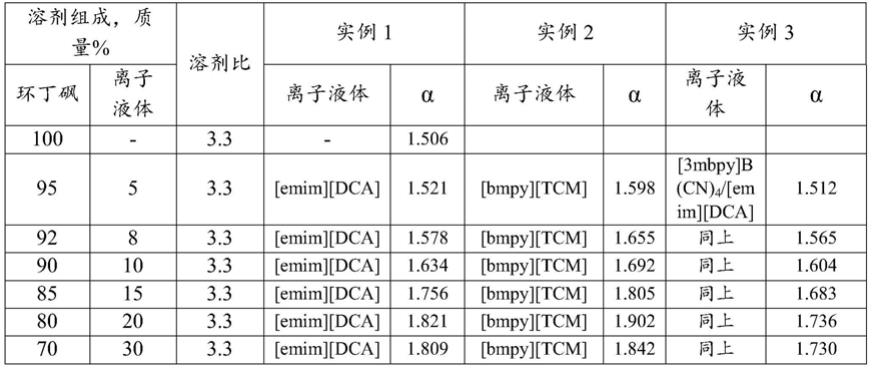
1.本发明为一种从烃类混合物中分离芳烃的复合溶剂及应用方法,具体地说,是一种利用萃取精馏从烃类混合物中分离高纯度芳烃所用的复合溶剂及应用方法。
背景技术:2.工艺和溶剂是芳烃抽提领域的核心,二者密不可分,直接决定了苯、甲苯、二甲苯(btx)产品的纯度和收率。从宽馏分混合物中分离c6~c8芳烃的主要工艺是液液抽提。未能使用萃取精馏工艺分离提纯btx的原因在于,原料馏分段变宽后,需要溶剂对苯的选择性更高,使其存在于萃取精馏塔塔釜,而较重的非芳烃(c8环烷烃)被蒸至塔顶。目前工业上应用最广泛的芳烃抽提溶剂为环丁砜,其选择性不足以实现上述分离,并且其溶解性有限,在萃取精馏塔的上部,尤其是溶剂进料位置与原料进料位置之间容易分相,从而导致萃取精馏塔操作困难。
3.如果在萃取蒸馏所用的溶剂环丁砜中加入一种助溶剂,提高其分离芳烃的选择性,则有利于用萃取精馏工艺分离btx,发挥其流程短、投资低、能耗小的优点。
4.近几年,离子液体作为一种新型溶剂引起了研究者的兴趣。离子液体是在室温及相邻温度下完全由离子组成的液体,通常具有以下优点:结构可设计、无毒、不可燃、不挥发、热力学稳定性高。因此,离子液体被认为是最有希望代替传统有机溶剂的“绿色溶剂”。然而,离子液体的阴离子通常含卤素、硫或氮,如果装置系统内有水,则容易和水中的h
+
结合形成酸,从而腐蚀设备,影响装置长周期运转。抽提系统内的水主要来自两方面,一是抽提原料油品中携带的水。目前重整或裂解加氢汽油中通常含有100~300mg/kg的溶解水,二是由于常规的减压蒸馏很难将溶剂中溶解的c
9+
重芳烃全部分离,需要向系统内补充水进行汽提或洗涤待再生溶剂。因此已工业化的芳烃抽提工艺系统内绝大多数都含水。
5.萃取精馏分离宽馏分原料中的芳烃另一个值得关注的问题是,萃取精馏原料,如裂解加氢汽油在上游加工过程中,由于负荷、苛刻度的变化容易产生极少量沸点高于200℃的c
9+
重非芳,c
9+
重非芳不溶于萃取溶剂,无法通过现有的闪蒸工艺分离。而c
9+
重非芳在贫溶剂中积累会导致贫溶剂分相,影响分离效果以及装置的长周期运转。
6.cn101265152a公开了一种离子液体作为萃取精馏分离苯和环己烷的溶剂的应用,使用离子液体为溶剂,所述离子液体的阳离子为咪唑阳离子,阴离子为六氟磷酸阴离子或卤素阴离子,离子液体含水量为0%~20%,可以将苯和环己烷通过萃取蒸馏分离。
7.cn104945328a公开了一种抽提分离柴油中芳烃和烷烃的复合溶剂,采用液液抽提分离柴油中的芳烃。所述复合溶剂包括离子液体和有机溶剂,并以离子液体为主溶剂,所述的离子液体阴离子为bf
4-、pf
6-、对甲基苯磺酸根、双三氟甲磺酰亚胺根、九氟丁磺酸根、十二烷基磺酸根、醋酸根或硫酸根,阳离子为咪唑类或吡啶类离子;采用的有机溶剂为n,n-二甲基甲酰胺、n,n-二甲基乙酰胺或环丁砜。所述抽提溶剂具有较好的芳烃溶解性,可有效分离柴油馏分中的芳烃,提高柴油馏分的十六烷值。
8.cn1062007c公开了一种芳烃抽提溶剂的再生方法,通过向待再生的溶剂中加入溶
剂量的50-400%的系统循环水,再通过机械过滤或床层过滤、吸附床层脱色净化处理,再生后的溶剂清亮、透明。所用溶剂为环丁砜、甘醇等有机溶剂。
9.cn106008457b公开了一种粗苯精制过程中溶剂再生工艺及装置,贫溶剂先后与非芳烃及水混合,再经两级分离槽分离出非芳烃及重烃组分,水和溶剂混合物进入水汽提塔进一步分离出非芳烃和水;经提纯后的贫溶剂再通过溶剂再生塔返回溶剂回收塔。
10.cn104271712a公开了一种利用抽余油置换和水洗涤去除贫溶剂中重组分的方法,并在贫溶剂循环管路增设磁性过滤器,去除顺磁性污染物,所述的重组分不外排,而是排入萃取蒸馏塔下部。
11.上述再生方法均需向系统内补充水,不适用于含离子液体的溶剂体系。
技术实现要素:12.本发明的目的是提供一种从烃类混合物中萃取精馏分离芳烃的复合溶剂及应用该复合溶剂萃取精馏分离芳烃的方法。所述的复合溶剂含有适量离子液体,对芳烃的选择性高,适用于从沸点范围宽的烃类原料中分离轻质芳烃。
13.本发明提供的从烃类混合物中萃取精馏分离芳烃的复合溶剂,由60~95质量%的环丁砜和5~40质量%的离子液体组成,所述离子液体的阳离子具有式(ⅰ)或式(ⅱ)的结构,阴离子为双氰胺离子、三氰基甲烷离子和四氰基硼酸根离子中的至少一种,
[0014][0015]
式(ⅰ)中,r1和r2分别选自c1~c4的烷基,式(ⅱ)中,r3和r4分别选自c1~c4的烷基。
[0016]
本发明提供的复合溶剂由环丁砜和适宜的离子液体组成,所述的离子液体在含量适宜的条件下,可与环丁砜协同作用,提高复合溶剂对芳烃的选择性,并增加对非芳烃的溶解性,并改善气液传质性能。
附图说明
[0017]
图1为使用本发明所述复合溶剂萃取精馏分离芳烃的流程示意图。
具体实施方式
[0018]
本发明所述的复合溶剂以环丁砜为主溶剂、离子液体为助溶剂,因含有适量离子液体,其沸点高、性质稳定,且对原料溶解性较好,芳烃选择性高,更适合采用萃取精馏分离沸点范围宽的c6~c8馏分中的混合芳烃(苯、甲苯和二甲苯),另外,本发明提供的复合溶剂中不含水,对装置无腐蚀,能够长周期运行。
[0019]
为使用本发明所述的复合溶剂,还提供了一种适合使用该复合溶剂萃取精馏分离烃类混合物中混合芳烃的方法,所述方法法中,设置抽余油反萃塔和反萃液精馏塔,可将贫溶剂中的c
9+
(碳数为9及以上)重芳烃脱除,从而净化贫溶剂,所用的净化剂为装置本身产生的抽余油,并不引入外来物质,另外,在萃取精馏塔和溶剂回收塔顶设置回流罐,定期排除
由原料带入并不断累积的水。所述方法操作简单,可充分发挥复合溶剂对原料的溶解性和芳烃选择性,提高分离芳烃的纯度和收率。
[0020]
本发明所述的复合溶剂优选由75~90质量%的环丁砜和10~25质量%的离子液体组成。
[0021]
本发明复合溶剂中,所述离子液体的阳离子可为式(ⅰ)所示的咪唑阳离子或式(ⅱ)所示的吡啶阳离子,式(ⅰ)中,r1和r2分别优选c1~c3的烷基,式(ⅱ)中,r4可处于吡啶环1~5位中的任意取代位,优选处于3位或4位;其中的r3优选c3~c4的烷基,r4优选c1~c2的烷基。
[0022]
优选地,所述的离子液体可为:1-乙基-3-甲基咪唑双氰胺[emim][dca]、1-乙基-3-甲基咪唑三氰基甲烷[emim][tcm]、1-丁基-4-甲基吡啶三氰基甲烷[bmpy][tcm]、1-丁基-3-甲基吡啶四氰基硼酸盐[3mbpy]b(cn)4,以及上述任意两种离子液体的混合物。
[0023]
本发明提供的从烃类混合物中萃取精馏分离芳烃的方法,包括将烃类混合物从中部引入萃取精馏塔,本发明所述的复合溶剂从上部引入萃取精馏塔,经过萃取精馏,非芳烃从塔顶排出,一部分作为抽余油产品排出装置,一部分返回萃取精馏塔上部,其余分成两部分:第一部分进入抽余油反萃塔下部作为反萃剂,第二部分进入反萃液精馏塔上部作为塔顶回流;富含芳烃的富溶剂从萃取精馏塔塔底排出进入溶剂回收塔中部,经过减压蒸馏,芳烃从溶剂回收塔塔顶排出,从塔底排出的贫溶剂大部分返回萃取精馏塔塔上部重新利用,小部分进入抽余油反萃塔上部,在抽余油反萃塔中,c
9+
重芳烃溶于抽余油形成的反萃液从塔顶排出进入反萃液精馏塔中部,脱除c
9+
重芳烃的净化贫溶剂从抽余油反萃塔排出返回溶剂回收塔下部,反萃液精馏塔中,经过蒸馏,c
9+
重芳烃从塔底排出,脱除c
9+
重芳烃的抽余油从塔顶排出,所述萃取精馏塔和溶剂回收塔均设有回流罐,定期将由原料带入的水排出系统。
[0024]
上述方法中,优选设置贫溶剂再生系统,即将从溶剂回收塔塔底排出的贫溶剂分出一部分引入贫溶剂再生系统脱除其中的固体杂质和c
9+
重非芳。
[0025]
所述贫溶剂再生系统包括耐高温过滤器和与其串连的罐式分相器,贫溶剂先进入耐高温过滤器进行过滤,滤渣从底部排出,滤液进入罐式分相器,经相分离,c
9+
重非芳从顶部排出,再生后的贫溶剂从底部排出返回溶剂回收塔下部。
[0026]
贫溶剂再生系统中耐高温过滤器可将贫溶剂中的机械杂质和固体聚合物脱除,得到滤渣,罐式分相器可将贫溶剂中的液相杂质
─c9+
重非芳脱除。所述的罐式分相器设置界位计,当c
9+
重非芳积累较多,罐内出现两相时,将上层c
9+
重非芳相由泵抽出,再生后的贫溶剂自罐底排出。所述罐式分相器的温度优选为140~170℃、压力优选0.1~0.2mpa。
[0027]
本发明方法为脱除贫溶剂中积累的c
9+
重芳烃,设置抽余油反萃塔和反萃液精馏塔对贫溶剂进行净化。所述的抽余油反萃塔用抽余油为溶剂萃取贫溶剂中的c
9+
重芳烃,使其从贫溶剂中脱除,得到净化贫溶剂,含有c
9+
重芳烃的反萃液在反萃液精馏塔中分离,c
9+
重芳烃排出,再生后的抽余油重新利用。优选地,抽余油反萃塔为多级逆流萃取塔或单级萃取液相混合器,优选多级逆流萃取塔。
[0028]
在萃取精馏塔中,进入萃取精馏塔的复合溶剂与烃类混合物的质量比,即溶剂比优选1~8、更优选5~8,萃取精馏塔的理论塔板数为40~90,回流比优选0.2~4、更优选0.2~2,复合溶剂入塔温度优选70~90℃,塔底温度优选110~170℃,塔顶压力优选0.1~
0.3mpa。
[0029]
所述溶剂回收塔的理论塔板数优选20~50,回流比优选0.5~2.0,塔顶压力优选0.01~0.06mpa,塔底温度优选155~190℃、更优选160~185℃。
[0030]
所述方法中,所述回流比为塔上部回流入塔物料与塔顶排出物料的质量比。
[0031]
抽余油反萃塔中,进入抽余油反萃塔的贫溶剂与从溶剂回收塔塔底排出的贫溶剂的质量比为0.1~3%,在抽余油反萃塔中,抽余油与进塔贫溶剂的质量比优选0.5~5:1、更优选1~4:1,反萃温度优选30~80℃,抽余油反萃塔的塔顶压力优选0.1~0.8mpa、更优选0.1~0.6mpa,理论塔板数优选1~10。
[0032]
所述反萃液精馏塔的理论塔板数优选5~20,塔顶压力优选0.1~0.15mpa,塔底温度优选70~180℃、更优选120~170℃,回流比为0~0.5、优选0.1~0.3。
[0033]
进入抽余油反萃塔的贫溶剂与从溶剂回收塔塔底排出的贫溶剂的质量比优选0.1~3%、更优选1~3%。
[0034]
引入贫溶剂再生系统的贫溶剂与从溶剂回收塔塔底排出的贫溶剂的质量比优选0.1~1%、更优选0.1~0.8%。
[0035]
本发明所述的烃类混合物为c6~c8的烃类,其中的芳烃含量为20~90质量%、优选50~90质量%。
[0036]
所述的c6~c8的烃类为裂解加氢汽油、凝析油、重整生成油的c6~c8馏分或焦油的粗苯馏分。
[0037]
本发明提供的复合溶剂和从烃类混合物中萃取精馏分离芳烃方法尤其适合从裂解加氢汽油c6~c8馏分中分离回收轻质芳烃
─
苯、甲苯和二甲苯。
[0038]
本发明中,萃取精馏所用的溶剂对被分离的两组分的选择性用相对挥发度(α)表征,其定义为:
[0039]
α=(y2/x2)/(y1/x1)
ꢀꢀ
(1)
[0040]
式(1)中,x1和x2分别表示组分1和组分2在液相中的质量分数,y1和y2分别表示组分1和组分2在气相中的质量分数。α值越大,表明萃取精馏溶剂的分离效果越好,可用较少的溶剂和较少的回流量得到纯度较高的目的产品。
[0041]
下面结合附图进一步说明本发明。
[0042]
图1中,烃类混合物原料由管线1经换热器101与贫溶剂换热后进入萃取精馏塔102的中部,复合溶剂由管线2从上部进入萃取精馏塔102,经萃取精馏,非芳烃从萃取精馏塔塔顶排出,进入冷凝器103冷凝,再进入回流罐104,在回流罐104中抽余油与水分离,水定期排放,由管线11排放出的抽余油一部分经管线3回流至萃取精馏塔102上部,一部分作为抽余油产品经管线14排出装置,其余分成两部分:第一部分经管线4进入抽余油反萃塔109的下部,第二部分经管线15进入反萃液精馏塔110上部,为反萃液精馏塔提供回流,可选地,反萃液精馏塔上部也可不引入抽余油,即不设回流。富含芳烃的富溶剂由萃取精馏塔塔底排出,经管线5从中部进入溶剂回收塔105,经减压蒸馏,混合芳烃由塔顶排出,进入冷凝器106冷凝,再进入回流罐107,在回流罐107中混合芳烃与水分离,水定期排放,从回流罐107排出的混合芳烃一部分由管线6返回至105塔,其余经管线7作为混合芳烃产品排出装置。贫溶剂由溶剂回收塔塔底排出,其中的大部分由管线8进入换热器换热后分成两路,大部分经管线2返回至萃取精馏塔102上部重新利用,小部分经管线10进入抽余油反萃塔109的上部。在抽
余油反萃塔中,贫溶剂中的c
9+
重芳烃被抽余油萃取,抽余油反萃塔109顶部排出溶有c
9+
重芳烃的抽余油,即反萃液,反萃液经管线12进入反萃液精馏塔110中部,底部排出的脱除c
9+
重芳烃的净化贫溶剂经管线16进入管线17返回溶剂回收塔下部。反萃液精馏塔110中,经过蒸馏,c
9+
重芳烃从塔釜排出装置,塔顶蒸出的脱除c
9+
重芳烃的再生抽余油经管线13返回,与从萃取精馏塔102塔顶排出的抽余油混合进入冷凝器103。将溶剂回收塔105塔底排出的贫溶剂分出一小部分由管线9送入耐高温过滤器108,过滤分出的滤渣从过滤器108底部排出,滤液经管线18送至罐式分相器111分离其中的c
9+
重非芳,分相得到的c
9+
重非芳定期从罐式分相器111顶部排放,脱除c
9+
重非芳再生后的贫溶剂经管线17返回溶剂回收塔105下部。
[0043]
下面通过实例进一步说明本发明,但本发明并不限于此。
[0044]
实例1
[0045]
以下实例考察本发明复合溶剂对芳烃/非芳烃的分离性能。
[0046]
将环丁砜和1-乙基-3-甲基咪唑双氰胺([emim][dca])按不同的质量比配成复合溶剂,将90质量%的苯和10质量%的乙基环己烷混合作为原料,加入配好的具有不同含量[emim][dca]的复合溶剂中得到混合溶液,复合溶剂与原料的质量比,即溶剂比为3.3。
[0047]
取10ml配制好的复合溶剂和原料的混合溶液,置于20ml密闭的样品瓶中,震荡摇匀,升温至100℃,静置30min,用气相色谱分析其气相组成。忽略因挥发进入气相对液相组成的影响,由式(1)计算乙基环己烷对苯的相对挥发度α,其中苯为组分1,乙基环己烷为组分2,不同[emim][dca]含量的复合溶剂的相对挥发度见表1。
[0048]
实例2
[0049]
按实例1的方法考察复合溶剂分离乙基环己烷和苯的性能,测定乙基环己烷对苯的相对挥发度,不同的是复合溶剂中的离子液体为1-丁基-4-甲基吡啶三氰基甲烷([bmpy][tcm]),不同[bmpy][tcm]含量的复合溶剂的相对挥发度见表1。
[0050]
实例3
[0051]
按实例1的方法考察复合溶剂分离乙基环己烷和苯的性能,测定乙基环己烷对苯的相对挥发度,不同的是复合溶剂中的离子液体为1-丁基-3-甲基吡啶四氰基硼酸盐([3mbpy]b(cn)4)与1-乙基-3-甲基咪唑双氰胺([emim][dca])的混合物,其中[3mbpy]b(cn)4与[emim][dca]的摩尔比为3:7。不同离子液体含量的复合溶剂的相对挥发度见表1。
[0052]
对比例1
[0053]
将90质量%的苯和10质量%的乙基环己烷混合作为原料,加入环丁砜得到混合溶液,环丁砜与原料的质量比,即溶剂比为3.3。
[0054]
取10ml混合溶液,置于20ml密闭的样品瓶中,震荡摇匀,升温至100℃,静置30min,用气相色谱分析其气相组成。忽略因挥发进入气相对液相组成的影响,由式(1)计算乙基环己烷对苯的相对挥发度α见表1。
[0055]
表1
[0056][0057]
由表1可知,在乙基环己烷/苯体系中,在溶剂比为3.3的条件下,以环丁砜为溶剂,乙基环己烷对苯的相对挥发度为1.506,在环丁砜中加入离子液体后得到的复合溶剂的乙基环己烷对苯的相对挥发度明显提高,说明复合溶剂的选择性高于环丁砜,但复合溶剂中离子液体的含量增至30质量%后,选择性下降。
[0058]
实例4
[0059]
本实例考察用抽余油反萃贫溶剂,脱除其中的c
9+
重芳烃的效果。
[0060]
将c6~c8正、异构烷烃及环烷烃配制成抽余油,其中正构烷烃含量为26.95质量%、异构烷烃含量为10.12质量%、环烷烃含量为62.93质量%;配制含5质量%c
9+
重芳烃的环丁砜/1-丁基-4-甲基吡啶三氰基甲烷([bmpy][tcm])复合溶剂,为含c
9+
重芳烃的贫溶剂,所述复合溶剂中环丁砜与[bmpy][tcm]的质量比为80:20。
[0061]
将抽余油按不同比例加入含c
9+
重芳烃的贫溶剂中,在40℃时进行一级反萃,达到液液相平衡后,分离油相,得到脱除c
9+
重芳烃后的净化复合溶剂,其中c
9+
重芳烃的含量见表2。
[0062]
表2
[0063][0064]
由表2可知,当抽余油/贫溶剂(质量比)大于2时,反萃后所得的净化复合溶剂中的c
9+
重芳烃的含量小于1质量%,说明用抽余油可有效脱除贫溶剂中的c
9+
重芳烃。
[0065]
实例5
[0066]
以组成为表3所示的裂解加氢汽油c6~c8馏分为原料,按图1的流程萃取精馏分离其中的烷烃和芳烃,使用的复合溶剂中含80质量%的环丁砜和20质量%的离子液体,所述离子液体为1-丁基-4-甲基吡啶三氰基甲烷([bmpy][tcm])。萃取精馏塔、溶剂回收塔、抽余
油反萃塔和反萃液精馏塔及罐式分相器的操作条件见表4,分离结果见表5。
[0067]
实例6
[0068]
按实例5的方法萃取精馏分离裂解加氢汽油c6~c8馏分中的芳烃,不同的是复合溶剂中的离子液体为1-乙基-3-甲基咪唑双氰胺,各塔操作条件见表4,分离结果见表5。
[0069]
实例7
[0070]
按实例5的方法萃取精馏分离裂解加氢汽油c6~c8馏分中的芳烃,不同的是复合溶剂中的离子液体为1-丁基-3-甲基吡啶四氰基硼酸盐([3mbpy]b(cn)4)与1-乙基-3-甲基咪唑双氰胺([emim][dca])的混合物,混合物中[3mbpy]b(cn)4/[emim][dca]的摩尔比为3:7,各塔操作条件见表4,分离结果见表5。
[0071]
对比例2
[0072]
以表3所示的裂解加氢汽油c6~c8馏分为原料,按现有的萃取精馏工艺分离原料中的芳烃,萃取精馏溶剂采用的溶剂为含水的环丁砜,溶剂中水含量为1质量%,萃取精馏工艺含萃取精馏塔、溶剂回收塔。贫溶剂通过减压闪蒸再生,再生贫溶剂为贫溶剂总量的0.2质量%,闪蒸罐操作温度为176℃,压力为0.02mpa,闪蒸罐底部不定期排渣。其它操作条件见表4,分离结果见表5。
[0073]
结果表明,本发明所述的复合溶剂较之对比例2的复合溶剂,在溶剂比较小及其它操作条件基本相同的情况下,分离所得的混合芳烃产品纯度、收率均较高。
[0074]
表3
[0075][0076]
表4
[0077][0078]
*贫溶剂总量为从溶剂回收塔底排出的贫溶剂量,**使用抽余油作为回流。
[0079]
表5
[0080]
项目实例5实例6实例7对比例2混合芳烃产品
ꢀꢀꢀꢀ
纯度,质量%99.9099.7099.8399.09收率,质量%99.999.899.799.2抽余油
ꢀꢀꢀꢀ
芳烃含量,质量%0.51.01.63.5