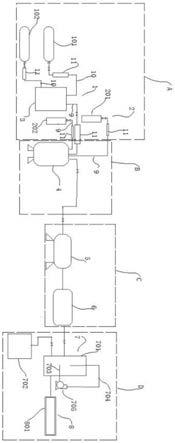
[0001]
本发明属于化工领域,具体涉及制备一氯频呐酮的工艺系统及工艺。
背景技术:[0002]
早在三十年代,国内外就有关于一氯频呐酮合成方法的探索。以频呐酮为原料,以氯仿、四氯化碳和二硫化碳为溶剂的室温氯化法,收率较低。频呐酮气相氯化收率有所提高,但产生大量的副产物。将频呐酮和氯在0℃下反应,反应过程不采用任何溶剂,此工艺的缺点是频呐酮转化率低,收率亦不理想。
[0003]
为了解决上述氯化过程中转化率和选择性偏低的问题,相继提出了改进方法。目前大多数工艺采用以甲醇为溶剂,频呐酮在-5~-10℃下与氯气反应,转化率控制在90%左右,反应结束后,加热蒸去频呐酮、溶剂甲醇以及氯化氢气体,反应选择性和一氯频呐酮含量均在97%以上,蒸出的甲醇套用,这是一种比较成熟的工艺。
[0004]
但是由于通入氯气时会出现局部浓度过大,导致生成二氯频呐酮杂质,其次,在蒸馏提纯时,物料会因物料停留时间过长,甲醇与氯化氢发生反应,产生较多水分,而水又会进一步与一氯频呐酮反应,影响产率及纯度。
技术实现要素:[0005]
为解决上述技术问题,本发明提供制备一氯频呐酮的工艺系统及工艺。
[0006]
具体技术方案如下:
[0007]
一种制备一氯频呐酮的工艺系统,其不同之处在于,所述制备一氯频呐酮的工艺系统包括:
[0008]
依次连接的加料单元、反应单元、纯化单元及后处理单元;
[0009]
所述加料单元包括气体加料装置及液体加料装置,所述气体加料装置包括气体混合釜、第一气体储存器及第二气体储存器,所述气体混合釜与所述第一气体储存器及第二气体储存器分别连接,所述液体加料装置包括第一液体储存瓶及第二液体储存瓶;
[0010]
所述反应单元包括反应釜,所述反应釜与所述气体混合釜、所述第一液体储存瓶及所述第二液体储存瓶分别连接;
[0011]
所述纯化单元包括依次连接的蒸馏釜及冷凝器;
[0012]
所述后处理单元包括与依次连接的气体吸收装置及气体回收装置,所述气体吸收装置与所述冷凝器连接。
[0013]
与现有技术相比,本发明的有益效果在于本系统可实现频呐酮与氯气的反应、提纯,并实现污染物的后续处理,不仅如此,在反应期间可以利用该装置通入氮气稀释氯气,避免氯气浓度过大,生成副产物。
[0014]
进一步,所述气体吸收装置包括吸收塔及与所述吸收塔分别连接的清水箱及抽水泵,所述抽水泵与所述吸收塔之间连接有进水管道与出水管道,所述进水管道连接于所述吸收塔的下端,所述出水管道连接于所述吸收塔的顶端。
[0015]
采取上述进一步技术方案的有益效果在于:通过此装置可以初步吸收盐酸,且循环吸收,可以获得高浓度盐酸与甲醇的混合液。
[0016]
进一步,所述气体回收装置包括与所述气体吸收装置连接的吸收管,所述吸收管内填充有无水氯化钙。
[0017]
采取上述进一步技术方案的有益效果在于:采取气体回收装置可以吸收残存在尾气中的有机杂质。
[0018]
进一步,所述第一液体储存瓶、所述第二液体储存瓶及所述气体混合釜通过原料输送管道与所述反应釜连接,所述原料输送管道上安装有流量计。
[0019]
进一步,所述第一气体储存器及第二气体储存器与所述气体混合釜通过气体输送管道连接,所述气体输送管道安装有流量计。
[0020]
进一步,所述第二气体储存器连接与所述气体混合釜下方连通。
[0021]
采取上述进一步技术方案的有益效果在于:第二气体储存器从气体混合釜连通,可以使氮气从下部通入,是气体混合更加均匀。
[0022]
进一步,所述反应釜及所述蒸馏釜采用搪瓷材料,所述冷凝器为石墨冷凝器。
[0023]
一种利用上述系统制备一氯频呐酮的工艺,其不同之处在于,所述制备一氯频呐酮的工艺包括:
[0024]
步骤s1:将频呐酮与甲醇混合后降温至0℃以下,得到液体混合原料;
[0025]
步骤s2:将包括氯气的反应气体通入所述液体混合原料,待氯气到达投入量时,停止通入反应气体,在0℃以下条件下反应,反应后,得到反应产物;
[0026]
步骤s3:往所述反应产物中投加脱氯剂,并将其混合,得到第一处理品;
[0027]
步骤s4:将第一处理品进行蒸馏后得到产物,蒸馏后产生的尾气中的可溶性物质去除;
[0028]
步骤s5:将未除净的小分子杂质去除。
[0029]
与现有技术相比,本发明的有益效果在于:采用脱氯剂降低反应液中的氯气含量。
[0030]
进一步,所述步骤s2中,反应过程中,随着反应时间推移,减小氯气通量,同时采用氮气将氯气稀释,通入所述液体混合原料的反应气体的流量为40m3/min~60m3/min;
[0031]
采取上述进一步技术方案的有益效果在于:可避免在频呐酮含量减小时,通入纯氯气导致局部浓度过大。
[0032]
进一步,在步骤s2过程中,一氯频呐酮的含量为理论生成量的40%~50%时,氯气的流量的减半,通入氮气稀释,此时氮气的流量与氯气的流量一样;一氯频呐酮的含量为理论生成量的75%~85%时,氯气的流量的再次减半,氮气的通入量增加至上次的1.5倍。
[0033]
采取上述进一步技术方案的有益效果在于:采用此调节方法,相较于传统的氮气稀释方式,此处更少,且设备要求更为简单,操作更为方便,以最小的调节次数,达到提高纯度及产率的目的。
[0034]
进一步,频呐酮与氯气物质的量之比为(2~5):1。
[0035]
采取上述进一步技术方案的有益效果在于:采用过量频呐酮进行反应,避免生成二氯频呐酮副产物。
[0036]
进一步,所述步骤s2中,反应温度为-3℃以下时,通反应气体,反应物维持在-5℃~0℃进行反应。
[0037]
进一步,在所述步骤s3中,所述脱氯剂为固体碳酸钠和/或碳酸钾。
[0038]
进一步,脱氯剂加入量为频呐酮投入质量的0.1%~2%,待反应结束后,投入脱氯剂后,搅拌5min~8min。
[0039]
采取上述进一步技术方案的有益效果在于:在降低与生成的氯化氢反应生成水的量前提下,降低液体中未反应的氯气含量,避免在后续升温脱溶剂过程中发生副反应,影响其产率及纯度。
[0040]
进一步,脱氯剂加入量为频呐酮投入质量的0.5%~1%,待反应结束后,投入脱氯剂后,搅拌6min~7min,采取上述进一步技术方案除氯效果更优。
[0041]
进一步,脱氯剂加入量为频呐酮投入质量的0.6%,待反应结束后,投入脱氯剂后,搅拌6min,采取上述进一步技术方案的除氯效果最优。
附图说明
[0042]
图1为本发明系统示意图;
[0043]
其中,加料单元-a,反应单元-b,纯化单元-c,后处理单元-d,气体加料装置-1,液体加料装置-2,气体混合釜-3,反应釜-4,蒸馏釜-5,冷凝器-6,气体吸收装置-7,气体回收装置-8,原料输送管道-9,气体输送管道-10,流量计-11,第一气体储存器-101,第二气体储存器-102,第一液体储存瓶-201,第二液体储存瓶-202,吸收塔-701,清水箱-702,进水管道-703,出水管道-704,抽水泵-705,吸收管-801。
具体实施方式
[0044]
以下结合附图对本发明的原理和特征进行描述,所举实例只用于解释本发明,并非用于限定本发明的范围。
[0045]
实施例1
[0046]
制备一氯频呐酮的工艺系统包括:
[0047]
依次连接的加料单元a、反应单元b、纯化单元c及后处理单元d;
[0048]
所述加料单元a包括:气体加料装置1及液体加料装置2,所述气体加料装置1包括气体混合釜3、第一气体储存器101及第二气体储存器102,所述气体混合釜3与所述第一气体储存器101及第二气体储存器102分别连接,所述液体加料装置2包括第一液体储存瓶201及第二液体储存瓶202;
[0049]
所述反应单元b包括反应釜4,所述反应釜4与所述气体混合釜3、所述第一液体储存瓶201及所述第二液体储存瓶202分别连接;
[0050]
所述纯化单元c包括依次连接的蒸馏釜5及冷凝器6;
[0051]
所述后处理单元d包括与依次连接的气体吸收装置7及气体回收装置8,所述气体吸收装置7与所述冷凝器6连接;
[0052]
所述气体吸收装置7包括吸收塔701及与所述吸收塔701分别连接的清水箱702及抽水泵705,所述抽水泵705与所述吸收塔701之间连接有进水管道703与出水管道704,所述进水管道703连接于所述吸收塔701的下端,所述出水管道704连接于所述吸收塔701的顶端。
[0053]
所述气体回收装置8包括与所述气体吸收装置7连接的吸收管801,所述吸收管内
填充有无水氯化钙。
[0054]
所述第一液体储存瓶201、所述第二液体储存瓶202及所述气体混合釜3通过原料输送管道9与所述反应釜4连接,所述原料输送管道9上安装有流量计11。
[0055]
所述第一气体储存器101及第二气体储存器102与所述气体混合釜3通过气体输送管道10连接,所述气体输送管道10安装有流量计11。
[0056]
所述第二气体储存器102连接与所述气体混合釜3下方连通。
[0057]
所述反应釜4及所述蒸馏釜5采用搪瓷材料,所述冷凝器6为石墨冷凝器。
[0058]
实施例2
[0059]
利用实施例1系统制备一氯频呐酮的工艺:
[0060]
频呐酮储存在第一液体储存瓶中,甲醇储存在第二液体储存瓶中,氯气储存在第一气体储存器中,氮气储存在第二气体储存器中。
[0061]
步骤s1:将频呐酮与甲醇加至反应釜中,混合后降温至-3℃时(通入反应釜的夹套的冷冻盐水降温),得到液体混合原料;
[0062]
步骤s2:将氯气与氮气通入气体混合釜中混合后得到反应气体,反应气体的流量为50m3/min,再通入液体混合原料,待氯气到达投入量时,停止通入反应气体,在0℃-5℃条件下反应,反应后,得到反应产物;
[0063]
反应过程中,不定时采样检测,一氯频呐酮的含量为理论生成量的50%时,氯气的流量的减半,通入氮气稀释,此时氮气的流量与氯气的流量一样;一氯频呐酮的含量为理论生成量的80%时,氯气的流量的再次减半,氮气的通入量增加至上次的1.5倍。
[0064]
步骤s3:往所述反应产物中投加固体碳酸钠脱氯剂,并将其混合,得到第一处理品,脱氯剂加入量为频呐酮投入质量的0.6%,待反应结束后,投入脱氯剂后,搅拌6min,期间温度控制在0℃以下。
[0065]
步骤s4:将第一处理品进行蒸馏后得到产物,蒸馏后产生的尾气中的可溶性物质通过吸收塔去除;
[0066]
步骤s5:将未除净的小分子杂质去除。
[0067]
频呐酮与氯气物质的量之比为2:1。
[0068]
实施例3
[0069]
按实施例2步骤制备一氯频呐酮,除此之外,频呐酮与氯气物质的量之比为3:1。
[0070]
实施例4
[0071]
按实施例2步骤制备一氯频呐酮,除此之外,频呐酮与氯气物质的量之比为4:1。
[0072]
实施例5
[0073]
按实施例2步骤制备一氯频呐酮,除此之外,频呐酮与氯气物质的量之比为5:1。
[0074]
实施例6
[0075]
按实施例2步骤制备一氯频呐酮,除此之外,脱氯剂加入量为频呐酮投入质量的0.5%。
[0076]
实施例7
[0077]
按实施例2步骤制备一氯频呐酮,除此之外,脱氯剂加入量为频呐酮投入质量的0.8%。
[0078]
实施例8
[0079]
按实施例2步骤制备一氯频呐酮,除此之外,脱氯剂加入量为频呐酮投入质量的1%。
[0080]
实施例9
[0081]
按实施例2步骤制备一氯频呐酮,除此之外,脱氯剂加入量为频呐酮投入质量的0.4%。
[0082]
实施例10
[0083]
按实施例2步骤制备一氯频呐酮,除此之外,脱氯剂加入量为频呐酮投入质量的1.8%。
[0084]
实施例11
[0085]
按实施例2步骤制备一氯频呐酮,除此之外,步骤s3中,加入脱氯剂后,搅拌时间为7min。
[0086]
实施例12
[0087]
按实施例2步骤制备一氯频呐酮,除此之外,步骤s3中,加入脱氯剂后,搅拌时间为8min。
[0088]
实施例13
[0089]
按实施例2步骤制备一氯频呐酮,除此之外,步骤s3中,加入脱氯剂后,搅拌时间为3min。
[0090]
对比例1
[0091]
按实施例2步骤制备一氯频呐酮,除此之外,步骤s2过程中,不采取氮气稀释氯气。
[0092]
对比例2
[0093]
按实施例2步骤制备一氯频呐酮,除此之外,不进行步骤s3,直接将反应后的产物进行蒸馏。
[0094]
实施例2~13及对比例1~2的产率(按氯气可生成理论产值计算)及纯度如表1所示。
[0095]
表1实施例及对比例的产率及纯度统计
[0096][0097][0098]
从上表可以看出,实施例与对比例1相比,相较于未用氮气稀释,采用氮气稀释,其产率与纯度更好。
[0099]
实施例与对比例2相比,相较于未使用脱氯剂的,本发明技术方案,其产率及纯度更加优良。
[0100]
不仅如此,本发明研发人员采用简便的氮气稀释氯气的方式,以此提高产率及纯度,再进一步通过控制脱氯剂的投量与反应时间增加纯度及产率。
[0101]
至于,频呐酮与氯气的摩尔比,虽然一定程度上,比值越大,其产率与纯度越大且到达4:1时,效果达到最优。
[0102]
以上所述仅为本发明的较佳实施例,并不用以限制本发明,凡在本发明的精神和原则之内,所作的任何修改、等同替换、改进等,均应包含在本发明的保护范围之内。