯基和取代苯基。
[0063]
优选的,r1和r2独立地选自h、甲基、乙基、丙基和苯基。
[0064]
本领域技术人员已知“环氧烷化合物”的制备方法,例如其可以通过烯烃化合物的氧化反应获得。
[0065]
可用作本发明的环氧烷化合物的实例包括但不限于:环氧乙烷、1,2-环氧丙烷、1,2-环氧丁烷、2,3-环氧丁烷、氧化苯乙烯或它们的混合物,特别优选环氧乙烷与1,2-环氧丙烷的混合物。
[0066]
当用于本发明时,术语“环氧烷化合物”还包括氧杂环烷烃,其实例包括但不限于:四氢呋喃和氧杂环丁烷。
[0067]
当用于本发明时,所述“胺”是指含有伯氨基、仲氨基、叔氨基或其组合的化合物。可用作本发明的胺的化合物的实例包括但不限于三乙醇胺、乙二胺、甲苯二胺、二亚乙基三胺、三亚乙基四胺以及它们的衍生物,优选为乙二胺、甲苯二胺,特别优选甲苯二胺。
[0068]
本发明的多元醇组分,优选聚醚多元醇,更优选的,包括如下组分的聚醚多元醇:
[0069]
b1)至少一种重均分子量为5000-12000g/mol,优选5000-6000g/mol(测试方法参照gb/t 21863-2008)的eo封端的,基于b1)组分总重量计氧亚乙基单元含量为10-20wt%的聚醚多元醇,其含量为70-90wt%,优选75-90wt%,基于组分b总重量计;
[0070]
b2)至少一种重均分子量为150-400g/mol,优选180-350g/mol(测试方法参照gb/t 21863-2008)的氨基硅烷,其含量为0.3-4.8wt%,优选0.3-4.5wt%,更优选0.5-3.5wt%,特别优选0.5-2.5wt%,基于组分b总重量计;
[0071]
b3)重均分子量为1000-2000g/mol(测试方法参照gb/t 21863-2008)的聚醚多元醇,其含量为5-15wt%,优选5-10wt%,基于组分b总重量计。
[0072]
本发明的氨基硅烷,是指r-氨基丙基三乙氧基硅烷,分子式为h2nch2ch2ch2si(oc2h5)3的化学物质。氨基硅烷可以从市场上购得,也可以通过公知的方法合成。本发明的
氨基硅烷,选用重均分子量为150-400g/mol,优选180-350g/mol(测试方法参照gb/t 21863-2008)的氨基硅烷,其含量为0.3-4.8wt%,优选0.3-4.5wt%,更优选0.5-3.5wt%,特别优选0.5-2.5wt%,更特别优选1.2-2.5wt%,基于组分b总重量计。具体而言,本发明的氨基硅烷,包括但不限于三乙氧基丙基硅烷、三甲氧基氨基丙基硅烷、γ-环氧丙氧基三甲氧基硅烷、γ-环氧丙氧基丙基三乙氧基硅烷等。优选的,本发明的氨基硅烷选自三乙氧基丙基硅烷、三甲氧基氨基丙基硅烷或其组合。
[0073]
与通常在聚氨酯硬质泡沫使用的硅油不同的是,首先,本发明的氨基硅烷是特定的小分子氨基硅烷,如前所述,其分子量为150-400g/mol,优选180-350g/mol,也就是说不超过400g/mol。而通常用于聚氨酯硬质泡沫的硅油分子量约为8000g/mol,与本发明的氨基硅烷有着根本的区别。其次,本发明的氨基硅烷不再是用作表面活性剂,而是用作扩链剂。
[0074]
催化剂
[0075]
本发明的可选用的催化剂包括但不限于叔胺类催化剂。所述的胺类催化剂,优选但不限于三乙基胺、三丁基胺、二甲基乙醇胺、双(二甲氨基乙基)醚、三亚乙基二胺、n-乙基吗啉、n,n,n’,n
’-
四甲基-乙二胺、五甲基二亚乙基三胺、二甲氨基丙基撑二胺、n,n,n’,n
’-
四甲基二丙烯三胺或它们的混合物以及所述叔氨类催化剂的弱酸改性产物中的一种、两种或两种以上。
[0076]
发泡剂
[0077]
本发明所使用的发泡剂为水。优选的,水的含量为1.5-3.0wt%,优选1.5-2.5wt%,基于组分b总重量计。
[0078]
表面活性剂
[0079]
本发明所选用的表面活性剂优选硅油,即烯丙基聚醚多元醇改性聚二甲基硅氧烷。其含量为0-1.2wt%,优选0-0.7wt%,基于组分b总重量计。
[0080]
通过反复实验,意外的,我们发现本发明的制备聚氨酯半硬质泡沫的方法,能够极大的改善聚氨酯半硬质泡沫与表皮材料之间的粘接强度,从而可以制备出性能更优越、更结实耐用和美观的聚氨酯复合材料。
[0081]
除非另外说明,本文所使用的所有技术和科学术语具有本发明所属领域技术人员通常理解的相同意义。当本文中术语的定义与本发明所属领域技术人员通常理解的意义有矛盾时,以本文中所述的定义为准。
[0082]
除非另外说明,否则本文中使用的表达成分的量、反应条件等的所有数值被理解为在被术语“约”修饰。
[0083]
本文中所用的“和/或”是指所提及的要素之一或全部。
[0084]
本文中所用“包括”和“包含”涵盖只存在所提及要素的情形以及除了所提及要素还存在其它未提及要素的情形。
[0085]
除非另外说明,本文中所有百分比均为重量百分比。
[0086]
现通过实施例以说明的目的而非限制描述本发明。
[0087]
实施例
[0088]
测试项目和测试方法说明:
[0089]
官能度,是指根据行业公式:官能度=羟值*分子量/56100测定而得的数值;其中,分子量通过gpc高效液相色谱测定;
[0090]
芯密度,是指在聚氨酯泡沫复合板制作过程中所用模具里有过量填充的情况下测试的泡沫中心密度,即模塑泡芯密度,由astm d 1622-03测定;
[0091]
剥离强度,是指粘贴在一起的材料,从接触面进行单位宽度剥离时所需要的最大力。剥离时角度有90度或180度,单位为:牛顿/米(n/m)。它反映材料的粘结强度。本发明的剥离强度测试方法参照pv 2034。
[0092]
原料说明:
[0093]
表1-实施例1-5及对比实施例1反应体系原料来源及配比
[0094][0095]
半硬质泡沫的制备
[0096]
将事先准备好的1张表皮置于模具的底部,将表1和表3的反应体系各组分均匀混合后注入模具中,发泡后脱模得到聚氨酯半硬质泡沫样品。
[0097]
根据前述测试方法,测试各样品的6个测试点的剥离强度,并计算平均值,测试结果见表2和表4。
[0098]
表2-实施例1-4及对比实施例1剥离强度测试结果
[0099]
[0100][0101]
表3-实施例5-7及对比实施例2反应体系原料来源及配比
[0102]
[0103][0104]
表4-实施例5-7及对比实施例2剥离强度测试结果
[0105][0106]
由以上实施例和对比实施例及其测试结果可知,添加了氨基硅烷的聚氨酯反应体系制得的聚氨酯半硬质泡沫的剥离强度远远大于没有添加氨基硅烷的聚氨酯反应体系。
[0107]
在实施例1-4中同时添加了苯乙烯/丙烯氰接枝聚醚(hypelite e 850)。可以看到,随着氨基硅烷重量的增加,剥离强度逐渐增加。而实施例5-7中,不含苯乙烯/丙烯氰接枝聚醚(hypelite e 850),其相对于未添加氨基硅烷(对比实施例2)的方案,剥离强度的增大程度更加明显。但是在氨基硅烷的含量继续增加,到3wt%(实施例7)时,剥离强度反而有所下降。
[0108]
除了剥离强度很高,本发明的制备聚氨酯半硬质泡沫的方法简单高效,能够制得
品质优良、令人满意的聚氨酯半硬质泡沫。
[0109]
尽管上文针对本发明目的详细说明了本发明,但应理解的是,这种详细说明只是示例性的,除了可以由权利要求书限定的内容外,在不偏离本发明的精神及范围的情况下,本领域技术人员可以进行各种改变。