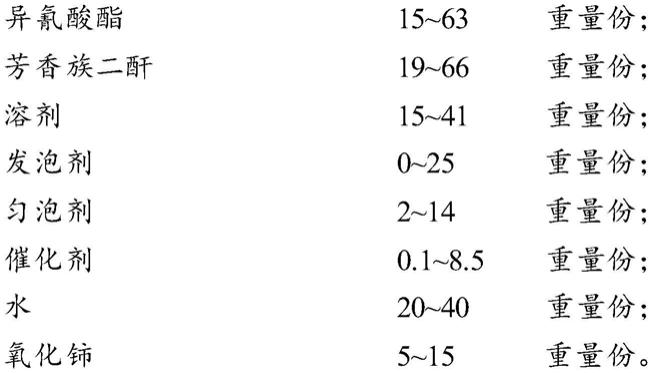
[0001]
本发明属于聚酰亚胺泡沫材料技术领域,涉及一种耐辐照聚酰亚胺泡沫材料及其制备方法、应用,尤其涉及一种船用耐辐照聚酰亚胺泡沫材料及其制备方法、应用。
背景技术:[0002]
聚酰亚胺泡沫材料是一种轻质多孔材料,具有轻质、优异的耐高低温、隔热、吸音降噪、阻燃、绝缘等性能。高性能的聚酰亚胺泡沫长期可耐250~300℃,短时可耐400~500℃,是有机聚合物中热稳定性最好的材料之一。高性能耐辐照聚酰亚胺泡沫材料还可耐极低温,在-269℃的液态氦中不发生脆裂等优点,自20世纪60年代被成功研制以来,凭借其在耐高低温、阻燃防火、吸声降噪、耐氧化、耐水解等性能方面的优异表现,引起了高分子材料领域内的广泛关注,由此也推动了聚酰亚胺泡沫材料行业的迅速发展。近年来在军工国防、航空航天、船舶航舰、轨道交通、电子和新能源等领域有着广泛的应用,据报道,目前已有超过15个国家将聚酰亚胺泡沫材料作为绝热保温材料应用于其海防舰船体系中,其中美国国防部已将聚酰亚胺泡沫指定为其海军船舶绝热保温专用材料。除此之外,聚酰亚胺泡沫材料在民用船舶体系中,如豪华游轮、快艇、液化天然气船上也有广泛的应用。
[0003]
随着石油资源的不断枯竭和环保要求的不断提高,从技术和经济的角度看,不依赖化石燃料、零污染排放、超长续航能力的核动力船舶将成为未来船舶的发展方向。由于反应堆的裂变,核动力船舶上的原子能设备存在大量的高能辐射。聚酰亚胺泡沫作为船舶重要的绝热隔声材料,在船舶内饰材料中占比超过40%,广泛应用于船舶的壳体、舱壁、舱顶、冷却水管线、高温蒸汽管线等众多场所。倘若未经任何改性的聚酰亚胺泡沫绝热隔声材料长期受到核辐射,将导致其机械性能、隔热性能、吸声性能等大幅下降,因此无法实现对船舶内设备与人员的有效隔离与保护;更严重的情况可能导致该材料失效,造成热失控而威胁船舶和人员的安全。由此可见,聚酰亚胺泡沫作为船舶专用绝热隔声材料,提升其耐辐照性能显得至关重要。
[0004]
现有技术中也公开了一些相关研究,如专利us6608319b2选用碳化钨、碳化硼作为γ射线的屏蔽材料,在硫酸钡、金刚石和靶绒等协同作用下制备了具有良好耐辐照性能的硫化硅橡胶,但强度低,且工艺繁琐。而专利cn1970636a选用苯基硅橡胶制备具有耐辐照性能的橡胶,但是其回弹性和机械强度明显降低。在已有报道的耐辐照材料中均含有铅或苯基等对环境存在潜在污染的物质,且其生产成本高、耐辐照性能有限。因此选用传统的铅、钨、钡等重金属添加剂,以及通过在主链或侧链引入苯基等方式无法满足如今该材料对耐辐照性能的需求以及应用领域对环保的要求。
[0005]
因此,如何提升聚酰亚胺泡沫的耐辐照性能,使其能够用作核动力船舶绝热隔声材料,解决上述实际应用中存在的问题,以提升船舶的安全性以及满足环保要求具有非常重要的意义,也是诸多研发型生产厂商以及一线研究人员广为关注的焦点之一。
技术实现要素:[0006]
有鉴于此,本发明要解决的技术问题在于提供一种耐辐照聚酰亚胺泡沫材料及其制备方法、应用,特别是一种船用耐辐照聚酰亚胺泡沫材料,本发明提供的耐辐照聚酰亚胺泡沫材料中复合有对核辐射具有阻挡屏蔽作用且环境友好的氧化铈,可有效提高船用聚酰亚胺泡沫材料的耐辐照性能,对提升核动力船舶安全性能和满足环保要求具有重要借鉴意义;而且工艺简单、易于控制,有利于实现工业连续化生产。
[0007]
本发明提供了一种耐辐照聚酰亚胺泡沫材料,所述耐辐照聚酰亚胺泡沫材料中含有氧化铈颗粒;
[0008]
所述耐辐照聚酰亚胺泡沫材料具有多孔结构;
[0009]
所述氧化铈颗粒复合在所述聚酰亚胺泡沫中。
[0010]
优选的,所述氧化铈颗粒的粒径为0.5~4μm;
[0011]
所述氧化铈颗粒的质量含量为5%~15%;
[0012]
所述多孔结构的孔径为100~700μm;
[0013]
所述氧化铈与聚酰亚胺的结合方式包括化学键键合;
[0014]
所述耐辐照聚酰亚胺泡沫材料包括船用耐辐照聚酰亚胺泡沫材料。
[0015]
优选的,所述耐辐照聚酰亚胺泡沫材料的开孔率为80%~99%;
[0016]
所述耐辐照聚酰亚胺泡沫材料的密度为9~12kg/m3;
[0017]
所述氧化铈颗粒填充在所述泡孔间隙中、位于泡孔中和依附在泡孔的孔壁上的一种或多种;
[0018]
所述氧化铈中的铈离子与聚酰亚胺结构中的酰亚胺环中的n和/或o原子通过配位键键合;
[0019]
所述耐辐照聚酰亚胺泡沫材料中还包括匀泡剂。
[0020]
本发明提供了一种耐辐照聚酰亚胺泡沫材料,按原料质量分数计,包括:
[0021][0022]
优选的,所述异氰酸酯包括pm-200、ne-466、pm-400、pm-700、8122、8214和pm-8223中的一种或多种;
[0023]
所述芳香族二酐包括btda、pmda和dsda中的一种或多种;
[0024]
所述溶剂包括dmso、dmf和dmac中的一种或多种;
[0025]
所述催化剂包括金属催化剂和/或胺类催化剂。
[0026]
优选的,所述异氰酸酯的异氰酸根含量为28%~35%;
[0027]
所述发泡剂包括丙酮、水、甲醇、乙醇和2-丁氧基乙醇中的一种或多种;
[0028]
所述匀泡剂包括聚醚改性硅油、硅酮类硅油和水溶性硅油的一种或多种;
[0029]
所述催化剂包括二月桂酸二丁基锡、辛酸亚锡、异辛酸铋、n,n-二甲基环己胺、n,n,n',n'-四甲基亚烷基二胺和n,n'-二乙基哌嗪中的一种或多种。
[0030]
本发明提供了一种如上述技术方案任意一项所述的耐辐照聚酰亚胺泡沫材料或上述技术方案任意一项所述耐辐照聚酰亚胺泡沫材料的制备方法,包括以下步骤:
[0031]
1)将芳香族二酐和溶剂进行混合后,得到第一溶液;
[0032]
将氧化铈、水、发泡剂、匀泡剂和催化剂再次混合后,得到第二溶液;
[0033]
2)将上述步骤得到的第一溶液和第二溶液预混合,再与异氰酸酯经过最后混合,然后在模具中经过发泡成型,最后固化得到耐辐照聚酰亚胺泡沫材料。
[0034]
优选的,所述混合的方式包括加热搅拌;
[0035]
所述混合的温度为60~80℃;
[0036]
所述混合的转速为300~500r/min;
[0037]
所述混合的时间为6~12h;
[0038]
所述再次混合的方式包括超声混合;
[0039]
所述超声混合的功率为100~150w;
[0040]
所述再次混合的时间为10~15min。
[0041]
优选的,所述最后混合的方式包括高速搅拌混合;
[0042]
所述最后混合的转速为1000~3000r/min;
[0043]
所述最后混合的时间为15~30s;
[0044]
所述发泡成型的时间为15~20min;
[0045]
所述固化的温度为200~300℃;
[0046]
所述固化的时间为4~8h。
[0047]
本发明还提供了上述技术方案任意一项所述的耐辐照聚酰亚胺泡沫材料、上述技术方案任意一项所述耐辐照聚酰亚胺泡沫材料或上述技术方案任意一项所述的制备方法所制备的耐辐照聚酰亚胺泡沫材料在船舶领域的应用。
[0048]
本发明提供了一种耐辐照聚酰亚胺泡沫材料,所述耐辐照聚酰亚胺泡沫材料中含有氧化铈颗粒;所述耐辐照聚酰亚胺泡沫材料具有多孔结构;所述氧化铈颗粒复合在所述聚酰亚胺泡沫中。与现有技术相比,本发明针对现有的耐辐照材料,存在强度低,且工艺繁琐,又或者是回弹性和机械强度明显降低等问题。而且已报道的耐辐照材料中均含有铅或苯基等对环境存在潜在污染的物质,且其生产成本高、耐辐照性能有限,同时选用传统的铅、钨、钡等重金属添加剂,以及通过在主链或侧链引入苯基等方式无法满足如今该材料对耐辐照性能的需求以及应用领域对环保的要求的缺陷。
[0049]
本发明特别设计了一种耐辐照聚酰亚胺泡沫材料,该耐辐照聚酰亚胺泡沫材料中含有氧化铈颗粒,而且氧化铈颗粒以特定的形式复合在多孔的聚酰亚胺泡沫中。本发明提供的聚酰亚胺泡沫材料中含有对核辐射具有阻挡屏蔽作用且环境友好的纳米级的氧化铈颗粒,稀土离子的外层空轨道与酰亚胺环中n和/或o原子提供的孤对电子或不定域电子有效结合形成键合作用,实现了物理复合和化学键合相结合的特定复合形式,进而有效提升了聚酰亚胺泡沫材料的耐辐照性能。与具有化学毒性的铅、钨、钡等重金属传统屏蔽材料相
比,氧化铈不仅能够有效提升聚酰亚胺泡沫材料的耐辐照性能,而且对环境无任何威胁。氧化铈之所以能够有效提升材料的耐辐照性能,主要在于当辐射在穿过氧化铈时,会发生能够吸收或者散射x射线、γ射线等辐射的光电效应、康普顿效应以及电子对效应,从而使其具有阻挡屏蔽辐射的作用。稀土离子的外层空轨道与酰亚胺环中n和o原子提供的孤对电子或不定域电子有效结合形成的稳定键合作用,可有效保证氧化铈在聚酰亚胺泡沫体系中均匀分散。
[0050]
而且本发明提供的耐辐照聚酰亚胺泡沫材料制备工艺简单、易于控制,有利于实现工业连续化生产,本发明可有效的提高船用聚酰亚胺泡沫材料的耐辐照性能,对提升核动力船舶安全性能和满足环保要求来说,具有重要的借鉴意义。
[0051]
实验结果表明,本发明提供的耐辐照聚酰亚胺泡沫在辐照过后,力学性能受到的影响较小,拉伸强度、撕裂强度、压缩强度有小幅度衰减,但明显优于辐照过后未加氧化铈颗粒的聚酰亚胺泡沫。氧化铈颗粒的加入提高了聚酰亚胺泡沫的耐辐照性能。
具体实施方式
[0052]
为了进一步理解本发明,下面结合实施例对本发明优选实施方案进行描述,但是应当理解,这些描述只是为了进一步说明本发明的特征和优点,而不是对发明权利要求的限制。
[0053]
本发明所有原料,对其来源没有特别限制,在市场上购买的或按照本领域技术人员熟知的常规方法制备的即可。
[0054]
本发明所有原料,对其纯度没有特别限制,本发明优选采用分析纯或船用聚酰亚胺泡沫材料制备领域常规的纯度要求。
[0055]
本发明所有原料,其牌号和简称均属于本领域常规牌号和简称,每个牌号和简称在其相关用途的领域内均是清楚明确的,本领域技术人员根据牌号、简称以及相应的用途,能够从市售中购买得到或常规方法制备得到。
[0056]
本发明提供了一种耐辐照聚酰亚胺泡沫材料,所述耐辐照聚酰亚胺泡沫材料中含有氧化铈颗粒;
[0057]
所述耐辐照聚酰亚胺泡沫材料具有多孔结构;
[0058]
所述氧化铈颗粒复合在所述聚酰亚胺泡沫中。
[0059]
本发明原则上对所述氧化铈颗粒的粒径没有特别限制,本领域技术人员可以根据实际生产情况、应用要求以及质量控制进行选择和调整,本发明为更好的提高聚酰亚胺泡沫材料的耐辐照性能,保证材料主体的结构,保证泡沫材料原有的性能,减少辐照后的性能降低,所述氧化铈颗粒的粒径优选为0.5~4μm,更优选为0.6~3μm,更优选为0.7~2μm,更优选为0.8~1μm。本发明所述氧化铈颗粒优选为通过超声剪切后,得到的氧化铈颗粒,即纳米级氧化铈颗粒。
[0060]
本发明原则上对所述氧化铈颗粒的质量含量没有特别限制,本领域技术人员可以根据实际生产情况、应用要求以及质量控制进行选择和调整,本发明为更好的提高聚酰亚胺泡沫材料的耐辐照性能,保证材料主体的结构,保证泡沫材料原有的性能,减少辐照后的性能降低,所述氧化铈颗粒的质量含量优选为5%~15%,更优选为7%~13%,更优选为9%~11%。
[0061]
本发明原则上对所述氧化铈与聚酰亚胺结合的具体方式没有特别限制,本领域技术人员可以根据实际生产情况、应用要求以及质量控制进行选择和调整,本发明为更好的提高聚酰亚胺泡沫材料的耐辐照性能,保证材料主体的结构,保证泡沫材料原有的性能,减少辐照后的性能降低,所述氧化铈与聚酰亚胺的结合方式优选包括化学键键合。具体的,所述氧化铈中的铈离子与聚酰亚胺结构中的酰亚胺环中的n和/或o原子优选通过配位键键合。在本发明中,铈可以分别和酰亚胺环中的n或o单独发生配位,也可以跟两者同时发生配位,形成单齿配位和/或多齿配位。
[0062]
本发明原则上对所述具有多孔结构的耐辐照聚酰亚胺泡沫材料的具体孔径大小没有特别限制,本领域技术人员可以根据实际生产情况、应用要求以及质量控制进行选择和调整,本发明为更好的提高聚酰亚胺泡沫材料的耐辐照性能,保证材料主体的结构,保证泡沫材料原有的性能,减少辐照后的性能降低,所述多孔结构的孔径优选为100~700μm,更优选为200~600μm,更优选为300~500μm。
[0063]
本发明原则上对所述耐辐照聚酰亚胺泡沫材料的开孔率没有特别限制,本领域技术人员可以根据实际生产情况、应用要求以及质量控制进行选择和调整,本发明为更好的提高聚酰亚胺泡沫材料的耐辐照性能,保证材料主体的结构,保证泡沫材料原有的性能,减少辐照后的性能降低,所述耐辐照聚酰亚胺泡沫材料的开孔率优选为80%~99%,更优选为84%~95%,更优选为88%~91%。
[0064]
本发明原则上对所述耐辐照聚酰亚胺泡沫材料的密度没有特别限制,本领域技术人员可以根据实际生产情况、应用要求以及质量控制进行选择和调整,本发明为更好的提高聚酰亚胺泡沫材料的耐辐照性能,保证材料主体的结构,保证泡沫材料原有的性能,减少辐照后的性能降低,所述耐辐照聚酰亚胺泡沫材料的密度优选为9~12kg/m3,更优选为9.5~11.5kg/m3,更优选为10~11kg/m3。
[0065]
本发明原则上对所述氧化铈颗粒的复合位置没有特别限制,本领域技术人员可以根据实际生产情况、应用要求以及质量控制进行选择和调整,本发明为更好的提高聚酰亚胺泡沫材料的耐辐照性能,保证材料主体的结构,保证泡沫材料原有的性能,减少辐照后的性能降低,所述氧化铈颗粒优选填充在所述泡孔间隙中、位于泡孔中和依附在泡孔的孔壁上的一种或多种,更优选为填充在所述泡孔间隙中、位于泡孔中和依附在泡孔的孔壁上。
[0066]
本发明原则上对所述耐辐照聚酰亚胺泡沫的具体应用没有特别限制,本领域技术人员可以根据实际生产情况、应用要求以及质量控制进行选择和调整,本发明为更好的提高聚酰亚胺泡沫材料的耐辐照性能,保证材料主体的结构,保证泡沫材料原有的性能,减少辐照后的性能降低,所述耐辐照聚酰亚胺泡沫材料优选包括船用耐辐照聚酰亚胺泡沫材料。
[0067]
本发明为完整和细化整体制备工艺,更好的提高聚酰亚胺泡沫材料的耐辐照性能,保证材料主体的结构,保证泡沫材料原有的性能,减少辐照后的性能降低,所述耐辐照聚酰亚胺泡沫材料中还优选包括匀泡剂。
[0068]
本发明提供了一种耐辐照聚酰亚胺泡沫材料,按原料质量分数计,包括:
[0069][0070][0071]
本发明上述耐辐照聚酰亚胺泡沫材料中,所述结构上的选择、组成和参数,以及相应的优选原则,与前述耐辐照聚酰亚胺泡沫材料中的结构上的选择、组成和参数,以及相应的优选原则,优选保持一致,在此不再一一赘述。在本发明中,重量份与质量百分含量仅是表述方式的不同,其本质含义是相同的,本领域技术人员能够基于基本常识清楚其正确含义,而且能够唯一确定。
[0072]
本发明所述异氰酸酯的加入量为15~63重量份,优选为20~58重量份,更优选为25~53重量份,更优选为30~48重量份,更优选为35~43重量份。本发明原则上对所述异氰酸酯的具体选择没有特别限制,本领域技术人员可以根据实际生产情况、应用要求以及质量控制进行选择和调整,本发明为更好的提高聚酰亚胺泡沫材料的耐辐照性能,保证材料主体的结构,保证泡沫材料原有的性能,减少辐照后的性能降低,所述异氰酸酯优选包括pm-200、ne-466、pm-400、pm-700、8122、8214和pm-8223中的一种或多种,更优选为pm-200、ne-466、pm-400、pm-700、8122、8214或pm-8223,具体的,可以为万华化学生产的pm-200、万华化学生产的ne-466、万华化学生产的pm-400、万华化学生产的pm-700、万华化学生产的8122、万华化学生产的8214或万华化学生产的pm-8223。本发明所述异氰酸酯的异氰酸根含量优选为28%~35%,更优选为29%~34%,更优选为30%~33%,更优选为31%~32%。
[0073]
本发明所述芳香族二酐的加入量为19~66重量份,优选为29~56重量份,更优选为39~46重量份。本发明原则上对所述芳香族二酐的具体选择没有特别限制,本领域技术人员可以根据实际生产情况、应用要求以及质量控制进行选择和调整,本发明为更好的提高聚酰亚胺泡沫材料的耐辐照性能,保证材料主体的结构,保证泡沫材料原有的性能,减少辐照后的性能降低,所述芳香族二酐优选包括btda、pmda和dsda中的一种或多种,更优选为btda、pmda或dsda。
[0074]
本发明所述溶剂的加入量为15~41重量份,优选为20~36重量份,更优选为25~31重量份。本发明原则上对所述溶剂的具体选择没有特别限制,本领域技术人员可以根据实际生产情况、应用要求以及质量控制进行选择和调整,本发明为更好的提高聚酰亚胺泡沫材料的耐辐照性能,保证材料主体的结构,保证泡沫材料原有的性能,减少辐照后的性能降低,所述溶剂优选包括dmso、dmf和dmac中的一种或多种,更优选为dmso、dmf或dmac。
[0075]
本发明所述发泡剂的加入量为0~25重量份,优选为5~20重量份,更优选为10~15重量份。本发明原则上对所述发泡剂的具体选择没有特别限制,本领域技术人员可以根据实际生产情况、应用要求以及质量控制进行选择和调整,本发明为更好的提高聚酰亚胺
泡沫材料的耐辐照性能,保证材料主体的结构,保证泡沫材料原有的性能,减少辐照后的性能降低,所述发泡剂优选包括丙酮、水、甲醇、乙醇和2-丁氧基乙醇中的一种或多种,更优选为丙酮、水、甲醇、乙醇或2-丁氧基乙醇。
[0076]
本发明所述匀泡剂的加入量为2~14重量份,优选为5~11重量份,更优选为8~9重量份。本发明原则上对所述匀泡剂的具体选择没有特别限制,本领域技术人员可以根据实际生产情况、应用要求以及质量控制进行选择和调整,本发明为更好的提高聚酰亚胺泡沫材料的耐辐照性能,保证材料主体的结构,保证泡沫材料原有的性能,减少辐照后的性能降低,所述匀泡剂优选包括聚醚改性硅油、硅酮类硅油和水溶性硅油的一种或多种,更优选为聚醚改性硅油、硅酮类硅油或水溶性硅油。
[0077]
本发明所述催化剂的加入量为0.1~8.5重量份,优选为2~6.5重量份,更优选为4~4.5重量份。本发明原则上对所述匀泡剂的具体选择没有特别限制,本领域技术人员可以根据实际生产情况、应用要求以及质量控制进行选择和调整,本发明为更好的提高聚酰亚胺泡沫材料的耐辐照性能,保证材料主体的结构,保证泡沫材料原有的性能,减少辐照后的性能降低,所述催化剂优选包括金属催化剂和/或胺类催化剂,更优选为金属催化剂或胺类催化剂。更具体的,所述催化剂优选包括二月桂酸二丁基锡、辛酸亚锡、异辛酸铋、n,n-二甲基环己胺、n,n,n',n'-四甲基亚烷基二胺和n,n'-二乙基哌嗪中的一种或多种,更优选为二月桂酸二丁基锡、辛酸亚锡、异辛酸铋、n,n-二甲基环己胺、n,n,n',n'-四甲基亚烷基二胺或n,n'-二乙基哌嗪。
[0078]
本发明所述水的加入量为20~40重量份,优选为24~36重量份,更优选为28~32重量份。
[0079]
本发明所述氧化铈的加入量为5~15重量份,优选为8~13重量份,更优选为10~11重量份。
[0080]
本发明提供了一种如上述技术方案中任意一项所述的耐辐照聚酰亚胺泡沫材料或上述技术方案中任意一项所述耐辐照聚酰亚胺泡沫材料的制备方法,包括以下步骤:
[0081]
1)将芳香族二酐和溶剂进行混合后,得到第一溶液;
[0082]
将氧化铈、水、发泡剂、匀泡剂和催化剂再次混合后,得到第二溶液;
[0083]
2)将上述步骤得到的第一溶液和第二溶液预混合,再与异氰酸酯经过最后混合,然后在模具中经过发泡成型,最后固化得到耐辐照聚酰亚胺泡沫材料。
[0084]
本发明上述耐辐照聚酰亚胺泡沫材料中,所述原料的选择和比例及其优选范围,与前述耐辐照聚酰亚胺泡沫材料中的原料的选择和比例及其优选范围优选保持一致,在此不再一一赘述。
[0085]
本发明首先将芳香族二酐和溶剂进行混合后,得到第一溶液。
[0086]
将氧化铈、水、发泡剂、匀泡剂和催化剂再次混合后,得到第二溶液。
[0087]
本发明原则上对混合的方式没有特别限制,本领域技术人员可以根据实际生产情况、应用要求以及质量控制进行选择和调整,本发明为更好的提高聚酰亚胺泡沫材料的耐辐照性能,保证材料主体的结构,保证泡沫材料原有的性能,减少辐照后的性能降低,所述混合的方式优选包括加热搅拌。
[0088]
本发明原则上对所述混合的温度没有特别限制,本领域技术人员可以根据实际生产情况、应用要求以及质量控制进行选择和调整,本发明为更好的提高聚酰亚胺泡沫材料
的耐辐照性能,保证材料主体的结构,保证泡沫材料原有的性能,减少辐照后的性能降低,所述混合的温度优选为60~80℃,更优选为64~76℃,更优选为68~72℃。
[0089]
本发明原则上对所述混合的转速没有特别限制,本领域技术人员可以根据实际生产情况、应用要求以及质量控制进行选择和调整,本发明为更好的提高聚酰亚胺泡沫材料的耐辐照性能,保证材料主体的结构,保证泡沫材料原有的性能,减少辐照后的性能降低,所述混合的转速优选为300~500r/min,更优选为340~460r/min,更优选为380~420r/min。
[0090]
本发明原则上对所述混合的时间没有特别限制,本领域技术人员可以根据实际生产情况、应用要求以及质量控制进行选择和调整,本发明为更好的提高聚酰亚胺泡沫材料的耐辐照性能,保证材料主体的结构,保证泡沫材料原有的性能,减少辐照后的性能降低,所述混合的时间优选为6~12h,更优选为7~11h,更优选为8~10h。
[0091]
本发明原则上对所述再次混合的方式没有特别限制,本领域技术人员可以根据实际生产情况、应用要求以及质量控制进行选择和调整,本发明为更好的提高聚酰亚胺泡沫材料的耐辐照性能,保证材料主体的结构,保证泡沫材料原有的性能,减少辐照后的性能降低,所述再次混合的方式优选包括超声混合。
[0092]
本发明原则上对所述超声混合的功率没有特别限制,本领域技术人员可以根据实际生产情况、应用要求以及质量控制进行选择和调整,本发明为更好的提高聚酰亚胺泡沫材料的耐辐照性能,保证材料主体的结构,保证泡沫材料原有的性能,减少辐照后的性能降低,所述超声混合的功率优选为100~150w,更优选为110~140w,更优选为120~130w。
[0093]
本发明原则上对所述再次混合的时间没有特别限制,本领域技术人员可以根据实际生产情况、应用要求以及质量控制进行选择和调整,本发明为更好的提高聚酰亚胺泡沫材料的耐辐照性能,保证材料主体的结构,保证泡沫材料原有的性能,减少辐照后的性能降低,所述再次混合的时间优选为10~15min,更优选为11~14min,更优选为12~13min。
[0094]
本发明最后将上述步骤得到的第一溶液和第二溶液预混合,再与异氰酸酯经过最后混合,然后在模具中经过发泡成型,最后固化得到耐辐照聚酰亚胺泡沫材料。
[0095]
本发明原则上对所述最后混合的方式没有特别限制,本领域技术人员可以根据实际生产情况、应用要求以及质量控制进行选择和调整,本发明为更好的提高聚酰亚胺泡沫材料的耐辐照性能,保证材料主体的结构,保证泡沫材料原有的性能,减少辐照后的性能降低,所述最后混合的方式优选包括高速搅拌混合。
[0096]
本发明原则上对所述最后混合的转速没有特别限制,本领域技术人员可以根据实际生产情况、应用要求以及质量控制进行选择和调整,本发明为更好的提高聚酰亚胺泡沫材料的耐辐照性能,保证材料主体的结构,保证泡沫材料原有的性能,减少辐照后的性能降低,所述最后混合的转速优选为1000~3000r/min,更优选为1400~2600r/min,更优选为1800~2200r/min。
[0097]
本发明原则上对所述最后混合的时间没有特别限制,本领域技术人员可以根据实际生产情况、应用要求以及质量控制进行选择和调整,本发明为更好的提高聚酰亚胺泡沫材料的耐辐照性能,保证材料主体的结构,保证泡沫材料原有的性能,减少辐照后的性能降低,所述最后混合的时间优选为15~30s,更优选为18~27s,更优选为21~24s。
[0098]
本发明原则上对所述发泡成型的时间没有特别限制,本领域技术人员可以根据实
际生产情况、应用要求以及质量控制进行选择和调整,本发明为更好的提高聚酰亚胺泡沫材料的耐辐照性能,保证材料主体的结构,保证泡沫材料原有的性能,减少辐照后的性能降低,所述发泡成型的时间优选为15~20min,更优选为16~19min,更优选为17~18min。
[0099]
本发明原则上对所述固化的温度没有特别限制,本领域技术人员可以根据实际生产情况、应用要求以及质量控制进行选择和调整,本发明为更好的提高聚酰亚胺泡沫材料的耐辐照性能,保证材料主体的结构,保证泡沫材料原有的性能,减少辐照后的性能降低,所述固化的温度优选为200~300℃,更优选为220~280℃,更优选为240~260℃。
[0100]
本发明原则上对所述固化的时间没有特别限制,本领域技术人员可以根据实际生产情况、应用要求以及质量控制进行选择和调整,本发明为更好的提高聚酰亚胺泡沫材料的耐辐照性能,保证材料主体的结构,保证泡沫材料原有的性能,减少辐照后的性能降低,所述固化的时间优选为4~8h,更优选为4.5~7.5h,更优选为5~7h,更优选为5.5~6.5h。
[0101]
本发明为完整和细化整个制备工艺,更好的提高聚酰亚胺泡沫材料的耐辐照性能,保证材料主体的结构,保证泡沫材料原有的性能,减少辐照后的性能降低,上述耐辐照聚酰亚胺泡沫材料的制备过程具体可以为以下步骤:
[0102]
(1)将19~66份芳香族二酐和15~41份溶剂混合,加热搅拌;
[0103]
(2)将5~15份氧化铈与20~40份水混合,超声分散,加入0~25份发泡剂,2~14份匀泡剂,0.1~8.5份催化剂,搅拌均匀;
[0104]
(3)将上述两种溶液混合均匀后,加入15~63份异氰酸酯,搅拌均匀,注入模具,室温发泡成型;进行烘烤固化,得到船用耐辐照聚酰亚胺泡沫材料。
[0105]
本发明还提供了上述技术方案中任意一项所述的耐辐照聚酰亚胺泡沫材料、上述技术方案中任意一项所述耐辐照聚酰亚胺泡沫材料或上述技术方案中任意一项所述的制备方法所制备的耐辐照聚酰亚胺泡沫材料在船舶领域的应用。
[0106]
本发明上述步骤提供了一种船用耐辐照聚酰亚胺泡沫材料及其制备方法、应用,该耐辐照聚酰亚胺泡沫材料中含有氧化铈颗粒,而且氧化铈颗粒以特定的形式复合在多孔的聚酰亚胺泡沫中。本发明通过超声波空化作用产生的高剪切力,将对核辐射具有阻挡屏蔽作用且环境友好的氧化铈颗粒细化成纳米级,经高速搅拌、室温成型和后固化等工序处理,复合在聚酰亚胺泡沫材料中,稀土离子的外层空轨道与酰亚胺环中n和/或o原子提供的孤对电子或不定域电子有效结合形成键合作用,实现了物理复合和化学键合相结合的特定复合形式,进而有效提升了聚酰亚胺泡沫材料的耐辐照性能。与具有化学毒性的铅、钨、钡等重金属传统屏蔽材料相比,氧化铈不仅能够有效提升聚酰亚胺泡沫材料的耐辐照性能,而且对环境无任何威胁。氧化铈之所以能够有效提升材料的耐辐照性能,主要在于当辐射在穿过氧化铈时,会发生能够吸收或者散射x射线、γ射线等辐射的光电效应、康普顿效应以及电子对效应,从而使其具有阻挡屏蔽辐射的作用。稀土离子的外层空轨道与酰亚胺环中n和o原子提供的孤对电子或不定域电子有效结合形成的稳定键合作用,可有效保证氧化铈在聚酰亚胺泡沫体系中均匀分散,最大化了量效比,减少了添加量对于整体性能的降低的影响。
[0107]
而且本发明提供的耐辐照聚酰亚胺泡沫材料制备工艺简单、易于控制,有利于实现工业连续化生产,本发明可有效的提高船用聚酰亚胺泡沫材料的耐辐照性能,对提升核动力船舶安全性能和满足环保要求来说,具有重要的借鉴意义。
[0108]
实验结果表明,本发明提供的耐辐照聚酰亚胺泡沫在辐照过后,力学性能受到的影响较小,拉伸强度下降11.1%、撕裂强度下降10.5%、压缩强度下降11.7%,而未加氧化铈颗粒的聚酰亚胺泡沫拉伸、撕裂、压缩强度分别下降了51.9%、59%、58.5%。由此可见,氧化铈颗粒的加入提高了聚酰亚胺泡沫的耐辐照性能。
[0109]
为了进一步说明本发明,以下结合实施例对本发明提供的一种耐辐照聚酰亚胺泡沫材料及其制备方法、应用进行详细描述,但是应当理解,这些实施例是在以本发明技术方案为前提下进行实施,给出了详细的实施方式和具体的操作过程,只是为进一步说明本发明的特征和优点,而不是对本发明权利要求的限制,本发明的保护范围也不限于下述的实施例。
[0110]
实施例1
[0111]
按配方将24份pmda和30份dmf混合,加热搅拌升温至80℃,反应6h;将5份氧化铈与30份水混合,150w功率超声分散15min,加入1.2份甲醇,2份聚醚改性硅油,0.5份金属催化剂,搅拌均匀;将上述两种溶液混合均匀后,加入40份pm-400,2000r/min搅拌12s,注入模具,室温发泡成型。以220℃进行烘烤固化5h,得到船用耐辐照聚酰亚胺泡沫材料。
[0112]
实施例2
[0113]
按配方将24份pmda和30份dmf混合,加热搅拌升温至80℃,反应6h;将10份氧化铈与30份水混合,150w功率超声分散15min,加入1.2份甲醇,2份聚醚改性硅油,0.5份金属催化剂,搅拌均匀;将上述两种溶液混合均匀后,加入40份pm-400,2000r/min搅拌12s,注入模具,室温发泡成型。以220℃进行烘烤固化5h,得到船用耐辐照聚酰亚胺泡沫材料。
[0114]
实施例3
[0115]
按配方将24份pmda和30份dmf混合,加热搅拌升温至80℃,反应6h;将15份氧化铈与30份水混合,150w功率超声分散15min,加入1.2份甲醇,2份聚醚改性硅油,0.5份金属催化剂,搅拌均匀;将上述两种溶液混合均匀后,加入40份pm-400,2000r/min搅拌12s,注入模具,室温发泡成型。以220℃进行烘烤固化5h,得到船用耐辐照聚酰亚胺泡沫材料。
[0116]
对比例1
[0117]
按配方将24份pmda和30份dmf混合,加热搅拌升温至80℃,反应6h;加入30份水,1.2份甲醇,2份聚醚改性硅油,0.5份金属催化剂,搅拌均匀;将上述两种溶液混合均匀后,加入40份pm-400,2000r/min搅拌12s,注入模具,室温发泡成型。以220℃进行烘烤固化5h,得到聚酰亚胺泡沫材料。
[0118]
对本发明实施例制备的耐辐照聚酰亚胺泡沫材料和对比例制备的聚酰亚胺泡沫材料进行性能检测。
[0119]
辐照后的样品数据为样品吸收10125gy辐照量后测试得到,辐照源为
60
co-γ射线。拉伸强度测试标准为gb/t 6344-2008、撕裂强度测试标准为gb/t529-2008、压缩强度测试标准为gb/t 8813-2008。
[0120]
参见表1,表1为本发明实施例制备的耐辐照聚酰亚胺泡沫材料和对比例制备的聚酰亚胺泡沫材料的性能检测结果。
[0121]
表1
[0122][0123]
由表1中的实验数据可以看出,氧化铈的加入能够保持聚酰亚胺泡沫的力学性能较为稳定,仅有很小幅度的下降,却大幅提高了聚酰亚胺泡沫的耐辐照性能。未加氧化铈的样品拉伸强度,在辐照过后下降了51.9%,加了5份氧化铈,10份氧化铈,15份氧化铈的样品拉伸强度下降了11.4%,11.1%,12%;未加氧化铈的样品撕裂强度,在辐照过后下降了59%,加了5份氧化铈,10份氧化铈,15份氧化铈的样品撕裂强度下降了13.3%,12.3%,10.5%;未加氧化铈的样品压缩强度,在辐照过后下降了58.5%,加了5份氧化铈,10份氧化铈,15份氧化铈的样品压缩强度下降了11.7%,13.2%,12.8%。因而,氧化铈的加入对聚酰亚胺泡沫的耐辐照性能有显著提升。
[0124]
以上对本发明提供的一种船用耐辐照聚酰亚胺泡沫材料及其制备方法、应用进行了详细的介绍,本文中应用了具体个例对本发明的原理及实施方式进行了阐述,以上实施例的说明只是用于帮助理解本发明的方法及其核心思想,包括最佳方式,并且也使得本领域的任何技术人员都能够实践本发明,包括制造和使用任何装置或系统,和实施任何结合的方法。应当指出,对于本技术领域的普通技术人员来说,在不脱离本发明原理的前提下,还可以对本发明进行若干改进和修饰,这些改进和修饰也落入本发明权利要求的保护范围内。本发明专利保护的范围通过权利要求来限定,并可包括本领域技术人员能够想到的其他实施例。如果这些其他实施例具有不是不同于权利要求文字表述的结构要素,或者如果它们包括与权利要求的文字表述无实质差异的等同结构要素,那么这些其他实施例也应包含在权利要求的范围内。