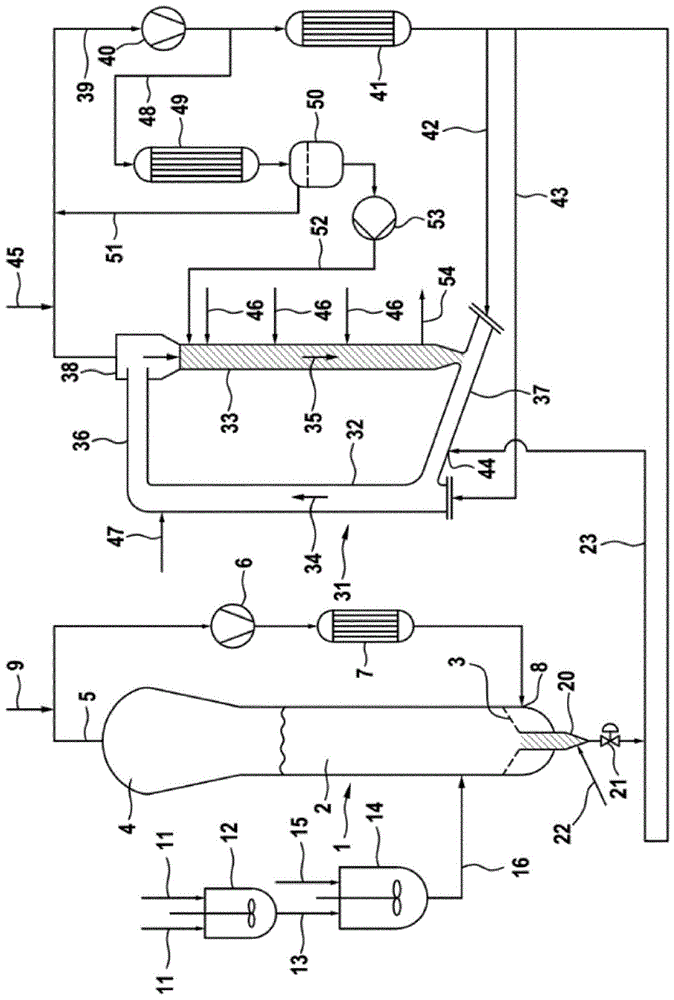
本公开提供用于在气相聚合反应器中制备乙烯聚合物的方法。本公开还提供了用于通过在气相聚合反应器中在预活化的聚合催化剂的存在下在包含丙烷作为聚合稀释剂的反应气体中使乙烯均聚或使乙烯与一种或多种c4-c8-1-烯烃共聚来制备颗粒形式的乙烯聚合物的方法。
背景技术:
:气相聚合方法是用于乙烯聚合的经济方法,例如使乙烯均聚或使乙烯与其它烯烃共聚。用于进行这些气相聚合的合适的反应器为例如流化床反应器、搅拌气相反应器或具有两个不同的互连气相聚合区的多区循环反应器。这些方法通常在气相中进行,所述气相包含乙烯和共聚单体,并且通常还包含其它气体组分,例如聚合稀释剂,例如氮气或烷烃,或作为低分子量反应产物的分子量改性剂的氢气。所获得的产物通常为通过通常包含固体催化剂组分的聚合催化剂体系形成的固体聚乙烯颗粒。进行聚合的反应气体的惰性组分充当聚合稀释剂并允许控制聚合速率。例如wo2006/082007a1公开了一种在气相反应器中在包含丙烷的反应气体存在下进行的乙烯聚合方法。为了使排出的聚乙烯颗粒脱气,这意味着将已经与聚乙烯颗粒一起从聚合反应器排出的反应气体的夹带部分作为晶间气体或作为溶解的烃除去,wo2006/082007a1使用已经在两阶段分离工艺中与反应气体分离的丙烷。通常收集从排出的聚乙烯颗粒分离的反应气体,再压缩至聚合压力并再循环至气相聚合反应器。然而,仅可以再循环在气相聚合反应器中使用的大部分反应气体;不能避免一些损失。这些损失量必须用新鲜进料代替。在气相聚合方法中,其在包含丙烷作为聚合稀释剂的反应气体的存在下进行,丙烷也可用于另外的目的。例如,wo2013/083548a2公开了用于烯烃聚合的多阶段方法,其中将聚烯烃颗粒从包含气体分配格栅和排出管的流化床反应器转移到第二气相聚合反应器,所述排出管与其进入分配格栅的上部开口整合并且含有从排出管的顶部移动到底部的聚烯烃颗粒的床。为了在聚烯烃颗粒的转移中防止第一聚合阶段的反应气体从流化床反应器携带到第二气相聚合反应器,将丙烷以一定的量引入到排出管中,使得在丙烷引入点上方的聚烯烃颗粒的床中引入丙烷的向上流,并且从排出管的下端取出聚烯烃颗粒。wo2018/087214a1公开了用于在至少一个气相反应器中在作为稀释剂的丙烷存在下制备乙烯聚合物的多步法,其中经由固体/气体分离器发生从第一气相聚合反应器到第二气相聚合反应器的转移。ep2803680a1公开了为这种分离器配备排出管。丙烷在此类气相聚合方法中的进一步用途(其也公开于例如wo2013/083548a2中)为在催化剂预活化步骤中利用丙烷作为液相,其中固体催化剂组分在引入聚合步骤之前与助催化剂(如烷基铝化合物)和任选地其它电子给体化合物接触。例如,在wo2008/022900a1中也公开了用丙烷作为稀释剂的催化剂预活化。已知可用作聚合反应的助催化剂的有机金属化合物如烷基铝也可用作极性化合物的清除剂,所述极性化合物可被带入聚合反应器中且可用作催化剂毒物。然而,有机金属化合物与极性化合物的反应改变了有机金属化合物作为乙烯聚合的助催化剂的可用性。这导致改变的反应器产率和产物性质。甚至更苛刻的是其中两个或更多个聚合反应器串联操作的情况,其中乙烯聚合物颗粒内的活性催化剂从一个反应器流动到后续反应器,并且各种进料流进料至每个反应器。在单独的聚合反应器中可获得的有机金属化合物的量的变化可以导致最终乙烯聚合物的性质的变化,然而进料流的杂质水平的波动可能使调节复杂化。用于纯化单体进料流的方法是已知的。为了在流化床反应器中由含杂质或次要组分如乙炔和乙烷的“原料乙烯”制备聚乙烯,wo03/014169a2公开了一种包括氢化阶段和聚合阶段的方法,在氢化阶段中“原料乙烯”与氢气反应以通过催化氢化除去乙炔而形成乙烯,部分乙烯转化成乙烷,在聚合阶段中离开氢化阶段的乙烯在气相中反应以形成聚乙烯,并且基于流化气体的总体积,在流化床反应器中使用的流化气体在进入反应器时包含乙烯和20至70体积%的乙烷。wo2018/022199a1公开了一种用于纯化从甲醇制烯烃设备产生的乙烯的方法,其包含(a)使包含至少99mol%乙烯的烯烃流通过硫保护床以除去硫化合物,(b)使来自(a)的流出物与氢化催化剂接触,(c)使来自(b)的流出物通过含铜金属的催化剂床以除去一氧化碳和氢气,和(d)使来自(c)的流出物通过干燥剂以除去极性污染物并产生包含大于或等于99.875mol%乙烯的纯化的乙烯流。然而,杂质不仅通过单体进料流引入聚合反应器中,而且还可以通过其它料流如丙烷进料流引入聚合过程中。由于与极性杂质的反应,使用低纯度的丙烷代替聚合过程中的丙烷损失可因此导致用作助催化剂的有机金属化合物的消耗,导致聚合反应器中有机金属化合物的浓度波动,并因此不利地影响反应器收率和选择性。然而,使用低纯度的丙烷代替丙烷损失也可能通过催化剂组分与极性杂质在聚合反应器中,特别是在预活化步骤中的副反应而影响催化剂性质。然而,也将非极性杂质如烯烃与丙烷进料流一起引入聚合反应器中可能不利地影响聚合过程。较低分子量的烯烃如丙烯可作为共聚单体引入聚乙烯链中并因此不利地影响聚合物性质,或者如果用于惰性化目的的气体组合物仍含有可聚合组分,则可通过成片或团块形成引起操作问题,例如在聚乙烯颗粒从第一聚合反应器转移到第二聚合反应器中。此外,在预活化步骤中存在较低分子量烯烃如丙烯可导致高分子量聚合物的形成,这是由于在不存在氢气的情况下烯烃与活化催化剂的不受控聚合。然而,这样的高分子量聚合物不与乙烯聚合物混溶并且可能降低所生产的聚乙烯的质量,例如通过形成凝胶。因此,需要提供一种在包含丙烷作为聚合稀释剂的反应气体的存在下制备乙烯聚合物,尤其是制备多峰乙烯聚合物的气相聚合方法,该方法确保稳定的催化剂预活化条件并使极性和非极性杂质对反应器收率和选择性以及对所得聚合物性质的不利影响最小化,并因此确保在聚合反应器中生产恒定结构和组成的乙烯聚合物,以便可靠地获得具有聚合物性质的目标最终组合的乙烯聚合物。此外,该方法在聚乙烯颗粒从第一聚合反应器转移到第二聚合反应器中不应具有操作问题。技术实现要素:本公开提供了一种用于制备乙烯聚合物的方法,包含在包含至少一个气相聚合反应器的气相聚合单元中,通过在20至200℃的温度和0.5至10mpa的压力下,在包含丙烷作为聚合稀释剂的反应气体中,在预活化的聚合催化剂存在下,使乙烯均聚或使乙烯和一种或多种c4-c12-1-烯烃共聚,形成颗粒形式的乙烯聚合物,其中将包含至少99mol%的丙烷和不超过100ppm-mol的丙烯的纯化的丙烷进料流进料到气相聚合单元,并且通过使烃流通过烃纯化单元进行纯化,所述烃纯化单元至少降低烃流中包含的丙烯、乙炔、一氧化碳、二氧化碳、氧气和水的浓度。在一些实施方案中,进料至气相聚合单元的纯化的丙烷进料流包含不大于0.03ppm-mol的一氧化碳,不大于0.4ppm-mol的二氧化碳,不大于2.0ppm-mol的氧,不大于3.0ppm-mol的乙炔和不大于2.0ppm-mol的水。在一些实施方案中,聚合催化剂的预活化通过在作为稀释剂的液体丙烷中使固体催化剂组分与有机金属化合物和任选的电子给体化合物接触以形成预活化的聚合催化剂来进行。在一些实施方案中,用作聚合催化剂预活化的液体稀释剂的丙烷取自纯化的丙烷进料流。在一些实施方案中,用于制备所述纯化的丙烷流的所述烃纯化单元中的一个是催化氢化单元。在一些实施方案中,催化氢化单元包含氢化催化剂,所述氢化催化剂是基于氧化铝载体的铂基或钯基组合物。在一些实施方案中,将已经通过催化氢化单元的烃流的一部分再循环至催化氢化单元的上游位置并与待氢化的烃流混合。在一些实施方案中,丙烷进料流的纯化如下进行:随后使烃流首先通过包含cu基催化剂的纯化单元,然后使所得流通过催化氢化单元,之后使所得流通过分离单元,然后使所得流通过干燥单元。在一些实施方案中,用于制备所述纯化的丙烷进料流的所述烃流是包含至少99mol%丙烯的纯化的丙烯流。在一些实施方案中,乙烯聚合物为多峰乙烯聚合物,并且所述气相聚合单元包含两个或更多个气相聚合反应器的反应器级联,所述反应器级联包含第一聚合反应器和一个或多个后续聚合反应器,所述第一聚合反应器中进料所述预活化的聚合催化剂,所述多个后续聚合反应器接收以活性形式并入在前述反应器中形成的乙烯聚合物颗粒中的聚合催化剂。在一些实施方案中,反应器级联的第一反应器是流化床反应器。在一些实施方案中,流化床反应器包含聚合物排出管,所述聚合物排出管含有从所述排出管的顶部移动到底部的乙烯聚合物颗粒的床,并且将丙烷以在所述丙烷引入点上方的所述乙烯聚合物颗粒的床中诱导所述丙烷的向上流的量引入到所述排出管中。在一些实施方案中,后续聚合反应器是多区循环反应器,在所述多区循环反应器中,一个聚合区是提升管,在所述提升管中生长的聚烯烃颗粒在快速流化或输送条件下向上流动,并且另一个聚合区是下降管,在所述下降管中,生长的聚烯烃颗粒以致密化的形式向下流动,其中提升管和下降管互连,离开提升管的聚烯烃颗粒进入下降管,离开下降管的聚烯烃颗粒进入提升管,从而通过提升管和下降管建立聚烯烃颗粒的循环。在一些实施方案中,乙烯聚合物为高密度聚乙烯,所述高密度聚乙烯具有根据dineniso1183-1:2004在23℃下测定的0.935g/cm3至0.970g/cm3的密度。附图说明图1示意性地示出了用于根据本公开的方法制备乙烯聚合物的聚合反应器级联的设置。图2示意性地示出了用于纯化进料到气相聚合单元的丙烷进料流的烃纯化单元和用于回收从聚合反应器排出的反应气体的组分的丙烷和单体后处理单元的设置。具体实施方式本公开提供一种用于制备乙烯聚合物的方法,所述方法包含在聚合催化剂存在下使乙烯均聚或使乙烯与作为共聚单体的一种或多种其它烯烃共聚。除了乙烯之外,可用于本公开的方法中的烯烃尤其为1-烯烃,即具有末端双键的烃,而不限于此。优选非极性烯烃化合物。特别优选的1-烯烃是直链或支链c4-c12-1-烯烃,特别是直链c4-c10-1-烯烃如1-丁烯、1-戊烯、1-己烯、1-庚烯、1-辛烯、1-癸烯或支链c2-c10-1-烯烃如4-甲基-1-戊烯、共轭和非共轭二烯如1,3-丁二烯、1,4-己二烯或1,7-辛二烯。合适的烯烃还包含其中双键为可具有一个或多个环系的环状结构的一部分的烯烃。实例是环戊烯、降冰片烯、四环十二碳烯或甲基降冰片烯或二烯如5-亚乙基-2-降冰片烯、降冰片二烯或乙基降冰片二烯。还可以使乙烯与两种或更多种烯烃的混合物共聚。作为乙烯聚合中的共聚单体,优选使用至多20wt.%,更优选0.01wt.%至15wt.%,特别是0.05wt.%至12wt.%的c4-c8-1-烯烃,特别是1-丁烯、1-戊烯、1-己烯和/或1-辛烯。特别优选其中乙烯与0.1wt.%至12wt.%1-己烯和/或1-丁烯,特别是0.1wt.%至12wt.%1-己烯共聚的方法。气相聚合方法是其中从包含一种或多种单体的气相获得固体聚合物的方法。这样的方法通过将固体预活化的聚合催化剂进料到气相聚合反应器中来进行,并且聚合物在这些颗粒上生长。所得聚乙烯颗粒具有或多或少规则的形态和尺寸,然而其取决于催化剂形态和尺寸以及取决于聚合条件。典型地,所获得的聚乙烯颗粒的平均粒径在从约500至约3000μm的范围内。烯烃的聚合可以使用所有常规的烯烃聚合催化剂进行。这意味着聚合可以使用基于氧化铬的菲利普催化剂,使用齐格勒或齐格勒-纳塔催化剂,或使用单点催化剂进行。出于本公开的目的,单点催化剂是基于化学上均匀的过渡金属配位化合物的催化剂。此外,还可以将这些催化剂中的两种或更多种的混合物用于烯烃的聚合。这种混合催化剂通常称为混合催化剂。这些用于烯烃聚合的催化剂的制备和使用通常是已知的。优选的催化剂是齐格勒型催化剂,优选包含钛或钒的化合物、镁的化合物和任选的电子给体化合物和/或粒状无机氧化物作为载体材料。在本公开的一个特别优选的实施方案中,气相α-烯烃聚合方法在齐格勒型催化剂的存在下进行,所述齐格勒型催化剂包含烷基铝与负载在卤化镁上的钛化合物的反应产物。作为钛化合物,通常使用三价或四价钛的卤化物或醇盐,其中烷氧基钛卤素化合物或各种钛化合物的混合物也是可能的。合适的钛化合物的实例为tibr3、tibr4、ticl3、ticl4、ti(och3)cl3、ti(oc2h5)cl3、ti(o-i-c3h7)cl3、ti(o-n-c4h9)c13、ti(oc2h5)br3、ti(o-n-c4h9)br3、ti(och3)2cl2、ti(oc2h5)2c12、ti(o-n-c4h9)2c12、ti(oc2h5)2br2、ti(och3)3cl、ti(oc2h5)3cl、ti(o-n-c4h9)3cl、ti(oc2h5)3br、ti(och3)4、ti(oc2h5)4或ti(o-n-c4h9)4。优选使用包含氯作为卤素的钛化合物。同样优选的是,除了钛之外仅包含卤素的卤化钛,并且在这些之中尤其是氯化钛,并且特别是四氯化钛。在钒化合物中,可以特别提及卤化钒、卤氧化钒、醇钒和乙酰丙酮钒。优选氧化态3至5的钒化合物。在固体组分的生产中,优选另外使用至少一种镁的化合物。这种类型的合适化合物是含卤素的镁化合物,例如卤化镁,特别是氯化物或溴化物和镁化合物,由它们可以以常规方式,例如通过与卤化剂反应获得卤化镁。对于本发明目的,卤素是氯、溴、碘或氟或两种或更多种卤素的混合物,优选氯或溴,特别是氯。可能的含卤素的镁化合物特别是氯化镁或溴化镁。可获得卤化物的镁化合物例如为烷基镁、芳基镁、烷氧基镁化合物或芳氧基镁化合物或格氏化合物。合适的卤化剂是例如卤素、卤化氢、sicl4或ccl4,优选氯或氯化氢。合适的无卤素镁化合物的实例是二乙基镁、二正丙基镁、二异丙基镁、二正丁基镁、二仲丁基镁、二叔丁基镁、二戊基镁、正丁基乙基镁、正丁基仲丁基镁、正丁基辛基镁、二苯基镁、二乙氧基镁、二正丙氧基镁、二异丙基氧基镁、二正丁基氧基镁、二仲丁氧基镁、二叔丁氧基镁、二戊酰氧基镁、正丁氧基乙氧基镁、正丁氧基仲丁氧基镁、正丁氧基辛氧基镁和二苯氧基镁。其中,优选使用正丁基乙基镁或正丁基辛基镁。格氏化合物的实例为甲基氯化镁、乙基氯化镁、乙基溴化镁、乙基碘化镁、正丙基氯化镁、正丙基溴化镁、正丁基氯化镁、正丁基溴化镁、仲丁基氯化镁、仲丁基溴化镁、叔丁基氯化镁、叔丁基溴化镁、己基氯化镁、辛基氯化镁、戊基氯化镁、异戊基氯化镁、苯基氯化镁和苯基溴化镁。作为用于制备固体催化剂组分的镁化合物,除了二氯化镁或二溴化镁之外,优选使用二(c1-c10烷基)镁化合物。优选地,齐格勒-或齐格勒-纳塔催化剂包含选自钛、锆、钒、铬的过渡金属。用于制备齐格勒型催化剂的合适的电子给体化合物是例如醇、二醇、酯、酮、胺、酰胺、腈、烷氧基硅烷和脂族醚。这些电子给体化合物可以单独使用或以彼此的混合物以及与另外的电子给体化合物的混合物使用。优选的醇是式r1oh的那些,其中r1基团是c1-c20烃基。优选地,r1是c1-c10烷基。具体实例是甲醇、乙醇、异丙醇和正丁醇。优选的二醇是碳原子总数低于50的那些。其中特别优选的是碳原子总数低于25的1,2或1,3二醇。具体实例为乙二醇、1,2-丙二醇和1,3-丙二醇。优选的酯是c1-c20脂族羧酸的烷基酯,特别是脂族单羧酸的c1-c8烷基酯,例如乙酸乙酯、甲酸甲酯、甲酸乙酯、乙酸甲酯、乙酸丙酯、乙酸异丙酯、乙酸正丁酯、乙酸异丁酯。优选的胺是式nr23的那些,其中r2基团独立地是氢或c1-c20烃基,条件是r2基团不同时是氢。优选地,r2是c1-c10烷基。具体实例为二乙胺、二异丙胺和三乙胺。优选的酰胺为式r3conr42的那些,其中r3和r4独立地为氢或c1-c20烃基。具体实例是甲酰胺和乙酰胺。优选的腈是式r1cn的那些,其中r1具有以上给出的相同含义。具体实例是乙腈。优选的烷氧基硅烷是具有式r5ar6bsi(or7)c的那些,其中a和b是0至2的整数,c是1至4的整数并且总和(a+b+c)是4;并且r5、r6和r7是任选地含有杂原子的具有1-18个碳原子的烷基、环烷基或芳基基团。特别优选的是硅化合物,其中a是0或1,c是2或3,r6是任选地含有杂原子的烷基或环烷基,并且r7是甲基。这种优选的硅化合物的实例是甲基三甲氧基硅烷、二甲基二甲氧基硅烷、三甲基甲氧基硅烷和叔丁基三甲氧基硅烷。优选的电子给体化合物选自酰胺、酯和烷氧基硅烷。齐格勒型催化剂通常在作为助催化剂的有机金属化合物的存在下聚合。优选的助催化剂是元素周期表第1、2、12、13或14族金属的有机金属化合物,特别是第13族金属的有机金属化合物,特别是有机铝化合物。优选的助催化剂为例如有机金属烷基、有机金属醇盐或有机金属卤化物。优选的有机金属化合物包含烷基锂、烷基镁或烷基锌、烷基卤化镁、烷基铝、烷基硅、硅醇盐和烷基卤化硅。更优选地,所述有机金属化合物包含烷基铝和烷基镁。还更优选地,有机金属化合物包含烷基铝,最优选三烷基铝化合物或其中烷基被卤素原子(例如氯或溴)替代的这类化合物。这样的烷基铝的实例是三甲基铝、三乙基铝、三异丁基铝、三正己基铝或氯化二乙基铝或其混合物。根据本公开的用于制备乙烯聚合物的方法在预活化的聚合催化剂的存在下进行。聚合催化剂的预活化优选通过在作为稀释剂的液体丙烷中使固体催化剂组分与有机金属化合物和任选的电子给体化合物接触以形成预活化的聚合催化剂来进行。催化剂预活化可以在单个预活化容器中或在两个或更多个催化剂预活化容器的序列中进行,其中催化剂组分的接触优选在-20℃至60℃,更优选20℃至50℃的温度下进行。固体催化剂组分优选连续引入到催化剂预活化容器中或引入到催化剂预活化容器序列的第一个中。本公开的方法在包含至少一个气相聚合反应器的气相聚合单元中进行。合适的气相聚合反应器为例如搅拌气相反应器、多区气相反应器或气相流化床反应器。这些类型的反应器通常是本领域技术人员已知的。搅拌气相反应器可以例如水平或垂直搅拌。优选地,气相聚合单元包含两个或更多个气相聚合反应器的反应器级联。气相聚合单元可以进一步包含例如用于进料、预活化和/或预聚合聚合催化剂的设备。气相聚合单元可以包含用于处理从聚合反应器排出的乙烯聚合物颗粒的设备和/或用于回收与乙烯聚合物颗粒一起从聚合反应器排出的反应气体的组分的设备。优选的反应器是流化床反应器,即包含通过从下方引入气体而保持在流化状态的聚合聚烯烃颗粒的床的反应器。然后通常在反应器的上端取出该气体,冷却以除去聚合热并在其下端再循环回到反应器中。优选的反应器为另外的多区循环反应器,其例如描述于wo97/04015和wo00/02929中,并且具有两个互连聚合区,提升管和下降管,在提升管中生长的聚烯烃颗粒在快速流化或输送条件下向上流动,在下降管中生长的聚烯烃颗粒在重力作用下以致密形式流动。离开提升管的聚烯烃颗粒进入下降管,并且离开下降管的聚烯烃颗粒被再次引入到提升管中,从而在两个聚合区之间建立聚合物循环,并且聚合物交替多次通过这两个区。通过在其提升管和下降管中建立不同的聚合条件,还可以在不同的聚合条件下操作一个多区循环反应器的两个聚合区。为此,可以部分或完全防止离开提升管并夹带聚烯烃颗粒的气体混合物进入下降管。这可以例如通过将气体和/或液体混合物形式的阻挡流体进料到下降管中,优选在下降管的上部中实现。阻挡流体应当具有与存在于提升管中的气体混合物的组成不同的合适组成。添加的阻挡流体的量可以以如下方式调节:产生与聚烯烃颗粒的流动逆流的气体的向上流动,特别是在其顶部,作为对来自提升管的颗粒中夹带的气体混合物的阻挡。以这种方式,可以在一个多区循环反应器中获得两个不同的气体组成区。此外,还可以在下降管的任何点,优选在屏障进料点以下引入补充单体、共聚单体、分子量调节剂如氢和/或惰性流体。因此,还可以容易地沿着下降管产生变化的单体、共聚单体和氢浓度,从而导致聚合条件的进一步差异。本公开的气相聚合在20至200℃,优选30至160℃,特别是65至125℃的温度下进行。用于制备乙烯聚合物的聚合压力为0.5mpa至10mpa,优选1.0mpa至8mpa,特别是1.5mpa至4mpa,其中这些压力,如本公开中给出的所有压力,必须理解为绝对压力,即具有尺寸mpa(绝对值)的压力。本公开的方法在包含丙烷作为聚合稀释剂的反应气体的存在下进行。反应器内的反应气体混合物另外包含待聚合的烯烃,即乙烯和一种或多种任选的共聚单体。在本公开的优选实施方案中,反应气体混合物具有30至99vol.%,更优选50至95vol.%,特别是60至90vol.%的惰性组分含量。该反应气体混合物可以进一步包含另外的组分,如抗静电剂或分子量调节剂如氢。反应气体混合物的组分可以气态形式或作为在反应器内蒸发的液体进料至气相聚合反应器中。聚合也可以以冷凝或超冷凝模式进行,其中将部分循环气体冷却至露点以下并作为液相和气相单独返回反应器或作为两相混合物一起返回反应器,以额外利用蒸发焓来冷却反应气体。在本公开的优选实施方案中,该方法在两个或更多个气相聚合反应器的反应器级联中进行,所述反应器级联包含其中进料预活化的聚合催化剂的第一聚合反应器,和一个或多个后续聚合反应器,所述后续聚合反应器接收以活性形式进料至第一聚合反应器的聚合催化剂,所述聚合催化剂并入在前述反应器中形成的乙烯聚合物颗粒中。反应器级联的气相聚合反应器可以是任何类型的气相聚合反应器,例如水平或垂直搅拌的气相反应器、多区循环反应器或流化床反应器。反应器级联的气相聚合反应器可以是相同类型的,或者反应器级联可以包含不同类型的气相聚合反应器。在一些实施方案中,反应器级联中的气相聚合可以在预聚合阶段之前进行,然后优选作为悬浮聚合,优选在环管反应器中进行。在本公开的一个特别优选的实施方案中,聚合在反应器级联中进行,所述反应器级联包含作为第一反应器的流化床反应器和布置在其下游的多区循环反应器。在用于实施本公开的方法的反应器级联中用作第一聚合反应器的优选的流化床反应器配备有用于从流化床反应器排出乙烯聚合物颗粒的排出管。排出管优选地以其上部开口整合到分配格栅的方式定位,并且排出管优选地基本上垂直地布置。配备有这样的排出管的流化床反应器例如公开于wo2013/083548a2中。在这种流化床反应器中,来自流化床的乙烯聚合物颗粒由于重力落入排出管中并在其中形成乙烯聚合物颗粒的致密床。在排出管的下端,乙烯聚合物颗粒被取出并转移到随后的气相反应器。因此,排出管内的乙烯聚合物颗粒在重力驱动下从排出管的顶部向下移动。优选地,乙烯聚合物颗粒作为塞流从排出管的顶部移动到底部。在其下端,排出管设置有排出阀,乙烯聚合物颗粒通过该排出阀从排出管排出。以在丙烷引入点上方的乙烯聚合物颗粒床中引入向上的丙烷流的量将丙烷进料至排出管中。优选地,将丙烷引入到排出管的下三分之一中,特别是在靠近排出管的下端的位置处。还可以在多于一个位置处将丙烷进料到排出管中。优选地,丙烷以这样的方式进料,即,其在丙烷引入点上方的区域中分布在排出管的整个横截面上。丙烷优选以气态形式进料到排出管中。因此,所引入的丙烷替代了流化床反应器的反应气体并且充当屏障,这防止了流化床反应器的反应气体被转移到第二聚合反应器。通过利用仅包含非常少量的不饱和组分如丙烯的纯化的丙烷,防止在排出管和/或在从流化床反应器到第二气相聚合反应器的输送管线中发生显著的聚合,其在聚乙烯颗粒从第一聚合反应器到第二聚合反应器的输送中引起排出管的操作问题,例如堵塞排出管和/或乙烯聚合物输送管线。在本公开的方法中获得的乙烯聚合物优选是多峰的。出于本公开的目的,术语“多峰”意指所获得的聚合物含有多种聚合物组分,每种组分在单独的反应器或反应器区中生产并且在共聚单体的类型和/或量或分子量分布方面不同于其它组分。如本文所用的术语“多峰”还应包括“双峰”。所述多峰乙烯聚合物优选在不同聚合条件下操作的聚合反应器或反应器区的级联中制备,并且最终聚合物是在相应的反应器或反应器区中制备的不同聚合物的混合物。将催化剂和聚合物以串联的方式从从一个反应器转移到另一个反应器。如图1所示,将预活化的催化剂与乙烯、丙烷、作为助催化剂的有机金属化合物和任选的氢气和/或共聚单体一起进料到级联的两个气相反应器的第一反应器中。离开第一反应器的聚合物源于该反应器中的催化剂活性和选择性,这又与存在的有机金属化合物的有效量、反应器温度、压力和进料浓度有关。然而,第一反应器中催化剂的催化剂活性和选择性受催化剂、有机金属化合物助催化剂和可能存在的催化剂毒物的相互作用影响。如果催化剂毒物例如与丙烷进料流一起进入反应器,则毒物与有机金属化合物发生化学反应,使得存在的有机金属化合物的有效量改变。这又可以改变催化剂体系的活性和选择性。在第二反应器和任何随后的反应器中,除了不添加新鲜的有机金属化合物和另外的聚合催化剂之外,在与丙烷一起进入的杂质,聚合物中的活性催化剂和有机金属化合物助催化剂之间发生相同的相互作用。相反,反应器接收来自在前反应器的乙烯聚合物颗粒内的活性催化剂和助催化剂。因此,在多反应器级联系统中,当乙烯的聚合在每个专用反应器中发生以制备各自具有其自身分子量的聚合物时,催化剂的活性和有机金属化合物助催化剂的浓度在每个反应器内并且从反应器到反应器变化。这种系统的复杂性随着反应器数量的增加而显著增加。与在单个反应器中生产的聚乙烯等级不同,多反应器聚合单元的聚合产物是至少两种聚合的结果,所述至少两种聚合靶向每个反应器或反应器区中的单独的聚合物以实现最终聚合物的期望的最终产物性质设定。特别是在制备多峰乙烯聚合物的情况下,对于多峰乙烯聚合物,在每个聚合反应器或反应器区中生产不同的乙烯聚合物,在单独的聚合反应器或反应器区中生产的乙烯聚合物部分的结构和组成的小差异可以导致最终乙烯聚合物的产物性质的显著差异。优选地,通过所述聚合方法生产的乙烯聚合物为优选具有0.935g/cm3至0.970g/cm3范围内的密度的高密度聚乙烯(hdpe)树脂。更优选地,密度在0.940g/cm3至0.970g/cm3的范围内。最优选地,密度在0.945g/cm3至0.965g/cm3的范围内。密度根据dineniso1183-1:2004,方法a(浸渍),用2mm厚的压塑板测量,所述压塑板用限定的热历史制备:在180℃,20mpa下压制8分钟,随后在沸水中结晶30分钟。优选地,hdpe树脂具有1g/10min至100g/10min,更优选1.5g/10min至50g/10min,并且最优选2g/10min至35g/10min的熔体流动速率mfr21.6。该mfr21.6是根据dineniso1133:2005,条件g在190℃的温度下在21.6kg的负荷下测量的。该聚合工艺生产的乙烯聚合物特别适用于制备薄膜、管或小型吹塑或大型吹塑聚乙烯制品。此类膜、管或小型吹塑或大型吹塑聚乙烯制品可以通过将已经通过根据本公开的方法制备的乙烯聚合物转化成膜、管或小型吹塑或大型吹塑聚乙烯制品来制备。图1示意性地示出了用于实施本公开的方法的包含流化床反应器和多区循环反应器的聚合反应器级联的设置。第一气相反应器,流化床反应器(1)包含聚乙烯颗粒的流化床(2)、气体分配格栅(3)和减速区(4)。与反应器的流化床部分的直径相比,减速区(4)通常具有增加的直径。通过向上流动的气体进料通过置于反应器(1)底部的气体分配格栅(3)使聚乙烯床保持流化状态。经由再循环管线(5)离开该减速区(4)的顶部的该反应气体的气态流被压缩机(6)压缩,该反应气体的气态流被转移到热交换器(7)中,在该热交换器中该反应气体的气态流被冷却,然后在位置(8)在气体分配格栅(3)下方的点处再循环至流化床反应器(1)的底部。补充单体、分子量调节剂和丙烷可以在各种位置进料到反应器(1)中,例如经由压缩机(6)上游的管线(9)。为了活化本公开的聚合方法中使用的聚合催化剂体系,将固体催化剂组分,助催化剂如烷基铝化合物和任选的外部电子给体化合物与作为液体稀释剂的丙烷一起经由一个或多个管线(11)进料到第一连续操作的搅拌槽(12)中,在该搅拌槽中组分接触。将搅拌槽(12)的内容物经由管线(13)转移到第二连续操作的搅拌槽(14)中。还可以经由一个或多个管线(15)将另外的组分例如另外的丙烷添加到第二搅拌槽(14)中。然而,还可以向第二搅拌槽(14)中另外引入乙烯或乙烯与一种或多种1-烯烃的混合物以进行预聚合。将第二搅拌槽(14)的内容物经由管线(16)转移至流化床反应器(1)。该流化床反应器(1)进一步包含排出管(20),该排出管与其进入该气体分配格栅(3)的上部开口整合的并且优选地被布置为基本上竖直的。该排出管(20)可以由均匀的直径制成,或优选地包含在向下方向上具有减小的直径的多个区段。该气体分配格栅(3)可以是平坦的,但优选地被赋予锥形形状,其方式为使得其朝向该排出管(20)的向下倾斜促进该聚乙烯颗粒由于重力进入该排出管(20)。排出管(20)的上部开口优选位于相对于气体分配格栅(3)的中心位置。在流化床反应器(1)的操作过程中,排出管(20)含有从排出管的顶部移动到底部的聚乙烯颗粒的床。聚乙烯颗粒通过上部开口进入排出管(20),聚乙烯颗粒优选通过排出阀(21)连续排出,该排出阀优选是分段式球阀。丙烷经由管线(22)进料到排出管(20)中,优选在靠近排出管下端的位置以使得在聚乙烯颗粒床中引起丙烷的向上流的量进料到排出管(20)中。排出阀(21)布置在用于将聚乙烯颗粒转移至第二气相反应器的输送管线(23)上方。第二气相反应器是具有两个反应区(提升管(32)和下降管(33))的多区循环气相反应器(31),其由聚乙烯颗粒重复通过。在提升管(32)内,聚烯烃颗粒在快速流化条件下沿着箭头(34)的方向向上流动。在下降管(33)内,聚乙烯颗粒在重力作用下沿着箭头(35)的方向向下流动。该提升管(32)和该下降管(33)通过这些互连弯管(36)和(37)适当地互连。聚乙烯颗粒和气态混合物在流过提升管(32)之后离开提升管(32)并输送至固体/气体分离区(38)。这种固体/气体分离可以通过使用常规分离装置例如像旋风分离器的离心分离器来实现。聚乙烯颗粒从分离区(38)进入下降管(33)中。离开所述分离区(38)的所述气态混合物借助于再循环管线(39)再循环至所述提升管(32),所述再循环管线(39)配备有压缩机(40)和热交换器(41)。在热交换器(41)的下游,再循环管线(39)分开,并且气体混合物被分成三个分离的流:管线(42)将一部分循环气体输送到互连弯管(37)中,管线(43)将另一部分循环气体输送到提升管(32)的底部,以便在其中建立快速流化条件,和将另一部分循环气体输送通过输送管线(23),用于将在流化床反应器(1)中获得的聚乙烯颗粒转移到多区循环气相反应器(31)中。来自第一气相反应器的聚乙烯颗粒经由在位置(44)中的互连弯管(37)处进入多区循环气相反应器(31)。可以将补充单体、补充共聚单体和任选的惰性气体或工艺添加剂经由一条,两条或更多条管线(45)或(46)进料至多区循环反应器(31),管线(45)或(46)适当地位于气体循环管线(39)或下降管(33)的任何点。用于进料工艺添加剂例如抗静电剂的优选路线是进一步经由管线(47)进料添加剂。离开分离区(38)的气体混合物的一部分在通过压缩机(40)之后离开再循环管线(39),并通过管线(48)送到热交换器(49),在热交换器中冷却到单体和任选的惰性气体部分冷凝的温度。分离容器(50)放置在热交换器(49)的下游。该分离的气态混合物通过管线(51)再循环至再循环管线(39)并且该分离的液体借助于泵(53)通过管线(52)进料到该下降管(33)中。在多区循环反应器(31)中获得的聚烯烃颗粒从下降管(33)的底部经由排出管线(54)连续地排出。在本公开的方法中,排出的乙烯聚合物颗粒的脱气优选在第一步骤中以丙烷作为气体进行,以除去已经与作为粒间气体或作为溶解的烃的乙烯聚合物颗粒一起从聚合反应器排出的夹带的部分反应气体。这种用丙烷的第一脱气通常在第一脱气容器中进行。从聚合反应器排出的乙烯聚合物颗粒与伴随排出的反应气体的主要部分的分离可以在时间或空间方面与乙烯聚合物颗粒的第一脱气步骤一起或分开进行。这意味着,在优选的实施方案中,固体乙烯聚合物颗粒与大部分反应气体的分离在分离容器中进行,所述分离容器通常在聚合反应器中的压力和第一脱气容器中的压力之间的压力下操作,并且之后将聚烯烃颗粒转移至第一脱气容器以与丙烷流接触。在本发明的另一个优选实施方案中,乙烯聚合物颗粒直接排出到第一脱气容器中,在第一脱气容器中,乙烯聚合物颗粒同时与伴随排出的反应气体的主要部分分离并与丙烷流接触。在优选的实施方案中,将从第一脱气容器取出的丙烷流(其富含未反应的乙烯和共聚单体、低聚物和其它烃)输送至丙烷和单体后处理单元,在该单元中将气体混合物分离成可以容易地以后处理形式再循环至聚合过程的部分。当在将乙烯聚合物颗粒转移到第一脱气容器中之前在首先将乙烯聚合物颗粒与伴随排出的反应气体的主要部分分离的情况下进行乙烯聚合物颗粒的排出时,从分离容器中取出的气体流优选与从第一脱气容器中取出的丙烷流合并,并且将合并的流输送至丙烷和单体后处理单元。这种脱气和后处理方法例如公开于wo2006/082007a1、wo2014/090860a1或国际申请第pct/ep2018/071031号。丙烷和单体后处理单元可以被指定为产生再循环至聚合单元的至少一个液体流。在优选的实施方案中,丙烷和单体后处理单元通过后处理气体混合物产生一个或多个液体流和一个或多个气体流。再循环至聚合单元的一个或多个液体流可以在再循环至聚合单元之前蒸发。所述丙烷和单体后处理单元可以采用用于将丙烷与较高分子量或较低分子量组分分离的任何合适的方法。可以使用的分离技术的实例是通过蒸馏分离或通过冷凝分离。优选通过蒸馏分离。优选地,丙烷和单体后处理单元包含两个分离阶段,一个分离阶段主要用于将丙烷与较高分子量气体组分分离,并且一个分离阶段主要用于将丙烷与较低分子量气体组分分离。较高分子量气体组分的实例是较高分子量烷烃如丁烷、己烷或辛烷,或较高分子量烯烃如1-丁烯、1-己烯或1-辛烯。较低分子量气体组分的实例是乙烷、乙烯、氢或氮。气体流可以首先通过用于将丙烷与较高分子量气体组分分离的分离阶段,或者气体流可以首先通过用于将丙烷与较低分子量气体组分分离的分离阶段。优选地,气体流首先通过用于将丙烷与较高分子量气体组分分离的分离阶段。优选地,以溶解形式例如抗静电剂加入到聚合过程中的用于添加剂的溶剂为从丙烷和单体后处理单元接收的液体丙烷。虽然这样的丙烷和单体后处理单元被设计为回收气体混合物的组分并将这些组分再循环至气相聚合单元,但是仅可以再循环在聚合中使用的大部分反应气体;不能避免一些损失。这些损失量必须用新鲜进料代替。为了替代来自聚合单元的丙烷损失,将新鲜丙烷的进料流进料至气相聚合单元。作为所有技术上使用的进料流,用作聚合稀释剂的丙烷也可以含有杂质。未纯化的丙烷流通常含有许多杂质。取决于丙烷的来源,在纯化之前丙烷进料的质量可以在杂质的量和组成上变化。此外,质量也可以随时间变化;这可以例如通过丙烷源的变化或通过丙烷生产过程中的波动而发生。未纯化的丙烷的典型杂质是氢;氧;一氧化碳;二氧化碳;具有含氧官能团的烃,例如醇、二醇、酚、醚、羰基化合物(如酮、醛、羧酸、酯或脂肪酸);水;含硫化合物,例如二氧化硫和三氧化硫、硫化氢(h2s)、硫化羰(cos)或硫醇;氮基分子如氨、胺或亚硝酸盐;或胂;或其混合物。其它杂质为饱和烃,例如甲烷、乙烷或丁烷;烯烃,例如丙烯;炔,例如乙炔;或二烯如1,3-丁二烯或丙二烯。根据本公开的方法,用于替代来自聚合单元的丙烷损失的进料流是纯化的丙烷流,其中通过使烃流通过烃纯化单元进行纯化,所述烃纯化单元至少降低烃流中所含的丙烯、乙炔、一氧化碳、二氧化碳、氧气和水的浓度。该纯化的丙烷流包含至少99mol%的丙烷和不超过100ppm-mol的丙烯,优选0.01-75ppmmol的丙烯。在本公开的优选实施方案中,进料到气相聚合单元的纯化丙烷进料流包含不大于0.03ppm-mol一氧化碳,和优选不大于0.01ppm-mol一氧化碳,不大于0.4ppm-mol二氧化碳,和优选不大于0.2ppm-mol二氧化碳,不大于2.0ppm-mol氧气,和优选不大于1.0ppm-mol氧气,不大于3.0ppm-mol乙炔,和优选不大于1.0ppm-mol乙炔,和不大于2.0ppm-mol水,和优选不大于1.0ppm-mol水。通过使丙烷进料流通过烃纯化单元,不仅流中杂质的总量降低,而且还确保计量加入聚合的杂质的水平保持恒定。这提供了用于催化剂预活化的稳定条件和聚合反应器中的稳定条件,并且尤其避免了聚合反应器中有机金属化合物浓度的不受控变化,从而导致催化剂敏感性的不受控变化。在本公开的优选实施方案中,用于制备纯化的丙烷流的烃纯化单元之一是催化氢化单元。催化氢化是一种化学反应,其中不饱和化合物如丙烯与氢在氢化催化剂存在下反应生成饱和化合物如丙烷。所使用的催化剂优选为通常用于氢化的催化剂,例如基于铂、钯、铑或过渡金属(如钼、钨、铬或铁、钴、铜和镍)的催化剂,其可单独使用或以混合物使用,通常应用于载体如氧化铝、二氧化硅-氧化铝、活性炭或陶瓷。在优选的实施方案中,氢化催化剂是在氧化铝载体上的基于铂或钯的组合物,特别优选在氧化铝上的铂或钯。特别优选的催化剂是包含在氧化铝载体上的0.01-2wt%钯的组合物。为了在催化氢化单元中实现不饱和化合物的几乎完全的转化,例如丙烯到丙烷的转化,可能需要待氢化的流中的丙烯和其它不饱和组分的浓度低于阈值浓度。在本公开的优选实施方案中,已经通过催化氢化单元的氢化流的一部分因此再循环至催化氢化单元的上游位置并与待氢化流混合以稀释该流。通过调节包含丙烯的新鲜流和已经通过催化氢化单元的再循环流的比,可以调节进入催化氢化单元的流中不饱和组分的浓度。优选地,丙烷进料流的纯化通过随后通过各种纯化单元进行。纯化单元的数量和顺序可以变化。优选地,纯化单元之一是催化氢化单元。在顺序通过的纯化单元中待纯化的烃进料流优选以液体形式提供。在本公开的优选实施方案中,在将纯化流进料至气相聚合单元之前,通过随后使烃流穿过四个纯化单元来进行丙烷进料流的纯化。所述第一纯化单元优选为用于使所述烃流中的杂质与适于从烃流中除去cos、h2s和胂的cu基催化剂反应的单元。所述第二纯化单元优选为用于催化氢化来自所述第一纯化单元的流的单元。所述第三纯化单元优选为用于将丙烷与较高分子量或较低分子量组分分离的单元。所述第四纯化单元优选为干燥单元。第一纯化单元中使用的催化剂优选为包含cu和zn以及任选的助催化剂和载体的催化剂。处于其还原形式(即,铜至少部分地作为cu存在,呈金属形式)的该催化剂可以通过用氢,优选在氢气氛中,在80至180℃的温度和1至50巴的压力下处理一种催化剂来获得,该催化剂包含:25至50wt%,优选35至45wt%cuo;30至65wt%,优选35至45wt%zno;5至40wt%,优选20至30wt%al2o3、sio2、tio2、mgo、氧化铁或其混合物;以及0至5wt%,更优选0至1wt%的促进剂。合适的促进剂可以是钾、钠、锰、铬、钴、钨、钼、镍、铁、镁、钙及其混合物。还可以原位获得还原形式的催化剂,即通过将足够量的氢混合到待纯化的单体流中。所述第二纯化单元优选为用于催化氢化来自所述第一纯化单元的流的单元。所述第三纯化单元优选为用于从来自所述第二纯化单元的所述丙烷流分离较高分子量或较低分子量组分的分离单元,并且更优选为蒸馏单元。优选地,第三纯化单元包含两个分离阶段,一个分离阶段主要用于将丙烷与较高分子量气体组分分离,并且一个分离阶段主要用于将丙烷与较低分子量气体组分分离。较高分子量气体组分的实例是较高分子量烷烃如丁烷、己烷或辛烷。较低分子量气体组分的实例是乙烷、乙烯、氢或氮。丙烷流可以首先通过用于将丙烷与较高分子量气体组分分离的分离阶段,或者气体流可以首先通过用于将丙烷与较低分子量气体组分分离的分离阶段。优选地,气体流首先通过用于将丙烷与较低分子量气体组分分离的分离阶段。该第四净化单元优选是用于通过吸附在干燥剂上而去除水和剩余的极性杂质的干燥单元。这样的水还原催化剂优选选自分子筛。分子筛是合成制备的沸石,碱金属铝硅酸盐的结晶形式,并且具有高结构一致性。它们可以通过除去它们的水合水而被活化以获得吸附剂性能。所得材料是高度多孔的,对水、特定气体和液体具有强亲和力。在第四纯化单元中,优选水和剩余的极性杂质二者与分子筛反应,其中水和剩余的极性杂质被分子筛吸附。所述第四净化单元优选包含密闭容器,所述密闭容器由与所述第四净化单元产物流的温度和压力一致的材料构成,并且布置为容纳所述水还原催化剂并分布所述第四净化单元产物流的流量,以实现与所述水还原催化剂的良好接触。当料流前进通过容器时,丙烷料流在水浓度和剩余极性杂质浓度方面变得贫乏。在本公开的优选实施方案中,在将纯化流进料至气相聚合单元之前,通过随后使烃流穿过四个纯化单元的不同组合来进行丙烷进料流的纯化。所述第一纯化单元优选为用于通过还原的cu基催化剂从烃流中除去氧气和一氧化碳的单元。所述第二纯化单元优选为干燥单元。所述第三纯化单元优选为用于通过cu基催化剂从来自所述第二纯化单元的流中除去cos、h2s和胂的单元。所述第四纯化单元优选为用于催化氢化来自所述第三纯化单元的流的单元。在本公开的优选实施方案中,不仅使进料至气相聚合单元的丙烷进料流通过烃纯化单元,而且使作为共聚单体进料至至少一个聚合反应器的乙烯和c4-c12-1-烯烃首先通过烃纯化单元,所述烃纯化单元至少降低一氧化碳、二氧化碳、氧气、乙炔和烯烃中所含的水的浓度(在进料至聚合单元之前)。图2示意性地示出了用于纯化丙烷进料流的烃纯化单元和用于回收从聚合反应器排出的反应气体的组分的丙烷和单体后处理单元的设置,所述丙烷进料流被进料到气相聚合单元以替代来自聚合单元的丙烷损失。经由管线(101)将包含丙烷和杂质的液体流提供至第一丙烷纯化容器(102),其包含包含cu、zn的催化剂和用于从丙烷料流除去含硫杂质的载体材料。将所获得的流经由管线(103)转移至包含催化氢化催化剂的第二丙烷纯化容器(104),所述催化氢化催化剂用于将不饱和化合物例如丙烯氢化成饱和化合物例如丙烷。氢化所需的氢气经由管线(105)加入。经氢化的丙烷流经由管线(106)从第二丙烷纯化容器(104)的底部取出并通过泵(107)转移至第一分离柱(108)。为了能够保持第二丙烷纯化容器(104)内的温度,进入第二丙烷纯化容器(104)的流中的丙烯和其它不饱和组分的浓度可以通过将经由管线(109)从第二丙烷纯化容器(104)取出的部分氢化丙烷流再循环并将该再循环部分与来自第一丙烷纯化容器(102)的丙烷流合并来降低。在第一分离塔(108)中,较低分子量组分与进入塔(108)的丙烷流分离并且经由管线(110)从塔(108)的顶部取出。该气体经由管线(110),其包含已经通过第二丙烷纯化容器(104)的未反应的氢气,可以经由管线(111)再循环至第二丙烷纯化容器(104)或者可以经由管线(112)作为废气被吹扫。从较低分子量气体组分中脱除的丙烷流通过管线(113)转移到第二分离塔(114)。在第二分离塔(114),较高分子量组分从进入塔(114)的丙烷流中分离并经由管线(115)从塔(114)的底部取出。经由管线(115)取出的包含较高分子量气体组分的该液体可以在蒸发之后作为废气进行吹扫。脱除较高分子量组分的丙烷流通过热交换器(116)用于液化,并经由管线(117)转移到包含用于除去水和剩余极性杂质的干燥剂的第三丙烷纯化容器(118)的底部。将所述经纯化的丙烷流从所述第三丙烷纯化容器(118)的顶部取出并经由管线(119)转移至丙烷储槽(120)。为了从自聚合反应器或聚合反应器的组合排出的反应气体和/或从来自第一脱气容器的气体混合物中回收丙烷、乙烯和共聚单体,图2显示了包含两个丙烷蒸馏塔(131)和(132)的丙烷和单体后处理单元。将从聚合反应器排出的气体和来自第一脱气容器的气体的组合流经由管线(133)引入第一丙烷蒸馏塔(131)中,其中较高分子量组分与进入塔(131)的丙烷流分离。包含用于聚合的共聚单体的较高分子量组分经由管线(134)以液体形式从第一丙烷蒸馏塔(131)的底部取出,并且可以通过泵(135)泵送回聚合单元。从较高分子量组分中脱除的气体流经管线(136)从第一丙烷蒸馏塔(131)的顶部取出并转移到第二丙烷蒸馏塔(132)中。经由管线(137)从第二丙烷蒸馏塔(132)的顶部取出引入第二丙烷蒸馏塔(132)的气体的较低分子量组分,其包括乙烯,并且可以将其再循环至聚合过程或可以作为废气进行吹扫。从较低分子量组分和较高分子量组分中脱除的回收的丙烷经由管线(138)以液体形式从第二丙烷蒸馏塔(132)中取出。经由管线(138)从第二丙烷蒸馏塔(132)取出的丙烷可以通过泵(139)以液体形式经由管线(140)或在热交换器(141)中蒸发之后经由管线(142)容易地转移回聚合过程。收集在储槽(120)中的纯化的新鲜丙烷可以经由管线(121)直接转移到聚合过程,例如转移到气相聚合单元的专用位置,或者纯化的新鲜丙烷可以通过经由管线(122)转移到第二丙烷蒸馏塔(132)而与在丙烷和单体后处理单元中获得的回收的丙烷组合。在本公开的优选实施方案中,用作预活化聚合催化剂的液体稀释剂的丙烷取自纯化的丙烷进料流。可以将全部纯化的丙烷进料流进料到预活化容器中,以代替从聚合单元中损失的丙烷。优选地,将纯化的丙烷进料流的一部分作为用于预活化聚合催化剂的液体稀释剂转移至预活化容器,并且将纯化的丙烷进料流的剩余部分在一个或多个不同位置引入气相聚合单元。在优选的实施方案中,将剩余的纯化的丙烷进料流转移至丙烷和单体后处理单元以引入气相聚合单元。在本公开的优选实施方案中,进料至气相聚合单元的丙烷进料流的纯化直接发生在将丙烷进料至气相聚合单元之前。在这样的实施方案中,烃纯化单元安装在与气相聚合单元相同的位置。这种设置允许购买未纯化的丙烷或未充分纯化的丙烷,并且因为气相聚合单元和烃纯化单元在这种情况下通常由相同的操作者运行,所以将丙烷纯化的完全控制给予气相聚合单元的操作者。因此,这样的实施方案可以经济地进行而无需大量的物流努力。在本公开的另一个优选实施方案中,丙烷的纯化和乙烯聚合或共聚被局部及时地分离。在这样的设置中,可商购的高纯度丙烷,其包含至少99mol%的丙烷和不超过100ppm-mol的丙烯,并且其已经通过烃纯化单元,所述烃纯化单元至少降低通过烃纯化单元的烃流中的丙烯、乙炔、一氧化碳、二氧化碳、氧气和水的浓度,供应至气相聚合单元的位置。这样的设置节省了用于气相聚合单元的操作者的烃纯化单元的构造,然而,对于在比中试装置大的聚合单元中的聚合,使用高纯度丙烷的供应需要来自物流点的大量努力并且不利地影响聚合工艺的经济性。在本公开的进一步优选的实施方案中,用于制备纯化的丙烷流的烃流为包含至少99mol%丙烯的纯化的丙烯流。在该实施方案中,丙烯的纯化和氢化在分开的阶段中发生。如果乙烯聚合物的制备发生在装备有丙烯纯化单元的丙烯聚合单元附近,则这样的实施方案可以具有经济意义。用于两个聚合单元的一个纯化单元或纯化单元的一个组合的这种组合使用可以允许实现丙烯纯化的规模经济,而用于制备乙烯聚合物的气相聚合单元中包括的催化氢化单元可以根据用于替代聚合过程中的丙烷损失的所需纯化的丙烷流的量来设计。实施例熔体流动速率mfr21.6根据dineniso1133-1:2012-03在190℃的温度和21.6kg的负荷下测定。熔体流动速率mfr5根据dineniso1133-1:2012-03在190℃的温度和5kg的负荷下测定。熔体流动速率mfr2.16根据dineniso1133-1:2012-03在190℃的温度和2.16kg的负荷下测定。流动速率比frr是mfr21.6/mfr5的比。根据dineniso1183-1:2004,方法a(浸没),用2mm厚的压塑板测定密度。用限定的热历史制备压塑板:在180℃,20mpa下压制8分钟,随后在沸水中结晶30分钟。在高压毛细管流变仪(rheograph25,werkstoff-gmbh,buchen,germany)中,在1440s-1的剪切速率下,在具有锥形入口(角度=20°,d=2mm,l=2mm,总长度=30mm)的30/2/2/20圆形穿孔模具中,在190℃的温度下,使用距离模具出口78mm放置的激光二极管测量溶胀比。在活塞到达离模具入口96mm的位置时,在离模具出口150mm的距离处切割该挤出物(通过来自的自动切割装置)。溶胀比(sr)[%]定义为差值(dmax-dd)×100除以dd,其中dmax是链的最大直径,dd是模具的直径;sr=(dmax-dd)100%/dd。根据astmd624898,使用来自bruker的ft-ir光谱仪tensor27,通过ir确定共聚单体含量,所述ft-ir光谱仪tensor27用化学计量模型校准,所述化学计量模型用于分别确定pe中用于作为共聚单体的1-丁烯或1-己烯的乙基侧链或丁基侧链。将结果与由聚合方法的质量平衡得到的估计的共聚单体含量进行比较并且发现是一致的。通过全缺口蠕变试验(fnct)根据国际标准iso16770:2004在表面活性剂水溶液中测定耐环境应力开裂性。由该聚合物样品制备压塑的10mm厚的片材。使用剃须刀在垂直于应力方向的四个侧面上刻出横截面为正方形(10x10x100mm)的棒。在m.fleissner在kunststoffe77(1987),第45页中描述的缺口装置用于深度为1.6mm的尖锐缺口。所施加的负荷由拉力除以初始韧带面积来计算。韧带面积是剩余面积=试样的总横截面面积减去缺口面积。对于fnct试样:10x10mm2-4倍梯形缺口面积=46.24mm2(失效过程/裂纹扩展的剩余横截面)。使用iso16770建议的标准条件,在50℃下以6mpa的恒定负荷在2wt%arkopaln100的水溶液中加载测试试样。直到检测到测试试样破裂所经过的时间。凝胶计数是通过制备流延膜,通过光学扫描装置分析膜缺陷并根据膜缺陷尺寸(圆直径)分类和计数膜缺陷来测定的。通过具有20mm螺杆直径和25d螺杆长度以及150mm缝模宽度的me202008-v3型ocs挤出机制备膜。该铸造线配备有冷却辊和卷绕器(型号ocscr-9)。该光学设备由具有26μmx26μm分辨率的型号为fta-100(闪光灯相机系统)的osc膜表面分析仪相机组成。在首先吹扫树脂1小时以稳定挤出条件之后,之后进行30分钟的检查和记录价值。在220℃下以约ca.2.7m/min的引出速度挤出树脂,以产生厚度为50μm的膜。冷却辊温度为70℃。用表面分析仪相机检查所制备的膜提供了凝胶的总含量和直径大于700μm的凝胶的含量。实施例1所述聚合方法在连续条件下在聚合单元中进行,所述聚合单元包含两个串联连接的气相反应器,作为反应器级联的第一反应器的流化床反应器和作为后续聚合反应器的包含提升管和下降管的多区循环反应器,如图1中所示。丙烷纯化用于替代聚合过程中的丙烷损失的丙烷进料流是通过使包含如表1中所示的丙烷和杂质的液体丙烷流通过安装在气相聚合单元附近的四个顺序布置的纯化单元而获得的纯化丙烷流。第一单元含有用于除去cos、h2s、氧气、一氧化碳和二氧化碳的cuo/zno催化剂床(r3-12t5x3,获自basfse,ludwigshafen,germany)。第二单元是含有用于将丙烯氢化成丙烷的钯基催化剂(puristarr0-20k2-4,获自basfse,ludwigshafen,germany)的催化氢化单元。第三单元是用于从丙烷中分离较高分子量或较低分子量组分的两级蒸馏单元,并且第四单元含有用于除去水的0.3nm分子筛。直接转移到气相聚合单元的所获得的纯化的液体丙烷具有表1中所示的组成。催化剂制备为了制备固体催化剂组分,按照us4,399,054的实施例2中描述的方法制备含约3mol醇的氯化镁和醇加合物,但是在2000rpm而不是10000rpm下工作。在氮气流下,在50至150℃的温度范围内对所述加合物进行热处理,直到达到25wt%的醇含量。在氮气吹扫的2l四颈圆底烧瓶中,在0℃下引入1lticl4。然后,在相同温度下,在搅拌下添加70g的含有25wt%的乙醇并如上所述制备的球形mgcl2/etoh加合物。在2小时内将温度升高至140℃并保持120分钟。然后,停止搅拌,使固体产物沉降并虹吸出上层清液。然后将固体残余物在80℃用庚烷洗涤一次并在25℃用己烷洗涤五次并在30℃真空干燥。将在20℃下的351.5cm3己烷和在搅拌下7g如上所述制备的催化剂组分在20℃下引入到配有搅拌器的260cm3玻璃反应器中。保持内部温度恒定,将在己烷(约370g/l)中的5.6cm3三正辛基铝(tnoa)和一定量的环己基甲基-二甲氧基硅烷(cmms)缓慢引入反应器中,使得tnoa/cmms的摩尔比为50,并且使温度达到10℃。在搅拌10分钟之后,在4小时的时间内在相同温度下小心地将10g丙烯引入反应器中。监测反应器中丙烯的消耗,并且当认为达到1g聚合物/g催化剂的理论转化率时停止聚合。然后,将整个内容物过滤并用己烷在30℃(50g/l)的温度下洗涤三次。干燥后,分析得到的预聚合催化剂(a),发现每克初始催化剂含有1.05g聚丙烯,2.7%ti,8.94%mg和0.1%al。为了将内电子给体负载在预聚合的催化剂上,将约42g如上所述制备的固体预聚合的催化剂组分装入用氮气吹扫的玻璃反应器中并在50℃下悬浮在0.8l己烷中。然后,小心地滴加(在10分钟内)乙酸乙酯,其量使得预聚合催化剂的mg与有机路易斯碱之间的摩尔比为1.7。将悬浮液在搅拌下保持2小时,仍然具有50℃作为内部温度。此后,停止搅拌并使固体沉降。在回收和干燥最终催化剂之前,在室温下进行一次己烷洗涤。聚合将13.8g/h的如上所述制备的固体催化剂组分(电子给体/ti摩尔进料比为8)加入到第一搅拌预活化容器中,其使用1kg/h的来自如上所述四个顺序布置的纯化单元的纯化的液体丙烷。还将三异丁基铝(tiba)、氯化二乙基铝(deac)和电子给体四氢呋喃(thf)计量加入第一搅拌预活化容器中。三异丁基铝与氯化二乙基铝的重量比为7∶1。烷基铝(tiba+deac)与固体催化剂组分的比为5∶1。烷基与thf的重量比为70。第一预活化容器保持在50℃,停留时间为30分钟。将第一预活化容器的催化剂悬浮液连续转移至第二搅拌预活化容器,其以30分钟的停留时间操作并且也保持在50℃。然后将催化剂悬浮液经由管线(10)连续转移到流化床反应器(fbr)(1)中。在第一反应器中,使用h2作为分子量调节剂并在作为惰性稀释剂的丙烷存在下聚合乙烯。通过管线9将50kg/h乙烯和200g/h氢气加入第一反应器中。没有共聚单体进料至第一反应器。聚合在80℃的温度和2.9mpa的压力下进行。将在第一反应器中获得的聚合物经由管线(11)间断地排出,与气体分离进入气/固分离器(12),并且经由管线(14)再引入到第二气相反应器中。在第一反应器中生产的聚合物具有81g/10min的熔体流动速率mfr2.16和0.969kg/dm3的密度。第二聚合反应器在约80℃的聚合条件和2.5mpa的压力下操作。该提升管具有200mm的内径和19m的长度。所述下降管的总长度为18m,上部为5m,内径为300mm,下部为13m,内径为150mm。通过在提升管(32)和下降管(33)内建立不同的单体和氢气浓度条件来操作第二反应器。这通过经由管线(52)将330kg/h的液流(液体屏障)进料到下降管(33)的上部中来实现。所述液体流的组成不同于存在于提升管中的气体混合物的组成。管线(52)的液体流来自冷凝器(49)中的冷凝步骤,在47℃和2.5mpa的工作条件下,其中一部分再循环流被冷却并部分冷凝。通过管线(45)和(46)将5kg/h的丙烷、50.8kg/h的乙烯和28kg/h的氢气进料至第二反应器。此外,将0.20kg/h的1-己烯在刚好位于所述屏障下方的位置处引入到所述下降管(33)中。最终的乙烯聚合物经由管线(54)不连续地排出。在第一反应器中制备约49wt%的从第二反应器排出的最终乙烯聚合物(分开49∶51)。聚合反应器中的一些其它聚合条件和最终乙烯聚合物的性质示于表2中。实施例2然而,使用由丙烷生产者纯化的纯化的丙烷重复实施例1的聚合,所述纯化的丙烷具有至少99.95vol.%的丙烷含量。丙烷购自德国汉堡ghcgerling,holz&co.handelsgmbh,并具有表1中所示的组成。丙烷以0.85mpa(abs)的压力在圆筒中供应并通过隔膜泵进料至第一预活化容器。可以在与实施例1相同的反应器条件下进行聚合。聚合反应器中的一些其它聚合条件和最终乙烯聚合物的性质示于表2中。对比例a重复实施例2的聚合,然而使用仅具有至少99.5vol.%的丙烷含量的丙烷。丙烷购自德国汉堡ghcgerling,holz&co.handelsgmbh,并具有表1中所示的组成。丙烷以0.85mpa(abs)的压力在圆筒中供应并通过隔膜泵进料至第一预活化容器。为了保持反应器级联的恒定生产能力,需要将催化剂进料增加至17.3g/h固体催化剂组分。保持电子给体/ti的摩尔进料比为8,同时保持液体丙烷至第一搅拌预活化容器的进料为1kg/h。为了实现最终乙烯聚合物的设计密度,在刚好位于屏障下方的位置处进料到下降管(33)的1-己烯的量必须降低至0.15kg/h。聚合反应器中的进一步聚合条件和最终乙烯聚合物的性质示于表2中。表1表2实施例1实施例2对比例a第一反应器h2/c2h4摩尔比2.62.62.5c2h4[vol.%]12.312.312.3密度[g/cm3]0.9690.9690.965mfr2.16[g/10min]817984第二反应器提升管中h2/c2h4摩尔比0.280.270.30提升管中c2h4[vol.%]12.612.512.3最终聚合物性能mfr21.6[g/10min]23.723.424frr19.819.720.9密度[g/cm3]0.95790.95800.9575溶胀比[%]1731751721-己烯含量[wt%]0.180.180.13fnct[h]18.118.312.2凝胶计数>700μm[1/m2]0.30.31.1凝胶计数总数[1/m2]5014801078催化剂生产率[g/g]733773455780实施例1和2的对比证明,在直接进料到气相聚合单元之前纯化含有杂质的丙烷流,因为购买了高纯度丙烷,使得可以生产具有良好性能组合和高催化剂生产率的乙烯聚合物。实施例2和对比例a的对比显示,通过使用具有较高含量的丙烯和极性杂质的丙烷,耐环境应力开裂性降低,凝胶数增加并且催化剂生产率降低。当前第1页12