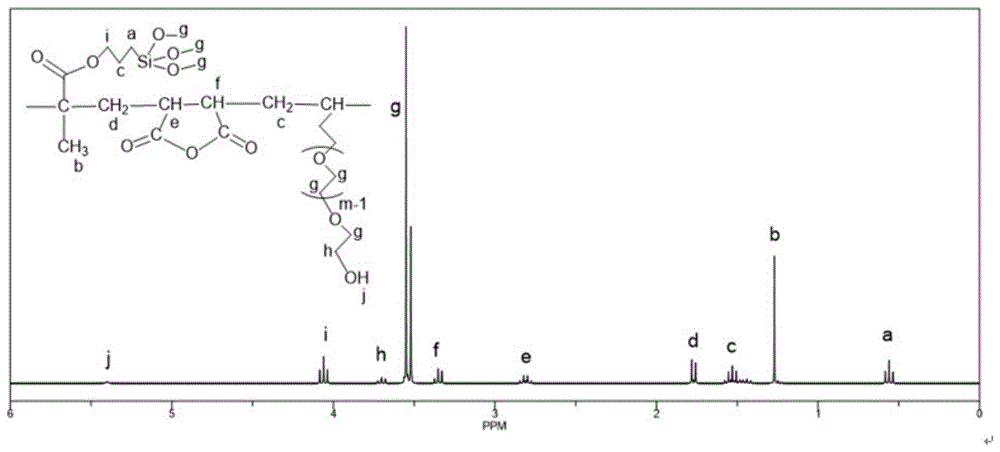
本发明属于油田开发的
技术领域:
,具体的涉及一种基于高温激发的岩石表面强亲水润湿剂及其制备方法。
背景技术:
:油田开发当中,油藏的界面包括驱替液-原油、驱替液-岩石和原油-岩石三种界面,而油藏界面的性质对油藏的采收率影响很大。目前人们普遍认为改变油藏的润湿性也能显著地提高油藏的采收率。润湿性是油藏物性的一个基本参数,对原油采收率有着很大的影响,因此如何有效地改变油藏的润湿性,从而提高采收率变得至关重要。水湿性储层具有最高的水驱采收率,所以获得最大水驱采收率的关键技术就是将储层岩石表面的润湿性改为水湿。常规的润湿性改进方法是使用表面活性剂,利用表面活性剂的亲油端吸附在疏水表面,亲水端向外整齐排列,用整齐排列的亲水端覆盖疏水表面,从而达到润湿翻转的目的,使岩石表面具有水润湿性。然而油气井底温度较高,且含有原油,导致大量表面活性剂聚集在油水界面,在岩石表面覆盖效率低,即便是有一部分在岩石表面吸附,也因为较高温度环境和溶解平衡的原因,逐渐转移到液相中,使岩石表面的水润湿性逐渐消失。技术实现要素:本发明的目的在于针对高温条件下,如何有效改变储层岩石润湿性的问题而提供一种基于高温激发的岩石表面强亲水润湿剂及其制备方法,所述岩石表面强亲水润湿剂针对的是高温油气井,该润湿剂可以改变其井内岩石的润湿性,降低岩石的表面能,降低岩石对聚合物的吸附;而且还可以使原油在通路中不吸附于岩石上,对保持油田的增产具有重要意义。本发明的技术方案为:一种基于高温激发的岩石表面强亲水润湿剂,其结构式为其中,a为b的20~100倍,m=5~100,n=200~300。所述润湿剂通过马来酸酐、γ-甲基丙烯酰氧基丙基三甲氧基硅烷和低分子量烯丙基聚醚在二甲基甲酰胺体系中进行加成聚合反应制得。其合成机理如下:所述基于高温激发的岩石表面强亲水润湿剂的制备方法,包括以下步骤:(1)首先将马来酸酐、引发剂和二甲基甲酰胺混合,搅拌加热至70~80℃,再加入低分子量烯丙基聚醚;(2)然后滴加由γ-甲基丙烯酰氧基丙基三甲氧基硅烷与二甲基甲酰胺组成的混合溶液,在70~80℃下保温反应3~5h;反应完全后减压蒸馏除去溶剂二甲基甲酰胺,得到黄色固体后粉碎,即为基于高温激发的岩石表面强亲水润湿剂。所述低分子量烯丙基聚醚的分子量为300。加入分子量为300的低分子量烯丙基聚醚,其目的是增加产物溶解性,利于后续强亲水润湿剂在高温水系里的进一步水解。按摩尔比所述马来酸酐:γ-甲基丙烯酰氧基丙基三甲氧基硅烷:低分子量烯丙基聚醚为1:1:(0.01~0.05)。其中马来酸酐不能自聚,在γ-甲基丙烯酰氧基丙基三甲氧基硅烷与马来酸酐摩尔比为1:1时,生成交替共聚物,再与少量的低分子量烯丙基聚醚进行聚合。所述步骤(1)中引发剂为偶氮二异丁腈;引发剂的用量为马来酸酐与γ-甲基丙烯酰氧基丙基三甲氧基硅烷质量总和的3%。所述步骤(1)中按质量比二甲基甲酰胺:马来酸酐为(1~3):1。所述步骤(2)中按质量比二甲基甲酰胺:γ-甲基丙烯酰氧基丙基三甲氧基硅烷为(1~3):1。所述岩石表面强亲水润湿剂在高温油气井的应用。应用的相应作业井温度为70~90℃。本发明的有益效果为:本发明所述岩石表面强亲水润湿剂进入高温油气井后,其应用原理通过以下反应实现:第一步:进入高温油气井后,润湿剂中硅原子连接的甲氧基会水解成羟基并与岩石壁面反应,形成牢固的化学键,从而将该强亲水润湿剂接枝到岩石表面,即可调控岩石表面的润湿性。由于是共价键连接,润湿剂分子不易从岩石表面剥离,能更长时间发挥润湿剂作用。第二步:在一定时间内,一定井温下,润湿剂中的马来酸酐水解成顺丁烯二酸,使得油气井内的岩石壁面改性为强亲水壁面。该强亲水润湿剂在应用时,随着井内温度升高,其亲水性增强,更有效地降低岩石表面能,减少降低聚合物吸附,使原油在通路中不吸附于岩石上。从而提高最终采收率打下基础。所述润湿剂通过马来酸酐、γ-甲基丙烯酰氧基丙基三甲氧基硅烷和低分子量烯丙基聚醚在二甲基甲酰胺体系中进行加成聚合反应制备所得。整个反应的条件温和,反应控制简单。整个方法通过逐步加入反应物进行反应,原料廉价易得,工艺简单,适合工业化生产。综上所述,从功能的发挥上,普通的表面活性剂依靠疏水基团的缔合作用产生有序排列,而本发明所述的润湿剂在工作过程中依靠共价键结合在岩石表面,可增加润湿剂有效工作时间;同时所述润湿剂在进入井下后会有部分基团发生从疏水转变为亲水的反应,有利于润湿剂分子早期在岩石表面的定位,后期亲水基团的增多,则有利于强化分子周围的亲水环境。附图说明图1为实施例5所得强亲水润湿剂的核磁氢谱。图2为亲油岩芯与水的接触角图片。图3为采用实施例5润湿剂处理后岩芯与水的接触角图片。具体实施方式下面通过实施例对本发明进行详细说明。实施例1所述基于高温激发的岩石表面强亲水润湿剂,其结构式为其中,a为b的20~100倍,m=5~100,n=200~300。所述基于高温激发的岩石表面强亲水润湿剂的制备方法,具体如下:首先将98g(1mol)马来酸酐,10.47g引发剂偶氮二异丁腈(aibn)和98g二甲基甲酰胺(dmf)加入至烧瓶中,不断搅拌加热至70℃,再加入3g(0.01mol)分子量为300的低分子量烯丙基聚醚;然后开始缓慢滴加由248g(1mol)γ-甲基丙烯酰氧基丙基三甲氧基硅烷与248gdmf组成的混合溶液,在75℃下保温反应5h,减压蒸馏除去溶剂dmf,得到黄色固体,将其粉碎,即得到基于高温激发的岩石表面强亲水润湿剂。实施例2所述基于高温激发的岩石表面强亲水润湿剂的制备方法,具体如下:首先将98g(1mol)马来酸酐,10.65g引发剂偶氮二异丁腈(aibn)和98g二甲基甲酰胺(dmf)加入至烧瓶中,不断搅拌加热至70℃,再加入6g(0.02mol)分子量为300的低分子量烯丙基聚醚;然后开始缓慢滴加由248g(1mol)γ-甲基丙烯酰氧基丙基三甲氧基硅烷与248gdmf组成的混合溶液,在75℃下保温反应5h,减压蒸馏除去溶剂dmf,得到黄色固体,将其粉碎,即得到基于高温激发的岩石表面强亲水润湿剂。实施例3所述基于高温激发的岩石表面强亲水润湿剂的制备方法,具体如下:首先将98g(1mol)马来酸酐,10.65g引发剂偶氮二异丁腈(aibn)和98g二甲基甲酰胺(dmf)加入至烧瓶中,不断搅拌加热至70℃,再加入9g(0.03mol)分子量为300的低分子量烯丙基聚醚;然后开始缓慢滴加由248g(1mol)γ-甲基丙烯酰氧基丙基三甲氧基硅烷与248gdmf组成的混合溶液,在75℃下保温反应5h,减压蒸馏除去溶剂dmf,得到黄色固体,将其粉碎,即得到基于高温激发的岩石表面强亲水润湿剂。实施例4所述基于高温激发的岩石表面强亲水润湿剂的制备方法,具体如下:首先将98g(1mol)马来酸酐,10.74g引发剂偶氮二异丁腈(aibn)和98g二甲基甲酰胺(dmf)加入至烧瓶中,不断搅拌加热至70℃,再加入12g(0.04mol)分子量为300的低分子量烯丙基聚醚;然后开始缓慢滴加由248g(1mol)γ-甲基丙烯酰氧基丙基三甲氧基硅烷与248gdmf组成的混合溶液,在75℃下保温反应5h,减压蒸馏除去溶剂dmf,得到黄色固体,将其粉碎,即得到基于高温激发的岩石表面强亲水润湿剂。实施例5所述基于高温激发的岩石表面强亲水润湿剂的制备方法,具体如下:首先将98g(1mol)马来酸酐,10.83g引发剂偶氮二异丁腈(aibn)和98g二甲基甲酰胺(dmf)加入至烧瓶中,不断搅拌加热至70℃,再加入15g(0.05mol)分子量为300的低分子量烯丙基聚醚;然后开始缓慢滴加由248g(1mol)γ-甲基丙烯酰氧基丙基三甲氧基硅烷与248gdmf组成的混合溶液,在75℃下保温反应5h,减压蒸馏除去溶剂dmf,得到黄色固体,将其粉碎,即得到基于高温激发的岩石表面强亲水润湿剂。为了表征该基于高温激发的岩石表面强亲水润湿剂的结构特征,对实施例5所得润湿剂样品进行了核磁氢谱测试,结果如图1所示。由图1结果表明,按照理论准确合成了基于高温激发的岩石表面强亲水润湿剂。用实施例5中的基于高温激发的岩石表面强亲水润湿剂通过喷涂方法对岩芯样本进行修饰(90℃),岩芯由原来的亲水转变为强亲水润湿状态。通过图2可知,未经实施例5润湿剂处理的岩芯呈明显的疏水特征,接触角分布在95~105°之间,在这种情况下,原油极易吸附在岩石表面。通过图3可知,经过实施例5润湿剂处理,岩石表面呈现明显的水润湿性,接触角分布在15~20°之间,水更容易吸附在岩石表面产生隔离层,可阻止原油在岩石表面的吸附。实施例6所述基于高温激发的岩石表面强亲水润湿剂的制备方法,具体如下:首先将98g(1mol)马来酸酐,10.83g引发剂偶氮二异丁腈(aibn)和196g二甲基甲酰胺(dmf)加入至烧瓶中,不断搅拌加热至70℃,再加入15g(0.05mol)分子量为300的低分子量烯丙基聚醚;然后开始缓慢滴加由248g(1mol)γ-甲基丙烯酰氧基丙基三甲氧基硅烷与248gdmf组成的混合溶液,在75℃下保温反应5h,减压蒸馏除去溶剂dmf,得到黄色固体,将其粉碎,即得到基于高温激发的岩石表面强亲水润湿剂。实施例7所述基于高温激发的岩石表面强亲水润湿剂的制备方法,具体如下:首先将98g(1mol)马来酸酐,10.83g引发剂偶氮二异丁腈(aibn)和196g二甲基甲酰胺(dmf)加入至烧瓶中,不断搅拌加热至70℃,再加入15g(0.05mol)分子量为300的低分子量烯丙基聚醚;然后开始缓慢滴加由248g(1mol)γ-甲基丙烯酰氧基丙基三甲氧基硅烷与496gdmf组成的混合溶液,在75℃下保温反应5h,减压蒸馏除去溶剂dmf,得到黄色固体,将其粉碎,即得到基于高温激发的岩石表面强亲水润湿剂。实施例8所述基于高温激发的岩石表面强亲水润湿剂的制备方法,具体如下:首先将98g(1mol)马来酸酐,10.83g引发剂偶氮二异丁腈(aibn)和196g二甲基甲酰胺(dmf)加入至烧瓶中,不断搅拌加热至80℃,加入15g(0.05mol)分子量为300的低分子量烯丙基聚醚;然后开始缓慢滴加由248g(1mol)γ-甲基丙烯酰氧基丙基三甲氧基硅烷与496gdmf组成的混合溶液,在80℃下保温反应5h,减压蒸馏除去溶剂dmf,得到黄色固体,将其粉碎,即得到基于高温激发的岩石表面强亲水润湿剂。下面对实施例1-8所得润湿剂进行性能测试:1、实验步骤:首先将实施例1-8所得基于高温激发的岩石表面强亲水润湿剂分别溶解在水中配置成1%的分散液,然后将石英砂砂体放置在分散液中,在90℃下反应48小时,取出石英砂晾干;清洗样品,烘箱中烘干,通过测定石英砂吸附前后溶液中聚丙烯酰胺的浓度,计算石英砂对聚丙烯酰胺的吸附量,通过空白石英砂与所得润湿剂涂敷修饰后石英砂之间的对比,得到降吸附能力的评价,详细见表1。2、结果与分析:表1:不同实施例中的基于高温激发的岩石表面强亲水润湿剂浸涂沙子后对聚丙烯酰胺的静态吸附量以及降低聚合物吸附程度。样品静态吸附量降低聚合物吸附程度未处理石英砂2258μg/g—实施例1涂敷石英砂546.6μg/g75.8%实施例2涂敷石英砂416.1μg/g81.6%实施例3涂敷石英砂286.1μg/g92%实施例4涂敷石英砂120.3μg/g94.7%实施例5涂敷石英砂46.8μg/g97.9%实施例6涂敷石英砂45.3μg/g98.0%实施例7涂敷石英砂45.6μg/g98.0%实施例8涂敷石英砂45.4μg/g98.0%通过表1可知,本发明所述基于高温激发的岩石表面强亲水润湿剂在低分子量烯丙基聚醚含量上升的时候,降低聚合物吸附程度明显增加,亲水程度增加,有效降低聚合物吸附。以上内容是对本发明所作的进一步详细说明,不能认定本发明的具体实施方式仅限于此,对于本发明所属
技术领域:
的普通技术人员来说,在不脱离本发明构思的前提下,还可以做出若干简单的推演或替换,都应当视为属于本发明由所提交的权利要求书确定保护范围。当前第1页12