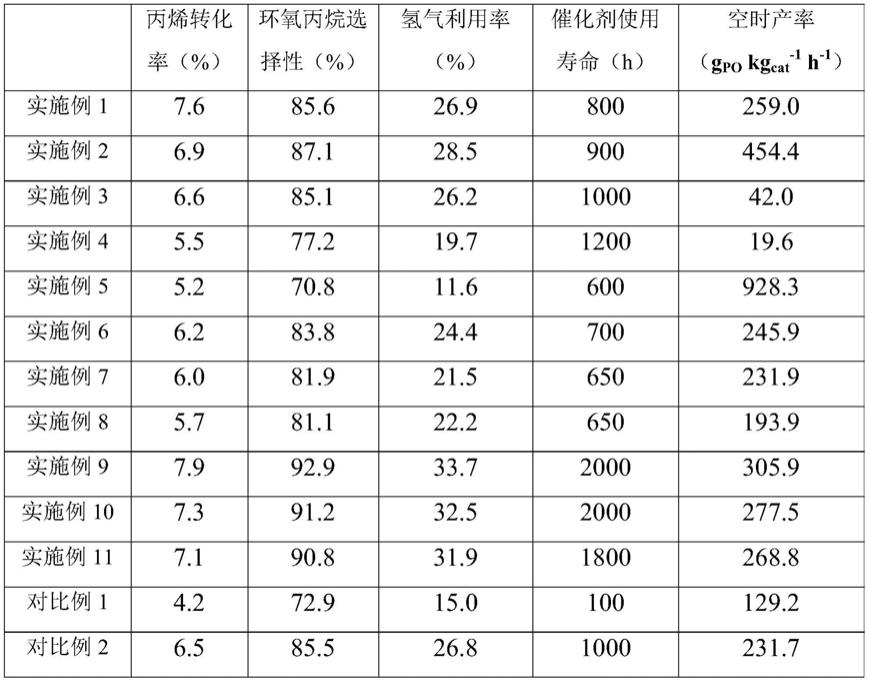
1.本发明涉及环氧丙烷制备领域,具体涉及一种丙烯直接环氧化以制备环氧丙烷的方法。
背景技术:2.环氧丙烷,又名氧化丙烯、甲基环氧乙烷,是非常重要的有机化合物原料,是仅次于聚丙烯和丙烯腈的第三大丙烯类衍生物。环氧丙烷为无色醚味液体,低沸点、易燃。有手性,工业品一般为两种对映体的外消旋混合物。与水部分混溶,与乙醇、乙醚混溶。与戊烷、戊烯、环戊烷、环戊烯、二氯甲烷形成二元共沸混合物。
3.环氧丙烷主要用于生产聚醚多元醇、丙二醇和各类非离子表面活性剂等,其中聚醚多元醇是生产聚氨酯泡沫、保温材料、弹性体、胶粘剂和涂料等的重要原料,各类非离子型表面活性剂在石油、化工、农药、纺织、日化等行业得到广泛应用。同时,环氧丙烷也是重要的基础化工原料。
4.目前工业上较新颖的环氧丙烷生产方法是hppo法,是以钛硅分子筛为催化剂,过氧化氢为氧化剂的直接氧化法。hppo法的产物中只有环氧丙烷和水,产品选择性高,副产物少,且工艺流程简单无污染。但是,该法存在催化剂寿命短、能耗高、溶剂量大、h2o2利用率低等问题。近年来,丙烯直接氧化制备环氧丙烷的方法由于其选择性高、反应过程简单等优点受到研究者越来越多的关注。该方法也没有解决催化剂寿命短(催化剂寿命都在100小时以下)的问题。
技术实现要素:5.本发明的目的是为了克服现有丙烯环氧化技术中存在的催化剂使用寿命短的问题,提供一种丙烯直接环氧化以制备环氧丙烷的方法。本发明以丙烷作为稀释气进行丙烯环氧化反应,在显著延长了催化剂的使用寿命的同时,还提高了反应选择性和丙烯转化率。
6.为了实现上述目的,本发明提供了一种丙烯直接环氧化的方法,该方法包括:在丙烯环氧化反应条件下,将反应原料气和稀释气的混合气体与催化剂进行接触反应,以得到环氧丙烷;其中,所述反应原料气包括丙烯、氧气和氢气,所述稀释气为丙烷。
7.优选的,所述环氧化反应在微通道反应器中进行。
8.优选的,所述催化剂与惰性填充物以分层堆积的方式填充于反应器中。
9.优选的,所述丙烯环氧化反应的空速为500-30000ml g
cat-1
h-1
。
10.优选的,以0.1-10℃min-1
的速率将反应体系的温度升温至丙烯环氧化反应所需温度。
11.优选地,该方法还包括对所述混合气体进行预混合和/或预热。
12.通过上述技术方案,本发明可取得如下的有益效果:
13.1.本发明以丙烷作为丙烯直接环氧化反应的稀释气,显著延长了催化剂的使用寿命,以在管式反应器中为例,可由常规的100小时延长至至少600小时,在微通道反应器中,
所述催化剂的寿命还能够进一步延长。
14.2.本发明以丙烷作为丙烯直接环氧化反应的稀释气,有效降低了稀释气的用量,例如,管式反应器中,采用本发明的方案可降低至62.5体积%以下,而在微通道中,可以进一步降低稀释气的用量,甚至可以降低至接近0的水平。此外,稀释气用量的降低还降低了后续产物分离困难,降低了能耗。
15.3.爆轰管燃爆实验显示,相比于n2作为稀释气,在丙烷为稀释气的情况下,体系可容忍极限氧含量更高,原料气比例可操作范围更广,因而可以更加安全而无燃爆风险,进一步实现了反应流程的本质安全化。
16.4.本发明以丙烷作为丙烯直接环氧化反应的稀释气,丙烷能够抑制副反应的产生。因此,进一步提高了环氧丙烷的选择性和丙烯的转化率。
17.5.在所述稀释气为丙烷时,丙烷的比热容较大,相比于氮气来说,丙烷作为稀释气可以迅速的吸收环氧化过程中释放出来的反应热,保证丙烯气相直接环氧化反应安全高效进行。
附图说明
18.图1是本发明使用的一种心形结构的微通道反应器;
19.图2是本发明使用的一种菱形结构的微通道反应器;
20.图3是本发明使用的一种s形结构的微通道反应器;
21.图4是本发明使用的一种螺旋形反应器;
22.图5是本发明提供的催化剂的填充方式。
具体实施方式
23.在本文中所披露的范围的端点和任何值都不限于该精确的范围或值,这些范围或值应当理解为包含接近这些范围或值的值。对于数值范围来说,各个范围的端点值之间、各个范围的端点值和单独的点值之间,以及单独的点值之间可以彼此组合而得到一个或多个新的数值范围,这些数值范围应被视为在本文中具体公开。
24.本发明提供了一种丙烯直接环氧化的方法,该方法包括:在丙烯环氧化反应条件下,将反应原料气和稀释气的混合气体与催化剂进行接触反应,以得到环氧丙烷;其中,所述反应原料气包括丙烯、氧气和氢气,所述稀释气为丙烷。
25.一般来讲,在丙烯直接环氧化反应中,通常会选用惰性气体,例如,氮气或氩气作为稀释气,如此会使得反应更为安全,燃爆风险更低。然而本发明的发明人在研究的过程中发现,在采用丙烷作为稀释气的情况下,除了能够提高催化剂的使用寿命,还能够降低稀释气的使用量,提高反应体系的氧气容忍度,因此,在降低反应产物后续分离压力的同时,降低了燃爆风险。同时由于稀释气用量的降低,反应气的浓度相对得到了提高,能够有效推进反应的正向进行,此外,丙烷也能够抑制副反应的产生,从而提高反应选择性和转化率。另外,由于稀释气用量的降低,稀释气的驱动和分离能耗也得到了降低。
26.根据本发明,通常情况下,为了确保反应的安全性,在所述混合气体中,氧气的浓度一般不得高于5体积%,然而根据本发明的方法,在所述混合气体中,氧气的比例可以大于12.5体积%,例如,氧气的比例可以为12.5体积%、13体积%、14体积%、15体积%、16体
积%、17体积%、18体积%、19体积%、20体积%、21体积%、22体积%、23体积%、24体积%、25体积%等等,优选大于14体积%,更优选大于20体积%。
27.根据本发明,所述氧气的浓度优选不高于45体积%。
28.根据本发明,通常情况下,为了确保反应的安全性,在所述混合气体中,稀释气的比例一般不得低于70体积%。然而根据本发明的方法,在所述混合气体中,所述稀释气的可以低于62.5体积%,例如,可以为25体积%、30体积%、35体积%、40体积%、45体积%、50体积%、55体积%、60体积%、62.5体积%;优选低于57.5体积%,更优选低于40体积%。
29.由以上可以看出,本发明的方法可以提高氧气的用量,提高反应气的浓度,可以促进反应的正向进行,并且可以降低稀释气的用量,可降低后续反应产物的分离工艺的压力。
30.根据本发明,所述丙烯环氧化反应可以在本领域常规的反应器中进行,只要选用本发明的丙烷作为稀释气,即可提高丙烯直接环氧化反应用催化剂的使用寿命,降低稀释气用量和提高反应气用量,提高反应选择性和转化率,以及降低能耗。
31.根据本发明一种具体的实施方式,所述丙烯环氧化反应在管式反应器中进行。所述管式反应器可以为本领域常规的各种管式反应器,例如,石英管反应器。
32.根据本发明另一种优选的实施方式,为了进一步实现本发明的目的,所述环氧化反应在微通道反应器中进行。在微通道反应器中,虽然由于微通道的器壁效应,可淬灭火焰传播,使得反应物浓度不再受爆炸极限限制,因此,可以不考虑氧气浓度的限制,也即,可以不使用稀释气。但通常情况下,因为稀释气有吹扫气的作用,可以将反应产物环氧丙烷及时从催化活性中心分离,促进反应平衡正向移动。因此,为了保证反应效率,通常会使用一定比例的稀释气,例如,稀释气在混合气体比例中的比例一般不低于40体积%。
33.根据本发明,所述微通道反应器可以为常规的各种反应器,本发明对此并没有特别的限制,根据本发明一种优选的实施方式,所述微通道反应器的结构为多个依次串联的不规则或规则结构,所述催化剂填充于所述多个不规则或规则结构中的至少一部分。其中,这些多个依次串联的不规则或规则结构可以形成蛇形结构,所述催化剂可以填充在所述蛇形结构的一段通道中,也可以填充在所有通道中。
34.其中,所述不规则或规则的结构的种类并没有特别的限制,优选的,所述不规则或规则结构选自心形、菱形、s形、三角形、长方形、正方形、圆形、交叉指形、螺旋形、v形、t形、c形等。
35.根据本发明一种具体的实施方式,所述微通道反应器为多个依次串联的心形结构,如图1所示。在该优选的技术方案下,以丙烷作为稀释气,所述稀释气的比例降低至小于30体积%的情况下,例如,10体积%、15体积%、25体积%、30体积%,也能够有效的保证反应具有相当或是更高的丙烯转化率和产物的选择性。
36.根据本发明一种具体的实施方式,所述微通道反应器为多个依次串联的菱形结构,如图2所示。在该优选的技术方案下,以丙烷作为稀释气,所述稀释气的比例降低至小于30体积%的情况下,例如,10体积%、15体积%、25体积%、30体积%,也能够有效的保证反应具有相当或是更高的丙烯转化率和产物的选择性。
37.根据本发明一种具体的实施方式,所述微通道反应器为多个依次串联的s形结构,如图3所示。在该优选的技术方案下,以丙烷作为稀释气,所述稀释气的比例降低至小于30体积%的情况下,例如,10体积%、15体积%、25体积%、30体积%,也能够有效的保证反应
具有相当或是更高的丙烯转化率和产物的选择性。
38.根据本发明一种优选的实施方式,所述微通道反应器为螺旋形微通道反应器,如图4所示,所述催化剂填充于螺旋形结构中的至少一部分。其中,所述螺旋形微通道反应器可以为以螺旋的方式形成的蛇形结构,所述催化剂可以填充在所述蛇形结构的一段通道中,也可以填充在所有通道中。在该优选的技术方案下,以丙烷作为稀释气,所述稀释气的比例降低至小于30体积%的情况下,例如,10体积%、15体积%、25体积%、30体积%,也能够有效的保证反应具有相当或是更高的丙烯转化率和产物的选择性。
39.根据本发明,所述微通道反应器的长度可以在较宽的范围内进行改变,优选的,其长度为1-1000mm,优选10-500mm。所述微通道反应器的结构为多个依次串联的不规则或规则结构时,每个不规则或规则结构的长度优选为1-100mm,优选5-50mm。
40.根据本发明,所述微通道反应器在径向方向上的宽度不受特别的限制,只要符合微通道反应器的标准即可,本发明所示的微通道反应器,其在径向方向上的宽度沿着微通道反应器的长度相同(例如,当所述微通道反应器为螺旋结构微通道反应器时)或不同(例如,当所述微通道反应器为心形结构反应器时),根据本发明一种优选的实施方式,相同时,其径向方向上的宽度为20-2000微米;不同时,其径向方向上的宽度最小处为10-1000微米,最大为处100-3000微米。
41.根据本发明,所述微通道反应器的材质可以为任意的能够耐受本发明反应温度且与本发明的原料和生成物不发生反应的材质,例如,其可为有机玻璃、陶瓷玻璃、不锈钢金属、石英、树脂材质等。
42.根据本发明,所述催化剂可以具有任意适合所述管式反应器或所述微通道反应器的尺寸和形状。
43.根据本发明,所述催化剂可以为现有技术公开的任意能够将丙烯、氧气、氢气和稀释气催化反应以生成环氧丙烷的催化剂,优选的,所述催化剂为负载型金属催化剂。其中,所述金属可以选自金、银、铜、钌、钯、铂、铑、钴、镍、钨、铋、钼及其氧化物中的至少一种,优选为金;用于负载所述金属的载体可以为炭黑、活性炭、二氧化硅、三氧化二铝、氧化铈、钛硅分子筛、沸石、树脂、聚合物和碱土金属碳酸盐中的至少一种,优选为钛硅分子筛。
44.根据本发明,在所述负载型金属催化剂中,以金属元素计的金属的含量可以在较宽的范围内改变,例如,催化剂中以金属元素计的金属的含量为0.01-50重量%,例如,可以为0.01重量%、0.05重量%、0.06重量%、0.07重量%、0.08重量%、0.09重量%、0.1重量%、0.2重量%、0.3重量%、0.4重量%、0.5重量%、0.6重量%、0.7重量%、0.8重量%、0.9重量%、1重量%、1.1重量%、1.2重量%、1.3重量%、1.4重量%、1.5重量%、1.6重量%、1.7重量%、1.8重量%、1.9重量%、2重量%、3重量%、4重量%、5重量%、10重量%、15重量%、20重量%、25重量%、30重量%、35重量%、40重量%、45重量%、50重量%,优选为0.05-5重量%,更优选0.1-2重量%。
45.根据本发明一种优选的实施方式,所述催化剂为负载金的钛硅分子筛(au@ts-1),其中,以金元素计的负载量为0.1-2重量%,ts-1分子筛可以通过水热合成的方式制备,活性金属au可以通过沉积沉淀的方法进行负载。
46.根据本发明,所述催化剂可以单独填充在丙烯环氧化反应的反应器中(如图5a所示),也可以与其他惰性物质结合填充在所述反应器中。但为了进一步提高催化剂的使用寿
命,提高反应的选择性、转化率、时空产率以及氢气利用率,降低催化剂的用量,优选的,所述催化剂以与催化剂和惰性填充物相结合的形式填充于所述反应器中。其中,所述惰性填充物可以为本领域常规使用的惰性固相物质,优选的,所述惰性填充物选自石英砂、al2o3、多孔硅胶和陶瓷环中的至少一种。
47.其中,所述惰性填充物的用量可以在较宽的范围内改变,但优选的,相对于1重量份的催化剂,所述惰性填充物的用量为1-200重量份(例如,可以为1重量份、10重量份、20重量份、50重量份、80重量份、90重量份、95重量份、100重量份、105重量份、110重量份、115重量份、120重量份、125重量份、130重量份、135重量份、140重量份、145重量份、150重量份、160重量份、170重量份、180重量份、190重量份、200重量份),优选为80-150重量份,更优选为90-110重量份。
48.根据本发明,所述催化剂与所述惰性填充物的结合形式可以不受特别的限制,例如,可以直接将二者混合后填充于所述反应器中,也可以将二者设计成三明治结构(如图5b),其中,催化剂或者惰性填充物位于中间。然而本发明的发明人在研究中发现,所述催化剂与惰性填充物以分层堆积的方式填充于所述反应器中(如图5c所示),能够进一步提高催化剂的寿命,反应的选择性、转化率、时空产率以及氢气利用率,以及降低催化剂的用量。其中,在该方式中,所述催化剂层和惰性填充物层的高度可以在较宽的范围内选择,他们可以以等高度的方式或不等高度的方式进行分层堆积,优选的,所述催化剂层和惰性填充物层各自独立地为1-2000层/米,例如,可以为1层/米、2层/米、3层/米、4层/米、5层/米、6层/米、7层/米、8层/米、9层/米、10层/米、15层/米、18层/米、20层/米,50层/米、100层/米、200层/米、300层/米、400层/米、500层/米、600层/米、700层/米、800层/米、900层/米、1000层/米、1200层/米、1400层/米、1600层/米、1800层/米、2000层/米;优选为1000-2000层/米,或者10-20层/米。
49.根据本发明,所述催化剂层和惰性填充物层的层高比可以在较宽的范围内改变,优选的,为了进一步提高本发明的效果,所述催化剂层和惰性填充物层的层高比为1:1-10,例如,可以为1:1、1:2、1:3、1:4、1:5、1:6、1:7、1:8、1:9、1:10,优选为1:1-3,进一步优选为1:1.5-2.5。
50.根据本发明,将所述催化剂填充于所述反应器中的方式可以不受特别的限制,例如,可以采用涂层法、电沉积法、溶液电镀法、机械填充法等。
51.根据本发明,优选的,相对于10ml的反应器,所述催化剂的用量为0.1-0.5g。通常情况下,催化剂的用量至少需要1g,而可以看出,本发明的技术方案还可以降低催化剂的用量。
52.根据本发明,所述丙烯环氧化反应的温度可以为本领域常规的反应温度,例如,可以为20-300℃,但为了进一步提高反应的转化率、选择性、时空产率以及氢气利用率,以及提高催化剂的使用寿命,降低催化剂的用量,优选的,所述反应的温度为50-250℃,更优选为120-200℃,例如,可以为120℃、125℃、130℃、135℃、140℃、145℃、150℃、155℃、160℃、165℃、170℃、175℃、180℃、185℃、190℃、195℃、200℃。
53.本发明的发明人在研究中发现,体系的升温速度也能够进一步影响反应的转化率、选择性、时空产率以及氢气利用率,催化剂的使用寿命,催化剂的用量,当以0.1-10℃min-1
,优选0.5-5℃min-1
,更优选0.5-2℃min-1
,(例如,可以为0.5℃min-1
、0.8℃min-1
、1.0
℃min-1
、1.2℃min-1
、1.5℃min-1
、2.0℃min-1
,进一步优选0.8-1.5℃min-1
)的速率将反应体系的温度升温至丙烯环氧化反应所需温度时,能够进一步提高反应的转化率、选择性、时空产率以及氢气利用率,以及提高催化剂的使用寿命,降低催化剂的用量和稀释气用量。
54.根据本发明,为了进一步提高反应的效率,在所述混合气体进入到所述反应器前,还优选对其进行预混合和/或预热。
55.根据本发明,所述预热的程度优选至少达到目标反应温度的50%,例如,50%、55%、60%、65%、70%、75%、80%、85%。
56.根据本发明,所述丙烯环氧化反应的压力可以为本领域常规的反应压力,例如,可以为0-5mpa,但为了进一步提高反应的转化率、选择性、时空产率以及氢气利用率,以及提高催化剂的使用寿命,降低催化剂的用量,优选的,所述反应的压力0-1.5mpa,更优选为0.05-0.25mpa,例如,可以为0.05mpa、0.07mpa、0.09mpa、0.11mpa、0.13mpa、0.15mpa、0.17mpa、0.19mpa、0.21mpa、0.23mpa、0.25mpa。
57.根据本发明,所述丙烯环氧化反应的空速可以为本领域常规的反应空速,但为了进一步提高反应的转化率、选择性、时空产率以及氢气利用率,以及提高催化剂的使用寿命,降低催化剂的用量,优选的,反应空速为500-30000ml g
cat-1
h-1
,更优选为1000-20000ml g
cat-1
h-1
,进一步优选为2000-15000ml g
cat-1
h-1
,例如,可以为2000ml g
cat-1
h-1
、3000ml g
cat-1
h-1
、4000ml g
cat-1
h-1
、5000ml g
cat-1
h-1
、6000ml g
cat-1
h-1
、7000ml g
cat-1
h-1
、8000ml g
cat-1
h-1
、9000ml g
cat-1
h-1
、10000ml g
cat-1
h-1
、12000ml g
cat-1
h-1
、13000ml g
cat-1
h-1
、14000ml g
cat-1
h-1
、15000ml g
cat-1
h-1
。
58.根据本发明,丙烯、氧气、氢气的用量体积比优选为0.5-2:0.5-2:1。
59.根据本发明,丙烯、氧气、氢气和稀释气的流速不受特别的限制,只要能够保证按照如上的用量体积比混合即可。
60.根据本发明,本发明的方法还可以包括对反应产物进行组分分析,可以在气相色谱分析设备中进行,例如,将反应产物引入到配备有tcd和fid检测器的气相色谱中进行分析。
61.更优选的,为了保证分析的效果,所述反应产物在50-200℃的加热条件下输送至组分分析设备中,具体可以在反应器的出口和组分分析设备进样口之间设置加热带以维持50-200℃的温度,优选80-150℃,例如,80℃、90℃、100℃、110℃、120℃、130℃、140℃、150℃。
62.根据本发明,本发明的方法提供的所述丙烯环氧化反应优选不在溶剂的存在下进行。其中,所述溶剂包括任意的外援引入的液相。
63.以下将通过实施例对本发明进行详细描述。
64.微通道反应单元:包括混合器、预热器和微通道反应器,其中,混合器、预热器和微通道反应器均为如图1所示心形结构,区别在于微通道反应器中填充有催化剂,外周设置有温度控制设备,预热器中的外周设置有加热装置;其中,每个心形结构的长度为7mm,心形结构的宽度最宽处为2mm,将相邻两个心形结构相连的管路横截面为圆形,直径为1mm,微通道反应器的总长度为1cm。
65.管式反应器为石英管反应器,直径3cm。
66.产物分析使用2台气相色谱仪,对产物采样进气相色谱分析。两台分析色谱型号均
为安捷伦7890b,其中气相色谱a的色谱柱为(1)hayesep q柱(sft 0.9m,od 1/8,id 2mm),(2)molsieve 5a柱(sft 2.44m,od 1/8,id 2mm),(3)porabond u柱(25m,0.32mm,7μm);配有tcd和fid检测器用于分析h2、o2、稀释气等永久性气体和丙烯、丙烷、环氧丙烷、丙烯醛、丙酮、丙醛、乙醛等,其中丙烯和氢气的出峰位置相似,两者相互影响不能准确区分,所以用气相色谱b辅助分析。气相色谱b的色谱柱为(1)hayesep q柱(sft 1.83m,od 1/8,id 2mm),(2)molsieve 5a柱(sft 2.44m,od 1/8,id 2mm),(3)hp-al\s柱(25m,0.32mm,8μm);配有tcd和fid检测器用于分析h2、o2、稀释气等永久性气体和丙烯、丙烷。
67.au@ts-1分子筛催化剂中,ts-1分子筛通过水热合成的方式制备,活性金属au通过沉积沉淀的方法进行负载。
68.燃爆实验
69.1)在微通道或管式反应器中,相对于10ml的反应器,填充0.3g au@ts-1分子筛催化剂(au的负载量为1重量%),其与30g石英砂分层堆积,如图5中(c)所示,其中,催化剂层和石英砂层的层高比为1:2,所述催化剂层和惰性填充物层各自独立地为15层/厘米,进行丙烯气相直接环氧化反应。
70.其中,原料气按照比例h2:o2:c3h6:丙烷=23%:23%:23%:31%通入混合器混合后进入预热器,预热至160℃后进入管式反应器中。
71.反应空速4000ml g
cat-1
h-1
,控制体系的反应压力0.2mpa,以1.5℃min-1
的速率程序升温至200℃。
72.其中,反应20min时间内,反应体系不爆炸。
73.在管式反应器中,将稀释气替换为氮气,无法安全进行。
74.以下实施例1-8以h2:o2:c3h6:稀释气=23%:23%:23%:31%的比例进行其他效果的验证。
75.实施例1
76.本实施例用于说明本发明提供的丙烯直接环氧化的方法
77.在管式反应器中,相对于10ml的反应器,将0.20g au@ts-1分子筛催化剂(au的负载量为1重量%)和20g石英砂分层填充在反应器中,如附图5中(c)所示,其中,催化剂层和石英砂层的层高比为1:2,所述催化剂层和惰性填充物层各自独立地为15层/厘米,进行丙烯气相直接环氧化反应。
78.其中,原料气h2、o2、c3h6、丙烷进入混合器混合后进入预热器,预热至160℃后进入管式反应器中,反应空速9000ml g
cat-1
h-1
,控制体系的反应压力0.15mpa,以0.8℃min-1
的速率程序升温至200℃,反应稳定20分钟后,丙烯气相直接环氧化反应分析如表1所示,并记录丙烯转化率、环氧丙烷选择性等指标开始下降时的大概时间(每50小时记录一次)。
79.实施例2
80.本实施例用于说明本发明提供的丙烯直接环氧化的方法
81.在管式反应器中,相对于10ml的反应器,将0.20g au@ts-1分子筛催化剂(au的负载量为1重量%)和18g石英砂分层填充在反应器中,如附图5中(c)所示,其中,催化剂层和石英砂层的层高比为1:1.5,所述催化剂层和惰性填充物层各自独立地为10层/厘米,进行丙烯气相直接环氧化反应。
82.其中,原料气h2、o2、c3h6、丙烷进入混合器混合后进入预热器,预热至130℃后进入
管式反应器中,反应空速15000ml g
cat-1
h-1
,控制体系的反应压力0.05mpa,以1.5℃min-1
的速率程序升温至170℃,反应稳定20分钟后,丙烯气相直接环氧化反应分析如表1所示,并记录丙烯转化率、环氧丙烷选择性等指标开始下降时的大概时间(每50小时记录一次)。
83.实施例3
84.本实施例用于说明本发明提供的丙烯直接环氧化的方法
85.在管式反应器中,相对于10ml的反应器,将0.20g au@ts-1分子筛催化剂(au的负载量为1重量%)和22g石英砂分层填充在反应器中,如附图5中(c)所示,其中,催化剂层和石英砂层的层高比为1:2.5,所述催化剂层和惰性填充物层各自独立地为20层/厘米,进行丙烯气相直接环氧化反应。
86.其中,原料气h2、o2、c3h6、丙烷进入混合器混合后进入预热器,预热至100℃后进入管式反应器中,反应空速2000ml g
cat-1
h-1
,控制体系的反应压力0.25mpa,以1.2℃min-1
的速率程序升温至120℃,反应稳定20分钟后,丙烯气相直接环氧化反应分析如表1所示,并记录丙烯转化率、环氧丙烷选择性等指标开始下降时的大概时间(每50小时记录一次)。
87.实施例4
88.本实施例用于说明本发明提供的丙烯直接环氧化的方法
89.在管式反应器中,相对于10ml的反应器,将0.20g au@ts-1分子筛催化剂(au的负载量为1重量%)和16g石英砂分层填充在反应器中,如附图5中(c)所示,其中,催化剂层和石英砂层的层高比为1:1,进行丙烯气相直接环氧化反应。
90.其中,原料气h2、o2、c3h6、丙烷进入混合器混合后进入预热器,预热至100℃后进入管式反应器中,反应空速1000ml g
cat-1
h-1
,控制体系的反应压力0.5mpa,以0.5℃min-1
的速率程序升温至100℃,反应稳定20分钟后,丙烯气相直接环氧化反应分析如表1所示,并记录丙烯转化率、环氧丙烷选择性等指标开始下降时的大概时间(每50小时记录一次)。
91.实施例5
92.本实施例用于说明本发明提供的丙烯直接环氧化的方法
93.在管式反应器中,相对于10ml的反应器,将0.20g au@ts-1分子筛催化剂(au的负载量为1重量%)和30g石英砂分层填充在反应器中,如附图5中(c)所示,其中,催化剂层和石英砂层的层高比为1:3,进行丙烯气相直接环氧化反应。
94.其中,原料气h2、o2、c3h6、丙烷进入混合器混合后进入预热器,预热至100℃后进入管式反应器中,反应空速25000ml g
cat-1
h-1
,控制体系的反应压力0.01mpa,以2.0℃min-1
的速率程序升温至250℃,反应稳定20分钟后,丙烯气相直接环氧化反应分析如表1所示,并记录丙烯转化率、环氧丙烷选择性等指标开始下降时的大概时间(每50小时记录一次)。
95.实施例6
96.本实施例用于说明本发明提供的丙烯直接环氧化的方法
97.按照实施例1的方法进行丙烯直接环氧化制备环氧丙烷,不同的是,所述催化剂按照图5中(b)中所示进行填装。分析如表1所示。
98.实施例7
99.本实施例用于说明本发明提供的丙烯直接环氧化的方法
100.按照实施例1的方法进行丙烯直接环氧化制备环氧丙烷,不同的是,所述催化剂按照图5中(a)中所示进行填装。分析如表1所示。
101.实施例8
102.本实施例用于说明本发明提供的丙烯直接环氧化的方法
103.按照实施例1的方法进行丙烯直接环氧化制备环氧丙烷,不同的是,在进入管式反应器单元之前不进行预热。分析如表1所示。
104.实施例9
105.本实施例用于说明本发明提供的丙烯直接环氧化的方法
106.按照实施例1的方法进行丙烯直接环氧化制备环氧丙烷,不同的是,将管式反应器替换为微通道反应器(包括混合器、预热器和微通道反应器,其中,混合器、预热器和微通道反应器均为如图1所示心形结构,区别在于微通道反应器中填充有催化剂,外周设置有温度控制设备,预热器中的外周设置有加热装置;其中,每个心形结构的长度为7mm,心形结构的宽度最宽处为2mm,将相邻两个心形结构相连的管路横截面为圆形,直径为1mm,微通道反应器的总长度为1cm)。分析如表1所示。
107.实施例10
108.本实施例用于说明本发明提供的丙烯直接环氧化的方法
109.按照实施例9的方法进行丙烯直接环氧化制备环氧丙烷,不同的是,所述微通道反应器的结构为螺旋形结构(如图4所示)。分析如表1所示。
110.实施例11
111.本实施例用于说明本发明提供的丙烯直接环氧化的方法
112.按照实施例9的方法进行丙烯直接环氧化制备环氧丙烷,不同的是,所述微通道反应器的结构为菱形结构(如图2所示)。分析如表1所示。
113.对比例1
114.本对比例用于说明参比的丙烯直接环氧化的方法
115.按照实施例1的方法进行丙烯直接环氧化制备环氧丙烷,不同的是,将稀释气替换为氮气,但为了确保反应的安全顺利进行,调节h2:o2:c3h6:n2=1:1:1:7,催化剂的填充量为0.3g。分析如表1所示。
116.对比例2
117.本对比例用于说明参比的丙烯直接环氧化的方法
118.按照实施例9的方法进行丙烯直接环氧化制备环氧丙烷,不同的是,所述微通道反应器不是心形结构,其为横截面是矩形的结构,该矩形结构长500微米,宽200微米,整个微通道反应器的长度为1厘米,催化剂的填充量为0.3g,稀释气为氮气。分析如表1所示。
119.表1
[0120][0121]
如表1所示,本发明使用丙烷作为稀释气,在能够提高催化剂使用寿命的同时,还能够降低稀释气用量和催化剂用量,以及能够提高丙烯转化率、环氧丙烷选择性空时产率氢气利用率催化剂使用寿命。而相比于管式反应器,微通道反应器在该反应上更具有优势,并且采用本发明优选的微通道反应器结构,在催化剂使用寿命、丙烯转化率、环氧丙烷的选择性、氢气的利用率上均有了进一步的提高。并且,在使用相同催化剂用量的情况下,本发明技术方案可以达到更好的效果,因此,本发明可以降低催化剂的用量。
[0122]
以上详细描述了本发明的优选实施方式,但是,本发明并不限于此。在本发明的技术构思范围内,可以对本发明的技术方案进行多种简单变型,包括各个技术特征以任何其它的合适方式进行组合,这些简单变型和组合同样应当视为本发明所公开的内容,均属于本发明的保护范围。