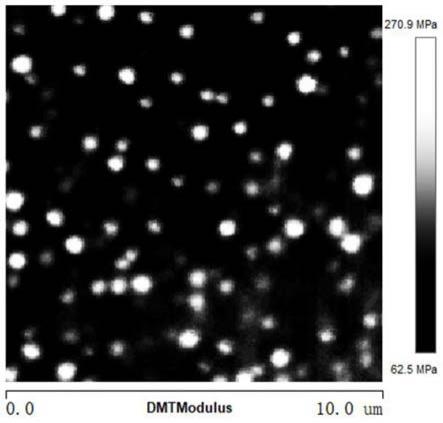
本发明属于高分子合成领域,具体涉及一种聚氨酯弹性体材料,尤其是一种耐低温耐油的热塑性硅橡胶-聚氨酯弹性体及其制备方法。
背景技术:
:硅橡胶是指主链由硅和氧原子交替构成,硅原子上通常连有两个有机基团的橡胶。传统的热塑性硅橡胶具有很多优点,如优异的低温柔顺性、耐热性、耐老化性和生物相容性等。正是由于这些优异的性能,硅橡胶在现代医学中发挥了非常重要的作用,各医院、科研单位和工厂相互协作,已成功研制了多种硅橡胶生物医用材料,并在生活中具有广泛的应用。然而,传统的热塑性硅橡胶耐油性很差,力学性能不佳,这也大大影响了其在生产和生活中的应用。热塑性聚氨酯(tpu)又称热塑性聚氨基甲酸酯,是由二元低聚物醇与二元有机异氰酸酯反应得到的一类主链上带有重复的氨基甲酸酯(-nhcoo-)基团的线性聚合物。传统的热塑性聚氨酯具有优异的力学性能,无需添加炭黑或白炭黑补强,亦无须添加芳烃油,系环境友好型材料。正是由于其优异的力学性能和可重复加工性,热塑性聚氨酯在生产和生活中具有十分广泛的应用,如3d打印,聚氨酯发泡材料等。然而,传统的聚氨酯仍存在一些不足,比如具有较差的耐高温性能和低温柔顺性。橡胶的耐油性取决于橡胶和油类的化学性质,油类能渗透到橡胶中使其产生溶胀,致使橡胶的强度和其它力学性能降低。橡胶的耐寒性是指橡胶在规定的低温下保持其弹性和正常工作的能力,主要取决于高聚物的两个基本过程——玻璃化转变和结晶。玻璃化转变温度是橡胶的分子链段由运动到冻结的转变温度,而链段运动是通过主链单键内旋转实现的,因此分子链的柔顺性是决定橡胶耐寒性的关键。也就是说,增加分子链的柔顺性有助于提高材料的低温性能,增大分子链的极性有助于提高材料的耐油性。yangmeng等(oilresistanceandmechanicalpropertiesofpolysiloxanenanocompositespreparedbyinsitureactionofreactivepolarmonomers[j].journalofappliedpolymerscience,2015,131(21):8558-8572.)研究了聚硅氧烷的耐油性,其在astm3#油中浸渍72h的体积变化率为50%-60%。meng,y.等(designandsynthesisofnon-crystallizable,low-tgpolysiloxaneelastomerswithfunctionalepoxygroupsthroughanioniccopolymerizationandsubsequentepoxidation.rscadvances,2014,4(59),31249-31260)研究了聚硅氧烷弹性体的耐寒系数,当温度从-60℃降到-70℃时,压缩耐寒系数kc从0.31降到近乎为0。上述聚硅氧烷弹性体并不能同时兼顾其弹性体材料的耐低温和耐油性能。技术实现要素:为了解决传统热塑性硅橡胶低强度且耐油性差等问题,同时保持其优异的耐低温性能,本发明在传统热塑性聚氨酯弹性体合成的基础上,引入聚硅氧烷作为软段,二异氰酸酯和小分子二元醇作为硬段,合成一种规整的热塑性硅橡胶-聚氨酯弹性体,该弹性体材料中,硬段的引入增大了分子链的极性,因此大大提升材料的耐油性。本发明的目的之一是提供一种耐低温耐油的热塑性硅橡胶-聚氨酯弹性体。本发明所提供的耐低温耐油的热塑性硅橡胶-聚氨酯弹性体以衍生自聚硅氧烷的链段为软段,以衍生自二异氰酸酯和小分子二元醇的链段为硬段;其中,以质量百分比来计,所述的热塑性硅橡胶-聚氨酯弹性体中软段含量为50~90%,优选65~85%;硬段含量为10~50%,优选15~35%。本发明所述的热塑性硅橡胶-聚氨酯弹性体的数均分子量优选为5~15万,分子量分布优选为1.5~3。本发明所述的热塑性硅橡胶-聚氨酯弹性体的玻璃化转变温度为-125~-110℃。其中,上述热塑性硅橡胶-聚氨酯弹性体中聚硅氧烷、二异氰酸酯和小分子二元醇的摩尔比为1:(1~4):(0.25~3),优选为1:(1.25~2.5):(0.25~1.5)。以上所述的聚硅氧烷分子量为1000~4000,优选1500~4000;以上所述的聚硅氧烷的玻璃化转变温度为-125~-110℃;以上所述聚硅氧烷为羟基封端的聚硅氧烷,选自羟基聚二甲基硅氧烷、羟基聚甲基苯基硅氧烷、羟基聚甲基苯基乙烯基硅氧烷中的至少一种,优选羟基封端聚二甲基硅氧烷;以上所述的二异氰酸酯选自二苯基甲烷二异氰酸酯、甲苯二异氰酸酯、异佛尔酮二异氰酸酯、六亚甲基二异氰酸酯、4,4'-二环己基甲烷二异氰酸酯、萘二异氰酸酯、对苯二异氰酸酯、1,4-环己烷二异氰酸酯、三甲基-1,6-六亚甲基二异氰酸酯、二甲基联苯二异氰酸酯中的至少一种,优选选自六亚甲基二异氰酸酯、4,4'-二环己基甲烷二异氰酸酯和二苯基甲烷二异氰酸酯中的至少一种;以上所述的小分子二元醇为1,4-丁二醇、乙二醇、顺-1,4-环己基二甲醇、反-1,4-环己基二甲醇中的至少一种,优选1,4-丁二醇。本发明的目的之二在于提供一种上述耐低温耐油的热塑性硅橡胶-聚氨酯弹性体的制备方法。上述热塑性硅橡胶-聚氨酯弹性体的制备方法包括将包含所述聚硅氧烷和二异氰酸酯在内的组分进行预聚反应,得到异氰酸酯封端的预聚体,随后加入扩链剂进行扩链反应,得到所述的耐低温耐油的热塑性硅橡胶-聚氨酯弹性体。其中,所述的聚硅氧烷为羟基封端的聚硅氧烷,分子量为1000~4000,优选1500~4000,进一步地,所述的聚硅氧烷选自羟基封端聚二甲基硅氧烷、羟基聚甲基苯基硅氧烷、羟基聚甲基苯基乙烯基硅氧烷的至少一种,优选选自羟基封端聚二甲基硅氧烷(htpdms);其中,所述的二异氰酸酯选自二苯基甲烷二异氰酸酯、甲苯二异氰酸酯、异佛尔酮二异氰酸酯、4,4'-二环己基甲烷二异氰酸酯、六亚甲基二异氰酸酯、二环己基甲烷二异氰酸酯、萘二异氰酸酯、对苯二异氰酸酯、1,4-环己烷二异氰酸酯、三甲基-1,6-六亚甲基二异氰酸酯、二甲基联苯二异氰酸酯中的至少一种,优选选自六亚甲基二异氰酸酯(hdi)、4,4'-二环己基甲烷二异氰酸酯(hmdi)和二苯基甲烷二异氰酸酯(mdi)中的至少一种;其中,所述的扩链剂为小分子二元醇,选自1,4-丁二醇、乙二醇、顺-1,4-环己基二甲醇、反-1,4-环己基二甲醇中的至少一种,优选选自1,4-丁二醇(bdo)。其中,所述的聚硅氧烷、二异氰酸酯和小分子二元醇的摩尔比为1:(1.25~4):(0.25~3),优选为1:(1.25~2.5):(0.25~1.5),始终控制体系的r值(-nco/oh)摩尔比等于1。上述热塑性硅橡胶-聚氨酯弹性体制备过程中,所述的预聚反应中采用的聚硅氧烷在与二异氰酸酯反应前,可以先进行脱水处理,脱水条件为在80~100℃(优选80℃)、0.090~0.096mpa(优选0.096mpa)的条件下持续搅拌2~3h;搅拌速率为90~120rad/min;上述的扩链反应优选在惰性条件下进行;上述的反应过程中还加入催化剂;以聚硅氧烷、二异氰酸酯和扩链剂的总质量来计,上述催化剂用量为0.05~0.3%;上述催化剂为有机锡催化剂,选自辛酸亚锡、二乙酸二丁基锡、二月桂酸二丁基锡、二(十二烷基硫)二丁基锡中的至少一种;上述的扩链反应过程中搅拌速率为300~500rad/min;扩链反应过程中,小分子二元醇扩链剂的滴加速率为1~2s/滴;上述的扩链反应后得到的热塑性硅橡胶-聚氨酯弹性体还可以进行固化处理。可采用现有技术中通常的固化处理,一般是将合成所得反应产物倒出后在置于真空烘箱,80~100℃(优选100℃)真空条件下固化10~30h(优选24h)。上述弹性体制备过程中,预聚反应温度为60~100℃,预聚反应时间2.5~3h;扩链反应温度为60~100℃,扩链反应时间20~60min。本发明提供的热塑性硅橡胶-聚氨酯弹性体在传统热塑性硅橡胶-聚氨酯弹性体合成的基础上,以衍生自聚硅氧烷的链段为软段,以衍生自二异氰酸酯和小分子二元醇的链段为硬段,得到一种规整的耐低温耐油的热塑性硅橡胶-聚氨酯弹性体。与现有技术相比,本发明的有益之处在于:1.本发明提供的耐低温耐油的热塑性硅橡胶-聚氨酯弹性体中,由于硬段的引入,其作为硅橡胶的化学连接点,在保证硅橡胶优异的低温柔顺性、耐热性、耐老化性和生物相容性的同时,大大提高了材料的力学性能,调节了聚氨酯弹性体的玻璃化转变温度,且产物的耐油性能大大提升,将来在生物医用材料的行业中有十分广阔的发展空间;2.本发明所提供的制备方法反应条件温和,不使用任何有机溶剂,不引入除反应物之外的其他任何杂质,制备工艺简单,重复性和可控性好。附图说明图1是实施例1~4的红外光谱图,其中a~d分别为实施例1~4的红外光谱图。图中,3300cm-1为n-h的伸缩振动峰,2830-2980cm-1为-ch2和-ch3的特征峰,1700-1740cm-1为-c=o的伸缩振动峰,在1020cm-1和1090cm-1处为-si-o-si-的特征峰,800cm-1和1260cm-1为-si-c-的伸缩振动峰,另外,-nco基团的吸收峰位置为2250-2280cm-1,实施例1~4并未出现明显的-nco特征峰,表明产物中不含-nco基团,-nco完全参与反应;图2是实施例1~4的应力-应变曲线,其中a~d分别为实施例1~4的应力-应变曲线,从图2中可以看出,随着硬段含量增大,嵌段硅橡胶-聚氨酯热塑性弹性体的拉伸强度增大,断裂伸长率有所下降,模量随硬段含量增大而增大,具有十分优异的力学性能;图3是实施例4的afm(原子力显微镜)图,相图中深色区域为聚氨酯弹性体材料中的软段硅橡胶基体,浅色的点状结构为聚氨酯弹性体材料中的硬段。由相图可以看出,硬段大小尺寸均匀,其在产物中的分布也很均匀;图4是实施例4的dma图,实施例4得到的耐低温耐油的热塑性硅橡胶-聚氨酯弹性体的玻璃化转变温度为-118℃;图5是实施例1~4的压缩耐寒系数kc随硬段含量的变化,图中两条曲线分别为实施例1~4在-50℃和-70℃的压缩耐寒系数,由图中曲线可以看出,随着硬段含量的增加,本发明制备的热塑性硅橡胶-聚氨酯弹性体的耐寒系数提高。具体实施方式下面结合具体实施例对本发明进行具体的描述,有必要在此指出的是以下实施例只用于对本发明的进一步说明,不能理解为对本发明保护范围的限制,本领域技术人员根据本
发明内容对本发明做出的一些非本质的改进和调整仍属本发明的保护范围。表1.实施例中所采用的测试仪器设备名称型号规格生产厂家凝胶渗透色谱仪(gpc)1525binaryhplcpump美国沃特世公司傅里叶变换红外光谱仪(ft-ir)8700/continuumxl美国尼高力公司差示扫描量热分析仪(dsc)204f德国耐驰公司原子力显微镜(afm)multimode8-hr德国布鲁克公司万能电子拉力机cmt4104中国深圳新三思仪器试验厂压缩耐寒系数测定仪bec-exmulti.pac2德国zwickroell公司实施例中所采用的测试条件及测试方法如下:1)耐油性测试方法:a.按照标准gb/t1690-2010,将摩尔比为1:1.25:0.25;1:1.5:0.5;1:2:1;1:2.5:1.5的si-tpu分别裁成25mm×25mm的正方形,每种比例的样品裁3个样,并分别编号#1,#2,#3;b.取测橡胶耐油性用的标准油irm903于500ml大烧杯中,并将样品悬空浸渍于标准油中,在常温(大概30℃)常压下浸泡72h;c.72h后取出样品,并用滤纸将样品表面的油渍擦拭干净,并在室温下晾3小时;d.对比前后质量和体积变化,并计算质量变化和体积变化。2)傅里叶变换红外光谱分析测试所使用的红外光谱分析(ft-ir)采用以下条件:使用atr模式,波数的扫描范围为4000~400cm-1,分辨率为4cm-1。3)凝胶渗透色谱分析测试所使用的凝胶渗透色谱分析采用以下条件进行测定:溶剂为四氢呋喃,标定物为一系列分子量梯度的聚苯乙烯。样品在四氢呋喃中完全溶解后,其中进样量为50ul,测试温度为30℃,样品浓度为3~5mg/ml,流动速度为1ml/min。4)应力应变测试实验过程中拉伸实验的测试条件:按照标准gb/t528-2009,将试样进行压片并裁成哑铃型样条,样条的工作区为15mm×4mm,拉伸速率为200mm/min,每组实验测试3~5根样条。5)微观形态分析实验过程中使用的原子力显微镜(afm)采用以下条件进行测试:试样在-60℃的条件下进行表面的抛光处理后,于afm下对其表面微观结构进行观察。6)耐寒性分析cl-1006型压缩耐寒系数测定仪是用于低温条件下的混炼胶的压缩耐寒试验,并符合gb/t6034-85《硫化橡胶的压缩耐寒系数的测定》、hg/t3866《硫化橡胶的压缩耐寒系数的测定》等国家标准的规定。将试样放在已冷却的仪器的压头和压缩平台之间,于5s内测量试样原高,再迅速将试样压缩至试样原高的80%并记录原高及压缩高。将仪器的压缩装置连同被压缩好的试样仪器置于冷却槽内,冷冻5min,松开手轮除去负荷并在10s内读取恢复高并记录。表2.实施例中采用的原料名称及来源原料名称来源羟基封端聚二甲基硅氧烷(htpdms)上海吉来德新材料科技有限公司1,4丁二醇(bdo)adamas试剂4,4-二环己基甲烷二异氰酸酯(hmdi)tci(上海)化成工业发展有限公司六亚甲基二异氰酸酯(hdi)上海阿拉丁生化科技股份有限公司二苯基甲烷二异氰酸酯(mdi)adamas试剂二月桂酸二丁基锡(tbdtl)tci(上海)化成工业发展有限公司高纯氮气北京市氧利来科技发展有限公司【实施例1】(1)软段除水:称取30g(0.02mol)分子量为1500的htpdms,加入带有搅拌装置的三口烧瓶中,在100℃,真空条件下除水2h,通过蒸馏装置接收馏出物;(2)预聚体的制备:将温度降至80℃,称取6.55g(0.025mol)的hmdi加入烧瓶中,在n2气氛中进行预聚反应,预聚过程持续3h;(3)热塑性硅橡胶-聚氨酯弹性体的制备:加入0.45g(0.005mol)扩链剂bdo进行扩链,半小时后加入一滴催化剂二月桂酸二丁基锡,并逐渐提高搅拌桨转速,大概一分钟后将产物倒出;(4)后固化处理:反应物倒出后置于真空烘箱,100℃真空条件下固化24h。【实施例2】(1)软段除水:称取30g(0.02mol)分子量为1500的htpdms,加入带有搅拌装置的三口烧瓶中,在100℃,真空条件下除水2h,通过蒸馏装置接收馏出物;(2)预聚体的制备:将温度降至80℃,称取7.86(0.03mol)g的hmdi加入烧瓶中,在n2气氛中进行预聚反应,预聚过程持续3h;(3)热塑性硅橡胶-聚氨酯弹性体的制备:加入0.9g(0.01mol)扩链剂bdo进行扩链,半小时后加入一滴催化剂二月桂酸二丁基锡,并逐渐提高搅拌桨转速,大概一分钟后将产物倒出;(4)后固化处理:反应物倒出后置于真空烘箱,100℃真空条件下固化24h。【实施例3】(1)软段除水:称取30g(0.02mol)分子量为1500的htpdms,加入带有搅拌装置的三口烧瓶中,在100℃,真空条件下除水2h,通过蒸馏装置接收馏出物;(2)预聚体的制备:将温度降至80℃,称取10.48g(0.04mol)的hmdi加入烧瓶中,在n2气氛中进行预聚反应,预聚过程持续3h;(3)热塑性硅橡胶-聚氨酯弹性体的制备:加入1.8g(0.02mol)扩链剂bdo进行扩链,半小时后加入一滴催化剂二月桂酸二丁基锡,并逐渐提高搅拌桨转速,大概一分钟后将产物倒出;(4)后固化处理:反应物倒出后置于真空烘箱,100℃真空条件下固化24h。【实施例4】(1)软段除水:称取30g(0.02mol)分子量为1500的htpdms,加入带有搅拌装置的三口烧瓶中,在100℃,真空条件下除水2h,通过蒸馏装置接收馏出物;(2)预聚体的制备:将温度降至80℃,称取13.1g(0.05mol)的hmdi加入烧瓶中,在n2气氛中进行预聚反应,预聚过程持续3h;(3)热塑性硅橡胶-聚氨酯弹性体的制备:加入2.7g(0.03mol)扩链剂bdo进行扩链,半小时后加入一滴催化剂二月桂酸二丁基锡,并逐渐提高搅拌桨转速,大概一分钟后将产物倒出;(4)后固化处理:反应物倒出后置于真空烘箱,100℃真空条件下固化24h。【实施例5】(1)软段除水:称取40g(0.02mol)分子量为2000的htpdms,加入带有搅拌装置的三口烧瓶中,在100℃,真空条件下除水2h,通过蒸馏装置接收馏出物;(2)预聚体的制备:将温度降至80℃,称取10.48g(0.04mol)的hmdi加入烧瓶中,在n2气氛中进行预聚反应,预聚过程持续3h;(3)热塑性硅橡胶-聚氨酯弹性体的制备:加入1.8g(0.02mol)扩链剂bdo进行扩链,半小时后加入一滴催化剂二月桂酸二丁基锡,并逐渐提高搅拌桨转速,大概一分钟后将产物倒出;(4)后固化处理:反应物倒出后置于真空烘箱,100℃真空条件下固化24h。【实施例6】(1)软段除水:称取40g(0.01mol)分子量为4000的htpdms,加入带有搅拌装置的三口烧瓶中,在100℃,真空条件下除水2h,通过蒸馏装置接收馏出物;(2)预聚体的制备:将温度降至80℃,称取5.24g(0.02mol)的hmdi加入烧瓶中,在n2气氛中进行预聚反应,预聚过程持续3h;(3)热塑性硅橡胶-聚氨酯弹性体的制备:加入0.9g(0.01mol)扩链剂bdo进行扩链,半小时后加入一滴催化剂二月桂酸二丁基锡,并逐渐提高搅拌桨转速,大概一分钟后将产物倒出;(4)后固化处理:反应物倒出后置于真空烘箱,100℃真空条件下固化24h。【实施例7】(1)软段除水:称取30g(0.02mol)分子量为1500的htpdms,加入带有搅拌装置的三口烧瓶中,在100℃,真空条件下除水2h,通过蒸馏装置接收馏出物;(2)预聚体的制备:将温度降至80℃,称取6.72g(0.04mol)的hdi加入烧瓶中,在n2气氛中进行预聚反应,预聚过程持续3h;(3)热塑性硅橡胶-聚氨酯弹性体的制备:加入1.8g(0.02mol)扩链剂bdo进行扩链,半小时后加入一滴催化剂二月桂酸二丁基锡,并逐渐提高搅拌桨转速,大概一分钟后将产物倒出;(4)后固化处理:反应物倒出后置于真空烘箱,100℃真空条件下固化24h。【实施例8】(1)软段除水:称取30g(0.02mol)分子量为1500的htpdms,加入带有搅拌装置的三口烧瓶中,在100℃,真空条件下除水2h,通过蒸馏装置接收馏出物;(2)预聚体的制备:将温度降至80℃,称取10g(0.04mol)的mdi加入烧瓶中,在n2气氛中进行预聚反应,预聚过程持续3h;(3)热塑性硅橡胶-聚氨酯弹性体的制备:加入1.8g(0.02mol)扩链剂bdo进行扩链,半小时后加入一滴催化剂二月桂酸二丁基锡,并逐渐提高搅拌桨转速,大概一分钟后将产物倒出;(4)后固化处理:反应物倒出后置于真空烘箱,100℃真空条件下固化24h。以实施例7为例来说明本发明提供的耐低温耐油的热塑性硅橡胶-聚氨酯弹性体的制备过程,可以看出采用本发明提供的制备方法可以得到结构规整的热塑性硅橡胶-聚氨酯弹性体材料。实施例7的制备过程如下:其中,上述分子结构中的r1和r2结构如下:上述实施例中,实施例1~4为探究不同硬段含量对产物结构与性能的影响,分别采用htpdms:hmdi:bdo为1:1.25:0.25、1:1.5:0.5、1:2:1、1:2.5:1.5的摩尔比,其硬段含量分别为18.9%、22.6%、29.0%、34.5%;实施例3、5和6为探索软段分子量对产物结构与性能的影响,控制htpdms:hmdi:bdo的摩尔比为1:2:1,分别采用1500、2000、4000三种不同分子量的htpdms作为软段;实施例3、7和8为探究不同二异氰酸酯对产物结构与性能的影响,保持软段分子量为1500和htpdms:hmdi:bdo的摩尔比为1:2:1不变,分别采用hmdi、hdi和mdi三种不同的二异氰酸酯。实施例1~8中得到的热塑性硅橡胶-聚氨酯弹性体的具体测试结果如下:表3.不同硬段含量的硅橡胶-聚氨酯弹性体的质量变化率和体积变化率硬段含量(%)δm/%δv/%实施例118.925.824.2实施例222.623.422.8实施例329.018.421.1实施例434.517.420.6表4.不同分子量软段合成的硅橡胶-聚氨酯弹性体的质量变化率和体积变化率软段分子量δm/%δv/%实施例3150018.421.1实施例5200023.222.5实施例6400035.629.7表5.不同硬段合成的硅橡胶-聚氨酯弹性体的质量变化率和体积变化率硬段化合物δm/%δv/%实施例3hmdi18.421.1实施例7hdi24.323.7实施例8mdi17.819.9表6.不同硬段含量的硅橡胶-聚氨酯弹性体在特定温度下的压缩耐寒系数硬段含量(%)kc(-50℃)/%kc(-70℃)/%实施例118.925.49.4实施例222.631.216.2实施例329.038.723.7实施例434.544.329.3表7.不同分子量软段合成的硅橡胶-聚氨酯弹性体在特定温度下的压缩耐寒系数软段分子量kc(-50℃)/%kc(-70℃)/%实施例3150038.723.7实施例5200036.221.2实施例6400026.510.9表8.不同硬段合成的硅橡胶-聚氨酯弹性体在特定温度下的压缩耐寒系数硬段化合物kc(-50℃)/%kc(-70℃)/%实施例3hmdi38.723.7实施例7hdi31.420.4实施例8mdi41.827.6表9.实施例1~4得到的硅橡胶-聚氨酯弹性体的测试数据mn/104mw/104pdi玻璃化转变温度/℃实施例111.931.72.6-118实施例29.624.52.5-118实施例37.212.41.7-118实施例47.318.52.5-118实施例58.419.22.3-122实施例69.823.52.4-125实施例79.419.22.0-118实施例810.328.72.8-118不同硬段含量的影响:由表3可以看出,随着硬段含量的提高,产物的质量变化率和体积变化率逐渐下降,说明产物的耐油性提高。极性基团的引入,大大提高产物的耐油性。同时,由表6可以看出,硬段含量的提高,也使得产物的压缩耐寒系数提高,产物耐寒性能更好。硬段的引入破坏了硅胶链段的规整结构,使分子链柔顺性下降,分子链结晶程度下降,因此耐寒性能提高。不同分子量软段的影响:由表4可以看出,软段分子量越高,其质量变化率和体积变化率增大,说明其耐油性下降。由于采用相同的摩尔比(1:2:1),软段分子量越高,其对应的硬段含量减少,耐油性下降。表7可以看出,高分子量的软段合成的产物其压缩耐寒系数更小,其耐寒性更差。不同硬段种类的影响:分别采用了hmdi、hdi和mdi三种不同的异氰酸酯。由表5可以看出,hmdi和mdi等带有刚性基团的异氰酸酯比hdi合成的产物具有更优异的耐油性。表8可以看出,mdi合成的产物压缩耐寒系数最高,其次为hmdi和hdi。由表9可以得到,合出的产物,其数均分子量均在7万以上,完全满足聚氨酯在生产应用上的要求。实施例1~4不同硬段含量的产物,其玻璃化转变温度(tg)均为-118℃;实施例3,5,6为不同分子量软段合成的产物,随着软段分子量的提高,其玻璃化转变温度提高。实施例3,7,8为不同硬段种类的产物,其玻璃化转变温度均为-118℃。以上结果表明,所得产物的tg主要表现为软段的玻璃化转变温度。本发明制备的热塑性硅橡胶-聚氨酯弹性体在astm3#油中浸渍72h的体积变化率为20%左右,远远低于现有技术中公开的聚硅氧烷在astm3#油中浸渍72h的体积变化率为50%~60%,说明本发明制备的产物耐油性大大提高。此外,现在技术公开的聚硅氧烷弹性体当温度从-60℃降到-70℃时,压缩耐寒系数kc从0.31降到0,本发明制备的热塑性硅橡胶-聚氨酯弹性体在-50℃的kc均在20%以上,温度降到-70℃时除了一两个产物之外基本上都达到20%,说明产物具有良好的耐低温性能。当前第1页12