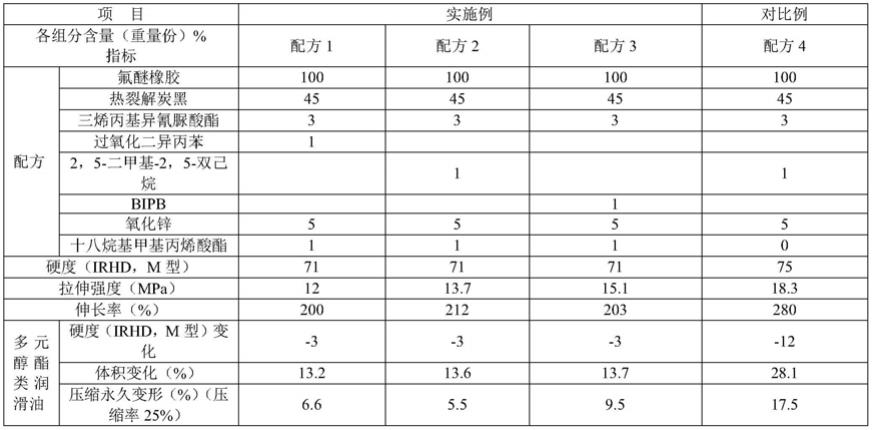
[0001]
本发明属于橡胶技术领域,特别涉及一种氟橡胶材料及其制备方法。
背景技术:[0002]
橡胶的耐油性,是指橡胶经油料浸泡后的性能衰减的能力,当橡胶制品与各种油料长期接触时,一方面,油料能渗透到橡胶中,使之膨胀或体积增大;另一方面,油介质可以从橡胶中抽出可溶性的配合剂,导致橡胶收缩或体积减小。通常溶胀随橡胶与油介质接触时间的增加而增大,直到油液不在被吸收为止,而后体积膨胀保持稳定,导致原本排列紧密的网状交联结构被扩张,橡胶制品的性能急剧下降,造成密封失效。
[0003]
某型飞机发动机需长期在零下几十度的低温或高达几百度的高温环境中使用,其油液系统的油料介质为多元醇酯类润滑油,为了防止多元醇酯类润滑油的氧化降解,而且能够对接触的金属部件提供一定的防腐能力,防止重金属元素,尤其是铜扩散到润滑油中,催化其氧化分解,多元醇酯类润滑油中常添加一些苯三唑衍生物类抑制剂,这些抑制剂为小分子活性基团,呈碱性,对密封作用的氟橡胶分子主链构成侵蚀,促进其主链脱氟化氢过程,从而形成不饱和键,导致主链降解,最终造成橡胶性能恶化,最终造成橡胶密封失效。
[0004]
为了适应航空发动机油液系统工作的要求,保证使用部位具有良好的密封性,需研究一种具有较高硬度、性能优异且成本低,环保的耐油氟橡胶材料,尤其是适用于-50℃~200℃温度下,而且在含有腐蚀抑制剂的多元醇酯类润滑油中能够长期使用的氟橡胶材料。
技术实现要素:[0005]
针对现有橡胶在多元醇酯类润滑油中无法长期使用的问题,本发明所要解决的第一个技术问题是提供一种氟橡胶材料。该氟橡胶材料,原料包括以下组分,以质量份数计为:橡胶基料90~110份,增强剂40~50份,硫化剂2~4份,硫化助剂1~2份,吸酸剂5~10份,硫化促进剂1~2份。
[0006]
进一步地,所述橡胶基料为flt
-ⅰ
型氟醚橡胶。
[0007]
进一步地,所述增强剂为热裂解炭黑。
[0008]
进一步地,所述硫化剂为三烯丙基异氰脲酸酯。
[0009]
进一步地,所述硫化助剂为过氧化二异丙苯、2,5-二甲基-2,5-双己烷或双叔丁基过氧异丙基苯(bipb)中至少一种。
[0010]
进一步地,所述吸酸剂为氧化锌、氧化镁、氢氧化钙或碳酸钙中至少一种。
[0011]
进一步地,所述硫化促进剂为十八烷基甲基丙烯酸酯、亚磷酸三(十八烷基)酯、三氯乙酸十八烷基酯或十八烷酸十八烷基酯中至少一种。
[0012]
本发明所要解决的第二个技术问题是提供一种氟橡胶材料的制备方法,包括以下步骤:将橡胶基料薄通后,加入其他原料,然后进行混炼,硫化,即得。
[0013]
进一步地,所述氟橡胶材料的制备方法,混炼过程中,混炼双辊温度25~80℃,一
次投料量10kg以下,辊距5~10mm,辊速比1:1~1.5。
[0014]
进一步地,所述氟橡胶材料的制备方法,混炼过程中,橡胶基料薄通5~15次,完成其他原料投料后再薄通5~15次,打三角包10~20次,整个混炼时间10~30分钟,最后出片厚度5~10mm。
[0015]
进一步地,所述氟橡胶材料的制备方法,硫化过程中,一段硫化温度150~175℃,时间10~50min,模具单位面积压力为10~20mpa。
[0016]
进一步地,所述氟橡胶材料的制备方法,硫化过程中,二段硫化是在持续鼓风下,升温至190~230℃,保温3~8h,随炉冷却至40℃以下。
[0017]
本发明的有益效果
[0018]
本发明提供一种氟橡胶材料及其制备方法,以橡胶基料、增强剂、硫化剂、硫化助剂、吸酸剂、硫化促进剂等混炼、硫化而成。所制备的氟橡胶材料各组分及含量配比,是通过大量创造性试验确定的,在氟橡胶不变的基础上,通过添加了硫化促进剂,改变了配方的硫化体系,提高了胶料的硫化程度,增加了分子结构的稳定性。同时调整了增强填料的配比,降低了胶料的刚性并同时提高其弹性。该氟橡胶材料所用原料成本低,环保,各组分及含量配比使所制备的氟橡胶材料硬度较高,在高温时,该氟橡胶材料长期处于多元醇酯类润滑油中硬度变化不大,体积变化较小,压缩变形性变小,有利于其在多元醇酯类润滑油中长期使用;特别适用于在-50℃~200℃温度下,含有腐蚀抑制剂的多元醇酯类润滑油中长期使用。
具体实施方式
[0019]
本发明针对现有橡胶在多元醇酯类润滑油中无法长期使用的问题,提出一种氟橡胶材料及其制备方法。该氟橡胶材料,原料包括以下组分,以质量份数计为:橡胶基料90~110份,增强剂40~50份,硫化剂2~4份,硫化助剂1~2份,吸酸剂5~10份,硫化促进剂1~2份。
[0020]
上述氟橡胶材料的制备方法,包括以下步骤:
[0021]
(1)首先将双辊炼胶机双辊温度调为25~80℃,一次投料量10kg以下,辊距5~10mm,辊速比为1:1~1.5,然后将橡胶基料在双辊炼胶机中薄通5~15次,形成均匀的包辊料,调节辊距以保持少量堆积胶,依次加入其他辅料:增强剂、硫化剂、硫化助剂、吸酸剂、硫化促进剂按成分配比配料;完成投料后再薄通5~15次,打三角包10~20次,使基料和辅料混合均匀,混炼过程要尽可能快,防止过炼和粘辊。将混合物反复投入并通过炼胶机的双辊,在反复混炼的过程中应逐渐缩短双辊间距,以达到使各组分混合均匀的目的,整个混炼过程为10~30分钟,最后调节辊距出片,厚度控制为5~10mm,最终获得混合均匀的混炼胶。
[0022]
(2)将混炼胶放入模具中,将模具放入平板硫化机中进行一段硫化,温度为150~175℃,时间10~50min,模具单位面积压力为10~20mpa;将一段硫化后的产品脱模后进行二段硫化:让产品在不受力的状态下放置于电热鼓风干燥箱内,升温至190~230℃,保温3~8h,完成后应继续保持鼓风的情况下随炉冷却至40℃以下,最终制成氟橡胶材料。
[0023]
上述氟橡胶材料,所述橡胶基料为flt
-ⅰ
型氟醚橡胶。
[0024]
上述氟橡胶材料,所述增强剂为热裂解炭黑。
[0025]
上述氟橡胶材料,所述硫化剂为三烯丙基异氰脲酸酯。
[0026]
上述氟橡胶材料,所述硫化助剂为过氧化二异丙苯、2,5-二甲基-2,5-双己烷或双叔丁基过氧异丙基苯中(bipb)至少一种。
[0027]
上述氟橡胶材料,所述吸酸剂为氧化锌、氧化镁、氢氧化钙或碳酸钙中至少一种。
[0028]
上述氟橡胶材料,所述硫化促进剂为十八烷基甲基丙烯酸酯、亚磷酸三(十八烷基)酯、三氯乙酸十八烷基酯或十八烷酸十八烷基酯中至少一种。
[0029]
在本发明中,若非特指,所有的设备及原料等均可从市场购得或是本行业常用的。
[0030]
为了获得优异的耐温、耐介质和耐强氧化剂的性能,上述氟橡胶材料,选用flt
-ⅰ
型氟醚橡胶为橡胶基料。
[0031]
为了提高硫化程度,稳定分子结构,上述氟橡胶材料,所述硫化促进剂应为1~2份;优选的,所述硫化促进剂为十八烷基甲基丙烯酸酯、亚磷酸三(十八烷基)酯、三氯乙酸十八烷基酯或十八烷酸十八烷基酯中至少一种。
[0032]
为了降低氟橡胶材料的刚性并同时提高其弹性,上述氟橡胶材料,所述增强剂为40~50份;优选的,所述增强剂为热裂解炭黑。
[0033]
为了确保橡胶制品的硫化程度,加快低分子化合物的释放,从而提高橡胶的力学性能和耐久性,上述氟橡胶材料的制备方法步骤(2)中,采用分段硫化。
[0034]
下面通过具体实施例对本发明进行具体描述。有必要在此指出的是以下实施例只用于对本发明进行进一步说明,不能理解为对发明保护范围的限制,本领域技术人员可根据上述本发明做出一些非本质的改进和调整。
[0035]
实施例1
[0036]
(1)首先将双辊炼胶机双辊温度调为50℃,采用5mm辊距,一次投料量5kg,辊速比为1:1.25,按照表1中的配方1,将flt
-ⅰ
型氟醚橡胶基料100份在双辊炼胶机中薄通10次,形成均匀的包辊料,调节辊距以保持少量堆积胶,依次加入其他辅料:热裂解炭黑45份、三烯丙基异氰脲酸酯3份、过氧化二异丙苯1份、氧化锌5份、十八烷基甲基丙烯酸酯1份;完成投料后通过薄通10次,打三角包15次,使基料和辅料混合均匀,混炼过程要尽可能快,防止过炼和粘辊。将混合物反复投入并通过炼胶机的双辊,在反复混炼的过程中应逐渐缩短双辊间距,以达到使各组分混合均匀的目的,整个混炼过程为15分钟,最后调节辊距出片,厚度控制为6mm,最终获得混合均匀的混炼胶。
[0037]
(2)将混炼胶放入模具中,将模具放入平板硫化机中进行一段硫化,温度为160℃,时间15min,模具单位面积压力为10mpa;将一段硫化后的产品脱模后进行二段硫化:让产品在不受力的状态下放置于电热鼓风干燥箱内,升温至200℃,保温3h,完成后应保持鼓风的情况下随炉冷却至40℃以下,最终制成氟橡胶材料。
[0038]
实施例2
[0039]
(1)首先将双辊炼胶机双辊温度调为50℃,采用5mm辊距,一次投料量5kg,辊速比为1:1.25,按照表1中的配方2,将flt
-ⅰ
型氟醚橡胶基料100份在双辊炼胶机中薄通10次,形成均匀的包辊料,调节辊距以保持少量堆积胶,依次加入其他辅料:热裂解炭黑45份、三烯丙基异氰脲酸酯3份、2,5-二甲基-2,5-双己烷1份、氧化锌5份、十八烷基甲基丙烯酸酯1份;完成投料后再薄通10次,打三角包15次,使基料和辅料混合均匀,混炼过程要尽可能快,防止过炼和粘辊。将混合物反复投入并通过炼胶机的双辊,在反复混炼的过程中应逐渐缩短双辊间距,以达到使各组分混合均匀的目的,整个混炼过程为15分钟,最后调节辊距出片,
厚度控制为6mm,最终获得混合均匀的混炼胶。
[0040]
(2)将混炼胶放入模具中,将模具放入平板硫化机中进行一段硫化,温度为160℃,时间15min,模具单位面积压力为10mpa;将一段硫化后的产品脱模后进行二段硫化:让产品在不受力的状态下放置于电热鼓风干燥箱内,升温至200℃,保温3h,完成后应继续保持鼓风的情况下随炉冷却至40℃以下,最终制成氟橡胶材料。
[0041]
实施例3
[0042]
(1)首先将双辊炼胶机双辊温度调为50℃,采用5mm辊距,一次投料量5kg,辊速比为1:1.25,按照表1中的配方3,将flt
-ⅰ
型氟醚橡胶基料100份在双辊炼胶机中薄通10次,形成均匀的包辊料,调节辊距以保持少量堆积胶,依次加入其他辅料:热裂解炭黑45份、三烯丙基异氰脲酸酯3份、bipb 1份、氧化锌5份、十八烷基甲基丙烯酸酯1份;完成投料后再薄通10次,打三角包15次,使基料和辅料混合均匀,混炼过程要尽可能快,防止过炼和粘辊。将混合物反复投入并通过炼胶机的双辊,在反复混炼的过程中应逐渐缩短双辊间距,以达到使各组分混合均匀的目的,整个混炼过程为15分钟,最后调节辊距出片,厚度控制为6mm,最终获得混合均匀的混炼胶。
[0043]
(2)将混炼胶放入模具中,将模具放入平板硫化机中进行一段硫化,温度为160℃,时间15min,模具单位面积压力为10mpa;将一段硫化后的产品脱模后进行二段硫化:让产品在不受力的状态下放置于电热鼓风干燥箱内,升温至200℃,保温3h,完成后应继续保持鼓风的情况下随炉冷却至40℃以下,最终制成氟橡胶材料。
[0044]
对比例1
[0045]
(1)首先将双辊炼胶机双辊温度调为50℃,采用5mm辊距,一次投料量5kg,辊速比为1:1.25,按照表1中的配方4,将flt
-ⅰ
型氟醚橡胶基料100份在双辊炼胶机中薄通10次,形成均匀的包辊料,调节辊距以保持少量堆积胶,依次加入其他辅料:热裂解炭黑45份、三烯丙基异氰脲酸酯3份、2,5-二甲基-2,5-双己烷1份、氧化锌5份;完成投料后再薄通10次,打三角包15次,使基料和辅料混合均匀,混炼过程要尽可能快,防止过炼和粘辊。将混合物反复投入并通过炼胶机的双辊,在反复混炼的过程中应逐渐缩短双辊间距,以达到使各组分混合均匀的目的,整个混炼过程为15分钟,最后调节辊距出片,厚度控制为6mm,最终获得混合均匀的混炼胶。
[0046]
(2)将混炼胶放入模具中,将模具放入平板硫化机中进行一段硫化,温度为160℃,时间15min,模具单位面积压力为10mpa;将一段硫化后的产品脱模后进行二段硫化:让产品在不受力的状态下放置于电热鼓风干燥箱内,升温至200℃,保温3h。完成后应继续保持鼓风的情况下随炉冷却至40℃以下,最终制成氟橡胶材料。
[0047]
将上述实施例1~3及对比例1中所制备的氟橡胶材料按标准测试样条制样,并测试力学性能,同时将样条置于200℃的多元醇酯类润滑油中22h,测试所制备的氟橡胶材料的耐醇酯类润滑油性能及变化,测试结果见表1。
[0048]
从表1中可以看出,实施例1~3所制备的氟橡胶材料的硬度均在71(irhd,m型),经过多元醇酯类润滑油长期浸泡后,其硬度降低3,变化不大,同时体积分别增大了13.2%、13.6%、13.7%,体积变化较小,说明油液被橡胶吸收较少;虽然实施例1、2、3拉伸强度分别降低为12mpa、13.7mpa、15.1mpa,但在200℃的多元醇酯类润滑油中浸泡22h,压缩永久变形性能从17.2%降低到5.5~9.5%。而从对比例1中可以看出,通过对比例1的配方所制备的
氟橡胶材料硬度降低了12,体积增大了28.1%,压缩永久变形为17.5%,和本发明相比,对比例1硬度变化大,体积变化较大,说明油液被橡胶吸收较多,同时与本发明相比,对比例1的压缩永久变形性能较差。
[0049]
表1实施例1~3及对比例1的配方组成及性能
[0050]