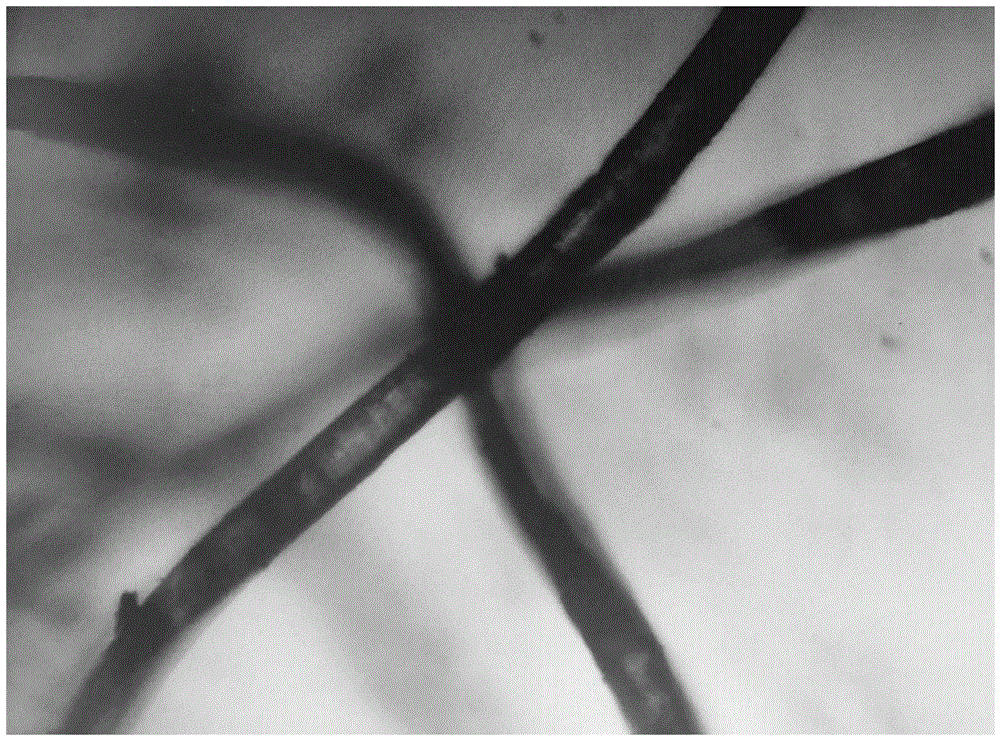
本发明涉及高导热复合材料
技术领域:
,具体为一种高导热复合材料的制备方法。
背景技术:
:塑料具有质轻,化学性稳定,耐腐蚀,易于加工等优点,在电子电器、包装行业、汽车工业、机械制作及航天航空等方面具有广泛的应用。然而塑料的热导率低,限制了其应用。为了获得高导热的塑料,通常的手法为添加导热填料,如:汪文等采用石墨烯为导热填料,添加到聚丙烯材料中,当石墨烯含量为60%时,导热系数提高到1.32w/(m·k),比纯聚丙烯提高了14倍,但热稳定性随之降低。专利zl200510101700.0公开了一种注塑成型的绝缘导热塑料,以金属氧化物、碳化硅为导热填料,当氧化铝、氧化镁填料与聚苯硫醚基体比例为7:1时,导热系数在1.967w/(m·k),拉伸强度为41.4mpa,比纯的聚苯硫醚(63mpa)降低34%。填料的添加量成为导热的决定因素,而大量填料必然导致聚合物机械性能、加工性能的降低,限制其应用。专利cn108017820a披露了一种纤维增强高密度聚乙烯/石墨烯复合材料及其制备方法,以植物纤维和石墨烯为添加剂进行混杂填充,这种方式虽能在一定程度上改善复合材料的力学性能,但对导热性能的影响有限。在当前的研究中,填料与聚合物基体的亲和性差且分散不匀,热导率提高的同时力学性能下降,这都限制了导热复合材料的应用。技术实现要素:针对上述存在的技术不足,本发明的目的是提供一种高导热复合材料的制备方法,以解决
背景技术:
中提出的问题。为解决上述技术问题,本发明采用如下技术方案:本发明提供一种高导热复合材料的制备方法,包括以下步骤:1)按以下组分及重量份配比配料:导热材料0.1-10份、分散剂0.5-2份、天然有机高分子材料1-5份、聚合物粉末100份;2)将导热材料、分散剂、天然有机高分子材料、聚合物粉末按照步骤1)的配比加入到水溶液中进行预分散处理,预分散处理后转移到蒸压反应釜中进行热处理;3)将步骤2)所得溶液进行干燥处理,经干燥后加入有机溶剂中,研磨,通过静电纺丝技术,得到微米级混合的导热聚合物纤维丝;4)将步骤3)所得导热聚合物纤维丝利用双螺杆挤出机熔融挤出、造粒,制得高导热聚合物母粒。优选地,所述的导热材料为新型碳材料、高导热无机非金属材料、金属或金属氧化物材料中的一种或几种;所述的天然有机高分子材料为淀粉、壳聚糖、纤维素或环糊精中的一种或几种;所述聚合物粉末为聚乙烯、聚丙烯中的一种或几种;所述分散剂为硅烷偶联剂、钛酸酯偶联剂、铝酸酯偶联剂的一种或几种。优选地,所述步骤3)中的有机溶剂为n,n二甲基甲酰胺。优选地,所述步骤3)的研磨细度为≤1μm,导热聚合物纤维丝的直径为5~10μm之间。优选地,所述步骤2)中蒸压反应釜热处理的条件为釜内温度大于140℃,压力大于0.2mpa,反应过程持续搅拌。优选地,所述步骤2)中预分散处理采用超声分散或砂磨机分散。优选地,所述步骤3)中干燥采用冷冻干燥或喷雾干燥,所述冷冻干燥条件为:冻干温度维持在-50~30℃,冻干时间10~40h,真空度1~300pa;所述喷雾干燥条件为:进口温度为100~350℃,出口温度为40~150℃,干燥介质为热空气。本发明的有益效果在于:1、本发明采用蒸压-纺丝-熔融共混的成型工艺,蒸压是通过天然有机高分子化合物助剂将导热材料与聚合物粉末复合,纺丝是将复合材料实现微米级的均匀混合,熔融共混使复合材料进一步混合均匀,实现复合材料的均匀混合,采用此工艺制备出的高导热复合材料热导率高于现有产品,导热性能优越。2、本发明采用蒸压-纺丝-熔融共混的成型工艺,实现复合材料微米级混合,提高了导热填料在聚合物中的分散性,解决了导热填料与聚合物基体相容性差的问题。3、本发明导热材料添加量不超过10%,避免了导热填料添加填充量过大引起的机械性能降低问题,同时利用蒸压-纺丝-熔融的成型工艺,还起到增强和增韧的作用。4、本发明制备的高导热复合材料同时具有导热填料添加量低、导热性能优越、分散性好等优点,并且拥有良好的机械性能,在得到高热导率的同时具有很好机械性能,解决了导热填料与聚合物基体的亲和性差且分散不匀,热导率提高的同时力学性能下降等问题。附图说明为了更清楚地说明本发明实施例或现有技术中的技术方案,下面将对实施例或现有技术描述中所需要使用的附图作简单地介绍,显而易见地,下面描述中的附图仅仅是本发明的一些实施例,对于本领域普通技术人员来讲,在不付出创造性劳动的前提下,还可以根据这些附图获得其他的附图。图1为本发明实施例1步骤3)所制得的导热聚合物纤维丝的显微镜照片。具体实施方式下面将结合本发明实施例中的附图,对本发明实施例中的技术方案进行清楚、完整地描述,显然,所描述的实施例仅仅是本发明一部分实施例,而不是全部的实施例。基于本发明中的实施例,本领域普通技术人员在没有做出创造性劳动前提下所获得的所有其他实施例,都属于本发明保护的范围。实施例1:如图1所示,本发明提供了一种高导热复合材料的制备方法,包括以下步骤:1)按以下组分及重量份配比配料:导热材料为石墨烯和铜粉的混合物,其中石墨烯0.4份、铜粉0.1份;分散剂为硅烷偶联剂,0.8份;天然有机高分子材料为淀粉,2份;聚合物粉末为聚乙烯,100份;2)将包括石墨烯、铜粉、硅烷偶联剂、淀粉、聚乙烯按照步骤1)的配比加入到水溶液中采用超声分散进行预分散处理,预分散处理后转移到蒸压反应釜中进行热处理,处理温度为150℃,压力为0.25mpa,反应过程持续搅拌;3)将步骤2)所得溶液进行冷冻干燥处理,处理条件为:冻干温度维持在-30℃,冻干时间25h,真空度100pa,经干燥后加入到n,n二甲基甲酰胺溶剂中,研磨至细度为≤1μm,通过静电纺丝技术,得到直径为5~10μm的导热聚合物纤维丝;4)将步骤3)所得导热聚合物纤维丝利用双螺杆挤出机熔融挤出、造粒,制得高导热聚合物母粒。实施例2:本发明提供了一种高导热复合材料的制备方法,包括以下步骤:1)按以下组分及重量份配比配料:导热材料为石墨烯和氧化铝的混合物,其中石墨烯0.4份、氧化铝0.1份;分散剂为钛酸酯偶联剂,0.7份;天然有机高分子材料为环糊精,1.5份;聚合物粉末为聚乙烯,100份;2)将包括石墨烯、氧化铝、钛酸酯偶联剂、壳聚糖、聚乙烯按照步骤1)的配比加入到水溶液中采用超声分散进行预分散处理,预分散处理后转移到蒸压反应釜中进行热处理,处理温度为150℃,压力为0.25mpa,反应过程持续搅拌;3)将步骤2)所得溶液进行冷冻干燥处理,处理条件为:冻干温度维持在-30℃,冻干时间25h,真空度100pa,经干燥后加入到n,n二甲基甲酰胺溶剂中,研磨至细度为≤1μm,通过静电纺丝技术,得到直径为5~10μm的导热聚合物纤维丝;4)将步骤3)所得导热聚合物纤维丝利用双螺杆挤出机熔融挤出、造粒,制得高导热聚合物母粒。实施例3:本发明提供了一种高导热复合材料的制备方法,包括以下步骤:1)按以下组分及重量份配比配料:导热材料为碳微球和碳化硅的混合物,其中碳微球0.2份、碳化硅0.2份;分散剂为铝酸酯偶联剂,1.5份;天然有机高分子材料为纤维素,2.5份;聚合物粉末为聚乙烯,100份;2)将包括碳微球、碳化硅、铝酸酯偶联剂、纤维素、聚乙烯按照步骤1)的配比加入到水溶液中采用采用砂磨机分散进行预分散处理,预分散处理后转移到蒸压反应釜中进行热处理,处理温度为160℃,压力为0.3mpa,反应过程持续搅拌;3)将步骤2)所得溶液进行喷雾干燥处理,处理条件为:进口温度为150℃,出口温度为60℃,干燥介质为热空气,经干燥后加入到n,n二甲基甲酰胺溶剂中,研磨至细度为≤1μm,通过静电纺丝技术,得到直径为5~10μm的导热聚合物纤维丝;4)将步骤3)所得导热聚合物纤维丝利用双螺杆挤出机熔融挤出、造粒,制得高导热聚合物母粒。实施例4:本发明提供了一种高导热复合材料的制备方法,包括以下步骤:1)按以下组分及重量份配比配料:导热材料为碳微球和氮化硅的混合物,其中碳微球0.2份、氮化硅0.2份;分散剂为铝酸酯偶联剂,0.5份;天然有机高分子材料为纤维素,1份;聚合物粉末为聚乙烯,100份;2)将包括碳微球、氮化硅、铝酸酯偶联剂、纤维素、聚乙烯按照步骤1)的配比加入到水溶液中采用采用砂磨机分散进行预分散处理,预分散处理后转移到蒸压反应釜中进行热处理,处理温度为160℃,压力为0.3mpa,反应过程持续搅拌;3)将步骤2)所得溶液进行喷雾干燥处理,处理条件为:进口温度为150℃,出口温度为60℃,干燥介质为热空气,经干燥后加入到n,n二甲基甲酰胺溶剂中,研磨至细度为≤1μm,通过静电纺丝技术,得到直径为5~10μm的导热聚合物纤维丝;4)将步骤3)所得导热聚合物纤维丝利用双螺杆挤出机熔融挤出、造粒,制得高导热聚合物母粒。实施例5:本发明提供了一种高导热复合材料的制备方法,包括以下步骤:1)按以下组分及重量份配比配料:导热材料为石墨烯和氧化铝的混合物,其中石墨烯5份、氧化铝1份;分散剂为硅烷偶联剂和铝酸酯偶联剂的混合物,其中硅烷偶联剂1份,铝酸酯偶联剂0.5份;天然有机高分子材料为环糊精,3份;聚合物粉末为聚丙烯,100份;2)将包括石墨烯、氧化铝、硅烷偶联剂、铝酸酯偶联剂、环糊精、聚丙烯按照步骤1)的配比加入到水溶液中采用采用砂磨机分散进行预分散处理,预分散处理后转移到蒸压反应釜中进行热处理,处理温度为200℃,压力为0.5mpa,反应过程持续搅拌;3)将步骤2)所得溶液进行喷雾干燥处理,处理条件为:进口温度为200℃,出口温度为80℃,干燥介质为热空气,经干燥后加入到n,n二甲基甲酰胺溶剂中,研磨至细度为≤1μm,通过静电纺丝技术,得到直径为5~10μm的导热聚合物纤维丝;4)将步骤3)所得导热聚合物纤维丝利用双螺杆挤出机熔融挤出、造粒,制得高导热聚合物母粒。实施例6:本发明提供了一种高导热复合材料的制备方法,包括以下步骤:1)按以下组分及重量份配比配料:导热材料为石墨烯、铜粉和氧化铝的混合物,其中石墨烯6份、铜粉2份、氧化铝2份;分散剂为铝酸酯偶联剂,2份;天然有机高分子材料为壳聚糖和环糊精的混合物,其中壳聚糖3份,环糊精2份;聚合物粉末为聚丙烯,100份;2)将包括石墨烯、铜粉、氧化铝、铝酸酯偶联剂、壳聚糖、环糊精、聚丙烯按照步骤1)的配比加入到水溶液中采用采用砂磨机分散进行预分散处理,预分散处理后转移到蒸压反应釜中进行热处理,处理温度为200℃,压力为0.5mpa,反应过程持续搅拌;3)将步骤2)所得溶液进行冷冻干燥处理,处理条件为:冻干温度维持在-20℃,冻干时间30h,真空度100pa,经干燥后加入到n,n二甲基甲酰胺溶剂中,研磨至细度为≤1μm,通过静电纺丝技术,得到直径为5~10μm的导热聚合物纤维丝;4)将步骤3)所得导热聚合物纤维丝利用双螺杆挤出机熔融挤出、造粒,制得高导热聚合物母粒。图1实施例1步骤3)所制得的导热聚合物纤维丝的显微镜照片,直径为5~10μm。实验例:样品a为实施例1制备得到的产品,样品b为实施例2制备得到的产品,样品c为实施例3制备得到的产品,样品d为实施例4制备得到的产品,样品e为实施例5制备得到的产品,样品f为实施例6制备得到的产品,对照样品为hdpe粉料,厂家:韩国lg-dow,型号;5019rq。1、抗拉强度试验试验依据:gb/16491-2008试验仪器:万能拉力试验机试验结果:通过表1可以看出,样品a、b抗拉强度均在35mpa以上,样品c抗拉强度为34.3mpa,样品d、e抗拉强度均在33mpa以上,样品f抗拉强度为32.7mpa,整体抗拉强度在32.7-35.5mpa之间,相对于对照样品的28.5mpa有明显提高,可见本发明所制备的高导热复合材料抗拉强度优于现有产品。表1抗拉强度试验结果样品抗拉强度(mpa)a35.1b35.5c34.3d33.8e33.1f32.7对照样品28.52、热导率试验试验依据:gb/t3399-1982试验仪器:导热系数测定仪试验结果:通过表2可以看出,样品a热导率为1.013w/(m·k),样品b热导率为0.917w/(m·k),样品c热导率为0.650w/(m·k),样品a热导率优于样品b,样品b热导率优于样品c,样品d热导率为0.708w/(m·k),样品e热导率为0.923w/(m·k),样品f热导率为1.009w/(m·k),而对照样品热导率仅为0.410w/(m·k),较样品a至f均低,可见本发明所制备的高导热复合材料热导率优于现有产品。表2热导率试验结果3、分散尺寸等级试验:试验依据:gb/t18251-2019试验仪器:炭黑分散度测试仪试验结果:通过表3可以看出,样品a分散尺寸等级为5.9,样品b分散尺寸等级为5.7,样品c分散尺寸等级为5.1,样品d分散尺寸等级为5.1,样品e分散尺寸等级为5.0,样品f分散尺寸等级为4.9,而对照样品分散尺寸等级仅为3.5,较样品a至f均低,可见本发明所制备的高导热复合材料分散尺寸等级优于现有产品,提高了导热填料在聚合物中的分散性。表3分散尺寸等级试验结果样品分散尺寸等级a5.9b5.7c5.1d5.1e5.0f4.9对照样品3.5显然,本领域的技术人员可以对本发明进行各种改动和变型而不脱离本发明的精神和范围。这样,倘若本发明的这些修改和变型属于本发明权利要求及其等同技术的范围之内,则本发明也意图包含这些改动和变型在内。当前第1页12